Abstract
Taking the non-standardized internal structural dimension parameters of rolling bearings as the design variable, the constrained optimization mathematical model of tapered roller bearings under the maximum target of basic static load rating and basic dynamic load rating has been established. Optimization results of the mathematical model have been obtained by using the improved multi-objective genetic algorithm, NSGA-II. After the above-mentioned methods were used to the optimization of the tapered roller bearing on the high-speed shaft of a 750 kW wind turbine gearbox, its basic rated static load and basic rated dynamic load can be increased by 15 % and 17 % compared with its standard value. Thus, the proposed methods are feasible and reliable, and has certain application value for improving the bearing performance and prolonging its service life.
1. Introduction
Tapered roller bearing is one of the core components of wind power gearbox, and its performance directly affects the working life, safety and stability of the gearbox [1]. Due to the high maintenance cost of wind power equipment, it is of great significance to extend its service life and reduce the maintenance times. Therefore, the research on rolling bearing around wind power equipment has become one of the key fields in recent years. The analysis shows that the performance of the rolling bearing is closely related to the geometric size and shape of each component of the bearing. The change of these parameter values has a great relationship with improving its working performance and extending its service life. Some valuable research results have been obtained by a series of researches. Zhang et al. [2] established a multi-objective optimal design model for cross roller bearings, and obtained the optimal parameters to significantly improve the rated dynamic load of bearings by adopted genetic algorithm. Eugenio [3] proposed an optimization model of tapered roller bearing system with arbitrary combination of radial force and axial force, and obtained the optimal matching among internal structure sizes of bearings under the maximum dynamic load and static load bearing capacity. Rajiv and Jat [4] took spherical roller bearings as the research object, established a three-objective optimization model of maximum dynamic bearing capacity, minimum elastic fluid dynamic oil film thickness and minimum bearing temperature, and obtained the optimal structural parameter values significantly improved bearing life by solving the genetic algorithm. Zhang et al. [5] took four-row tapered roller bearings with large conical angles as the research object, and established a constrained optimization model taking the root thickness of the inner ring guard, the minimum inner diameter of the outer ring and the nominal contact Angle as the design variables, and solved. Yuan et al. [6] took the double-row tapered roller bearing in wind power transmission system as the research object, established the optimization model of minimum volume and maximum life, and obtained satisfactory results. Zhou et al. [7] solved the optimization model of double-row tapered roller bearing with genetic algorithm, analyzed the different crossover rates on the influence of the optimization target value.
From the existing research, the multi-objective optimization of tapered roller bearing is mostly solved by converting the multi-objective optimization model into the single objective optimization model. The optimization results are subject to too much human intervention and cannot fully reflect the advantages of multi-objective optimization. Thus, the main goal of this work is focused on the development of a theoretical model that can be used to study the larger load, longer life and more convenient maintenance tapered roller bearings for wind power gearbox. This paper is organized as follows. Section 2 gives a detailed introduction about the construction method of the optimization model of tapered roller bearing. Section 3 introduces the solution method of the optimization model mentioned above. In Section 4, numerical results for a tapered roller bearings for wind power gearbox are obtained and discussed. Finally, the conclusions are presented in Section 5.
2. The optimization model of tapered roller bearing
2.1. Design variables
The wind turbine gearboxes are typical helical cylindrical speed incremental drives where the high speed stage shaft is supported by a pair of tapered roller bearings. Feedback from users indicates that the bearings have a short life and therefore need to be optimized to improve their performance. The tapered roller bearing consists of a number of parts, including a series of balls, one cage, the inner and outer raceways, as shown in Fig. 1. The bearing parameters, such as the outer diameter, ; the inner diameter, , and the bearing width of the bearing, have formulated strict standards in GB/ T272-2017. The others, such as the mean diameter, ; the number of rollers, ; the effective contact length of roller, ; the contact Angle, ; and the half cone Angle, etc. are not standardized. Different combination among the values of these parameters will have an important impact on the bearing performance. Thus, the above parameters are selected as design variables. In order to ensure that the optimization parameter values can better meet the actual engineering requirements, the other independent design variables of the optimization model of tapered roller bearing are as follows: control coefficient of rolling body diameter, and ; width control factor, ; control coefficient of bearing pitch diameter, ; and outer ring thickness control factor, . Therefore, the independent design variables of the optimal model of tapered roller bearing can be expressed as:
