Abstract
Taking high performance concrete (HPC) in hydraulic engineering as an example, this paper discusses the influence of different mixing methods of slag powder and fly ash on its frost resistance and chloride ion permeability. The results show that the compressive strength decreases with the addition of HPC; Proper addition of mineral admixtures is beneficial to improve the anti chloride ion permeability of HPC and reduce the electric flux; The HPC flux of 28d and 90 reaches 680C and 280C, when the mass ratio of slag powder to fly ash is 15:35 and the content of mineral admixture is 35 %; The frost resistance of HPC gradually deteriorates with the increase of mineral admixture under the condition of constant air content and water binder ratio. The frost resistance grade of HPC without mineral admixture reaches F200, and its frost resistance is the best.
1. Introduction
In order to facilitate the construction and ensure the strength of concrete, hydraulic concrete is usually produced by increasing the water consumption per cubic meter and increasing the amount of cement [1]. Practice shows that this method is difficult to ensure the durability of concrete [2]. Due to its excellent durability, mechanical properties and mixture properties, high performance concrete (HPC) is widely used in reservoir dams, river embankments and other engineering fields, and plays a positive role in reducing the comprehensive cost of the whole life cycle and improving the project quality [3-4].
When popularizing the application of HPC, we should consider the adverse erosion factors, actual climatic conditions and other scientific design of mix proportion and the selection of mineral admixtures [5]. In recent years, domestic scholars have discussed through experiments that the frost resistance or chloride ion corrosion resistance of HPC specimens are affected by different water binder ratios and mineral admixtures [6]. However, due to the diversity of the environment of hydraulic structures and the differences in the performance and quality of raw materials, there are few reports on the durability of mineral admixtures under the action of multiple or double damage factors. In view of this, taking HPC with water binder ratio of 0.42 as an example, this paper studies the influence of the single content of slag powder, fly ash and the compound content of slag powder and fly ash on the frost resistance and chloride ion permeability of HPC, and discusses the relationship between the frost resistance and electric flux of HPC and the output of mineral admixture, in order to provide some reference for the mix proportion optimization design of HPC.
2. Materials and measurements
2.1. The materials
The materials used in the test include P.O 42.5 cement, grade II fly ash, S75 slag powder, polycarboxylic acid high-performance water reducer, water reducer, coarse and fine aggregates and water. Taking C30 HPC as an example, the water binder ratio is maintained to be 0.43, the content of slag powder and fly ash is changed, and the effects of mineral admixtures on the frost resistance, chloride ion penetration resistance and compressive strength of HPC are explored. See Table 1 for HPC mix proportion design. 1# is the standard mix proportion of concrete. 11#, 12#, 13#, 14# are single fly ash with the mixing amount of 15 %, 25 %, 35 % and 45 %. 21#, 22#, 23#, 24# are single slag powder with the mixing amount of 15 %, 25 %, 35 % and 45 %. 31#, 32#, 33#, 44# are double fly ash and slag powder with the ratio of 50:0, 35:15, 25:25, 15:35 and 0:50, and the total content is 50 %.
Table 1HPC mix design
Specimen number | Cement / kg.m-3 | Slag powder / % | Fly ash / % | Sand / kg.m-3 | Stone / kg.m-3 | Water / kg.m-3 | Water reducing agent / % |
1# | 375 | 0 | 0 | 852 | 998 | 145 | 1.8 |
11# | 340 | 0 | 15 | 852 | 998 | 145 | 1.8 |
12# | 300 | 0 | 25 | 852 | 998 | 145 | 1.8 |
13# | 250 | 0 | 35 | 852 | 998 | 145 | 1.8 |
14# | 230 | 0 | 45 | 852 | 998 | 145 | 1.8 |
21# | 375 | 15 | 0 | 852 | 998 | 145 | 1.8 |
22# | 340 | 25 | 0 | 852 | 998 | 145 | 1.8 |
23# | 300 | 35 | 0 | 852 | 998 | 145 | 1.8 |
24# | 250 | 45 | 0 | 852 | 998 | 145 | 1.8 |
31# | 230 | 50 | 0 | 852 | 998 | 145 | 1.8 |
32# | 230 | 35 | 15 | 852 | 998 | 145 | 1.8 |
33# | 230 | 25 | 25 | 852 | 998 | 145 | 1.8 |
34# | 230 | 15 | 35 | 852 | 998 | 145 | 1.8 |
35# | 230 | 0 | 50 | 852 | 998 | 145 | 1.8 |
2.2. Test instruments and methods
The instruments used in the test include CABR -HDK9rapid freeze-thaw tester and CABR-RCP9 chloride ion electric flux tester. Previous studies have shown that the accuracy of the measurement results of these instruments is high [1].
