Abstract
The tire industry involves complex processes that require high temperatures and pressures for tire production and processing. In these processes, rubber dough is placed in molds using baking presses and shaped under high temperature and pressure. Manifold blocks are used to feed the molds in these presses and to ensure equal temperature distribution between the molds. However, existing manifold blocks tend to deform in a short time under high temperature and pressure and require constant maintenance. These changes can affect production continuity, reduce production quality and increase maintenance costs. Therefore, there was a need to research a more durable and low-maintenance manifold solution. In this study, Thermal Flow analysis was performed on the Cooking Press Manifold using the “Generative Design” method and the appropriate operating level of the system was determined.
1. Introduction
The global tire market is a sector that constantly develops demand due to the increase in the number of vehicles and the increase in travel times [1]. This development makes competition increasingly complex [2]. Tire manufacturers need end-to-end solutions they can use to optimize the availability of their facilities, reduce overall operating costs, and improve time to market [3-6]. Mechatronic system design and new business models introduced by digitalization help in improving these processes [7-12].
Tire is a product name and is a compound consisting of natural rubber, synthetic rubber, carbon black and oil [13-14]. Here, rubber, which is a natural material and produced from the rubber tree, has a volumetric size of around 80 % [15, 16]. However, synthetic rubber can also be produced in Europe [17, 18]. It can be defined as a rubber matrix structure. The remaining ingredients constitute the supplement part. Tires get their black color from Carbon and this additive is called Carbon black. Oil is used as another additive. Oil is used as a plasticizer [19-21]. In the production of the tire, the mixture is heated at 120 °C. The duration of this heating process and the type of rubber are selected according to the intended use of the tire [22].
Diversification of tires according to their intended use depends on production recipes [23, 24]. Production methods are as important a factor as components in the production of tires [25]. When the components are placed on the drum in the assembly lines, they begin to take shape on the surface of the stretching machine. Pressure is applied to the component placed on the loading wheel of the machine and the tire appears. Vulcanization method is applied in the shaping process [26]. The rubber is taken to the hardening unit and the shaping process is completed with high steam pressure [27]. In determining the quality of the tire [28, 29], the material content [30] as well as the precision and control in the production process have an important impact.
The manifold structure developed in the study is a device used to give the final shape to the tires to be produced by applying pressure. Tire production for all transportation vehicles is carried out using similar systems. Tires produced with this system can be used in air, land and even sea vehicles. Automation in the production system can be improved or transformed depending on the green tire standard (tire structure before product state). A production system suitable for the intended use of the tire should be developed. In addition, this developed production system is a determinant of tire quality as well as tire type [31].
Tire curing presses can be operated individually or jointly depending on developing production technologies. These presses have a long column design that uses a locking and clamping system according to the desired features [32]. Although we have special designs, we can focus on 2 types of presses: mechanical tire curing press and hydraulic tire curing press. The mechanical press, which keeps the mold closed through articulated connections, is more preferred due to its easy maintenance. However, there are hydraulic presses in which hydraulic oil is used for the movement of the machine. Hydraulic presses secure the mold with a wedge lock mechanism [5, 33].
The aim of this study is to examine the performance of the system that controls the effect of high temperature and pressure in the pressing method used in the final stage of tire production and to redesign the geometry in the flow part of the manifold with productive design.
2. Method
As the process temperature increases, instability and complexity in thermal behaviour may be observed. This may have an effect that makes it difficult to control the production system. By placing the tire compounds into the molds, the system reaches high pressure and temperature values. Proper production of the product requires maintaining equal temperature in the manifolds. Otherwise, deterioration and deformation will occur in the products, which will cause losses such as cost, resources, time and processing time as faulty production. Maintenance costs arise when the system is stressed. In this study, a design that is durable and requires less maintenance in the production line has been put forward to eliminate the mentioned problems.
In the study, the optimum operating level of the system was determined by performing Thermal Flow analysis on the Cooking Press Manifold using the Generative Design method. Finite element analysis was used to achieve the targeted results in the study.
