Abstract
Viscoelastic damping structures under shock loading with variable amplitude and frequency are always in the multifactorial dynamic state, of which the shock response is obviously different from that under low strain rate. In order to accurately describe the impact mechanical properties of viscoelastic damped materials, a fractional order Maxwell model (FMM) is constructed. To verify the adopted model, the dynamic experiments for different strain rates (1800 s-1, 2500 s-1, 3500 s-1 and 4000 s-1) are performed by SHPB system. The experimental stress-strain curves should be divided into three stages: the linear stage, the strain-softening stage and the strain-hardening stage. As increase with the strain rate, the peak strain, the peak stress and the curvature of the curve in strain-softening stage increase, and the hardening effect in the strain-hardening stage tends to stronger, demonstrating a distinct strain rate effect in viscoelastic damped materials. The reason is that as increase of the strain rate, the action time of external loading gets closer to the relaxation time of the molecular chain segment, indicating the apparent strain rate-dependence of molecular slip and friction. The comparisons are made between the models of FMM, fractional Kelvin-Voight, ZWT and Ogden considering the strain rate-dependent. As a fractional-order model, FMM model has the minimum mean of RMSE 0.460 among the four models. The results indicate that FMM model could accurately describe the impact mechanical behavior characteristics of viscoelastic materials in a wider range of strain rate with comprehensive superiority of higher fitting precision, fewer parameters and clear physical meaning.
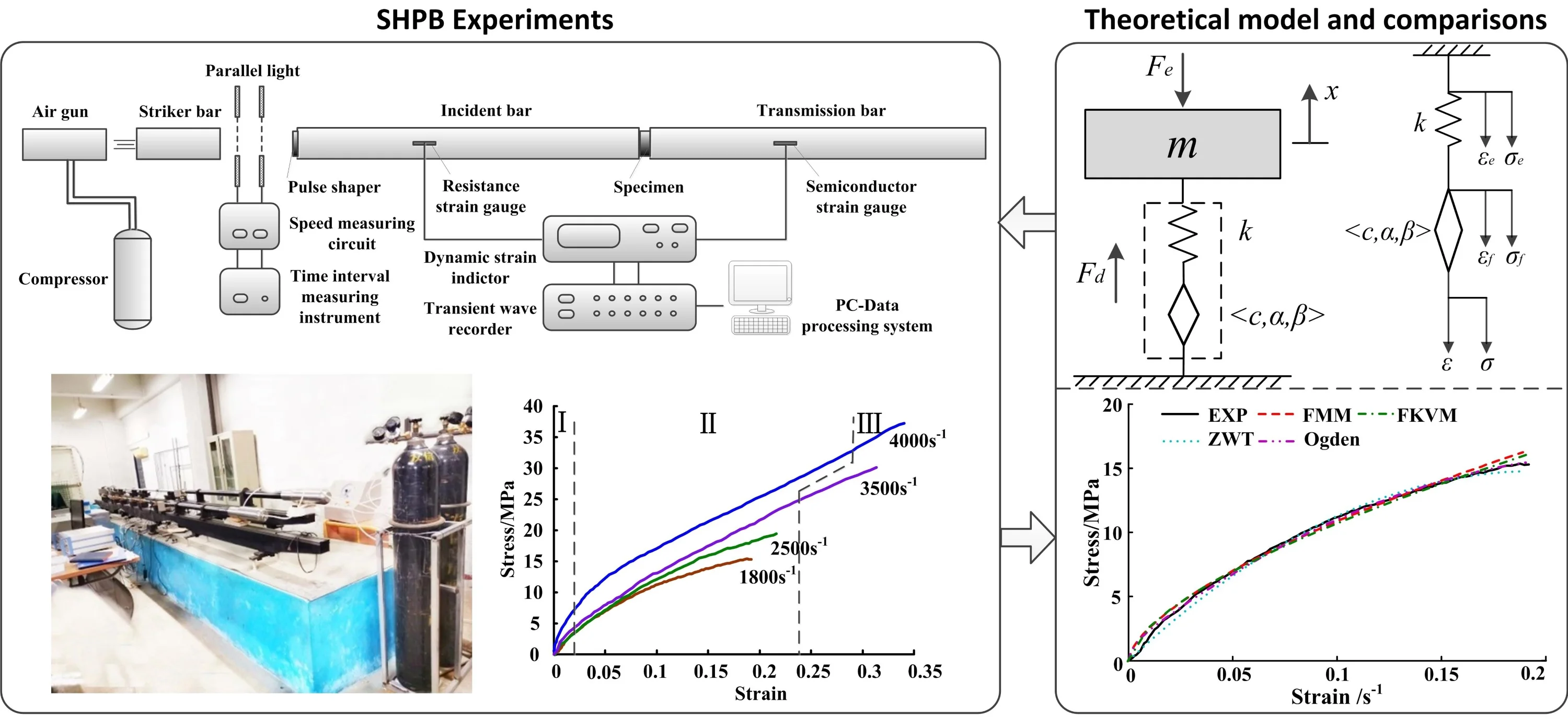
Highlights
- Investigation of the dynamic response of viscoelastic oscillator under shock loading conditions is presented
- The strain rate effect could be observed. With the strain rate increasing, the peak strain, the peak stress and the curvature of the curve in strain-softening stage increase, and the hardening effect
- Models of FMM, FKVM, ZWT and Ogden considering the strain rate-dependent are compared studied with SHPB experiments
- FMM model has a comprehensive superiority of higher fitting precision, fewer parameters and clear physical meaning to describe the shock mechanical behavior characteristics of viscoelastic materials
1. Introduction
Heavy-duty engineering vehicles, aeronautics and astronautics are often subjected to shock vibration with time-varying frequency and amplitude, inducing system equipment damage or failure. Viscoelastic damping structures are mounted on above systems to control vibration and noise by converting mechanical energy into heat consumption. The heat consumption is generated from internal friction, induced by hysteretic damping of viscoelastic materials. It is very common that viscoelastic engineering bears the shock loading with high amplitude and short duration. The strain rate of viscoelastic material under shock loading is about six or seven orders of magnitude higher than that of conventional quasi-static experiment. Under shock loading with variable amplitude and frequency, the damping structures are always in a multifactorial dynamic state, of which the dynamic responses are obviously different from that under low strain rates. A large number of studies on viscoelastic behavior of materials under low strain rate are mainly based on static load, quasi-static load and harmonic excitation experiments. The dissipation performance of damping structures based on above analyses could not well match to system parameters. Therefore, it is essential that the viscoelastic material characteristics at high train rate could be accurately and reliably described for the shock response analysis of viscoelastic damping structures.
