Abstract
In this paper, red mud and slag were used as the main cementitious materials, and desulfurization gypsum and exciter materials were mixed to prepare red mud-based cementitious materials with excellent performance. The mechanical properties of red mud-based cementitious material stabilized gravel material were investigated by carrying out the compaction test, unconfined compressive strength test, splitting strength test and fatigue performance test. The test results show that with the increase in the dose of cementitious material, the hydration is more significant, generating more hydrated calcium silicate (C-S-H) gel, which in turn makes the unconfined compressive strength and splitting strength increase to a certain extent. Adding exciter and desulfurization gypsum in the appropriate amount is conducive to improving the hydration of red mud, improving the structural compactness, and improving the mechanical properties, volumetric stability and seepage resistance of the cementitious material.
1. Introduction
With the rapid development of China's highway, the demand for raw materials for road construction is also increasing, and the mining of gravel and the production of cement have caused serious ecological damage and environmental pollution. At present, the semi-rigid (sub) base material of asphalt pavement in China is mainly cement-stabilized gravel, and the road bed improvement is mostly hydraulic soil or lime soil. The production of lime and cement produces a large amount of carbon dioxide, which causes serious air pollution and jeopardizes human health. At present, in order to protect the environment, stone factories and sand factories in many areas have all been closed, which causes a shortage of materials needed for road construction, and the quality of raw materials is difficult to guarantee, which creates a greater quality risk to the project. Therefore, in order to protect the quality of the project and reduce the cost of the project, the use of industrial solid waste materials with gelling activity to prepare roadbed gelling materials has become a hotspot in the current research of roadbed materials [1].
Among the many industrial solid waste materials, red mud, slag and other industrial solid wastes have a large historical stockpile and a large new increase, which has caused great pressure on the environment and the task of utilization is very arduous [2-3]. China is the world's largest aluminum refining country, the annual production of alumina emissions close to 150 million tons, but the comprehensive utilization rate is only 4 %, piles of red mud caused by environmental pollution is becoming more and more serious [4]. China in the “Eleventh Five-Year Plan”, “Twelfth Five-Year Plan” and “Thirteenth Five-Year Plan” related development plans are very clearly put forward the comprehensive management of red mud, to encourage large-scale, high-quality development of red mud comprehensive utilization [5]. Based on this, many researchers at home and abroad have done a lot of research work on red mud disposal and comprehensive utilization [6-9]. Chang [10] used a direct reduction roasting and magnetic separation process to recover iron from red mud, and ultimately obtained iron concentrates with grades and recoveries of 81.75 % and 85.96 %, respectively. Zhu and Xia [11] used the special physicochemical properties of red mud waste as SO2 absorbent for wet desulfurization. Due to its high specific surface area, anti-sintering ability and low price, red mud can also be used as a catalyst and catalyst carrier in a variety of non-homogeneous catalytic reaction systems [12]. In the application of road materials, as early as 1996, Liang and Zhang [13] analyzed and investigated the road performance of cemented red mud concrete through indoor tests in terms of mechanical strength, stiffness, permeability and frost resistance. Zhang and Gao [14] prepared high dosage red mud-based roadbed filling materials by Bayer red mud, high water absorption resin and sulfoaluminate cement, and the results showed that the red mud-based filling materials meet the needs of roadbed filling projects. In order to solve the problems of low cohesion and poor water stability of powdered soil in the Yellow River alluvial plain area.
In this paper, red mud as the main material, and slag and other solid waste grinding and mixing to prepare red mud-based cementitious materials, so that it has good physical and mechanical properties and cementitious properties. Based on this, further research on the application of semi-rigid grass-roots level conditions, through the compaction test, unconfined compression, splitting and fatigue test conditions to analyze the changing law of road performance of different red mud-based cementitious materials dosage. Scanning electron microscope (SEM) was used to observe the microscopic morphology of hydrated cementitious materials, and analyze and explore the mechanism of hydrated cementitious materials. If it is applied to the pavement grass-roots level, it can not only consume a large amount of red mud and other solid waste materials, but also reduce the demand for cement, lime and other raw materials for engineering construction, reduce the cost of the project, and it can provide a reference for the evaluation of the performance of the red mud-based materials in the road and the application of the promotion and reference significance.
