Abstract
In the research of new reactors, lithium has become a research direction as a new coolant after sodium. Lithium working fluids introduce various metallic and non-metallic impurities such as oxygen, calcium, carbon, nitrogen, etc. to a greater or lesser extent during production, filling, and even operation. In addition, the processing, welding, and cleaning steps of the pipeline and equipment in the circuit during manufacturing inevitably result in residual dirt, grease, surface oxides, and moisture. These will have a certain impact on the performance of heat transfer and circuit safety through accelerated corrosion or plugging. Therefore, in high-temperature lithium circuits, the impurity concentration of lithium working fluid must be strictly controlled and purified before use. At present, the detection methods for impurity content in lithium working fluids can be divided into two categories: sampling analysis method and online measurement method. Sampling analysis is the most direct detection and analysis method, which can directly obtain the content of various impurities in lithium working fluids, and the results are relatively accurate; The online detection method can generally only detect non-metallic impurities, but it is relatively fast and simple, and is currently a commonly used measurement method on lithium working fluid devices. The plugging meter method has been studied and used as a rather convenient online detection method. This article introduces a small, self-heating, and mobile high-temperature lithium plugging meter system to meet the online detection of different points in the lithium circuit of system engineering.
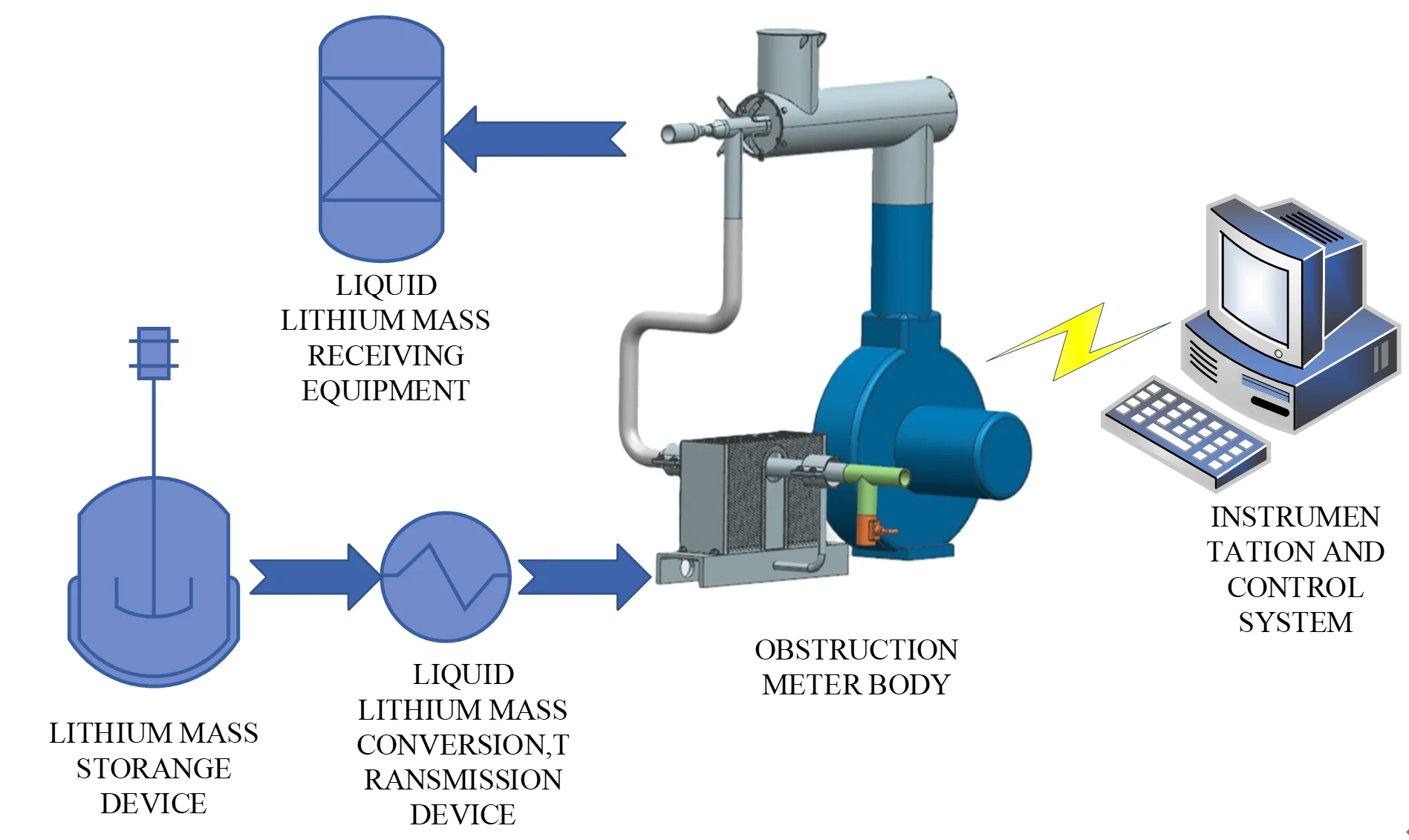
Highlights
- A small self-heating blockage gauge system is designed based on liquid lithium metal medium, which provided a new solution for controlling the concentration of impurities in the lithium working fluid and improving the purity of the lithium working fluid in the pipeline.
