Abstract
Research on knocking combustion is vitally essential since it impacts engine performance regarding noise and emissions, fuel consumption, power density, and durability. Because of end-gas auto-ignition, current SI engines may experience conventional knock, which restricts increasing the compression ratio to increase thermal efficiency. Therefore, this paper examined the in-cylinder pressure and vibration of a port fuel-injected gasoline engine under knocking and non-knocking conditions. The heat release rate was calculated from pressure traces where the crank angle resolutions were not constant, and the conversion from the time domain to the frequency domain of knock sensor signals by using the Fourier Transform was performed. The result reveals that more heat is released during knocking combustion than during non-knocking combustion. When there is a knock, the temperature variation increases. This would facilitate the use of heat transfer studies to detect knock occurrences. Moreover, knocking is caused by an ignition timing that is too advanced, 22°BTC, compared to the non-knocking spark case, 14°BTC. In the frequency domain, the amplitude of the knocking combustion is higher than the amplitude of the non-knocking combustion, indicating the engine’s noise and vibration.
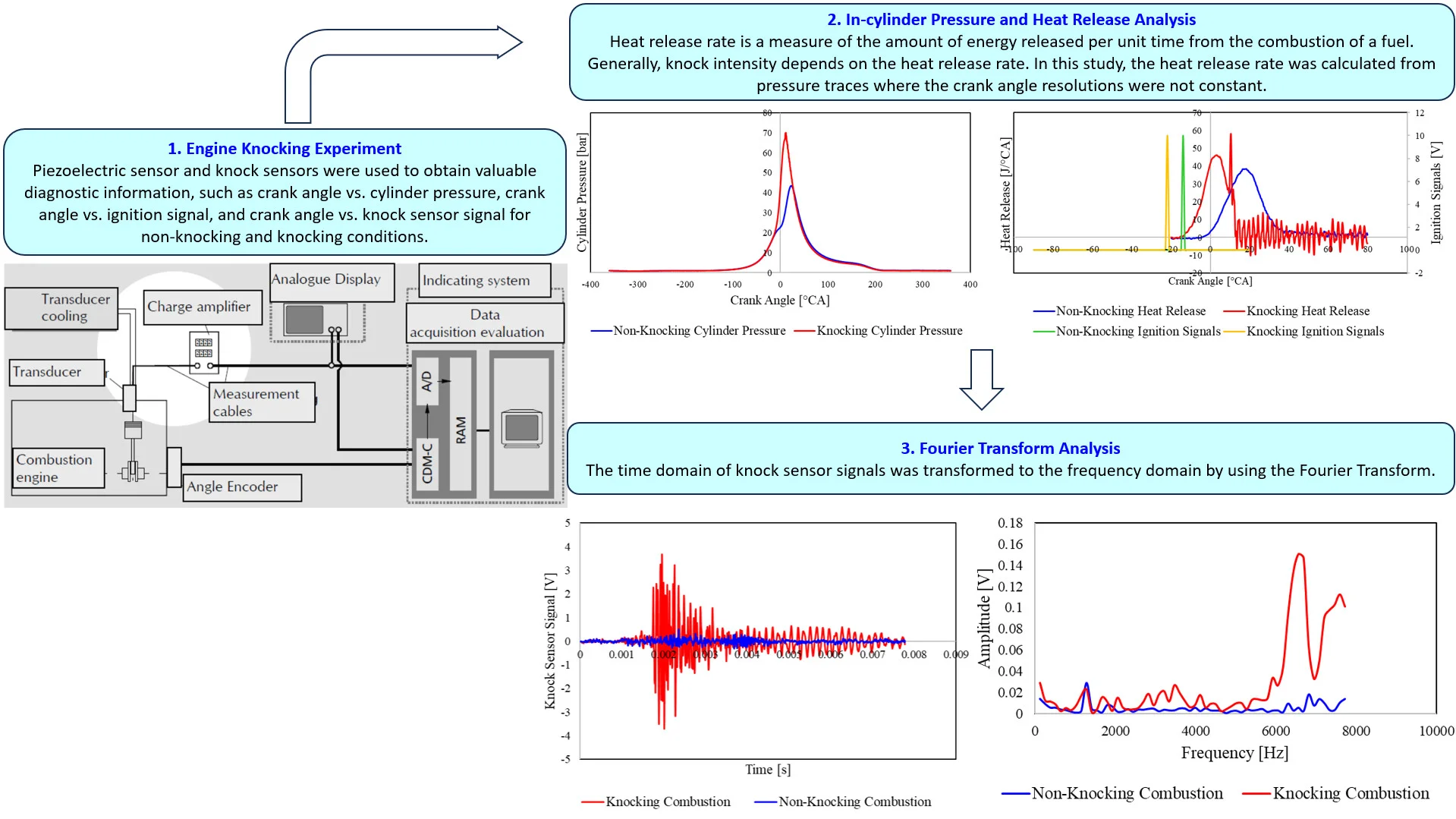
Highlights
- Engine Knocking Experiment: Piezoelectric sensor and knock sensors were used to obtain valuable diagnostic information, such as crank angle vs. cylinder pressure, crank angle vs. ignition signal, and crank angle vs. knock sensor signal for non-knocking and knocking conditions.
