Abstract
The traditional low-alloy steel rose-bow spring of subway pantograph is easily occurred the corrosion and fracture after being used for a central period of time, which interrupts the train current collection and cannot provide power for the train, as a result of the interruption of the normal operation of subway trains. Therefore, an optimal design and improved processing technology for the rose-bow titanium alloy spring of subway pantograph was studied in this paper. The heat treatment tests on the two titanium alloy springs, made of TC18 and TB6 materials, were conducted respectively. The improved process flow of the rose-bow titanium alloy spring was also determined. Fatigue test results show that both TC18 and TB6 titanium alloy springs of pantograph can meet the corresponding requirements.
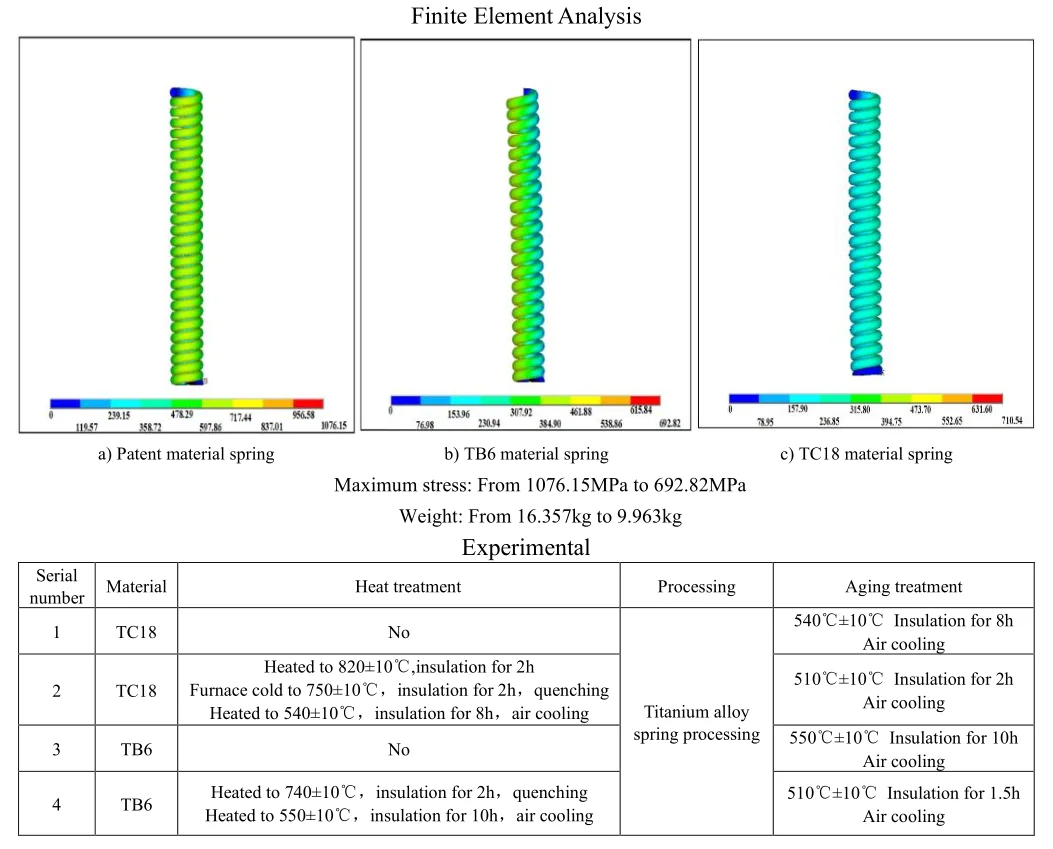
Highlights
- There is no application of titanium alloy in the field of rail transit, and the researches and reports on the processing of coiling spring with titanium alloy material are very little.
- TB6 and TC18 materials can meet the technical requirements of installation space and spring stiffness of the rose-bow spring, and have interchangeability with the original spring.
- After the spring material is changed to titanium alloy, the maximum stress is reduced by 35.6% and the weight is reduced by 39.1% through optimal design.
- Titanium alloy spring has the characteristics of corrosion resistance, which can improve the service life of the rose-bow spring of subway pantograph.
