Abstract
The use of ultrasound in synthesis of polyvinylpyrrolidone copolymers with methacrylic esters as well as in the presence of calcium-containing mineral fillers has been researched. The influence of ultrasound on the polyvinylpyrrolidone destruction is determined. The activating impact of ultrasound on initiation of polymerization is confirmed. The ultrasound application significantly intensifies the process of porous composites obtaining that based on polymer-monomer compositions and calcium-containing mineral fillers including nanosized. The developed (nano)composites can be used in medicine to replace damaged bone tissue.
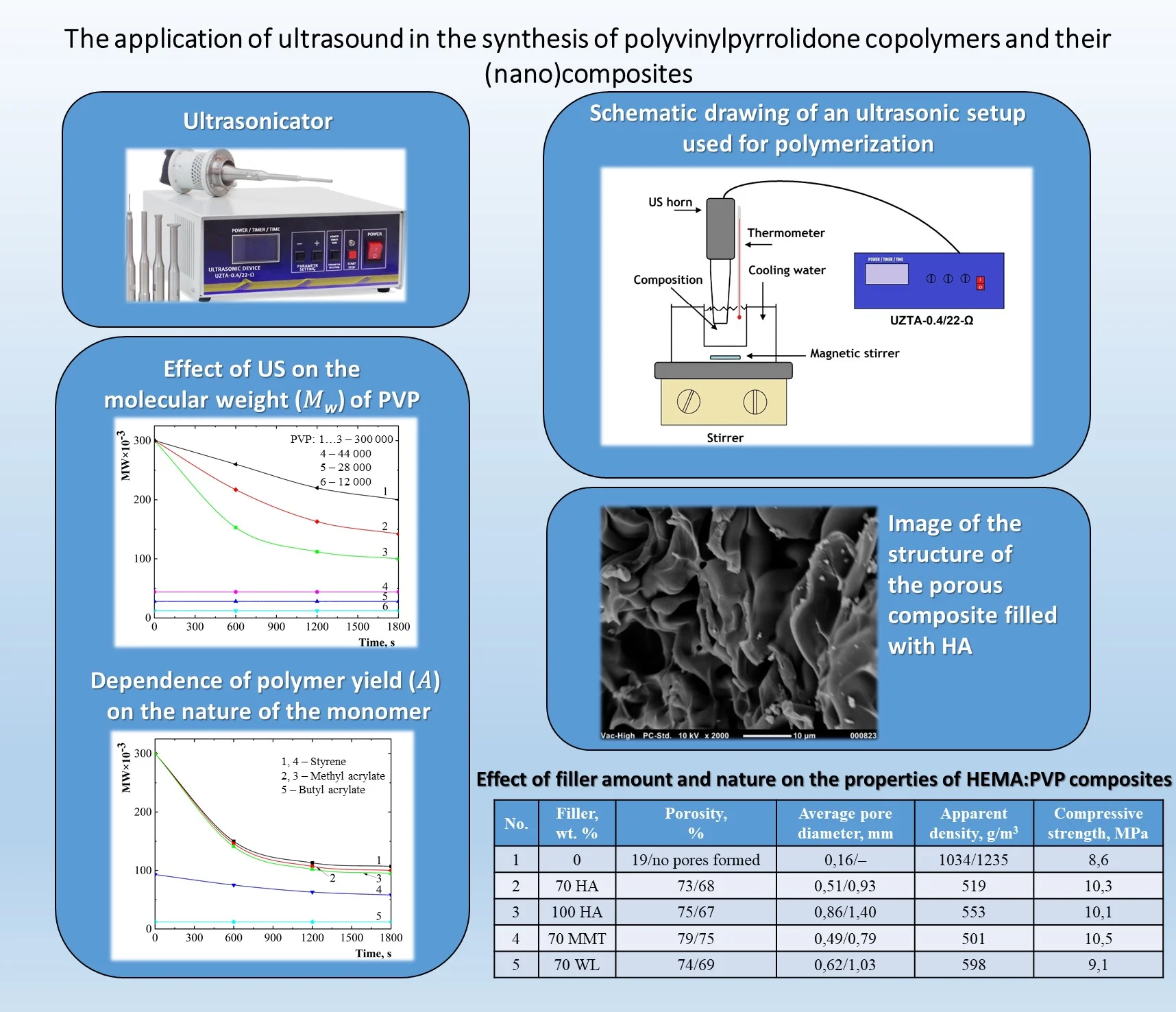
Highlights
- Ultrasound (US) activates the polymerization of monomers of various types in the presence of polyvinylpyrrolidone.