Fig. 1CAD model and pneumatic diagram of the baking press manifold system
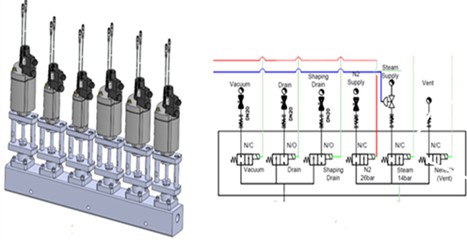
3. Results
3.1. System flow analysis
The behavior affecting the flow analysis of the system is based on the system being cooked with rubber water vapour on the manifold and cooled with nitrogen gas. The system cooks the semi-finished tire with water vapour at 230 °C under 14 bar and cools it with nitrogen under 26 bar pressure, reducing the temperature to 25 °C. In this study, the flow analyses of different materials used in these two different processes in the developed system, under different pressures, were examined in order to keep the variable pressure and temperature values of the system stable. Different analyses were made for pressure and temperature effects in flow analyses. For these analyses, the volumes with flow were investigated in the CAD model and volume regions were created for two different analyses. (Fig. 2) Additionally, the temperature distribution under the temperatures applied to the tire baking press manifold was calculated using finite element analysis.
Fig. 2Flow analysis study region to be analyzed flow (water vapor and nitrogen)
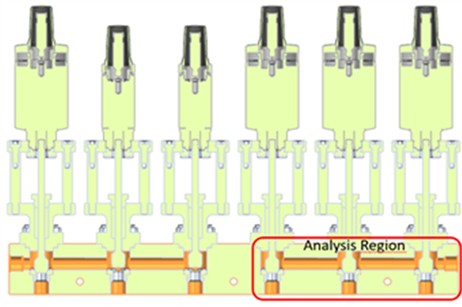
a)
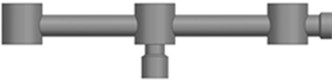
b)
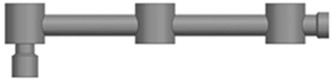
c)
Finite element analysis values (FEA) were obtained in the case of two different scenarios in flow analyses, cooking with steam and cooling the tire with nitrogen.
In the flow analysis of water steam cooking process, the pressure measurements in the flow volume region and the flow velocity changes in the flow volume as a result of the flow analysis of water vapor under 26 bar are presented in Fig. 3. The pressure measurements of the Nitrogen gas used to cool the cured tire in the process and the flow rate changes.
Fig. 3Analysis results during flow analysis in the Tire Curing and Cooling process as pressure changes (bar) and flow rate changes (m/s)
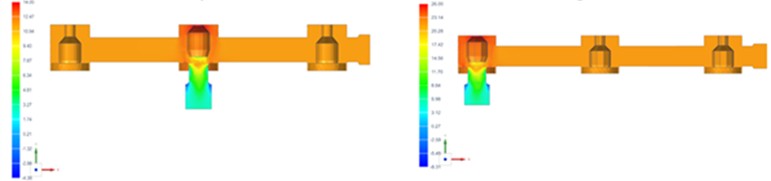
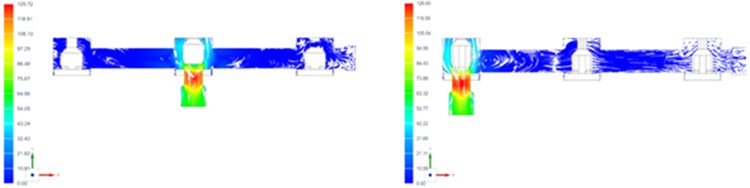
Flow analysis results show that; It can be seen that the new manifold design we designed feeds the tire compound evenly. In this way, product quality and efficiency increased in the production of tires. The same analysis method was applied to observe the temperature changes in the manifold part of the flow of the designed system. Thermal analysis results are seen in Fig. 4.
Fig. 4Temperature distribution of the Tire Curing manifold during the process
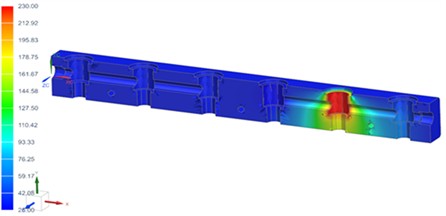
3.2. Redesigning the flow path with generative design (GD)
This approach offers a different perspective from traditional design processes. It can automatically generate a large number of possible solutions to solve design problems.
