Abstract
Composite cold recycled mixture is commonly used in pavement regeneration. The performance of it, including the unconfined compressive strength, splitting strength, dry shrinkage, temperature shrinkage and freeze-thaw resistance, are studied based on vibration mixing with different blending ratios of asphalt surface and cement-stabilized base. The results show that vibration mixing can effectively improve the mixing uniformity of the recycled mixture and increase the strength by up to 30 %. Besides, the change of reclaimed asphalt pavement (RAP) admixture will affect the mechanical performance and road performance of the recycled mixture. When the admixture of RAP material is 30 %, the strength is the highest, and when the admixture is 40%, the dry shrinkage is the smallest. The temperature shrinkage coefficient decreases with the increase of RAP material admixture, and the freeze-thaw resistance is enhanced with the increase of RAP material admixture.
Highlights
- Vibration mixing can effectively improve the uniformity of the recycled mixture, and enhance the strength of the composite recycled mixture. The increase percentage can reach up to 30%.
- Generally, more RAP material in mixture and more mud content will lead to more water absorption and better water conservation, which will affect the dry shrinkage performance of the mixture. In the designed experiment, when the content of RAP is 40% in the mixture, the dry shrinkage reaches the minimum.
- RAP is more sensitive to temperature changes. The temperature shrinkage increases with the increase of RAP amount. In the designed experiment, the temperature shrinkage coefficient is the smallest when the amount of RAP material is 20%.
1. Introduction
In recent years, many of China’s semi-rigid base asphalt pavement suffered from not only the function decline in asphalt surface, but also different degrees of damages in semi-rigid base structure. Some even have lost the bearing capacity and are no longer suitable for use as road base. Therefore, during pavement transformation, the recycling of asphalt surface layer and semi-rigid base should be considered as well as the structural reinforcement. Therefore, in some asphalt pavement maintenance and recycled projects, a composite cold recycled method is frequently adopted. In this method, the milled RAP and semi-rigid base material are mixed according to a certain proportion. And then, a certain amount of cement, emulsified asphalt or foam asphalt are added. The mixture will be mixed in situ or plant, then directly applied on the upper base of the pavement [1, 2]. Compared with the separate recycling of asphalt surface layer and semi-rigid base, the composite cold recycling is advanced in two aspects. Firstly, it can recycle the asphalt surface and base at the same time, and almost achieve the goal of 100 % waste utilization [3]. Secondly, the composite cold recycled base can make up for the cracking of semi-rigid subgrade and the deficiency of strength and rigidity in flexible subgrade. It is a technical optimization of the traditional semi-rigid pavement structure, which is especially suitable for secondary and lower grade roads with thin asphalt surface [4-6].
Nevertheless, composite cold recycling is similar to other recycling technologies, that the utilization rate of RAP is inversely proportional to the quality of recycled. At present, the practical engineering applications of composite cold recycled show that problems such as uneven recycled cement coating, unstable performance, poor durability are to be solved. Therefore, the advantages of composite cold recycled are not fully played. The major reasons for this analysis are as follows.
Firstly, the complexity of material composition is disregarded. The composition of composite recycled material is more complex than the asphalt surface or semi-rigid base recycled alone. Milling of RAP is flexible while old base mixture is a semi-rigid material. They are different in physical, chemical and hydraulic properties. During cold recycling of cement, rough field cold recycling method and ordinary plant mixing (continuous static mixing) cold recyling method cannot help cement to wrap evenly to two different materials. That is the key issue for cement agglomeration, instability of recycled mixture performance, and other problems [7-9].
Secondly, current researches on composite recycling is insufficient for generalization. Especially, in-depth research on the formation mechanism of the strength of semi-rigid cement-stable and flexible asphalt mixture materials, the evaluation of material properties, the design of regeneration mixture composition and the adaptability of regeneration methods, are in urgent need [10, 11].
