Abstract
The transition to electric vehicles (EVs) has heightened the significance of secondary noise sources, such as buzz, squeak, and rattle (BSR), which can detract from vehicle quality and customer satisfaction. Among these, body squeaking noise, particularly during the electro-coating (e-coating) process, presents a notable challenge due to its impact on vehicle acoustic comfort. Despite advancements in automotive noise, vibration, and harshness (NVH) control, the specific viscoelastic mechanisms contributing to squeaking noise under varying thermal and mechanical conditions remain inadequately understood. This study addresses these gaps by employing the Maxwell Viscoelastic Model to investigate the time-dependent mechanical behavior of body-in-white (BIW) coatings during the e-coating process. Key finding indicates that the glass transition temperature (Tg) of the coating material plays a critical role in noise occurrence, particularly under high-temperature conditions and road-induced vibrations. This research contributes novel insights to the field by integrating theoretical analysis with empirical data to enhance the understanding of viscoelastic properties in automotive coatings.
1. Introduction
In electric vehicles (EVs), squeak and rattle (S&R) noises are more prominent due to the absence of engine sounds, raising consumer expectations for noise control and leading to increased warranty claims [1]. Body squeaking is particularly concerning, as it often stems from inadequate design and manufacturing quality controls, making source identification challenging, especially in fully assembled vehicles [2]. Establishing robust manufacturing processes is essential to eliminate body squeaking.
Previous research emphasizes the importance of addressing S&R issues to improve customer satisfaction and vehicle quality. For identification and resolution of car body noises, Mainkar et al. [2] outlined methods for identifying and resolving body noises, noting that improper oven temperature control can lead to thermal stresses and buckling in the body-in-white (BIW), resulting in squeaks. An efficient method to predict vehicle body temperature profiles presented in [3]. The manufacturing process is the other primary factor for vehicle body noise, Liang and Zhu [4] examined how ambient temperature and electrophoretic oven settings affect e-coating properties. While substantial research has been conducted on vehicle squeak and rattle detection and manufacturing quality improvement, the issue of squeaking noise from automotive body painted coatings remains under-explored.
This paper builds on existing research by exploring the theoretical mechanisms behind automotive body squeaking noise and introducing one key metric for noise elimination during the manufacturing phase. It also focuses on optimizing manufacturing process controls, particularly the baking oven temperature, by adjusting heating rate and holding time to raise the e-coating's glass transition temperature, crucial for noise reduction.
2. Material and Method
Vehicle body is typically constructed from multiple individual metal panels that are joined together to form a cohesive unit. These panels are often fabricated from high-strength steel, which ensures the requisite strength and stiffness for the vehicle’s body while maintaining a minimal overall performance.
2.1. Subjective evaluation on body squeak noise
In this study, five vehicles were subjectively evaluated on uneven road surfaces, where metal panels experienced road-induced vibrations transmitted through the suspension system, leading to torsional deformation. This motion often produces high-pitched noises that cause significant annoyance and psychological discomfort. Notably, this squeaking is more pronounced at elevated temperatures and subsides when the temperature returns to normal. Table 1 presents the subjective evaluation results, categorized by severity levels: severe (A), medium (B), and slight (C), with levels B and C indicating moderate and slight annoyance, respectively.
Table 1Statistic of body squeak on different road conditions
Vehicle | Conditions | Temperature | ||
23 ℃ | –29 ℃ | 49 ℃ | ||
1# | Twist | None | None | None |
Rough | B | None | B | |
2# | Twist | C | None | C |
Rough | B | None | B | |
3# | Twist | B | None | C |
Rough | C | None | C | |
4# | Twist | None | None | C |
Rough | C | None | B | |
5# | Twist | None | None | C |
Rough | B | None | B |
Statistical data collected from evaluated vehicles reveals two key findings concerning body squeak. Firstly, the majority of body squeaking noise is ranked at level B, indicating that a significant portion of customers will notice and experience annoyance. Secondly, the occurrence of squeaking noise is notably associated with high-temperature conditions.
