Abstract
This study provides a comprehensive evaluation of the stability of crimping of the same terminal on FLRY A cables using three different applicators. The research involved conducting pull tests on 50 samples for each applicator type, analyzing the results using Minitab software to assess the consistency and strength of the crimp connections. The findings indicate that while the Demirel applicator produces the highest average pull test values, the Tyco applicator demonstrates superior consistency, making it more suitable for applications where process stability is critical.
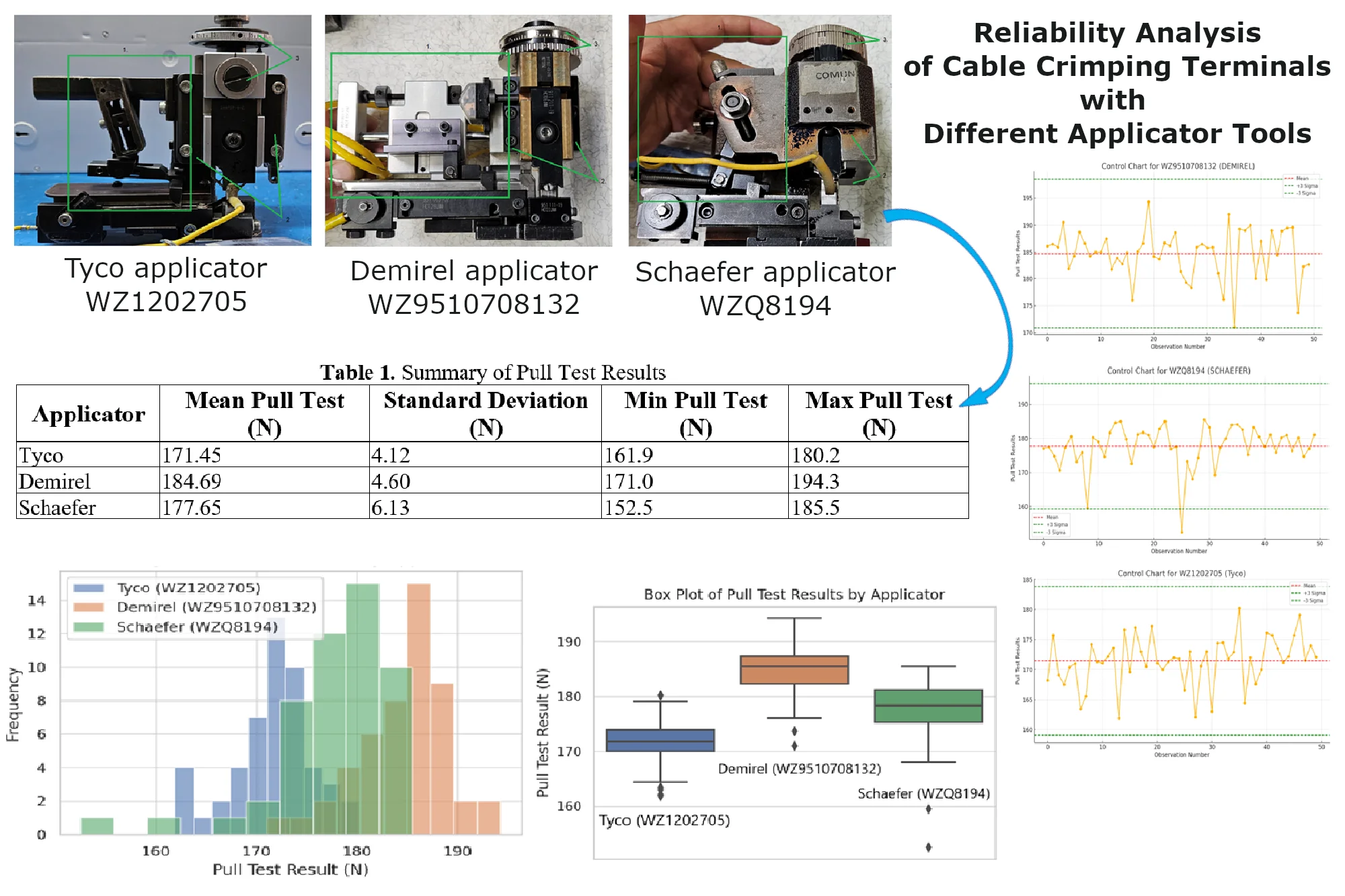
Highlights
- This study provides a comprehensive evaluation of the stability of crimping of the same terminal and on the same cables using three different applicators.
- The research involved conducting pull tests on 50 samples for each applicator type, analyzing the results using Minitab software to assess the consistency and strength of the crimp connections..
- One applicator demonstrates superior consistency with the lowest variability in pull test results, indicating a highly stable crimping process.