2. Experimental
2.1. Raw materials
The main constituent materials of red mud-based cementitious materials used in this test are Bayer red mud, slag micro powder, desulfurization gypsum, and the chemical composition is shown in Table 1. The red mud is Bayer red mud, which is taken from Shandong WeiqiaoChuangye Group Co. Its pH value is 11.74, specific surface area is 443.6 m2/kg, density is 2.86 g/cm3, Al2O3, Fe2O3, SiO2, Na2O are the main components of red mud. The slag is S95 blast furnace slag micro powder, taken from Shandong Luxin Building Materials Co., Ltd, with a specific surface area of 410.3 m2 /kg, density of 2.84 g/cm3, and the main components of Al2O3, SiO2 and CaO. Desulfurization gypsum is taken from Shandong WeiqiaoChuangye Group Co., Ltd, and the main component of CaSO4-H2O. The excitant is sodium silicate, purchased from Sinopharm Chemical Reagent Co. Ltd, the main component is Na2SO4-9H2O, modulus 1.03. All raw materials according to the red mud: slag: gypsum: sodium silicate = 50:43:6:1 preparation of red mud-based cementitious materials, cementitious materials of the physical properties of the indicators shown in Table 2, can be found that the red mud-based cementitious materials have a good performance, and its cementitious strength indicators higher than the ordinary silicate 32.5 cement. The aggregate used in the test is limestone, which is divided into four grades of 20-30 mm, 10-20 mm, 5-10 mm and 0-5 mm according to the particle size, and the sieving results of the aggregate meet the requirements of the specification, and the physical indexes of each grade of aggregate are shown in Table 3.
Table 1Chemical composition of main materials (%)
Makings | SiO2(%) | Al2O3(%) | Fe2O3(%) | CaO (%) | MgO (%) | SO3(%) | Na2O (%) |
Red mud | 16.42 | 25.20 | 40.2 | 2.02 | 0.17 | 0.28 | 7.81 |
Slag | 24.81 | 14.36 | 0.72 | 43.86 | 7.71 | 2.25 | 0.37 |
Gypsum | 1.01 | 0.39 | 0.11 | 35.13 | 0.01 | 43.01 | 1.03 |
Table 2Physical property parameters of cementitious materials
Experimental | Density (g/cm3) | Stability (mm) | Freezing time (h) | Compressive strength (MPa) | Flexural strength (MPa) | |||
condensation | congeal | 3 d | 28 d | 3 d | 28 d | |||
Results | 2.6-3.2 | <5 | >3 | 6-10 | >15 | >33.5 | >3 | >5.5 |
Table 3Physical parameters of aggregate
Experimental | Density (g/cm3) | Absorbency (%) | Crushing value (%) | Needle-flake (%) | Weak grain (%) | < 0.075 mm granularity (%) |
20-30 mm | 2.739 | 0.47 | / | 2.2 | 0.0 | 0.1 |
10-20 mm | 2.734 | 0.76 | 20.1 | 6.1 | 0.0 | 0.1 |
5-10 mm | 2.726 | 1.16 | / | 9.8 | 0.0 | 0.3 |
0-5 mm | 2.695 | / | / | / | / | 8.7 |
2.2. Mixing ratio design
According to the sieving results of the four grades of aggregates, the skeleton dense cement stabilized gravel material was prepared. The external mixing method is used to add cementitious materials with mass fractions of 4 %, 5 %, 6 %, 7 % and 8 %, respectively, and the compaction test is carried out according to the C method in the Test Procedure for Stabilized Materials of Inorganic Binding Materials for Highway Engineering (JTG E51-2009), to obtain the maximum dry density and the best water content.
