Abstract
This study delves into the risks associated with 3D-printed hand prostheses lacking mechanical feasibility studies. Such unvalidated prostheses may exhibit various issues like durability shortcomings, anatomical incompatibility, functional safety concerns, manufacturing quality deficiencies, and health risks due to inappropriate materials. These issues can lead to damage or premature failure during use, discomfort, skin irritation, injuries, inability to withstand functional loads, and health hazards from toxic or allergenic substances. Therefore, ensuring the safety, quality, and effectiveness of these prostheses is crucial. The study focuses on a mechanical feasibility study conducted through Finite Element Analysis (FEA) simulations on an open-source hand prosthesis model. It evaluates mechanical properties, stress concentration areas, and displacement on the prosthesis surface. The methodology comprises three key steps: acquiring the virtual model, conducting computational simulations, and selecting the 3D printing material. The simulations assess the prosthesis’s ability to withstand compressive forces and identify stress concentration areas. Results from the study indicate that using PETG as the constituent material demonstrates mechanical viability and satisfactory performance under static force conditions. This finding underscores the importance of rigorous testing and adherence to standards in developing 3D-printed hand prostheses. Such studies contribute significantly to enhancing these devices’ safety and effectiveness, facilitating their broader adoption in healthcare settings. In summary, this study highlights the critical need for mechanical feasibility studies in the development of 3D-printed hand prostheses. It emphasizes the significance of following strict standards and regulations to ensure these devices’ safety, quality, and functionality. By doing so, it paves the way for the widespread use of these prostheses in healthcare, benefiting users and advancing the field of prosthetic technology.
1. Introduction
In recent years, additive manufacturing has emerged as a revolutionary technology in various fields, enabling the efficient production of complex parts quickly and accurately. This advancement holds great promise for the manufacturing of limb prostheses, offering opportunities to create customized, accessible devices with excellent dimensional accuracy. However, despite these advancements, challenges persist in the area of prosthetic development, particularly concerning the evaluation of mechanical feasibility and clinical functionality [1], [2].
The development of open-source hand prostheses, facilitated by platforms like Thingiverse and e-NABLE, signifies a significant step forward in technological evolution. This approach fosters collaboration and innovation among designers, engineers, and users while aiming to democratize access to more effective healthcare solutions tailored to individual needs. The open-source model encourages global contributions to improve prosthetic functionality, comfort, and aesthetics, creating a dynamic and collaborative community [3], [4].
Nevertheless, many open-source hand prostheses lack thorough mechanical feasibility studies and clinical functionality assessments, posing potential risks to users if not developed and tested rigorously. These risks include durability issues, anatomical compatibility concerns, functional safety challenges, and variations in quality and precision [5].
In light of these challenges, this study addresses the critical need to evaluate the mechanical feasibility of open-source hand prostheses manufactured through additive manufacturing. Three-dimensional (3D) printing technology offers diverse materials and manufacturing methods, allowing for the creation of prosthetic models with varied geometries, textures, and strengths. This diversity enables a comprehensive analysis of mechanical properties such as impact resistance, durability, and the ability to withstand functional loads.
Furthermore, the study delves into the role of Finite Element Analysis (FEA) software in simulating and evaluating the structural behavior of prostheses. FEA enables the prediction of a device's performance under different usage conditions, identification of stress concentration areas, optimization of design, and assurance of safety and effectiveness in the final product [6], [7].
The contributions of this study lie in its thorough investigation into the current challenges faced in prosthetic development, the latest advancements in Finite Element Analysis (FEA) for assessing prosthetic devices, and its emphasis on the importance of rigorous testing and adherence to standards in ensuring the safety, quality, and functionality of 3D-printed hand prostheses. These insights pave the way for enhancing prosthetic technology and fostering greater confidence in the widespread adoption of these devices in healthcare settings.
2. Methodology
This study focuses on evaluating the mechanical feasibility of open-source hand prostheses through a comprehensive methodology. The research methodology comprises three distinct steps (Fig. 1).
Fig. 1Methodology workflow chart
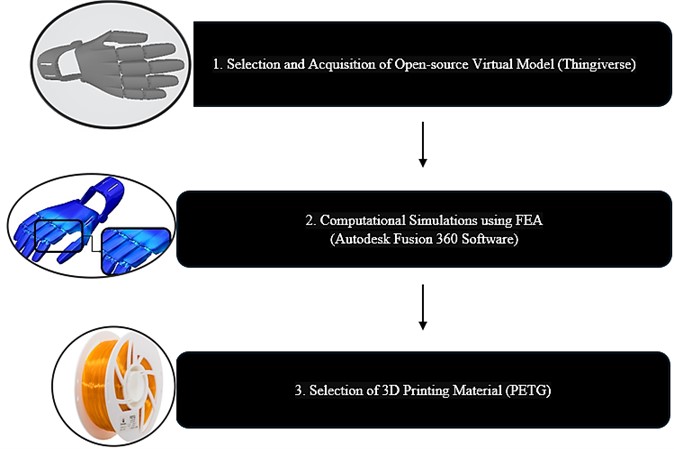
1) Selection and acquisition of virtual model. The first step involved acquiring an open-source virtual model of a mechanical hand prosthetic designed for patients with transcarpal amputations (Fig. 2). The model was obtained in STL file format from the Thingiverse website, a platform known for its repository of free downloadable 3D printing models. This model is specifically designed for patients with wrist flexion capabilities and the absence of all five fingers, operating through mechanical movements facilitated by traction cables [8], [9].