- These findings have direct engineering implications for automotive manufacturing, particularly in the assembly of wiring harnesses. They also provide valuable insights for selecting crimping tools in other industries where reliable electrical connections are essential.
1. Introduction
Crimping is a critical process in manufacturing electrical connections, particularly in the automotive industry, where reliability directly impacts vehicle safety and performance. It involves compressing a terminal onto the end of a wire to create a secure, mechanically and electrically sound connection. The quality of these connections is influenced by various factors, such as crimp height, material properties of the wire and terminal, and the precision of the crimping equipment. Given that automotive crimped connections must endure harsh environmental conditions – including extreme temperatures, vibrations, and corrosive elements – ensuring stability and consistency in the crimping process is essential. Variations in crimp quality can lead to electrical failures, compromising vehicle safety and resulting in costly recalls.
Existing research highlights several approaches to optimize and assess crimping processes. Mocellin and Petitprez [1] developed a computational model validated by experiments to predict mechanical resistance in crimped assemblies, particularly for aeronautical applications. Studies like these emphasize the importance of optimizing crimping processes to ensure reliability in various sectors, including automotive and aerospace. The role of material properties and manufacturing precision is also critical, as minor components, such as electrical terminals, can significantly affect safety and performance in vehicles [2]. Furthermore, methodologies like response surface designs have been employed to optimize tensile mechanical properties, identifying optimal crimp dimensions to ensure compliance with industry standards [3].
Various tools and techniques have been developed to improve crimping accuracy and efficiency. For example, Castro et al. [4] created a versatile crimping tool that can adapt to different terminal types, enhancing operational efficiency and precision. Standards such as USCAR-21 [5] provide detailed specifications for testing the performance of crimped connections, ensuring they meet safety and durability requirements. Additionally, studies utilizing Finite Element Method (FEM) analysis have explored the impact of design variables on compression rates, optimizing punch stroke and terminal length for better performance [6]. The focus was also on improving defect detection in automated crimping processes by implementing skewed tolerance settings, which significantly reduce miss rates and false alarms [7].
Building upon prior studies, this research focuses on evaluating the stability of crimping identical terminals using three different applicators – Tyco WZ1202705, Demirel WZ9510708132, and Schaefer WZQ8194 – on FLRY A cables, which are commonly used in the automotive industry. This comparative analysis isolates the effect of the applicators themselves on crimp performance, providing valuable insights for optimizing tool selection to enhance production consistency. Previous research by Ilca et al. [8] explored the wear and tear of crimping tools, emphasizing the importance of tool lifespan in reducing production costs. This study extends that work by examining the uniformity and strength of crimps under different conditions, contributing to a deeper understanding of crimping tool performance in automotive electrical systems.
2. Methods and experimental setup
This study evaluates the stability of crimped connections using three different crimp applicators on FLRY A cables (0.75 sq. mm) and terminals (5-0963715-1), commonly used in automotive applications. By keeping the cable and terminal types consistent, the study aimed to isolate the performance of the applicators, ensuring a fair comparison.
The experiment involved three different crimp applicators:
• Tyco WZ1202705: High-precision applicator known for consistent performance, featuring mechanical terminal feeding, half-open RAM clamping, and curved terminal geometry after crimping (Fig. 1).
• Demirel WZ9510708132: A robust, widely used pneumatic applicator with similar RAM clamping and curved terminal geometry (Fig. 2).
• Schaefer WZQ8194: Designed for versatility, featuring mechanical feeding with a spiral spring, closed RAM clamping, and a straighter terminal base after crimping (Fig. 3).
Fig. 1Tyco applicator WZ1202705
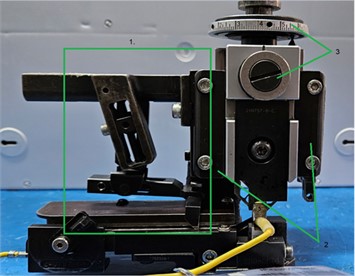
Fig. 2Demirel applicator WZ9510708132
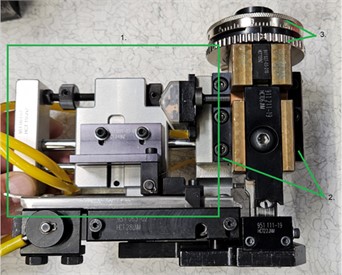
Fig. 3Schaefer applicator WZQ8194
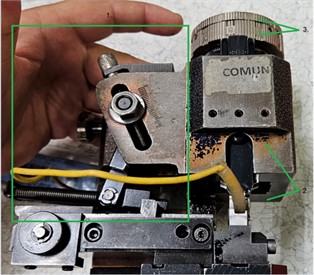
For each applicator, 50 samples were prepared using the same cable and terminal, with crimp height adjusted per manufacturer specifications. A Schaefer EPS300 press was used for crimping, and pull tests were conducted to measure the force required to separate the crimped terminal from the cable.
