Abstract
In this article, authors dealt with general solution of differential equation of orthotropic rectangular plate with clamped boundary conditions under bi-parabolic temperature variations. Rayleigh Ritz technique is adopted to solve the resultant equation and evaluate the frequencies for first four modes of vibration. The effect of circular thickness and density on frequencies of orthotropic plate are analyzed which is not done yet. The objective of the study is to optimize the frequency modes by choosing the appropriate variation in plate parameters. Th findings of the study complete the objective of the article. All the results are provided in tabular form.
1. Introduction
Orthotropic rectangular plate with various plate parameters is widely used in various engineering branches like aerospace, aircraft, automobiles etc. A significant work has been reported by many researchers on orthotropic rectangular plate along with different variations in plate parameters but few work has been reported to study the effect of circular variation in plate parameters (thickness and density).
Effect of nonhomogeneity on vibration of orthotropic rectangular plates of varying thickness resting on Pasternak foundation is discussed in [1]. Free vibration analysis of laminated composite plate with elastic point and line supports by using finite element method was presented by [2]. Buckling analysis of rectangular isotropic plate having simply supported boundary conditions under the influence of non-uniform in-plane loading by using first-order shear deformation theory (FSDT) has been implemented in [3] Free vibration of orthotropic rectangular plate with thickness and temperature variation is studied in [4] and [5] by using Rayleigh Ritz method. Theoretical analysis on time period of vibration of rectangular plate with different plate parameters was proposed by [6] and [7].
New straight forward benchmark solutions for bending and free vibration of clamped anisotropic rectangular thin plates by a double finite integral transform method is described in [8]. Natural vibration of skew plate on different set of boundary conditions with temperature gradient is analyzed in [9]. Free vibration analysis of isotropic and laminated composite plate [10] on elastic point supports using finite element method (FEM) is studied. Vibration frequencies of a rectangular plate with linear variation in thickness and circular variation in Poisson’s ratio was provided in [11]. Thermally induced vibrations of shallow functionally graded material arches is considered and analyzed in [12] by using classical theory of curved beams. Fast converging semi analytical method was developed by [13] for assessing the vibration effect on thin orthotropic skew (or parallelogram/oblique) plates. A mathematical model is presented in [14] to analyse the vibration of a tapered isotropic rectangular plate under thermal condition.
In this study, authors examined the behavior of frequencies of orthotropic rectangular plate having circular variations in thickness and density. Authors also discussed the frequency variation when temperature increased on the plate. The present study provided how we can optimize the frequency value by choosing circular variation in plate parameters which will be helpful to structural engineering to get ride from unwanted vibrations.
2. Problem geometry and analysis
Consider a nonhomogeneous orthotropic rectangle plate with sides a and b, thickness l and density ρ as shown in Fig. (1).
Fig. 1Orthotropic rectangular plate with 2D circular thickness
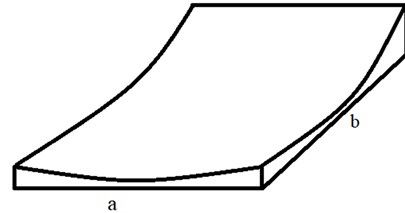
The kinetic energy and strain energy for vibration of plate are expressed in the following manner as in [15]:
where Φ deflection function, ω natural frequency, Dx=Exl3/12(1-νxνy), Dy=Eyl3/12(1-νxνy) are flexural rigidities in x and y directions respectively and Dxy=Exl3/12(1-νxνy) is torsional rigidity.
To solve frequency equation, Rayleigh Ritz technique is implemented which requires:
Using Eqs. (1), (2), we get functional equation:
Now, introducing non-dimensional variable as:
together with two dimensional circular thickness, we get:
where l0 is thickness at origin and β1, β2(0≤β1,β2≤1) are tapering parameters.
For non-homogeneity consideration, authors assumed one dimensional circular variation in density:
Two dimensional parabolic temperature distribution is taken as in [5]:
where τ and τ0 denotes the temperature on and at the origin respectively.
For orthotropic materials, modulus of elasticity is given by [17]:
where Ex and Ey are the Young’s modulus in x and y directions, Gxy is shear modulus and γ is called slope of variation. Using Eq. (7), Eq. (8) becomes:
Ey(x)=E2(1-α(1-ζ21)(1-a2b2ψ12)),
Gxy(x)=G0(1-α(1-ζ21)(1-a2b2ψ12)),
where α=γτ0(0≤α<1) is called thermal gradient. Using Eqs. (5), (6), (9) and non dimensional variable, the functional in Eq. (4) become:
where:
We choose deflection function which satisfies all the edge condition as taken in [16]:
where Ψi, i=0,1,2...n are unknowns and the value of e, f, g, h can be 0, 1 and 2, corresponding to free, simply supported and clamped edge conditions respectively. To minimize Eq. (11), we impose the following condition:
Solving Eq. (11), we have the following frequency equation:
where P=[pij]i,j=0,1,..n and Q=[qij]i,j=0,1,..n are square matrix of order (n+1).