1. Introduction
Pantograph is a kind of electrical equipment installed on the roof of the subway train, which is able to get electric energy from the catenary. It needs to withstand wind and rain and corrosion, so the application conditions are very harsh. And rose-bow spring is an important part of the pantograph which makes the height of pantograph head changed with the height of catenary while the train running. It ensures that the pantograph is in good contact with the catenary and maintains a certain stable contact pressure, which makes the train current collection stable and provides a stable power source for the train. While running, the subway train is affected by track irregularity and other excitations, and the catenary itself is also affected by the external wind load and so on. Therefore, the rose-bow spring bounces and swings between the pantograph and catenary, that is, the vibration in kinematics and its amplitude are expected to be as small as possible. While the pantograph is damaged, the pantograph will be rapidly lowered and controlled at the lowest height by hydraulic damper. At present, the pantograph rose-bow springs used on domestic subway trains are all low-alloy steel springs, and in order to ensure the reliability of work, the rose-bow springs are all imported with the materials protected by patent. However, corrosion and fracture will occur after long-term use, resulting in failure of the spring. There are other problems that can cause the pantograph to lack strength to raise, for example, lack of initial tension. The subway train loses power source due to the failure of rose-bow spring, which will only lead to fault shutdown. It is necessary to require that the spring has the advantages of corrosion resistance, small stress and good damping performance in order to improve the service life of rose-bow spring. In this paper, the optimization design and experimental study of the rose-bow spring made of titanium alloy bar are carried out.
Titanium alloy is an alloy composed of other elements with Ti as matrix. Titanium alloy is widely used in aviation, aerospace, military, medical, food, chemical, automotive, island construction and other fields because of its good properties, such as high strength, good corrosion resistance, high heat resistance, low density, good mechanical properties, good toughness and so on. titanium alloy is a versatile material with high specific strength, and good matching of strength, toughness and fatigue properties can still be obtained with large cross section. The widely applied β titanium alloys include TB6, TB22, BetaC, Ti-15-3 Beta21S, and so on [1]. Among these alloys, TB6 can obtain the best matching of strength, toughness and high cycle fatigue strength when the processing conditions are appropriate. The main characteristics of TB6 are high specific strength, good fracture toughness, low forging temperature, good hardenability and strong resistance to stress corrosion, so TB6 is suitable for coiling high strength titanium alloy spring. TC18 is a new type of dual phase titanium alloy with nominal composition as Ti-5Al-5Mo-5V-1Cr-1Fe. It not only has the characteristics of common titanium alloy, but also has good toughness [2] and hardenability, and the hardening depth is up to 250 mm. Using TC18 titanium alloy [3] instead of TC4 or high strength steel, the weight of aircraft can be reduced by 15 %-20 %, and the reasonable matching of high strength, high plasticity and fracture toughness can be obtained by heat treatment. TC18 titanium alloy has gained popularity in the aviation industry and attracted extensive attention at home and abroad. But so far, the researches and reports on the processing of coiling spring with titanium alloy material are very little.
Titanium alloy has been applied to the manufacture of automotive suspension spring and valve spring. The automotive business department of TIMET (Titanium Metals Corporation) in USA introduces the latest application of titanium in Ferrari Challenge Stradale car model. All the suspension spring material of this model is Timetal LCB alloy, and it is the first time in automobile industry that suspension springs of the whole car are all made of titanium alloy. Timetal LCB alloy can also be used for the valve spring of high-performance racing car, the torsion spring of snowmobile, and the suspension spring of Volkswagen LuPo car. By adopting titanium alloy, the weight of the valve spring can be reduced by 34 %, and the weight of the torsion spring of snowmobile can be reduced by 30 % to 50 %. In the field of aerospace engineering, (Ti-3Al-8V-6Cr-4Mo-4Cr) titanium alloy has been used for more than 10 years. In addition, TC3/TC4, TB3 and other materials have also been applied in the production and research of titanium alloy spring [4].
The development and production of titanium alloy spring are carried out by many domestic units. After forging, rotary forging, annealing and polishing, three kinds of titanium alloy materials TB3, -C and TC4 are processed into Ø3 mm wire materials. Then through coiling, stress-relief annealing, separating, end face grinding, spring, sandblasting, pickling and other processes, wire materials are made into titanium alloy cylindrical helical compression springs, and finally performance test is carried out. ZHFP421 fatigue machine can be used for the pressure-pressure fatigue test of titanium alloy spring. When the stress is 690 MPa, the fatigue lives of all the three kinds of spring before and after blasting are more than 500 thousand times, and there is no obvious difference among them. The quality of each kind of titanium alloy spring reaches the second grade accuracy specified by “GB/T l239.1-2009 Cold coiled helical springs technical specifications-Part 1: Extension spring”. In addition, the domestic titanium alloy spring materials Ø0.1-7.0 mm TC3 and TC4 meet the requirements of “GB 3623-1983 titanium and titanium alloy wire”. The material of TC3 and TC4 have good properties, the strength limit is greater than or equal to 930 MPa, is greater than or equal to 685 MPa, and the elastic modulus and shear modulus of the material are 44100 MPa, 11074 MPa, respectively. And these titanium alloy springs have been successfully applied in more than 40 natural gas chemical plants in Yunnan, Sichuan and other provinces, realizing the localization of imported equipment.
