Abstract
To study the effects of different mixing processes on the mixing uniformity of cement-stabilized macadam, three mixing processes, namely, ordinary static mixing, vibratory mixing and vibratory machine off-vibration mixing, are compared and studied by visual identification, coarse aggregate distribution statistics in core sample section, mixture sieving and cement dosage titration. The results show that the cement slurry produced by the vibratory mixing process has the best adhesion effect on coarse aggregate, and its variability in the number of coarse aggregate distribution in the core sample section, the key sieve passing rate of the aggregate and variability of cement dosage titration are the lowest. In conclusion, vibratory mixing can improve the homogeneity of cement-stabilized macadam, thus improve internal friction resistance and cohesion of the mixture, and enhance the road performance.
1. Introduction
Cement-stabilized macadam is the main basic semi-rigid material for all levels of highways in China, for its advantages of high strength, good performance and low engineering cost. However, with the rapid growth of highway traffic in China in recent years and the increasingly serious phenomenon of overloading transportation, the semi-rigid base asphalt pavements in various parts of China have different degrees of early damage, such as cracks, loose, mud, etc., among which the cracks are especially prominent [1-4]. Therefore, to figure out a method for effective crack prevention and reduction has become vital in improving the durability of semi-rigid subgrade asphalt pavement.
According to the engineering practice experience and research results of semi-rigid base construction in China [5, 6], the major reasons for cracks in cement-stabilized macadam base can be divided into internal reasons and external reasons. The internal reasons include gradation composition of cement-stabilized macadam, water content of mixture and cement dosage, which will inevitably cause a certain degree of humidity shrinkage cracking and temperature shrinkage cracking. The main external cause is mixing uniformity, both in microscopic and macroscopic. Due to the limitation of the mixing process, cement and water are not fully combined or hydrated, and hydrates are not fully dispersed, which can lead to poor homogeneity of the water-stabilized mixture, resulting in many vulnerable spots in the water-stabilized subgrade, thus leading to early damage of the semi-rigid subgrade. In recent years, domestic scholars have mostly focused on improving the road performance of cement-stabilized macadam mixture by studying the internal factors, such as optimizing the gradation, adjusting the cement dosage and water content, etc. [7-13], which have improved the road performance and durability of cement-stabilized macadam to some extent.
In this paper, external influential factors of cement-stabilized macadam semi-rigid subgrade are studied based on on-site construction. By comparing static mixing, vibratory mixing and vibratory machine off-vibration mixing, the influence mechanism of mixing homogeneity on the performance of cement-stabilized macadam road is studied. The results can better guide the engineering applications.
2. Vibration machine and vibration characteristics
The vibration machine adopts continuous double horizontal shaft vibration mixing mode. During the continuous mixing process, the vibration transmission device transmits the vibration directly to the two mixing shafts by an exciter, which makes the two mixing shafts vibrate and stir at the same time. This strengthens the mixing effect and improves the micro-homogeneity of the mixture, so a more desirable mixing effect is obtained. In the process of vibration mixing, due to the vibration effect applied while mixing, the cement particles in the mixture are in a flutter state, and the water film on the surface of cement particles will be damaged under a certain amplitude, which destroys the viscous connection between cement particles, greatly reduces its internal friction, and enables the cement particles to be distributed quickly and evenly.
3. Materials
3.1. Technical performance of raw materials
Four blocks of aggregates produced by Yunnan Desheng quarry were used. The sizes are 0-5 mm, 5-10 mm, 10-20 mm and 20-30 mm respectively, with the maximum particle size being 31.5 mm. The technical performances are shown in Tables 1 and Table 2. P·S·A 32.5 slag silicate cement is adopted, and the technical performance test results are shown in Table 3, which meets the requirements of General Silicate Cement GB 175-2007.
