Abstract
Seats are one of the most significant components of vehicles. Customer’s expectations for the comfort in vehicle seats rise continuously. Designing of automobile seats has always been a challenge for engineers as design parameters for automobile seats are complex. When it comes to the design of automobile seats, three design objectives, namely comfort, safety and health need to be fulfilled simultaneously. Vibration analysis plays a major role in engineering including the area of design for automobile comfort. Human structure, as a mechanical system, is immensely complex and the mechanical properties of human body readily undergo change. In addition, the vibration can initiate the development of pressure ulcer and other long-term diseases. Comfort measurement is challenging because of such factors as user subjectivity, seat geometry, occupant anthropometry and amount of time spent sitting. The purpose of this study is to identify the most significant parameters that make vibration in the vehicle seat which reduce passenger comfort and to identify the design parameters that can impact on appropriate seat design. Suspension systems, seat cushion and sitting postures are some of the vital parameters that have huge impacts on comfort analysis. This review could help in design of seat cushions with appropriate material properties and in analysing the comfort levels of human body to reduce the vibration transmissibility at the critical frequency bands.
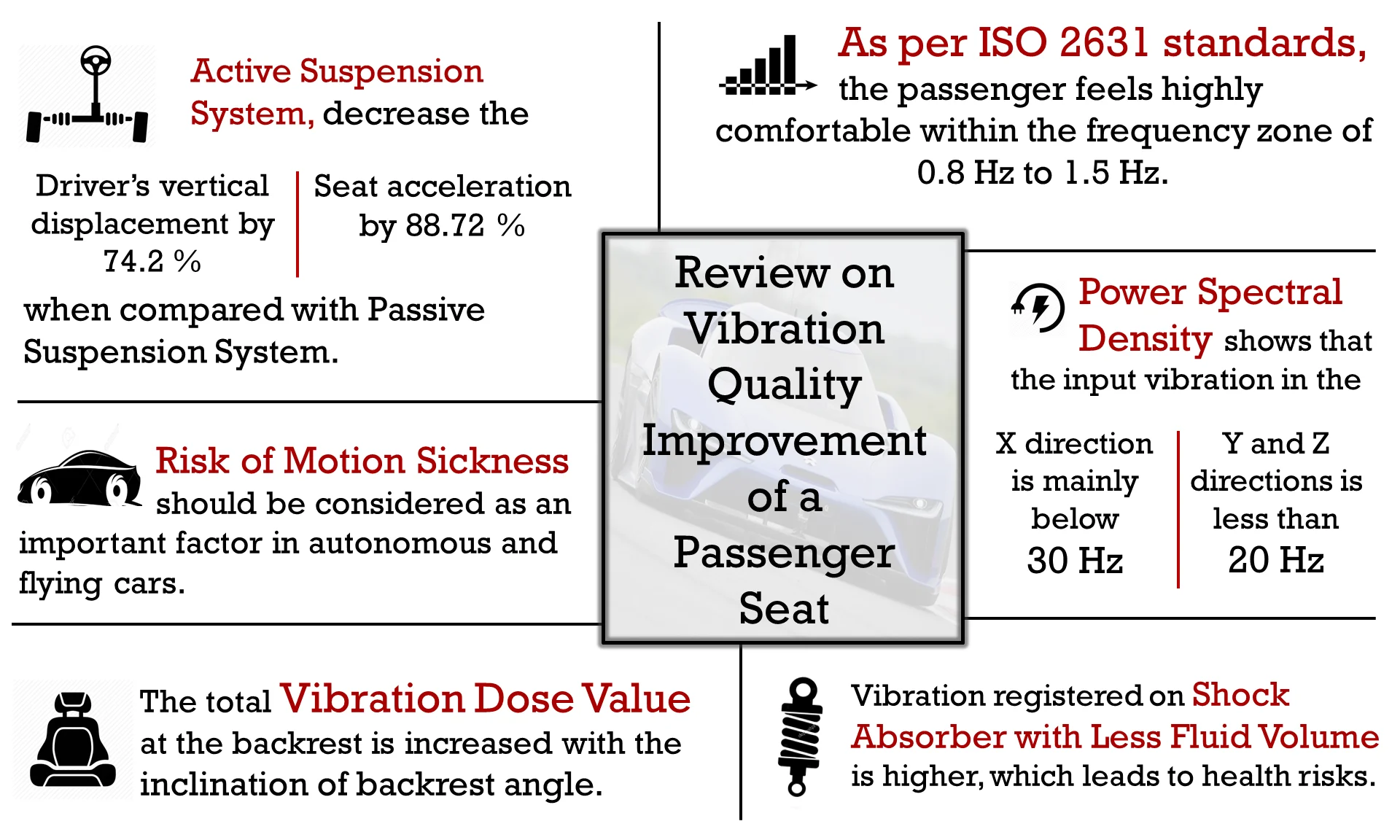
Highlights
- As per ISO 2631, passenger feels highly comfortable within frequency zone of 0.8Hz and 1.5Hz
- The input vibration in 𝑥-direction (longitudinal axis) is higher among the three directions
- Increasing foam thickness decreased the resonance frequency and related vertical transmissibility of vehicle seat cushion
- Active suspension has better potential than the passive suspension to increase comfort and road holding
- The total VDVs at the backrest is increased with the inclination of backrest angle
- Risk of motion sickness is to be reduced in autonomous and flying cars
1. Introduction
The present paper highlights the impact of vehicle vibration on human body, the parameters that are useful in vehicle seat design and dynamic evaluation of a vehicle seat. A large group of people who are exposed to general vibration includes car drivers, passengers, tram drivers and, building and road machinery operators. Vibration transmits into the human organism through vehicle seats via the pelvis, the back and lateral parts of the body as well as via the vehicle floor panel through feet. The evidence suggests that short time exposure to vibration causes small physiological effects such as an increase in muscle tension and increase in heart rate. Long term exposure causes effects such as disc to spine and effects on the female reproductive organs and digestive system peripheral veins.