2. Finite element analysis of pantograph rose-bow spring
According to the technical characteristics of the pantograph rose-bow spring, combined with the experience of automotive and natural gas industry, TC18 and TB6 titanium alloys are selected as spring materials. As a large number of subway trains have been operated, the interface of the titanium alloy rose-bow spring should be the same as that of the original low alloy steel spring without changing the structure of the train and the catenary. It is required that the parameters before and after spring replacement should be as same as possible, that is, the value of (nominal free length of spring), (spring rate) and (spring force) should be the same, the value of (nominal diameter of bar) and (mean diameter of coil) should be similar. Therefore, it is necessary to carry out finite element analysis of the new spring to ensure the rationality of its design. The information of spring parameters is shown in Table 1.
Table 1Spring parameter information
Names and symbols | Unit | Spring steel | titanium alloy | titanium alloy approximate |
Patent material | TB6 | TC18 | ||
Density: | g/cm3 | 7.85 | 4.62 | 4.62 |
Modulus of rigidity: | N/mm2 | 81500 | 41300 | 43000 |
Modulus elasticity: | N/mm2 | 206000 | 104000 | 111000 |
Poisson’s ratio | – | 0.3 | 0.3 | 0.3 |
Mean diameter of coil: | mm | 93 | 93 | 93 |
Nominal diameter of bar: | mm | 17 | 19 | 19 |
Number of active coils: | – | 25.8 | 20.4 | 21.2 |
Total number of coils: | – | 31.8 | 26.4 | 27.2 |
Nominal free length of spring: | mm | 540±3 | 540±3 | 540±3 |
Spring bars expansion length | m | 9.3066 | 7.732 | 7.965 |
Spring bars expand effective length | m | 7.5573 | 5.985 | 6.218 |
Spring rate: | N/mm | 41 | 41 | 41.08 |
Spring bar weight: | kg | 16.357 | 9.963 | 10.268 |
Using HyperMesh as the processing software, the finite element model of spring is discretized by SOLID186 solid mesh. All of the three finite element models constrain the notch plane of the lower support ring of the spring and apply a tension load at the other end of the spring, the size of which is 147,200 N. After that, using ANSYS software to solve and post-process, the spring stress nephogram is shown in Fig. 1.
Fig. 1The spring stress nephogram
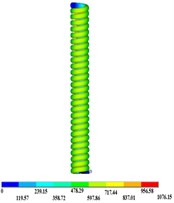
a) Patent material spring
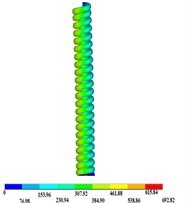
b) TB6 material spring
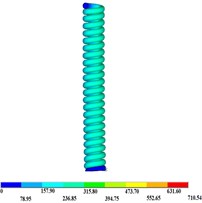
c) TC18 material spring
Fig. 2Pantograph’s Rose-bow TB6 spring test site
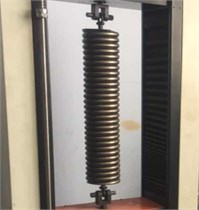
As can be seen from the above analysis: i) One of the main reasons for the fracture of extension spring is that the maximum working stress of the rose-bow spring coiled with original patent material is large. By optimization design (TB6), when the rose-bow spring material is converted into titanium alloy, the maximum working stress is reduced from 1076.15 MPa to 692.82 MPa; ii) After changing the spring material to titanium alloy, the weight of rose-bow spring decreased from 16.357 kg to 9.963 kg (TB6); iii) TB6 and TC18 materials can meet the technical requirements of installation space and spring stiffness of the rose-bow spring, and have interchangeability with the original spring; iv) The advantages and disadvantages of the rose-bow springs coiled of TB6 and TC18 materials are subjected to further experimental evaluation.