Fig. 1Distribution of body squeak noise locations
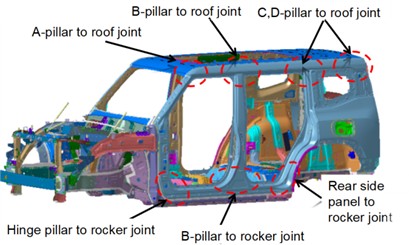
Further observation of the noise source signifies that squeaking noise predominantly originates from areas characterized by complex overlapping structures, involving multiple components or multi-layer sheet metal configurations. Statistical classification of body squeaking noise sources is depicted in Fig. 1.
2.2. Theoretical model: Maxwell viscoelastic model
In this paper, a linear viscoelasticity model is developed by considering combinations of a linear elastic spring and a linear viscous dash-pot [5]. The constitutive equation for a material that behaves as a linear elastic spring follows Hooke's Law, expressed as Eq. (1):
where: σ is the stress, E is the modulus of elasticity, ε is the strain. Notably, the stress-strain ratio of the spring remains constant over time, demonstrating instantaneous elastic deformation and recovery.
Fig. 2The linear elastic spring
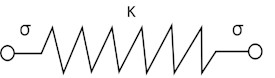
Fig. 3The linear dash-pot
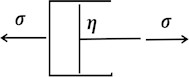
Fig. 4The Maxwell model
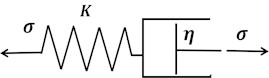
For the linear viscous dash-pot, as seen Fig. 2, the electro-coating studied in this paper behaves similarly to a viscous dash-pot [10]. This dash-pot configuration resembles a piston-cylinder arrangement, as illustrated in Fig.3, with the cylinder filled with a viscous fluid. Strain is induced by displacing the piston through the fluid. This fundamental principle underscores the viscous damping effect inherent in such systems, where the rate of deformation is directly linked to the applied force, refer to Eq. (2):
where, η represents the viscosity of the material, dε/dt denotes the strain rates. Notably, in accordance with Newton’s law of viscosity, the strain rate is directly proportional to the applied stress. This relationship implies that as the stress increases, the strain rate also increases proportionally.
The Maxwell model stands as the most widely utilized framework for describing linear viscoelastic forces [5]. This model comprises a Maxwell element-a combination of a linear spring and a nonlinear dash-pot-aimed at stimulating the dynamic mechanical behavior of vehicle body coatings during vibration (as seen in Fig. 4). By partitioning the total strain into components attributable to the spring (ε1) and the dash-pot (ε2), the strain of the entire Maxwell viscoelastic model [6] can be expressed Eq. (3):
Then, put the Eq. (1) and Eq. (2) into the Eq. (3):
Transform Eq. (4) into Eq. (5):
The relaxation time, denoted as τ, characterizes the behavior of stress relaxation. In stress relaxation, deformation remains unchanged over time. Physically, this means that when the strain remains constant, the stress decreases exponentially over time, its physical meaning is that when the strain remains constant, the stress decrease exponentially over time. This constitutive equation has been put in what is known as standard form [6].
All polymeric materials in passenger cars exhibit viscoelastic properties [7]. When the ambient temperature exceeds the polymer’s Tg, it becomes increasingly prone to deformation as the temperature rises. In this state, even minimal external force can cause significant deformation. Once the force is removed, the polymer gradually returns to its original form. This repeated microscopic deformation generates noise. Enhancing the Tg of the electrophoretic coating material in the BIW can reduce the deformations in the polymer, effectively preventing noise caused by such deformations. And the process is illustrated in Fig. 5.
Fig. 5Body coating deformation under viscoelastic stress
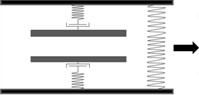
a) Initial state
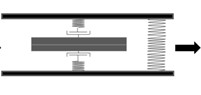
b) Compression under stress
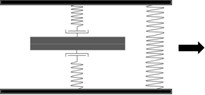
c) Stress release
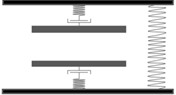
d) Paint film rebound to separation
3. Results
To verify the influence of the temperature of electrophoretic coating on vehicle body squeaking noise, two painting shops' body coating baking oven temperatures were measured and compared. One shop experiences squeak issues, while the other does not.
3.1. Comparison baking oven temperature of vehicle body coating
To confirm the adequacy of baking time for the electrophoretic paint on the test sample vehicle, the baking oven temperature in the coating workshop was meticulously monitored. High-temperature sensors were strategically deployed to track changes in the baking oven temperature. The monitoring locations are depicted in Fig. 6.