3. Numerical results and discussion
Vibrational frequency of orthotropic rectangular plate having circular variation for first four modes under thermal effect with circular variation in thickness and density is discussed. Frequency equation is solved by using Rayleigh-Ritz technique with the help of Maple software. Frequency values for first four modes is calculated on different variations of plate parameters (i.e., thermal gradient, tapering parameters and nonhomogeneity). The results have been presented in the form of tables. In through out calculation the aspect ratio i.e., ratio of length to breadth of the plate is considered to be 1.5.
Tables 1 and 2 represents the frequencies for first four modes corresponding to tapering parametersβ1, β2 for three different values of thermal gradient, tapering paramter and nonhomogeneity m i.e., α=β2=m=0.2, α=β2=m=0.4, α=β2=m=0.6.(In Table 1) i.e., α=β1=m=0.2, α=β1=m=0.4, α=β1=m=0.6 (In Table 2).
Table 1Tapering parameter β1 vs vibrational frequency λ
β1 | α=β2=m=0.2 | α=β2=m=0.4 | α=β2=m=0.6 | |||||||||
λ1 | λ2 | λ3 | λ4 | λ1 | λ2 | λ3 | λ4 | λ1 | λ2 | λ3 | λ4 | |
0.0 | 16.2250 | 62.5266 | 140.527 | 314.224 | 15.4920 | 59.2450 | 132.974 | 303.002 | 114.7460 | 55.8753 | 125.414 | 291.617 |
0.2 | 16.9440 | 64.3744 | 145.547 | 331.268 | 16.2045 | 61.5334 | 137.954 | 319.324 | 15.4520 | 58.1060 | 130.414 | 306.785 |
0.4 | 17.7186 | 67.3744 | 151.897 | 347.316 | 16.9703 | 63.9622 | 143.549 | 334.372 | 16.2086 | 60.4747 | 135.793 | 322.357 |
0.6 | 18.5423 | 70.0079 | 156.897 | 366.204 | 17.7826 | 66.5125 | 149.182 | 353.426 | 17.0089 | 62.9527 | 141.414 | 341.070 |
0.8 | 19.4086 | 72.7501 | 163.162 | 384.709 | 18.6352 | 69.1850 | 155.236 | 372.291 | 17.8470 | 65.5327 | 147.325 | 359.995 |
1.0 | 20.3118 | 75.5910 | 169.577 | 405.599 | 19.5224 | 71.9365 | 161.609 | 391.622 | 18.7174 | 68.1935 | 153.484 | 380.389 |
Table 2Tapering parameter β2 vs vibrational frequency λ
β2 | α=β1=m=0.2 | α=β1=m=0.4 | α=β1=m=0.6 | |||||||||
λ1 | λ2 | λ3 | λ4 | λ1 | λ2 | λ3 | λ4 | λ1 | λ2 | λ3 | λ4 | |
0.0 | 16.6318 | 63.8209 | 143.168 | 325.058 | 16.3257 | 61.8337 | 138.677 | 320.118 | 16.0163 | 59.7280 | 134.016 | 317.501 |
0.2 | 16.9440 | 64.8730 | 145.547 | 331.223 | 16.6431 | 62.8843 | 141.117 | 326.682 | 16.3380 | 60.7803 | 136.374 | 325.163 |
0.4 | 17.2665 | 65.9491 | 147.895 | 339.639 | 16.9703 | 63.9622 | 143.549 | 334.372 | 16.6691 | 61.8582 | 138.930 | 332.343 |
0.6 | 17.5987 | 67.0584 | 150.517 | 345.112 | 17.3068 | 65.0711 | 146.010 | 342.215 | 17.0089 | 62.9517 | 141.463 | 340.544 |
0.8 | 17.9401 | 68.1874 | 153.129 | 352.618 | 17.6521 | 66.2017 | 148.587 | 349.894 | 17.3571 | 64.0756 | 144.056 | 348.595 |
1.0 | 18.2902 | 69.3457 | 155.639 | 361.626 | 18.0057 | 67.3523 | 151.159 | 359.151 | 17.7131 | 65.2175 | 146.720 | 357.118 |
From Tables 1 and 2, the following facts can be interpreted:
1) Frequency increases in both the Tables 1 and 2 with the increasing in value of tapering parameters β1andβ2.
2) for fixed values of both the tapering parameters β1andβ2, frequency decreases in both the Tables 1 and 2.
