Abstract
This study investigates the comparative performance of Copper-Iron (CuFe) and Copper-Tin (CuSn) alloys in crimping processes, with a focus on their mechanical, electrical, and corrosion-resistance properties. Crimping is a critical method for creating reliable electrical and mechanical connections, particularly in environments subjected to significant mechanical stress and varying temperatures [1]. CuFe alloys, known for their superior mechanical strength and hardness, present challenges in crimping due to their increased resistivity and reduced ductility. Conversely, CuSn alloys offer a balance between electrical conductivity, ease of crimping, and corrosion resistance, making them a preferred choice in many industrial applications. This research aims to provide a comprehensive analysis of how the distinct properties of CuFe and CuSn alloys influence the crimping process, ultimately guiding material selection for optimized performance in various applications [2]. Experimental data will be drawn from tensile strength tests, electrical resistance measurements, and corrosion tests, providing a holistic understanding of the advantages and limitations of each alloy.
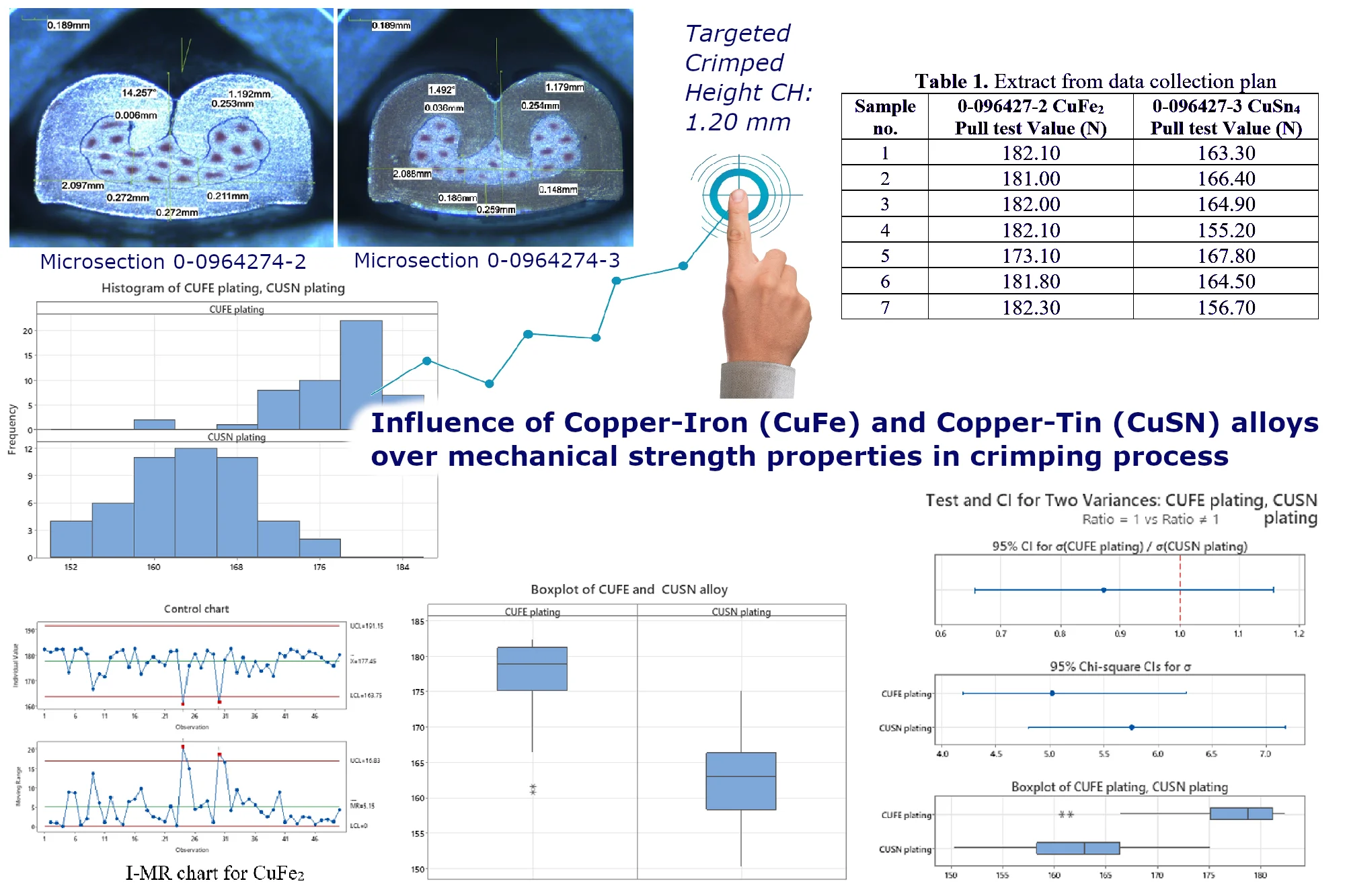
Highlights
- CuFe2 alloys higher tensile strength.