- The system is compact and can be used for mobile on-line detection at different sites in the system loop.
- The system calculates and designs the heating and heat dissipation of the pipeline, and the experimental results show that the random error of the blocking temperature is not more than 1%, which has good repeatability and measurement stability.
- The system can be used not only in high-temperature lithium fluids, but also in other paramagnetic alkali metal fluids.
1. Introduction
In the research of new reactors, lithium has become a research direction as a new coolant after sodium and in the research of new reactors, lithium has become a research direction as a new coolant after sodium and sodium potassium alloys. Lithium working fluids introduce various metal and non-metallic impurities such as oxygen, calcium, carbon, nitrogen, etc. to a greater or lesser extent during production, filling, and even operation [1]-[3]. Nitrides, oxides, carbides, hydrides, and silicides are common non-metallic impurities. These impurities in lithium generally exist in the form of compounds such as Li3N, Li2O, and LiH, causing a rapid increase in the corrosion rate of structural materials; When the temperature is below saturation, impurities in the cold section of the system's pipeline will form solid residue, causing pipeline blockage when deposited, which has a certain impact on heat transfer performance and circuit safety [4]-[6]. Although lithium does not have a long-lived radioactive isotope, which is its advantage as a coolant in nuclear power plants, it may form long-lived radioactive substances after impurities are added, thus challenging system maintenance and repair [7]-[9]. Therefore, the impurity concentration of lithium working fluid in high-temperature lithium circuits must be strictly controlled and purified before use.
