Abstract
As a promising renewable resource, waste tire rubber powder has been utilized to enhance asphalt performance but it has compatibility concerns with matrix asphalt. To solve the phase separation between crumb tire rubber (CTR) and asphalt, waste cooking oil (WCO) has been successfully employed as the solvent to desulfurize crumb rubber. However, about 30 % of carbon black is wrapped in crumb rubber, which has a high recycling value. The cross-linking network structure of the crumb rubber can be loosened by waste cooking oil, and the carbon black will gradually peel off. This study desulfurizes crumb rubber with waste cooking oil at 180 ℃, and the carbon black produced by the evolution of rubber structure was separated by Soxhlet extraction. The rubber-cracked carbon black (RCCB) and the industrial carbon black N330 were added to asphalt, and the impact of the two different carbon black on the anti-deformation of asphalt was analyzed by dynamic shear rheometer (DSR). The results indicated that at the same dosage of 5 %, the carbon black separated from rubber will weaken the deformation resistance of asphalt at high temperatures, rather than improving it like N330 produced in the industry.
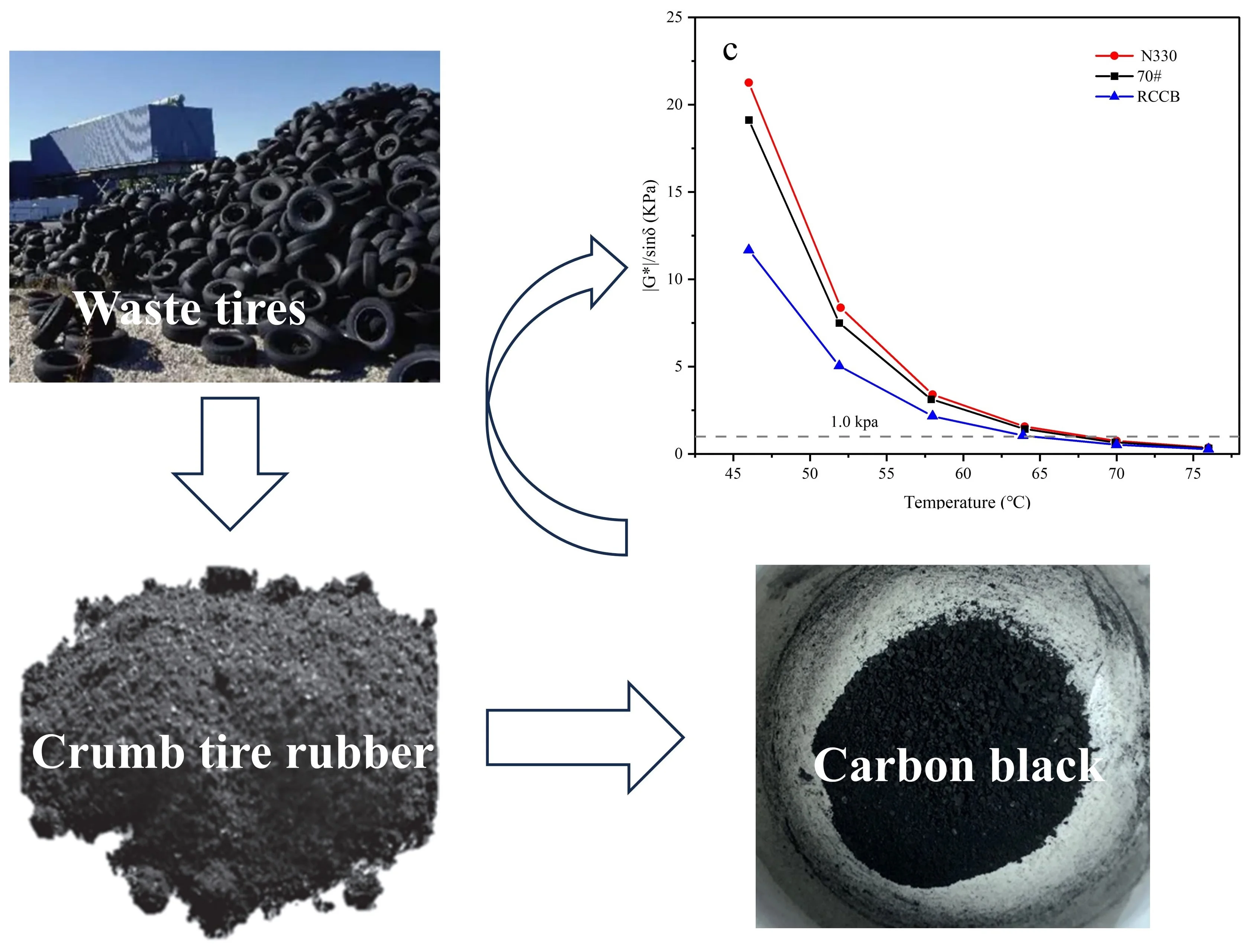
Highlights
- Mix and pyrolysis of crumb tire rubber and waste cooking oil at 180℃
- Extract carbon black from the mixture of rubber and oil
- Use rubber-cracked carbon black as an asphalt modifier
1. Introduction
Waste tires are recognized as industrial hazardous solid waste, but effectively treated waste tire rubber can become a valuable source of secondary raw materials for the circular economy [1]. According to practical research, crumb tire rubber (CTR) as an additive can improve the mechanical properties of asphalt pavement, leading to high performance in terms of resistance to rutting, cracking, and water damage [2]. However, the complex composition, structure, and chemical properties of CTR affect the processing and application of rubber-modified asphalt.