- CuSn4 alloys lower tensile strength but inside international standard requirements.
- No significant statistical difference between the 2 alloys in relation to crimping process stability.
- The choice between usage of CuFe2 or CuSn4 should be driven by the application and not by the crimp design.
1. Introduction
Crimping is a widely used method in electrical and mechanical engineering for joining components, particularly in the assembly of connectors, terminals, and other conductive elements. The integrity of crimped connections is highly dependent on the materials used, as they must ensure both mechanical robustness and electrical conductivity while withstanding environmental stresses [3]. Among the materials commonly used in crimping, copper-based alloys such as Copper-Iron (CuFe) and Copper-Tin (CuSn) have gained significant attention due to their distinctive properties.
CuFe alloys are known due to their high mechanical strength and hardness, properties obtained by the addition of iron to copper. These characteristics make CuFe alloys suitable for applications requiring high durability and resistance to mechanical deformation. However, the increased resistivity and reduced ductility of CuFe alloys pose challenges in crimping processes, where ease of deformation and low electrical resistance are crucial.
On the other hand, CuSn alloys, formed by alloying copper with tin, present a more balanced set of properties. The addition of tin enhances the corrosion resistance and maintains high electrical conductivity while offering sufficient ductility for effective crimping. These properties make CuSn alloys favorable in applications where long-term reliability and electrical performance are critical.
The existing literature provides substantial insights into the individual properties of CuFe and CuSn alloys, particularly concerning their mechanical and electrical behavior. However, a direct comparison of their performance in crimping processes remains underexplored. This research aims to fill this gap by systematically examining how the unique properties of CuFe and CuSn alloys affect the quality and reliability of crimped connections with a clear focus of understanding if there is a significant influence on the geometry of the crimped connection [4]. Through a combination of experimental analysis and theoretical modeling, this study will evaluate the suitability of each alloy in different crimping applications, providing valuable guidance related to the overall influence over the mechanical strength obtained following the behavior of the pull test values.
2. Methods
The study consists in the analysis of one hundred samples divided in two groups: 50 samples using one type of terminal 0-0964274-2 (CuFe2) and 50 samples using terminal 0-0964274-3 (CuSn4) in combination with the same type of cable FLRY A with a cross-sectional area of 1.00 square millimeters [5], which are commonly used in automotive applications due to their flexibility and durability. The Crimped Height (CH) targeted was the one specified by the supplier of the terminal CH: 1.20 mm valid for all the one hundred samples used [6].
To achieve the agreed crimp height configuration we utilized a bech press Schafer EPS 2000 and the crimped dimensions were ensured using the specification requirments from the terminal data sheet and obtaining in both cases the same crimp height (CH) measurement of 1.20 mm (Figs. 1-2).
Fig. 1Microsection 0-0964274-2
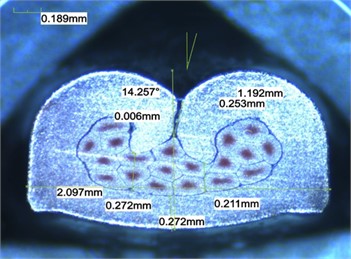
Fig. 2Microsection 0-0964274-3
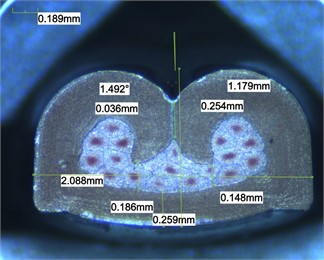
The pull test was conducted using a calibrated tensile testing machine Mecmesin AFG 1000, which applies a steadily increasing force to the crimped terminal until failure occurs. The machine was set to operate at a constant speed, and the pull test values were recorded in a data collection plan (Table 1).
Table 1Extract from data collection plan
Sample no. | 0-096427-2 CuFe2 pull test value (N) | 0-096427-3 CuSn4 pull test value (N) |
1 | 182.10 | 163.30 |
2 | 181.00 | 166.40 |
3 | 182.00 | 164.90 |
4 | 182.10 | 155.20 |
5 | 173.10 | 167.80 |
6 | 181.80 | 164.50 |
7 | 182.30 | 156.70 |
3. Statistical analysis
The full range of the one hundred samples measurements were used as an input in the next phase of the experiment related to the statistical analyses of the recorded data using Minitab Software [7], as processing tool. The base of this study was to determine if during the life cycle of a crimped joint the main characteristic which is the geometry of the assembly expressed by the crimp height together with the connected characteristic as pull test values for the two different terminals with different alloys CuFe and CuSN have a relationship between them, if these variables are influencing each other and if they do what is the degree of interdependency.