The hysteresis properties of viscoelastic stress-strain relationship have attracted great attention of many researchers. Previous studies focus on the mechanical properties of viscoelastic material at low strain rates [1, 2]. These models may be divided into following several kinds of standard rheological model, complex modulus model, mini-oscillator model, fractional derivative model and fractional exponential model. The Maxwell, Kelvin-Voigt, standard linear solid, Bürgers and Zener models are the traditional and typical models. More recently, some viscoelastic constitutive model based new theories and methods are proposed. Xu Mingyu et al. [3] proposed a viscoelastic model based on new generalized fractional element networks, which should extend the model solutions to the generalized function space by adding the coordination equation and introducing the inverse Laplace transform using discrete data. Mulianaa A. et al. [4] formulated a nonlinear viscoelastic constitutive model based on multiple natural configurations and a single integral constitutive representation, which incorporated the effect of microstructural changes on the macroscopic deformations of polymers. Fractional viscoelastic models with non-singular kernels and the different performance of the models defined by different fractional derivative were investigated [5]. A fuzzy fractional K-V model considering the uncertainty in variables and the numerical algorithm using a spectral tau technique were presented [6]. Alotta G. et al. [7] came up with three-dimensional isotropic fractional viscoelastic model to simulate the viscoelastic behavior of complex components, and also proved that the model can satisfy the correspondence principles for the viscoelastic Poisson’s ratio.
The low-rate response of viscoelastic damping materials has been adequately studied, while a few researches focus on the shock response. The shock response can only be obtained by high strain rate experiments, but not by conventional quasi-static experiments. The split Hopkinson pressure bar (SHPB), invented by Kolsky in 1949, is a classical device to quantify the constitutive behavior of various materials at high strain rates [8-11]. The impedance and wave velocity of viscoelastic damping material is so small that some difficulties during the traditional SHPB test are encountered. On the one hand, the transmission signal is too weak to reach a better signal-to-noise ratio. On the other hand, it’s difficult to ensure the homogeneous deformation and stress equilibrium during the SHPB experiment. Meenken T et al. [12] presented a modified SHPB for testing low impedance materials and investigated large deformations of EPDM and PU rubber sample. Zhao Xijin et al. [13] investigated the dynamic compressive behaviors of a silicon rubber at high strain rates by applying quartz crystal. Lee O. S. et al. [14] analyzed the dynamic deformation of rubber by using the SHPB technique, and found that the relationships between the stresses and the strain rates at the transition point are found to be bilinear. Doman D. A. et al. [15] performed the high-rate, uniaxial compression tests using a Polymeric SHPB, and studied the effectiveness of both the modified quasi-linear viscoelastic model and the non-linear hyper-viscoelastic model to describe the low-rate and high-rate behavior of polyurethane rubber. Zhu Zhaoxiang et al. [16] proposed the ZWT nonlinear viscoelastic constitutive model, and then analyzed the strain rate effect and the time-temperature equivalence relation on mechanical properties of epoxy resin. Zhou Haixia et al. [17] performed the low, intermediate and high strain rate compressive testing and employed ZWT model to study the compressive mechanical behaviors of the propellant. It was proved that four Maxwell elements at least in the model should be required to accurately describe rate-dependent mechanical properties. By applying characteristics method of wave propagation, Zhu Jue et al. [18] numerically studied the SHPB tests for the so-called ZWT viscoelastic materials to explore how the basic assumption of uniform distribution of stress can be satisfied. L. M. Yang et al. [19] presented a visco-hyperelastic constitutive model to analyze the large-deformation response of incompressible rubber under high strain rates, which should characterize the static hyperelastic behavior, rate-sensitivity and strain history dependence. By replace Rivlin function with Yeoh function in the constitutive model, Zhou Xiangrong et al. [20] proposed a new nonlinear constitutive based on Yeoh strain energy function to describe intermediate and high strain rate effects of rubber.
