Abstract
The article addresses results of the research on the structure and propagation of vibration of vehicle for different parameters of suspension damping system. Long term exposure to whole-body vibration in transport may cause health risk and many diseases. Suspension is the most important system of vehicle for vibration control of level of wave emission to car-body and passengers. Thus the research on structure and propagation of vibration were conducted for different damping parameters of shock absorbers. For the sake of the analysis of exposure to whole-body vibration signals of general vibration were recorded at locations where vibration penetrated the human organism by the feet inside the vehicle. The vibrations have to be analyzed in the domains of amplitudes, time, frequency and time-frequency. Chosen estimators were defined and compared for the sake of the analysis of vibration propagation in terms of energy and dynamics. To evaluate the exposure to vibration it is important to analyse the dynamics of phenomena and main frequency components of vibration. For the spine response in vertical direction calculation of the model presented in ISO 2631 was used. The calculations of acceleration dose and equivalent static compressive stress for the assessment of health effects were done. Due to the large capacity of information in vibration signal the scope of presented research can be used for active diagnostics experiments on determining of estimators of technical condition of suspension elements.
1. Introduction
The consequences of the impact of vibration on humans are all kinds of adverse effects in the body, resulting from exposure to vibration. Range and process behavior of these changes depends largely on where they penetrate into the body. A very large group of persons exposed to general vibrations comprises car drivers, passengers, tram drivers or building and road machinery operators. Vibrations propagate into the human organism through vehicle seats via the pelvis, the back and lateral parts of the body as well as through the vehicle floor panel via feet. The most harmful to people vibrations are those input frequency of which is close to the free vibration pulsation of human organs. The scope and the procedure of handling them depend to a considerable extent on the location where they penetrate the organism [1-6].
Vibration can be considered in many terms, as effects of different generators and linear or nonlinear functions of propagation [7-10]. Vibrations perceived as internal phenomena reduce the efficiency of transport processes as well as transport safety and comfort [11, 12]. It is more and more common that vibrations, being undesirable residual phenomena, are used in machinery monitoring and diagnostics [13-18]. A vehicle suspension system, which consists of damping, springing and steering elements, is responsible to a considerable extent for damping of vibrations generated by road roughness [11]. The purpose of every shock absorbing system and element is to minimise the impact exerted by vibrations on other systems as well as on the persons inside the vehicle. It can be considered as vibration control system [19, 20]. Oscillatory waves propagate and influence people via the vehicle structure, i. e. the frame or the body. Changes in the structure and composition of material may affect its capacity for the oscillatory wave propagation and materials properties, so all physical relation have to be considered [21-24]. General vibrations are mainly transferred on men via lower extremities as well as the middle and lower section of the spine.
As far as random vibration phenomena are concerned, the signals recorded are of non-stationary nature which requires that the signal distribution is observed in the domains of time and frequency simultaneously [25].
2. Research method
For the car moving at a speed of ca. 80 km/h the most energy of the vibration signal is contained in the band up to 20-30 Hz with the assumptions of secondary roads class and an average wavelength of existing roads.
The active research experiments were conducted on real passenger car. The vehicle was excited to vibration by special kinematic excitation machine with an inductor controlled with a frequency converter. It enabled the system to be excited to vibrate within the chosen band of stabilised frequencies band. The range of the frequency of the forced vibrations was set as dynamic linear increase up to ca. 21 Hz, excitation with constant frequency (ca. 21 Hz) for 5 seconds and once the testing station had been switched off, this made it possible to analyse the free damping vibrations. This set up allows analysis of bands of sprung and unsprung masses resonances.
