Abstract
The objective of this study is to investigate the natural vibration of a rectangular plate made of orthotropic material with circular thickness (two dimensions) and temperature variation on the plate is parabolic (two dimensions) in nature. The solution to the problem is obtained by utilizing the Rayleigh-Ritz technique and the first four frequency modes are obtained under clamped edge conditions. The study aims to provide numerical data that demonstrate how circular variation in tapering parameters of plate can effectively control and optimized vibrational frequencies of the plate. Orthotropic rectangular plate, thermal gradient, circular tapering, aspect ratio.
1. Introduction
To design structures or understand system characteristics, it becomes vital to investigate the vibrational properties of plates. Many systems and structures such as bridges, buildings, and aircraft wings consist of plates of various shapes. The vibration characteristics of a plate are influenced by plate parameters such as tapering, non-homogeneity (in the case of nonhomogeneous materials), and thermal gradient. A considerable number of studies in the literature have focused on various values of plate parameters.
The approach outlined in [1] was utilized to amalgamate solutions for plates with different geometries (such as circular, annular, circular sector, and annular sector plates) under various boundary conditions. In [2], the wave-based method (WBM) was utilized to forecast the flexural vibrations of orthotropic plates. In [3], a solution based on two-variable refined plate theory of Levy type was developed for free vibration analysis of orthotropic plates. In [4], a new analytical solution utilizing a double finite sine integral transform technique was introduced for the vibration response of plates reinforced by orthogonal beams. In [5], the Rayleigh Ritz method was utilized to determine the frequency of an orthotropic rectangular plate, whereas in [6], the time period of transverse vibration of a skew plate with different edge conditions was assessed. In [7], the influence of temperature on the frequencies of a tapered plate was discussed, while [8] investigated a non-uniform triangular plate subjected to a two-dimensional parabolic temperature distribution. The investigation of time period of rectangular plates with varying thickness and temperature was examined in [9]. Time period analysis of isotropic and orthotropic visco skew plate having circular variation in thickness and density at different edge conditions is discussed in [10] and [11].
It is noticeable from the literature that most of the authors have investigated either linear or parabolic variations in tapering parameters, but no one has focused on circular variation in tapering parameter. This study aims to fill this research gap by exploring the influence of two dimension circular thickness on the vibrational frequency of an orthotropic rectangular plate under a two dimension parabolic temperature profile. The circular variation examined in this paper results in a reduction in the variation in frequency modes, as shown in the numerical results section.
2. Problem geometry and analysis
Taking into account that the nonhomogeneous rectangular plate shown in Fig. 1 with sides a, b and thickness l.
Fig. 1Orthotropic rectangular plate with 2D circular thickness
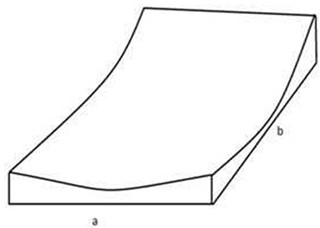
The formulation of the kinetic energy and strain energy for plate vibration is given below, similar to the approach presented in [12]:
where ϕ is deflection function, ω is natural frequency, Dζ=Eζl3/12(1-νζνψ), Dψ=Eψl3/12(1-νζνψ), Dζψ=Eζl3/12(1-νζνψ). Here, Dζ and Dψ is flexural rigidity in ζ and ψ directions respectively and Dζψ is torsional rigidity.
In order to address the investigated problem, the Rayleigh-Ritz method is utilized, which necessitates:
Using Eqs. (1), (2), we have:
Proposing non-dimensional variable as ζ1=ζ/a, ψ1=ψ/a along with two dimension circular thickness as:
where l0 is thickness at origin and β1, β2≤1 are tapering parameters.
The two-dimensional parabolic temperature distribution, as presented in Eq. (6):
where τ and τ0 represent the temperature at a given point and at the origin respectively.
For orthotropic materials, modulus of elasticity is evaluated by:
where Eζ and Eψ are the Young’s modulus in ζ and ψ directions, Gζψ is shear modulus and γ is called slope of variation.