After the lithium working fluid is purified, its impurity content should meet the limit requirements for impurity content in the lithium circuit before use. Therefore, relevant instruments need to be used for detection. It is generally believed that the purification technology of lithium and the detection of impurity content are carried out together, which makes it strenuous to divorce them. The purification effect needs to be confirmed through testing, and the tools involved are usually installed in the same place as the purification equipment [10]-[12]. The detection methods for impurity content can be roughly divided into two types: sampling analysis method and online measurement method. The sampling analysis method is to directly collect samples of lithium working fluid, using physical or chemical methods and relevant instruments to obtain accurate impurity content values. It has very rigid requirements for pollutant control during sampling, transportation, analysis, storage, and other processes, and the operation is cumbersome. Online detection methods can generally only measure the content of 1-2 impurities, but compared with sampling methods, they are relatively fast and simple, making them a commonly used measurement method on lithium working fluid devices [13], [14]. The commonly-used online detection methods for liquid metals include Blake meter method, electrochemical oxygen meter method, and blockage meter method [15]. The maturity, reliability, and convenience of the first two technologies are relatively low, while the use of blockage meters is fairly effective, which can achieve the measurement of oxygen impurity content in liquid metal working fluids within a few minutes [16], [17]. In foreign countries, the development of blockage meters has been accompanied by the development of sodium cooled fast reactors. In the early 1960s, the design and testing of blocking meters were carried out in fast reactor research in the United States and France. At present, experience in using blocking meters only exists in the research process of sodium reactors in China. The sodium reactor has introduced an ESPRESSO blocking meter system from Italy, which was introduced from France in the 1970s and early 1980s. In recent years, in response to the demand for sodium cooled reactors, a new sodium working fluid blockage meter has been developed, following the structure of the Italian ESPRESSO circuit, and is currently approaching the stage of engineering application. However, the melting point and heat transfer characteristics of sodium are significantly different from those of lithium, and cannot be directly used for the measurement of lithium working fluids. From the current research situation in China, it can be seen that there is only a history of the application of blocking meters for sodium working fluids, while the development of blocking meters for lithium working fluids in other fields has not yet been carried out. The design of blocking holes and the overall operation mechanism of blocking meters are also not thorough enough. Besides, to meet the development needs of other types of alkali metal devices, it is necessary to carry out the development of blocking meters as soon as possible to provide convenient and fast online measurement methods for the purification effect of working fluids. This article introduces a small, self-heating, and mobile high-temperature lithium blockage meter system to fulfill the online detection of different points in the lithium circuit of system engineering.
2. Measurement mechanism
Manual obstruction meter, program control obstruction meter and automatic control obstruction meter have been devised consequently in the development process of domestic and foreign obstruction meter. Manual obstruction meter is manually controlled. After the start of measurement, the obstruction meter body heater is first manually cut off, the fan cooling system is started, and the temperature and flow rate changes are observed in the workpiece through the thermocouples and flow meters. When a program-controlled obstruction meter is in operation, the number, speed and limits of the measurement process are carried out according to a fixed program. Automatically controlled obstruction meters are similar to programmed control methods, but the measurement period and parameters can be automatically adjusted to the operating conditions of the mass. Of the three types of obstruction meters, the manual obstruction meter is simpler to monitor, but less in accuracy; the automatic obstruction meter is more accurate, but the control system is more complex; and the programmed obstruction meter is in between in terms of accuracy and complexity. Manual control used to be dominant. Comparatively, adopting an automatic control mode, this design of this mobile blockage meter system combines the characteristics of lithium, which is relatively simple in control system, high in precision, and small in size.
The working mechanism of the plugging meter system is that the solubility of non-metallic impurities in liquid alkali metals varies with temperature [18], [19]. After the measurement program is started, the heating device is continuously adjusted to maintain a constant temperature for the working fluid inside the plugging meter. Then, the working fluid is cooled. When the temperature of the working fluid drops below the saturation temperature, impurities precipitate in the form of crystals on the wall of the plugging hole, causing a decrease in the cross-sectional area of the flow channel and a decrease in flow rate. The flow rate rapidly decreases with a significant decrease in temperature. The plugging temperature in the plugging meter is the temperature at which the flow rate begins to decrease, which can reflect the overall level of non-metallic impurities. To quantitatively calculate the impurity content, the plugging temperature can be substituted into the solubility formula to obtain the critical impurity mass, which is the impurity content of the circuit. FIG. 1 shows the measurement mechanism diagram of the obstruction meter system.
Nitrogen and hydrogen have limited solubility in liquid lithium medium and are unstable and prone to decomposition under high temperature conditions [20]. Therefore, the main non-metallic impurity in the circuit is oxygen. According to Yonco et al. experiment, the oxygen saturation solubility formula is as follows:
where: C – solubility of oxygen in lithium (wpm); T – temperature of lithium (K), 450 K<T< 1007K.