There are different causes of vibration of a vehicle such as road roughness, whirling of shafts due to the cam forces, the instability of the engine and tensional fluctuations etc. [1]. The vibration of frequency in the range of 4 to 10 Hz creates pain in the chest. The range falls between 8 to 12 Hz procures headaches, eye strain and irritations in the intestines. Bladder pains are usually related to frequencies between 10 to 20 Hz [2]. The comfort of vehicle drivers is strongly related to various seat design factors, such as posture, range, ease of adjustments and ride vibration environment. Various approaches have been proposed during the past three decades to perform qualitative and quantitative measurements of pressure at the human-seat and human-bed interface. Majority of the early studies on the pressure distribution at the human-seat interface were performed to reduce the risks of skin ulceration or the pressure-sores among the paralyzed patients [3-5].
The influence of seat cushion designs on the seating comfort and driver posture has been evaluated through a number of subjective and objective studies. A study performed by Ng et al. reported that adequate driver-seat support can reduce the stresses in muscles of the back, buttocks, and legs caused by prolonged sitting during daily driving activities [6]. Accordingly, the expectations of users regarding the seat comfort are continuously increasing and manufacturers try to fulfil that with proper seat design in higher quality and comfort.
2. Seat design parameter overview
The most harmful category of vibration to people is those which the frequency is near to the free vibration pulsation of human organs. To reduce the vibration in the vehicle there are so many technologies and systems that are being used in the automobile industry. The suspension system, especially shock absorber is the most significant part of a vehicle for vibration control on the level of wave emission to vehicle-body and passengers. Fluid volume in the shock absorber cylinder and pressure distribution affects the efficiency of the suspension system. Design objectives such as maximum acceleration of vehicle seat and sprung mass, root mean square (RMS) weighted acceleration and sprung mass of a seat as per ISO 2631 standards, and seat movement are presented as design objectives for accessing comfort ability of the suspension.
Seat location can be considered significant because different seat locations such as driver’s, front and rear passenger seats absorb different values of vibration frequencies. While the searching space of the parameters is very huge, the solution space is very tight due to the presence of various restrictions. To go deep through this impact, we should consider about daily equivalent static compressive stress (Sed) that is a value for the assessment of health effects of general vibration according to the approaches from ISO 2631-5. The International Organization for Standardization and Technical Committee (ISO/TC) 108 has presented the standards ISO 2631 1-5; Mechanical vibration and shock – valuation of human exposure to whole-body vibration. It is generally appropriate in cases where adverse health effects in the lumbar spine are concerned.