Fig. 2Virtual model of a mechanical hand prosthetic
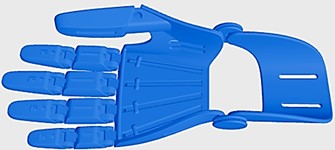
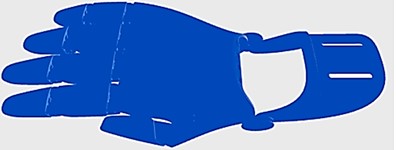
2) Computational Simulations using FEA: The second phase focused on conducting virtual simulations using Autodesk Fusion 360 software, a product of Autodesk Inc. known for its application of the Finite Element Method (FEM). This method allows for a detailed analysis by dividing the model into small geometric elements to simulate real-world conditions. Parameters such as mesh size, element geometry, and boundary conditions were carefully selected to ensure accurate representation and evaluation of the mechanical properties of the prosthesis under static loads. The mesh generation process involved creating a finite element mesh that accurately represents the geometry of the prosthesis. The prosthesis geometry was discretized into tetrahedral elements due to their suitability for complex shapes and compatibility with the analysis software. The number of elements in the mesh was approximately 160,000, ensuring a high-resolution model without compromising computational efficiency. Additionally, boundary conditions were applied at points where the prosthesis interacts with physiological structures to simulate realistic loading conditions. This step also included mesh reduction techniques, where the complexity of the original prosthesis mesh was reduced using point cloud reduction methodologies. This reduction facilitated efficient finite element analysis, optimizing computational resources while maintaining accuracy in the evaluation of mechanical behavior.
3) Selection of 3D Printing Material: In the third phase, the Polyethylene Terephthalate Glycol (PETG) polymer filament was chosen as it is an affordable material for use in 3D printing and has great potential for constructing prosthetic devices. This decision was based on research and references regarding the necessary polymer properties for 3D printing, considering factors such as mechanical strength, flexibility, hardness, elongation, transparency, gloss, and ease of printing. Table 1 shows the values for some properties provided by the supplier for the polymer filament in question. Thus, PETG is used in additive manufacturing with FDM (Fused Deposition Modeling) technology printers due to its compatibility with the printing process and suitability for creating durable and functional prostheses. Furthermore, FDM printing technology is highly significant due to its accessibility, enabling efficient production of complex and functional parts. It provides flexibility in material usage and is widely used in prototyping, customized parts, and even prosthetics, becoming an essential technology in the additive manufacturing industry, [4], [10], [11].
Table 1PETG mechanical properties filament supplier catalog
Mechanical Properties of PETG | Test method | Value |
Tensile strength at break | D638 | 28 MPa |
Elongation at break | D638 | 130 % |
Flexural modulus | D790 | 2160 MPa |
Hardness | D785 | 106 HR |
3. Results and discussion
The mechanical functionality of the prosthesis was assessed through static force simulation using Finite Element Analysis (FEA). For the simulation, the reaction forces at the fingertips of the prosthesis, manufactured using AM in PETG, were considered in a scenario of compressing a solid object. The average reaction forces based on previous studies, representing an effort of 7 N on the fingers, were considered [8].
Additionally, mesh reduction was necessary, i.e., simplifying the complexity of the original prosthesis’ triangular mesh using point cloud reduction methodologies to enable mesh formation work through finite element study. The model was reduced by 60.13 %, from an original total of 160,136 faces to approximately 96,000 faces.
Fig. 3Static load analysis applied to prosthesis
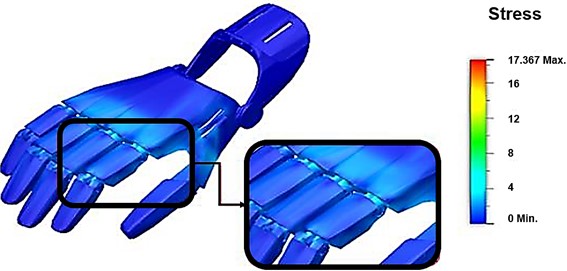
Fig. 4Surface deformation in response to the application of static loads on the prosthesis
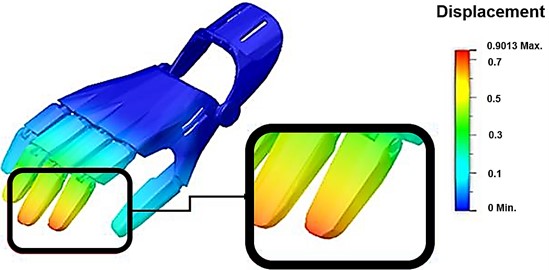
The static force analysis (Fig. 3) revealed that the prosthesis manufactured with PETG material has adequate mechanical feasibility to withstand the compression of solid objects under a force of 7 N, without presenting surface ruptures or plastic deformations. The force application resulted in a maximum reaction of 17.367 MPa, concentrated in the most stressed area defined as the connection between the palm of the prosthesis and the fingers.