2.3. Test protocol
The preparation of specimens and the determination of mechanical properties were carried out according to the Test Procedure for Stabilized Materials of Inorganic Binding Materials for Highway Engineering (JTG E51-2009). Firstly, the homogeneous mixture was prepared by hydrostatic molding method to prepare the specimens of corresponding sizes, and then the specimens were sealed in plastic bags and put into the standard curing room for curing, and finally the specimens were put into the water to soak for 24 h for the test of the mechanical properties one day before reaching the specified age. Scanning electron microscope (SEM) was used to analyze the micro-mechanisms of the cementitious materials tested at different ages.
3. Results and discussion
3.1. Analysis of compaction test results
The optimum moisture content and maximum dry density of stabilized gravel with cementitious material can be obtained from the compaction test, and the results of the optimum moisture content and maximum dry density of stabilized gravel with the dosage of red mud-based cementitious material are shown in Table 4. It can be seen that the optimum moisture content and maximum dry density of stabilized gravel material increase gradually with the increase of the dosage of red mud-based cementitious material. In the range of cementitious material dosage, the optimum moisture content is between 4.5 % and 5.4 %, and the maximum dry density is between 2.403 g/cm3 and 2.448 g/cm3.
Table 4Compaction test results of different types of cementitious materials
Doping (%) | Optimum water content (%) | Maximum dry density (g/cm3) | Compaction (%) |
4 | 4.5 | 2.403 | 98 |
5 | 4.6 | 2.412 | 98 |
6 | 4.8 | 2.423 | 98 |
7 | 5.1 | 2.439 | 98 |
8 | 5.4 | 2.448 | 98 |
3.2. Compressive strength test
The 7-day unconfined compressive strength test was carried out on different types of cementitious materials stabilized gravel materials. The specimen size is a cylindrical specimen of φ150 mm×150 mm, and the results of unconfined compressive strength are shown in Fig. 1. The results in Fig. 1. show that the representative value of 7-day unconfined compressive strength increases with the increase of cementitious material dosage, and the representative value of the strength of the specimen when the dosage of cementitious material is 5 % meets the strength requirement of the base layer of the highway, and the representative value of the strength of the specimen when the dosage is 4 % meets the strength requirement of the subbase layer. In addition, the strength of the specimen gradually tends to a certain value with the increase of age. The strength value of stabilized gravel material mainly depends on the following three aspects: one is the skeleton embedding effect between coarse aggregates, the second is the filling effect of fine aggregates, and the third is from the bonding effect between cement and aggregates. Under the same condition of grading, the increase of binder dosage highlights the bonding effect between binder and aggregate, which further increases the 7-day unconfined compressive strength value of specimen.
Fig. 1Variation of compressive strength with a) cementitious material dosage and b) different ages
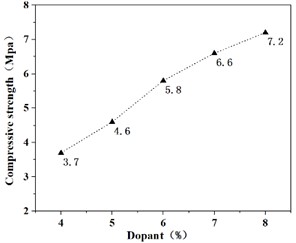
a)
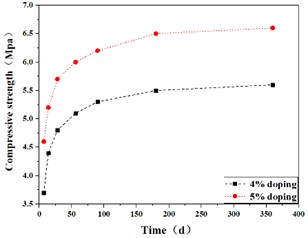
b)
3.3. Splitting strength test
The split strength test is used to evaluate the strength of the semi-rigid base layer material and reflect the tensile property of the material through the size of its split strength. Cylindrical specimens of φ150 mm×150 mm was prepared for the splitting test with different dosages. Fig. 2. shows the splitting strength results of stabilized aggregates under different maintenance age conditions. It can be seen that as the dosage of cementitious material increases, the corresponding indirect splitting strength shows a gradual increase. This is attributed to the fact that as the dosage of cementitious material increases, the hydration is more significant, generating more hydrated calcium silicate (C-S-H) gels, which in turn leads to an increase in the splitting strength.