Investigation of the different seating conditions and pressure distribution in the seat would be vital parameters to manufacture cushions for healthy travelling. Seat-interface pressure distribution has been used as a vital measure for discomfort prediction and a good indicator for reducing the subcutaneous stress [7]. The foam seat, as the main interface of human-automobile interaction, strongly affects sitting comfort. And the pressure distribution on the automobile seat has been identified as the most important objective parameter for discomfort prediction [8].
Over the seat cushion, the maximum pressure obtained is located right below the ischial tuberosity, and high pressures appear under the thigh and the knee popliteal fossa in the sitting position [9]. Contact pressure is known to be varying considerably in different sitting positions. The acceleration transmissibility can be used to identify, how the movement of the seat differs with the exciting frequency. Changes in the structure and properties of cushion material may affect its capacity for the oscillatory wave propagation and materials properties, thus all physical relations have to be considered [11-13]. Even, changes in body posture and seating condition would affect the transmission of vibration through a compliant seat [14]. Seating condition would be the main parameter that gives huge impact on vibration dose value (VDV). Appropriate seat position shall minimize encumbrance on spine, abdominal, pelvic and thigh muscles of the driver.
2.1. Design parameter considerations
As per ISO 2631 standards, the passenger feels highly comfortable if the weighted RMS acceleration is lower than 0.315 m/s2 and very uncomfortable above 1.25 m/s2. The frequency of vibration is proportional to the acceleration amplitude and in other words, the passenger feels comfortable within a frequency zone of 0.8 Hz and 1.5 Hz [15, 16]. Table 1 defines the ranges for comfort with the weighted RMS acceleration value.
For the sake of the investigation of human exposure to general vibration, the methods of enumerating vibration comprising multiple shocks in relation to human health in ISO 2631-5 have been used. Adversative effects on the lumbar spine are the dominating health risks. Therefore, the analysis is focused with the lumbar spine response. According to ISO 2631-5, assessment of adverse health effects at lifetime exposure are acceptable where Sed value is below 0.5 and very dangerous when it is above 0.8 [17].
The maximum pressure on the seat cushion is ranging from 51.52 kPa to 107.33 kPa, where the values are in the same order as that has been reported in previous studies. Brienza et al. said that an average maximum pressure is 76.2 kPa on one of his published work [18]. To inspect the effects of different seating conditions on the vibration absorbed by the seat backrest, it should be tested up to an inclination of an angle of 120°. While researchers used measurements of power spectral density (PSD) to determine the input vibration in the vehicle seat in x, y, z directions that impacts between ranges from 0 to 4×10-3 (m/s2)2 Hz in these three directions.
Table 1RMS acceleration ranges for comfort
Vibration (weighted RMS acceleration) | Reaction |
Less than 0.315 m/s² | Not uncomfortable |
0.315 to 0.63 m/s² | A little uncomfortable |
0.5 to 1 m/s² | Fairly uncomfortable |
0.8 to 1.6 m/s² | Uncomfortable |
1.25 to 2.5 m/s² | Very uncomfortable |
Greater than 2 m/s² | Extremely uncomfortable |
3. Recent developments in seat design research
A comfortable car seat shall provide with an adopting of correct posture, proper backrest from orthopedic perspective, and appropriate pressure distribution on the seat bottom and backrest surfaces. The shock absorber is a hydraulic device that contains fluid in the rod. Moreover, the volume of the fluid inside gives an impact on the amount of vibration or shock transferring to the passenger seat. Researchers tested the fluid volume from 50 % to 100 % and it was observed that the RMS values of the vibration signal with shock absorber with less fluid volume are greater. As it is seen the vibrations of a vehicle with shock absorber with less fluid volume have many more frequency components in a wider range of frequency band [19].