Studies have shown that viscoelastic damping material has not only the elastic and viscous coexisting characters, but also the obvious historical dependence. The integer order model has many parameters and unclear physical meaning, which could not reflect the historical correlation of materials. Other studies have been proved that four integer Maxwell elements at least with many unclear physical meaning parameters are required to accurately describe the rate-dependent mechanical properties of viscoelastic materials. However, the fractional calculus could well represent the historical correlation of the system due to its global definition [21]. The fractional model has fewer parameters and clear physical meaning, which has been proved a powerful model to simulate the dynamic properties of viscoelastic damping material.
In conclusion, yet few of researches have investigated the shock behavior of viscoelastic materials with the fractional constitutive model. In this paper, the fractional Maxwell model (FMM) is presented based on the fractional constitutive model and the typical Maxwell model. The compressive experiments can be conducted on the aluminum SHPB system to verify the adopted model. Besides, the experimental stress-strain curves of materials are explained based on the damping dissipation mechanism. Afterwards, a set of model parameters are obtained by the least-squares fitting algorithm. Finally, the comparison is made between FMM model and the other models including the fractional Kelvin-Voight model, ZWT model and Ogden model considering the strain rate-dependent.
2. Fractional Maxwell constitutive model
The viscoelastic oscillator (VEO) is the fundamental physical unit of viscoelastic damping structures. The VEO depicted in Fig. 1(a) consists of an isolated mass, viewed as m whose displacement is represented by x, a viscoelastic isolator with the specific geometric elements namely the area A and the height l, and the external excitation Fe. The viscoelastic isolator is installed on the rigid support.
The fractional constitutive equation including the strain ε and the stress σ for viscoelasticity takes the following form [22]:
where the fractional constitutive operators P and Q are respectively defined by:
where pi and qi are coefficients, Dαit and Dβit are fractional derivative operators whose Caputo definitions are respectively defined by:
where αi, βi are the fractional orders, n=[αi], [βi], n-1<αi, βi≤n.
The FMM model is employed to characterize the viscoelastic stress-strain relationship, which consists of the fractional dashpot 〈c,α,β〉 in series with the ideal Hooke spring element k, shown in Fig. 1(b). Compared with the original Maxwell model, the integer order sticky strain element is replaced by the fractional dashpot in the FMM model. According to the FMM model, the relations σe=σe=σf, ε=εe+εf are established, where σe, εe are the stress and strain of the spring element, and σf, εf are the stress and strain of the fractional dashpot, respectively. Based on the above models, the VEO concluding FMM shown in Fig. 1(c) is built. The comprehensive function of the viscoelastic isolator counts as a fractional damping force Fd. Herein, Fd=σA=σeA=σfA. In the FMM model, the parameters of viscoelasticity are as follows. n=1, p0=1, p1=c/k, β0=0, β1=β, m=1, q0=0, q1=c, α1=α. Therefore, the fractional Maxwell constitutive equation including the strain ε and the stress σ for viscoelasticity is derived:
Fig. 1VEO and FMM models
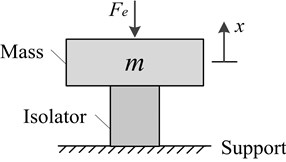
a) Physical model of VEO
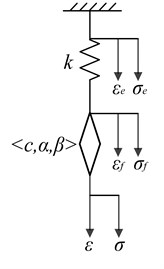
b) FMM model
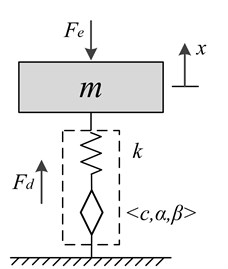
c) VEO concluding FMM
3. SHPB experiment
3.1. Experimental scheme
As an essential experiment of the shock dynamic properties, the compression experiment could undergo large deformation without necking, which is different from the conventional quasi-static tensile experiment. Using the wave propagation principle, the experiment in this paper is conducted on the aluminum alloy separated Hopkinson pressure bar (SHPB) with low impedance. The SHPB system is mainly composed of the striker bar, the incident bar and the transmission bar with the same diameters of 14.5 mm, mass density 2.8×103 kg/m3, Young’s modulus 72 GPa and longitudinal wave velocity 4982 m/s, and the different lengths (0.60 m, 2.00 m and 2.00 m, respectively). The specimen is located between the incident and transmission bars. By the gas from the air gun, the strike bar is propelled forward against the incident bar, generating compression stress waves. When the waves are transmitted to the specimen, a part of the waves is reflected as tensile wave back to the incident bar, while the other portion is transmitted to the transmission bar. The above pulse signals are recorded by the strain gauges located on the incident bar and the transmission bar respectively. The real photos and the schematic of the SHPB test machine are shown in Figs. 2-3, respectively.
