Abstract
The thermal damage process of the energetic material sample D-RDX was simulated by the thermal accelerated aging test, and the physical and explosive properties of the thermally damaged D-RDX energetic material were measured. The results showed that the physical properties of D-RDX did not change significantly under the test conditions, but the impact safety was significantly different, and the safety of the thermally damaged D-RDX sample showed greater dispersion.
1. Introduction
In the process of ammunition storage, under the influence of environmental factors such as temperature, humidity, salt fog, salt water and corrosive gas, some irreversible changes may occur in the energetic substances, affecting their safety and explosive performance, and thus threatening the entire ammunition system.
The performance of energetic substances is not only related to their own properties, but also closely related to the environmental stimuli it receives. E. James even believes that the sensitivity of energetic substances is not a performance of energetic substances themselves, but a reflection of energetic substances to the environment. The rules obtained by different stimulus sources may be completely opposite [1-2]. Therefore, to study the threat of these irreversible changes to ammunition or personnel, two aspects of work need to be done: long-term storage of samples and production of stimulus sources.
D-RDX is one of the most commonly used booster explosives, and its long-term storage performance has received great attention. In this paper, the accelerated aging test under constant temperature and air conditions is used to simulate the long-term storage process of D-RDX booster. The clapboard test device is used as the standard stimulus source and the result judgment basis to study its impact initiation performance. The results obtained can provide a reference for the analysis of the reliable initiation and sympathetic detonation sensitivity of D-RDX booster after long-term storage.
2. Experiment
2.1. Materials and instruments
А-Ⅸ-I (donor charge, 7 charge columns), charge weight 1.200 g, density 1.65g·cm-3; D-RDX (acceptor charge, 7 sections of charge), charge weight 1.230 g, density 1.67 g·cm-3; No. 21 instantaneous detonator; Micrometer, accuracy 0.01 mm; Depth gauge, accuracy 0.01 mm; Electronic balance, accuracy 0.001 g; Constant temperature accelerated aging instrument; 20# mild steel identification block; 45# steel sleeve; PMMA organic gaps.
2.2. Accelerated aging test
According to the environmental test standard and MIL-STD-1751A, the single temperature accelerated aging test temperature is 71 ℃. Select the chemical reaction temperature coefficient R10=2.7, according to Arrhenius equation, obtain the calculation formula of 71 ℃ aging method, see Eq. (1):
The samples were divided into five groups for experiment, and the aging time was 0, 4, 19, 38 and 76 days respectively. The corresponding natural aging (25 °C) time was calculated by Eq. (1) as 0, 1, 5, 10 and 20 years respectively.
2.3. Gap test
The detonator detonates the main charge column, and the shock wave generated by the main charge column acts on the acceptor energetic material after being attenuated by the PMMA GAP. The dent depth on the identification block determines whether the acceptor energetic material will explode under the action of the shock wave. The experimental principle is shown in Fig. 1.
The design of the device shall refer to GJB2178-1994 Safety Test Method of Booster Explosive [3-4]. There is detonator, detonator, sleeve, 7 main charge columns, partition, sleeve, 7 main charge columns and identification block. The gap used in each experiment are monolithic, and the thickness listed in Table 2 is the actual measured value.
Select the initial partition value for the test according to experience. If “go” occurs, increase the partition value, or reduce the partition value. Take the arithmetic mean of the maximum partition value with three consecutive “go” and the minimum partition value with three consecutive “no go” as the 50 % critical partition value of the final sample. If the dent depth of the identification block exceeds half of the dent depth during the zero gap test, it will be determined as “go”, otherwise it will be determined as “no go”. In this experiment, under the condition of zero gap, the dent depth of the identification block is 1.810 mm-1.869 mm (with different aging time, the dent depth changes slightly, but does not affect the result judgment).
Fig. 1Test principle
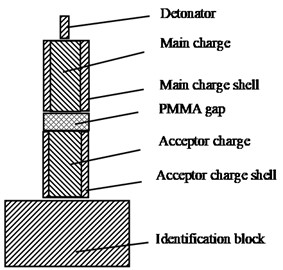
3. Results and discussion
3.1. Experimental results
The appearance of the sample will change irreversibly after accelerated aging at high temperature. The diameter, height and mass of the sample have been measured in this paper. The results are shown in Table 1. Table 2 lists the critical partition thickness values for 50 % “go” of samples before and after aging.