3) Rate of decrement of frequencies reported in Table 2 is much slow as compared to Table 1.
Table 3 summarizes the frequency for first four modes corresponding to thermal gradient α for three different value of tapering parameters β1,β2 and non homogeneity m i.e., β1=β2=m=0.2, β1=β2=m=0.4, β1=β2=m=0.6. Table 4 presents frequency for first four modes corresponding to nonhomogeneity m for three different values of thermal gradient α, tapering paramters β1, β2 i.e., β1=β2=α=0.2, β1=β2=α=0.4, β1=β2=α=0.6 respectively.
From Tables 3 and 4, it can be concluded that:
1) Increase in thermal gradient α and nonhomogeneity m results in decrease in frequency in both the tables 3 and 4.
2) Rate of decrement of frequency in nonhomogeneity is slower as compared to thermal gradient.
3) Here, behavior of both the Tables 3 and 4 is quite similar but in Table 4 have higher frequency values as compared to Table 3.
4) Without thermal effect, Table 3 have maximum frequency value then it decreases gradually with the increase in thermal gradient.
Table 3Thermal gradient α vs vibrational frequency λ
α | β1=β2=m=0.2 | β1=β2=m=0.4 | β1=β2=m=0.6 | |||||||||
λ1 | λ2 | λ3 | λ4 | λ1 | λ2 | λ3 | λ4 | λ1 | λ2 | λ3 | λ4 | |
0.0 | 17.7264 | 68.0981 | 152.773 | 344.414 | 18.5608 | 70.5842 | 158.161 | 359.868 | 19.4501 | 73.1977 | 163.831 | 377.364 |
0.2 | 16.9440 | 64.8730 | 145.547 | 331.268 | 17.7860 | 67.3676 | 151.009 | 347.406 | 18.6797 | 69.9838 | 156.690 | 365.602 |
0.4 | 16.1196 | 61.4568 | 138.000 | 317.463 | 16.9703 | 63.9628 | 143.544 | 334.381 | 17.8688 | 66.5801 | 149.261 | 353.332 |
0.6 | 15.2450 | 57.8227 | 129.915 | 303.204 | 16.1054 | 60.3435 | 135.542 | 321.048 | 17.0089 | 62.9563 | 141.409 | 340.651 |
0.8 | 14.3085 | 53.9052 | 121.350 | 288.101 | 15.1795 | 56.4381 | 127.131 | 306.930 | 16.0884 | 59.0494 | 133.108 | 327.429 |
1.0 | 13.2923 | 49.6287 | 112.057 | 272.273 | 14.1752 | 52.1774 | 118.015 | 292.304 | 15.0893 | 54.7852 | 124.157 | 313.803 |
Table 4Nonhomogeneity m vs vibrational frequency λ
m | α=β1=β2=0.2 | α=β1=β2=0.4 | α=β1=β2=0.6 | |||||||||
λ1 | λ2 | λ3 | λ4 | λ1 | λ2 | λ3 | λ4 | λ1 | λ2 | λ3 | λ4 | |
0.0 | 17.2013 | 65.9667 | 148.314 | 335.442 | 17.4856 | 66.1290 | 148.314 | 348.144 | 17.7821 | 66.1528 | 149.118 | 362.262 |
0.2 | 16.9440 | 64.8663 | 145.634 | 331.105 | 17.2222 | 65.0210 | 145.943 | 341.903 | 17.5128 | 65.0309 | 146.362 | 355.401 |
0.4 | 16.6979 | 63.8335 | 143.210 | 323.724 | 16.9703 | 63.9628 | 143.544 | 334.381 | 17.2554 | 63.9650 | 143.309 | 348.519 |
0.6 | 16.4622 | 62.8448 | 140.797 | 318.704 | 16.7292 | 62.9605 | 141.119 | 328.422 | 17.0089 | 62.9572 | 141.309 | 341.897 |
0.8 | 16.2363 | 61.8978 | 138.611 | 313.065 | 16.4980 | 62.0028 | 138.814 | 323.043 | 16.7728 | 61.9888 | 139.107 | 334.293 |
1.0 | 16.0193 | 60.9914 | 136.613 | 306.693 | 16.2762 | 61.0890 | 136.707 | 316.661 | 16.5461 | 61.0639 | 136.860 | 329.374 |
4. Conclusions
Present model provides frequencies of orthotropic rectangular plate with circular variations in thickness and density. from above results and discussion, authors concluded that increasing in tapering parameters β1andβ2, results the decrease in frequency as shown in tables 1 and 2. but increase in thermal gradient α and non homogeneity m, results the increase in frequency is illustrated in tables 3 and 4. the variation in frequency mode (increasing or decreasing) are very slow due to implementation of circular variation in plate parameters i.e., there is no sudden increment or decrement reported in frequencies.