Table 1Technical performance of coarse material
No. | Size (mm) | Crushing value (%) | Apparent density (g·cm-3) | Stacking density (g·cm-3) | Macadam < 0.075 (%) | Needle macadam (%) | Water absorption (%) |
1# | 20-30 | 19.5 | 2.826 | 1.42 | 0.3 | 4.4 | 0.38 |
2# | 10-20 | 2.832 | 1.46 | 0.6 | 5.9 | 0.62 | |
3# | 5-10 | 2.839 | 1.48 | 0.7 | 7.3 | 0.82 |
Table 2Technical performance of fine material
No. | Size (mm) | Apparent density (g·cm-3) | Stacking density (g·cm-3) | Sand equivalent | Water absorption (%) | Liquid limit (%) | Plastic Index |
4# | 0~5 | 2.826 | 1.691 | 69 | – | 18.3 | 2 |
3.2. Gradation settings of mixture
The ratio of cement-stabilized macadam mixture used in this paper is set as follows: 1) The macadam with the size of 0-5 mm is considered fine macadam. The proportion of coarse macadam is 75 % and the fine macadam is 25 %. 2) In coarse macadam, the proportion of 20-30 mm macadam is 50 %, for 10-20 mm is 30 %, and for 5-10 mm is 20 %. 3) The maximum dry density is 2.287 g/cm3. 4) When the dosage of cement is 3.5 %, the best moisture content is 4.8 %.
The gradation settings of mixture are shown in Table 4.
Table 3Technical performance of cement
Tested items | Result | Criterion | ||
Fineness: 0.08 mm square hole sieving residue (%) | 1.8 | ≤ 10 | ||
Standard water consumption (%) | 25.0 | – | ||
Coagulation Time | Initial setting time (min) | 361 | ≥ 180 | |
Final setting time (min) | 473 | ≥ 360 | ||
Soundness by Le Chatelier test (mm) | 2.0 | ≤ 5.0 | ||
Mortar strength | Fracture resistance | 3 d/MPa | 3.7 | ≥ 2.5 |
28 d/MPa | 8.3 | ≥ 5.5 | ||
crushing resistance | 3 d/MPa | 17.2 | ≥ 10.0 | |
28 d/MPa | 37.1 | ≥ 32.5 |
Table 4Gradation Settings of mixture
Sieving (mm) | 31.5 | 19.0 | 9.5 | 4.75 | 2.36 | 0.6 | 0.075 |
Upper limit (%) | 100 | 86 | 58 | 32 | 28 | 15 | 5 |
Lower limit (%) | 100 | 68 | 38 | 22 | 16 | 8 | 0 |
Designed gradation (%) | 100 | 75.2 | 49.4 | 26.6 | 20.6 | 11.7 | 4.6 |
4. Experiment
4.1. Experiment design
Ordinary static mixing, vibration mixing, and vibration machine off-vibration mixing are adopted to investigate the influence of different mixing processes on the mixing homogeneity of cement stabilized macadam mixtures. The vibration machine off-vibration mixing means the vibration function of vibration machine is turned off. The static mixing machine adopted is WCB600T, and the device for vibration mixing and vibration machine off-vibration mixing is WZD600.
4.2. Experiment methods
(1) Visual identification method. Visual identification can identify the uniformity of coarse macadam and mixtures, and is usually used as a baseline for other quantitative identification methods, though it cannot be used for fine macadam [15]. During the test road paving, the mixtures mixed by the three mixing processes were taken samples from the material truck respectively for visual identification to check homogeneity.
(2) Macadam distribution in core sample section. Seven days after the test road compaction, the three mixing methods paving sections were randomly drilled 9 core samples, and then cut the core sample cross-section at the same location (2 cm from the top of the core sample). Then, count the numbers of macadam with the size of 10-20 mm and 20-30 mm in each sample for macroscopic uniformity evaluation of the mixture.
(3) Mixture Sieving. Take samples of mixtures by three mixing processes from paver fabricator for eight times and the interval is 10 minutes. Wash, dry and sieve the samples to get the passing rate of specific sieving holes with the sizes of 19 mm, 9.5 mm and 4.75 mm respectively.
