Abstract
The purpose of this research is to develop the spherical ultrasonic motor (SUSM) for space. The SUSM is a small multi-DOF motor. The various performances are requested of the motor for space. The experiments under the high temperature environment were carried out to check the durability to the radiant heat from the sun this time. Our experimental results showed that SUSM for space also maintains the drive performance under the high temperature environment. The material of piezoelectric elements and adhesives which influence the performances of SUSM for space will be reported in detail.
1. Introduction
In recent years, space development is active with progress of science and technology. Posture control and course correction of the spacecraft (the artificial satellite, the International Space Station, etc.) which exist in circling orbit of the earth are performed by jetting the thrusters periodically. However, the thrusters are equipped in the spacecraft because the direction of the installation of general thruster is fixed. This is the restriction of miniature and the factor of weight increase to the spacecraft. When changing thrusters to a thruster with a multi-DOF motor, miniaturization of the spacecraft is achieved.
The purpose of this research is to develop the spherical ultrasonic motor (SUSM) [1-3] for space. The SUSM is a small multi-DOF motor. The compatibility with SUSM and the small satellite which tends to be increased is very good. On the other hand, the various performances are requested of the motor for space. The experiments under the high temperature environment were carried out to check the durability to the radiant heat from the sun this time. Our experimental results showed that SUSM for space also maintains the drive performance under the high temperature environment. The material of piezoelectric elements and adhesives which influence the performances of SUSM for space will be reported in detail.
2. Spherical ultrasonic motor
2.1. Feature of SUSM
The ultrasonic motor consists of a rotor of drive part and a circle stator of a piezoelectric element and a metallic elastic body, and drives by mechanical vibration in 20 kHz or any more ultrasonic range. Our SUSM catches globular rotor in three of circle stator as shown in Fig. 1. The most excellent feature of this motor is to have 3 degree of freedom by one individual.
2.2. Specification of motor for space
In the SUSM for space of this research, a diameter of stator is 30 mm and a diameter of rotor is 45 mm. These are the size suitable for the thruster of the spacecraft. And the following performance is requested as a motor for space. These performances should also be satisfied completely to use SUSM as the motor for space.
1) Drive at the ultrahigh vacuum environment (approximately 10-6 Pa).
2) Thermal resistance in a vacuum environment.
3) Outgassing isn’t released in a vacuum environment.
4) Shock resistance and acceleration resistance in a lift-off (100 Hz, 20 G).
5) Space radiation resistance.
6) Drive by maintenance-free in an operating period of a satellite.
On the other hand, a satellite receives radiant heat from the sun and radiates thermal for space by the other side of the satellite. Therefore superficies of satellite receives severe thermal cycles. Thermal cycling test of JAXA (Japan Aerospace Exploration Agency) is performed from –120 °C to +120 °C. Drive of SUSM under the high temperature environment included in this temperature range (from normal room temperature to +120 °C) set as the first target of this research. A thruster jet for vehicle posture control of a satellite is about 20 times per a year and is about 20 seconds for once. When an operating period of a satellite is 10 years, our durable target of SUSM is drive for total of 70 minutes.
Fig. 1Schematic of SUSM
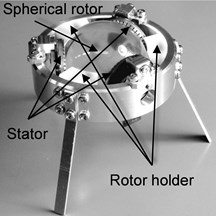
3. Consideration of piezoelectric element
3.1. Choice of piezoelectric element
A Curie point of a piezoelectric element of former SUSM was 120 °C. When making a piezoelectric element warp, piezoelectric loss generates heat. And when the stator temperature of SUSM for space reached about 120 °C assumed in space, the actual stator temperature becomes higher than 120 °C. Therefore former SUSM can’t maintain the drive performance under the high temperature environment of ambient temperature 120 °C.
So at first, selection of a piezoelectric element with a high Curie point was tried. These other conditions of the piezoelectric element requested of SUSM for space are that an electromechanical coupling coefficient, a mechanical quality coefficient and a piezo-electric constant are high respectively. The electromechanical coupling coefficient shows the change efficiency to the mechanical energy observed as the amplitude of the travelling wave from electrical input. The mechanical quality coefficient shows the size of the elasticity loss when a piezoelectric element has an elastic strain. And the piezo-electric constant shows the size of the distortion of the piezoelectric element to the given electric field. It was based on these selecting conditions, and a piezoelectric element using N6 material made by NEC/TOKIN Co. was selected by this experiment. Here, this piezoelectric element is called N6 piezoelectric element. A Curie point of N6 piezoelectric element is 325 °C, and it can be predicted that it's possible to indicate piezoelectric even under the assumed high temperature environment.