The measurement process of CABR-HDK9 rapid freeze-thaw tester are as the follows: (1) Confirm that the antifreeze in the test box has good performance, and confirm that the antifreeze level can be at least flush with the upper surface of the test piece in the sample barrel. (2) Embed the temperature sensor of the central test piece into the test piece. (3) Put the test piece into the rubber bucket at the center of the test box, take out the test piece that has been cured and soaked in water, weigh the test piece with an electronic scale and number it one by one. (4) Measure the test piece and make corresponding records. (5) Put the test piece with the rubber cylinder into the test chamber and inject water into the test piece in the rubber cylinder. (6) Set the corresponding slave parameters and start the machine for operation. (7) Cut off the power supply, keep it clean and fill in the instrument use record after the work.
The measurement process of CABR - RCP9 chloride ion electric flux tester are as the follows: (1) Prepare the test block to ensure that there is enough water for the water saturation test. (2) Put the prepared test blocks into the vacuum chamber of the water saturation machine, and the test blocks shall not overlap to ensure that the vacuum chamber does not leak. (3) Parameter setting. (4) Inject NaCl and NaOH. (5) Carry out the experiment.
According to the standard of test methods for durability, long-term performance and mechanical properties of ordinary concrete, the frost resistance, chloride ion permeability and compressive strength of concrete specimens are tested according to the recommended quick freezing method and electric flux method, and the 28d chloride ion permeability resistance is emphatically analyzed.
3. The results and analysis
3.1. The influence of mineral admixture on chloride ion permeability
3.1.1. The influence of fly ash on chloride ion permeability
HPC electric flux is affected by the content of fly ash, as shown in Fig. 1. It can be seen from Fig. 1 that the HPC electric flux at the age of 28 days decreases first and then increases with the increase of fly ash content. The HPC electric flux reaches the minimum 698C when the fly ash content is 25 % (Specimen number: 12#), and the chloride ion permeability resistance is the best under this condition. This is because the filling effect and polarization effect reach the best when fly ash is mixed with 25 %, and the micro structure of HPC is improved to a great extent. The interior of HPC is denser, so the power on is small. The power on increases to 1350C, when 45 % fly ash is added. To sum up, the increase of fly ash content slows the hydration reaction of protozoan, reduces the hydration degree of gel material, makes the compactness of HPC worse and brings negative effects. The increase of HPC power on the contrary reduces the resistance to chloride ion penetration.
The HPC electric flux at the age of 90 days decline at first and then tends to be gentle. The electric flux of HPC reaches the minimum 290C, when the content of fly ash is 35 % (Specimen number: 13#). The electric flux of 90d (Specimen number: 13#) decreases by 77.5 % compared with 28d and 68.5 % compared with that without fly ash (Specimen number: 1#). The electric flux increases slightly when the content of fly ash exceeds 35 %.