Fig. 1Measurement mechanism diagram of the obstruction meter system
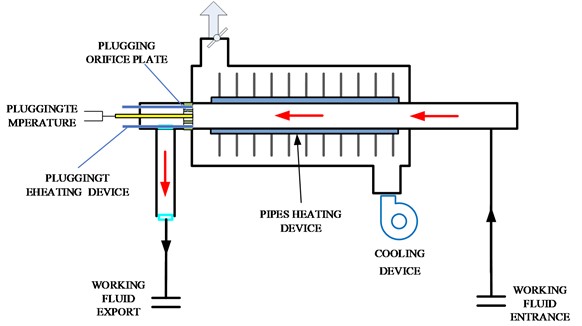
3. Design and implementation of instrument control electronics
The system consolidates all control devices (displays, data collectors, power regulators, and programmable controllers) into a cabinet, and these control devices are connected according to a certain logical relationship to form a hardware control system. Together with the software program in the programmable controller, the control of the plugging meter is achieved. Fig. 2 shows the flowchart of a lithium plugging meter.
The system is composed of temperature control module, wind control module, insulation layer and shell, and industrial computer. The temperature module preheats the pipeline and stabilizes it at the set temperature. The wind control module starts to reduce the temperature of the pipeline when it needs rapid cooling or other needs, and assists the temperature control module in stabilizing the pipeline temperature at the set temperature. The temperature control module actuator has a protective shell outside, which is wrapped with an insulation layer to isolate heat exchange inside and outside the shell. The overall plan is shown in Fig. 3.
Fig. 2Flow chart of lithium plugging meter
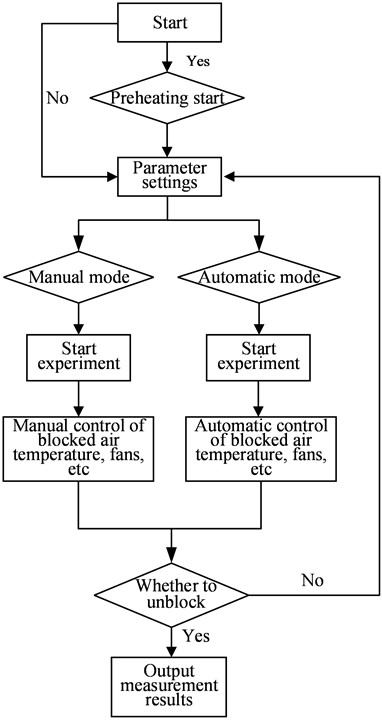
Fig. 3Diagram of overall technical scheme block
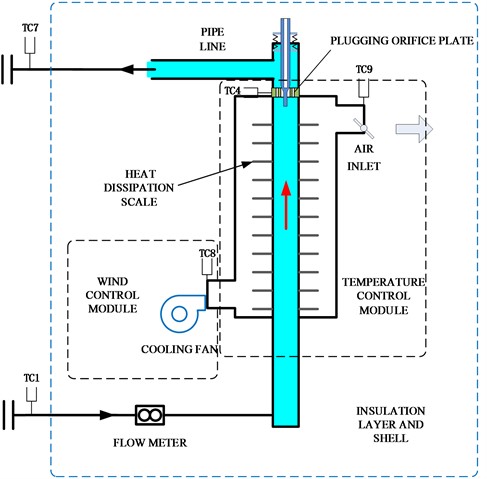
The programmable controller is the core part of the system, which performs functions such as collecting sensor feedback signals, logical calculations, and driving the executing mechanism. After the measurement starts, the variable frequency fan automatically adjusts the output to cool the working fluid temperature at the plugging orifice position at the set cooling rate until the flow meter signal significantly decreases, and outputs the temperature value at this time; Subsequently, the fan stops and the heater starts until it returns to the original flow level, thus completing a measurement. Fig. 4 shows the automatic measurement control model.