The measured results of daily equivalent static compressive stress for the shock absorber contains 100 % of fluid is Sed = 0.32142 and for 50 % of fluid is Sed = 0.7990. These results are observed only for the vertical vibration and show a huge effect of damping parameters on of human exposure to vibration in passenger car [19]. According to ISO 2631-5, evaluation of adverse health effect at lifetime exposure is very dangerous when it is more than 0.8. Through these values, it can be observed when the percentage of fluid in the shock absorber goes down the risk of health to the passengers increase.
Active and passive suspension systems have shown a huge difference in the experimented values on the vital parameters of vibration. From the earlier researches, it can be seen that the decrease of the driver’s peak vertical displacement is approximately 74.2 % and seat acceleration and sprung mass vertical acceleration is decreased by 88.72 % and 88.17 % respectively in active suspension when compared with passive suspension. Also, the vertical weighted RMS acceleration of seat is decreased from 0.3032 m/s2 to 0.0534 m/s2 in the active suspension system that is highly comfortable for the passenger as mentioned above. The research further reveals active suspension has better values in comfort zone [20].
Seating cushion and sitting condition are the other important parameters for designing the vehicle seat. In a seated upright posture, the maximum pressures occur inferior to the ischial tuberosity. Therefore, the vehicle seat cushion is used to lower the maximum seating pressure on buttocks while reducing the transmission of vibration to the human body. Ebe K. and Griffin M. J. found that increasing foam thickness from 50 to 120 mm decreased the resonance frequency and the related vertical transmissibility of a vehicle seat cushion, with a more expectable effect [21]. Over the frequency range 1-20 Hz, the damping improved between 13 % and 24 % when the thickness reduced from 100 mm to 60 mm. Changes in foam thickness made quantitative variations in the damping that was linearly proportional to the thickness of the foam [22]. The magnitude of a vibration transmitted to the subject or the acceleration level at the interface is strongly dependent upon the viscoelastic properties of the seat.
Cushion’s both hyper-elastic and viscoelastic behaviours could be effective in reducing the amplitude of varying maximum contact pressure, especially for the frequency ranging between 10-20 Hz, which belong to the frequency range of vibration created mostly by vehicles and aircraft [23]. A vibration-reducing material outwardly disperses the energy caused by vibrations, by reducing the amplitude and frequency of the vibrational waves, usually in the form of thermal energy. Finally, it should perform over a wide range of frequencies and temperatures, and withstand the conditions of a harsh industrial environment.
Input vibration to the seat in all direction to be examined before investigating the seating posture and backrest angle. The Society of Automotive Engineers (SAE) defines the axis system through SAE J670 – Vehicle Dynamics Terminology and it shows directions x, y and z are specifying longitudinal axis (direction of wheel heading), lateral axis and vertical axis respectively [24]. PSD shows that the input vibration in the x-direction is mainly below 30 Hz while the input vibration in both the y- and z-directions is less than 20 Hz in the vehicle seat. The result depicts the input vibration in x-direction is higher among the three directions. Vehicle seats should have the ability to reduce the vibration at frequencies coinciding with the resonance frequencies of the human body to avoid discomfort or health issues due to vibration [25].
An inclination of backrest gives a big impact on VDV, is the parameter that combines the magnitude of vibration and the time for which it occurs. On average, the value of VDV in the x-direction is increased by around 90 % and in the z-direction is decreased by around 20 % at the backrest when the backrest angle inclined from 90° to 120°[25]. Statistically significant differences in the VDVs between the different conditions were found in all directions except y-direction, where there were no major differences from the inclement of backrest angle. Research result proved that there was a significant impact on the total VDVs observed on the seat rather than in an individual direction. Fairley T. showed a major effect of backrest angle on the vibration transmissibility to vehicle seat [26, 27]. As a result, the total VDVs at the backrest is increased with the increase in the inclination of backrest. Therefore, using less inclination of backrest gives a healthier ride.
4. Future directions in vehicle seat design
The future of the automobile seat design is complex, with a wide list of requirements to fulfil. As luxury vehicles, autonomous vehicles and even flying cars enter the market, this complex list of problems will elongate. To cater to those needs, the future of vehicle seat design must be enhanced in various directions. Analysis of body pressure distribution (BPD) at the human-seat contact interface would help in the proper justification of the comfort level of the new seat designs in a virtual environment by using a digitized human model also known as a manikin [28].
