Abstract
Conduct alkali silica reaction (ASR) tests on concrete by using cement with different alkali contents and according to different test standards. The influence of cement alkali content on the alkali-silica reaction of concrete was explored, and the effects of different test methods on the results of alkali-silica reaction tests were compared. The results indicate that: the type of cement and the testing method used have no significant impact on the experimental results of the alkali silica reaction. The rate of alkali silica reaction accelerates with the increase of cement alkali content. When the alkali content of cement is greater than 2.0 %, there is no potential harm of alkali silica reaction in the aggregate, which will cause harm of alkali silica reaction. The research conclusion can provide reference for the control value of alkali content in engineering cement.
1. Introduction
Alkali aggregate reaction (AAR) refers to the reaction between the alkali activated aggregate (solid phase) in concrete and the alkali solution (liquid phase) in pore solution. It mainly refers to the chemical reaction of alkaline components (Na2O+K2O) released from cement, mineral admixture, chemical admixture, external environment and the alkali active mineral components in aggregate [1]. After the volume expansion of reaction products, stress concentration is generated in the concrete, which induces the expansion or cracking of concrete and reduces the mechanical properties and durability of concrete [2]. AAR damage of concrete usually aggravates reinforcement corrosion, concrete salt corrosion, concrete carbonization and so on. This poses a serious threat to the safe operation of concrete buildings [3-5]. It can be seen that the study of AAR is of great significance to improve the durability of concrete and control the engineering quality.
Since Stanton discovered the harm of concrete alkali aggregate reaction in 1940 [6], scholars at home and abroad have carried out a large number of experimental research and formed a series of standard test methods and evaluation criteria. Among them, Accelerated Mortar Bar Test Method is an accurate and reliable inspection method. Different standards have different requirements for the initial alkali content of cement required for alkali aggregate reaction test [7], and most of the tests are carried out for conventional single cement [8-9]. At present, there are few studies on the effects of different cement varieties and different alkali content of cement on alkali aggregate reaction.
The alkali aggregate reaction of concrete can be divided into alkali silicate reaction (ASR) and alkali carbonate reaction (ACR) according to the reaction mechanism [10]. Here, a comparative test of rapid ASR is carried out for cement with different alkali content and different aggregates. The influence of cement alkali content on aggregate alkali silica reaction under different standards was studied. The alkali content conditions of ASR hazards of aggregates are discussed, which are those aggregates without potential ASR hazards and those aggregates that cannot determine whether there are potential ASR hazards. It provides a basis for the selection of engineering cement and the control of alkali content in alkali silica reaction test.
2. Test overview
2.1. Raw materials
Three types of cement are used. C1 stands for P·I 42.5 portland cement. C2 stands for P·O 42 5 ordinary portland cement. C3 stands for P·MH 42.5 medium heat portland cement. Three types of sand are used as aggregate, including natural sand (S1), artificial sand (S2) and artificial sand (S3). The chemical composition of cement is shown in Table 1. The determination results of aggregate activity are shown in Table 2.
Table 1Chemical composition of cement
Main chemical compositions (%) | |||||
Varieties | SiO2 | Al2O3 | Fe2O3 | CaO | MgO |
C1 | 21.14 | 4.69 | 3.15 | 64.02 | 2.57 |
C2 | 24.54 | 4.39 | 4.00 | 57.16 | 1.48 |
C3 | 21.08 | 2.81 | 4.78 | 61.28 | 1.76 |
Varieties | fCaO | SO3 | Na2Oeq | Loss on ignition | |
C1 | 0.92 | 2.09 | 0.56 | 1.36 | |
C2 | 0.65 | 1.38 | 0.49 | 4.38 | |
C3 | 0.11 | 2.14 | 0.34 | 1.57 |
Table 2Mechanical performance indicators of cement
Varieties | S1 | S2 | S3 |
Preliminary ASR test results | Non-potential ASR hazard aggregate | Cannot be determined as potential ASR hazard aggregate | Potential ASR hazard aggregate |
2.2. Test scheme
Three kinds of cement and three kinds of aggregate were used for the comparative test of rapid alkali silica reaction. The biggest difference between the two standards is whether to adjust the initial alkali content of cement. Therefore, the initial alkali content of cement without adjustment is called standard Ⅰ. If the initial alkali content of cement needs to be adjusted to 0.9 %±0.1 %, it is called standard Ⅱ. The comparative test scheme are shown in Table 3.
