Abstract
Pipe piles have been widely used in composite foundation treatment by virtue of the advantages of assembly line production, easy control of pile quality, fast construction, high bearing capacity of single pile and green environmental protection. By introducing elastic cushion in the static load test method of pipe pile composite foundation, and using theoretical analysis and field test to study the change rule of settlement, pile-soil stress ratio and pile top stress of pipe pile composite foundation with different cushion stiffness. It is concluded that it is feasible to replace the sand cushion layer recommended by the current specification with elastic cushion layer. The study shows that the elastic cushion method of static load test of pipe pile composite foundation is closer to the bearing state of real working condition. The elastic cushion has better pile-soil stress adjustment effect, which is more responsive to the stress adjustment effect of actual engineering cushion, and the elastic cushion provides an improved method for the static load test method of composite foundation.
1. Introduction
Pipe piles are widely used in composite foundation treatment works because of their convenient construction, high bearing capacity and low cost. The cushion layer is a key factor affecting the bearing characteristics of composite foundation, and scholars at home and abroad have carried out a lot of research on the performance of cushion layer in composite foundation [1-3], and there are still many uncertainties in the theoretical and experimental studies of cushion layer. For instance, the French ASIRI guideline recommends the thickness of cushion layer to be 400-800 mm, while the Chinese specification suggests 100-300 mm. under the action of embankment load, the cushion layer and the soil between piles produce compressive deformation, the pile with larger stiffness will be stabbed into the cushion layer, and the cushion layer particles will fill up the vacancies produced by stabbing on the pile, so that the upper load will be transferred to the soil between piles, and the pile-soil stress regulation will be accomplished. Zhou et al. [4] studied the change rule of pile-soil stress ratio of tubular piles through on-site static load test. Dai et al. [5] concluded that increasing the thickness of cushion layer can effectively improve the seismicity of composite foundation through load model test. Yu et al. [6] studied the change rule of peripile soil disturbance and the bearing characteristics of tubular piles when they penetrate through the visual model test. Rui et al. [7] improved the static load test method by physical modeling and numerical modeling test method to obtain the bearing properties of composite foundation under different cushion thickness conditions, which reduced the test workload. In terms of theoretical research, Yang and Zhou [8] used the deformation coordination method to derive the expression of soil bearing capacity between piles of rigid pile composite foundation. Zhuang and Wang [9] utilized Abaqus software to mechanically analyze the pile body, deduced the formula for calculating the pile-soil stress ratio, and gained useful conclusions. It can be seen that many scholars for the composite foundation matting research are mostly focused on the matting stress adjustment mechanism and foundation bearing, deformation characteristics of the research, rarely for the static load test method of the rationality of the research. The current specification [10] stipulates that 100-150 mm sand cushion layer is laid under the bearing plate of static load test to realize the bearing characteristics of simulated actual working conditions. For the pile body has the difference of flexible pile and rigid pile, the reasonableness of adopting this provision uniformly for different pile types is worth discussing. As the thinner sand cushion layer is nearly rigid under the action of pressure plate, it is difficult to play the role of pile-soil stress adjustment, resulting in the soil bearing capacity is difficult to play. The existing static load test method of static load only reflects the quality of pile construction, and does not well reflect the actual working condition of composite foundation.
In order to solve the defect that the current static load test method cannot reflect the real working condition, this paper proposes an elastic cushion method to improve the current static load test method of composite foundation. Through the field test of pipe pile composite foundation, the experimental study of composite foundation bearing capacity under two conditions of elastic cushion and sand cushion is carried out, and the change rules of settlement, pile-soil stress ratio and pile top stress of pipe pile composite foundation are analyzed and studied in comparison to obtain the reasonableness of the application of elastic cushion, and to provide references for the improvement and application of static loading test method of composite foundation.
2. Rationale for elastic cushion
Under the action of upper load, the elastic cushion layer will produce compression and the pile body will stab upward into the cushion layer, and the upper load is rapidly transferred to the soil around the pile. With the increase of load, the increase of cushion layer compression decreases, the soil around the pile is under pressure to settle, the pile's upward stabbing amount increases, the pile's bearing capacity is gradually exerted, the pile-soil stress ratio increases, the elastic cushion layer plays the role of pile-soil stress regulation, when the soil around the pile is compressed and the pile's upward stabbing is balanced, the composite foundation can play a better role in their respective bearing capacity. The compression amount of the elastic cushion itself can be calculated and determined according to the pile-soil sharing capacity of the actual working condition. Considering that the stiffness of the bearing plate in the field static load test is much larger than that of the soil layer of the embankment in the actual working condition, there is no upward puncture damage of the pile. The thinner the cushion layer in the static load test, the weaker the pile-soil stress adjustment ability. Reasonable setting of cushion layer thickness can realize the pile-soil stress distribution in actual working condition.