Based on the one-dimensional stress wave assumption, the strain rate, strain and stress could be calculated by:
where εi(t), εr(t) and εt(t) are the incident, reflected and transmitted strain propagating within Hopkinson pressure bars, respectively. The parameters A0, E0, and c0 are the cross-sectional area, the Young’s modulus and the elastic wave velocity of the bars. The parameters As and Ls are the cross-section area and the thickness of the specimen.
Fig. 2The photos of the SHPB test system
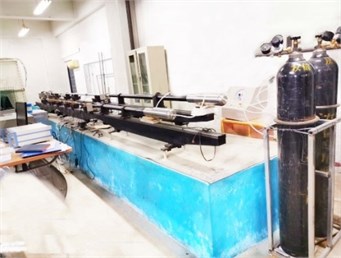
a) SHPB experimental facilities
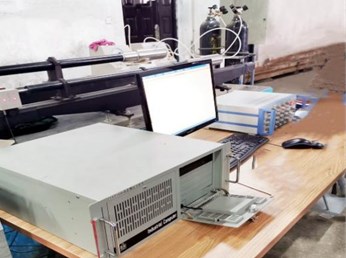
b) Data processing devices
Fig. 3The schematic of the SHPB test system
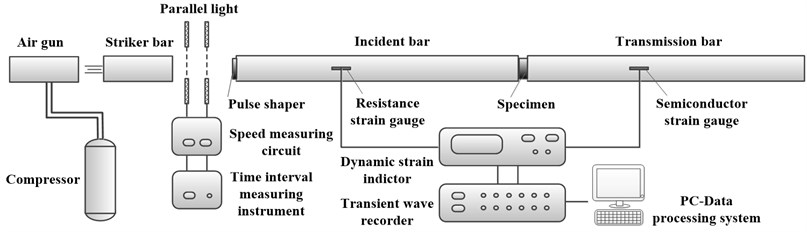
The natural rubber with hardness 70 HS is chosen as the experimental material. Considering viscoelastic damping material with low impedance and low wave velocity, the specimen of small thickness is chosen in order to shorten the time of stress wave propagation and achieve the stress equilibrium. On the other hand, the optimal length-diameter ratio of the specimen is h/r=√3/2 [23]. Thus, the specimen is designed to be a short cylindrical with 6.5 mm in diameter and 2 mm in length. To reduce the influence of the interfacial friction between the specimen and the bar ends, a thin layer of petroleum jelly are used to lubricate the two contact surfaces of the specimen. The incident bar is instrumented with the resistor strain gauges of sensitivity coefficient 2.1±1 %, while the semiconductor strain gauges of sensitivity coefficient 110±5 % are associated on the transmission bar for capturing the weak transmitted pulse.