Table 3Test scheme
Cement varieties | Alkali contents of cement (%) | Types of aggregate |
C1 | 0.56 (original) | S1, S2, S3 |
1.0 (adjusted) | ||
1.2 (adjusted) | S1, S2 | |
1.5 (adjusted) | ||
2.0 (adjusted) | ||
C2 | 0.49 (original) | S1, S2, S3 |
1.0 (adjusted) | ||
C3 | 0.34 (original) | |
1.0 (adjusted) |
According to the scheme in Table 3, the alkali activity test is carried out by Accelerated Mortar Bar Test Method, and the expansion rate is calculated according to Eq. (1), accurate to 0.001 %:
where εt is the expansion rate (%) of the specimen at the age of t; Lt is the length of the specimen at the age of t (mm); L0 is the reference length of the specimen (mm); Δ is the probe length (mm). Take the average value of the measured values of each group of specimen as the expansion rate of this group. The evaluation criteria are as follows:
When the 14 d expansion rate is less than 0.1 %, it can be determined that there is no potential harm of alkali silica reaction in most cases;
When the 14 d expansion rate is greater than 0.2 %, it can be determined that there is potential harm of alkali silica reaction;
When the 14 d expansion rate is 0.1 %-0.2 %, the potential harm of alkali silica reaction cannot be finally determined.
3. Analysis of test results
3.1. Analysis of Influence of different test standards on ASR
According to the two kinds of test standards, the rapid alkali silica reaction comparative test is carried out for different kinds of cement and aggregate. The test results are shown in Table 4. Fig. 1 to Fig. 3 show the comparison of mortar expansion rates of aggregate S1 to S3 under different cement and test standards.
Table 4Comparative test results of rapid alkali silica reaction
Specimen Num | Alkali content of cement (%) | Expansion rate of mortar bar at different ages (%) | |||
3 d | 7 d | 14 d | 28 d | ||
C1-Ⅰ-S1 | 0.56 | 0.011 | 0.025 | 0.049 | 0.087 |
C1-Ⅱ-S1 | 1.00 | 0.013 | 0.026 | 0.050 | 0.086 |
C2-Ⅰ-S1 | 0.54 | 0.014 | 0.027 | 0.042 | 0.077 |
C2-Ⅱ-S1 | 1.00 | 0.014 | 0.028 | 0.044 | 0.079 |
C3-Ⅰ-S1 | 0.34 | 0.013 | 0.026 | 0.046 | 0.078 |
C3-Ⅱ-S1 | 1.00 | 0.014 | 0.028 | 0.045 | 0.080 |
C1-Ⅰ-S2 | 0.56 | 0.068 | 0.128 | 0.178 | 0.268 |
C1-Ⅱ-S2 | 1.00 | 0.065 | 0.132 | 0.183 | 0.266 |
C2-Ⅰ-S2 | 0.54 | 0.066 | 0.132 | 0.183 | 0.254 |
C2-Ⅱ-S2 | 1.00 | 0.064 | 0.133 | 0.180 | 0.259 |
C3-Ⅰ-S2 | 0.34 | 0.054 | 0.116 | 0.160 | 0.248 |
C3-Ⅱ-S2 | 1.00 | 0.057 | 0.121 | 0.164 | 0.251 |
C1-Ⅰ-S3 | 0.56 | 0.035 | 0.148 | 0.281 | 0.479 |
C1-Ⅱ-S3 | 1.00 | 0.037 | 0.151 | 0.293 | 0.483 |
C2-Ⅰ-S3 | 0.54 | 0.045 | 0.139 | 0.273 | 0.492 |
C2-Ⅱ-S3 | 1.00 | 0.043 | 0.142 | 0.270 | 0.495 |
C3-Ⅰ-S3 | 0.34 | 0.029 | 0.132 | 0.267 | 0.483 |
C3-Ⅱ-S3 | 1.00 | 0.034 | 0.139 | 0.272 | 0.486 |
Notes: The specimen number such as “C1-Ⅰ-S1” stands for the cement variety is C1, the test standards is Ⅰ, and the type of aggregate is S1. |
From Fig. 1 to Fig. 3, it can be seen that the type of cement has a significant impact on the expansion rate of mortar specimens, and the same type of cement has different effects on the expansion rate of mortar specimens under different aggregates. The test standards have little impact on the expansion rate test results of aggregates. That is, the alkali content of cement has a relatively small impact on the determination of aggregate alkali activity.
For natural sand S1, rapid alkali silica reaction was carried out according to standard Ⅰ, and the 14 day expansion rates of mortar specimens were 0.049 %, 0.042 %, and 0.046 %, respectively. According to standard Ⅱ, rapid alkali silica reaction was carried out, and the expansion rates of the mortar specimens after 14 days were 0.05 %, 0.044 %, and 0.045%, respectively. The maximum value of these 6 experimental results is 0.05 %, the minimum value is 0.042 %, the average value is 0.046 %, and the maximum difference from the average value is 8.7 % of the average value. This indicates that natural sand S1 is an aggregate without potential ASR.