Lots of methods have been put forward to enhance the compatibility of rubber-asphalt systems, including improved production processes, adding additives, pre-devulcanization and degradation, etc. Among them, pre-devulcanization mainly includes microwave radiation, plasticization and mechanical extrusion palletization [3]. However, these methods result in environmental pollution because of the direct emission of polluting gases containing substances such as hydrogen sulfide during the devulcanization process. To solve the issue of gas emissions, the popular method namely Terminal Blend (TB) adopts high-temperature neat asphalt as a solvent to desulfurize crumb tire rubber, but it leads to asphalt aging as well as problems with fuel consumption safety [4]. Therefore, scholars have attempted to pre-desulfurize CTR by using vegetable oil, waste edible oil, furfural oil, waste engine oil, etc. [2-6].
Oil stretches the cross-linking network of vulcanized rubber, weakens the intermolecular force of rubber, and reduces the entanglement of CTR chains so that carbon black covered with bound rubber can be separated [5]. Carbon black is the most commonly applied reinforcing filler in rubber manufacture, it accounts for about 30 % of the CTR. The particle size, structure, and surface properties of carbon black will be directly impacted by different production or recycling processes. Relevant studies showed that carbon black has a good affinity with asphalt, adding it to asphalt can reduce temperature sensitivity and improve the rutting resistance performance [7]. The carbon black separated from the degradation of CTR in waste cooking oil (WCO) is different from the carbon black produced from the thermal decomposition of coal or heavy oil in industry. Few studies have explored the characteristics of carbon black recovered from waste oil desulfurizing rubber and its affinity with asphalt. This work desulfurizes CTR with waste cooking oil (WCO) at 180 ℃, and separates the carbon black by Soxhlet extraction. The separated carbon black compared with the industrial carbon black N330 was added to asphalt, dynamic shear rheometer (DSR) was used to analyze the impact of these two different carbon black on the anti-deformation performance at high temperature of asphalt.
2. Materials and test methods
2.1. Materials
2.1.1. Asphalt, CTR, WCO and Carbon Black N330
The A-70 asphalt selected in this research was produced by Maoming Donghai Asphalt Co., LTD (Maoming, China). The basic properties of asphalt were presented in Table 1. The crumb tire rubber (CTR) was 40-mesh, and its component is presented in Table 2. The fundamental characteristics and major contents of WCO are listed in Table 3. In this study, N330 was produced by Hejin Jinlong Technical Co., LTD (Hejin, China), and the characteristics of the carbon black N330 was shown in Table 4.
Table 1Basic properties of asphalt
Properties | Unit | Value |
Softening point (ring and ball method) | ℃ | 71 |
Penetration (25 ℃, 100 g, 5 s) | 0.1 mm | 48 |
Ductility (15 ℃, 5 cm/min) | cm | > 100 |
Dynamic viscosity (60 ℃) | Pa·s | 223 |
Flash point | ℃ | > 300 |
Wax content | % | 1.9 |
Density (15 ℃) | g/cm3 | 1.031 |
Table 2Component of CTR
Operating oil (wt.%) | Rubber hydrocarbon (wt.%) | Carbon black (wt.%) | Mineral filler (wt.%) |
4.53 | 56.2 | 30.49 | 8.78 |
Table 3Main contents of WCO
Flash point (℃) | Saturated fatty acid (wt.%) | Unsaturated fatty acid (wt.%) |
304 | 17.54 | 82.46 |
Table 4Basic properties of carbon black N330
Properties | Unit | Value |
Iodine absorption | g/kg | 82 |
DPB absorption | cm3/100g | 100.8 |
Heating loss | % | 0.75 |
Ash content | % | 0.35 |
2.1.2. Separate carbon black from CTR
Based on the research of Song [5], Zhao [3], etc., who used oil phase medium to crack rubber at a low temperature of 140-260 °C, the mass ratio of CTR and waste cooking oil was selected as 1:1. CTR and waste cooking oil contained in steel cups were pyrolyzed at 180 °C for 2 h using a double-layer spiral fan-blade mixer with a mixing speed of 250-300 rpm, and timing was started when the temperature was stabilized at 180±10 °C. Finally, a mixture of CTR and waste cooking oil named waste rubber/oil (WRO) was obtained [3].