- US significantly enhances the formation of porous composites based on polyvinylpyrrolidone copolymers and calcium-containing fillers.
- The polymerization rate of monomer-polymeric compositions depends on the type of calcium-containing filler (hydroxyapatite, montmorillonite, wollastonite).
- The developed nanocomposites based on polyvinylpyrrolidone copolymers and silver nanoparticles exhibit fungicidal properties and potential for osteogenesis applications.
1. Introduction
In the chemical industry ultrasound (US) energy – acoustic vibrations with frequencies of 20 kHz or higher – is frequently utilized to enhance and intensify various technological processes [1-4]. However, the complexity of the US’s mechanism of action makes it challenging to interpret the phenomena and processes that occur during its application. In each specific case, detailed studies are required to investigate the impact of US on both the chemical reaction pathways and the structure and properties of the synthesized substances and materials. Under the influence of US, the significant differences in the effects of various factors, particularly temperature and atmospheric oxygen, during chemical transformations were observed [1-4]. Reactions often proceed at high rates even at relatively low temperatures. As a result, there is a significant interest in studying polymerization in an ultrasonic field, as this can simplify the polymerization technology and reduce the temperature-time conditions required for producing polymers and composites. Moreover, it opens up broad possibilities for imparting additional, sometimes unique, properties to polymers and composites based on them.
Polyvinylpyrrolidone (PVP) copolymers with (meth)acrylic esters are widely and effectively used in various aspects of human life, particularly in medicine, biotechnology, and pharmacy [5, 6]. These copolymers are utilized in the production of hydrogel contact lenses, artificial lenses, dental materials, dialysis membranes, granular and film systems for controlled drug release, osteoplastic composites for bone tissue repair, etc. [7-9]. These copolymers are synthesized through block, solution, suspension, and emulsion polymerization methods [5]. In some cases, it is anticipated that the use of US may not only intensify polymerization reactions but also modify the structure and properties of the resulting polymers and their composites.
The aim of this study was to investigate the influence of US on the polymerization process of homogeneous and heterogeneous compositions of (meth)acrylic esters with polyvinylpyrrolidone and to explore the potential of using US to fabricate (nano)composites based on these materials.
2. Experimental part
For the presented studies, PVP from AppliChem GmbH with a molecular weight ranging from 12×103 to 360×103 was used. The following monomers were utilized: 2-Hydroxyethyl methacrylate (HEMA) CAS No 868-77-9 Bisomer™ (purified by vacuum distillation, residual pressure 130 N/m2, boiling point = 351 K); methyl acrylate (MA) CAS No 96-33-3 Merck™, butyl acrylate (BA) CAS No 141-32-2 Merck™ (both monomers were washed with 5 % Na2CO3, dried with Na2SO4 and Na2O zeolite, and twice distilled using a distillation column); styrene (St) Merck™ (washed with 5 % NaHSO3, 10 % NaOH, distilled water, dried with CaCl2 and Na2O zeolite, distilled under a residual pressure of 40 mm Hg, 333 K. As fillers for composites, the following were used: Hydroxyapatite (HA) Ca10-x(PO4)6(OH)2 CAS No 1306-06-5 Acros OrganicsTM, Montmorillonite (MMT) (Na, Ca)0,3(Al, Mg)2[Si4O10](OH)2∙nH2O K-10 surface area 220-270 m2/g CAS No 1318-93-0 Sigma-Aldrich™, Wollastonite (WL) CaSiO3 CAS No 1344-95-2 Sigma-Aldrich™.
The destruction of polymers under US was studied by measuring changes in their molecular weight using viscometry. The rate of polymerization was assessed by evaluating the amount of unreacted monomer through chemical methods [10].
