Abstract
Lightweight can not only reduce the running energy consumption of the railway vehicle, but also reduce the running wheel-rail dynamic force, and unsprung mass lightweight has a more significant impact. Titanium alloy is very suitable for spring railway vehicle manufacturing. Titanium alloy spring can reduce its own weight and stress, and it has the capability of anticorrosion. But there is no experience in titanium alloy spring material heat treatment and strengthening process for reference. In this paper, the research is carried out, and the heat treatment method and strengthening process suitable for the titanium alloy spring manufacture is summarized. And the observation of the microstructure and mechanical properties test of the spring show that the titanium alloy spring can meet the technical requirement by adopting appropriate heat treatment method and strengthening process.
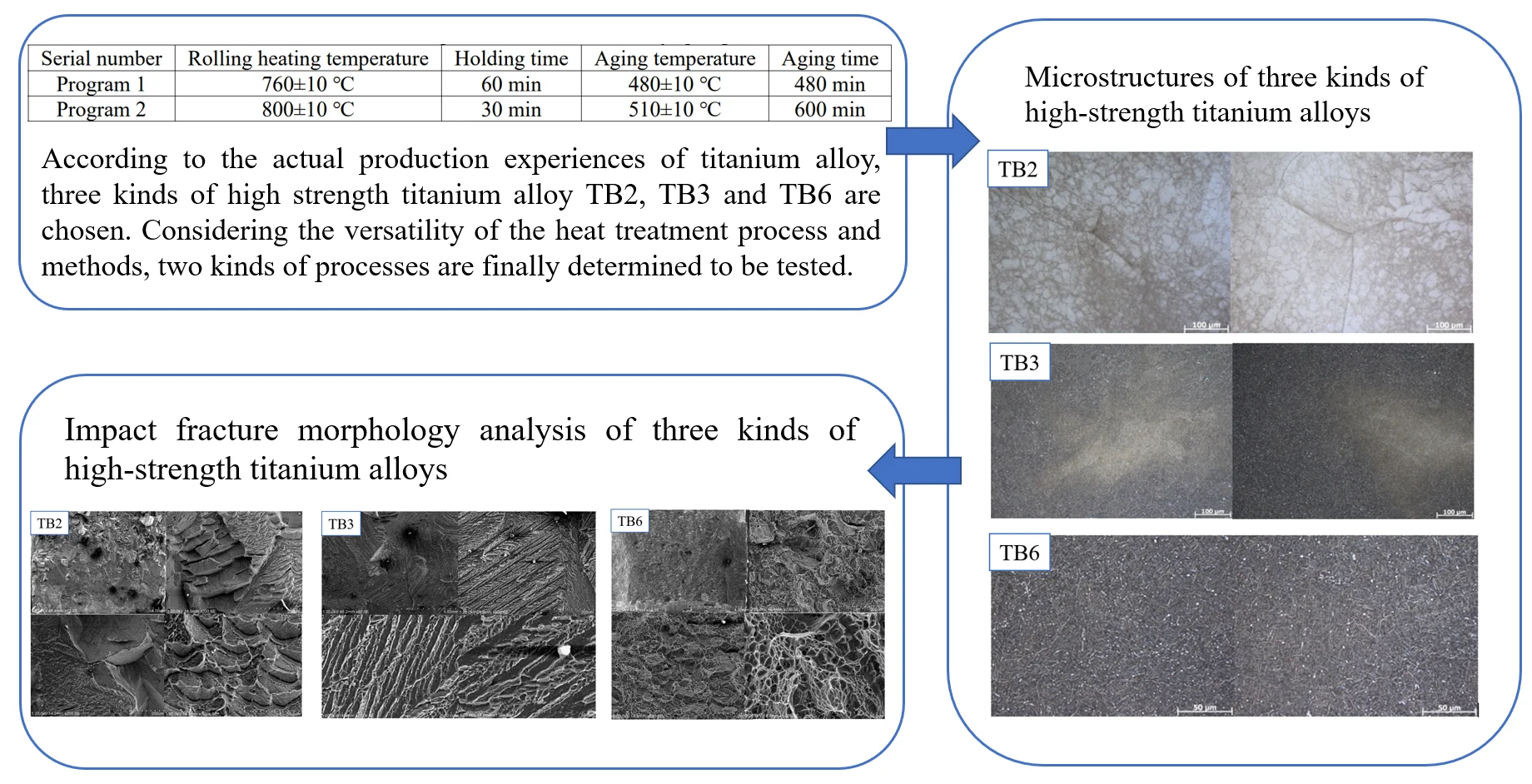
Highlights
- The excellent characteristics of titanium and titanium alloy suitable for rail vehicle springs are summarized.