In summary, in order to significantly improve the application performance of composite cold recycling technology, in addition to systematic research on mechanism, material composition, design, and evaluation methods, it is necessary to optimize the mixing process of composite cold recycling. Vibration mixing is a new method to improve the performance of cement concrete and cement stabilized gravel mixes, and enhance the strength and durability of the structures. Its technical principle is to make the cement concrete and cement stabilized gravel always in vibration during the mixing process through the continuous excitation of the lower lying shaft. In this way, the mixing inefficiency is effectively eliminated, the cement coating rate and utilization rate are improved, and the homogeneity and stability of the mixes are enhanced. Thus, the mechanical properties and road performance of the mix are improved [12, 13]. The practical application of several projects shows that the strength of cement stabilized gravel mixes can be increased by 10 %-20 % and the variability reduced by 10 %-20 %, and the dry temperature shrinkage and scouring resistance are significantly improved by using vibration mixing [14]. In conclusion, the effect of vibration mixing on the performance improvement of the mixes with cement as the binder is significant. In addition, the reduction of experimental variability by vibration mixing is also beneficial for laboratory performance studies, which can reduce the errors caused by the mixture forming process and accurately locate the influencing factors of mixture performance.
Based on practical needs, this study will include the comprehensive analysis and evaluation of the traits of old asphalt surface and subgrade materials, the design method of composite recycled material composition of old surface and subgrade based on vibration mixing, and the impact factors and performance evaluation of composite recycled mixture.
2. Materials and methods
2.1. Performance evaluation of recycled material
In this paper, the recycled material mainly comes from the RAP material and cement stabilized base material of some sections of G243 Meitan Moonba-Yuqing Highway in Guizhou. Their main performance indexes are shown in Table 1. The mud content of the recycled material seriously exceeds the specification range [15]. The high mud content will directly lead to a large water absorption rate of the mixture, which will affect the strength, impermeability, and frost resistance of the composite cold recycled mixture, and also increase the shrinkage and deformation of the mixture.
2.2. Composition design of composite cold recycled
Sieving results of RAP and reclaimed cement-stabilized macadam are shown in Table 2.
According to the recommended gradation range of cement stabilized graded macadam in JTGT F20-2015 Technical Regulations for Road Pavement Base Construction, the median value of C-C-2 gradation is selected as the reference gradation, and the proportional blending of recycled materials is carried out as in Table 3.
After a series of compaction tests with reference to the C compaction method in the relevant specification [15], the optimum moisture content of the composite recycled material is determined for different gradations and cement admixtures, and the final composition of the mixture is shown in Table 4.
Table 1Performance indexes of recycled materials
Sources | Test items | Test results |
RAP | Content of asphalt / % | 5 |