US studies were conducted using an ultrasonic unit UZTA-0.4/22-Ω, with a frequency of mechanical oscillations of 22 ± 1,65 kHz and a maximum power of 400 VA. The power regulation range is 30 to 100 %. The diameter ratio of the magnetostrictor to the reactor is 0,5. The composition for studying was placed into the reactor, which is equipped with a thermostatic jacket. The magnetostrictor was then inserted into the reactor with the composition, the unit was activated, and the desired US intensity was set.
The structure of the composites was examined using a JEOL JEM 200 CX transmission electron microscope (TEM). Compressive strength was measured with a Kimura RT-601U universal testing machine, capable of applying forces up to 10 kN. Composite samples with a diameter of 15 mm and a height of 10 mm were tested. Compression forces were recorded at 10 % deformation (P10, H). Compressive strength was calculated using the formula P10/S, where S is the cross-sectional area of the sample in m².
The average pore diameter () of the samples was determined by measuring the sizes of 100 to 150 pores using an Sigeta МВ-130 microscope. The total porosity and density of the composites were assessed using the Liquid-Liquid Displacement Porosimetry method as described in [11].
3. Results and discussion
The polymerization of vinyl monomers in the presence of PVP under the influence of US was conducted in homogeneous systems, where PVP was dissolved in the monomer or its solution, as well as in heterogeneous systems, where the monomer formed a phase on the boundary with the PVP solution. Taking into account that the polymerization was performed under US influence, it was crucial to examine its effect on the components of the reaction mixture, especially the polymer matrix. According to the literature sources [1, 12, 13], polymer matrices can undergo destruction under US, leading to a reduction in molecular mass and the formation of radicals and macroradicals. These (macro)radicals can serve as active centers for following graft or block copolymerization [12].
The destruction of polymer matrix under the influence of US was studied by monitoring changes in their molecular weight. PVP with various molecular weights – 360×103, 44×103, 28×103, and 12×103 were used for the research. Aqueous polymer solutions with a concentration of 1 % were subjected to US at an intensity ranging from 1 to 5×104 W/m2 for 30 minutes.
As shown in Fig. 1, ultrasonic treatment of a PVP solution with a molecular weight of 360×103 leads to a reduction in its molecular weight. The character of the curves resembles those of mechanical destruction, where the molecular weight decreases to a certain threshold value [14]. The most intense macromolecule destruction occurs within the first 10 min, with the rate of destruction increasing with the length of the polymer macromolecules. At an US intensity of less than 1∙104 W/m², destruction of polymer proceeds at a much slower rate. Similar destruction regularities were observed with US exposure to dilute solutions of polyvinyl acetate, nitrocellulose, rubber, and polyacrylamide [14].
Fig. 1Effect of US on the molecular weight (MW) of PVP: CPVP= 1 %; T= 293 K; I= 10-4 W/m2: 1 – 1; 2 – 3; 3…6 – 5; MWPVP×10-3: 1…3 – 360; 4 – 44; 5 – 28; 6 – 12
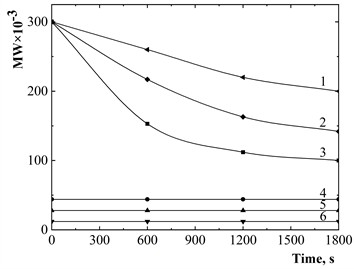
Fig. 2Dependence of polymer yield (A) on the nature of the monomer: MWPVP= 28×103; T= 293 K; I= 5×104 W/m2; CM, mol/dm3: 1, 2, 4, 5 – 1; 3 – 0,4; monomer: 1, 4 – styrene; 2, 3 – methyl acrylate; 5 – butyl acrylate

The degradation susceptibility under US treatment decreases with a reduction in the molecular weight of the polymer matrix (Fig. 1). PVP with molecular weights of 28∙10³ and 12∙10³ exhibits minimal changes even after prolonged US exposure. This suggests that longer polymer chains are primarily prone to destruction by US.
Polymerization in the presence of PVP, influenced by US as an active factor affecting the interface and surface activation, was conducted using several hydrophobic (meth)acrylic monomers and styrene. The experiments were performed at an irradiation intensity of (1–5)×104 W/m2 and a temperature of 293 K in the presence of air, without additional polymerization initiators. The results revealed a consistent pattern among the studied monomers: all polymerize in the presence of PVP under US without an induction period. The rate of polymerization increases in the order butyl acrylate < methyl acrylate < styrene (Fig. 2).