Fig. 1Influence of fly ash content on HPC electric flux
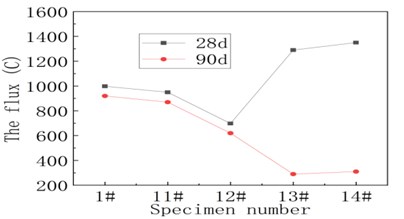
Fig. 2Influence of slag powder content on HPC electric flux
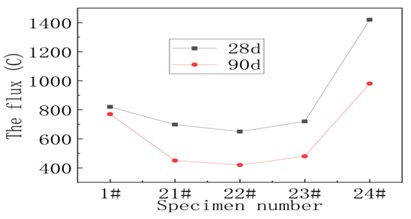
3.1.2. The influence of slag powder on chloride ion permeability
HPC electric flux is affected by the content of slag powder, as shown in Fig. 2. It can be seen from the Fig. 2 that the HPC electric flux at the age of 28d and 90d decreases first and then increases with the increase of slag powder content. The HPC electric flux reaches the minimum when the slag powder content is 25 % (Specimen number: 22#), and the electric flux at the age of 28 days and 90 days are 650C and 420C, respectively. The chloride ion permeability resistance is the best with the slag powder content of 25 %. HPC electric flux reaches the maximum when 45 % slag powder is added, and the electric flux at the age of 28 days and 90 days are 1420C and 980C, respectively, which increases by 73.2% and 27.3 % compared with those without slag powder. The 90d HPC power of 1#, 21#, 22#, 23#, 24# is less than their 28d power, and the 90d and 28d HPC power without slag powder is less than that with slag powder. The electric flux of HPC decreased most significantly when 45 % slag powder was added, and the electric flux of 90d decreased by 31 % compared with 28d.
Although the polarization reaction of slag powder is slow, it can improve the composition of hydration products and the internal micro structure of HPC, that is, the strength and porosity of HPC mixed with slag powder have decreased at the same age, further reduce the electric flux of HPC and improve its resistance to chloride ion corrosion. In addition, the morphology of mechanically ground slag particles is mostly irregular, and the further increase of the content will lead to the decrease of the compactness of the gel system. Therefore, the HPC flux shows a downward or upward trend with the increase of the content. The reaction degree of slag powder will increase relatively with the increase of age, so as to increase the structural compactness. Therefore, the electric flux at the age of 28 days is smaller than that at the age of 90 days under the same dosage.
3.1.3. The influence of fly ash and slag powder mixture on chloride ion permeability
Keep the content of mineral admixtures and the total amount of cementation materials unchanged, change the ratio of slag powder to fly ash, and test its resistance to chloride ion permeability. The influence of fly ash and slag powder mixture on HPC electric flux is as shown in Fig. 3.
The results show that when 50 % mineral admixture is added, the electric flux of HPC gradually decreases with the increase of the proportion of fly ash. The electric flux of HPC at the age of 28 days and 90 days is the smallest when the ratio of slag powder to fly ash is 15:35. The electric flux at the age of 28 days and 90 days is 680C and 280C, respectively under this condition. The HPC flux will increase again when the content of fly ash accounts for 100 % of the mineral admixture. The HPC flux at the age of 28 days and 90 days of 35# test specimen increase by 113.2 % and 3.57 % compared with 34# test specimen.
To sum up, the superposition effect and gradation effect of cementation materials are different. The gradation of cementation system is the best, when the ratio of slag powder to fly ash is 15:35. The gross pore diameter inside the structure is the smallest and the compactness is the highest, so the electric flux of HPC is the smallest and its resistance to chloride ion permeability is the most consumed under this condition.
Fig. 3Influence of fly ash and slag powder mixture on HPC electric flux
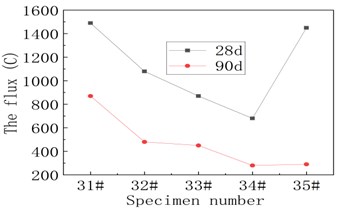
Fig. 4Influence of mineral admixture on the HPC compressive strength
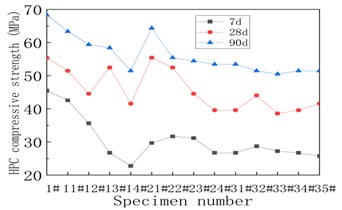
3.2. The influence of mineral admixture on compressive strength
HPC compressive strength can be calculated with Eqs. (1) and (2) [7]:
where fc(t) is the compressive strength at age of t, βc(t) is the compressive strength development coefficient at age of t, c is the coefficient related to the nature of concrete.