For artificial sand S2, rapid alkali silica reaction was carried out according to standard Ⅰ, and the 14 day expansion rates of mortar specimens were 0.178 %, 0.183 %, and 0.160 %, respectively. According to standard Ⅱ, rapid alkali silica reaction was carried out, and the 14 day expansion rates of mortar specimens were 0.183 %, 0.18 %, and 0.164 %, respectively. The maximum value of these 6 experimental results is 0.183 %, the minimum value is 0.16 %, the average value is 0.175 %, and the maximum difference from the average value is 8.6 % of the average value. This indicates that artificial sand S2 cannot be determined as an aggregate with potential ASR hazards.
For artificial sand S3, rapid alkali silica reaction was carried out according to standard Ⅰ, and the 14 day expansion rates of mortar specimens were 0.281 %, 0.273 %, and 0.267 %, respectively. According to standard Ⅱ, rapid alkali silica reaction was carried out, and the 14 day expansion rates of mortar specimens were 0.293 %, 0.27 %, and 0.272 %, respectively. The maximum value of these 6 experimental results is 0.293 %, the minimum value is 0.267 %, the average value is 0.276 %, and the maximum difference from the average value is 6.2 % of the average value. This indicates that artificial sand S3 is a potentially hazardous aggregate for ASR.
Based on the above analysis, the influence of cement varieties on the alkali activity of aggregates is relatively small. When the alkali content of cement is adjusted to 1.0 %, the alkali activity test results of various aggregates are basically consistent. Therefore, when the alkali content does not exceed 1.0 %, the impact on the alkali activity of aggregates is relatively small and may not be considered in engineering.
Fig. 1Comparison of mortar expansion rates of aggregate S1
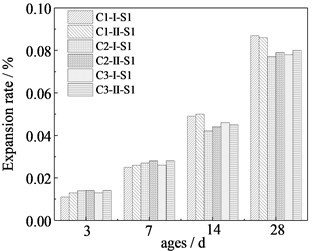
Fig. 2Comparison of mortar expansion rates of aggregate S2
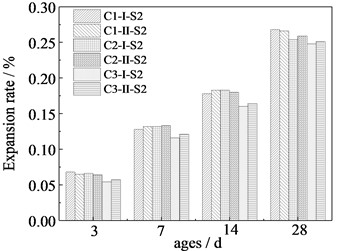
Fig. 3Comparison of mortar expansion rates of aggregate S3
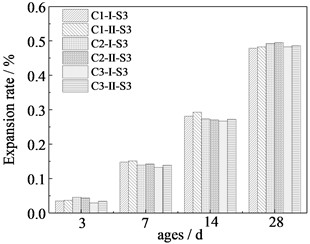
3.2. Influence of alkali content of cement on ASR
Combined with the research results in part A, the influence of different cement alkali content on the ASR of mortar specimens was studied for C1 kinds of cement. The test results of ASR of mortar specimens under different cement alkali content are shown in Table 5.
It can be seen from Table 5 that when the alkali content of cement exceeds 1.0 %, too much alkali in cement accelerates the reaction with the active components in the aggregate. The expansion rate of mortar bar specimen shows an increasing relationship with the alkali content of cement, and the increasing relationship becomes more and more obvious with the increase of alkali content of cement.
As shown in Fig. 4(a) and Fig. 4(b), the variation laws of expansion rate of S1 and S2 mortar bars at different ages under different cement alkali content are given respectively. For non-potential ASR hazard aggregates, ASR hazards will occur when the alkali content of cement exceeds 2.0 %. For aggregates cannot be judged to have potential alkali silica reaction, when the alkali content of cement exceeds 1.2 %, the harm of alkali silica reaction will occur.