The waste rubber/oil (WRO) was wrapped in filter paper and extracted with toluene in a Soxhlet extractor for 48 h to remove low molecular weight solutes and other additives, and the residue was dried in a vacuum oven at 70 °C for 4 h to a constant weight. Finally, the dried residue was ground into powder using a mortar and pestle to obtain rubber-cracked carbon black (RCCB).
2.1.3. Preparation of CB Modified Asphalt
Weighing 150 g of matrix asphalt in a steel cup with an inner diameter of 9 cm, the matrix asphalt was heated to 135 °C. RCCB and industrial carbon black N330 were added at 5 % of the asphalt respectively. The carbon black modified asphalt mixtures were stirred using a three-bladed mixer with a fan blade diameter of 3cm at 300-400 rpm for 1h after the temperature had reached 180±10 ℃. To investigate the state of carbon black in WRO, modified asphalt externally blended with 5 % WRO was prepared by the same process.
2.2. Test methods
2.2.1. Basic properties
Due to the limited amount of RCCB-modified asphalt, the softening point using less asphalt content was selected to characterize the basic properties.
2.2.2. Rheological properties
The rheological properties of asphalt binder can be estimated by the dynamic shear rheological test (DSR). According to AASHTO M320, the complex modulus (G*) and phase angle (δ) of the asphalt were determined by dynamic shear oscillatory test performed on TA dynamic shear rheometer AR 1500 ex. In this paper, the temperature scanning test of asphalt was performed under the controlled strain of 12 % mode. The scanning temperature ranged from 46-76 °C in increments of 6 °C/min, and the scanning frequency was 10 rad/s. The plate employed was 25 mm in diameter, and the gap between parallel plates was 1 mm.
2.2.3. Multiple stress creep recovery (MSCR) test
The MSCR test can be employed to investigate the rutting resistance of asphalt and was performed at 64 ℃ on matrix asphalt, RCCB and industrial carbon black N330 modified asphalt according to the AASHTO TP-70. The stress levels of the experiments were 0.1 kPa and 3.2 kPa, respectively. MSCR cycle consisted of constant 1s creep and 9 s recovery period, and the test was repeated 10 times for 100 s at each stress level, 20 creep and recovery cycles were performed at creeping stress of 0.1 kPa while 10 creep and recovery cycles were performed at creeping stress of 3.2 kPa, lasting for a total time of 300 s. The data were analyzed from cycles 11 to 20 at 0.1 kPa and from cycles 21 to 30 at 3.2 kPa. The cumulative strain curves at the two strain levels and the non-recoverable creep compliance measured at 3.2 kPa (Jnr3.2) were applied to evaluate the durability of asphalt to permanent deformation under repeated loading conditions [9].
3. Results and discussion
3.1. Softening point
The softening point of WRO, RCCB and industrial carbon black N330 modified asphalt were tested and the results are shown in Fig. 1.
Fig. 1Softening point of asphalt
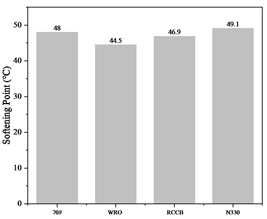
Fig. 1 shows that the addition of WRO and RCCB reduced the softening point of asphalt, while industrial carbon black N330 increased it. At a dosage of only 5 %, there was a significant difference in the influence of the two types of carbon black on the softening point of asphalt. The decrease in the softening point of asphalt by WRO indicates that some components in WRO will dilute and soften asphalt. RCCB is a component isolated from WRO, and although it has an appearance similar to N330, its purity can be affected by the extraction process. According to some research, the addition of carbon black particles can increase the viscosity of asphalt, reduce its flexibility, and may have an adsorption effect on some light components in asphalt [10]. Industrial Carbon Black N330 is produced from the pyrolysis of crude oil and natural gas, while RCCB is recycled from WRO and it may be wrapped with a layer of organic shell [11]. Therefore, the purity of RCCB may be lower than industrial carbon black N330, and encapsulated by impurities may prevent the carbon black particles from absorbing light components. These factors may result in the different performances in the softening point of asphalt.