Penetration (100 g, 25 ℃, 5 s) / 0.1 mm | 26 | |
Ductility (5 ℃, 5 cm/min) / cm | 0 | |
Ductility (15 ℃, 5 cm/min) / cm | 9 | |
Soften point (TR&B) / ℃ | 59.8 | |
Cement-stabilized base | Content of needle particle / % | 3.5 |
Mud content / % | 7.1 | |
Crushing value / % | 28.7 |
Table 2Sieving results of recycled materials
Category | Mass percentage passing below square holes / % | ||||||||||||
26.5 | 19 | 16 | 13.2 | 9.5 | 4.75 | 2.36 | 1.18 | 0.6 | 0.3 | 0.15 | 0.075 | ||
Asphalt | 1 | 100 | 100 | 100 | 100 | 92.7 | 60.7 | 37.4 | 21.6 | 14.3 | 9.3 | 6.2 | 2.1 |
2 | 100 | 100 | 100 | 100 | 87.2 | 50.4 | 30.2 | 18.2 | 11.8 | 7.7 | 5.1 | 3.2 | |
Mean | 100 | 100 | 100 | 100 | 89.9 | 55.5 | 33.8 | 19.9 | 13 | 8.5 | 5.6 | 2.6 | |
Cement | 1 | 95.2 | 82.9 | 75.4 | 65.5 | 49.6 | 30.7 | 17 | 10 | 8.2 | 5.4 | 4.6 | 4.3 |
2 | 92.6 | 75.6 | 67.8 | 59 | 45.9 | 30.3 | 17.4 | 10.4 | 8.9 | 5.6 | 4.6 | 4.2 | |
Mean | 93.9 | 79.3 | 71.6 | 62.3 | 47.7 | 30.5 | 17.2 | 10.2 | 8.6 | 5.5 | 4.6 | 4.2 |
Table 3Gradation of recycled mixture with different mixing proportion
Recycled mix (cement: asphalt) | Mass percentage passing below square holes / % | |||||||||||
26.5 | 19 | 16 | 13.2 | 9.5 | 4.75 | 2.36 | 1.18 | 0.6 | 0.3 | 0.15 | 0.075 | |
80:20 | 97.1 | 87.7 | 81.2 | 74.6 | 62.7 | 43.9 | 26.6 | 16.2 | 12.0 | 10.6 | 7.5 | 6.7 |
70:30 | 97.6 | 86.2 | 80.2 | 72.0 | 59.8 | 39.5 | 24.7 | 17.8 | 11.3 | 8.0 | 6.3 | 5.2 |
60:40 | 96.8 | 86.3 | 80.2 | 71.7 | 58.9 | 39.4 | 24.8 | 16.9 | 11.0 | 7.6 | 6.1 | 5.1 |
Upper limit | 100 | 87 | 82 | 75 | 66 | 50 | 36 | 26 | 19 | 14 | 10 | 7 |
Lower limit | 90 | 73 | 65 | 58 | 47 | 30 | 19 | 12 | 8 | 5 | 3 | 2 |
Table 4Proportion of composite recycled mixture
Proportion / % | Cement / % | Gradation type | Optimum water content / % | |
Cement | RAP | |||
80 | 20 | 5 | Technical regulations for road pavement base construction C-C-2 medium gradation | 9.1 |
70 | 30 | 8.6 | ||
60 | 40 | 8.3 |
2.3. Experiment
The experiment involves the tests on unconfined compressive strength, splitting strength, dry shrinkage, temperature shrinkage and freeze-thaw resistance performance of the composite recycled mixture. The experiment follows the corresponding test method in JTG E51-2009 Test Procedure for Inorganic Binding Material Stabilization for Highway Engineering.
3. Data analysis
3.1. Mechanical performance
In this paper, the composite recycled materials with different mixing methods are first tested for unconfined compressive strength, in which six sets of parallel tests are conducted for each strength value, and the test results are shown in Table 5.
In Table 5, vibration mixing has a significant impact on the strength of composite recycled mixtures compared with static mixing, and the increase rate can reach 30 %, which is sufficient to meet the strength requirements of graded pavement subgrade. In addition, from the standard deviation or coefficient of variation, vibration mixing can significantly reduce the standard deviation of the strength test, which is mainly due to the fact that vibration mixing can reduce the agglomeration phenomenon in the mixing process, making the mixture more uniform and stable. Therefore, the subsequent performance tests in this paper are conducted by vibration mixing.
By studying the unconfined compressive strength and splitting strength of the composite recycled mixture at different time, the representative values of the unconfined compressive strength and splitting strength are obtained as shown in Table 6.