- In-cylinder Pressure and Heat Release Analysis: Heat release rate is a measure of the amount of energy released per unit time from the combustion of a fuel. Generally, knock intensity depends on the heat release rate. In this study, the heat release rate was calculated from pressure traces where the crank angle resolutions were not constant.
- Fourier Transform Analysis: The time domain of knock sensor signals was transformed to the frequency domain by using the Fourier Transform.
1. Introduction
Currently, more than one billion vehicles are in the world, and more than 60 % are equipped with gasoline spark ignition engines. Compared with diesel engines, gasoline engines can meet stringent emission regulations and have more significant potential for further improvement in engine efficiency. However, the primary obstacle to enhancing thermal efficiency in an SI engine is its tendency to knock, which keeps engines from reaching optimal combustion and increased compression ratios. Therefore, knock occurring in high-efficiency engines must be well understood to meet future fuel economy and emission regulations [1].
Generally, there are two forms of abnormal combustion. The first is a detonative combustion known as “knock”, and the second is autoignition. Considering the functionality of a combustion engine, both of these combustion malfunctions are very serious due to the possibility of engine damage or causing higher noise levels in better cases [2]. Knock is the name given to the noise associated with auto-ignition, a portion of the fuel-air mixture ahead of the propagating flame front [3]. The knock phenomenon is caused by the combustion chamber’s auto-ignition of air and fuel mixture due to the increased local temperature and pressure [4]. It is an inherent problem that plagues internal combustion engines and has been studied intensively for decades. Knock is widely recognized as a major barrier to the ongoing enhancement of the thermal efficiency of SI engines and the lifetimes of internal combustion engines. Long-term knocking can have several detrimental effects, including cylinder head erosion, piston melting, engine compression ratio limitations, increased air pollution, decreased engine efficiency, a significant increase in engine-specific fuel consumption, and the potential for structural damage to the engine [5].
Spark knock is an engine combustion problem caused by the spark plug firing too soon in relation to the position of the piston. Over-advanced ignition timing causes combustion pressure to slam into the upward-moving piston. This yields maximum cylinder pressure before TDC. Spark knock, and preignition produce about the same symptoms [6].
Fig. 1Crank-angle vs. cylinder pressure traces for individual cycles [3]
![Crank-angle vs. cylinder pressure traces for individual cycles [3]](https://static-01.extrica.com/articles/23960/23960-img1.jpg)
a) Normal combustion, spark 28°BTC
![Crank-angle vs. cylinder pressure traces for individual cycles [3]](https://static-01.extrica.com/articles/23960/23960-img2.jpg)
b) Slight knock, spark 28°BTC
![Crank-angle vs. cylinder pressure traces for individual cycles [3]](https://static-01.extrica.com/articles/23960/23960-img3.jpg)
c) Intense knock, spark 32°BTC
The cylinder pressure variation is depicted in Fig. 1 for three different engine cycles: normal combustion, slight knock, and intense knock. The advanced ignition timing and operating conditions of Fig. 1(a) and (b) are identical. In this engine, normal smooth cylinder pressure recordings were found in about one-third of the cycles under these conditions, as indicated in Fig. 1(a). With a slight knock, knock occurs late in the burning process, at close to the peak pressure, and the amplitude of the pressure fluctuations is small as shown in Fig. 1(b). The peak pressure is higher and earlier than that in normal combustion. This is a faster-burning cycle. With an intense knock, as shown in Fig. 1(c), knock happens closer to the top center earlier in the combustion process, and the initial amplitude of the pressure fluctuation is much higher. These pressure fluctuations produce knocks due to the essentially spontaneous release of the chemical energy of the end-gas fuel. This produces a substantial local gas pressure and temperature increase, thereby causing a strong pressure wave to propagate away from the end-gas region across the combustion chamber. This strong pressure wave, the expansion wave accompanying it, and the reflection of these waves by the chamber walls create oscillatory pressure [3].
