Abstract
The measurement of bite force can be essential for assessing oral health and the functioning of the stomatognathic system. However, its use in dental offices is limited due to operational complexities and costs. This study focused on evaluating the mechanical strength of the user-friendly and low manufacturing cost load cell under development within LABBIO – Bioengineering Laboratory at UFMG, the gnathodynamometer, tailored for children. 3D modeling in SolidWorks and Finite Element Method (FEM) structural analysis were employed to ensure its ability to withstand the desired 1000 N load. Initially, the device did not meet the desired load, resulting in iterations to modify its geometry. After iterations including the replacement of the initial material with a more suitable alternative, removal of edges, and other adjustments, a final prototype meeting mechanical strength and functionality requirements was developed.
1. Introduction
The measurement of bite force, known as Occlusal Bite Force (OBF), is a dental inspection capable of assessing overall oral health conditions, checking the effectiveness of dental treatments, and diagnosing potential irregularities in the dental arch. OBF refers to the force applied between the upper and lower teeth during jaw elevation, resulting from the isometric contraction of the mandibular muscles [1], [2].
The OBF can be measured by positioning an appropriate transducer between a pair of teeth, and currently, there are patented and/or literature-described devices capable of reliably performing this operation. However, it is understood that their use in dental and public health settings is not yet widely adopted due to operational complexities, mobility limitations, and associated costs [3].
A project currently in development within LABBIO (Laboratory of Bioengineering at UFMG), encompasses the development of a load cell called gnathodynamometer, designed to be mechanically straightforward and simple to manufacture, employ low-cost materials and also be particularly suitable for measurements in children [3].
Alongside the work of Orlando Santiago Júnior, this thesis aimed to evaluate and propose enhancements to the base prototype of this ongoing project, in regards to its material and geometry.
2. Methodology
The methodology employed corresponded exclusively to the analysis of the mechanical behavior of the gnathodynamometer and referring to the model of the first prototype manufactured and experimentally evaluated, which mechanically failed under the applied test load.
The gnathodynamometer (Fig. 1) is manufactured in stainless steel 316, a non-toxic material that can withstand antiseptic procedures. The key components which characterize the load cell include a strain gauge located on the outside surface of the joint body, a clamp, and two detachable, interchangeable and articulated bite tips. Coupling between the bite tips and clamp is to be made using removable pins or bolts. The clamp, bite tips and pins are manufactured using the same material [3], [4].
Fig. 1Gnathodynamometer featuring bite tip rotation
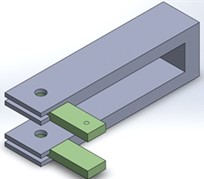
a) Bite tips facing sideways
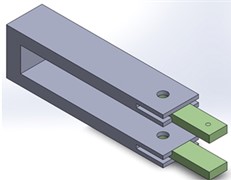
b) Bite tips facing forward
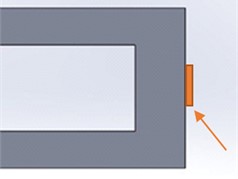
c) Strain gauge location
Any proposed changes were implemented in a manner that does not alter the fundamental characteristics that define the gnathodynamometer, as conceived in its patent [4].
The establishment of load parameters for the gnathodynamometer project was grounded in a review of scientific literature examining human bite force, leading to the identification of a suitable maximum load limit of 1000 N for the intended application of the device.
The structural analysis of the first prototype followed the established guidelines for the maximum load. The assessment employs the three-dimensional structural analysis software SolidWorks, where the prototype was digitally constructed and then subjected to static load simulation using the Finite Element Method (FEM) [5].
The testing force is applied on the exposed outside facing surface of each bite tip, allowing proper simulation of a bite with one of them acting as an anchor. Local simulations for the tips and attachment point allowed for free movement between components, where the anchor is now the surface originated from the cut of the clamp’s arm. Finite element meshing was automatically generated based on the model's geometry and curvatures. Post-structural analysis, outcomes related to von Mises internal stresses are visually depicted on the body's surface using a color scale from blue (lower stress) to red (critical stress).
Modifications to the prototype followed static analysis results. Inferences were drawn regarding material and geometry effectiveness. Iterative modifications were made based on observed results until the final performance aligned with the project requirements.
3. Evaluation of the initial prototype and proposed modifications
Modeled with stainless steel 316 [3], featuring a yield strength of 172 MPa, the prototype was subjected to a load of 100 N load using SolidWorks Simulation. The simulation (Fig. 2) revealed a resistance below the target, as the device failed under a load 10 times lower than the intended capacity.
Fig. 2Static load analysis of the initial prototype: 100 N load
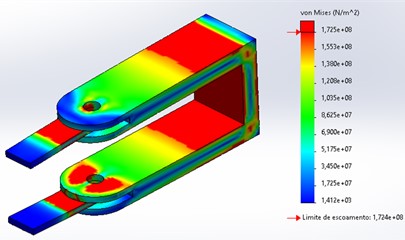
Changes were implemented iteratively. An initial thickness increases still allowed for widespread plastic deformation, prompting the need for a material with a higher yield strength. Reconstruction using martensitic tempered stainless steel (440 A), featuring a yield strength of 1650 MPa, showed improved resistance but exhibited failure in tabs and arm connections due to reduced ductility.
Testing with forward-facing bite tips revealed higher stresses on the clamp’s tips and joint (Fig. 3), and further iterations involving corner removal and augmentation of the clamp’s height and length outside the mouth region resulted in increased load capacity, user support ease, and improved placement of strain gauges.