Fig. 1Research and testing diagram and location of the vibration sensors
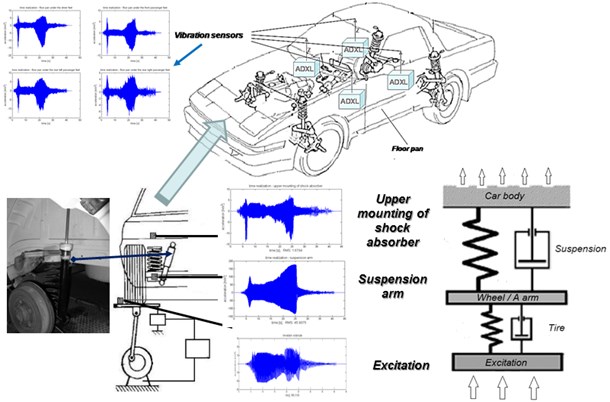
Fig. 2Chosen applied damping characteristics of hydraulic shock-absorber: black – damping characteristics corresponding to the shock absorber with 60 % of fluid volume, red – 70 % of fluid volume, blue – 80 % of fluid volume, green – 90 % of fluid volume, yellow – 100 % of fluid volume
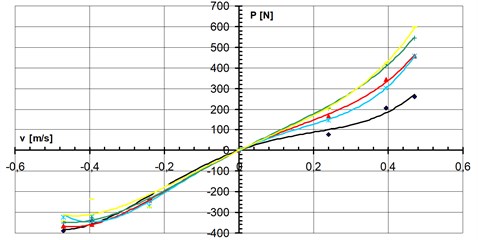
The scope of the research allows analysis of quantity of vibration isolation by suspension system. For the sake of the analysis of exposure to general vibration signals they were recorded at locations where vibration penetrated the human organism by the feet inside the vehicle. The research method and location of measurement points has been depicted in Fig. 1.
It was assumed that the main factor of technical condition of the vibration damping element is the degree to which the shock absorber cylinder is filled with shock absorbing fluid [26]. Some of the results of damping characteristics of shock absorbers with different volume of fluid have been depicted in Figure 2.
Fig. 3Distribution of acceleration of vibration of floor panel under the feet of passengers (shock absorber with 100 % of fluid volume)
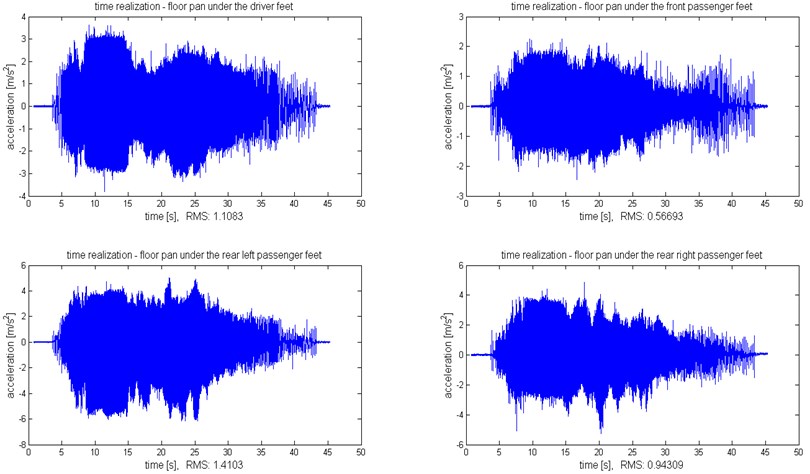
Fig. 4Distribution of acceleration of vibration of floor panel under the feet of passengers (shock absorber with 50 % of fluid volume)
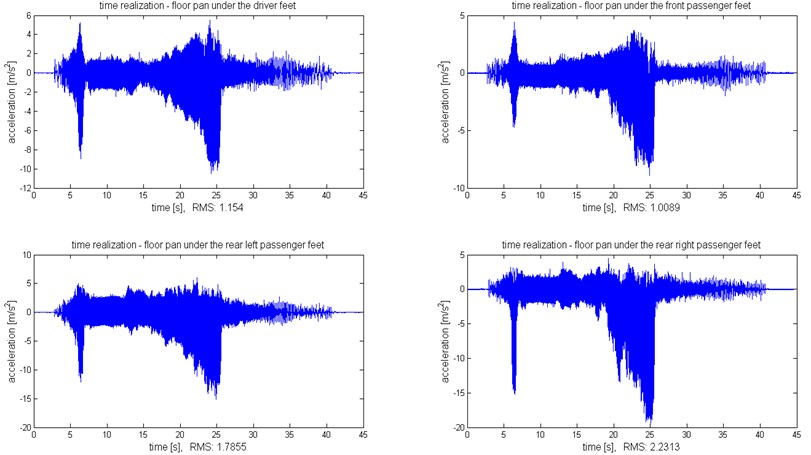
3. Research results
Due to the complexity resulting from nonlinear and random nature of vibration phenomena in automotive vehicles, the analysis in question is multidimensional. The vibration is analyzed in the domains of amplitudes, time, frequency and time-frequency.