It was reported that because of the intricacy of the phenomena involved, the combustion mechanisms linked to knock are not entirely understood [7]. Therefore, developing a prediction method for investigating knock sources would be crucial. The reasons behind engine knocks have been the subject of some experimental investigations. The complexity of knock prediction presents a challenge to researchers [5]. Corti and Forte studied statistical analysis of indicating parameters for knock detection using an in-cylinder pressure sensor signal [8]. Shi et al. studied the effects of multiple spark ignition on engine knock under different compression ratios and fuel octane number conditions. It was found that multiple-spark ignition generates higher power output and lower cycle-to-cycle variations [9]. Since accurate heat release analyses are rather complex and time-consuming, directly utilizing the in-cylinder pressure is often the preferred option to obtain fast, although approximate, results with the possibility of real-time calculation [10]. The net heat release should decrease, and the heat losses will increase when knocking occurs. This method looks at the burning rate as a measure of the combustion characteristics. Using the first law of thermodynamics, the heat release rate is typically calculated using the in-cylinder pressure signal as a basis [5]. The fundamental components of vibrating frequencies can be obtained by transferring the pressure signal from the time domain to the frequency domain by the application of Fourier transform analysis [11]. According to the above literature, the study of engine knock and vibration remains limited. Therefore, this study investigated the effect of knock on in-cylinder pressure and vibration analysis on port fuel injection gasoline engine. It aims to investigate the non-knocking and knocking cycles where the heat release rate was calculated from pressure traces where the crank angle resolutions were not constant. In addition, the conversion from the time domain to the frequency domain of knock sensor signals by using the Fourier transform was performed to compare the non-knocking and knocking cycles. This study is significant for optimizing ignition timing to eliminate knock and enhance engine efficiency.
2. Methodology
2.1. Experimental procedure
To observe the knocking phenomenon, the engine knocking experiment was conducted with a 1.5-liter, four-cylinder MPI engine. The engine specification is indicated in Table 1. Spark plugs were used to initiate sparks at varying ignition timing, thus causing non-knocking and knocking phenomena inside the combustion chamber. Various sensors were used to obtain valuable diagnostic information, such as crank angle vs. cylinder pressure, crank angle vs. ignition signal, and crank angle vs. knock sensor signal for non-knocking and knocking conditions. In-cylinder pressure is used to evaluate cycle-to-cycle variation, thus indicating the tendency to knock phenomena. Then, heat release was calculated by using Eqs. (1) to (2) with instantaneous cylinder volume calculation, integral of heat release, and moving average filter. The time domain to frequency domain of knock sensor signals was performed by using the Fourier Transform as expressed in Eqs. (3). Knocking and non-knocking cycles were compared. Finally, the results and discussions, and conclusion were drawn.
Table 1Engine specifications and parameters
Parameters | Symbol | Value | Unit |
For port fuel injected gasoline engine, ratio of specific heats | κ | 1.32 | [–] |
Engine speed | n | 3000 | [1/min] |
Stroke | Z | 85.9 | [mm] |
Conrod length | l | 140 | [mm] |
Bore | D | 74.5 | [mm] |
Compression ratio | ε | 10.85 | [–] |
Fig. 2 shows the piezoelectric pressure measurement system, which consists of the piezoelectric pressure transducer, charge amplifier, measurement cabling, crank angle encoder, indicating equipment, pressure transducer cooling, and display. The piezoelectric sensor (KISTLER 6115CF-4DQ02) with sensitivity of 10.4 pC/bar was integrated in the engine cylinder to measure the in-cylinder pressure. The sampling rates were 1°CA, 0.1°CA, and 1°CA @ CAD range from –360°CA to –31°CA, –30°CA to 89.9°CA, and 90°CA to 359°CA, respectively. The piezoelectric sensor for knocking was used to detect knocking from the engine. Two knock sensors (part number: 030.905.377.D) were used at the same time – the first for ECU and the second one for knock measurement. The sampling rate of knock sensor was 0.05°CA @ CAD range from –20°CA to 120°CA.