Fig. 6a) Inside the front longitudinal beam; b) inside the rear longitudinal beam; c) inside the front longitudinal beam; d) inside B-pillar
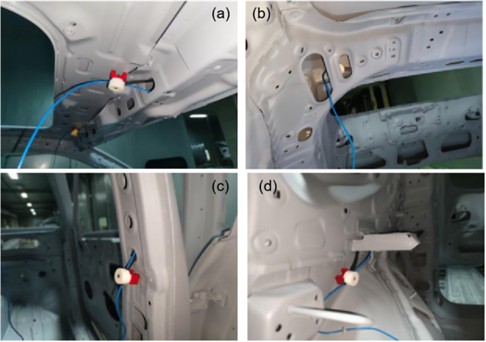
Subsequently, the obtained curing time and maintaining period were analyzed. A comparison was drawn between the squeak area and non-squeak area with the vehicle body electrophoretic paint's required curing window, as depicted in Fig. 7.
Primarily, temperatures above 106 ℃ are maintained for about 15 minutes, while most positions are held for approximately 20 minutes. Notably, the duration above 160 ℃ inside the cavity is shorter than for the vehicle’s exterior. Additionally, a comparison with factories that do not experience body squeak issues shows that the baking time above 160 ℃ is significantly longer in those with squeak noise problems.
Fig. 7a) Baking temperature of the body cavity; b) baking temperature of the body outer
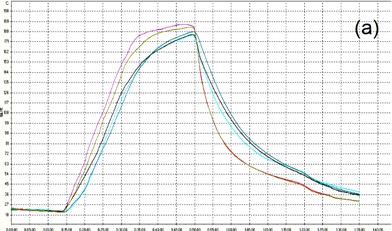
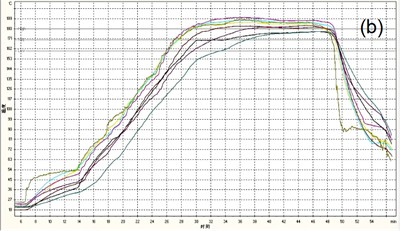
3.2. Testing glass transition temperature of sample sheet metal
To ascertain whether the glass transition temperature of the electrophoretic coating on the prototype car with squeaking noise is lower than the ambient temperature of the entire vehicle test (49 ℃), a glass transition temperature testing was conducted [8]. This testing employed the differential scanning calorimetry (DSC) method.
Fig. 8Outer sheet metal test result – A position

Fig. 9Outer sheet metal test result – B position

Fig. 10The sheet metal in cavity area test result
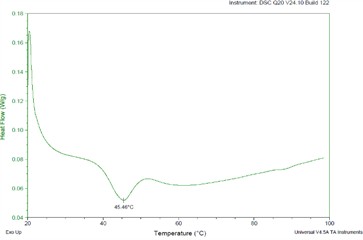
Fig. 11Deformation-temp curve of polymers
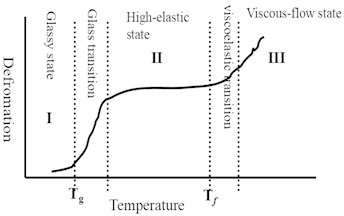
As demonstrated in the above figures, as shown in Fig. 8 and Fig. 9, no endothermic or exothermic reactions were observed between 20 ℃ and 80 ℃ during the standard sample testing process. However, in the second test, a folded sample was utilized, representing overlapping sheet metal parts inside the cavity near the occurrence of annoying noise and insusceptible to bake. This setup aimed to simulate real-world conditions more accurately, as shown in the below Fig. 10. At 88.66 ℃, a noticeable endothermic reaction occurred in the sample, indicating a physical state transition at a lower temperature, namely a glass transition.
The test results shown in Fig. 10 reveal a significant endothermic peak at 45.46 ℃, indicating a physical state transition where the material begins to melt or undergo plastic deformation [9]. Further analysis of the glass transition temperature shows that the inner sheet metal paint in the overlap area of the squeak noise region transitions at around 45 ℃, which is lower than the test ambient temperature of 49 ℃. In contrast, the outer sheet metal paint transitions at 88 ℃, which is higher than the ambient temperature.