Material considerations can also be taken into account in order to provide the cushion vibration absorption, breathability and stiffness to the seat model. Currently, Polyurethane Foam is the main cushion material choice due to its lightweight and ease of manufacturability characteristics [28]. Another option of material is Alcantara, which is a microfiber material that is composed of about 68 % polyester and 32 % polyurethane and particularly resistant to staining and vibration absorbing. Nowadays, luxury and performance cars are all over the world including Lamborghini, uses Alcantara for their seats and interior designs. Manufacturers should consider this kind of materials at affordable prices for the normal passenger vehicle [29].
Autonomous driving is no longer a futuristic vision. According to Business Insider fully autonomous cars will debut on the roads in 2019 and by 2020 there will be 10 million road-registered cars with self-driving features [30]. Furthermore, relevant features of autonomous vehicle seats are to be identified, investigated and visualized. The word “driver seat” does not even exists in these cars and have face-to-face seat arrangement, which creates more vibration because of the instability, and requires new thinking about safety feature. Risk of motion sickness is an important factor that is to be reduced. Research shows that it is possible to have a radically different driving posture was maintaining comfort [31], but there is still significant research needed to be completed in order to establish the requirements and objectives of the necessary seat design for future vehicles.
5. Conclusions
The objective of this paper is to investigate the problems caused by vibration to the passengers and the recent development of vehicle seat design which are available in current literature. Moreover, it gives a general idea about the future direction for unsolved problems that arise in practice. It was analysed the suspension system, seating condition, sitting posture, cushion materials and future trends as well. The presented results show that vibration registered on shock absorber with less fluid are higher and also it has higher Sed value, which leads to health risks. Measured values indicate that active suspension system has better potential than the passive suspension system to increase both comfort and road holding. The inclination of backrest gives a huge impact on VDV and when the angle of inclination increases it absorbs a high level of vibration. These parameters have been regarded as the most important objectives for discomfort prediction. The future researches should concern about autonomous and flying cars, which are going to dominate the world in future. Thus, this paper summarises the effects and design parameters on vibration and the methods of reducing the transmission of vibration at a certain frequency ranges in order to improve the comfortable and healthy riding.
References
-
Giri N. K. Automobile Mechanics. 7th Ed, Khanna Publishers, Delhi, p. 466-491.
-
Katu U., Desavale R., Kanai R. Effect of vehicle vibration on human body – RIT experience. 11th National Conference on Machines and Mechanisms, 2003.
-
Treaster D. Measurement of seat pressure distribution. Human Factors, Vol. 29, Issue 5, 1987, p. 563-575.
-
Key A. G., Manley M. T., Wakefield E. Pressure redistribution in wheelchair cushion for paraplegics: its application and evaluation. Paraplegia, Vol. 16, 1979, p. 403-412.
-
Makhsous M., Rowles D. M., Rymer W. Z., Bankard J., Nam E. K., Chen D., Lin F. Periodically relieving ischial sitting load to decrease the risk of pressure ulcers. Archives of Physical Medicine and Rehabilitation, Vol. 88, Issue 7, 2007, p. 862-870.
-
Ng D., Cassar T., Gross C. M. Evaluation of an intelligent seat system. Applied Ergonomics, Vol. 26, Issue 2, 1995, p. 109-116.
-
Verver M., Hoof J., Oomens J., Wismans M., Baaijens T. A finite element model of the human buttocks for prediction of seat pressure distributions. Computer Methods in Biomechanics and Biomedical Engineering, Vol. 7, Issue 4, 2004, p. 193-203.
-
Nicol K., Rusteberg D. Pressure distribution on mattresses. Journal of Biomechanics, Vol. 26, Issue 12, 1993, p. 1479-1486.
-
Huang S., Zhang Z., Xu Z., He Y. Modeling of human model for static pressure distribution prediction. International Journal of Industrial Ergonomics, Vol. 50, 2015, p. 186-195.
-
Wu X., Rakheja S., Boileau E. Distribution of human-seat interface pressure on a soft automotive seat under vertical vibration. International Journal of Industrial Ergonomics, Vol. 24, 1999, p. 545-557.