Fig. 2Structural diagram of the piezoelectric pressure measurement system [12]
![Structural diagram of the piezoelectric pressure measurement system [12]](https://static-01.extrica.com/articles/23960/23960-img4.jpg)
2.2. Heat release analysis
Heat release rate is a measure of the amount of energy released per unit time from the combustion of a fuel. Generally, knock intensity depends on the heat release rate. In this study, the heat release rate was calculated from pressure traces where the crank angle resolutions were not constant. Rate of heat release can be described as follows [5]:
By integrating Eq. (1), the rate of heat release can be expressed as:
where φ denotes crank angle in [rad], κ denotes specific heat ratio, p denotes in-cylinder pressure [Pa], and V denotes cylinder volume in [m3].
2.3. Fourier transform analysis
The time domain was transformed to the frequency domain of knock sensor signals by using the Fourier Transform. Fourier transform calculation can be performed as follows [11]:
∆α=αfinal-αinitial(indegree),
¯pm=12π∫2π0pmd(ωt),Ai=1π∫2π0pmcos(iωt)d(ωt),
Bi=1π∫2π0pmsin(iωt)d(ωt),Ci=√A2i+B2i,fi=iω2π,i=1,2…,60,
where pm is measured signal [V], ¯pm is mean of measured signal [V], Ai is coefficient of real number, Bi is coefficient of imaginary number, Ci is amplitude [V], ω is rotational speed [rad/s], fi is frequency [Hz], and n is engine speed in [rps] (revolutions per second).
3. Results and discussions
Fig. 3 shows in-cylinder pressure under non-knocking and knocking combustion. It can be observed that there is a significant pressure difference when a knock occurs. Under knocking combustion, the peak pressure is higher and earlier than normal combustion. This is caused by over-ignition timing 22°BTC, which causes a high heat release rate and eventually leads to high pressure around 69.9 bar. Under normal ignition timing, the in-cylinder pressure is around 43.5 bar, which is the normal case of gasoline combustion.
Fig. 4 illustrates the heat release and ignition signals versus crank angle with and without knock. It is obvious that the ignition timing determines the knock and the heat release rate. Knock is caused by too advanced ignition timing of 22°BTC at ignition signal 10 V, while the non-knocking ignition timing is 14°BTC at ignition signal 10 V. Compared to non-knocking combustion, knocking combustion releases more heat. This will cause high-temperature variations and support the use of heat transfer analysis for knock detection. High-frequency pressure variations are seen during knocking, and their magnitude decays with time. It shall be noted that the pressure distribution within the combustion chamber is no longer consistent after a knock, and the wave propagation is damped out. Before the flame front arrives, the end-gas auto-ignition takes place, which results in an abnormal rise in heat release rates and ultimately deviates from the normal combustion process. In non-knocking cycles, the flame front ignites the air/fuel mixture, causing weak pressure vibrations, and the heat release rate increases gradually to peak values before decreasing once the entire mixture is consumed. As a result, the flame propagates smoothly.
Fig. 3In-cylinder pressure under non-knocking and knocking combustion
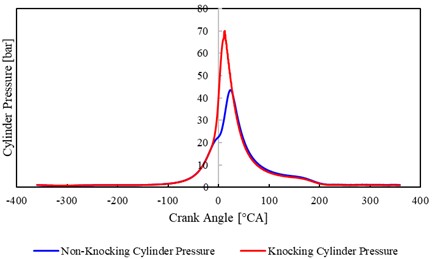
Fig. 4Heat release and ignition signals versus crank angle with non-knocking combustion, spark 14°BTC and knocking combustion, spark 22°BTC
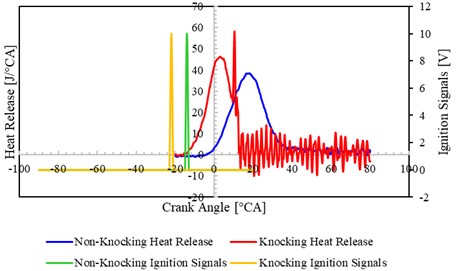
Fig. 5a) Time domain of knock sensor signals under non-knocking and knocking cycle, b) frequency domain of knock sensor signals under non-knocking and knocking cycle
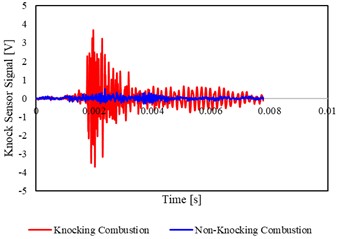
a)
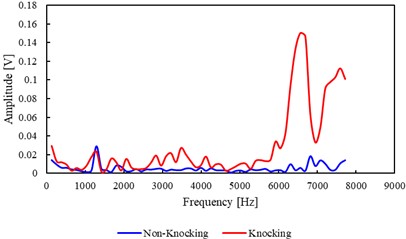
b)
Time domains of non-knocking and knocking combustion were converted to frequency domains using the Fourier transform, as shown in Fig. 5. In the non-knocking cycle, the frequency is 1285.7142 Hz with maximum amplitude 0.02922 V while knocking cycle with the frequency 6557.1428 Hz and maximum amplitude 0.1503 V. It can be observed that the amplitude of the knocking combustion is higher than the amplitude of the non-knocking combustion indicating the noise and vibration of engine. This determines the occurrence of knock by measuring the vibration level of the engine. When a knock happens, the combustion chamber will experience large pressure waves. In addition to causing engine block vibrations and the audible knock signal, pressure waves can directly radiate sound within the audible frequency range.