Fig. 4Automatic measurement control model
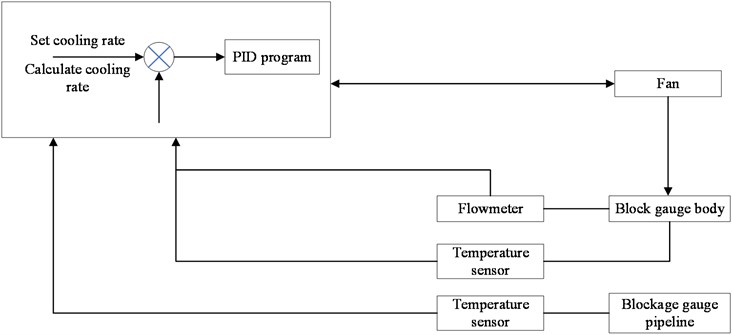
The control logic program of the system completes the measurement operation according to the control logic of cooling plugging, outputting measurement results, and heating resistance resolution. The temperature control program and measurement program are integrated into the overall program of the lithium process testing device. After the measurement starts, the variable frequency fan automatically adjusts the output to cool the working fluid temperature at the plugging orifice position at the set cooling rate until the flow meter signal significantly decreases, and outputs the temperature value at this time; Subsequently, the fan stops and the heater starts until it returns to the original flow level, thus completing a measurement.
4. Experimental analysis
4.1. Experimental platform
In order to verify the functions and reliability of the system, an experimental platform was specially constructed. The experimental platform consists of lithium mass storage device, liquid lithium mass conversion, transmission device, blocking meter body, instrumentation and control electrical system and liquid lithium receiving equipment. Fig. 5 shows a schematic diagram of the experimental platform, and Fig. 6 shows a physical drawing of the product. Among them, the lithium workmass storage device is specially designed to store liquid lithium metal, liquid lithium workmass conversion, transmission device is to charge liquid lithium workmass from the storage device to the experimental circuit, the instrumentation and control electrical system collects and monitors the temperature, flow and other parameters in the blocking body and controls the heating device, fan and other operational overall system, through the purified lithium workmass through the circuit to the liquid lithium receiving equipment.
4.2. Heating power calculation
When this heating system is working, there are two main working states of the system:
State 1: During cyclic operation, the external output liquid lithium itself has a certain temperature, and the heater only needs to increase its temperature or maintain the existing temperature.
Fig. 5Schematic diagram of experimental platform
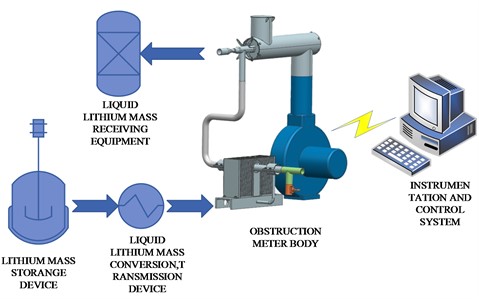
Fig. 6Product picture
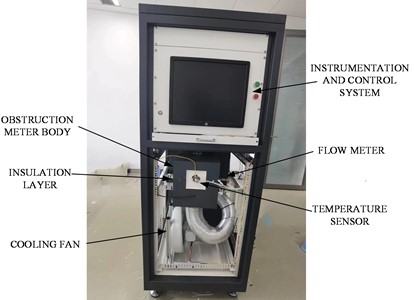
State 2: Discharge mode, the heater must heat the remaining solid lithium in the pipeline to 300 degrees Celsius before discharging.
It is obvious that state 2 requires more power, so when calculating the heating power, the heating limit required for the system is calculated according to state 2. Lithium has a specific heat at room temperature of 3.6 kJ/kg, a density of 494 kg/m3, and a specific heat of melting of 418 kJ/kg. According to the requirement, all pipelines should be heated from room temperature of 20 degrees Celsius to 300 degrees Celsius through a heater in state 2. The required work W for heating can be calculated using the following formula:
where, C represents the specific heat of lithium at room temperature of 3.6 kJ/kg, ∆T represents the temperature difference between the required heating temperature and room temperature, where it is 280 degrees Celsius. The required heating power W is obtained and heated to 1008 kJ/kg. The specific heat of melting of work W is 418 kJ/kg. The total work required to heat to 300 degrees Celsius is 1.426×106 J/kg. For a 16mm pipeline, the density of lithium is 0.01 kg/m. According to the Eq. (2), the calculation shows that the work required to heat every 1 m of pipeline to 300 degrees Celsius is W, which is 1.426×104 J/m. For this project, the heating power P of heaters 1, 2, and 3 is the lowest, usually set at 100 W/m during actual operation. According to the following formula, the heating time T is approximately 142 seconds to reach the target temperature of 300 degrees Celsius:
In reality, due to the energy loss caused by the transmission of individual heat between different media, and it is estimated that the time required for heat conduction in each medium, taking into account the above factors, can be controlled within 30 minutes.