The influence of mineral admixture on the HPC compressive strength is as shown in Fig. 4. The results show that the compressive strength of HPC in each group decreases with the increase of the output of mineral admixture. According to the in-depth analysis, the cement hydration product Ca (OH) 2 needs to react with slag powder and fly ash to produce gel hydration products, and the cement hydration rate is higher than this reaction rate. Therefore, replacement of the cement with the slag powder and fly ash will reduce hydration rate of the gel system. Under the condition that the amount of mineral admixture and the total amount of gel materials remain unchanged, the compressive strength of 31#, 32#, 33#, 34#, 35# changes slightly in the same age, and the strength at each age is significantly lower than that of 1#, which also reduces the hydration rate of the cementation material with the larger amount of mineral admixture.
3.3. The influence of mineral admixture on frost resistance
The influence of mineral admixtures on the relative dynamic elastic modulus of HPC is shown in Fig. 5. The influence of mineral admixtures on the mass loss rate of HPC freeze-thaw cycle is shown in Fig. 6. Where “–10” means that the test is stopped when the relative dynamic elastic modulus is reduced to 60 %. The air content is uniformly set as (2.5 ± 0.2) %, and the mass and dynamic elastic modulus of HPC are measured every 25 freeze-thaw cycles in the test.
It can be seen from Fig. 5 and Fig. 6 that the frost resistance grade of 1# test piece reaches F200, and this group has the best frost resistance. The frost resistance of HPC gradually deteriorates with the increase of content when slag powder or fly ash is added alone. HPC can withstand 75 freeze-thaw cycles, and can reach F50 frost resistance grade according to the evaluation standard, when the content of slag powder or fly ash is 40 % of cementation material. The HPC frost resistance grade is F50when the total amount of slag powder and fly ash is 40 % of cementation material with the freeze-thaw cycle data of 31#, 32#, 33#, 34# and 35# test pieces. The surface of HPC is eroded by cement slurry, but the overall condition is good, and the mass loss rate does not exceed the standard of 5 % after the freeze-thaw cycle. Therefore, the decrease of dynamic elastic modulus is the main form of HPC failure.
Fig. 5The influence of mineral admixtures on the relative dynamic elastic modulus of HPC
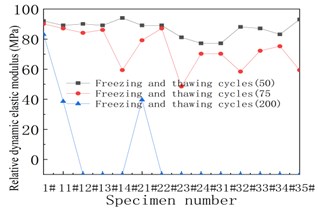
Fig. 6The influence of mineral admixtures on the mass loss rate of freeze-thaw cycle Mass loss rate
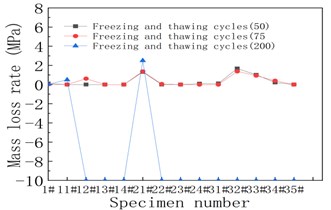
4. Conclusions
This paper studies the influence of different mixing methods of slag powder and fly ash on the frost resistance and chloride ion permeability of high-performance concrete, which can provide basic data for optimizing the mix design of high-performance concrete in underwater engineering. The main conclusions are as follows:
1) The compressive strength of HPC28d and HPC90d gradually decreases with the increase of the content when the cement is replaced with slag powder or fly ash with keeping the total amount of cementation materials and water binder ratio unchanged. The compressive strength of HPC at each age is lower than that of the 1# test piece.