3.4. Fatigue performance test
According to the specification using hydrostatic pressure method to form the specimen of 100 mm×100 mm×400 mm center beam, using the method of three-point loading of different dosage and type of cementitious material stabilized gravel mixture for 28 d bending and tensile strength test, the test results are shown in Fig. 3. As shown in Fig. 3, under the condition of the same age, the fatigue life of stabilized gravel material increases with the increase of the dosage of red mud-based cementitious material, and the fatigue life of the mixture is improved by about 30 %-40 % for every 1 % increase of cementitious material dosage. A large amount of AFt in the system can play the role of fiber reinforcement in the system, bear part of the tensile stress in the stress process, reduce the cracking phenomenon of stabilized gravel material, thus improving the splitting strength and resistance to bending and tensile deformation of the mixture.
Fig. 2Relationship between splitting strength and cementitious material type and content
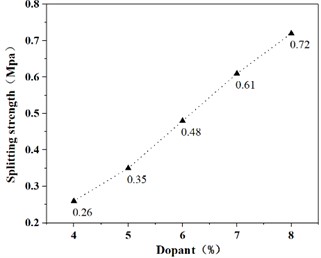
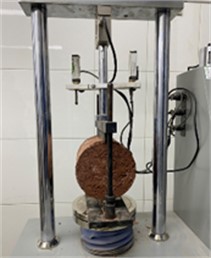
Fig. 3Fatigue life at different stress ratios for different red mud dosages
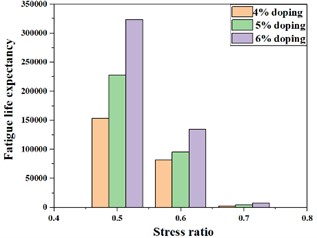
3.5. Microanalysis
SEM was used to analyze the microscopic morphology and physical phase composition of the hydration products of the red mud-based cementitious materials, and Fig. 4 shows the SEM photographs of the specimens at different ages, respectively.
Fig. 4SEM of samples of a) 7 d and b) 28 d
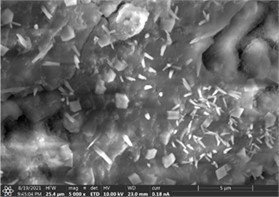
a)
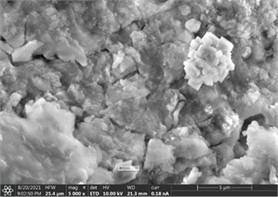
b)
As can be seen from Fig. 4, the surface of the specimen hydrated for 7 days has hexagonal plates of calcium hydroxide and needle-and-rod AFt, while more unreacted materials are embedded in the slurry, with more obvious pits on the surface and loose structure. With the prolongation of hydration age, the hydration degree increased, a large amount of gypsum was consumed to generate AFt, and a large number of needle-and-rod AFt intertwined to improve the flexural strength of the material, and the surface of the specimen hydrated to the age of 28 days was very dense, and there were a lot of AFt and C-S-H gels stacked and cemented together with each other.
4. Conclusions
1) Red mud has a certain activity, can form a compound mixing cementitious material with slag and desulfurization gypsum, and under the action of sodium silicate as an exciter, a structure with a certain strength is formed.
2) The optimum moisture content and maximum dry density of stabilized gravel material increase gradually with the increase of cementitious material dosage, and the 7-day unconfined compressive strength of stabilized gravel under 4 % red mud-based cementitious material dosage meets the specification of the strength requirements of the subgrade.
3) Red mud-based cementitious materials have better mechanical properties, volume stability and seepage resistance, mainly due to the addition of lime and desulfurization gypsum can promote the hydration of fly ash, the formation of more hydration products, desulfurization gypsum will produce volume expansion, reduce the porosity, and further enhance the structural properties.