The size of the upward stabbing of the top of the pile into the cushion can be determined by the relationship between the pile-soil stress difference in the plane of the top of the pile and the cushion resistance, shown as:
where ∆ is the puncture volume at the top of the pile, is the amount of puncture per unit pressure of the cushion, is the bearing capacity at the top of the pile and is the soil stress in the same plane as the top of the pile.
If is difficult to determine, the principle of pile-soil deformation coordination can be based on the principle of ignoring the self-compression of the tubular pile, and equating the upward stabbing volume of the pile to the compression of the soil around the pile:
where is the positive soil stresses at depth meters below the plane of the pile tops, is the compression modulus of soil, and is the depth of influence of soil pressure in the plane at the top of the pile. , the coefficient is generally 0.4-0.67, is the diameter of the pile and is the net area of the soil under the bearing plate.
According to K. V. Terzaghi’s theory of ultimate bearing capacity of TSA foundations, the stresses in the spurs at the top of the pile when the soil region at the top of the pile is in ultimate equilibrium are shown in Eq. (4). The expression for the pile-soil stress ratio is shown in Eq. (5):
where is the angle of internal friction of the cushion, is the coefficient of carrying capacity, .
Based on engineering experience, the amount of pile spurs on the pile for actual working conditions can be calculated and determined, and then the mechanical parameters and thickness of the elastic cushion layer can be determined. Determine the pile-soil stress ratio to meet the actual working condition. Calculated by Eq. (1)-(5), the theoretical amount of pile spurs of pipe pile composite roadbed is generally greater than 10 mm, and the thickness of elastic cushion layer should be 40-60 mm, and the measurable pile-soil stress ratio is generally greater than 15, which is in line with the actual working condition.
3. Field static load test program
In order to verify the feasibility and rationality of the elastic cushion method for static load test of composite foundation of pipe piles, a comparative field static load test between the standardized method and the elastic cushion method is carried out. The elastic cushion for the field test is made of elastic rubber sheet with hardness of 55-60 and thickness of 40-60 mm. In order to increase the comparability and adaptability of the test, the static load test of the elastic cushion method for 8 test piles and the specification method for 3 test piles are completed respectively at the similar sites, and the verification test is carried out in the form of pile loading on the test section as the actual working condition.
3.1. Pipe pile static load test
The “elastic cushion method” of static load test of pipe pile composite foundation is to replace the sand cushion layer in the current specification with elastic rubber sheet, i.e. “load plate + elastic cushion layer + pile soil composite foundation”, and the other loading, data collection, etc. are carried out in accordance with the current specification. The representative test piles are selected from the same site with the same technology according to the standardized method and the elastic cushion method respectively to complete the static load test. The main test and collection processes are as follows. (1) Soil pressure collection: soil pressure meter buried at the top of pile and soil between piles respectively, of which 1 is at the top of pile and 4 are uniformly laid in the soil between piles; (2) Settlement collection: the meter is laid and collected in accordance with the current specification; (3) Load loading: slow sustained load method is adopted in accordance with the specification.
Representative piles for Foshan City Huayang Road South Extension prefabricated pipe piles, diameter 0.4 m, pile spacing 2.5 m, design pile length of 21 m. square layout piles, single pile bearing capacity design value of 700 kN, design value of the composite foundation bearing capacity of 150 kPa. test bearing plate for the square plate, the side of the length of 2 m, the test of the maximum loading up to 340 kPa. pile top planar soil body embedded in the soil manometer 5, the top of the pile layout of a, 10 mm fine sand as a leveling layer. 10 mm fine sand is laid as leveling layer. The elastic cushion layer adopts the rubber plate thickness of 40 mm. set up the test section on the site, according to the same way to bury the test instrumentation, using the form of pile load layer by layer to measure the pile, soil stress values, pile load up to 4.5 m, pile load close to the design value of the bearing capacity of the composite foundation, as shown in Fig. 1.