4.3. Heat dissipation power calculation
The fan acts on the heat dissipation scale of heater 4 and can be dissipated through the surface area heat dissipation formula:
where, α is the convective heat transfer coefficient, also known as the surface heat transfer coefficient, which also refers to the amount of heat that can be transferred between a fluid and a wall per unit area at a unit temperature difference and per unit time. S is the contact area between the heat dissipation surface and the air, and ∆t is the surface temperature and air temperature of the heat source.
When the surface area heat dissipation is conducted between the heat carrier and air, the quasi-numerical relationship of the convective heat transfer coefficient is:
where Nu=lα/λ is the Nusselt number, Gr=gl3/V2∙β∆t the Grayshev number; Pr is the Land number; l is the characteristic size of the object, as for this heat sink, the length of the plate; V is the kinematic viscosity of air; β is the volume expansion coefficient of the fluid.
Through deduction, there are:
By looking up tables:
Assuming that the fan takes away all the heat; ∆t = 300 – 30 = 270; S= 0.49 m2. So you can get Q=1055 W, that is to say, under this condition, the natural convection of the heat sink can remove 1055 joules of heat per second. According to the heat difference formula: Q=cm∆t.
Where c is the specific heat capacity of copper: 0.39×103 J/(kg·℃); M is the mass: 20.9 kg; By substituting it into the formula, the temperature drop per second is calculated to be 0.129 ℃, which is equivalent to 7.74 ℃/min and meets the usage requirements of 0.5 ℃/min-5 ℃/min.
4.4. Temperature and flow measurement
The system is equipped with 12 temperature measurement points, including pipeline inlet and outlet, flow meter inlet and outlet, cooling fan outlet, air inlet, thermocouple well, plugging meter front end, middle end, rear end, and near the plugging orifice plate. The layout of temperature measurement points is shown in Fig. 7.
4.5. Experimental results
After the lithium work charge in the circuit, several experimental measurements were carried out at 400 °C circuit temperature, and the experimentally measured blocking curves and measurement results are shown in Fig. 8, and Fig. 9 shows experimental thermogram. The system has successfully completed the measurement operation many times and realized unblocking in a reasonable time, and the impurity content is less than the required range.