Using Eq. (6), Eq. (7) becomes:
Gζψ=G0(1-α(1-ζ21)(1-a2ψ1b22)),
where α=γτ0(0≤α<1) is called thermal gradient.
Using Eqs. (5), (8) and non dimensional variable, the functional in Eq. (4) become:
∙(1+β2{1-√1-a2b2ψ12})3{(∂2Φ∂ζ21)2+E2E1(∂2Φ∂ψ21)2+2νζE2E1(∂2Φ∂ζ21)(∂2Φ∂ψ21)
+4G0E1(1-νζνψ)(∂2Φ∂ζ1∂ψ1)2}]dψ1dζ1-λ2∫10∫ba0[(1+β1{1-√1-ζ12})
∙(1+β2{1-√1-a2b2ψ12})]Φ2dψ1dζ1=0,
where D0=12(E1l3012(1-νζνψ)) and λ2=12a4ρω2(1-νζνψ)E1h02.
The deflection function that meets all the edge conditions is taken as in [13]:
where Ψi, i=0,1,2...n are unknowns and the value of e, f, g, h can be 0, 1 and 2, corresponding to given edge condition.
Eq. (10) can be minimized by imposing the following condition:
Solving Eq. (11), we have frequency equation:
where P=[pij]i,j=0,1,..n and Q=[qij]i,j=0,1,..n are square matrix of order (n+1).
3. Numerical results and discussion
In this study, the first four natural frequencies of a clamped orthotropic rectangular plate with two dimension circular thickness and two dimension parabolic temperature variations are investigated corresponding to various plate parameters aspect ratio a/b, tapering parameters β1 and β2, and thermal gradient α. The numerical calculations are based on the subsequent parameter values:
Table 1Modes of frequency of clamped orthotropic rectangular plate corresponding to β1
β2 | α=0.2 | α=0.4 | α=0.6 | |||||||||
λ1 | λ2 | λ3 | λ4 | λ1 | λ2 | λ3 | λ4 | λ1 | λ2 | λ3 | λ4 | |
0.0 | 17.002 | 65.265 | 146.471 | 335.761 | 17.085 | 64.734 | 145.409 | 344.526 | 17.173 | 64.058 | 144.568 | 353.913 |
0.2 | 17.747 | 67.704 | 151.913 | 351.645 | 17.848 | 67.198 | 151.149 | 359.343 | 17.951 | 66.545 | 150.178 | 372.482 |
0.4 | 18.548 | 70.301 | 157.829 | 367.708 | 18.665 | 69.815 | 156.993 | 378.568 | 18.782 | 69.169 | 156.353 | 390.070 |
0.6 | 19.400 | 73.032 | 163.844 | 388.066 | 19.531 | 72.556 | 163.396 | 397.071 | 19.660 | 71.918 | 162.620 | 412.912 |
0.8 | 20.295 | 75.877 | 170.500 | 405.951 | 20.439 | 75.414 | 169.982 | 417.520 | 20.579 | 74.769 | 169.561 | 432.019 |
1.0 | 21.228 | 78.822 | 177.057 | 430.024 | 21.385 | 78.367 | 176.579 | 443.749 | 21.534 | 77.713 | 176.455 | 457.574 |
Table 2Modes of frequency of clamped orthotropic rectangular plate corresponding to β2
α | β1=β2=0.2 | β1=β2=0.4 | β1=β2=0.6 | |||||||||
λ1 | λ2 | λ3 | λ4 | λ1 | λ2 | λ3 | λ4 | λ1 | λ2 | λ3 | λ4 | |
0.0 | 18.539 | 70.998 | 159.217 | 364.788 | 20.306 | 76.727 | 172.199 | 403.590 | 22.244 | 82.942 | 186.104 | 449.270 |
0.2 | 17.747 | 67.705 | 151.912 | 351.645 | 19.507 | 73.367 | 164.790 | 391.249 | 21.429 | 79.480 | 178.659 | 437.433 |
0.4 | 16.912 | 64.226 | 144.209 | 338.017 | 18.665 | 69.816 | 156.984 | 378.585 | 20.571 | 75.821 | 170.826 | 425.369 |
0.6 | 16.027 | 60.520 | 136.028 | 323.885 | 17.772 | 66.023 | 148.867 | 365.262 | 19.660 | 71.917 | 162.636 | 412.879 |