- The heat treatment method and strengthening process measure for the titanium alloy spring coiling are groped and summarized.
- The composition, microstructure and properties of 3 kinds of high strength β type titanium alloy spring materials are preliminarily studied.
- The reason why titanium alloy spring needs surface strengthening treatment and why shot peening is adopted is explained.
1. Introduction
With the constant speed-raising of the rail vehicle, the lightweight requirements of the rail vehicle are getting higher and higher. Lightweight can not only reduce the running energy consumption of the rail vehicle, but also reduce the wheel-rail dynamic force; especially the influence of the unsprung mass lightweight is more significant. Therefore, aluminum alloy car body, luggage rack and seats made of composites and so on have been widely used in high-speed EMU. But because unsprung parts such as wheel, axle, axle box and axle box spring bear a lot of dynamic and static loads, and they directly affect the operating safety, so relevant lightweight research has been no breakthrough so far. With excellent comprehensive properties of low density, high specific strength, high temperature resistance, corrosion resistance, no magnetism, good biocompatibility and so on, titanium and titanium alloy get more and more applications in aviation, aerospace, ship, weapon, petroleum, artificial island, chemical industry, medical, food and other fields, and attract worldwide attention. So can titanium alloy make a difference in the unsprung part lightweight of rail vehicle?
Titanium alloy is an important structural material developed from 1950s. It is an alloy composed of other elements with Ti as matrix. Titanium and titanium alloy have many excellent characteristics, and they are very suitable for rail vehicle, which mainly reflect on the following aspects [1]:
1) High specific strength. Titanium alloy has very high strength, and its tensile strength is 686-1176 MPa, while the density is only 3/5 of steel and half of copper. Titanium alloy has the same excellent mechanical properties as steel. From the point of view of equal strength design, the weight of steel spring can be reduced by 40 % [2].
2) High hardness. The hardness of titanium alloy (annealed) is HRC 32-38.
3) Low modulus of elasticity. The elastic modulus of titanium alloy (annealed) is 107.8-117.6 GPa, which is about half of that of steel and stainless steel, making it easy to bend. Titanium alloy can be used in elastic element due to this characteristic.
4) Properties are excellent at high and low temperature. At high temperature, titanium alloy can still maintain good mechanical properties, and its heat resistance is well above that of aluminum alloy. And the working temperature range is wide. At present, the working temperature of new heat resistant titanium alloy can reach 550-600 ℃. At low temperature, the strength of titanium alloy is higher than that at normal temperature, and it has good toughness. Cryogenic titanium alloy can maintain good toughness at –253 ℃.
5) High corrosion resistance of titanium. In the air below 550 ℃, the surface of titanium can quickly form thin and dense titanium oxide film. So in the atmosphere, sea water, nitric acid, sulfuric acid and other oxidizing media and strong alkali, its corrosion resistance is superior to most stainless steel. Especially in seawater and marine atmosphere environment, the corrosion resistance is extremely high. In addition, the corrosion resistance of pure titanium in alkaline solution and most organic acid compounds is also very high. And the prominent feature of corrosion of titanium alloy is that local corrosion and intergranular corrosion don’t occur, and the corrosion is generally uniform.
6) Titanium has a strong tendency to passivation. Titanium has a strong affinity to oxygen. In the air or media containing oxygen, a layer of dense, strong-adhesion, inert oxide film will form on the surface of titanium to protect titanium matrix from corrosion. Even if the oxide film is damaged due to mechanical wear, a new layer of oxide film will soon form.