Fig. 7Schematic diagram of temperature measurement point layout position
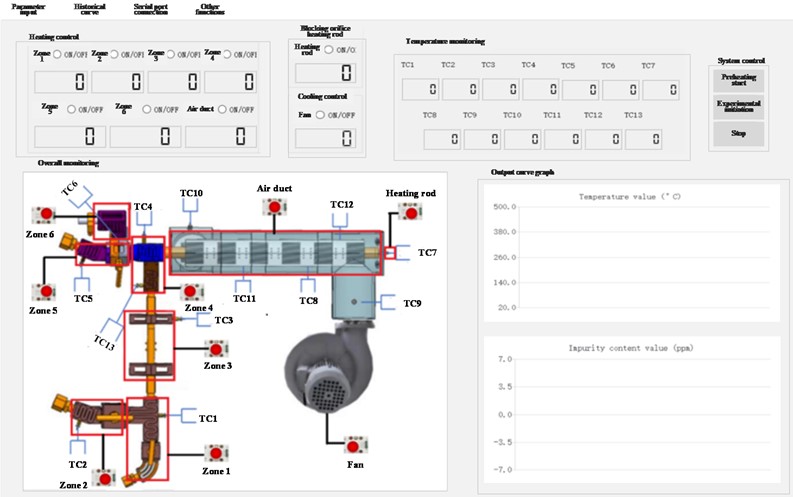
Fig. 8Experimental measurement results
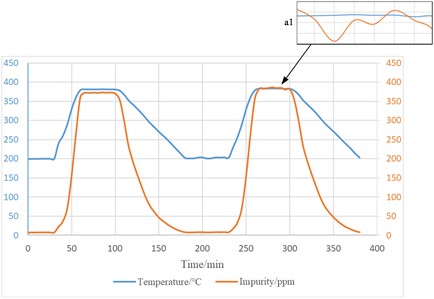
Fig. 9Experimental thermogram
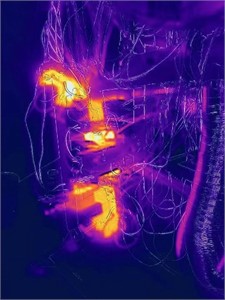
From the figure, it can be seen that the solubility of oxygen changes with the change of temperature, when the temperature gradually increases, the solubility of oxygen gradually increases, and the oxygen content in liquid lithium metal decreases; on the contrary, when the temperature decreases, the solubility of oxygen gradually decreases, and oxide crystals precipitate from liquid lithium metal; the system heating can be completed within 30 min, and the heating efficiency is high.
The measured blocking temperature when the loop is adjusted to 210 ℃ is shown in Table 1. It is known through the experiment that the random error of the measured blocking temperature is not more than 1 %, which indicates that the blocking meter has a very good repeatability and measurement stability.
It can be seen through the experiment, see the mini-figure a1, the temperature fluctuation will have a greater impact on the oxygen solubility. Cooling rate is too small will cause the temperature curve jitter, resulting in the output of the wrong measurement results, so the cooling rate should be greater than 1.5 ℃/min, and relatively easy to control; at the same time, we must also consider that the cooling rate is too fast will lead to local thermal stress, affecting the service life of the blocking meter system, but also bring safety hazards. Therefore, combining the above factors, it is recommended to control the cooling rate of the blocking hole position in the range of 1.5-3.5 ℃/min.
Table 1The aggregated plugging temperature
Experiment | First | Second | Third |
Temperature / ℃ | 200.2 | 199.8 | 202.2 |
random error / % | –0.23 | –0.43 | 0.7 |
5. Conclusions
On the basis of completing the design and manufacturing of the self-heating high-temperature lithium plugging meter system, a series of experimental studies are conducted in this design, and the following conclusions are obtained:
1) The self-heating high-temperature lithium plugging meter measures accurately and has good working stability, with a random error of no more than 1 % in the plugging temperature.
2) This system cannot only be applied to high-temperature lithium working fluids, but also other paramagnetic alkali metal working fluids (such as lithium, sodium, potassium, and sodium potassium alloys) can be used through experiments; By extension, it can work normally in diamagnetic working fluids (such as lead, bismuth, and lead bismuth alloys), thus expanding the application range of the system.
3) In order to ensure the safe operation and good measurement effect of the high-temperature alkali metal circuit, the cooling rate at the plugging hole should be within the range of 1.5 to 3.5 ℃/min.
References
-
В. K. Grishin, M. G. Glazunov, and A. G. Araklov, Properties of Lithium. (in Chinese), Soviet Union: China Industrial Press, 1966.
-
X. Xu and J. Qian, “Overall design and installation debugging of liquid metal lithium circuit,” (in Chinese), Nuclear Power Engineering, Vol. 15, No. 5, 1994.
-
N. I. Loginov, A. D. Efanov, and M. N. Arnoldov, “Lithium in nuclear and thermonuclear power engineering,” in Journal of Physics Conference Series, Vol. 98, No. 7, 2008.
-
C. Latgé and S. Sellier, “Oxidation of zirconium-titanium alloys in liquid sodium: validation of a hot trap,” in Liquid Metal Systems, Springer US, 1995, pp. 351–371.