3.1. General vibration propagation
Research on general vibration propagation has been conducted and the vertical vibrations of floor panel have been measured. The measurement points have been placed at locations where vibration penetrated the human organism by the feet inside the vehicle (Fig. 3 and 4). For the sake of the analysis of vibration propagation in terms of energy the values of RMS (Root Mean Square) were calculated and compared (Fig. 5).
Fig. 5Vibration energy propagation – comparison of RMS of floor pan vibration signals (blue – 50 % of shock absorber fluid, red – 100 % of shock absorber fluid): 4 – front left, 5 – front right, 6 – rear left, 7 – rear right
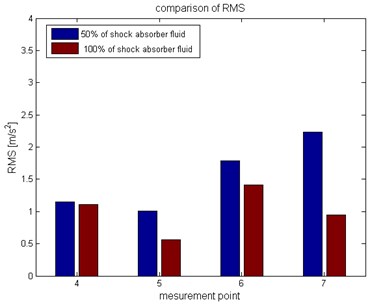
Fig. 6Spectrums of vibration of floor panel under the feet of passengers (blue line – shock absorber with 100 % of fluid volume, green dash-dot line – shock absorber with 50 % of fluid volume)
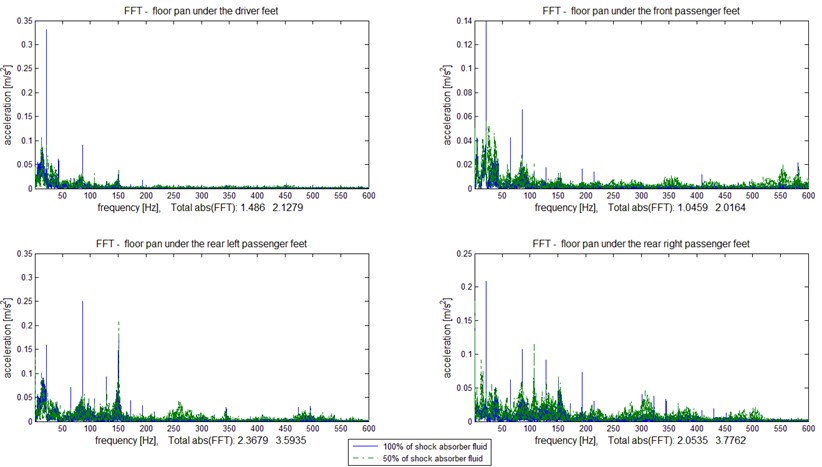
Fig. 7Time-frequency structure of vibration signals of floor panel under the feet of passengers (shock absorber with 100 % of fluid volume)
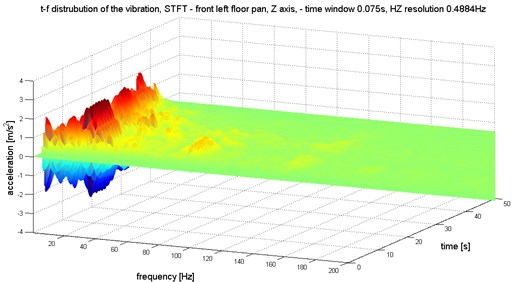
a)
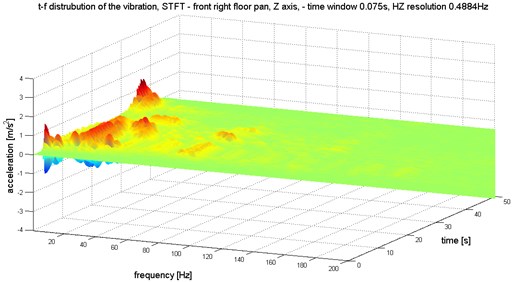
b)
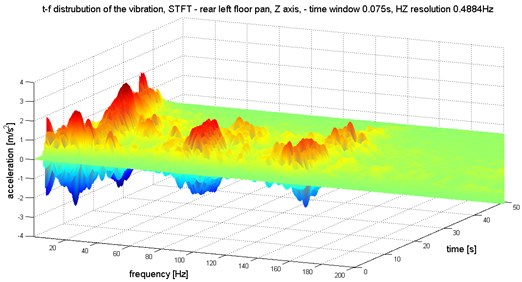
c)
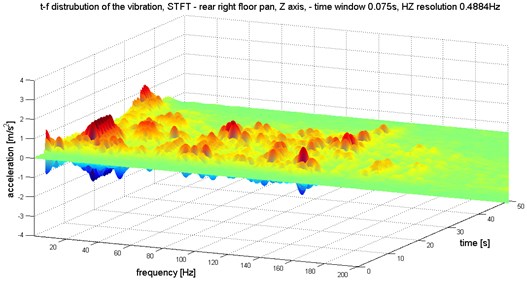
d)
It can be observed that RMS values of the vibration signal with shock absorber with 50 % of fluid volume are greater. Especially vibration for the 20-25 seconds of signal period. For the analysis of the dynamics of the vibration the spectrum of the signals, calculated by Fast Fourier Transformation (FFT), have been depicted