Titanium alloy has superior properties, but the price is high, so its application has been greatly restricted, and it must be used to give full play to its performance advantages in order to get high cost performance [3]. Titanium alloy is a kind of metal material which has the highest specific strength, and the material itself has good damping to dissipate a portion of vibrational energy. Both two characteristics make titanium particularly suitable for coiling spring [4, 5]. High-strength type titanium alloy has good forming ability. By solid solution aging and heat treatment process, titanium alloy can obtain the excellent matching performance among strength, plasticity and toughness, so the titanium alloy is very suitable for coiling spring of rail vehicle.
Titanium alloy is favored by aircraft designers. The main reason is that it cannot only ensure the structural strength, but also greatly reduce the structural quality [6]. Ti-13V-11Cr-3Al (Ti-13-11-3) and other type titanium alloys were developed and applied in America as early as the 1950s [7]. McDonnell-Douglas Corporation started using cold working + Ti-13-11-3 alloy at aging state to coiling spring used on civil aircraft in 1970s. The Boeing Company used Ti-11.5Mo-4Sn-6Zr alloy hatch spring on Boeing 747. The initial commercial application of Ti-3Al-8V-6Cr-4Mo-4Zr alloy was also coiling aviation spring. In the early and middle 1980s, Ti-38-6-44 (-C) spring was used to replace Ti-13-11-3 [8]. The amount of titanium used by Boeing aircraft has increased from 0.5 % of the Boeing 707 to 14 % of the Boeing 787 [9].
American automotive industry began to pay attention to the application of titanium alloy in the early 1980s. At that time, Ford Motor Company made a large number of evaluations of titanium alloy suspension spring, valve, valve spring, etc. But because of cost, titanium parts have not been assembled on mass-produced models. At present, titanium is mainly used in automobile engine valve system (valve spring, valve seat), exhaust system, automobile connecting rod and car body frame [10].
Coiling spring is one of the best uses of titanium alloy. It can not only give full play to the high specific strength of titanium alloy, but also reduce the weight of spring and make full use of its damping property.
According to the literature and news reports consulted so far, the application of titanium alloy in railway transportation has not been introduced yet. In this paper, the composition, microstructure and properties of 3 kinds of high strength type titanium alloy spring materials are preliminarily studied. And the heat treatment method and strengthening process measure for the titanium alloy spring coiling are groped and summarized.
2. The experimental setup
According to the actual production experiences of titanium alloy, three kinds of high strength titanium alloy TB2, TB3 and TB6 are chosen. First of all, basic test of heat treatment process is carried out on the titanium alloy. Next various specifications of titanium alloy spring are tentatively coiled. Then the titanium alloy springs are put into destructive test and sampled, with microstructures of the samples are observed and mechanical properties are tested. Considering the versatility of the heat treatment process and methods, two kinds of processes are finally determined to be tested, and the specific process programs are shown in Table 1.
The coiling and analysis process of titanium alloy spring is as follows: raw material preparation → raw material inspection → raw material heat treatment process research → spring coiling → spring body sampling → chemical constituents’ analysis → microstructure observation and analysis → mechanical properties testing.
Table 1Two heat treatment processes of titanium alloy spring
Serial number | Rolling heating temperature | Holding time | Aging temperature | Aging time |
Program 1 | 760±10 ℃ | 60 min | 480±10 ℃ | 480 min |
Program 2 | 800±10 ℃ | 30 min | 510±10 ℃ | 600 min |
3. Chemical constituents, properties and test scheme of the materials
3.1. Chemical constituents of three kinds of high-strength titanium alloys
Chemical constituents of three kinds of materials TB2, TB3 and TB6 are shown in Tables 2-4 respectively.