During the SHPB experiment, it is vital to obtain the dynamic stress equilibrium and constant strain rate. In the traditional SHPB experiment of soft materials, the above conditions are difficult to be guaranteed, so that the experimental results cannot truly reflect the material properties. To achieve desired experimental results, the most widely applied approach is the technique of placing pulse shapers between the strike bar and the incident bar. The reason is that the plastic deformation of the shapers during the loading process could change the shape of pulse. Some achievements about pulse shapers have been made based on the dynamic experiments of the soft material. To study rubber materials, Pang Baojun et al. [24] used a lead block with a side 3 mm to adjust the pulse. Chen [25] employed the polymer wafer as the incident-pulse shaper to test the dynamic compressive response of polymeric nanocomposites. Chang Xinlong [26] studied the constitutive model for HTPB propellant using the rubber wafer as the pulse shaper. Lu Fangyun [27] performed the SHPB experiments of silicone rubber and foam materials by applying the combination pulse shaper of a main shaper, a very small copper shaper and even a smaller silicone rubber shaper. Wang Baozhen [28] studied the constitutive model of porcine liver by means of the shaping technique of multi-layer medical plaster. In this paper, considering viscoelastic materials with low stiffness, the multi-layer adhesive plaster of 1 mm thickness is employed to shape the incident pulse. The comparison between strain curves before and after the shaping technology is illustrated in Fig. 4. It should be seen that the shaper of multi-layer adhesive plaster could eliminate the high frequency shock introduced by the dispersion effect, and thus help the specimen to early achieve and maintain the uniform stress and constant strain rate.
To study the shock response of viscoelastic damping material, SHPB experiments are conducted for four different strain rates (1800 s-1, 2500 s-1, 3500 s-1 and 4000 s-1). The experimental stress-strain curves are presented in Fig. 5.
Fig. 4The comparison between strain curves before and after the shaping technology
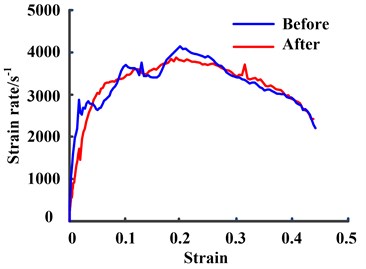
Fig. 5The experimental stress-strain curves of viscoelastic damping material
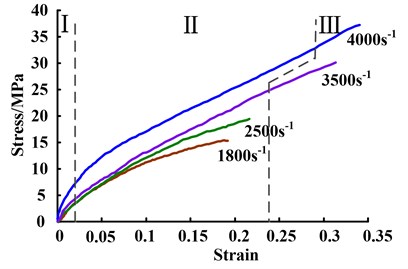
3.2. Result and discussion
The stress-strain curves of viscoelastic damping material at high strain rates are non-linear related, shown in Fig. 5. The curves could be divided into three stages: the linear stage, the strain-softening stage and the strain-hardening stage, as shown the region I, II, and III in Fig. 5, respectively. This is similar to the typical three-stage process of the quasi-static stress-strain curve. At the linear stage, the initial strain mainly induced by the deformation of molecule chains is the recoverable elastic deformation. The elasticity modulus is equal to the linear slope. Compared to the quasi-static mechanical, the linear phase at high strain rates lasts a shorter time. At the strain-softening stage, the stress-strain relationship exhibits apparent delay. This is because that the slip motion and the friction between molecular chains are thermal irreversible, which explains the viscosity of viscoelastic damping material providing damping effect. Besides, the internal temperature rise occurs with the increase of strain, further leading to a gradual decrease in the tangent slop of the stress-strain curve. At the strain-hardening stage, the curve has linear segment. Compared to the strain-softening stage, its slope in this stage is steeper. The strain-hardening effect can be interpreted by the strengthening of molecular entanglement and molecular chains orientation, i.e. orientation hardening.
As can be seen from Fig. 5, both the peak stress and peak strain go up with the increase of the strain rate. At the high strain rates, the action time of the external loading is far more than the relaxation time of the molecular chain segment, so that the relaxation of molecular chain segment cannot keep up with the compression of the molecular chain. This explains why the stress values at the same strains are greater with the increase of the strain rate. By comparing the results at strain rate 4000 s-1 and strain rate 1800 s-1, when the strains are 0.05, 0.10, and 0.15, the stresses increase by 75.3 %, 52.3 %, and 54.6 %, respectively. In the strain-softening stage, the higher the strain rate is, the more the heat dissipation during sliding friction is. Additionally, considering viscoelastic damping material at high strain rates in the adiabatic approximation, the temperature of the material becomes higher. As a result, the curvature in strain-softening stage tends to larger with the increase of strain rate. In the strain-hardening stage, the molecular entanglement is stronger with the increase of the strain rate, inducing the worse segmental dynamic and the greater hardening effect. The energy-absorption capability is determined by the area under the stress-strain curves [29]. The deformation of molecule chains and the slip motion between molecular chains are enhanced when strain rate is increased. Therefore, the energy-absorption capability increases with the increasing of strain rate. According to the above analysis of the stress-strain curves, viscoelastic damping material represents rate-dependent behavior at high strain rates.