3. Chemical composition, materials properties and experimental program
According to the technical characteristics of pantograph rose-bow spring, two kinds of titanium alloy TC18 and TB6 are selected to be the spring materials, and the chemical composition and tensile properties of the materials are shown in Table 2 and Table 3, respectively. Fig. 2 shows the TB6 spring test site of subway pantograph rose-bow. At present, the research on titanium alloy spring has just started, especially the titanium alloy spring with large size and long length, and there is no report on the processing technology of titanium alloy spring at home and abroad [5]-[7]. In the absence of reference, the titanium alloy spring processing technology is explored on the basis of spring steel processing technology, and the following 4 schemes are selected for experimental research, details of which are shown in Table 4.
Table 2Chemical composition of materials
Grade | Composition | ||||||||
Al | V | Fe | Mo | Cr | C | H | O | N | |
TC18 | 5.3 | 5.0 | 1.0 | 5.2 | 1.1 | 0.02 | 0.005 | 0.12 | 0.01 |
TB6 | 3.13 | 9.56 | 2.06 | – | – | 0.022 | 0.0035 | 0.007 | 0.005 |
Table 3Tensile properties of materials
Heat treatment state | Tensile strength (MPa) | Yield strength (MPa) | Elongation (%) | Cross-section contraction (%) | |
TC18 | R | 1174 | 1125 | 8 | 26 |
STA | 1220 | 1172 | 17.6 | 48.4 | |
TB6 | R | 1248 | 1155 | 11 | 43 |
STA | 1279 | 1220 | 12 | 51 |
Table 4Experimental program
Serial number | Material | Heat treatment | Processing | Aging treatment |
1 | TC18 | No | Titanium alloy spring processing | 540±10 ℃ Insulation for 8h Air cooling |
2 | TC18 | Heated to 820±10 ℃, insulation for 2 h Furnace cold to 750±10℃, insulation for 2 h, quenching Heated to 540±10 ℃, insulation for 8h, air cooling | 510±10 ℃ Insulation for 2 h Air cooling | |
3 | TB6 | No | 550±10 ℃ Insulation for 10 h Air cooling | |
4 | TB6 | Heated to 740±10 ℃, insulation for 2 h, quenching Heated to 550±10 ℃, insulation for 10 h, air cooling | 510±10 ℃ Insulation for 1.5 h Air cooling |
4. Processing technology
The processing technology of titanium alloy spring includes roll forming, spring grinding, aging treatment, non-destructive testing, shot peening treatment and properties testing. Details of each step are as follows: 1) Roll forming: using numeric control spring machine, centerless cold forming. 2) Spring grinding: numeric control spring machine, wet grinding. 3) Aging treatment: 500-550 ℃ [5], 1.5-10 h, air cooling. 4) Non-destructive testing: penetration testing, inspection level of A. 5) Shot peening treatment [8]: coverage scale of 100 %, 12 minutes. 6) Properties testing: dimension and stiffness testing.
With the above-mentioned spring forming process, whether the material is TB6 or TC18, the pantograph spring has good application effect after product delivery, and the rose-bow spring malfunction caused by corrosion phenomenon does not occur again after long time application. The service life of the product is greatly improved and the production cost is low, which makes it suitable for mass production.
5. Forming principle and analysis of titanium alloy spring
5.1. Effect of raw material condition
TC18 is a highly alloyed titanium alloy with the nominal composition Ti-5Al-5Mo-5V-1Cr-1Fe, and the alloy can be strengthened by solid solution strengthening and aging strengthening, with phase transition temperature of 870 ℃±20 ℃ [9]-[10]. Practical experience shows that twice solid solution treatments and rapid cooling at 750 ℃ (below the phase transition point temperature) can get the fine equiaxed alpha phase and beta phase. TB6 titanium alloy has the characteristics of high specific strength, good fracture toughness and low forging temperature [11]-[13]. The comprehensive mechanical properties of the alloy can be adjusted in a wide range by heat treatment to match with different levels of strength, plasticity and toughness. And it meets the requirements of high reliability and low manufacturing cost. Taking the cost of the process research and market promotion into account, a total of 2 states are selected, which are hot rolled peeling and solid solution aging.
It is a very important part to confirm the state of the material before the titanium alloy spring coiling [14]. Therefore, the forming principle of the titanium alloy spring needs to be clearly analyzed and it is necessary to have an accurate grasp of this part in theoretical analysis. The practical experience shows that the material must be treated by heat treatment to stabilize the microstructure and properties of the material, so as to achieve the titanium alloy spring coiling [15].