Table 2Chemical constituents of high-strength titanium alloy of TB2 (w/%)
Grade | Parts | Ti | Al | Mo | V | Cr | Fe | C | N | H | O |
TB2 | Upper | Matrix | 3.08 | 5.18 | 4.93 | 7.61 | 0.26 | 0.026 | 0.005 | 0.002 | 0.007 |
Middle | Matrix | 2.99 | 4.98 | 4.92 | 7.59 | 0.18 | 0.022 | 0.005 | 0.001 | 0.005 | |
Lower | Matrix | 3.09 | 5.19 | 4.98 | 7.63 | 0.22 | 0.024 | 0.005 | 0.002 | 0.006 |
Table 3Chemical constituents of high-strength titanium alloy of TB3 (w/%)
Grade | Parts | Ti | Al | Mo | V | Fe | C | N | H | O |
TB3 | Upper | Matrix | 3.21 | 10.09 | 7.93 | 0.98 | 0.036 | 0.006 | 0.002 | 0.008 |
Middle | Matrix | 3.19 | 10.06 | 7.92 | 0.96 | 0.023 | 0.006 | 0.001 | 0.005 | |
Lower | Matrix | 3.20 | 10.09 | 7.98 | 0.99 | 0.034 | 0.006 | 0.002 | 0.007 |
Table 4Chemical constituents of high-strength titanium alloy of TB6 (w/%)
Grade | Parts | Ti | Al | V | Fe | C | N | H | O |
TB6 | Upper | Matrix | 3.02 | 9.78 | 1.89 | 0.027 | 0.011 | 0.001 | 0.11 |
Middle | Matrix | 3.07 | 10.23 | 1.92 | 0.030 | – | 0.001 | – | |
Lower | Matrix | 3.08 | 10.31 | 1.82 | 0.026 | 0.010 | 0.002 | 0.11 |
3.2. Properties of three kinds of high-strength titanium alloys
Three kinds of high-strength titanium alloys are coiled into springs by hot treatment, and samples are destructively taken from both ends of each spring. The tensile and impact properties of the samples are tested and evaluated, and the numerical values are shown in Table 5.
3.3. Microstructures of three kinds of high-strength titanium alloys
In order to grope the heat treatment method suitable for the titanium alloy spring material, two comparison programs are proposed: program 1 and program 2. Program 1: Coiling spring at the heating temperature of 760 ℃ and the aging temperature of 480 ℃. Program 2: Coiling spring at the heating temperature of 800 ℃ and the aging temperature of 510 ℃. The details is seen in Table 1.
Table 5Room temperature tensile properties and impact properties of titanium alloy spring materials under different conditions
Program | Parts | / MPa | / MPa | / % | / % | / J |
Program 1 | TB2 | 1180 | 1140 | 5 | 26 | 20 |
TB3 | 1160 | 1090 | 8 | 32 | 21 | |
TB6 | 1194 | 1120 | 11 | 35 | 26 | |
Program 2 | TB2 | 1060 | 1020 | 12 | 41 | 20 |
TB3 | 1120 | 1085 | 10 | 39 | 22 | |
TB6 | 1090 | 1030 | 14 | 40 | 21 |
After treated with program 1 and 2, the microstructures of three kinds of high-strength type titanium alloys TB2, TB3 and TB6 are shown in Fig. 1-3 respectively.
Fig. 1(a) and Fig. 1(b) are the microstructures sampled from the spring bodies after the heat treatment of program 1 and program 2 respectively. In the pictures, it’s clear that two programs both have a certain number of strengthening phase dissolved into the matrix, clear grain boundary, and large grain size. The features above lead to high material strength and poor plasticity of spring body, so that the spring is easy to fragment when it’s compressed. Therefore, the TB2 material is not suitable for spring production with heat treatment processes program 1 and 2.
Fig. 1Spring microstructure of TB2 material
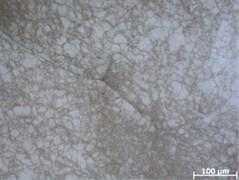
a) Program 1 Spring 200 times microstructure of TB2 material
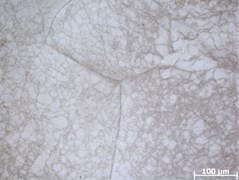
b) Program 2 Spring 200 times microstructure of TB2 material
Fig. 2 is the microstructure of TB3 spring, magnified 200 times. Precipitation strength is one of the methods to strengthen alloy. When stable element content in alloy is high, due to the small phase transformation driving force, aging at low temperature often takes a relatively long time to reach the peak of enhancement. From Fig. 2(a) and Fig. 2(b), it’s apparent that material composition is not uniform, resulting in inhomogeneous material properties, which will eventually result in shortening the service life of the product. Therefore, spring material requires not only good surface quality, but also uniform distribution of structure inside the material.