4. Comparison study
The parameters of FMM are obtained by least-squares fitting against the SHPB experiment data as c=2.7×106 N·s/mm, k= 4.5×107 N/mm, β=0.101, α=0.381, 0.384, 0.387, 0.395, corresponding strain rate 1800 s-1, 2500 s-1, 3500 s-1and 4000 s-1, respectively. The mechanical behavior of viscoelastic damping material under different strain rates could be embodied by the fractional order of the FMM model, which could not be reflected by the classical viscoelastic model. For purpose of comparing study, the fractional Kelvin-Voight model (FKVM), ZWT model and Ogden model considering the strain rate-dependent are also applied to predict the shock stress-strain curves of viscoelastic damping material by SHPB.
The constitutive equation of FKVM model [30] is:
where, q0=k, q1=c are material parameters.
The constitutive equation of ZWT [16] model is:
where, C0, α, β are the elastic constants of nonlinear elements, C1, θ1 and C2, θ2 are elastic constants and relaxation times of the two Maxwell elements, respectively.
Considering the influence of the strain rate, the engineering stress of Ogden model for rubber materials under uniaxial compression condition is expressed as [31]:
where, λ1 is the principal stretch, λ1=1-ε and ˙λ1=˙ε. αj, μj, and Gi, βi are material parameters.
The fitting results are shown in Fig. 6. The root mean square error (RMSE) is also implemented to measure the fitting quality between the experimental data and theoretical models. The definition of RMSE is:
where, yt, ye are the experimental data and the theoretical value, respectively. The RMSE of the different model-fitting data at each strain rate is represented in Table 1.
Fig. 6The comparisons between predicted models and experimental data at different strain rates
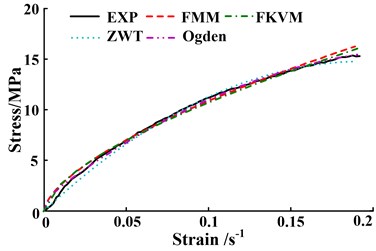
a) Strain rate 1800 s-1

b) Strain rate 2500 s-1
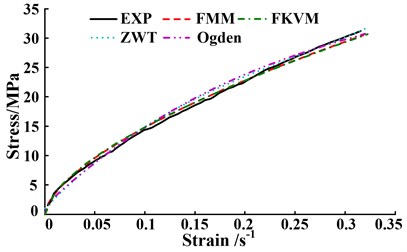
c) Strain rate 3500 s-1
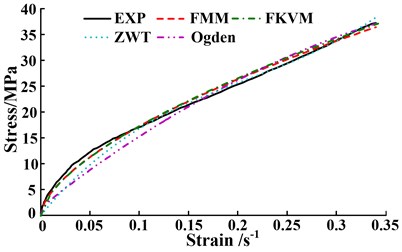
d) Strain rate 4000 s-1
Table 1The RMSE of different model-fitting data
Strain rate / s-1 | FMM | FKVM | ZWT | Ogden |
1800 | 0.380 | 0.480 | 0.370 | 0.313 |
2500 | 0.273 | 0.639 | 0.259 | 0.216 |
3500 | 0.498 | 0.575 | 1.024 | 1.173 |
4000 | 0.690 | 0.618 | 1.395 | 2.600 |
The comparisons illustrated in Figs. 6(a)-(b) and Table 1 show that at strain rates 1800 s-1 and 2500 s-1, the Ogden model has the highest fitting accuracy to experimental data, closely followed by the ZWT and FMM models, and the FKVM is the worst. The difference of the fitting accuracy between the FMM model and the Ogden model is very small, and the RMSE differences between them are 0.067 and 0.057, respectively. The RMSE differences between the FKVM model and the Ogden model are 0.167 and 0.423, respectively. Additionally, the high-precision fitting of the Ogden and ZWT models at strain rates 1800 s-1and 2500 s-1 may be built on the complex fitting of multiple parameters with ambiguous physical meaning. The fitting of the parameters also require longer convergence time. There are two relaxation times varying within their range in the ZWT model, which increase the flexibility and uncertainty of fitting process.
At strain rates 3500 s-1and 4000 s-1, the FMM and FKVM models perform much better agreement with experimental data than the ZWT and Ogden models, shown in Figs. 6(c)-(d) and Table 1. Especially at strain rate 4000 s-1, the ZWT and Ogden models significantly deviate from experimental values in small strain region, of whose RMSEs are larger one order than that of FMM model.
The mean of RMSE for above models is 0.460, 0.578, 0.762 and 1.076, respectively. As a fractional-order model, FMM model has the minimum mean of RMSE among the four models. Besides, the FMM model just has four parameters. More importantly, the fractional orders of the FMM model could reflect the elastic and viscous distribution of materials under different strain rates. The FMM model has a better comprehensive superiority in the characterization of viscoelastic shock mechanical behavior. The superiority is embodied at higher fitting precision, fewer parameters and clear physical meaning.