Preliminary studies on the effect of PVP concentration on the kinetics of styrene polymerization revealed that PVP influences initiation and accelerates polymer formation. The polymerization rate exhibits a pronounced peak with a maximum at a PVP concentration of approximately 1 wt. % in the aqueous phase [12]. As the molecular weight of PVP increases, the polymerization rate decreases (Table 1), primarily due to the increased viscosity of PVP aqueous solutions. Additionally, the nature of the polymer matrix significantly impacts the kinetics of polymerization. Although PEG ( 10×103) and PVP ( 12×103) have similar molecular weights, their effects on polymerization differ significantly. PVP considerably accelerates the process, whereas PEG has only a negligible impact on the polymerization rate.
The threshold intensity for US-assisted polymerization of styrene identified in the studies is 1×104 W/m2 (Table 1). Above this intensity, the polymerization rate increases proportionally with the US intensity up to the maximum value used in the experiments (5×104 W/m2). Kinetic studies indicate that the initiation and progression of the reaction in the US field are influenced by several factors, with the primary ones being the energy of the US and the intermolecular interactions between monomer molecules and PVP macromolecules at the phase boundary. Considering that polymerization occurs at the phase boundary, it can be predicted that one of the primary reasons for the enhanced process is the high dispersion of the reaction system achieved through US. This is supported by the observation that homogeneous systems polymerize much more slowly and require the additional introduction of an initiator into the original composition. For example, during the polymerization of styrene in a PVP composition (with a 1 % solution of PVP at a 7:1 mass ratio), a polymer yield of over 80 % can be achieved in 30 minutes. In contrast, for HEMA-PVP compositions with the same component ratio and in the presence of a radical polymerization initiator, the polymer yield after the same period is only 16 % [12].
Table 1Dependence of the polymerization rate of styrene (St) on the nature of the polymer matrix (PM) and US intensity (I) (St: aqueous solution of PM = 1:7 wt. parts, [PM] = 1 wt. %, T= 293 K, I= 5×104 W/m²)
×10-3 | Polymerization rate, ×104, mol/(dm3∙s) |
12 | 9,5 |
28 | 5,9/1,7 |
3,6 ( 3×104 W/m2) 2,2 ( 2×104 W/m2) 0,8 ( 1×104 W/m2) 0,7 ( 5×103 W/m2) | |
44* | 4,1 |
90** | 0,5 |
In the denominator for the composition without PVP; PM: * – Polyvinyl alcohol, ** – PEG |
The established effects of US on the polymerization of vinyl monomer compositions in the presence of PVP were also applied to the polymerization of HEMA compositions with calcium-containing mineral fillers, leading to the preparation of (nano)composites. These composites, when given a porous structure, are effective osteoplastic materials for replacing damaged bone tissue [3, 15].
Studies has shown that homopolymerization of HEMA does not occur under homogeneous conditions (Table 2). However, in the presence of PVP without mineral filler, the compositions polymerize at a moderate rate.
Table 2The influence of US on the polymerization rate of compositions (1 wt. % benzoyl peroxide, [AgNO₃] = 1 wt. %, T= 293 K, I= 5×104 W/m²)
The composition of the mixture, mass parts. | Polymerization rate, ×103 mol/(dm³∙s) | Maximum monomer conversion, % | Time to reach maximum conversion, s | ||
HЕМА | PVP | Filler | |||
10 | 0 | 0 | 0 | – | – |
7 | 3 | 0 | 22 | 90 | 190 |
7 | 3 | 7 HA | 104/4, 2* | 94 | 40 |
7 | 3 | 7 WL | 118 | 96 | 35 |
7 | 3 | 7 MMT | 166 | 95 | 25 |
* in the denominator – without US, 333 K |
Mineral fillers form a heterogeneous environment within the compositions, leading to rapid polymerization and simultaneous foaming under the influence of US. This effect offers significant technical and economic advantages in the development of the process for producing porous composites. The use of US allows conducting the polymerization at room temperature, with an initial polymerization rate more than 20 times higher than that of polymerization without US, even when performed at a higher temperature (Table 1). The time required to reach the maximum monomer conversion is reduced from 2-3 hours to just 1-3 minutes.