Fig. 2Spring microstructure of TB3 material
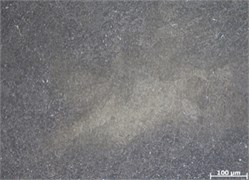
a) Program 1 Spring 200 times microstructure of TB3 material
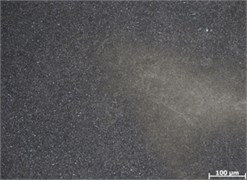
b) Program 2 Spring 200 times microstructure of TB3 material
In Fig. 3, supersaturated solid solution of TB6 alloy is obtained by solid solution treatment, and then the strength properties of alloy are improved by aging strengthening. Aging is the process of the second phase precipitating from supersaturated solid solution. And it’s also a kind of solid phase transition with formation and growth of the new phase nucleation. During aging at 480 ℃ and 510℃, transition and phase induced nucleation occur. As long as a secondary slice forms at dislocation, grain boundary or other grain defect, the nucleation probability of phase can greatly increase in the matrix near the slice. It’s clear in Fig. 3(a) and Fig. 3(b) that the organization of the TB6 spring material is uniform, indicating that TB6 material is suitable for spring production with treatments program 1 and program 2.
Fig. 3Spring microstructure of TB6 material
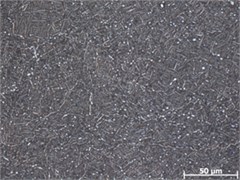
a) Program 1 Spring 200 times microstructure of TB6 material
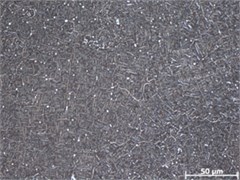
b) Program 2 Spring 200 times microstructure of TB6 material
3.4. Impact fracture morphology analysis
The impact fracture morphologies of three kinds of high–strength β type titanium alloys TB2, TB3 and TB6 after heat treatment with program 2 are shown in Fig. 4-6 respectively.
Fig. 4 shows the macro and micro features of fracture toughness specimens of TB2 spring. Fig. 4(a) is the macro fracture morphology. It can be seen that fracture fiber region has more dimples. Fiber and radial region are obviously. It shows the fracture mechanism is ductile fracture and the plasticity of alloy is good. Since the fracture is in plane stress state, fiber region is formed in the crack propagation, and impact fracture has fiber region with small area, as shown in Fig. 4(b) and Fig. 4(c). Due to shear stress, shear lip region shows dimple morphology, as shown in Fig. 4(d).
Fig. 4The macro and micro features of fracture toughness specimens of TB2 spring
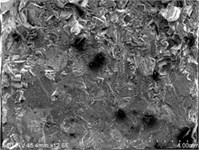
a) Macroscopic micrographs
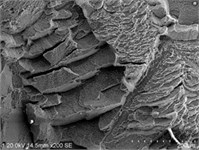
b) Microscopic cross region
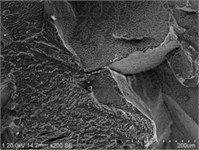
c) Microscopic fatigue region
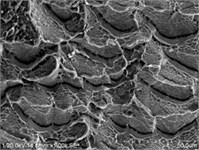
d) Microscopic expansion region
Fig. 5 shows the macro and micro features of fracture toughness specimens of TB3 spring. Fig. 5(a) is the macro fracture morphology. The macro fracture surface is rough, and the rough fracture increases the tortuosity of the crack propagation path, so that more energy can be absorbed during the crack propagation, which is beneficial to improve toughness. In Fig. 5(b) white points are strengthening phases distributing along grain boundaries, and phases in the juncture is not significantly different from phases in the non-juncture, also there is a lot of tearing ridge. The crack propagation and fracture are sensitive to microstructure, and fracture characteristics in the pre-cracked region are micro-region facet and tear ridge. Wide and deep secondary cracks can be seen in Fig. 5(c), making the organization have high fracture toughness. The microscopic morphological characteristic in propagation region is shallow tear dimple, as shown in Fig. 5(d), weakening the toughness fracture mechanism.