Fig. 1Static load test with elastic cushion layer for pipe pile composite foundation

a) Pipe pile under test
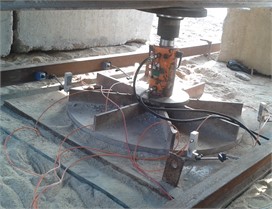
b) Loading tests for the elastic cushion method
3.2. Static load test analysis of pipe pile composite foundation
Fig. 2 and Fig. 3 show the load settlement curves and pile-soil stress ratio curves of static load test, respectively. As can be seen from Fig. 2, the characteristics of the load settlement curves measured by the two static load test methods, sand cushion method and elastic cushion method, are basically similar. The load settlement curve of the elastic cushion method is relatively gentle, mainly because the elastic cushion layer has strong integrity, and the pile-soil stress regulation is played by the elastic compression, and the settlement of the bearing plate is smooth, which indicates that the elastic cushion layer does not have much influence on the load settlement curve. The load settlement curve is approximately linear in character, the maximum settlement is 38.16 mm, the unloading rebound rate reaches 21.0 %, and the composite foundation shows relatively stable elastic deformation.
As can be seen in Fig. 3, the pile-soil stress ratios measured by the sand cushion method, the elastic cushion method and the actual working condition differ greatly. The overall development of the pile-soil stress ratio curve measured by the sand cushion method is more rapid, and the measured result reaches 30; the curve measured by the elastic cushion method is more gentle, and the final value reaches 22, while the pile-soil stress ratio is 13.6 in the actual working condition due to the filling of the 4.5 m high soil body, and the external load is close to the characteristic value of the bearing capacity. The pile-soil stress ratio curve measured by the elastic cushion method is smooth, and the pile-soil stress ratio at the beginning of loading is small compared with that of the sand cushion method, which indicates that the elastic compression of the cushion layer transfers the external load to the soil body obviously, and with the increase of external load, the elastic compression of the cushion layer continues to play a role in the bearings of the soil between the piles, and the pile-soil stress ratio is smaller than that of the sand cushion method, and the curve increases smoothly, and the increase of the pile-soil stress ratio is weakening in the end of the loading period, mainly due to the deformation of the piles. The increase of pile-soil stress ratio is weakened at the end of loading, mainly due to the deformation of the pile.
The elastic cushion can effectively change the pile-soil stress ratio. From the development of the test stress ratio curves, the sand cushion and elastic cushion can respond to the characteristics of pile-soil stress adjustment to bear the load together compared with the actual working conditions. The measured pile-soil stress ratios of the three test methods were 15.3, 12.3, and 11.6 when loaded with 1700 kPa. The elastic cushion method was closer to the actual working conditions, while the sand cushion method differed greatly. From the test results, the elastic cushion method is closer to the measured real working conditions than the sand cushion method.
Fig. 2Load-settlement curves of pipe pile
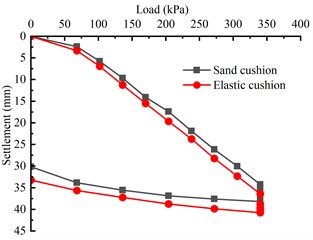
Fig. 3Pile-soil stress ratio curves of pipe pile
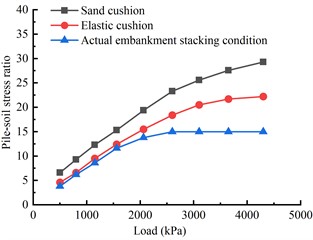
3.3. Statistical analysis of the results of the field trial program
In order to fully verify the feasibility and reasonableness of the elastic cushion method for static load test of composite foundation with pipe piles, four test piles were tested for each of the two working conditions of 40 mm and 60 mm thickness of elastic cushion, and three test piles were selected to be tested according to the standardized method. The statistical results of the tests are shown in Table 1. As can be seen from Table 1, the measured pile-soil stress ratios for different thicknesses of elastic cushion are generally in the range of 14 to 18, and the test results are relatively stable. The pile-soil stress ratio decreases as the thickness of the elastic cushion layer increases, which is in line with the conclusion of the relevant research results [11]. When the thickness of the elastic cushion layer is 60 mm, the measured data are more in line with the actual working conditions. The pile-soil stress ratio measured by the normative method is large, generally greater than 25, mainly because of the sand cushion particles are difficult to play the mobility under the binding of the bearing plate.
Table 1Summary of verification test results for composite foundations
Serial No. | Elastic cushion | Elastic cushion | |||||||
Cumulative settlement (mm) | Pile top stress (kPa) | Pile-soil stress ratio | Cushion thickness (mm) | Cumulative settlement (mm) | Pile top stress (kPa) | Pile-soil stress ratio | Cushion thickness (mm) | ||
1 | 20.34 | 3200 | 14.5 | 40 | 7 | 31.58 | 3300 | 15.6 | 60 |
2 | 25.29 | 3500 | 16.8 | 40 | 8 | 40.22 | 3500 | 16.8 | 60 |
3 | 28.36 | 3400 | 16.2 | 40 | Sand cushion | ||||
4 | 47.0 | 3600 | 18.1 | 40 | 1 | 35.16 | 4100 | 25 | 100 |
5 | 29.62 | 3200 | 14.6 | 60 | 2 | 51.22 | 4300 | 25.2 | 100 |
6 | 48.12 | 3400 | 15.9 | 60 | 3 | 39.41 | 4500 | 26.4 | 100 |
4. Conclusions
This study conducted theory analysis and on-site static load tests on pipe pile composite foundation under different cushion materials (sand cushion and elastic cushion layer). The variations in load-settlement relationship, pile-soil stress ratio, and pile head stress were analyzed and compared. The main conclusions are as follows:
1) Compared with the standardized method, the elastic cushion method can significantly reduce the pile-soil stress ratio, which is close to the actual working condition, indicating that the elastic cushion method is feasible and reasonable.