Table 5Unconfined compressive strength of composite recycled mixture with different mixing methods
Proportion / % | Unconfined compressive strength / MPa | ||||||||
Static mixing | Vibration mixing | ||||||||
Cement | Asphalt | 7 d | Standard deviation | 28 d | Standard deviation | 7 d | Standard deviation | 28 d | Standard deviation |
80 | 20 | 2.4 | 0.51 | 2.6 | 0.32 | 3.2 | 0.70 | 3.9 | 0.49 |
70 | 30 | 3.1 | 0.43 | 3.3 | 0.35 | 4.5 | 0.66 | 5.4 | 0.31 |
60 | 40 | 3.0 | 0.33 | 3.3 | 0.17 | 3.6 | 0.53 | 4.5 | 0.22 |
Table 6Strength representative value of composite recycled mixture
Proportion / % | 7d unconfined compressive strength / MPa | 28d unconfined compressive strength / MPa | 60d unconfined compressive strength / MPa | 90d unconfined compressive strength / MPa | 28d splitting strength / MPa | 90d splitting strength / MPa | |
Cement | RAP | ||||||
80 | 20 | 3.2 | 3.9 | 4.1 | 4.3 | 0.79 | 0.93 |
70 | 30 | 4.5 | 5.4 | 5.7 | 5.9 | 0.88 | 1.06 |
60 | 40 | 3.6 | 4.5 | 4.7 | 4.8 | 0.62 | 0.87 |
From the test results in Table 6, it can be seen that the effect of RAP material admixture on the strength of recycled mix is not monotonic. When the proportion of RAP material is 30%, its unconfined compressive strength and splitting strength at all times are higher than the remaining two test groups, and the 7d compressive strength has exceeded 4MPa, which basically meets the requirements of the grade pavement use.
The reason why the recycled material can be mixed into a composite recycled mixture and achieve the strength for applications, is that the recycled cement-stabilized material has a low content of needle particles, and many aggregates are covered with old cement mortar on the surface, which produces a secondary exothermic phenomenon when mixed and vibrated. In addition, the surface of the recycled cement-stabilized material is rough and has a good angular structure. This structure of the aggregates, on the contrary, increases the embedded effect of the recycled mixture when re-bonding.
3.2. Road performance
3.2.1. Dry shrinkage performance
The dry shrinkage performance of the recycled material is closely related to the water loss rate, so the preliminary maintenance during highway overhaul and reconstruction is vital to prevent the adverse effects of excessive water loss on the recycled base. Therefore, in this paper, the dry shrinkage performance test of the composite recycled mixture is carried out and the water loss rate and dry shrinkage at different times are tested. The results are shown in Fig. 1 and Fig. 2.
Fig. 1Water loss rate of composite recycled mixture
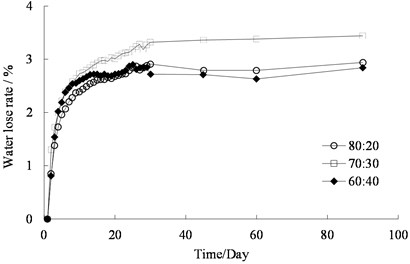
Fig. 2Dry shrinkage of composite recycled mixture
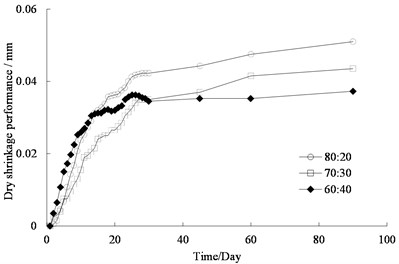
It can be seen from Fig. 1 that the water loss rate of the recycled mixes under all blending ratios increases as the time changes, with the water loss rate in the first 20 d being more obvious. This may be due to the high mud content of the reclaimed material, which is more absorbent. Meanwhile, the optimum moisture content in the early compaction test is high, with some blending ratios reaching 9 % water addition, so the water loss is also faster. In addition, due to the secondary exothermic effect of the recycled material in the early stage of molding, the temperature inside the mixture slightly increases at a shorter time, which makes it easier for water to evaporate, causing capillary tension effects, intermolecular forces in absorption water, dry shrinkage of interlayer water, and carbonation dehydration, which eventually triggered a change in the overall volume of the material. The water loss triggers the shrinkage deformation of the material, so the dry shrinkage of the mixture increases as time goes, and the trend of change is roughly the same as the water loss rate. The dry shrinkage of the mixture is the smallest when the mixing ratio of recycled material is 60:40.
3.2.2. Temperature shrinkage performance
The temperature shrinkage coefficient of the composite recycled mixture is shown in Fig. 3.