in Figure 6. As it is seen the vibrations of vehicle with shock absorber with 50 % of fluid volume have many more of frequency components in wider range of frequency band. For the signals of vibration with shock absorber with 100 % of fluid volume it can be assumed that vibrations are strongly correlated with frequency of constant excitation.
3.2. Structure and exposure to general vibration
To evaluate the exposure to vibration it is important to analyse the dynamics of phenomena and main frequency components of vibration. It is necessary to analyse structure of vibration signals as multidimensional. The vibrations have to be analyzed in the domains time-frequency. Simultaneous extraction of information concerning the time-frequency structure of a signal being analysed is possible owing to a Short Time Fourier Transform (STFT). Application of this method allows identifying with good precision the time when the resonance occurs. The resonances are well noticeable as the local increase of the amplitude of vibration, both in time and frequency domains (Fig. 7 and 8).
Fig. 8Time-frequency structure of vibration signals of floor panel under the feet of passengers (shock absorber with 50 % of fluid volume)
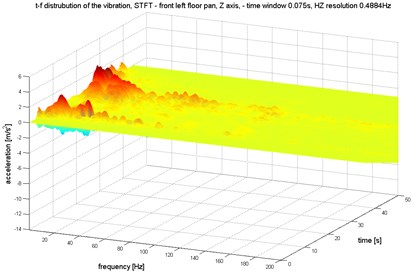
a)
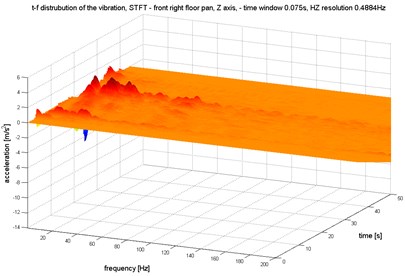
b)
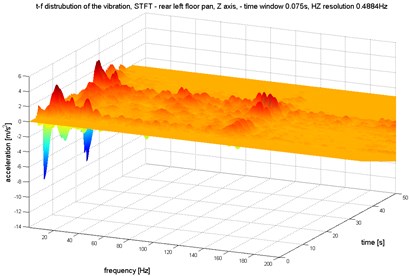
c)
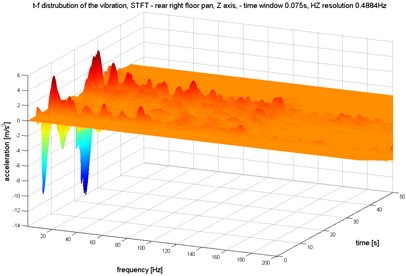
d)
Based on the time-frequency distribution (structure) of the signals it can be calculated the time exposure to vibration in specified frequency correlated to the free vibration pulsation of human organs.