(4) Cement EDTA titration. The test process refers to JTG E51-2009 “Test Procedures for Inorganic Bonding Material Stabilization of Highway Engineering” and related specifications. Eight samples are selected for parallel experiments. The mixing homogeneity can be evaluated by the average value and standard deviation of titration dose.
5. Results
5.1. Visual identification
Through the visual identification, we found that the coarse, medium and fine macadam are more uniform in the vibration mixing mixture, with many medium and small-sized macadam wrapped around the large-sized macadam, and the medium and small-sized aggregates are more evenly distributed among the large-sized macadam. However, in mixture mixed by vibration machine off-vibration mode, the coarse macadam is rarely wrapped, and the medial and small macadam are comparatively concentrated. In static mixing mixture, the coarse and small macadam are more than medium macadam, and the coarse macadam are rarely wrapped. From this perspective, vibration mixing is superior to the other two mixing processes.
5.2. Macadam distribution in core sample section
The statistic of coarse macadam distribution in core sample section of the three mixing processes is recorded in Tables 5-7. The core sample section is shown in Fig. 1.
Table 5Number of 20-30 mm macadam in core sample section
Mixing processes | Number | ||||||||
1 | 2 | 3 | 4 | 5 | 6 | 7 | 8 | 9 | |
Vibration mixing | 3 | 5 | 3 | 2 | 1 | 2 | 3 | 3 | 3 |
Vibration machine off-vibration mixing | 2 | 0 | 0 | 0 | 1 | 0 | 2 | 6 | 5 |
Static mixing | 1 | 0 | 1 | 0 | 4 | 0 | 1 | 1 | 0 |
Table 6Number of 10-20 mm macadam in core sample section
Mixing processes | Number | ||||||||
1 | 2 | 3 | 4 | 5 | 6 | 7 | 8 | 9 | |
Vibration mixing | 14 | 9 | 12 | 11 | 14 | 15 | 13 | 14 | 12 |
Vibration machine off-vibration mixing | 12 | 14 | 8 | 13 | 16 | 16 | 16 | 7 | 13 |
Static mixing | 10 | 18 | 16 | 17 | 10 | 19 | 11 | 16 | 14 |
Table 7Coarse macadam distribution in core sample section
Mixing processes | 20-30 mm | 10-20 mm | 10-30 mm | |||
Mean | Standard deviation | Mean | Standard deviation | Mean | Standard deviation | |
Vibration mixing | 2.8 | 1.093 | 12.7 | 1.871 | 15.4 | 1.424 |
Vibration machine off-vibration mixing | 1.8 | 2.279 | 12.8 | 3.346 | 14.6 | 3.167 |
Static mixing | 0.9 | 1.269 | 14.6 | 3.468 | 15.4 | 2.789 |
Fig. 1Distribution of macadam in core sample section of three mixing processes
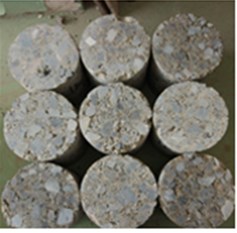
a) Vibration
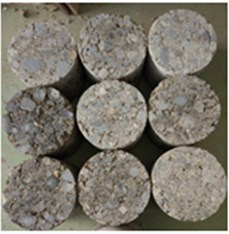
b) Vibration machine off-vibration mixing
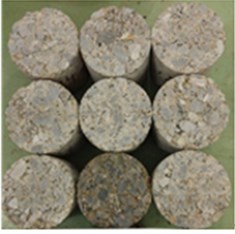
c) Static mixing
It can be seen from Table 7 that the average numbers of coarse macadam (10-30 mm) in core samples by vibration mixing, vibration machine off-vibration mixing, and static mixing are 15.4, 14.6 and 15.4, respectively. The total numbers of coarse macadam differ very little, which can verify that the difference of material sources of the three mixing methods can be ignored. The standard deviations of the three processes are 1.424, 3.167 and 2.789 respectively, which proves that vibration mixing can provide more homogeneous mixture than other two processes. By analyzing Table 5 alone, the 20-30 mm macadam distribution in cross-sections of vibration mixing is comparatively uniform, with almost three macadam in each cross-section. For the other two processes, almost half of the cross-sections have no 20-30mm macadam, while on some cross-sections, 4-6 macadam appeared. So, the 20-30 mm macadam distribution also support that vibration mixing can provide more homogeneous mixture than other two processes. Comparing the distribution of 10-20 mm macadam and 20-30 mm macadam, the 10-20 mm macadam distribution tends to be more uniform with a little difference in total amount of macadam. But the standard deviations are 1.871, 3.346 and 3.368 respectively, which also support that vibration mixing is superior to others.