We begin our statistical analysis with a capability study for each group of data sets to understand if there is a significant difference in the stability of the crimping process (Fig. 3).
Fig. 3I-MR chart
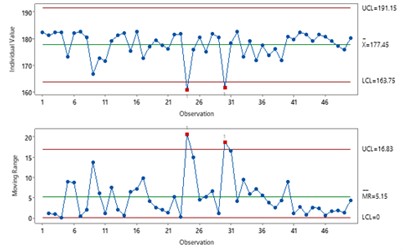
a) CuFe2
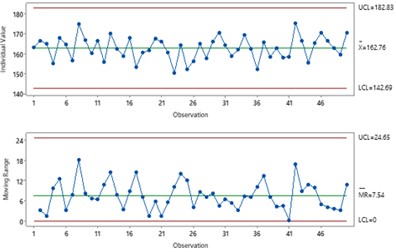
b) CuSn4
What we observed is that from stability of the crimping process point of view the terminal with CuSn4 alloy have all the data point inside the control limits and seems more stable that the terminal with CuFe2 alloy. We still need to specify that these control limits were calculated versus the process and that actually in the global accepted standards there is only a lower control limit specification LCL = 120 N [8], or even less according to European standards LCL = 108 N [9], as minimum requirement. Taking this in consideration both terminal are way above this limit and so we plot the data in a Box plot format to understand if there is a significant difference in relation to the mean and the median on both groups (Fig. 4).
Fig. 4Box plot for CuFe2 and CuSn4 alloy
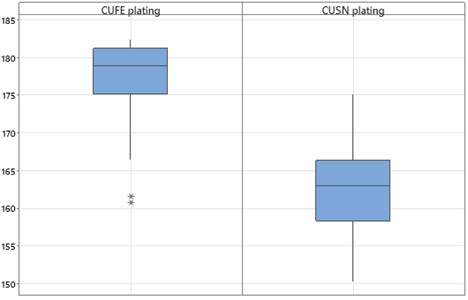
Looking at the results we could conclude that the terminal with CuFe2 alloy is showing a better much stronger connection with main values above 175 N in comparison to the CuSn4 alloy which is below that range.
To assess from statistical point of view this conclusion we finally perform a test of equal variance that have the purpose of showing if there is a significant statistical difference and subsequently showing that the alloys used in the crimping process will have a significant impact in the geometry of the crimping assembly (Figs. 5-6).
Fig. 5Pull test histogram of CuFe2 and CuSn4 alloy
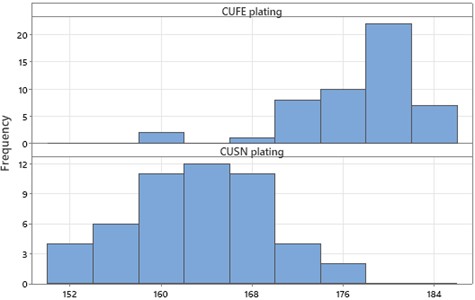
Fig. 6F-test report for two variances of both alloys
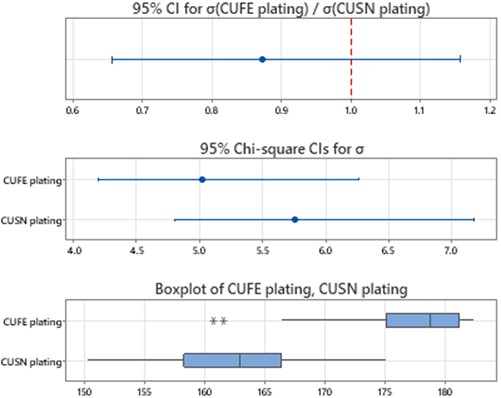
4. Tests results and additional considerations
The -value of 0.345 indicates that there is a 34.5 % probability of obtaining a test statistic as extreme as, or more extreme than, the one observed, assuming that the null hypothesis is true (i.e. assuming that the variances are equal). A higher p-value suggests weaker evidence against the null hypothesis. In hypothesis testing, common significance levels used to determine whether to reject the null hypothesis are 0.05, 0.01, or 0.10. Since 0.345 is greater than these common significance levels, we fail to reject the null hypothesis. This means there isn’t strong enough evidence to conclude that the variances are different. In other words, the data does not provide sufficient evidence to suggest that the two variances are significantly different.
Based on the -value of 0.345, we do not have enough evidence to reject the null hypothesis. Therefore, we would conclude that there is no significant difference between the two variances at the chosen significance level. This outcome suggests that, according to the data and under the assumption of the test, the variances of the two populations are not statistically significantly different.