Table 1Physical parameters of samples
Aging time / d | Height / mm | Relative change rate / ‰ | Diameter / mm | Relative change rate / ‰ | Mass / mg | Relative change rate / ‰ |
0 | 5.375 | – | 4.985 | – | 1240 | |
4 | 5.377 | 0.37 | 4.984 | –0.21 | 1237 | –0.031 |
19 | 5.383 | 1.49 | 4.985 | 0.00 | 1231 | –0.092 |
38 | 5.389 | 2.38 | 4.989 | 0.81 | 1233 | 0.078 |
76 | 5.390 | 2.80 | 4.990 | 1.01 | 1231 | –0.092 |
Table 2Test results of diaphragm of aged samples
Aging time / d | Upper limit of thickness / mm | Lower limit of thickness / mm | Average thickness / mm | Upper and lower limit difference / mm |
0 | 7.00 | 6.81 | 6.91 | 0.19 |
4 | 7.10 | 6.81 | 6.96 | 0.29 |
19 | 7.60 | 7.30 | 7.45 | 0.30 |
38 | 8.30 | 7.90 | 8.10 | 0.40 |
76 | 8.00 | 7.50 | 7.75 | 0.50 |
3.2. Effect of accelerated aging time on physical properties of samples
Analyze the data in Table 1 and plot the relative change rate of sample height, diameter and mass with the aging time of the sample. See Fig. 2 for the results. It can be seen from the figure that the relative change rate of the physical parameters of the sample is less than 0.3 % compared with that of the sample without aging, indicating that the change of the physical parameters of the sample is not significant. The research of Liu et al. [5] shows that energetic material particles tend to swell under high temperature heating conditions. However, due to the excellent high temperature mechanical properties of F2603 used in the sample, the small swelling of energetic material particles under the constraint of the spatial network structure formed by F2603 is not shown macroscopically.
Fig. 2Change rule of relative change rate with aging time
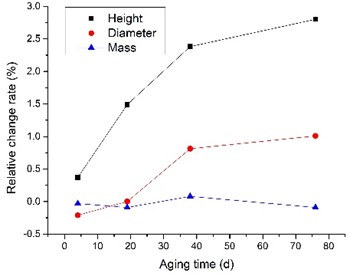
In order to obtain more direct information, the laser confocal tester was used to obtain the local morphology photos of the cross section of the sample, and the results are shown in Fig. 3. The white part in the figure is the energetic material particles, and the black part is the polymer components. It can be seen that with the increase of aging time, the interface between the energetic material particles and the polymer binder becomes more and more blurred, and the energetic material particles in the sample aged for 76 days become uneven, indicating that the coating layer indicated by the energetic material particles is partially damaged, which may be mainly caused by the swelling behavior of the energetic material particles.
Fig. 3Photos of sample surface morphology

3.3. Effect of accelerated aging time on impact initiation performance of samples
After aging, the shock wave sensitivity of the sample increases. With the increase of aging time, the shock wave sensitivity has a change rule of first increasing and then decreasing.
D-RDX is a heterogeneous energetic material composed of RDX, F2603 and graphite. In order to further understand the impact initiation mechanism of the sample, the hole distribution in the fixed area of the unaged sample was tested by CT. The results are shown in Fig. 4. It can be seen that there are small holes of different sizes in the seemingly dense grain (the calculation shows that the porosity at the fixed area of the sample is 1.59 %). Under the action of shock wave, the reaction of energetic material can be divided into three stages: hot spot formation and ignition, surface combustion of energetic material particles, combustion acceleration and convergence. Because the diameter and height of the sample in this experiment are very small, the reaction form of the sample is mainly determined by the formation of hot spots and the reaction rate at the stage of igniting the surrounding energetic substances, and the reaction rate is determined by the shock wave pressure acting on the sample and the size and number of defects in the sample. Fig. 5 shows two typical reaction forms. The upper end of the sleeve in the left figure is intact and the lower end is cracked, indicating that the sample has undergone a combustion to detonation transition reaction. The upper end of the sleeve in the right figure is intact and the lower end is reamed, indicating that the sample has undergone a combustion to detonation transition reaction.