4. Conclusions
Knock is an undesirable combustion phenomenon leading to engine damage and power loss. Knock occurs when the compression stroke generates too high in-cylinder pressure near TDC. Over-advanced ignition timing is prone to knocking. Ignition timing that is advanced too far causes combustion pressure to slam into the upward-moving piston, producing maximum cylinder pressure before TDC. In engine design, this phenomenon can be eliminated by retarding ignition timing. The engine noise and vibration can be seen in that the knocking combustion has a higher amplitude than the non-knocking combustion. In non-knocking cycles, the heat release rate increases steadily to peak values and then decreases after the whole mixture is consumed because the air/fuel mixture is ignited by the flame front, giving rise to weak pressure vibrations. When compared to non-knocking combustion, knocking combustion releases a lot more heat. This will increase temperature fluctuations and improve heat transfer analysis's ability to identify knock occurrences.
References
-
Z. Wang, H. Liu, and R. D. Reitz, “Knocking combustion in spark-ignition engines,” Progress in Energy and Combustion Science, Vol. 61, pp. 78–112, Jul. 2017, https://doi.org/10.1016/j.pecs.2017.03.004
-
K. Páv, “Abnormal Combustion Cases,” 2010.
-
John B. Heywood, Internal Combustion Engine Fundamentals. McGraw-Hill Education, 2018.
-
A. Moshrefi and M. Shalchian, “Improved knock detection method based on new time-frequency analysis in spark ignition turbocharged engine,” Automotive Science and Engineering, Vol. 8, No. 3, pp. 2759–2768, Sep. 2018, https://doi.org/10.22068/ijae.8.3.2759
-
X. Zhen et al., “The engine knock analysis – an overview,” Applied Energy, Vol. 92, pp. 628–636, Apr. 2012, https://doi.org/10.1016/j.apenergy.2011.11.079
-
J. E. Duffy, Modern Automotive Technology. The Goodheart-Willcox Company, 2017.
-
B. Radu, G. Martin, R. Chiriac, and N. Apostolescu, “On the knock characteristics of LPG in a Spark ignition engine,” in Powertrain and Fluid Systems Conference and Exhibition, pp. 2005–1, Oct. 2005, https://doi.org/10.4271/2005-01-3773
-
E. Corti and C. Forte, “Statistical analysis of indicating parameters for knock detection purposes,” in SAE World Congress and Exhibition, pp. 2009–1, Apr. 2009, https://doi.org/10.4271/2009-01-0237
-
H. Shi, Q. Tang, K. Uddeen, B. Johansson, J. Turner, and G. Magnotti, “Effects of multiple spark ignition on engine knock under different compression ratio and fuel octane number conditions,” Fuel, Vol. 310, p. 122471, Feb. 2022, https://doi.org/10.1016/j.fuel.2021.122471
-
S. D. ’Ambrosio, A. Ferrari, and L. Galleani, “In-cylinder pressure-based direct techniques and time frequency analysis for combustion diagnostics in IC engines,” Energy Conversion and Management, Vol. 99, pp. 299–312, Jul. 2015, https://doi.org/10.1016/j.enconman.2015.03.080
-
H. Shi, K. Uddeen, Y. An, Y. Pei, and B. Johansson, “Statistical study on engine knock oscillation and heat release using multiple spark plugs and pressure sensors,” Fuel, Vol. 297, p. 120746, Aug. 2021, https://doi.org/10.1016/j.fuel.2021.120746
-
R. Pischinger, “Engine Indicating,” Institute for Combustion Engines and Thermodynamics, University of Technology Graz, 2002.
About this article
The authors have not disclosed any funding.
The datasets generated during and/or analyzed during the current study are available from the corresponding author on reasonable request.
The authors declare that they have no conflict of interest.