So far, there have been no reports on hot rolled peeling status of TC18 and TB6, nor on the direct use of bars longer than 10 meters to process parts. With few tensile properties data and no reference, if the spring process is carried out directly and successfully, the high cost of some processes such as material heat treatment can be saved, so the prospect is considerable. The actual test results show that: i) After hot rolled peeling, TC18 and TB6 have characteristics of moderate strength and low plasticity, and serious fracture occurred during spring process; ii) After heat treatment, TC18 and TB6 have superior properties. Although there is a problem that the spring back value is large during the spring cold process, the final product has superior properties.
5.2. Effect of material heat treatment
Properties testing are carried out after using different solution temperatures, cooling rates after solid solution treatment and aging temperatures. On the premise that the material has middle-high strength, the elongation should be more than 8 %, so that the material can be processed and formed into titanium alloy spring. Through the experiments, after (heating to 740±10 ℃, thermal insulation for 2 h, quenching; heating to 550±10 ℃, insulation for 10 h, air cooling) heat treatment of TB6 and TC18, the best match between strength and fracture toughness of the materials is obtained, with which the materials are suitable for titanium alloy spring process.
By using solid solution + aging heat treatment to process TC18, the dispersed acicular ɑ phase is obtained. Instead, lamellar ɑ phase and equiaxial ɑ phase can be obtained by double solution + aging heat treatment. With the increase of the aging temperature, the number of primary phases in the organization decreases significantly. Both solid solution + aging heat treatment and double solution + aging heat treatment can make the mechanical properties of the alloy meet the material requirements of titanium alloy spring. However, considering the cost of mass production, solid solution + aging heat treatment is chosen.
TB6 titanium alloy consists of phase + phase + trace phase at the solid solution temperature of 740 ℃. The microstructure of the alloy from the phase after water cooling is primary phase particles distributed on the metastable substrate. With the increase of the heating temperature, the number of the primary phase particles decreases and the size of the primary phase particles increases. Cooling from the heating temperature at different speeds will lead to changes in the shape, size and quantity of the primary phase particles. With air cooling instead of water cooling, the content of the primary phase, the proportion of the spherical particles and the average diameter of the particles increase, resulting in a decrease in strength and an increase in plasticity and fracture toughness. So the heat treatment of TB6 titanium alloy should be “740 ℃, insulation 2 h, water-cooling”.
After solid solution aging treatment, the microstructures of TB6 titanium alloy are the primary ɑ phase, the secondary phase and the diffusion-enhanced phase. The dispersion degree of the secondary phase is mainly determined by the aging temperature and the insulation time. After aging at 480℃, tiny dispersive sheet secondary phase is separated out. With the increase of the aging temperature, the thickness and length ratio of the secondary sheet phase increases, which leads to the decrease of the strength, the increase of the plasticity and the fracture toughness. The material has a certain strength and needs good plastic properties in order to be cold processed into the spring, so “the 550 ℃, 10 h, air cooling” and other aging processes are selected.
In the field of aviation, TC18 and TB6 are used instead of TC4 and high-strength steel, which can reduce the weight of the aircraft by nearly 15 %. Through heat treatment, the reasonable match of high strength, high plasticity and high fracture toughness can be obtained. The experiments results show that TC18 and TB6 have good effect in practical application to titanium alloy spring cold working, under the condition of 740±10 ℃, thermal insulation for 2 h, quenching, heating to 550±10 ℃, insulation for 10 h and air cooling heat treatment.
5.3. Effect of spring forming method
The spring forming methods are classified into 2 categories: the mandrel coiling and the no-mandrel coiling. The mandrel coiling is widely used in small and medium batch production or spring coiling with special design and special requirements. In mass production, this method is also applicable to coil torsion springs and some extension springs. In coiling, some necessary technical measures should be taken to ensure that the extension spring can have a certain initial tension. In the mass production, the automatic spring coiling machine is widely adopted to coil spring, and the coiling method is the no-mandrel coiling. The no-mandrel coiling can realize operations like automatic winding, cutting and counting, and has a certain working cycle to complete the forming process of the spring. So the no-mandrel coiling has advantages of low labor intensity, high production efficiency and high material utilization rate, and can realize multi-machine operation. The automatic spring coiling machine with single mandrel is more suitable for coiling the spiral spring with high initial tension. There are many factors affecting the initial tension of tension spring, such as the tensile strength, elongation, elastic modulus, yield ratio, dimensional accuracy, surface conditions, feeding length and coiling speed of the material, the technical level of the operator and so on. As the initial tension of the rose-bow spring is 2420 N, further processing methods and heat treatment processes of large initial tensile force will be further studied.