While GM can increase the originality and innovativeness of the design, it can also improve the functionality, cost-effectiveness and performance of the design. At the same time, GD can be an effective tool to solve complex and difficult to optimize design problems. This approach offers designers the opportunity-ty to explore solutions they might not have considered before and encourages creativity. It is especially used in areas such as product development, industrial design, architecture and engineering. This new approach can be used to solve design problems for fluids (such as liquids or gases). Such de-signs may often need to incorporate fluid dynamics, heat transfer, and similar physical phenomena. GD for fluids; It can be used in energy efficiency, fluid dynamics optimization, thermal design and many other areas. This approach can accelerate the design process to understand and optimize complex fluid behavior and help you achieve improved results. Thus, it helps optimize factors such as pressure and velocity in the gas flow. Thanks to automatic algorithms, different design options can be produced. It may be possible to increase energy efficiency and performance. It also offers more creative solutions by managing complex constraints. It accelerates the design process and ensures cost-performance balance.
Fig. 5Analysis of the flow region with GD

The accuracy of the model put forward in the analysis of the system with GD was investigated. For this reason, as in flow analysis, the geometry used by the fluid was created in the CAD environment as shown in Fig. 5. Some inputs of the model created with GD have been entered into the system (Fig. 5). In these inputs, as shown in the figure, the regions that should be in my model (green color) and the regions that I do not want to be in my model (red color) are defined. Regions where gas cannot circulate or have limited circulation are identified in red. It is the part where the physical quantities (pressure, flow rate, etc.) in the part where the flow occurs are defined. As a result of these inputs, artificial intelligence-supported flow analysis of the model was investigated.
Fig. 6Analysis results and evaluation
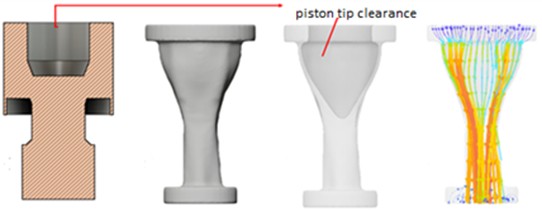
The model presented as a result of the analysis shows that the conical structure in the outlet region of the piston cavity in the initial design should be redesigned. A model has been put forward in which it would be appropriate to create an accurate flow model in order to maintain the outlet diameter of the flow as a constant diameter. The velocity changes resulting from the flow analysis of the model put forward by GD are shown in Fig. 7. As a result of the analysis, it caused an increase in the flow rate in the proposed model compared to the primitive model.
Fig. 7Changes in flow velocity (m/s) of the model proposed by GD
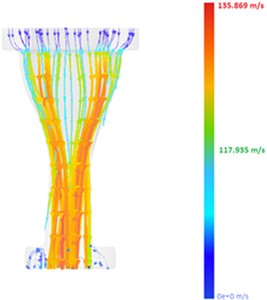
4. Conclusions
A new manifold solution that addresses the inadequacies of manifold blocks used in curing presses in the tire industry has been scientifically evaluated. This new solution offers an option that has a longer life, requires less maintenance and improves production quality. Flow and thermal analysis results also support the effectiveness of this new solution.
The model presented by GD to optimize the existing flow is a model proposed as a result of artificial intelligence-supported finite element study. It can be seen that the analysis results of this model can give better results than the first designed model.
These results show that the models put forward by GD contain a more complex geometry than their natural forms. In order to produce these models, production methods different from traditional production methods must be used. Although this situation seems to be a disadvantage of GM, there are rapid developments in production techniques and technologies. The GM method can produce better results for new generation manufacturing techniques such as additive manufacturing techniques.
In the flow analysis of the first design identified in the study, the suitability of the model is seen thanks to the negligibility of pressure change losses as a result of the formation of laminar flow and the opportunities provided by the production of the model with the classical method. We hope that this study and the design designed to solve this problem will contribute to the literature.