The macro and micro features of fracture toughness specimens of TB6 spring are shown in Fig. 6. Fig. 6(a) is the macro fracture morphology. It is clear that the macro fracture is relatively smooth, indicating that the fracture is little affected by the microstructure. Fig. 6(b) is the pre-cracked region, and the fracture surface is smooth, and basically shows a pattern of clouds seeing in Fig. 6(c). And the microscopic morphological characteristic in propagation region is dimple as shown in Fig. 6(d), which is the typical toughness fracture, and it’s also the root cause of high plasticity of TB6 spring.
Fig. 5The macro and micro features of fracture toughness specimens of TB3 spring
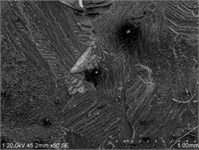
a) Macroscopic micrographs
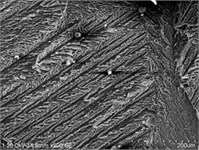
b) Microscopic cross region
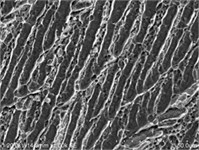
c) Microscopic fatigue region
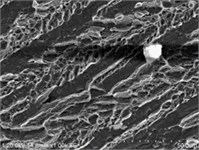
d) Microscopic expansion region
Fig. 6The macro and micro features of fracture toughness specimens of TB6 spring
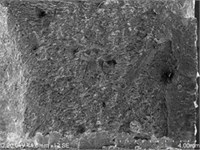
a) Macroscopic micrographs
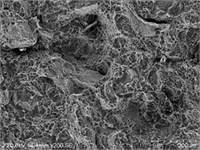
b) Microscopic cross region
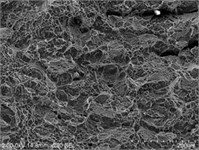
c) Microscopic fatigue region
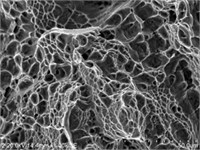
d) Microscopic expansion region
3.5. Shot peening of titanium alloy spring
The primary spring of railway vehicle is installed on the axle box. It is exposed outside and suffers from erosion by wind, rain, snow, sunlight and even gravel impact. And the force between wheel and rail will be directly transmitted to the primary spring through axle and axle box, and the primary spring will directly affect the traffic safety. Therefore, the life of primary spring is strictly stipulated in railway transportation. At present, the trial of the primary spring on high-speed EMU in China is executed referring to EN13298 “Railway applications – Suspension components – Helical suspension springs, steel” UIC 822 “Technical specification for the supply of helical compression springs, hot or cold coiled, for tractive and trailing stock” and TJ/CL 285-2013 “EMU axle box spring” (Provisional). The stress of primary spring is large, especially the tensile stress, so the strength of the titanium alloy spring material should be more than 1250 MPa. And there is a clear requirement on impact toughness of the primary spring: 5 mm deep U-shape, in the room temperature of 20 ℃, KU ≥ 10 J; in the low temperature of –20 ℃, KU ≥ 10 J; in the low temperature of –40 ℃, KU ≥ 8 J. In addition, fatigue life requirement of primary spring is: when the dynamic coefficient is 0.5, fatigue life is 5×105 times; when the dynamic coefficient is 0.3, fatigue life is 2.05×107 times. After both two trials are completed, fatigue crack or break must not appear. Therefore, the surface strengthening treatment of titanium alloy spring is necessary to improve its fatigue life.
Surface strengthening treatment methods are usually classified into two categories: surface shot peening strengthening and surface roll strengthening. Because the spring is spiral, and there is not much space between the two adjacent circles, it is difficult to use surface roll strengthening, so surface shot peening strengthening is adopted.
Shot peening mechanism is forming a certain depth of residual compressive stress field by process. The residual compressive stress field can not only inhibit the initiation of fatigue crack, but also increase crack closure effect and reduce the propagation rate of short fatigue crack, even produce arrest phenomenon. Because the residual compressive stress produced by shot peening can counteract the effect of external tensile stress on material, and the concentration of stress around micro crack on the material surface is lower when tensile stress is smaller, and therefore the residual compressive stress can inhibit the formation and propagation of crack. The residual stress field formed by shot peening can transfer fatigue crack from surface layer to sub-surface layer, which can significantly improve the fatigue life of material and achieve the goal of improving the fatigue life of the spring.