0.8 | 15.079 | 56.527 | 127.337 | 309.053 | 16.816 | 61.942 | 140.183 | 351.597 | 18.684 | 67.710 | 153.955 | 400.094 |
1.0 | 14.050 | 52.161 | 118.026 | 293.397 | 15.777 | 57.482 | 130.883 | 337.433 | 17.620 | 63.109 | 144.730 | 386.914 |
Table 3Modes of frequency of clamped orthotropic rectangular plate corresponding to α
α | β1=β2=0.2 | β1=β2=0.4 | β1=β2=0.6 | |||||||||
λ1 | λ2 | λ3 | λ1 | λ2 | λ3 | λ1 | λ2 | λ3 | λ1 | λ2 | λ3 | |
0.0 | 18.539 | 70.998 | 159.217 | 364.788 | 20.306 | 76.727 | 172.199 | 403.590 | 22.244 | 82.942 | 186.104 | 449.270 |
0.2 | 17.747 | 67.705 | 151.912 | 351.645 | 19.507 | 73.367 | 164.790 | 391.249 | 21.429 | 79.480 | 178.659 | 437.433 |
0.4 | 16.912 | 64.226 | 144.209 | 338.017 | 18.665 | 69.816 | 156.984 | 378.585 | 20.571 | 75.821 | 170.826 | 425.369 |
0.6 | 16.027 | 60.520 | 136.028 | 323.885 | 17.772 | 66.023 | 148.867 | 365.262 | 19.660 | 71.917 | 162.636 | 412.879 |
0.8 | 15.079 | 56.527 | 127.337 | 309.053 | 16.816 | 61.942 | 140.183 | 351.597 | 18.684 | 67.710 | 153.955 | 400.094 |
Table 1 presents the modes of frequency (first four modes) corresponding to β1. Specifically, the values of β2=α chosen were 0.2, 0.4, and 0.6 respectively. Based on the results presented in Table 1, it can be inferred that:
1. The frequency modes increase in all four modes as β1 rises from 0.0 to 1.0.
2. As both β1 and α increase from 0.2 to 0.6 (i.e., β2=α=0.2 to β2=α=0.6), the modes of frequency also show an increment.
3. The modes of frequency (rate of increment) are predominantly influenced by β1, as opposed to the α and β2.
Table 2 presents the modes of frequency (first four modes) corresponding to β2, with fixed values of tapering parameter β1 and thermal gradient α i.e., β1=α=0.2, β1=α=0.4, and β1=α=0.6, respectively. Based on the findings in Table 2, it is evident that:
1. The modes of frequency exhibit an increase as β2 varies from 0.0 to 1.0.
2. The modes of frequency decrease as β1 and α increase from 0.2 to 0.6 (i.e., β1=α=0.2 to β1=α=0.6), when β2 changes from 0.0 to 0.6. However, the modes of frequency increase as β1 and α increase from 0.2 to 0.6 (i.e., β1=α=0.2 to β1=α=0.6), when β2 varies from 0.8 to 1.0.
3. In terms of the rate of change in modes of frequency, β2 exerts a stronger influence compared to α and β1.
4. The tables 1 and 2 indicate that the modes of frequency are primarily influenced by β2 as compared to β1.
Table 3 presents the modes of frequency (first four modes) for various values of α, while keeping both β1 and β2 fixed at 0.2, 0.4, and 0.6, respectively. By examining Table 3, the subsequent key findings can be observed:
1. The frequency modes also increase with an increase in β1 and β2 from 0.0 to 1.0, while the modes of frequency decrease with an increase in the value of α from 0.0 to 1.0.
2. Compared to β1 and β2, α has a greater influence on the modes of frequency (i.e., rate of change in the modes of frequency).