5. Conclusions
In this study, the FMM model is presented for the shock response of viscoelastic damping material. The dynamic experiments for four strain rates (1800 s-1, 2500 s-1, 3500 s-1 and 4000 s-1) are performed by SHPB system to examine the proposed model. Meanwhile, the models of FMM, fractional Kelvin-Voight, ZWT and Ogden considering the strain rate-dependent are comparatively studied with the experiment. The conclusions could be summarized as follows.
1) The stress-strain curves at high strain rates should be divided into three stages, i.e. the linear stage, the strain-softening stage and the strain-hardening stage. The strain rate effect could be observed. With the strain rate increasing, the peak strain, the peak stress and the curvature of the curve in strain-softening stage increase, and the hardening effect in the strain-hardening stage presents increasing tendency. It is because the action time of external loading gets closer to the relaxation time of the molecular chain segment with increase of the strain rate, thus leading to the apparent strain rate-dependence of molecular slip and friction.
2) At strain rates 1800 s-1and 2500 s-1, the Ogden model has the highest fitting accuracy to experimental data. The difference of the fitting accuracy between the FMM model and the Ogden model is very small, and the RMSE differences between them are 0.067 and 0.057, respectively. At strain rates 3500 s-1and 4000 s-1, the FMM and FKVM models perform much better agreement with experimental data than ZWT and Ogden models. Additionally, as a fractional-order model, FMM model has the minimum mean of RMSE 0.460 among the four models.
3) In general, the FMM model has a comprehensive superiority of higher fitting precision, fewer parameters and clear physical meaning to describe the shock mechanical behavior characteristics of viscoelastic materials in a wider range of strain rate.
References
-
Lee J. H., Kim K. J. Characterization of complex modulus of viscoelastic materials subject to static compression. Mechanics of Time-Dependent Materials, Vol. 5, Issue 3, 2001, p. 255-271.
-
Pan Y., Zhong Z. A viscoelastic constitutive modeling of rubber-like materials with the Payne effect. Applied Mathematical Modelling, Vol. 50, 2017, p. 621-632.
-
Xu Mingyu, Tan Wenchang Representation of the constitutive equation of viscoelastic materials by the generalized fractional element networks and its generalized solutions. Science in China, Vol. 46, Issue 2, 2003, p. 145-157.
-
Muliana A., Rajagopal K., Tscharnuter D., et al. A nonlinear viscoelastic constitutive model of polymeric solids based on multiple natural configuration theory. International Journal of Solids and Structures, Vols. 100-101, Issues 1, 2016, p. 95-110.
-
Long J. M., Xiao R., Chen W. Fractional viscoelastic models with non-singular kernels. Mechanics of Materials, Vol. 127, 2018, p. 55-64.
-
Ahmadian A., Ismail F., Salahshour S., Baleanu D., Ghaemi F. Uncertain viscoelastic models with fractional order: A new spectral tau method to study the numerical simulations of the solution. Communications in Nonlinear Science and Numerical Simulation, Vol. 53, 2017, p. 44-64.
-
Alotta G., Barrera O., Cocks A. C. F., Paola M. D. On the behavior of a three-dimensional fractional viscoelastic constitutive model. Meccanica, Vol. 52, 2017, p. 2127-2142.
-
Irausquín I., Pérez-Castellanos J. L., Miranda V., Teixeira-Diasc F. Evaluation of the effect of the strain rate on the compressive response of a closed-cell aluminium foam using the split Hopkinson pressure bar test. Materials and Design, Vol. 47, 2013, p. 698-705.
-
Li Qinghua, Zhao Xin, Xu Shilang, Gao Xiang Influence of steel fiber on dynamic compressive behavior of hybrid fiber ultra high toughness cementitious composites at different strain rates. Construction and Building Materials, Vol. 125, 2016, p. 490-500.
-
Sharma A., Shukla A., Prosser R. A. Mechanical characterization of soft materials using high speed photography and split Hopkinson pressure bar technique. Journal of Materials Science, Vol. 37, Issue 5, 2002, p. 1005-1017.
-
Hu Shisheng, Wang Lili, Song Li, Zhang Lei Review of the development of Hopkinson pressure bar technique in China. Explosion and Shock Waves, Vol. 34, Issue 6, 2014, p. 4-20.
-
Meenken T., Hiermaier S. Large strain dynamic compression for soft materials using a direct impact experiment. Journal De Physique IV, Vol. 134, 2006, p. 653-659.
-
Zhao XiJin, Lu FangYun, Lin Yuliang Research on dynamic compressive testing and mechanical properties of silicon rubber. Chinese Journal of High Pressure Physics, Vol. 18, Issue 4, 2004, p. 41-45.