5. Conclusions
This study presents a comparative analysis of Copper-Iron (CuFe) and Copper-Tin (CuSn) alloys in the context of their application in the crimping process, particularly focusing on mechanical strength as measured by pull test values. The research aimed to determine if the different properties of these alloys would significantly influence the crimp geometry and ultimately affect the reliability of the electrical connections.
The experimental results revealed that while CuFe alloys tend to exhibit higher mechanical strength, as indicated by their superior pull test values (above 175 N), CuSn alloys also maintain sufficient strength, with pull test values consistently above the industry-standard lower control limit of 90 N. Despite these differences, the statistical analysis, including capability studies and variance testing, indicated that there is no significant statistical difference between the two materials in terms of their impact on the crimping process's stability and crimp geometry. The -value obtained (0.345) from the F-test suggests that the variances between the two alloy groups are not statistically different. This outcome implies that although CuFe and CuSn alloys exhibit distinct mechanical properties, their influence on the crimp geometry is comparable, and neither alloy demonstrates a statistically significant advantage over the other in terms of crimp reliability.
These findings suggest that both CuFe and CuSn alloys are suitable for use in crimping processes under similar conditions, with the choice of material being driven more by specific application requirements – such as corrosion resistance or conductivity – rather than concerns over crimp geometry or mechanical robustness. This insight provides valuable guidance for industries that rely on crimped connections, ensuring that material selection can be optimized based on the broader operational demands rather than solely on crimping performance.
By providing a comparative analysis of Copper-Iron (CuFe) and Copper-Tin (CuSn) alloys, the study highlights the importance of material properties in determining mechanical strength, electrical performance. In crimping processes, where mechanical robustness and electrical conductivity are crucial, understanding the behaviour of these alloys is critical for optimizing the performance of electrical connections under various environmental stresses. For mechanical engineers, these insights are valuable in improving the reliability and longevity of crimped connections, a fundamental aspect of many industries, from automotive to electronics. Material scientists can further benefit from the detailed exploration of how alloy composition influences performance metrics such as pull test values, providing a foundation for future research in alloy optimization for specific engineering applications.
The novelty of this study lies in its direct comparative analysis of CuFe and CuSn alloys in crimping processes, a subject that has been relatively unexplored in existing literature. While prior research has addressed the individual properties of these alloys, this study uniquely focuses on their performance in practical crimping applications, offering a clear understanding of how their mechanical and electrical characteristics influence the reliability of crimped connections. The use of comprehensive experimental data, including tensile strength tests and statistical analyses, provides new insights into how material selection impacts crimp geometry and overall connection quality. This study not only fills a critical gap in the existing body of knowledge but also sets the stage for further investigations into the interplay between alloy composition and crimping technologies, paving the way for more informed material choices in industrial applications.
References
-
F. J. G. Silva, L. Morgado, A. Teixeira, J. C. Sá, L. P. Ferreira, and F. Almeida, “Analysis and development of a failure prediction model for electrical terminals used in the automotive industry,” Procedia Manufacturing, Vol. 51, pp. 207–214, Jan. 2020, https://doi.org/10.1016/j.promfg.2020.10.030
-
K. Jongwuttanaruk and C. Thavornwat, “Optimization of mechanical crimping in the terminal crimping process using a response surface methodology,” Advances in Materials Science and Engineering, Vol. 2022, p. 6508289, Feb. 2022, https://doi.org/10.1155/2022/6508289
-
T. A. M. Castro, F. J. G. Silva, and R. D. S. G. Campilho, “Optimising a specific tool for electrical terminals crimping process,” Procedia Manufacturing, Vol. 11, pp. 1438–1447, Jan. 2017, https://doi.org/10.1016/j.promfg.2017.07.274
-
F. Dragomir, T. Manescu, and Z.-I. Praisach, “Crimping standard DIN vs USCAR gap analysis,” Studia Engineering, Vol 60, Special Issue, Vol. 60, pp. 47–54, 2023, https://doi.org/1024193/subbeng.2023.spiss.5
-
“Leoni Kabel,” Technical data sheet, FLRY10-A, 76783050.
-
“Application Specification Micro-Timer 2+3,” 114-18081, Oct. 2021.
-
M. R. Delozier and S. Orlich, “Discovering influential cases in linear regression with MINITAB,” Statistical Methodology, Vol. 2, No. 2, pp. 71–81, Jul. 2005, https://doi.org/10.1016/j.stamet.2004.11.005
-
“Performance specification for cable-to-terminal electrical crimps,” SAE/USCAR21-4, SAE International, 2020.
-
“Solderless connections, Part2: solderless crimped connections, general requirements, test methods and practical guidance,” SR EN 6032-2:2006/A1:2014, 2014.
About this article
The authors have not disclosed any funding.
The datasets generated during and/or analyzed during the current study are available from the corresponding author on reasonable request.
The authors declare that they have no conflict of interest.