Additionally, the maximum displacement observed was 0.9013 mm (Fig. 4), mainly at the tips of the index and middle fingers of the prosthesis.
4. Conclusions
From the proposed analyses and the conducted study on the mechanical feasibility of the open-source prosthesis, several important conclusions can be drawn. Firstly, evaluating the mechanical functionality of the prosthesis through static force simulations using FEA and considering the reaction forces at the fingertips revealed that the prosthesis, manufactured with PETG as the constituent material, demonstrates mechanical feasibility by withstanding the compression of solid objects with a force of 7 N. It was observed that the prosthesis surface did not exhibit plastic deformations or ruptures during the tests, indicating its ability to withstand these load conditions.
Analyzing the maximum reaction on the prosthesis, which was 17.367 MPa concentrated in the connection structure between the palm region of the prosthesis and the phalanges and observing the displacement of 0.9013 mm at the tips of the index and middle fingers of the device, it can be concluded that the device performed well under the employed analysis conditions. These results suggest that the prosthesis has satisfactory mechanical strength for its intended purpose.
Therefore, considering the conducted simulations and the results obtained, the PHP Hand Prosthesis has proven to be a viable and promising solution, demonstrating its ability to provide adequate mechanical support for its functionalities. This is crucial for its effective and safe application in real-world contexts by its users. Under the analyzed conditions, the prosthesis shows mechanical feasibility for recommendations and execution of everyday trivial activities. For future analyses, a complementary study can be developed with the purpose of conducting the study to evaluate mechanical feasibility for dynamically applied loads on the device.
References
-
J. Edgar and S. Tint, “Additive manufacturing technologies: 3D printing, rapid prototyping, and direct digital manufacturing,” Johnson Matthey Technology Review, Vol. 59, No. 3, pp. 193–198, Jul. 2015, https://doi.org/10.1595/205651315x688406
-
H. Fashandi, Y. Liao, and S. H. Hajiagha, “Current trends and challenges in additive manufacturing of personalized prosthetic devices,” International Journal of Advanced Manufacturing Technology, Vol. 128, No. 1-4, pp. 639–653, 2022.
-
J. Moore and M. Gardan, “Exploring open source 3D printed prosthetic hand designs: a research review,” International Journal of Advanced Manufacturing Technology, Vol. 107, No. 1-4, pp. 223–237, 2020.
-
R. C. D. Silveira Romero, A. A. Machado, K. A. Costa, P. H. R. G. Reis, P. Paiva Brito, and C. B. Santos Vimieiro, “Development of a passive prosthetic hand that restores finger movements made by additive manufacturing,” Applied Sciences, Vol. 10, No. 12, p. 4148, Jun. 2020, https://doi.org/10.3390/app10124148
-
R. Morrison and B. Mcadam, “The development of open-source upper-limb prosthetic devices: a critical review,” Journal of Rehabilitation Robotics, Vol. 45, No. 5, pp. 464–474, 2021.
-
M. S. Rahman, “An assessment of the mechanical and functional performance of open-source 3d-printed prosthetic hands,” Journal of Rehabilitation Robotics, Vol. 10, No. 2, pp. 112–123, 2022.
-
K. M. Lee and J. Kim, “Risk assessment of open-source 3D-printed upper-limb prostheses: a case study,” Medical Devices: Evidence and Research, Vol. 14, pp. 127–135, 2021.
-
E. R. Serina, E. Mockensturm, C. D. Mote, and D. Rempel, “A structural model of the forced compression of the fingertip pulp,” Journal of Biomechanics, Vol. 31, No. 7, pp. 639–646, Jul. 1998, https://doi.org/10.1016/s0021-9290(98)00067-0
-
“Partial Hand Prosthesis.” Thingverse, 2017, https://www.thingiverse.com/thing:2565845.
-
M. Kopar and A. R. Yildiz, “Experimental investigation of mechanical properties of PLA, ABS, and PETG 3-d printing materials using fused deposition modeling technique,” Materials Testing, Vol. 65, No. 12, pp. 1795–1804, Dec. 2023, https://doi.org/10.1515/mt-2023-0202
-
“3Dfila,” https://3dfila.com.br/
About this article
The authors would like to express their gratitude to the Federal University of Minas Gerais (UFMG), especially the Laboratory of Bioengineering (Labbio), the Financier of Studies and Projects (FINEP), and the Coordination for the Improvement of Higher Education Personnel (CAPES) for the support that made this work possible to be carried out.
The datasets generated during and/or analyzed during the current study are available from the corresponding author on reasonable request.
Rodrigo Romero: conceptualization, data curation, methodology, project administration, software, visualization, writing-original draft preparation. Kliftom Costa: methodology, software, visualization. Claysson Vimieiro: conceptualization, data curation, funding acquisition, methodology, project administration, supervision, visualization, writing-review and editing.
The authors declare that they have no conflict of interest.
Not applicable.