3.2. Evaluation of selected piezoelectric element
The torque and the number of rotations were measured to new SUSM using a selected N6 piezoelectric element and former SUSM. The result is indicated in Table 1. The impedances were measured using an impedance analyzer. The result is indicated on Fig. 2. Further, the impedances were measured in the normal room temperature (25 °C) and the atmosphere pressure. Here, in impedance curved line of piezoelectric element, the frequency which indicates a minimum value of impedance is called a resonant frequency. Output of ultrasonic motor becomes biggest by this frequency. And indicators with the size of the piezoelectric effect are the difference between the minimum value and the maximum value of the impedance, and the sharpness of impedance of the resonant frequency and the anti-resonance frequency (the frequency when impedance indicates the maximum).
On the other hand, an axis was installed in the spherical rotor, a load was given to an axis by suspending a weight through a pulley, and the torque of SUSM was measured. Table 1 and Fig. 2 show that change to a new piezoelectric element doesn’t have a remarkable influence on the torque, the number of rotations and the resonant frequency.
Table 1Torque and rotation speed of SUSM
Piezoelectric element | Torque [mNm] | Rotation speed [rpm] |
Old material | 29.3 | 74.2 |
New material (N6) | 41.5 | 62.5 |
Fig. 2Impedance characteristic of piezoelectric element at 25 °C
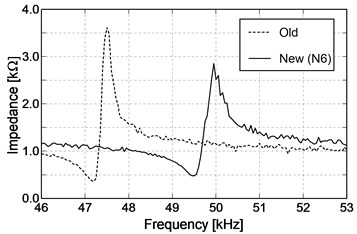
Fig. 3Impedance characteristic of stator using N6 material
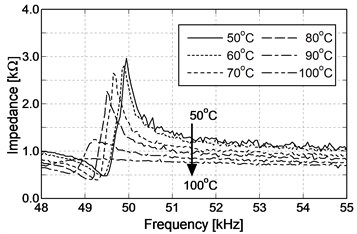
3.3. Performance test of piezoelectric element
To confirm that a selected N6 piezoelectric element indicates piezoelectric under the high temperature environment, the impedances were measured under the atmospheric pressure, increasing the stator temperature of SUSM. Thermocouple was set the surface of stator using N6 piezoelectric element, and the stator was established in the thermostatic chamber. The chamber temperature is set as 50 °C, the state that the stator temperature became equal to the chamber temperature is defined as the thermal balance and measurement of impedance of stator has been begun from that time. And impedances were measured every 10 °C until the chamber temperature was 100 °C.
Results of the acquired impedance characteristic are indicated on Fig. 3. When setting the temperature of stator to 50 °C, impedance showed a sudden change around the resonant frequency and the anti-resonance frequency. When involving temperature increase of stator, impedance in a resonant frequency and in the anti-resonance frequency neighborhood were a gentle change, and when the temperature of stator was 100 °C, a sharp peak of an impedance curved line wasn’t seen any more. Further when making the temperature of stator decrease from 100 °C to 50 °C, the result similar to Fig. 3 mostly was obtained. There is reproducibility in loss of piezoelectric by the temperature. Therefore the cause by which piezoelectric is lost by about 100 °C isn’t because the internal temperature of the piezoelectric element reached a Curie point.
For softening of adhesive, piezoelectric is lost under the high temperature environment. On the other hand, to join a metallic elastic body to a piezoelectric element in SUSM, adhesive of thermal hardening is used. The travelling wave which generated by a piezoelectric element is transmitted to a metallic elastic body through adhesive. Molecular motion will be suddenly extensively under the high temperature environment, and adhesive of thermal hardening increases fluidity. This temperature which begins to show fluidity is called glass transition point. When ultrasonic motor is driven by temperature environment higher than glass transition point, the travelling wave which generated by a piezoelectric element isn't communicated to a rotor by buffer action of adhesive. And when adhesive softened, a transformable load by the metallic elastic body which was controlling elastic deformation of a piezoelectric element disappears, and the impedance falls. A sudden change of the impedance in the resonant frequency and in the anti-resonance frequency neighborhood is lost. When the adhesive beyond glass transition point is cooled, the adhesive is hardened again, and it's possible to communicate the travelling wave which has generated by a piezoelectric element to a metallic elastic body. The result like Fig. 3 was obtained by such factor.