References
-
S. M. R. Costa, D. Fowler, G. A. Carreira, I. Portugal, and C. M. Silva, “Production and upgrading of recovered carbon black from the pyrolysis of end-of-life tires,” Materials, Vol. 15, No. 6, p. 2030, Mar. 2022, https://doi.org/10.3390/ma15062030
-
C. Koch et al., “A matheuristic approach for solving a simultaneous lot sizing and scheduling problem with client prioritization in tire industry,” Computers and Industrial Engineering, Vol. 165, p. 107932, Mar. 2022, https://doi.org/10.1016/j.cie.2022.107932
-
N. Sunthonpagasit and M. R. Duffey, “Scrap tires to crumb rubber: feasibility analysis for processing facilities,” Resources, Conservation and Recycling, Vol. 40, No. 4, pp. 281–299, Mar. 2004, https://doi.org/10.1016/s0921-3449(03)00073-9
-
M. L. Kreider, W. D. Cyrs, M. A. Tosiano, and J. M. Panko, “Evaluation of quantitative exposure assessment method for nanomaterials in mixed dust environments: application in tire manufacturing facilities,” Annals of Occupational Hygiene, Vol. 59, No. 9, pp. 1122–1134, Jul. 2015, https://doi.org/10.1093/annhyg/mev052
-
M. Fazli-Khalaf, B. Naderi, and M. Mohammadi, “Design of a reliable supply chain network with responsiveness considerations under uncertainty: case study of an Iranian tire manufacturer,” Journal of Industrial and Systems Engineering 11. Special issue: 14th International Industrial Engineering Conference, Vol. 11, pp. 120–131, 2018.
-
R. Shahpasand, A. Talebian, and S. S. Mishra, “Investigating environmental and economic impacts of the 3D printing technology on supply chains: The case of tire production,” Journal of Cleaner Production, Vol. 390, p. 135917, Mar. 2023, https://doi.org/10.1016/j.jclepro.2023.135917
-
J. Stolfa et al., “Automotive engineering skills and job roles of the future?,” in Systems, Software and Services Process Improvement: 27th European Conference, 2020.
-
L. Lattanzi, R. Raffaeli, M. Peruzzini, and M. Pellicciari, “Digital twin for smart manufacturing: a review of concepts towards a practical industrial implementation,” International Journal of Computer Integrated Manufacturing, Vol. 34, No. 6, pp. 567–597, Jun. 2021, https://doi.org/10.1080/0951192x.2021.1911003
-
S. Krüger, B. D. S. Saulo, and B. Milton, “Perceptions of a digital twin application case in the auto industry,” in International Conference on Flexible Automation and Intelligent Manufacturing, 2022.
-
N. Xu et al., “A Direct Slip Ratio Estimation Method based on an Intelligent Tire and Machine Learning,” arXiv:2106.08961, 2021.
-
C. Tian, B. Leng, X. Hou, L. Xiong, and C. Huang, “Multi-sensor fusion based estimation of tire-road peak adhesion coefficient considering model uncertainty,” Remote Sensing, Vol. 14, No. 21, p. 5583, Nov. 2022, https://doi.org/10.3390/rs14215583
-
L. Chen, Y. Luo, M. Bian, Z. Qin, J. Luo, and K. Li, “Estimation of tire-road friction coefficient based on frequency domain data fusion,” Mechanical Systems and Signal Processing, Vol. 85, pp. 177–192, Feb. 2017, https://doi.org/10.1016/j.ymssp.2016.08.006
-
R. G. Dos Santos, C. L. Rocha, F. L. S. Felipe, F. T. Cezario, P. J. Correia, and S. Rezaei-Gomari, “Tire waste management: an overview from chemical compounding to the pyrolysis-derived fuels,” Journal of Material Cycles and Waste Management, Vol. 22, No. 3, pp. 628–641, Feb. 2020, https://doi.org/10.1007/s10163-020-00986-8
-
L. Torosian and I. Chernyaev, “Method of creating control framework for environmental safety of car tires,” Transportation Research Procedia, Vol. 50, pp. 689–697, Jan. 2020, https://doi.org/10.1016/j.trpro.2020.10.081
-
A. Akbas and N. Y. Yuhana, “Recycling of rubber wastes as fuel and its additives,” Recycling, Vol. 6, No. 4, p. 78, Dec. 2021, https://doi.org/10.3390/recycling6040078
-
M. Momeen Ul Islam, J. Li, R. Roychand, and M. Saberian, “Investigation of durability properties for structural lightweight concrete with discarded vehicle tire rubbers: A study for the complete replacement of conventional coarse aggregates,” Construction and Building Materials, Vol. 369, p. 130634, Mar. 2023, https://doi.org/10.1016/j.conbuildmat.2023.130634
-
V. Mahler, “Allergic reactions to rubber components,” in Contact Dermatitis, Cham: Springer International Publishing, 2020.