6. Conclusions
An optimal design and improved processing technology for the rose-bow titanium alloy spring of subway pantograph was studied in this paper, some main conclusions can be drawn out as follows: 1) TB6 and TC18 materials can meet the technical requirements of installation space and spring stiffness of the rose-bow spring, and have interchangeability with the original spring. 2) The large maximum working stress of the original rose-bow spring is also one of the main causes of the extension spring fracture. When the rose-bow spring material is changed into titanium alloy, the maximum working stress is reduced from 1076.15 MPa to 692.82 MPa (TB6) and the weight is reduced from 16.357 kg to 9.963 kg (TB6) through optimization design. 3) There are two kinds of heat treatment methods for hot rolled bars, namely, “heating to 740±10 ℃, 2 h thermal insulation, quenching” and “heating to 550±10 ℃, 10 h insulation, air cooling”. 4) The titanium alloy spring forming process includes roll forming, spring grinding, aging treatment, non-destructive testing, shot peening treatment and properties testing. 5) In order to roll spring with large initial tension, further research on the processing method and heat treatment process is required.
References
-
C. Y. Wang and W. J. Xi, “Investigation on notch sensitivity of TC18 titanium alloy,” Rare Metal Materials and Engineering, Vol. 41, No. 4, pp. 663–666, 2012.
-
Z. H. Huang, C. Wang, L. S. Sun, and J. Zhou, “Application prospect of titanium alloy materials in rail transit,” (in Chinese), Electric Drive for Locomotives, Vol. 254, No. 1, pp. 14–16, 2017.
-
Z. H. Huang, H. J. Zhang, and Y. P. Sun, “Design of primary spring for three-axle bogie,” (in Chinese), Electric Drive for Locomotives, Vol. 191, No. 4, pp. 36–37, 2005.
-
Z. H. Huang et al., “Discussing on dynamic load coefficient of locomotive’s first spring,” (in Chinese), Electric Drive for Locomotives, Vol. 214, No. 3, pp. 39–41, 2009.
-
H. Hao et al., “Research on the technics of aging treatment for blade spring,” (in Chinese), Vacuum and Cryogenics, Vol. 19, No. 1, pp. 30–35, 2013.
-
L. Y. Zeng and P. Ge, “Progress in high strength titanium alloy for spring,” (in Chinese), Titanium Industry Progress, Vol. 26, No. 5, pp. 5–9, 2009.
-
G. Q. Shang et al., “Development of ultra-high strength titanium alloy,” (in Chinese), Rare Metals, Vol. 35, No. 2, pp. 286–291, 2011.
-
Y. K. Gao, “Effect of shot peening on tensile-tensile properties of TC18 titanium alloy,” (in Chinese), Rare Metal Materials and Engineering, Vol. 33, No. 9, pp. 1000–1001, 2004.
-
G. Wang, S. X. Hui, and W. J. Ye., “Microstructure and tensile properties of low cost titanium alloy at different colling rate,” Rare Metals, Vol. 31, No. 6, pp. 531–536, 2012.
-
H. Shao, Y. Zhao, W. Zeng, P. Ge, and Y. Yang, “Review on influence of microstructure on strength and fracture toughness in α+β titanium alloy,” (in Chinese), Rare Metal Materials and Engineering, Vol. 41, No. 7, pp. 1313–1316, Jul. 2012.
-
Z. An, Jinshan Li, and Yong Feng, “Microstructure evolution of a new near-β titanium alloy: Ti555211 during high-temperature deformation,” Rare Metals, Vol. 34, No. 11, pp. 757–763, 2015.
-
Z. An, J. S. Li, and Y. Feng., “Optimization of thermal processing parameters of Ti555221 alloy using processing amps based on Murty criterion,” Rare Metals, Vol. 35, No. 2, pp. 154–161, 2016.
-
H. Wu, Y. Zhao, W. Zeng, and L. Qian, “Fatigue crack growth behaviors of a new burn-resistant highly-stabilized beta titanium alloy,” Rare Metals, Vol. 28, No. 6, pp. 545–549, Dec. 2009, https://doi.org/10.1007/s12598-009-0105-4
-
L. Li et al., “Impact of solution and aging treatment on the properties of TB9 alloy and its spring,” (in Chinese), Titanium Industry Progress, Vol. 29, No. 5, pp. 30–32, 2012.
-
J. Y. Zhou and D. Q. Wang, “Study and application of titanium alloy spring,” (in Chinese), Materials Development and Application, Vol. 26, No. 1, pp. 92–95, 2011.
About this article
This study is supported by National Natural Science Foundation of China (U19A20109).