4. Conclusions
The above observation suggests that the plate parameters have a significant impact on the frequency modes of the plate. The selection of appropriate plate parameters can enable the manipulation of frequency modes and their variations as per the system requirements. Thus, it can be inferred that circular variation in plate parameters can be effective in minimizing and regulating frequency modes and their variations.
References
-
A. K. Rai and S. S. Gupta, “Nonlinear vibrations of a polar-orthotropic thin circular plate subjected to circularly moving point load,” Composite Structures, Vol. 256, p. 112953, Jan. 2021, https://doi.org/10.1016/j.compstruct.2020.112953
-
X. Xia, Z. Xu, Z. Zhang, and Y. He, “Bending vibration prediction of orthotropic plate with wave-based method,” Journal of Vibroengineering, Vol. 19, No. 3, pp. 1546–1556, May 2017, https://doi.org/10.21595/jve.2016.17326
-
H.-T. Thai and S.-E. Kim, “Levy-type solution for free vibration analysis of orthotropic plates based on two variable refined plate theory,” Applied Mathematical Modelling, Vol. 36, No. 8, pp. 3870–3882, Aug. 2012, https://doi.org/10.1016/j.apm.2011.11.003
-
K. Zhang, J. Pan, and T. R. Lin, “Vibration of rectangular plates stiffened by orthogonal beams,” Journal of Sound and Vibration, Vol. 513, p. 116424, Nov. 2021, https://doi.org/10.1016/j.jsv.2021.116424
-
A. Sharma, “Vibration frequencies of a rectangular plate with linear variation in thickness and circular variation in Poisson’s ratio,” Journal of Theoretical and Applied Mechanics, Vol. 57, No. 3, pp. 605–615, Jul. 2019, https://doi.org/10.15632/jtam-pl/109707
-
R. Bhardwaj, N. Mani, and A. Sharma, “Time period of transverse vibration of skew plate with parabolic temperature variation,” Journal of Vibration and Control, Vol. 27, No. 3-4, pp. 323–331, Feb. 2021, https://doi.org/10.1177/1077546320926887
-
A. Khodiya and A. Sharma, “Temperature effect on frequencies of a tapered triangular plate,” Journal of Applied Mathematics and Computational Mechanics, Vol. 20, No. 1, pp. 37–48, Mar. 2021, https://doi.org/10.17512/jamcm.2021.1.04
-
Snehlata, N. Mani, K. Kumar, A. Sharma, R. Bhardwaj, and P. Kumar, “Frequencies of nonuniform triangular plate with two-dimensional parabolic temperature,” in Advances in Intelligent Systems and Computing, Singapore: Springer Singapore, 2021, pp. 41–51, https://doi.org/10.1007/978-981-16-1696-9_4
-
N. Lather and A. Sharma, “Natural vibration of skew plate on different set of boundary conditions with temperature gradient,” Vibroengineering PROCEDIA, Vol. 22, pp. 74–80, Mar. 2019, https://doi.org/10.21595/vp.2019.20550
-
A. Sharma, R. Bhardwaj, N. Lather, S. Ghosh, N. Mani, and K. Kumar, “Time period of thermal-induced vibration of skew plate with two-dimensional circular thickness,” Mathematical Problems in Engineering, Vol. 2022, pp. 1–12, Mar. 2022, https://doi.org/10.1155/2022/8368194
-
N. Lather, R. Bhardwaj, A. Sharma, and K. Kumar, “Time period analysis of orthotropic skew plate with 2-d circular thickness and 1-D circular density,” Mathematical Problems in Engineering, Vol. 2022, pp. 1–15, Oct. 2022, https://doi.org/10.1155/2022/7880806
-
A. W. Leissa, “Vibration of plates,” Scientific and Technical Information Division, National Aeronautics and Space Administration, 1969.
-
S. Chakraverty, Vibration of Plates. CRC Press, 2008, https://doi.org/10.1201/9781420053968
About this article
The authors have not disclosed any funding.
The datasets generated during and/or analyzed during the current study are available from the corresponding author on reasonable request.
The authors declare that they have no conflict of interest.