2) Compared with the static load test of standardized method, the settlement and pile-soil stress ratio change rule of the elastic cushion method is closer to the actual working condition, which provides a new way of thinking for the improvement of the static load test method of composite foundation with tubular piles.
3) The thickness of elastic cushion is 60 mm for static load test of composite foundation of pipe piles, and the best thickness of elastic cushion can also be calculated according to the actual working condition of pile body.
References
-
R. Rui et al., “Simulation of working characteristics of composite foundation cushion based on Winkler foundation discrete element model,” (in Chinese), Journal of Architecture and Civil Engineering, Vol. 40, No. 1, pp. 123–132, 2023, https://doi.org/10.19815/j.jace.2021.09079
-
F. Han, E. Ganju, R. Salgado, and M. Prezzi, “Comparison of the load response of closed-ended and open-ended pipe piles driven in gravelly sand,” Acta Geotechnica, Vol. 14, No. 6, pp. 1785–1803, Dec. 2019, https://doi.org/10.1007/s11440-019-00863-1
-
P. Staubach, J. Machaček, J. Skowronek, and T. Wichtmann, “Vibratory pile driving in water-saturated sand: Back-analysis of model tests using a hydro-mechanically coupled CEL method,” Soils and Foundations, Vol. 61, No. 1, pp. 144–159, Feb. 2021, https://doi.org/10.1016/j.sandf.2020.11.005
-
Y. Zhou et al., “Pile-soil stress ratio and settlement of in-situ shallow solidification-combined pipe-pile composite foundation under embankment load,” (in Chinese), Rock and Soil Mechanics, Vol. 43, No. 3, pp. 688–696, 2022, https://doi.org/10.16285/j.rsm.2021.0730
-
G. L. Dai et al., “Experimental study on bearing performance of caisson-cushion-piles composite foundation under low cyclic loading,” (in Chinese), China Journal of Highway and Transport, Vol. 35, No. 7, pp. 142–153, 2022, https://doi.org/10.19721/j.cnki.1001-7372.2022.07.011
-
H. C. Yu et al., “Visual model experimental study on penetration behaviour of open-ended and closed-ended pipepiles,” (in Chinese), Science Technology and Engineering, Vol. 23, No. 15, pp. 6573–6580, 2023.
-
R. Rui et al., “Hybrid test study of working performance of composite foundation cushion,” (in Chinese), Building Structure, Vol. 53, No. 9, pp. 128–132, 2023, https://doi.org/10.19701/j.jzjg.20211309
-
G. H. Yang and P. D. Zhou, “Discussion on the method of determining the bearing capacity of the soil between piles of rigid pile composite foundation in complicated stratum,” (in Chinese), Building Structure, Vol. 52, No. S1, pp. 2442–2449, 2022, https://doi.org/10.19701/j.jzjg.22s1632
-
Y. Zhuang and K. Wang, “Analytical solution for reinforced piled embankments on elastoplastic consolidated soil,” International Journal of Geomechanics, Vol. 17, No. 9, p. 06017, Sep. 2017, https://doi.org/10.1061/(asce)gm.1943-5622.0000926
-
“Technical code for ground treatment of buildings (JGJ79-2012),” The Ministry of Housing and Urban Rural Development of the People’s Republic of China, China Reconstructs Press, Beijing, 2012.
-
W. Sun et al., “Analysis of the ground treatment scheme for the nuclear island plant of a nuclear power station (in Chinese),” (in Chinese), Building Structure, Vol. 52, No. 8, pp. 35–139, 2022, https://doi.org/10.19701/j.jzjg.ls201816
About this article
This work was sponsored by the Project of Nanjing Institute of Technology School-level Research Fund: Research on bearing characteristics of pile-soil composite roadbed and new testing method (Grant No. ZKJ201802).
The datasets generated during and/or analyzed during the current study are available from the corresponding author on reasonable request.
The authors declare that they have no conflict of interest.