4. Discussion
The properties of automotive coatings are directly influenced by the curing process. The thermal performance of vehicle body coatings stands as a crucial parameter in this regard [10]. Polymer materials exhibit three distinct states-glassy state, high-elastic state, and viscous state-under varying external conditions such as temperature and pressure, as illustrated in Fig. 11. During the high-elastic state, the coating experiences an increase in molecular kinetic energy, causing chain segments to unfold into a network structure. As a result, the modulus of the body electro-coating rapidly decreases, demonstrating characteristics of both elasticity and viscosity [11]. The glass transition temperature serves as a critical threshold at which polymer materials undergo a transformation, impacting properties such as film hardness, drying rate, and solvent resistance.
It holds particular significance in the car body curing process. Tg is closely associated with various mechanical properties of polymers [12], including tensile strength, modulus of elasticity, and operational temperature range. Below the glass transition temperature, polymers tend to exhibit brittleness, while above this temperature, they demonstrate elasticity.
5. Conclusions
This study offers a thorough analysis of the mechanisms behind BIW squeaking noise, providing both theoretical insights and practical solutions for its mitigation. The application of the Maxwell Viscoelastic Model, combined with empirical data from manufacturing processes, allows for a deeper understanding of how material properties and process parameters influence noise generation.
References
-
J. Pang, Noise and Vibration Control in Automotive bodies. John Wiley & Sons, 2018, https://doi.org/10.1002/9781119515500
-
V. Mainkar, S. Gosavi, K. Ghadage, and A. Wayal, “Annoying car body squeak and amp; creak – a systematic detection and prevention approach,” in Symposium on International Automotive Technology, Sep. 2021, https://doi.org/10.4271/2021-26-0273
-
Y. H. Wu, S. Surapaneni, K. Srinivasan, and P. Stibich, “Automotive vehicle body temperature prediction in a paint oven,” in SAE 2014 World Congress and Exhibition, Apr. 2014, https://doi.org/10.4271/2014-01-0644
-
B. Liang and M. Zhu, “Studies on the influence of baking oven temperature on squeak noise of body sheet metal,” in Lecture Notes in Electrical Engineering, Vol. 769, Singapore: Springer Nature Singapore, 2022, pp. 1301–1317, https://doi.org/10.1007/978-981-16-2090-4_83
-
W. Flügge, Viscoelasticity. Berlin, Germany: Springer Science & Business Media, 2013.
-
H.P. Rink, “Polymeric engineering for automotive coating applications,” in Automotive Paints and Coatings, Wiley, 2008, pp. 211–257, https://doi.org/10.1002/9783527622375.ch7
-
C. Geipel and P. Stephan, “Experimental investigation of the drying process of automotive base paints,” Applied Thermal Engineering, Vol. 25, No. 16, pp. 2578–2590, Nov. 2005, https://doi.org/10.1016/j.applthermaleng.2004.11.025
-
M. Doerre, L. Hibbitts, G. Patrick, and N. K. Akafuah, “Advances in automotive conversion coatings during pretreatment of the body structure: a review,” Coatings, Vol. 8, No. 11, p. 405, Nov. 2018, https://doi.org/10.3390/coatings8110405
-
N. Jafarzadehpour, M. Bidlingmaier, and B. Corves, “Integrating body-in-white influences on vehicle dynamics into real-time models,” SAE International, 400 Commonwealth Drive, Warrendale, PA, United States, Automotive Technical Papers, Sep. 2021.
-
N. Akafuah, S. Poozesh, A. Salaimeh, G. Patrick, K. Lawler, and K. Saito, “Evolution of the automotive body coating process – a review,” Coatings, Vol. 6, No. 2, p. 24, Jun. 2016, https://doi.org/10.3390/coatings6020024
-
M. Schmidt and G. Strannhage, “Rheological challenges in automotive production,” Annual Transactions of the Nordic Rheology Society, Vol. 14, p. 139, 2006.
-
M. Schmidt and G. Strannhage, “Understanding viscoelastic material behaviour in car body engineering and manufacturing,” Annual Transactions of the Nordic Rheology Society, Vol. 19, 2011.
About this article
The authors have not disclosed any funding.
The datasets generated during and/or analyzed during the current study are available from the corresponding author on reasonable request.
The authors declare that they have no conflict of interest.