The pull test, a standard method for assessing crimp strength, applies tensile force to the terminal until failure. The force at which separation occurs is recorded, with higher values indicating stronger connections.
The tests were performed using a calibrated tensile testing machine set to a constant speed, and the results were analyzed using Minitab software. Minitab calculated key metrics, such as mean, standard deviation, and range of pull test results for each applicator. Capability analysis was also performed to evaluate each applicator’s ability to meet quality standards, with process control charts visualizing consistency and hypothesis testing identifying significant performance differences.
3. Results and discussions
The pull test results for the three applicators are summarized in Table 1. The data shows that the Demirel applicator produced the highest average pull test values, indicating that it creates the strongest crimp connections. However, the Tyco applicator exhibited the lowest variability in pull test results, suggesting that it provides more consistent performance. The Schaefer applicator, while also producing strong connections, showed the highest variability, which may indicate less stable performance.
To better understand the performance of each applicator, graphical representations of the data were created. These graphs include histograms, box plots, and control charts to visually assess the distribution and stability of the crimping process.
Table 1Summary of pull test results
Applicator | Mean pull test (N) | Standard deviation (N) | Min pull test (N) | Max pull test (N) |
Tyco | 171.45 | 4.12 | 161.9 | 180.2 |
Demirel | 184.69 | 4.60 | 171.0 | 194.3 |
Schaefer | 177.65 | 6.13 | 152.5 | 185.5 |
Histogram (Fig. 4) show the distribution of pull test results for each applicator. The Tyco applicator displays a relatively tight distribution centered around 171.45 N, indicating consistent performance. The Demirel applicator shows a higher mean value, with a slightly broader distribution. The Schaefer applicator's distribution is the broadest, highlighting the variability in its performance.
Fig. 4Histogram with data distribution per applicator
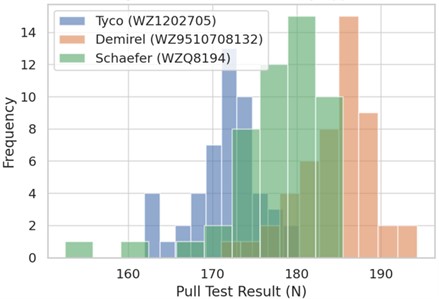
The box plot (Fig. 5) provides a visual summary of the pull test results, showing the median, quartiles, and potential outliers. The Tyco applicator exhibits a narrow interquartile range (IQR), indicating consistent crimp quality. The Demirel applicator, while having a higher median pull test value, shows a wider IQR. The Schaefer applicator has the widest IQR and several outliers, suggesting variability in crimp performance.
Fig. 5Box plot showing median, quartiles, and outliers per applicator
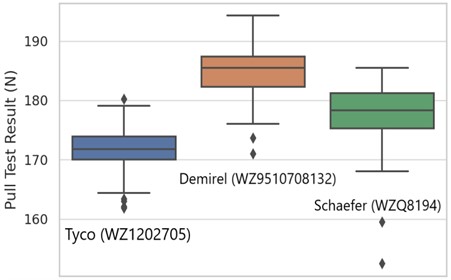
Fig. 6Control charts
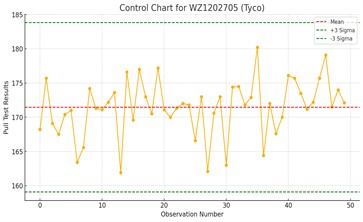
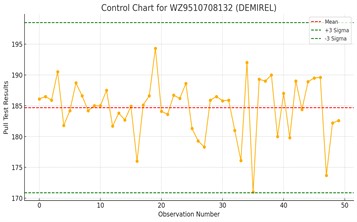
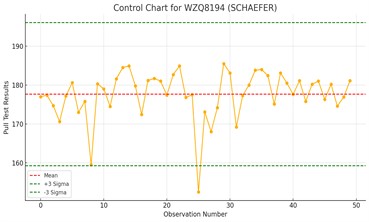
Control charts (Fig. 6) were generated to assess the stability of the crimping process for each applicator. The charts plot the pull test results over time (sample number) and include control limits to identify any out-of-control points.
Tyco (WZ1202705): The control chart for Tyco shows all points within the control limits, indicating a stable and consistent process.
Demirel (WZ9510708132): The Demirel chart also shows a stable process, with most points within the control limits, though a few points approach the upper control limit.
Schaefer (WZQ8194): The Schaefer control chart displays several points outside the control limits, indicating variability and potential issues with process stability.