3.2. Anti-deformation performance at high temperature
3.2.1. Analysis of rheological properties
The complex shear modulus (G*) can represent the deformation resistance of asphalt under repeated pulse shear stress to some extent. As shown in Fig. 2(a), the complex shear modulus of the two types of carbon black modified asphalt decreases with increasing temperature. The complex shear modulus of matrix asphalt was improved by adding 5 % carbon black N330, while the RCCB reduced it.
Phase angle (δ) is related to the proportion of viscous components to elastic components in asphalt, the larger value indicates a larger proportion of viscous components in asphalt, which means more prone to plastic deformation under external forces. It can be seen from Fig. 2(b), that as temperature increases, the phase angle becomes larger indicating that the proportion of viscosity in asphalt increases and the deformation-recovering ability decreases. Besides, it is interesting that at the initial temperature of 46 ℃, the phase angle of RCCB-modified asphalt is greater than that of N330 and 70# asphalt. At 52 ℃, the three asphalts are very close, and RCCB-modified asphalt is still the largest among them. But after 58 ℃, the order becomes N330>70#>RCCB, which indicates that during the 46-52 ℃, the relative proportion of viscous components that are prone to plastic deformation in RCCB-modified asphalt is relatively small. However, when the temperature further increases to above 58℃, the viscous components of RCCB-modified asphalt increase and its growth rate is faster than N330 and matrix asphalt, resulting in the phase angle of RCCB-modified asphalt being the smallest among them.
The rutting factor (G*/sinδ) can be applied to evaluate the deformation resistance of asphalt. Fig. 2(c) shows the rutting factor of all types of asphalt decreases with increasing temperature. The rutting factor of carbon black N330 modified asphalt is greater than that of matrix asphalt, while the rutting factor of RCCB-modified asphalt is the smallest. The rutting factor of RCCB-modified asphalt is lower than 1.0 kPa after 64 ℃, while carbon black N330 modified asphalt and matrix asphalt are about 68 ℃. These data indicate that N330 improves the deformation resistance of asphalt at high temperatures, while RCCB deteriorates its deformation resistance. The organic shell insoluble in toluene in RCCB may soften the asphalt system with increasing temperature, thereby reducing the deformation resistance of the asphalt.
Fig. 2Results of performance grading test: a) complex shear modulus, b) phase angle, c) rutting factor
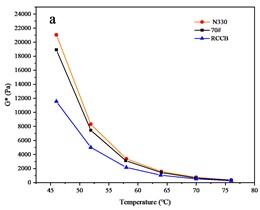
a)
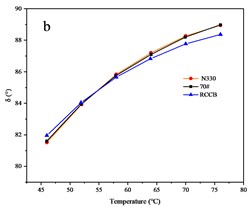
b)
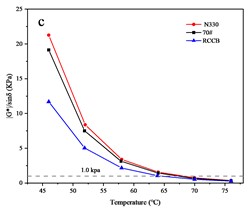
c)
3.2.2. Analysis of the MSCR Test
Fig. 3(a), (b) displays the cumulative strain curves of asphalt at the stress level of 0.1 and 3.2 kPa at 64 ℃. At the 0.1 kPa stress level, the cumulative strain of RCCB-modified asphalt is higher than matrix asphalt, indicating that the creep deformation of RCCB-modified asphalt is relatively large. When the stress level cone to 3.2 kPa, the cumulative strain of the three asphalt significantly increases, and the cumulative strain curve of RCCB modified asphalt becomes close but slightly higher than matrix asphalt, indicating that under heavy traffic load, the elastic recovery performance of RCCB modified asphalt is similar with matrix asphalt. However, the cumulative strain of N330 is the lowest at both stress levels, indicating that N330 improves the high-temperature deformation resistance of matrix asphalt. The asphalt with lower Jnr3.2 values is more resistant to deformation. According to Fig. 3(c), N330 modified asphalt has the best resistance to deformation and RCCB has the worst, which is consistent with the results of the rutting factor.