5.3. Mixture sieving
The passing rates of three mixtures through major sieving holes are shown in Table 8.
In Table 8, the mean values of the passing rate of each key sieve hole show no significant difference, which indicates that the material source of cement-stabilized macadam is stable. However, by comparing the standard deviations of the passage rates, the standard deviation of vibration mixing product is significantly smaller than the other two mixing methods. Compared with vibration machine off-vibration mixing, the deviation coefficients of the three sieve holes in vibration mixing product are reduced by 26.9 %, 19.4 % and 23.6 %. Compared with static mixing, the deviation coefficients of the three sieve holes in vibration mixing product are reduced by 32.7 %, 37.8 % and 33.0 %. The result can support that vibration mixing method can improve the homogeneity of cement-stabilized macadam.
Table 8Passing rate of three mixtures through major sieving holes
Mixing processes | Vibration mixing | Vibration machine off-vibration mixing | Static mixing | ||||||
Size of Sieving hole (mm) | 19 | 9.5 | 4.75 | 19 | 9.5 | 4.75 | 19 | 9.5 | 4.75 |
Passing rate (%) | 74.6 | 48.9 | 25.3 | 76.8 | 50.6 | 23.7 | 77.5 | 44.8 | 27.9 |
72.3 | 48.2 | 24.8 | 73.5 | 50.1 | 28.7 | 74.3 | 47.5 | 22.6 | |
73.5 | 47.8 | 26.7 | 73.4 | 47.3 | 27.2 | 78.9 | 41.3 | 24.8 | |
72.8 | 50.2 | 23.4 | 72.1 | 48.5 | 23.4 | 80.7 | 45.7 | 28.4 | |
75.4 | 46.7 | 26.4 | 72.3 | 46.7 | 26.4 | 81.2 | 42.4 | 26.7 | |
77.2 | 47.2 | 26.8 | 77.4 | 46.2 | 24.1 | 76.6 | 46.3 | 22.9 | |
76.9 | 50.4 | 27.7 | 78.2 | 49.8 | 25.3 | 74.7 | 46.7 | 23.6 | |
74.8 | 47.1 | 24.1 | 73.1 | 46.7 | 27.4 | 75.3 | 42.8 | 25.1 | |
Mean | 74.7 | 48.3 | 25.7 | 74.6 | 48.2 | 25.8 | 77.4 | 44.7 | 25.3 |
Standard deviation | 1.674 | 1.316 | 1.392 | 2.293 | 1.632 | 1.823 | 2.488 | 2.117 | 2.078 |
5.4. Cement EDTA titration
The experiment is conducted on the road with a paved cement dose of 3.5 %. When comparing the homogeneity of cement distribution under the three mixing methods, the deviation of the titration results from the set cement dose of 3.5 % was not compared. Then compare the standard deviations of eight samples for each group of tests. The titration results of cement stabilized macadam mixture under the three different mixing methods are shown in Table 9.