References
-
Guo Bin, Liang Feng, Wu Fan, Tu Guangfu, and Gao Qian, “Study on new high strength cementitious material of Gaoguanying iron mine,” (in Chinese), Jinshu Kuangshan, Vol. 48, No. 11, pp. 8–13, 2019.
-
J. W. Wang, C. S. Lv, and X. L. Ji, “Review on the comprehensive utilization of red mud,” Guangzhou Chemical Industry, Vol. 40, No. 16, pp. 3–6, 2012.
-
W. Liu, X. Chen, W. Li, Y. Yu, and K. Yan, “Main categories of red mud and its environmental impacts,” Journal of Cleaner Production, Vol. 84, No. 9, pp. 606–610, Dec. 2014, https://doi.org/10.1016/j.jclepro.2014.06.080
-
T.-A. Zhang, Y. Wang, G. Lu, Y. Liu, W. Zhang, and Q. Zhao, “Comprehensive utilization of red mud: current research status and a possible way forward for non-hazardous treatment,” in The Minerals, Metals and Materials Series, pp. 135–141, 2018, https://doi.org/10.1007/978-3-319-72284-9_18
-
S. G. Xue, Y. B. Li, and Y. Guo, “Environmental impact of bauxite residue: a comprehensive review,” (in Chinese), Journal of University of Chinese Academy of Science, Vol. 34, No. 4, pp. 401–412, 2017.
-
M. Zhao et al., “Freeze-thaw durability of red mud slurry-class F fly ash-based geopolymer: Effect of curing conditions,” Construction and Building Materials, Vol. 215, pp. 381–390, Aug. 2019, https://doi.org/10.1016/j.conbuildmat.2019.04.235
-
N. Ye et al., “Synthesis and strength optimization of one-part geopolymer based on red mud,” Construction and Building Materials, Vol. 111, pp. 317–325, May 2016, https://doi.org/10.1016/j.conbuildmat.2016.02.099
-
Q. M. Ma and L. P. Huang, “Effect of alkali concentration and modulus of alkaline activator on the compressive properties and hydration products of alkali activated slag cementitious materials,” Bulletin of The Chinese Ceramic Society, Vol. 37, No. 6, pp. 2002–2007, 2018.
-
S. Wang, Y. Boyjoo, A. Choueib, and Z. H. Zhu, “Removal of dyes from aqueous solution using fly ash and red mud,” Water Research, Vol. 39, No. 1, pp. 129–138, Jan. 2005, https://doi.org/10.1016/j.watres.2004.09.011
-
J. Chang, “Reduction roasting – magnetic separation study of red mud in Yunnan,” (in Chinese), Light Matals, Vol. 8, pp. 8–14, 2017.
-
T. Zhu and N. Xia, “Experimental research and application of flue gas desulfurization characteristics based on red mud desulfurizer,” (in Chinese), China Sciencepaper, Vol. 11, No. 9, pp. 1056–1061, 2016.
-
Z. P. Hu, L. F. Zhang, and Z. Y. Yuan, “Application of red mud in the field of catalytic industry,” Journal of Petroleum (Petroleum Processing), Vol. 35, No. 1, pp. 197–209, 2019.
-
N. X. Liang and D. L. Zhang, “Research on road performance of cemented red mud concrete,” (in Chinese), China Highway Journal, Vol. 9, No. 2, pp. 6–11, 1996.
-
N. Zhang and Y. F. Gao, “Experimental study on high doping red mud-based roadbed filling material,” China Resources Comprehensive Utilization, Vol. 38, No. 11, pp. 14–17, 2020.
About this article
This study was financially supported by the Shandong Province Key R&D Program (Major Technological Innovation) (No. 2020CXGC011405).
The datasets generated during and/or analyzed during the current study are available from the corresponding author on reasonable request.
The authors declare that they have no conflict of interest.