-
Lee O. S., Kim M. S., Kim K. J., et al. Dynamic deformation behavior of rubber under high strain rate compressive loading. International Journal of Modern Physics B, Vol. 17, Issues 8-9, 2008, p. 1415-1420.
-
Doman D. A., Cronin D. S., Salisbury C. P. Characterization of polyurethane rubber at high deformation rates. Experimental Mechanics, Vol. 46, Issue 3, 2006, p. 367-376.
-
Zhu Zhao-xiang, Xu Da-ben, Wang Li-li Thermoviscoelastic constitutive equation and time-temperature equivalence of epoxy resin at high strain rates. Journal of Ningbo University, Vol. 1, Issue 1, 1988, p. 58-68.
-
Zhou Haixia, Li Shipeng, Xie Kan, Sui Xin, Yang Long Research on the viscoelastic constitutive model of HTPB propellant over a wide range of strain rates. Journal of Solid Rocket Technology, Vol. 40, Issue 3, 2017, p. 325-396.
-
Zhu Jue, Hu Shisheng, Wang Lili Analysis on stress uniformity of viscoelastic materials in split Hopkinson bar tests. Explosion and Shock Waves, Vol. 26, Issue 4, 2006, p. 29-36.
-
Yang L.W., Shim V. PW., Lim C. T. A visco-hyperlastic approach to modeling the constitutive behavior of rubber. International Journal of Impact Engineering, Vol. 24, 2000, p. 545-560.
-
Zhou Xiangrong, Wang Qiang, Wang Baozhen A nonlinear visco-hyperelastic constitutive model based on Yeoh strain energy function with its application to impact simulation. Journal of Vibration and Shock, Vol. 26, Issue 5, 2007, p. 33-37+151.
-
Huimin Zhao, Haodong Liu, Junjie Xu, Wu Deng Performance prediction using high-order differential mathematical morphology gradient spectrum entropy and extreme learning machine. IEEE Transactions on Instrumentation and Measurement, Vol. 68, Issue 10, 2019, p. 1-8.
-
Li Zhanlong, Liu Zhiqi, Sun Dagang, Yan Bijuan, Meng Jie Fractional Maxwell model of viscoelastic oscillator and its frequency response. Journal of Vibration Engineering and Technologies, Vol. 6, Issue 1, 2018, p. 1-6.
-
Davies E. D. H., Hunter S. C. The dynamic compression testing of solids by the method of the split Hopkinson pressure bar. Journal of the Mechanics and Physics of Solids, Vol. 11, Issue 3, 1963, p. 155-179.
-
Pang Baojun, Yang Zhenqi, Wang Liwen, Chi Runqiang Dynamic compression properties and constitutive model with strain rate effect of rubber material. Chinese Journal of High Pressure Physics, Vol. 25, Issue 5, 2011, p. 407-415.
-
Chen W., Song B. Dynamic compressive response of polymeric nanocomposites. ICCCES, Vol. 3, Issue 1, 2007, p. 51-55.
-
Chang Xinlong, Lai Jianwei, Zhang Xiaojun, Hu Kuan, Qi Wei High strain-rate viscoelastic constitutive model for HTPB propellant. Journal of Propulsion Technology, Vol. 35, Issue 1, 2014, p. 123-127.
-
Lu Fang-Yun, Chen W., Frew D. J. A design of SHPB experiments for soft materials. Explosion and Shock Waves, Vol. 22, Issue 1, 2002, p. 15-19.
-
Wang Baozhen, Hu Shisheng Research on dynamic mechanical response and constitutive model of procine liver. Chinese Journal of Theoretical and Applied Mechanics, Vol. 49, Issue 6, 2017, p. 1399-1408.
-
Xiao L. J., Song W. D., Wang C., Liu H. Y., Tang H. P., Wang J. Z. Mechanical behavior of open-cell rhombic dodecahedron Ti-6Al-4V lattice structure. Materials Science and Engineering A, Vol. 640, 2015, p. 375-384.
-
Li Z. L., Qin, Sun, Jia B. C. L., Zhang W. J., Yan B. J., Shi Q. L. A fractional approach to the time-temperature dependence of dynamic viscoelastic behavior. Journal of Mechanical Science and Technology, Vol. 33, Issue 1, 2019, p. 139-147.
-
Lin Yuliang, Lu Fangyun, Lu Li Constitutive behaviors of a silicone rubber at high strain rates. Chinese Journal of High Pressure Physics, Vol. 21, Issue 3, 2007, p. 289-294.
About this article
This work was supported by the National Natural Science Foundation of China (Grant No. 51805347), Project funded by China Postdoctoral Science Foundation (Grant No. 2019M661058), STIP (Grant No. 2019L0635, 201802086). Natural Science Foundation of Shanxi Province, China (Grant No. 201801D121168).