Table 5The test results of ASR of mortar specimens under different cement alkali content
Specimen Num | Expansion rate of mortar bar at different ages (%) | |||
3 d | 7 d | 14 d | 28 d | |
C1-1.0-S1 | 0.013 | 0.026 | 0.050 | 0.086 |
C1-1.2- S1 | 0.025 | 0.051 | 0.095 | 0.157 |
C1-1.5- S1 | 0.049 | 0.096 | 0.160 | 0.237 |
C1-2.0- S1 | 0.081 | 0.152 | 0.258 | 0.386 |
C1-1.0-S2 | 0.065 | 0.132 | 0.183 | 0.266 |
C1-1.2-S2 | 0.087 | 0.145 | 0.201 | 0.298 |
C1-1.5-S2 | 0.131 | 0.177 | 0.238 | 0.365 |
C1-2.0-S2 | 0.185 | 0.268 | 0.360 | 0.491 |
Fig. 4Variation law of mortar bar expansion rate of sand with different cement alkali content at different ages
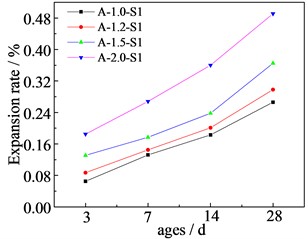
a) Natural sand S1
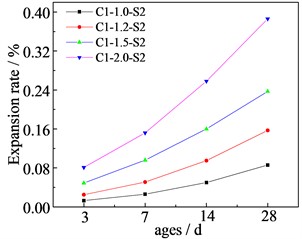
b) Artificial sand S2
This is because some alkali substances in concrete or mortar participate in the hydration reaction to generate cementitious materials, while others are adsorbed on the surface of particles, leaving a large amount of OH- present inside the concrete or mortar. After these OH- ions participate in the alkali silica reaction, there is still residual, and the formed osmotic pressure still exists, leading to the reaction of active ingredients in the aggregate all the time, which eventually leads to the increase of the generated expansive products, thus causing the expansion of concrete or mortar. This also explains why it is suspected that after increasing the alkali content of the cement, the expansion rate of the mortar rod increases significantly, until there is a significant harm of alkali aggregate reaction. However, non-reactive aggregates are not devoid of any active ingredients but cannot exhibit significant expansion in general environmental conditions. Due to the increase of alkali content in cement, a small amount of active ingredients continuously reacts with alkali under the action of Osmotic pressure until they are completely consumed. At this point, if the active ingredients in the non-active aggregate reach a certain amount, that is, if the generated expansive products reach a certain amount, it will also cause a more obvious alkali silica reaction. It is important that even under the action of Osmotic pressure, the internal structure of non-active ingredients will expand, so for non-active aggregates, obvious alkali aggregate reaction hazards can also occur under the condition of having a certain amount of active ingredients and a high alkali content.
4. Conclusions
The influence of cement variety on the results of rapid alkali silica reaction test of aggregates can be ignored, that is, for active aggregates, suspected active aggregates, and non-active aggregates, whether the alkali content of cement is adjusted has little impact on the results. When the alkali content of cement does not exceed 1.0 %, both Standard Ⅰ and Standard Ⅱ methods are applicable.
When the alkali content of cement exceeds 1.0 %, the alkali content can accelerate the ASR. When the alkali content of cement exceeds 1.2 %, Aggregate cannot be determined as potential ASR hazard will produce ASR hazard. When the alkali content of cement exceeds 2.0 %, aggregate without potential activity will cause ASR hazard.
References
-
D. Y. Lu, Z. Z. Xu, and M. S. Tang, “ASR models for siliceous aggregates with different texture and structure characteristics,” (in Chinese), Journal of the Chinese Ceramic Society, Vol. 30, No. 2, pp. 149–154, 2002.
-
H. F. Wen and H. B. Zhang, “Review of alkali-aggregate reaction and supplementary cementious materials (SCMs) on its inhibition mechanism,” (in Chinese), Bulletin of the Chinese Ceramic Society, Vol. 38, No. 6, pp. 1782–1787, 2019.
-
G. B. Yue, H. J. Wei, and C. Guo, “Review on the mechanism of alkali-aggregate reaction and its inhibition measures,” (in Chinese), Low Temperature Architecture Technology, Vol. 43, No. 11, pp. 63–67, 2021.
-
H. Q. Yang, P. X. Li, and X. Chen, “Summary of research on alkali aggregate reaction in hydraulic concrete,” (in Chinese), Journal of Yangtze River Scientific Research Institute, Vol. 31, No. 10, pp. 58–62, 2014.
-
D. M. Jang and M. Q. Zhang, “Summarize problems about alkali-aggregate reaction in concrete,” (in Chinese), Industrial Construction, Vol. 31, No. 7, pp. 45–47, 2001.
-
W. Wang, L. X. Liu, and X. Zhao, “Experimental study on inhibition of fly ash alkali aggregate reaction (in Chinese),” (in Chinese), Concrete, No. 3, pp. 74–77, 2019.
-
Y. C. Jiang, Q. Wang, and Y. Wang, “Review of alkali-aggregate reaction test methods and evaluation (in Chinese),” (in Chinese), China Building Materials Science and Technology, Vol. 26, No. 3, pp. 1–5, 2017.
-
“CSA A23.2-25A. Test method for detection of alkali-silica reactive aggregate by accelerated expansion of mortar bars,” Canadian Standards association, 1994.
-
D. Y. Lu, Z. Z. Xu, Y. N. Lv, and M. S. Tang, “A Review on the testing methods for identifying the ASR reactivity of aggregate,” Journal of Nanjing University of Chemical Technology, No. 2, pp. 87–93, 1998.
-
C. H. Meng and B. Zhao, “Analysis of alkali aggregate reaction in concrete,” Yellow River, Vol. 29, No. 2, pp. 70–71, 2007.
About this article
The authors have not disclosed any funding.
The datasets generated during and/or analyzed during the current study are available from the corresponding author on reasonable request.
The authors declare that they have no conflict of interest.