In Table 9, the standard deviations of cement dose for the three mixing methods (vibration mixing, vibration machine vibration mixing, and ordinary static mixing) are 0.074, 0.139, and 0.155, respectively. The standard deviation of vibration mixing is 46.8 % lower than vibration machine off-vibration mixing, and 52.3 % lower than static mixing, showing that cement-stabilized macadam is more uniform in vibration mixing product. The reason is that the vibration reduces the chance of cement particles forming clumps and makes the cement particles disperse more uniformly.
Table 9Test results of cement titration
Mixing processes | Cement dosage (%) | Mean (%) | Standard deviation | ||||||||
Vibration mixing | 3.6 | 3.5 | 3.6 | 3.4 | 3.5 | 3.6 | 3.5 | 3.6 | 3.5 | 3.5 | 0.074 |
Vibration machine off-vibration mixing | 3.6 | 3.4 | 3.6 | 3.4 | 3.2 | 3.4 | 3.3 | 3.4 | 3.5 | 3.4 | 0.139 |
Static mixing | 3.7 | 4.0 | 3.7 | 3.8 | 3.6 | 3.5 | 3.6 | 3.8 | 3.7 | 3.7 | 0.155 |
5.5. Influence mechanism of vibration mixing on road performance
Based on Mohr-Coulomb Intensity Theory, the embedded friction between aggregates provides the internal friction resistance, while the cement paste provides the cohesive force [14-18]. The greater the internal friction resistance and cohesive force, the greater the strength of cement-stabilized macadam is. The results of this paper show that vibration mixing makes the aggregate distribution more uniform in cement-stabilized macadam mixture. For the same gradation composition, the more uniform the aggregate distribution is, the homogeneity of aggregates is proportionate to the embedding effect of structure, internal frictional resistance and the strength of mixture.
The mechanism of vibration mixing to improve the cohesion of the mixture can be explained from the following two aspects. Firstly, cement agglomerates can be effectively eliminated by vibration mixing, so the dispersion of cement paste is better, and the utilization rate of cement and hydration efficiency are improved. Secondly, vibration mixing helps the fine aggregate and cement paste to wrap around the coarse aggregate. The area of the cement paste wrapped around the aggregate surface is increased and the surface area of hydration on the aggregate surface is increased. Thus, the hydration products are uniformly wrapped around the aggregate and the surface adhesion of aggregate is increased. In addition, theoretically, the increase of cohesion in cement-stabilized macadam mixture will also have a positive effect on its humidity or temperature shrinkage and scouring resistance properties.
6. Conclusions
In this paper, the mixing homogeneity of cement-stabilized macadam by three processes has been studied. And on this basis, the influence mechanism of mixing homogeneity on road performance has been analyzed. Two findings are supported by the experiments and can provide guidance for future applications.
1) Compared with static mixing and vibration machine off-vibration mixing, vibration mixing is superior in mixing homogeneity, by helping cement paste and fine macadam to wrap coarse macadam and reducing the number of coarse macadam in core sample section. The passing rate of the aggregate through major sieving holes and the standard deviation of the cement dosage titration in vibration mixing mixture are the lowest among the three processes.
2) Mechanically, the improvement of mixing homogeneity of cement-stabilized macadam is beneficial to improve the internal friction resistance and cohesion of the mixture, thus improving the road performance such as strength, humidity or temperature shrinkage, and scour resistance of the mixture.
References
-
K. M. Mane, D. K. Kulkarni, and K. B. Prakash, “Performance of various pozzolanic materials on the properties of concrete made by partially replacing natural sand by manufactured sand,” Journal of Building Pathology and Rehabilitation, Vol. 4, No. 1, pp. 1–9, Dec. 2019, https://doi.org/10.1007/s41024-019-0061-9
-
W. Dong, Z. Feng, and L. Zhao, “Experimental research on the influence of vibration intensity on performance of cement stabilized macadam,” IOP Conference Series: Earth and Environmental Science, Vol. 283, No. 1, p. 012011, May 2019, https://doi.org/10.1088/1755-1315/283/1/012011
-
X. Li, X. Lv, W. Wang, J. Liu, M. Yu, and Z. You, “Crack resistance of waste cooking oil modified cement stabilized macadam,” Journal of Cleaner Production, Vol. 243, p. 118525, Jan. 2020, https://doi.org/10.1016/j.jclepro.2019.118525
-
X. Bai, “Study on comprehensive evaluation system of crack resistance of cement stabilized macadam base,” (in Chinese), Chongqing, Chongqing Jiaotong University, 2013.