The International Organization for Standardization and Technical Committee ISO/TC 108 prepared the standards ISO 2631 1-5 – Mechanical vibration and shock – Evaluation of human exposure to whole-body vibration. For the sake of the analysis of human exposure to general vibration the methods of quantifying vibration containing multiple shocks in relation to human health have been used. Adverse effects on the lumbar spine are the dominating health risk. Therefore the analysis is concerned with the lumbar spine response. For the spine response in vertical direction calculations of the model presented in ISO 2631-5:2004 (chapter 5.2.3) were used. The calculations of acceleration dose and equivalent static compressive stress for the assessment of health effects were done (see Table 1).
Some of the results of spine response and acceleration dose and equivalent static compressive stress of vibration of the floor panel under the driver feet have been depicted in Figure 9.
Table 1Estimators of human exposure to whole-body vibration (ISO 2631-5:2004)
Acceleration dose | Average daily dose | Equivalent static compressive stress | Daily equivalent static compressive stress |
is the th peak of the response acceleration, is direction of acceleration ( in calculation), is the duration of the daily exposure (30 min in calculation), is the period over which has been measured (0.75 min in calculation), is direction of vibration factor (for axis 0.032). |
Fig. 9Measured results of vertical vibration of floor panel under the driver feet (left) and response in the spine calculated by the non-linear model presented in ISO 2631-5:2004 and estimators of human exposure to whole-body vibration (right) – the upper results of the 100 % of shock absorber fluid, the lower results of the 50 % of shock absorber fluid
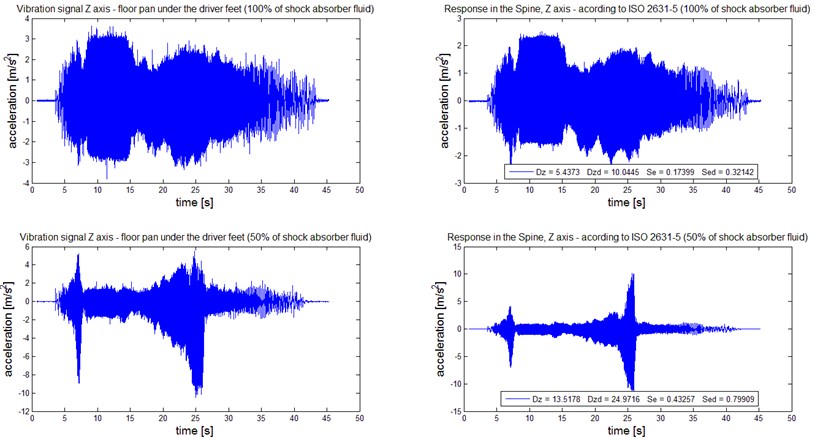
4. Conclusions
Designers of automotive vehicles strive to limit the vibrations of sprung masses, trying to maintain sufficient rigidity of the suspension system at the same time, so that suitable steerability is ensured. Consequently, material properties and metallurgical technologies applied in the automotive industry and repair technology are gradually growing in importance [27-32].
The presented results showed that there are many of frequencies of occurred vibration, especially during the time of passing the resonances. The vibrations registered in research on shock absorber with 50 % of fluid are higher. It can be strongly recognized in resonances phase.
For the purpose of analysis of vibration propagation in vehicle construction it is important to determine the energy and dynamics of the vibration. The global estimators of energy as RMS can be useful for preliminary evaluation of level of vibration exposure on passengers by floor pan. On the human perception the frequency of vibration is very important. The analysis of spectrum of the signals (FFT) allows to determine the dominant frequency component.