Fig. 3Results of MSCR test: a) 0.1 kPa stress level; b) 3.2 kPa stress level; c) Jnr3.2
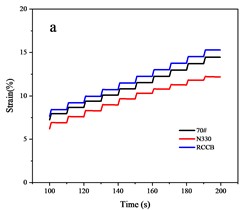
a)
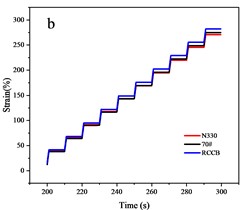
b)
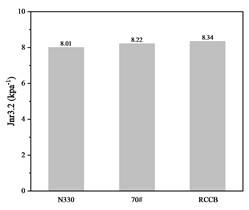
c)
4. Conclusions
The softening point of industrial carbon black N330 and RCCB modified asphalt was examined. The rheological properties and MSCR test were conducted using DSR to determine the deformation resistance of N330 and RCCB modified asphalt at high temperature.
1) The addition of industrial carbon black N330 increased the softening point of the base asphalt, while rubber extract carbon black reduced it, indicating that carbon black obtained through different production methods has varying effects on the softening point of asphalt.
2) The rutting factor, cumulative strain, and Jnr3.2 collectively demonstrate that the addition of N330 enhances the anti-deformation performance of asphalt at high temperature, while RCCB reduces the high-temperature resistance to deformation of asphalt.
3) Taking into account the diminishing effect of WRO on the softening point of asphalt and the studies carried out by other researchers on the composition of RCCB, it is highly probable that the softening of asphalt induced by RCCB is associated with its specific composition and purity.
References
-
X. Wu, S. Wang, and R. Dong, “Lightly pyrolyzed tire rubber used as potential asphalt alternative,” Construction and Building Materials, Vol. 112, pp. 623–628, Jun. 2016, https://doi.org/10.1016/j.conbuildmat.2016.02.208
-
R. Dong and M. Zhao, “Research on the pyrolysis process of crumb tire rubber in waste cooking oil,” Renewable Energy, Vol. 125, pp. 557–567, Sep. 2018, https://doi.org/10.1016/j.renene.2018.02.133
-
R. Dong, M. Zhao, and N. Tang, “Characterization of crumb tire rubber lightly pyrolyzed in waste cooking oil and the properties of its modified bitumen,” Construction and Building Materials, Vol. 195, pp. 10–18, Jan. 2019, https://doi.org/10.1016/j.conbuildmat.2018.11.044
-
R. Dong, M. Zhao, W. Xia, X. Yi, P. Dai, and N. Tang, “Chemical and microscopic investigation of co-pyrolysis of crumb tire rubber with waste cooking oil at mild temperature,” Waste Management, Vol. 79, pp. 516–525, Sep. 2018, https://doi.org/10.1016/j.wasman.2018.08.024
-
P. Song, C. Wan, Y. Xie, K. Formela, and S. Wang, “Vegetable derived-oil facilitating carbon black migration from waste tire rubbers and its reinforcement effect,” Waste Management, Vol. 78, pp. 238–248, Aug. 2018, https://doi.org/10.1016/j.wasman.2018.05.054
-
A. Aljarmouzi and R. Dong, “Sustainable asphalt rejuvenation by using waste tire rubber mixed with waste oils,” Sustainability, Vol. 14, No. 14, p. 8246, Jul. 2022, https://doi.org/10.3390/su14148246
-
F. Wang et al., “Microwave heating mechanism and Self-healing performance of scrap tire pyrolysis carbon black modified bitumen,” Construction and Building Materials, Vol. 341, p. 127873, Jul. 2022, https://doi.org/10.1016/j.conbuildmat.2022.127873
-
L. A. Wilke, C. G. Robertson, D. A. Karsten, and N. J. Hardman, “Detailed understanding of the carbon black-polymer interface in filled rubber composites,” Carbon, Vol. 201, pp. 520–528, Jan. 2023, https://doi.org/10.1016/j.carbon.2022.09.032
-
K. Zhong, Z. Li, J. Fan, G. Xu, and X. Huang, “Effect of carbon black on rutting and fatigue performance of asphalt,” Materials, Vol. 14, No. 9, p. 2383, May 2021, https://doi.org/10.3390/ma14092383
-
P. Cong, P. Xu, and S. Chen, “Effects of carbon black on the anti aging, rheological and conductive properties of SBS/asphalt/carbon black composites,” Construction and Building Materials, Vol. 52, pp. 306–313, Feb. 2014, https://doi.org/10.1016/j.conbuildmat.2013.11.061
-
S. Li, C. Wan, X. Wu, and S. Wang, “Core-shell structured carbon nanoparticles derived from light pyrolysis of waste tires,” Polymer Degradation and Stability, Vol. 129, pp. 192–198, Jul. 2016, https://doi.org/10.1016/j.polymdegradstab.2016.04.013
About this article
The authors have not disclosed any funding.
The datasets generated during and/or analyzed during the current study are available from the corresponding author on reasonable request.
The authors declare that they have no conflict of interest.