Fig. 4Three-dimensional structure of the fixed area inside the sample
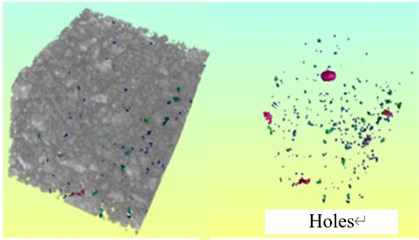
Fig. 5Sleeve after test
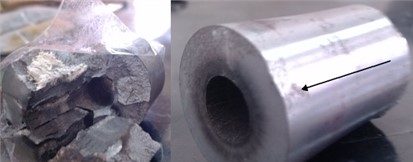
The size and number of holes (or microcracks) in the sample are the key factors to determine the impact initiation characteristics of the sample. Considering that graphite in the sample is the most insensitive, the change of its properties can be ignored. Under the long-term high temperature, the sample will have three main single changes, namely, the aging of fluor rubber, the damage of the indicated coating of RDX, and the self-repairing of RDX crystal, as well as the comprehensive influence of three factors [6-7]. The first two factors will cause the original stable system between the sample components to be affected by internal stress and temperature stress, and in serious cases, microcracks or visible holes will appear. These changes will lead to an increase in the number of hot spots in the sample, making the detonation reaction easier to form, which may be the main reason for the increase in shock sensitivity of the aged sample [8]. The influence of the self-repairing change of RDX crystal on the shock wave sensitivity gradually appears, which may be the reason for the slight reduction of the shock wave sensitivity of the sample aged for 76 days.
The data in the last column in Table 2 shows that with the increase of aging time, the difference between the upper and lower limit values of the diaphragm increases gradually. During the test, we tried to conduct a exploratory test with a step of 0.1mm near the upper and lower limits, and found that the test results are highly dispersed. In order to ensure the reliability of the test results, we can only increase the difference between the upper and lower limits of the diaphragm. This result shows that the original balance in the sample has been broken under the long-term high temperature effect, which increases the dispersion of the sample structural parameters and finally leads to the increase of the dispersion of the sample impact initiation performance.
4. Conclusions
1) The height and diameter of D-RDX grain increased slightly compared with the value without aging, but the relative change rate was less than 0.3 %, the mass decreased slightly, and the relative change rate was less than 0.01 %, indicating that the physical parameters of JH-14C did not change significantly under high temperature accelerated aging conditions;
2) After aging, the shock wave sensitivity of D-RDX grain increases. With the increase of aging time, the shock wave sensitivity first increases and then decreases, and with the increase of aging time, the dispersion of shock initiation performance of D-RDX grain gradually increases.
3) The difference of thermal expansion coefficient between explosive particles and binder leads to the increase of interface gap, even interface shedding, which shows obvious dispersion under the action of shock wave and the regularity of shock wave sensitivity data decreases; After long-term storage, the safety and reliability of explosives should be fully considered, and the life of explosives should be evaluated in multiple dimensions.
References
-
J. H. Yi et al., “Measurement method and application for wave velocity during deflagration-to-detonation transition based on microwave phase-shifting principle,” Chinese Journal of Explosives and Propellants, Vol. 44, No. 4, pp. 532–537, 2021, https://doi.org/10.14077/j.issn.1007-7812.202006019
-
X. G. Dai, Y. Xiang, and C. Y. Shen, “Reaction ability of PBX-2 before and after accelerated aging by projectile impact (Steven test),” Chinese Journal of Energetic Materials, Vol. 14, No. 6, pp. 453–456, 2006, https://doi.org/10.3969/j.issn.1006-9941.2006.06.013
-
“Test method for safety of booster explosives, GJB2178-94,” 1994.
-
X. S. Feng, S. X. Zhao, and X. P. Li, “The shock sensitivity of a recrystallizing RDX,” Chinese Journal of Energetic Materials, Vol. 15, No. 6, pp. 581–584, 2007, https://doi.org/10.3969/j.issn.1006-9941.2007.06.006
-
Y. C. Liu, Z. S. Wang, T. Chai, and J. L. Zhang, “Influence of HMX particle size and gradation on the shock sensitivity and output of a PBX explosive,” Acta Armamentarii, Vol. 21, No. 4, pp. 357–360, 2000, https://doi.org/10.3321/j.issn:1000-1093.2000.04.018
-
J. B. Fu, Fox-7 for Insensitive Boosters. Shanxi: Central North University, 2010.
-
C. Zhang et al., “Shock wave sensitivity of modified double-base propellant containing CL-20,” Chinese Journal of Explosives & Propellants, Vol. 43, No. 5, pp. 549–552, 2020, https://doi.org/10.14077/j.issn.1007-7812.201905011
-
D. Y. Gao et al., “Accelerated aging on effect of safety for explosive parts,” Chinese Journal of Energetic Materials, Vol. 19, No. 6, pp. 673–678, 2011, https://doi.org/10.3969/j.issn.1006-9941.2011.06.017
About this article
The authors have not disclosed any funding.
The datasets generated during and/or analyzed during the current study are available from the corresponding author on reasonable request.
The authors declare that they have no conflict of interest.