-
Folęga P., Siwiec G. Numerical analysis of selected materials for flex splines. Archives of Metallurgy and Materials, Vol. 57, Issue 1, 2012, p. 185-191.
-
Konieczny Burdzik L. R., Lazarz B. Analysis of properties of automotive vehicle suspension arm depending on different materials used in the MSC. Adams environment. Archives of Materials Science and Engineering, Vol. 58, Issue 2, 2012, p. 171-176.
-
Mencik J. Determination of parameters of visco-elastic materials by instrumented indentation. Part 3: rheological model and other characteristics. Chemicke Listy, Vol. 104, 2010, p. 275-278.
-
Mansfield N. J., Holmlund P., Lundstrom R., Lenzunic P., Nataletti P. Effect of vibration magnitude, vibration spectrum and muscle tension on apparent mass and cross axis transfer functions during whole-body vibration exposure. Journal of Biomechanics, Vol. 39, 2006, p. 3062-3070.
-
Wong J. Y. Theory of Ground Vehicles. John Wiley and Sons Inc., New York, 1998.
-
Griffin M. J. Handbook of Human Vibration. Academic Press, New York, 2003.
-
ISO 2631-1: 1997, Mechanical Vibration and Shock – Evaluation of Human Exposure to Whole-Body Vibration. International Organization for Standardization, Switzerland, 1997.
-
Brienza D., Chung K., Brubaker C., Wang J., Karg T., And Lin C. A system for the analysis of seat support surfaces using surface shape control and simultaneous measurement of applied pressures. IEEE Transactions on Rehabilitation Engineering, Vol. 4, Issue 2, 1996, p. 103-113.
-
Burdzik R., Konieczny L. Research on structure, propagation and exposure to general vibration in passenger car for different damping parameters. Journal of Vibroengineering, Vol. 15, Issue 4, 2013, p. 1680-1688.
-
Shirahatt A. Optimal design of passenger car suspension for ride and road holding. Journal of the Brazilian Society of Mechanical Sciences and Engineering, Vol. 66, Issue 76, 2008, p. 30-1.
-
Ebe K., Griffin M. J. Qualitative models of seat discomfort including static and dynamic factors. Ergonomics, Vol. 43, 2000, p. 771-790.
-
Zhang X., Michael Y., Griffin M. J. Transmission of vertical vibration through a seat: effect of thickness of foam cushions at the seat pan and the backrest. International Journal of Industrial Ergonomics, Vol. 48, 2015, p. 36-45.
-
Chak T., Wai C., Chi Pont T. Finite element analysis of contact pressures between seat cushion and human buttock-thigh tissue. Scientific Research, Vol. 2, Issue 9, 2010, p. 721-726.
-
SAE J670 – Vehicle Dynamics Terminology. Vehicle Dynamics Standards Committee, SAE International, 2008, p. 73.
-
Nawayseh N. Effect of the seating condition on the transmission of vibration through the seat pan and backrest. International Journal of Industrial Ergonomics, Vol. 45, 2015, p. 82-90.
-
Fairley T. Predicting the Dynamic Performance of Seats. Ph.D. Thesis, University of Southampton, 1986.
-
Fairley T. Predicting seat transmissibilities: the effect of the legs. Proceeding of Joint French-English Meeting, 1988.
-
Mishra L., Singh H. Re-Design of Drivers’ Car Seat Using Three Dimensional Reverse Engineering. Bachler Thesis, National Institute of Technology Rourkela, 2014.
-
What Does It Mean to Have Alcantara Seats? Lamborghini Palm Beach, 2018, https://www.lamborghinipalmbeach.com/blog/what-is-alcantara.
-
10 Million Self-Driving Cars Will Be on the Road By 2020. Business Insider, 2016, https://www.businessinsider.com/report-10-million-self-driving-cars-will-be-on-the-road-by-2020-2015-5-6.
-
Smith J., Mansfield N., Gyi D., Pagett M., Bateman B. Driving performance and driver discomfort in an elevated and standard driving position during a driving simulation. Applied Ergonomics, Vol. 49, 2015, p. 25-33.