The attempts to use the acceleration dose and equivalent static compressive stress for the assessment of health effects of general vibration according to methods from ISO 2631-5 have been successful. The vibration measurement requirements included in ISO 2631-1 are to measure in 3 orthogonal directions on driver seat. The presented calculation was for measurement only in one vertical direction on floor panel, but it still corresponded with general vibration and adverse effects on the lumbar spine. According to ISO 2631-5 assessment of adverse health effect at lifetime exposure are acceptable where is below 0.5 and very dangerous when it is above 0.8. The obtained results for the shock absorber with 100 % of fluid ( 0.32142) and 50 % of fluid ( 0.79909), with notification that the results are only for the vertical vibration, show huge impact of damping parameters on human exposure to vibrations in a passenger car. If the horizontal vibration (, axis) is counted the probability of an adverse health effect will be very high.
Based on STFT transformation some sensitive estimators of exposure to whole-body vibration, based on general vibration can be calculated. Thus it can be calculated that the sum of the energy of the vibration in chosen frequency bands corresponds to the free vibration pulsation of human organs. It can be very useful for vehicle car vibration monitoring and active control of vibration system. The results of previous and conducted research show some possibilities to develop the active system for monitoring and decreasing human vibration exposure in passenger cars.
References
-
Bubulis A., Reizina G., Korobko E., Bilyk V., Efremov V. Controllable vibro-protective system for the driver seat of a multi-axis vehicle. Journal of Vibroengineering, Vol. 13, Issue 3, 2011, p. 552-557.
-
Paddan G., Griffin M. Evaluation of whole-body vibration in vehicles. Journal of Sound and Vibration, Vol. 253, Issue 1, 2002, p. 195-213.
-
Tiemessen I., Carel T., Hulshof J., Monique H., Frings-Dresen W. An overview of strategies to reduce whole-body vibration exposure on drivers: a systematic review. International Journal of Industrial Ergonomics, Vol. 37, 2007, p. 245-256.
-
Wyllie I. H., Griffin M. J. Discomfort from sinusoidal oscillation in the pitch and fore-and-aft axes at frequencies between 0.2 and 1.6 Hz. Journal of Sound and Vibration, Vol. 324, 2009.
-
Gallais L., Griffin M. J. Low back pain in car drivers: a review of studies published 1975 to 2005. Journal of Sound and Vibration, Vol. 298, 2006, p. 499-513.
-
Qiu Y., Griffin M. J. Transmission of roll, pitch and yaw vibration to the backrest of a seat supported on a non-rigid car floor. Journal of Sound and Vibration, Vol. 288, 2005, p. 1197-1222.
-
Ragulskis K., Kanapeckas K., Jonušas R., Juzėnas K. Vibrations generator with a motion converter based on permanent magnet interaction. Journal of Vibroengineering, Vol. 12, Issue 1, 2010, p. 124-132.
-
Bubulis A., Jūrėnas V., Stepanenko D., Chigarev A., Minchenya V. Nonlinear effects related to vibrations of long elastic waveguides: formulation of nonlinear equations. Journal of Vibroengineering, Vol. 10, Issue 2, 2008, p. 222-224.
-
Dąbrowski Z., Dziurdź J., Klekot G. Studies on propagation of vibroacoustic energy and its influence on structure vibration in a large-size object. Archives of Acoustics, Vol. 32, Issue 2, 2007, p. 231-240.
-
Burdzik R. Material vibration propagation in floor pan. Archives of Materials Science and Engineering, Vol. 59, Issue 1, 2013, p. 22-27.
-
Burdzik R. Monitoring system of vibration propagation in vehicles and method of analysing vibration modes. Edited by J. Mikulski: TST 2012, CCIS 329, Springer, Heidelberg, 2012, p. 406-413.
-
Burdzik R. Research on structure and directional distribution of vibration generated by engine in the location where vibrations penetrate the human organism. Diagnostyka, Vol. 14, Issue 2, 2013, p. 57-61.
-
Grządziela A. Modelling of propeller shaft dynamics at pulse load on structure and directional distribution of vibration generated by engine in the location where vibrations penetrate the human organism. Polish Maritime Research, Vol. 15, Issue 4, 2008, p. 52-58.
-
Grządziela A. An analysis of possible assessment of hazards to ship shaft line, resulting from impulse load. Polish Maritime Research, Vol. 3, 2007, p. 14-17.