Fig. 3Static load analysis of early iterations: 1000 N load
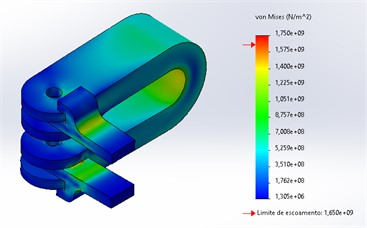
a) 4th iteration: bite tip design modification
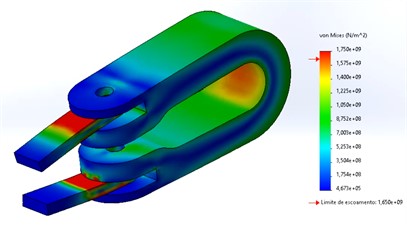
b) 3rd iteration: increased thickness
4. Concluding design iteration
After eleven iterations, a final design (Fig. 4) that met the targets for mechanical and elastic resistance was developed.
Fig. 4Gnathodynamometer’s concluding geometry
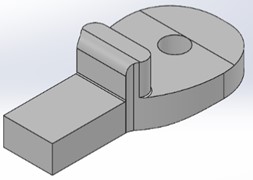
a) Bite tip
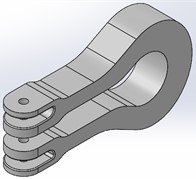
b) Clamp body
The results of static load analysis through FEM (Fig. 5) are shown below.
Fig. 5Static load analysis of the final design: 1000 N load
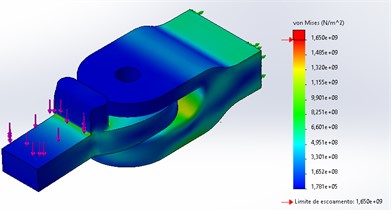
a) Bite tip analysis with free movement conditions
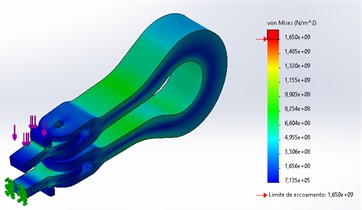
b) Clamp body analysis
Focusing on the clamp arms and the rear body for strain gauge attachment, stress levels stayed well below the material yield limit, under 1000 MPa. The most substantial stresses occurred where the bite tips connect to the clamp, on the lower support tab. The area recorded stresses of approximately 1400 MPa.
The chosen material proved suitable for the application, supporting applied loads. The developed geometry met set limits while preserving fundamental gnathodynamometer design features.
5. Conclusions
The initial clamp version faced challenges, including stress concentration and low material deformation resistance. Iterative modifications, backed by finite element method simulations, gradually improved device performance, meeting requirements for measuring human bite force.
While a wider safety margin would be desirable, considering the data for bite force measured on adults, the device performance was deemed suitable for pediatric use, where the bite force typically ranges around 200 N [6].
The gnathodynamometer is still in early development, laying the groundwork for deeper understanding. Investigating variations in bite tip position for load readings and considering an automatic detection system could offer valuable insights.
References
-
M. Bakke, “Bite force and occlusion,” in Seminars in Orthodontics, Vol. 12, No. 2, pp. 120–126, Jun. 2006, https://doi.org/10.1053/j.sodo.2006.01.005
-
S. C. C. S. Araújo, M. M. Vieira, C. A. Gasparotto, and S. Bommarito, “Análise da Força de Mordida nos diferentes tipos de maloclusões dentárias, Segundo Angle,” (in Portuguese), Revista CEFAC, Vol. 16, No. 5, pp. 1567–1578, Oct. 2014, https://doi.org/10.1590/1982-021620145113
-
O. Santiago Jr., “Desenvolvimento de um dinamômetro de baixo custo com pontas articuladas para medição de força de mordida,” Programa de Pós-Graduação em Engenharia Mecânica da UFMG, Belo Horizonte, Brazil, 2023.
-
R. Huebner, T. H. R. Cunha, R. G. Lacerda, O. Santiago Jr., and M. V. L. Ferreira, “Dinamômetro de mordida com ponta articulada,” BR Patent 10 2021 023693 0 A2, 2023.
-
D. L. Logan, K. K. Chaudhry, and P. Singh, A First Course in the Finite Element Method. Stamford, C Connecticut: Cengage Learning, 2011.
-
G. Mountain, D. Wood, and J. Toumba, “Bite force measurement in children with primary dentition,” International Journal of Paediatric Dentistry, Vol. 21, No. 2, pp. 112–118, Aug. 2010, https://doi.org/10.1111/j.1365-263x.2010.01098.x
About this article
The authors have not disclosed any funding.
The datasets generated during and/or analyzed during the current study are available from the corresponding author on reasonable request.
Pedro Ivo Santos Rodrigues centered on evaluating and refining the gnathodynamometer prototype. Employing Finite Element Method simulations, he conducted assessments of its mechanical properties and structural integrity, scrutinizing the device’s performance across different load conditions. By delving into stress distribution analysis, he pinpointed areas for enhancement and conducted iterative design modifications. This iterative approach aimed to elevate the device’s reliability and functionality, ultimately ensuring its applicability for measuring pediatric bite force. Orlando Santiago Júnior played a pivotal role in the creation of the evaluated device in this study. He collaborated closely with me during the assessment of mechanical properties and provided valuable insights for geometric modifications to enhance the device. His expertise and dedication significantly contributed to the refinement of the gnathodynamometer prototype, ensuring its mechanical strength and functionality. Rudolf Huebner, serving as the Work Supervisor, played a crucial role in guiding the overall development of the study. His mentorship extended beyond providing technical assistance, encompassing insightful contributions to the research process. Professor Huebner’s guidance was instrumental in shaping the project's direction and ensuring its alignment with scholarly standards. His mentorship greatly enhanced the overall quality and depth of the work.
The authors declare that they have no conflict of interest.
This study did not involve the participation of humans(s), biological matter or their data.