4. Consideration of adhesive
4.1. Choice of adhesive
The adhesive used in SUSM for space based on results of measurement of impedance under the high temperature environment was considered. Selecting conditions of an adhesive suitable for SUSM for space can mention high glass transition point, large the detaching bonding strength and the shearing bonding strength without conductivity after setting and high hardness after setting. For vibration by electrostrictive strain of piezoelectric element to give big load to all directions to adhesive, the strength of the adhesive has to be kept by the shearing direction and the detaching direction hard together. The hardness of the adhesion linkage after adhesive indurating has to be high to transmit to a metallic elastic body without travelling-wave vibration by piezoelectric element being absorbed by adhesion linkage.
Three kinds of adhesive indicated below were compared based on the selecting conditions of adhesive mentioned above.
1) Made by ThreeBond Co., Ltd., TB2285.
2) Made by Aremco Products Inc., Aremco-Bond 570.
3) Made by Tokyo Chemical Industry Co., Ltd., B1796/M0567/D0688 (3 liquid mixtures).
The stators were made using these adhesives and drive experiments of spherical rotor were carried out respectively using 1 axis experimental device indicated on Fig. 4. As results, the spherical rotor which drove was only stator using TB2285. Further, glass transition point of TB2285 is 185 °C, and travelling wave is estimated to communicate without softening under the high temperature environment of the target (120 °C).
4.2. Evaluation of selected adhesive
Stators were made using selected adhesive TB2285, and the impedance was measured while heating it in the thermostat chamber. Further, a piezoelectric element is the above-mentioned N6 piezoelectric element. Impedance characteristics of result of measurement are indicated on Fig. 5. This result is compared with Fig. 3. The adhesive TB2285 maintains piezoelectric under the high temperature environment. Sharpness of the impedance curved line isn’t lost under the high temperature environment of the target (120 °C), and piezoelectric is maintained.
5. Durability of thermal load to SUSM for space
5.1. Performance evaluation by separate stator
Stator was made using selected piezoelectric element, adhesive and metallic elastic body, and the performance of separate stator was evaluated. Polyimide suitable for drive of SUSM was chosen in the material of the spherical rotor. This polyimide has a high good record of performance as the structure material for space. The drive experiments were carried out using 1 axis experimental device indicated on Fig. 4. The temperature of the stator surface was heated from 30 °C to 160 °C in the thermostat chamber. The experiment which drives a motor for 20 seconds in the temperature every 10 °C was carried out. To check the number of rotations of the motor from a frame rate and the number of recorded frames, a motor-driven animation was acquired using a video camera. And a change in the number of rotations of the motor by the rise of the temperature was measured. The experimental results are indicated on Fig. 6. The number of rotations of the spherical rotor is falling gradually with a rise of the stator temperature. But the drive of the motor in the target state (120 °C) could be confirmed.
Fig. 4Single axis SUSM using selected adhesive
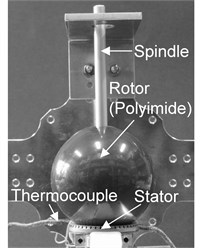
Fig. 5Impedance characteristic of stator using selected adhesive
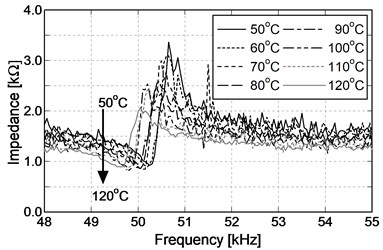
Fig. 6Result of limit temperature experiment (single axis)
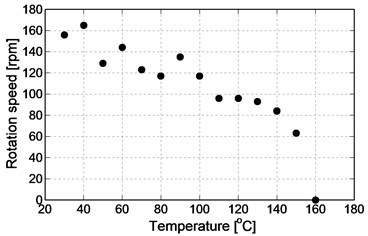
Fig. 7Result of thermal load experiment (single axis)
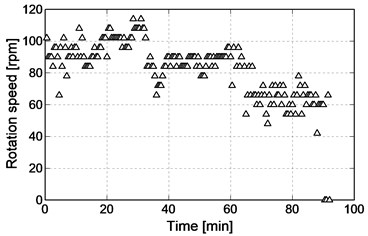
5.2. Test of durability with thermal load
The durability experiments with thermal load were carried out using 1 axis experimental device. After becoming equivalent in the temperature of the thermostat chamber (120 °C) and the temperature of the stator, the stator was driven for 20 seconds. After pause for 1 minute, the stator was driven for 20 seconds again. This work was repeated, and a change in the number of rotations to the total time of the drive was measured. This work is based on a thruster jet of a satellite in space being performed for about 20 seconds once for 2-3 weeks. The experimental state was acquired by a video camera. And the number of rotations of the motor was calculated from the number of recorded frame and frame rate. The experimental results are indicated on Fig. 7. 70 minutes of a target were achieved because the spherical rotor was driven for 90.5 minutes under the high temperature environment of 120 °C. But accumulation of internal generated heat is a factor for a stop of the motor which has occurred 90.5 minutes later.