-
E. Wakai et al., “Nitrogen hot trap design and manufactures for lithium test loop in IFMIF/EVEDA project,” Plasma and Fusion Research, Vol. 11, pp. 2405112–2405112, Jan. 2016, https://doi.org/10.1585/pfr.11.2405112
-
J. Zhang and R. Kapernick, “Oxygen chemistry in liquid sodium-potassium systems,” Progress in Nuclear Energy, Vol. 51, No. 4-5, pp. 614–623, May 2009, https://doi.org/10.1016/j.pnucene.2008.12.001
-
Sun Zhen, “My country nuclear energy system coolant technology has achieved new breakthroughs,” (in Chinese), People’s Daily, 2018.
-
M. Anderson, “Component and technology development for advanced liquid metal reactor,” 2017.
-
M. Huang, G. Zuo, and X. Meng, “Design and preliminary experimental research on flowing liquid lithium circuit,” (in Chinese), Nuclear Fusion and Plasma Physics, Vol. 37, No. 3, pp. 346–353, 2017, https://doi.org/10.16568/j.0254-6086.201703018
-
K. A. Davis, “liquid metal inline impurity measuring instruments state-of-the-art study,” Liquid Metal Engineering Center Report, 1968.
-
X. Xue, W. Zhang, and H. Zuo, “Purification and online detection system for liquid lithium circuit,” (in Chinese), Nuclear Fusion and Plasma Physics, Vol. 36, No. 3, pp. 271–275, 2016.
-
Y. Liu and P. Tan, “Numerical investigation on heat transfer characterization of liquid lithium metal in pipe,” (in Chinese), JUSTC, Vol. 52, No. 1, Jan. 2022, https://doi.org/10.52396/justc-2021-0043
-
H. Liu, “Simulation of residual stresses in functionally gradient Al2O3 coatings,” (in Chinese), Chinese Journal of Mechanical Engineering, Vol. 44, No. 8, p. 26, Jan. 2008, https://doi.org/10.3901/jme.2008.08.026
-
J. B. Pearson, T. J. Godfroy, and R. S. Reid, “NaK plugging meter design for the feasibility test loops,” in International Congress on Advances in Nuclear Power Plants, 2008.
-
O. J. Foust, Handbook of Sodium, Sodium and Potassium Engineering. (in Chinese), Beijing: China Institute of Atomic Energy, 1986, pp. 305–316.
-
S. H., “Investigation of a manual plugging meter for monitoring impurities in sodium,” (in Chinese), Atomic Energy Science and Technology, Vol. 23, No. 2, pp. 32–38, 1989.
-
L. Wenlong and Y. Chunli, “Research on calibration method of obstruction meter,” (in Chinese), Atomic Energy Science and Technology, Vol. 52, No. 11, pp. 2033–2037, 2018.
-
Z. Xie, S. G. Dong, and H. Zhu, “Design of mobile integrated control device for domestic sodium-cooled fast reactor’s plugging meter,” (in Chinese), Yuanzineng Kexue Jishu/Atomic Energy Science and Technology, Vol. 50, No. 12, pp. 2214–2218, 2016, https://doi.org/10.7538/yzk.2016.50.12.2214
-
W. Zeming, C. Baohua, and L. Yuyi, “Experimental Study on NaK Alloy automatic plugging meter,” (in Chinese), Nuclear Science and Engineering, Vol. 42, No. 5, pp. 1053–1058, 2022.
-
H. U. Burgost and C. K. Mazeus, “Alkali metal applied chemistry,” (in Chinese) in Fast Reactor Sodium Materials and Sodium Technology Assembly, Beijing: China Institute of Atomic Energy, 1991.
About this article
This work was supported in part by the National Natural Science Foundation of China [No. 52105068].
The datasets generated during and/or analyzed during the current study are available from the corresponding author on reasonable request.
Wu Xiaodong wrote and prepared the original draft; LeiZhufeng reviewed.
The authors declare that they have no conflict of interest.