References
-
R. Lal and Dhanpati, “Effect of Nonhomogeneity on Vibration of orthotropic rectangular plates of varying thickness resting on Pasternak foundation,” Journal of Vibration and Acoustics, Vol. 131, No. 1, Feb. 2009, https://doi.org/10.1115/1.2980399
-
S. Ghosh, S. Haldar, and S. Haldar, “Free vibration analysis of laminated composite plate with elastic point and line supports using finite element method,” Journal of the Institution of Engineers (India): Series C, pp. 1–12, Jan. 2022, https://doi.org/10.1007/s40032-021-00799-0
-
S. Das and P. Jana, “Analytical solution for buckling of rectangular plate subjected to non-uniform uniaxial compression using FSDT,” Lecture Notes in Mechanical Engineering, pp. 487–496, 2022, https://doi.org/10.1007/978-981-16-6490-8_40
-
A. Sharma, A. K. Sharma, A. K. Raghav, and V. Kumar, “Effect of vibration on orthotropic visco-elastic rectangular plate with two dimensional temperature and thickness variation,” Indian Journal of Science and Technology, Vol. 9, No. 2, pp. 1–7, Jan. 2016, https://doi.org/10.17485/ijst/2016/v9i2/51314
-
S. K. Sharma and A. K. Sharma, “Rayleigh-Ritz method for analyzing free vibration of orthotropic rectangular plate with 2D thickness and temperature variation,” Journal of Vibroengineering, Vol. 17, No. 4, pp. 1989–2000, Jun. 2015.
-
A. Sharma, A. Kumar, N. Lather, R. Bhardwaj, and N. Mani, “Effect of linear variation in density and circular variation in Poisson’s ratio on time period of vibration of rectangular plate,” Vibroengineering PROCEDIA, Vol. 21, pp. 14–19, Dec. 2018, https://doi.org/10.21595/vp.2018.20367
-
N. Lather, A. Kumar, and A. Sharma, “Theoretical analysis of time period of rectangular plate with variable thickness and temperature,” Advances in Basic Science (ICABS 2019), Vol. 2142, No. 1, p. 110027, 2019, https://doi.org/10.1063/1.5122487
-
D. An, Z. Ni, D. Xu, and R. Li, “New straightforward benchmark solutions for bending and free vibration of clamped anisotropic rectangular thin plates,” Journal of Vibration and Acoustics, Vol. 144, No. 3, Jun. 2022, https://doi.org/10.1115/1.4053090
-
A. Sharma and N. Lather, “Natural vibration of skew plate on different set of boundary conditions with temperature gradient,” Vibroengineering Procedia, Vol. 22, pp. 74–80, Mar. 2019, https://doi.org/10.21595/vp.2019.20550
-
S. Ghosh and S. Haldar, “Free Vibration analysis of isotropic and laminated composite plate on elastic point supports using finite element method,” Lecture Notes in Mechanical Engineering, pp. 371–384, 2022, https://doi.org/10.1007/978-981-16-6490-8_31
-
A. Sharma, “Vibration frequencies of a rectangular plate with linear variation in thickness and circular variation in Poisson’s ratio,” Journal of Theoretical and Applied Mechanics, Vol. 57, 2019.
-
M. M. Khalili, A. Keibolahi, Y. Kiani, and M. R. Eslami, “Application of ritz method to large amplitude rapid surface heating of FGM shallow arches,” Archive of Applied Mechanics, Vol. 92, No. 4, pp. 1287–1301, Apr. 2022, https://doi.org/10.1007/s00419-022-02106-4
-
A. M. Farag and A. S. Ashour, “Free vibration of orthotropic skew plates,” Journal of Vibration and Acoustics, Vol. 122, No. 3, pp. 313–317, Jul. 2000, https://doi.org/10.1115/1.1302085
-
A. Khanna and A. Singhal, “Effect of plates parameters on vibration of isotropic tapered rectangular plate with different boundary conditions.,” Journal of Low Frequency Noise, Vibration and Active Control, Vol. 35, No. 2, pp. 139–151, 2016.
-
A. W. Leissa, “Vibration of plates,” Scientific and Technical Information Division, National Aeronautics and Space Administration, 1969.
-
S. Chakarverty, Vibration of Plates. CRC Press: Boca Raton, 2008.
-
A. Sharma, R. Bhardwaj, N. Lather, S. Ghosh, N. Mani, and K. Kumar, “Time period of thermal-induced vibration of skew plate with two-dimensional circular thickness,” Mathematical Problems in Engineering, Vol. 2022, pp. 1–12, Mar. 2022, https://doi.org/10.1155/2022/8368194