A comparison of the polymerization rates of various compositions based on the nature of the filler revealed that compositions containing montmorillonite and wollastonite exhibit higher reactivity than those with hydroxyapatite as the mineral filler. We believe the high reactivity of compositions with montmorillonite is due to its complex surface structure, which contains both negative and positive charges, as well as metal salts with variable oxidation states. This unique structure allows montmorillonite to act as a catalyst for ionic polymerization [15].
The use of US enables conducting the polymerization at room temperature, with a significantly higher polymerization rate compared to polymerization without US, even at 333 K (Table 2). As a result, polymerization in the US field achieves a high degree of monomer conversion to polymer in a relatively short time, greatly intensifying the process of producing porous composites and improving productivity.
The inclusion of silver salts in the initial composition enables the synthesis of silver nanoparticles within the composite structure, imparting fungicidal properties to the composites [16]. Composites produced under the influence of US exhibit a distinctly porous structure, as confirmed by transmission electron microscopy images (Fig. 3).
Fig. 3Image of the structure of the porous composite filled with HA
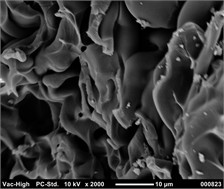
The key properties of porous composites, depending on the initial composition, as well as the nature and quantity of the filler, are presented in Table 3. While it was not possible to obtain a porous material without US in the absence of HA; US treatment resulted in the formation of porous material even without filler, albeit with low porosity (Table 3, item 1).
Table 3Effect of filler amount and nature on the properties of composites (НEMA:PVP = 70:30 wt. %, T= 298 K, I= 5×104 W/m², synthesis duration 180 s)
No. | Filler, wt. % | Porosity, % | Average pore diameter, mm | Apparent density, kg/m3 | Compressive strength, MPa |
1 | 0 | 19/no pores formed | 0,16/– | 1034/1235 | 8,6 |
2 | 70 HA | 73/68 | 0,51/0,93 | 519 | 10,3 |
3 | 100 HA | 75/67 | 0,86/1,40 | 553 | 10,1 |
4 | 70 MMT | 79/75 | 0,49/0,79 | 501 | 10,5 |
5 | 70 WL | 74/69 | 0,62/1,03 | 598 | 9,1 |
In the denominator, without US, = 343 K; the composition additionally contains 10 wt. % of the foaming agent cyclopentane. |
In all cases, US promotes the formation of more porous materials, although with smaller pore diameters. With the same filler content, composites containing MMT exhibit the smallest average pore size. In contrast, composites with WL have the largest pore diameter and the lowest mechanical properties.
4. Conclusions
The activating effect of US on the initiation of polymerization in methacrylic ester compositions with PVP has been demonstrated. In homogeneous compositions, polymerization in the presence of US occurs only when polymerization initiators are added. However, monomers that form a phase boundary with an aqueous PVP solution can be polymerized under US without the need for initiators, even under mild conditions. US significantly enhances the process of producing porous composites based on PVP monomer compositions and calcium-containing mineral fillers, such as hydroxyapatite, montmorillonite, and wollastonite. The nature of the calcium-containing filler significantly influences the polymerization rate. The developed (nano)composites, which incorporate silver nanoparticles, exhibit fungicidal properties and hold potential for use in osteogenesis applications.
References
-
M. Ashokkumar, Handbook of Ultrasonics and Sonochemistry. Singapore: Springer Singapore, 2016, https://doi.org/10.1007/978-981-287-278-4
-
D. Peters, “Ultrasound in materials chemistry,” Journal of Materials Chemistry, Vol. 6, No. 10, p. 1605, Jan. 1996, https://doi.org/10.1039/jm9960601605
-
V. Skorokhoda, I. Dziaman, G. Dudok, T. Skorokhoda, J. M. Bratychak, and N. Semenyuk, “The Ultrasonic effect on obtaining and properties of osteoplastic porous composites,” Chemistry and Chemical Technology, Vol. 13, No. 4, pp. 429–435, Dec. 2019, https://doi.org/10.23939/chcht13.04.429
-
S. V. Sancheti and P. R. Gogate, “A review of engineering aspects of intensification of chemical synthesis using ultrasound,” Ultrasonics Sonochemistry, Vol. 36, pp. 527–543, May 2017, https://doi.org/10.1016/j.ultsonch.2016.08.009
-
V. Y. Skorokhoda, O. V. Suberlyak, N. B. Semenyuk, and Y. Y. Melnyk, Biomedical materials based on polyvinylpyrrolidone (co)polymers. (in Ukrainian), Lviv, Ukraine: Publishing House of Lviv Polytechnic National University, 2015.