Fig. 3Temperature shrinkage coefficient of composite recycled mixture
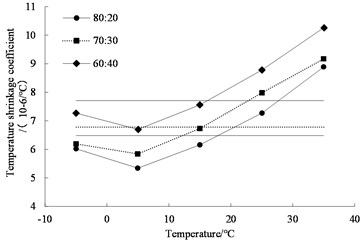
It can be seen that the temperature shrinkage coefficient of the recycled mixture under the three blending ratios showed a trend of decreasing and then increasing with the decrease of temperature. When the temperature is 0 ℃ to 40 ℃, the temperature shrinkage coefficient decreases. When temperature is from –10 ℃ to 0 ℃, the temperature shrinkage coefficient increases, and the minimum value appears in the interval of 0 ℃ to 10 ℃. During the change from –10 ℃ to 40 ℃, the temperature shrinkage coefficients of 60:40 group is larger than 70:30 group, and that of 70:30 group is bigger than 80:20 group, indicating that the RAP material is more sensitive to the change of temperature. The temperature shrinkage coefficient of recycled material gradually increases with the increase of RAP material content, especially when the RAP material increases to 40 %, the temperature shrinkage coefficient increases significantly. When the temperature is low, the bonding interface of the composite recycled mixture will become brittle, so that the mixture bonding strength is reduced, resulting in the generation of reflective cracks, thus weaken the material resistance to temperature contraction.
3.2.3. Freeze-thaw resistance performance
In order to study the freeze-thaw resistance of the recycled mixture, the unconfined compressive strength (UCS) and weight loss rate (Wn) of the cold recycled material after different times of freeze-thaw cycles are tested at three blending ratios, and the results are shown in Table 7.
Table 7Freeze-thaw cycle test result of composite recycled mixture
Proportion (cement: RAP) | Recycle for 5 times | Recycle for 10 times | Recycle for 15 times | |||
UCS / MPa | Wn / % | UCS / MPa | Wn / % | UCS / MPa | Wn / % | |
80∶20 | 3.4 | 2.1 | 3.1 | 4.8 | 2.5 | 8.2 |
70∶30 | 4.1 | 3.2 | 3.8 | 6.1 | 3.1 | 9.3 |
60∶40 | 2.9 | 3.6 | 2.6 | 6.4 | 2.1 | 10.6 |
In Table 7, with the increase of cycle times, the UCS of the composite cold recycled base material decreases gradually, while Wn gradually increases, indicating that the process of freeze-thaw reduces the road performance of the composite cold recycled base material. After the freeze-thaw cycles, as the amount of RAP material increases from 20 % to 40 %, the loss percentage of compressive strength is getting less, i.e., the loss rate of compressive strength is reduced as the amount of RAP material is increased.
In the process of freeze-thaw cycles from 10 to 15 times, both the mass loss and the magnitude of compressive strength loss are greater than the that of freeze-thaw cycles from 0 to 5 and 5 to 10 times, while the loss magnitude is more stable when the times of freeze-thaw cycles are less than 10. This indicates that when the times of freeze-thaw cycles are less, the freeze-thaw resistance of the recycled mixture tends to decay mildly, but after the number of freeze-thaw cycles exceeds a certain number, the freeze-thaw resistance of the recycled mixture will be significantly reduced, and even affect the normal use of the pavement.
4. Conclusions
In this paper, the road performance and mechanical performance of composite cold recycled mixture based on vibration mixing are studied. The influential factors and development directions are analyzed.
1) Vibration mixing can effectively improve the uniformity of the recycled mixture, and enhance the strength of the composite recycled mixture. The increase percentage can reach up to 30 %.
2) Generally, more RAP material in mixture and more mud content will lead to more water absorption and better water conservation, which will affect the dry shrinkage performance of the mixture. In the designed experiment, when the content of RAP is 40 % in the mixture, the dry shrinkage reaches the minimum.
3) RAP is more sensitive to temperature changes. The temperature shrinkage increases with the increase of RAP amount. In the designed experiment, the temperature shrinkage coefficient is the smallest when the amount of RAP material is 20 %.