2) The HPC electric flux first decreases and then increases with the increase of fly ash content when adding fly ash alone. The HPC electric flux reaches the minimum 680C (28d) when the fly ash content is 25 %, and the chloride ion permeability resistance is the best under this condition. The electric flux of 90d (Specimen number: 13#) decreases by 77.5 % compared with 28d and 68.5 % compared with that without fly ash (Specimen number: 1#). The HPC flux decreases first and then increases with the increase of slag powder content when adding slag powder alone. The HPC flux reaches the minimum 650C (28d) when the slag powder content is 25 %, and the chloride ion permeability resistance is the best under this condition.
3) The electric flux of HPC gradually decreases with the increase of the proportion of fly ash when 40 % mineral admixture is added. The electric flux of HPC at the age of 28 days and 90 days is the smallest when the ratio of slag powder to fly ash is 15:35, and the resistance to chloride ion permeability is the best under this condition. The HPC flux at the age of 28 days and 90 days of 35# test specimen increase by 113.2 % and 3.57 % compared with 34# test specimen.
4) The frost resistance of HPC is the best without mineral admixture keeping the water binder ratio and content unchanged, and the frost resistance grade reaches F200. The frost resistance of HPC gradually deteriorates with the increase of content, when slag powder or fly ash is added alone. The frost resistance grade of HPC is F50 when slag powder and fly ash are added together with a total amount of 40 % amount is 40 % the cementation materials, and the frost resistance grade does not change with the change of the mixing proportion.
5) Adding an appropriate amount of slag powder and fly ash into the concrete can improve the anti chloride ion permeability to a certain extent, but it is not conducive to the frost resistance of the concrete. For the concrete with frost resistance requirements, the output of mineral admixture should be determined through tests. An appropriate amount of air end training agent can be added in order to enhance its frost resistance.
References
-
C. W. Xu, J. Gao, Y. Zhang, and M. H. Yang, “Influence of mineral blending materials on the concrete penetrability with orthogonal experiment,” Concrete, No. 3, pp. 101–110, 2012.
-
B. G. Luo and H. Y. Qin, “Influence of Mineral Admixture on Anti-chloride Ion Permeability of Recycled Aggregate Concrete,” Highway Engineering, Vol. 39, No. 5, pp. 114–118, 2014.
-
J. Liu and Y. G. Wang, “Effects of compound admixtures with steel slag on anti-chloride ion penetration performance of high performance concrete,” China Concrete and Cement Products, No. 8, pp. 9–12, 2013, https://doi.org/10.19761/j.1000-4637.2013.08.003
-
H.-B. Ly, T.-A. Nguyen, and B. T. Pham, “Investigation on factors affecting early strength of high-performance concrete by Gaussian Process Regression,” PLOS ONE, Vol. 17, No. 1, p. e0262930, Jan. 2022, https://doi.org/10.1371/journal.pone.0262930
-
M. A. Al-Osta, S. Ahmad, M. K. Al-Madani, H. R. Khalid, M. Al-Huri, and A. Al-Fakih, “Performance of bond strength between ultra-high-performance concrete and concrete substrates (concrete screed and self-compacted concrete): An experimental study,” Journal of Building Engineering, Vol. 51, p. 104291, Jul. 2022, https://doi.org/10.1016/j.jobe.2022.104291
-
N. S. Ha, S. S. Marundrury, T. M. Pham, E. Pournasiri, F. Shi, and H. Hao, “Effect of grounded blast furnace slag and rice husk ash on performance of ultra-high-performance concrete (UHPC) subjected to impact loading,” Construction and Building Materials, Vol. 329, p. 127213, Apr. 2022, https://doi.org/10.1016/j.conbuildmat.2022.127213
-
P. R. Gadag, H. M. Somasekharaiah, V. Ghorpade, and H. S. Rao, “Evaluation of strength parameters of metakaolin and nanosilica incorporated high-performance concrete,” in IOP Conference Series: Earth and Environmental Science, Vol. 822, p. 01202, 2021, https://doi.org/10.1088/1755-1315/822/1/01202
About this article
This work is supported by Research Project of China Power Construction Group East China Survey Design & Research Institute Company Limited (KY2020-JG-32-01-2021).