Shot peening is beneficial to improve the fatigue life of titanium alloy spring. Large plastic deformation is formed on the surface layer of the metal material after shot peening, making the stress state of the surface layer change greatly; that is, large residual compressive stress and micro stress are produced. It is the existence of residual compressive stress and micro stress that counteract the effect of tensile stress on the spring surface, which has a beneficial effect on the mechanical properties of the spring.
Shot peening process parameters include the diameter of shot, jet velocity, shot flow, jet angle, distance between nozzle and spring surface and jet time. These parameters have a direct impact on quality and depth of the product surface strengthening layer after shot peening. In the actual shot peening process, shot peening process parameters affect the shot peening strength. If the shot peening strength is too small, it can’t meet the requirement of strengthening; while the shot peening strength is too large, it will produce defects or micro cracks on the sprayed surface. Only in the best shot peening strength can the spring obtain the best fatigue property. And this is one of the contents on which next study and trial lay emphasis.
4. Conclusions
By sampling and microscopic observing the spring bodies coiled with three kinds of high-strength titanium alloys TB2, TB3 and TB6, after heat treatment with program 1 and 2, only the microstructure of the TB6 material spring is uniform, so TB6 material is suitable for spring coiling. The following mechanical test to the spring shows that the TB6 titanium alloy spring coiled with the two methods above meets the design requirements. Therefore, the following conclusions are drawn as follows:
1) Heat treatment methods of program 1 and program 2 are suitable for TB6 spring coiling.
2) The heat treatment methods of program 1 and program 2 are not ideal to coil spring with the two kinds of materials TB2 and TB3. And the heat treatment of coiling spring with the two kinds of materials remains to be studied.
3) Shot peening must be carried out to improve the fatigue life of spring.
References
-
G. Wang, S. Hui, W. Ye, X. Mi, Y. Wang, and W. Zhang, “Microstructure and tensile properties of low cost titanium alloys at different cooling rate,” Rare Metals, Vol. 31, No. 6, pp. 531–536, Dec. 2012, https://doi.org/10.1007/s12598-012-0552-1
-
Z. H. Huang et al., “Application prospect of titanium alloy spring in rail transit,” Electric Drive for Locomotives, No. 1, pp. 14–16, 2017.
-
C. Y. Wang and W. J. Xi, “Investigation on notch sensitivity of TC18 titanium alloy,” Rare Metal Materials and Engineering, Vol. 41, No. 4, pp. 663–666, 2012.
-
Z. H. Huang et al., “Application prospect of titanium alloy materials in rail transit,” Electric Drive for Locomotives, Vol. 2, pp. 11–13, 2017.
-
Z. H. Huang, H. J. Zhang, and Y. P. Sun, “Design of primary spring for three-axle bogie,” Electric Drive for Locomotives, Vol. 4, pp. 36–37, Dec. 2012.
-
Liu Shifeng, Song Xi, Xue Tong, Ma Ning, Wang Yan, and Wang Liqiang, “Application and development of titanium alloy and titanium matrix composites in aerospace field,” Journal of Aeronautical Materials, Vol. 40, No. 3, pp. 77–94, Jun. 2020, https://doi.org/10.11868/j.issn.1005-5053.2020.000061
-
Y. J. Li and K. Liu., “Application and advanced bonding technology of titanium alloy in aviation industry,” Aeronautical Manufacturing Technology, Vol. 16, pp. 34–37, 2015.
-
Y. K. Gao, “Effect of shot peening on tensile-tensile properties of TC18 titanium alloy,” Rare Metal Materials and Engineering, Vol. 33, No. 9, pp. 1000–1002, 2004.
-
Q. M. Liu et al., “Application and development of titanium alloy in aerospace and military hardware,” Journal of Iron and Steel Research, Vol. 27, No. 3, pp. 1–4, 2015.
-
Z. Li, “Applications of titanium and titanium alloys in automotive field,” The Chinese Journal of Nonferrous Metals, Vol. 20, pp. 1034–1038, 2010.
About this article
The authors acknowledge the financial supports from the National Natural Science Foundation of China (U19A20109).