-
K. Sadasivuni, D. Ponnamma, M. Rajan, B. Ahmed, and M. Al-Maadeed, “Polymer Nanocomposites in Biomedical Engineering,” in Lecture Notes in Bioengineering, Cham: Springer International Publishing, 2019, https://doi.org/10.1007/978-3-030-04741-2
-
Y. Melnyk, Y. Stetsyshyn, V. Skorokhoda, and Y. Nastishin, “Polyvinylpyrrolidone-graft-poly(2-hydroxyethylmethacrylate) hydrogel membranes for encapsulated forms of drugs,” Journal of Polymer Research, Vol. 27, No. 11, pp. 1–11, Nov. 2020, https://doi.org/10.1007/s10965-020-02335-7
-
V. Skorokhoda, N. Semenyuk, I. Dziaman, K. Levytska, and G. Dudok, “The influence of the nature of a calcium-containing filler on the preparation and properties of osteoplastic porous composites,” (in Ukrainian), Voprosy Khimii i Khimicheskoi Tekhnologii, Vol. 2, pp. 101–108, 2018.
-
V. Skorokhoda, Y. Melnyk, N. Semenyuk, N. Ortynska, and O. Suberlyak, “Film hydrogels on the basis of polyvinylpyrrolidone copolymers with regulated sorption-desorption characteristics,” Chemistry and Chemical Technology, Vol. 11, No. 2, pp. 171–174, Jun. 2017, https://doi.org/10.23939/chcht11.02.171
-
V. Selyakova and Y. Kashevarova, Methods of Analysis of Acrylates and Methacrylates. (in Russian), Moscow, Russia: Khimiya, 1982.
-
M. B. Tanis-Kanbur, R. I. Peinador, J. I. Calvo, A. Hernández, and J. W. Chew, “Porosimetric membrane characterization techniques: A review,” Journal of Membrane Science, Vol. 619, No. 3, p. 118750, Feb. 2021, https://doi.org/10.1016/j.memsci.2020.118750
-
V. Skorokhoda, Y. Melnyk, N. Semenyuk, and O. Suberlyak, “Obtaining peculiarities and properties of PVP copolymers with hydrophobic vinyl monomers,” Chemistry and Chemical Technology, Vol. 9, No. 1, pp. 55–59, 2015.
-
M. Kubo, T. Kondo, H. Matsui, N. Shibasaki-Kitakawa, and T. Yonemoto, “Control of molecular weight distribution in synthesis of poly(2-hydroxyethyl methacrylate) using ultrasonic irradiation,” Ultrasonics Sonochemistry, Vol. 40, pp. 736–741, Jan. 2018, https://doi.org/10.1016/j.ultsonch.2017.08.011
-
A. Weissler, “Cavitation in ultrasonic depolymerisation,” Journal of the Acoustical Society of America, Vol. 23, No. 3, pp. 370–373, 1991.
-
V. Skorokhoda, N. Semenyuk, I. Dziaman, and O. Suberlyak, “Mineral filled porous composites based on polyvinylpyrrolidone copolymers with bactericidal properties,” Chemistry and Chemical Technology, Vol. 10, No. 2, pp. 187–192, Jun. 2016, https://doi.org/10.23939/chcht10.02.187
-
V. J. Skorokhoda, N. B. Semenyuk, G. D. Dudok, and H. V. Kysil, “Silver-containing osteoplastic nanocomposites based on polyvinylpyrrolidone copolymers,” (in Ukrainian), Voprosy Khimii i Khimicheskoi Tekhnologii, Vol. 3, No. 3, pp. 67–73, Jun. 2022, https://doi.org/10.32434/0321-4095-2022-142-3-67-73
About this article
The authors have not disclosed any funding.
The datasets generated during and/or analyzed during the current study are available from the corresponding author on reasonable request.
The authors declare that they have no conflict of interest.