-
X. L. Wang Xuelian, X. M. Huang, and G. J. Bian, “LSPM’s analysis on the mechanism of preventing and curing reflective cracks in semi-rigid base asphalt pavement,” (in Chinese), Journal of Highway and Transportation Research and Development, Vol. 11, No. 3, pp. 8–15, 2016.
-
M. J. Li, Y. J. Jiang, and J. L. Dai, “Mechanism of shrinkage cracking of cement stabilized macadam and its application in gradation design,” (in Chinese), Journal of Wuhan University of Technology, Vol. 32, No. 3, pp. 1–4, 2010.
-
X. P. Xu, “Research on construction organization and quality control technology of water-stable base with dense skeleton structure,” (in Chinese), Xi′an, Chang’an University, 2009.
-
Z. C. Xu et al., “Strength and uniformity analysis of cement stabilized macadam mixture based on vibration mixing process,” (in Chinese), Technology of Highway and Transport, Vol. 33, No. 6, pp. 4–8, 2017.
-
“Detailed rules for construction technology of highway pavement base: JTG TF20-2015,” (in Chinese), China Standards Press, Beijing, Research institute of highway ministry of transport, 2007.
-
Z. X. Feng, X. Y. Wang, and J. S. Feng, “Durable anti-cracking vibration mixing technology and engineering application of cement stabilized macadam base,” (in Chinese), Construction Machinery, Vol. 47, No. 4, pp. 1–9, 2016.
-
S. Q. Xue, “Experimental study on the effect of vibration stirring on the performance of cement stabilized macadam,” (in Chinese), Chang’an University, Xi'an, 2016.
-
Lz Dan et al., “Study on road performance of cement stabilized macadam mixture based on vibration mixing process,” (in Chinese), Technology of Highway and Transport, Vol. 34, No. 5, pp. 21–25, 2018.
-
Q. Li and Fj Ni, “Prediction of shrinkage cracking spacing for cement stabilized macadam Base,” (in Chinese), Highway, Vol. 59, No. 2, pp. 102–106, 2014.
-
Sha Ai-Min, “Material Characteristics of Semi-rigid Base,” (in Chinese), China Journal of Highway and Transport, Vol. 21, No. 1, pp. 1–5, Mar. 2014.
-
L. Xiao-Feng et al., “Research on cracking of cement-stabilized macadam base during highway construction,” (in Chinese), Journal of Guangxi University (Natural Science Edition), Vol. 37, No. 4, pp. 716–722, 2012.
-
R. K. Li, C. C. Luosang, and H. M. Wang, “Comparative study on strength performance of cement stabilized gravel mix under vibration stirring,” (in Chinese), Journal of Chongqing Jiaotong University (Natural Science), Vol. 36, No. 11, pp. 33–36, 2017.
-
Q. Liu and Y. Xiong, “Pavement performance of cement stabilized macadam through vibrating mixing,” (in Chinese), Road Machinery and Construction Mechanization, Vol. 35, No. 4, pp. 74–76, 2018.
-
Zhang Liang-Q., “The development and industrial tests of vibratory cement stable macadam mixer,” (in Chinese), Journal of Guangxi University (Natural Science Edition), Vol. 40, No. 5, pp. 1155–1161, 2015.
About this article
This study was funded by the Science and Technology Project of Department of Transport of Yunnan Province (YunJiaoKeJiao(2016)140(B)).