5.3. Test of durability with thermal load to SUSM for space
Prototype SUSM for space was made using N6 piezoelectric element and TB2285 adhesive. Prototype SUSM for space was indicated on Fig. 8. The durable experiment with thermal load was carried out by the same way as 1 axis driven experiment. Further, drive of Prototype SUSM for 20 seconds was carried out along a rail in the fixed direction. To radiate heat which generated from a piezoelectric element during a pause, the pause was set to 10 minutes.
Experimental results are indicated on Fig. 9. The durable experiment with thermal load of SUSM for space was carried out. Total driven time of a target (70 minutes) was achieved. The drive performance exceeded 90.5 minutes of 1 axis driven experiment. SUSM at this time also kept driving beyond 90 minutes and didn’t stop it.
Fig. 8Schematic of prototype SUSM for space using selected materials
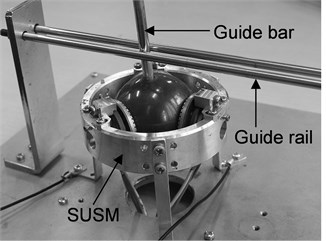
Fig. 9Result of thermal load experiment (prototype SUSM for space)
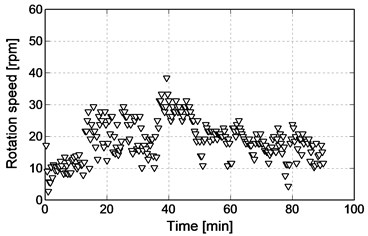
6. Summary
Development of spherical ultrasonic motor (SUSM) for universe is being tried by this research. Much performance is requested of a motor for space. The durable experiment was carried out to confirm that developed SUSM for space maintains the drive performance under the high temperature environment by this paper. The durable target is drive time beyond 70 minutes under the high temperature environment, ambient temperature +120 °C.
The piezoelectric element was selected at first. The Curie point of the piezoelectric element has to be high in drive of SUSM for space under the high temperature environment. The result showed that glass transition point of adhesive under the high temperature environment becomes one of problems. The piezoelectric element and the metallic elastic body are stuck using adhesive. And the adhesive was selected at the same time. The piezoelectric element and the adhesive were selected appropriately and prototype SUSM for space was made. The stator in prototype SUSM maintained the piezoelectric performance under the high temperature environment. The durable experiment of thermal load was carried out under the high temperature environment. Total of 70 minutes which are the target value of drive time were achieved.
In the future, the drive performance of SUSM for space will be estimated under the low temperature environment of –120 °C assumed as temperature environment of space. And moreover, the drive performance about thermal cycle of ±120 °C which is temperature environment near operational condition at the space is estimated. Finally, realization of SUSM for space is aimed at.
References
-
Oohashi T., Nishizawa U., Fukaya N., Toyama S. Spherical ultrasonic motor for space. Proceedings of the 6th ICMDT, No. 15-204, 2015, p. 258-259.
-
Toyama S., Oohashi T., Fukaya N. Development of spherical ultrasonic motor for space. Proceedings of Actuator, Vol. 14, 2014, p. 289-292.
-
Oohashi T., Toyama S. Development of spherical ultrasonic motor for space. Applied Mechanics and Materials, Vol. 555, 2014, p. 26-31.