-
H. Chittella, L. W. Yoon, S. Ramarad, and Z.-W. Lai, “Rubber waste management: A review on methods, mechanism, and prospects,” Polymer Degradation and Stability, Vol. 194, p. 109761, Dec. 2021, https://doi.org/10.1016/j.polymdegradstab.2021.109761
-
H. Xu et al., “Plasticization effect of bio-based plasticizers from soybean oil for tire tread rubber,” Polymers, Vol. 12, No. 3, p. 623, Mar. 2020, https://doi.org/10.3390/polym12030623
-
M. Nur Raihan et al., “Perspective on opportunities of bio-based processing oil to rubber industry: A short review,” Iranian Polymer Journal, Vol. 32, No. 11, pp. 1455–1475, 2023.
-
S. M. Al-Salem, “Slow pyrolysis of end of life tyres (ELTs) grades: Effect of temperature on pyro-oil yield and quality,” Journal of Environmental Management, Vol. 301, p. 113863, Jan. 2022, https://doi.org/10.1016/j.jenvman.2021.113863
-
A. Sanchís, A. Veses, J. D. Martínez, J. M. López, T. García, and R. Murillo, “The role of temperature profile during the pyrolysis of end-of-life-tyres in an industrially relevant conditions auger plant,” Journal of Environmental Management, Vol. 317, p. 115323, Sep. 2022, https://doi.org/10.1016/j.jenvman.2022.115323
-
B. S. Okan et al., “Graphene from waste tire by recycling technique for cost-effective and light-weight automotive plastic part production,” in 35th International Conference of the Polymer Processing Society (PPS-35), 2020.
-
L. Rodriguez‐Guadarrama, “Modeling of batch production of high vinyl styrene/butadiene copolymers for high performance tires,” Journal of Applied Polymer Science, Vol. 137, No. 45, p. 49415, Dec. 2020, https://doi.org/10.1002/app.49415
-
Y. Dong, Y. Zhao, M. U. Hossain, Y. He, and P. Liu, “Life cycle assessment of vehicle tires: A systematic review,” Cleaner Environmental Systems, Vol. 2, p. 100033, Jun. 2021, https://doi.org/10.1016/j.cesys.2021.100033
-
H. Huang, Z. Wang, C. Dai, J. Guo, and X. Zhang, “Volatile organic compounds emission in the rubber products manufacturing processes,” Environmental Research, Vol. 212, p. 113485, Sep. 2022, https://doi.org/10.1016/j.envres.2022.113485
-
I. A. Mikhailov, K. V. Sukhareva, E. A. Mamin, Y. O. Andriasyan, and A. A. Popov, “Extension of Working Resources of Diaphragms for Tire Forming and Vulcanization Presses,” in International Industrial Engineering Conferences, May 2023.
About this article
The authors have not disclosed any funding.
The datasets generated during and/or analyzed during the current study are available from the corresponding author on reasonable request.
Ahmet Çağrı Çağlıyan: conceptualization, data curation, formal analysis, funding acquisition, investigation, methodology, validation, visualization. Fikret Akyüz: conceptualization, project administration, software, supervision. Ahmet Feyzioğlu: resources, writing-original draft preparation, writing-review and editing. Sezgin Ersoy: conceptualization, resources, software, validation, writing-original draft preparation.
The authors declare that they have no conflict of interest.