4) When RAP increases from 20 % to 40 %, the loss of compression resistance gradually decreases. So, the increase of RAP can help reducing the loss of compression resistance after freezing and thawing.
5) The raw materials in this paper are from the same section of national road. For other composite recycled materials in different road sections, more tests will be done in the future.
References
-
A. Stimilli, G. Ferrotti, A. Graziani, and F. Canestrari, “Performance evaluation of a cold-recycled mixture containing high percentage of reclaimed asphalt,” Road Materials and Pavement Design, Vol. 14, No. sup1, pp. 149–161, Apr. 2013, https://doi.org/10.1080/14680629.2013.774752
-
C. Schwartz, B. Diefenderfer, and B. Bowers, “Material Properties of Cold-In-Place Recycled and Full-Depth Reclamation Asphalt Concrete,” National Cooperative Highway Research Program Report, Transportation Research Board, Washington, 2017.
-
Z. F. Hu, “actors influencing the road performance of asphalt pavement composite cold regeneration base mixture,” Pearl River Water Transport, Vol. 24, pp. 22–25, 2014.
-
H. M. Wang, C. B. Xiong, and D. C. Zhang., “Study on influence of compaction characteristics of emulsified asphalt cold recycled mixture,” Technology of Highway and Transport, Vol. 35, No. 3, pp. 31–36, 2019.
-
H. M. Wang et al., “Research on evaluation methods for construction workability of emulsified asphalt cold-recycled mixture,” Technology of Highway and Transport, Vol. 6, pp. 21–26, 2015.
-
F. D. Chen, “Study on performance of asphalt pavement composite cement cold recycled base mixture,” New Building Materials, Vol. 46, No. 4, pp. 150–155, 2019.
-
Z. H. Hao, C. Lan, and Q. W. Zhou, “The design and construction of the combinational cold recycling base,” Journal of Highway and Transportation Research and Development, Vol. 28, No. 12, pp. 41–46, 2011.
-
F. L. Zhang and L. Q. Zhang, “Application of vibration mixing technology in construction of cement stabilized macadam base,” Construction Machinery and Maintenance, Vol. 9, pp. 101–105, 2017.
-
L. Z. Dan, F. Chen, and W. Chen, “Road performance study of cement stabilized gravel mixture based on vibratory mixing technology,” Technology of Highway and Transport, Vol. 5, pp. 34–38, 2018.
-
L. Huang, Z. H. Hao, and W. J. Wu, “Research on construction technology and technical of composite cold regeneration base course,” Technology of Highway and Transport, Vol. 5, pp. 57–60, 2011.
-
F. Gu, W. Ma, R. C. West, A. J. Taylor, and Y. Zhang, “Structural performance and sustainability assessment of cold central-plant and in-place recycled asphalt pavements: A case study,” Journal of Cleaner Production, Vol. 208, pp. 1513–1523, Jan. 2019, https://doi.org/10.1016/j.jclepro.2018.10.222
-
Z. C. Xu, L. Z. Dan, and S. H. Lyu, “Strength and mixture uniformity analysis of cement stabilized gravel mixture based on vibratory mixing technology,” Technology of Highway and Transport, Vol. 6, pp. 49–55, 2017.
-
R. K. Li, H. Wang, and C. Lausanne, “Comparative study on strength performance of cement stabilized gravel mix under vibration stirring,” Journal of Chongqing Jiao Tong University (Natural Science Edition), Vol. 11, pp. 45–52, 2017.
-
R. H. Ying, K. Li, and H. W. Hu, “Study on the mixing method of cement stabilized gravel,” Highways and Automotive Applications, Vol. 5, pp. 126–128, 2018.
-
Research Institute of Highway Ministry of Transport, Test Methods of Materials Stabilized with Inorganic Binders for Highway Engineering JTG E51-2009. Beijing: China Communication Press, 2019.
About this article
This study is supported by the Science and Technology Project of the Department of Transportation of Yunnan Province (YunJiaoKeJiao(2016)140(B)).