To ensure consistency in evaluating crimping process stability, identical terminal (5-0963715-1) and cable type (FLRY A) were used across all tests. By maintaining uniform parameters such as crimp height and material properties, we isolated the primary variable – the stability of the crimping process – minimizing external influences. This setup allowed for a fair comparison of three different crimp applicators: Tyco WZ1202705, Demirel WZ9510708132, and Schaefer WZQ8194, each representing unique design approaches. Differences in applicator geometry, mechanical design, and material composition were critical in understanding the performance variations observed.
Crimp parameters, such as crimp height and force, were adjusted within manufacturer-specified tolerances, ensuring consistency in performance. This adherence to tolerances reflects the real-world conditions in automotive manufacturing, where maintaining tight control over process parameters is essential for producing reliable crimped connections.
The graphical analysis of pull test results highlights distinct performance trends among the applicators:
– Tyco WZ1202705: Exhibited minimal variability, with a tight distribution and no outliers, indicating a stable and consistent crimping process. Despite a lower mean pull test value compared to Demirel, its uniformity suggests it is highly reliable for applications requiring consistent crimp quality.
– Demirel WZ9510708132: Showed the highest mean pull test value, producing robust connections, though with greater variability. Some results approached control limits, indicating that enhanced process control may be needed to ensure consistent quality.
– Schaefer WZQ8194: Displayed the highest variability, with a wide distribution and multiple outliers, pointing to potential inconsistencies in the crimping process. While capable of strong connections, its lack of consistency raises concerns for applications requiring stringent quality control.
4. Conclusions
The pull test analysis of the Tyco, Demirel, and Schaefer crimp applicators highlights key differences that are critical for automotive applications. The Demirel applicator achieves the highest mean pull strength, making it ideal for applications where maximum crimp strength is essential. However, high strength alone is not sufficient; consistency and process stability must also be considered.
The Tyco applicator demonstrates superior consistency with the lowest variability in pull test results, indicating a highly stable crimping process. This makes Tyco the optimal choice for applications requiring uniformity and reliability, even though its pull strength is slightly lower than Demirel’s. For environments where crimp quality must be consistently high across all connections, Tyco’s stability is crucial.
The choice of crimp applicator depends on the specific needs of the application. The Tyco applicator is recommended for high-stakes environments where both strength and consistency are required. The Demirel applicator, while offering superior strength, is better suited to situations where some variability can be tolerated. Schaefer may require further optimization to be used in critical applications.
These findings have direct engineering implications for automotive manufacturing, particularly in the assembly of wiring harnesses. They also provide valuable insights for selecting crimping tools in other industries where reliable electrical connections are essential, such as aerospace, telecommunications, and electronics.
References
-
K. Mocellin and M. Petitprez, “Experimental and numerical analysis of electrical contact crimping to predict mechanical strength,” Procedia Engineering, Vol. 81, pp. 2018–2023, Jan. 2014, https://doi.org/10.1016/j.proeng.2014.10.274
-
F. J. G. Silva, L. Morgado, A. Teixeira, J. C. Sá, L. P. Ferreira, and F. Almeida, “Analysis and development of a failure prediction model for electrical terminals used in the automotive industry,” Procedia Manufacturing, Vol. 51, pp. 207–214, Jan. 2020, https://doi.org/10.1016/j.promfg.2020.10.030
-
K. Jongwuttanaruk and C. Thavornwat, “Optimization of mechanical crimping in the terminal crimping process using a response surface methodology,” Advances in Materials Science and Engineering, Vol. 2022, Feb. 2022, https://doi.org/10.1155/2022/6508289
-
T. A. M. Castro, F. J. G. Silva, and R. D. S. G. Campilho, “Optimising a specific tool for electrical terminals crimping process,” Procedia Manufacturing, Vol. 11, pp. 1438–1447, Jan. 2017, https://doi.org/10.1016/j.promfg.2017.07.274
-
“Performance specification for cable-to-terminal electrical crimps,” SAE/USCAR-21, 2022.
-
S. M. Gu, H. S. Choi, and Y. S. Kim, “Effects of design variables on compression rate of wire in connector crimping process of wire harness using FEM,” Transactions of Materials Processing, Vol. 19, No. 5, pp. 305–310, Aug. 2010, https://doi.org/10.5228/kspp.2010.19.5.305
-
L. Zeng and D. Qin, “Improving performance of defect detection by setting skewed tolerance and joint tolerances in crimp force monitor,” Engineering Reports, May 2024, https://doi.org/10.1002/eng2.12912
-
D. Ilca, T. Manescu, and C. Tufisi, “Crimping tool wear and tear analysis,” Studia Universitatis Babeș-Bolyai Engineering, Vol. 68, No. Special Issue, pp. 55–65, Dec. 2023, https://doi.org/10.24193/subbeng.2023.spiss.6
About this article
The authors have not disclosed any funding.
The datasets generated during and/or analyzed during the current study are available from the corresponding author on reasonable request.
The authors declare that they have no conflict of interest.