-
Figlus T., Wilk A., Madej H., Łazarz B. Investigation of gearbox vibroactivity with the use of vibration and acoustic pressure start-up characteristics. Archive of Mechanical Engineering, Vol. 58, Issue 2, 2011, p. 209-221.
-
Jasinski M., Radkowski S. Use of the higher spectra in the low-amplitude fatigue testing. Mechanical Systems and Signal Processing, Vol. 25, Issue 2, 2011, p. 704-716.
-
Dziurdź J. Transformation of nonstationary signals into pseudostationary signals for the needs of vehicle diagnostics. Acta Physica Polonica A, Vol. 118, Issue 1, 2010, p. 49-53.
-
Michalski R., Wierzbicki S. An analysis of degradation of vehicles in operation. Maintenance and Reliability, Vol. 1, Issue 3, 2008, p. 30-32.
-
Tůma J., Šimek J., Škuta J., Los J. Active vibrations control of journal bearings with the use of piezoactuators. Mechanical Systems and Signal Processing, Vol. 36, Issue 2, 2013, p. 618-629.
-
Farana R., Wagnerova R. Sliding mode controls of complex control systems. Mine Planning and Equipment Selection, Editors R. K. Singhal, B. P. Singh, 2001, p. 11-17.
-
Folęga P., Siwiec G. Numerical analysis of selected materials for flexsplines. Archives of Metallurgy and Materials, Vol. 57, Issue 1, 2012, p. 185-191.
-
Konieczny Ł., Burdzik R., Łazarz B. Analysis of properties of automotive vehicle suspension arm depending on different materials used in the MSC. Adams environment. Archives of Materials Science and Engineering, Vol. 58, Issue 2, 2012, p. 171-176.
-
Mencik J. Determination of parameters of visco-elastic materials by instrumented indentation. Part 3: Rheological model and other characteristics. Chem. Listy, Vol. 104, 2010, p. 275-278.
-
Kaźmierczak-Bałata A., Bodzenta J., Trefon-Radziejewska D. Determination of thermal-diffusivity dependence on temperature of transparent samples by thermal wave method. International Journal of Thermophysics, Vol. 31, Issue 1, 2010, p. 180-186.
-
Jamro E., Wielgosz M., Bieniasz S., Cioch W. FPGA – ARM heterogeneous system for high speed signal analysis. Solid State Phenomena, Vol. 180, 2012, p. 207-213.
-
Burdzik R., Konieczny Ł., Łazarz B. Influence of damping characteristics changes on vehicles vibration research. 19th International Congress on Sound and Vibration (ICSV19), Conference Proceedings, 2012, p. 657.
-
Burdzik R., Folęga P., Łazarz B., Stanik Z., Warczek J. Analysis of the impact of surface layer parameters on wear intensity of frictional couples. Archives of Materials and Metallurgy, Vol. 57, Issue 4, 2012, p. 987-993.
-
Blacha L., Siwiec G., Oleksiak B. Loss of aluminium during the process of Ti-Al-V alloy smelting in a vacuum induction melting (VIM) furnace. Metalurgija, Vol. 52, Issue 3, 2013, p. 301-304.
-
Blacha L., Łabaj J. Factors determining the rate of the process of metal bath components evaporation. Metalurgija, Vol. 51, Issue 4, 2012, p. 529-533.
-
Węgrzyn T., Piwnik J., Burdzik R., Wojnar G., Hadryś A. New welding technologies for car body frame welding. Archives of Materials Science and Engineering, Vol. 58, Issue 2, 2012, p. 245-249.
-
Węgrzyn T., Piwnik J., Łazarz B., Hadryś D. Main micro-jet cooling gases for steel welding. Archives of Materials and Metallurgy, Vol. 58, Issue 2, 2013, p. 551-553.
-
Dobrzański L., Bonek M., Hajduczek E., Klimpel A., Lisiecki A. Application of high power diode laser (HPDL) for alloying of X40CRMOV5-1 steel surface layer by tungsten carbides. Journal of Materials Processing Technology, Vol. 155/156, 2004, p. 1956-1963.