Fig. 1Structural dimension parameters of tapered roller bearings
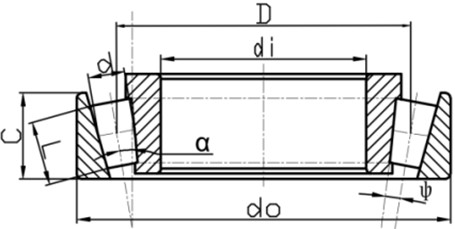
2.2. Objective functions
2.2.1. Maximum basic static load rating
The main performance index of tapered roller bearings working at low speed and heavy load is the basic rated static load. The greater the basic rated static load is, the higher the static strength of rolling bearing is. Therefore, in order to improve the working performance of bearings under low speed and heavy load conditions, the larger the basic rated static load of tapered roller bearings is, the better the carrying capacity is. The corresponding objective function is shown in Eq. (2):
2.2.2. Maximum basic rated dynamic load
The basic dynamic load rating is the main determinant of fatigue life of rolling bearings under medium and high-speed operating conditions. The larger the basic dynamic load rating is, the longer the fatigue life of rolling bearing is. The Lundberg-Palmgren formula is used internationally to calculate the basic dynamic load rating. Therefore, the objective function for the basic dynamic load rating of tapered roller bearings is expressed as follows:
where is the number of bearing rows, is the correction factor, = 1.1, is a coefficient, expressed as follows:
2.3. Constraint conditions
Tapered roller bearing is composed of inner ring, outer ring, tapered roller and cage that their geometric sizes are interrelated. Therefore, the design variables of the optimization model must meet some regulations and requirements, which constitute the constraints of the optimization model.
2.3.1. Constraints on the mean diameter of rollers
In order to ensure the reasonable assembly of bearings, the average diameter of rollers must be limited within a certain range by the inner and outer diameters of bearings. Here, it is limited by and . The corresponding constraint conditions can be expressed as follows:
2.3.2. Constraints on pitch diameter of bearings
In order to ensure the good operation of rollers in bearings, the pitch diameter of bearings, which is expressed by , should not be too different from its average diameter. The constraint conditions are written as:
2.3.3. Constraints on the effective contact length of rollers
The effective contact length of rollers is limited by the bearing width. After introducing the bearing width control parameter , the constraint condition can be expressed as:
In order to ensure the bearing capacity of tapered roller bearings, should not be less than , the constraint condition can be expressed as:
2.3.4. Constraints on the number of rollers
The more rollers there are, the greater the bearing capacity. But the number of rollers is limited by the bearing assembly space. The constraint condition which ensure that rollers can be smoothly assembled between inner and outer rings can be expressed as:
2.3.5. Constraints on raceway thickness of bearing outer ring
According to the standard, the thickness of the bottom of the outer ring of the bearing should be greater than or equal to .Thus, the constraint equation of the bottom thickness of the outer ring is derived as follows:
2.3.6. Constraints on roller spacing
In order to avoid collision between rollers, there must be a certain gap between two adjacent rollers, so the constraint condition can be expressed as:
2.4. Optimization algorithm selection
As previously mentioned, the optimization model is a nonlinear constrained optimal model with two objective functions and nine constraints. In order to avoid the disadvantages which have to take derivative of the functions and is difficult to obtain global optimal solutions using the conventional optimal algorithm, a fast non-dominated sorting algorithm, NSGA-II is selected as the solution algorithm.
2.5. Engineering example
2.5.1. Design conditions
The bearing (32222) used in the high speed shaft of 750 kW wind power gearbox is chosen as an example to demonstrate the application of the methodologies presented in this paper. Using bearing geometry and performance data obtained by checking the standards are as follows: the outer diameter is = 200 mm, the inner diameter is = 110 mm, the width is = 46 mm, the number of columns is = 1, the basic rated dynamic load is = 343830 N, the basic rated static load is = 524650 N. The radial load borne by the bearing is = 13215 N, and the axial load borne by the bearing is = 18820 N.
2.5.2. Range of values for design variables
The literature [8] gives the value range of design variables as follows: [0.3, 0.4], [0.5, 0.6], [0.01, 0.07], [0.7, 0.85], [0.4, 0.5]. The value ranges of other design variables determined by structural analysis are: [15, 30], [15, 25], [30, 38], [10, 30], [1, 10], [148, 157].
2.5.3. Optimization results
According to the previous experience using NSGA-II optimization algorithm and the needs of this optimization design, the relevant parameters required by the algorithm are selected as follows: the number of population is 100, the maximum number of generations is 500, the crossover probability is 0.8, the mutation probability is 0.08, the cross distribution index is 1, the mutation distribution index is 1, and the random seed is 0.5. Fig. 2 shows the 100 Pareto solutions that satisfy this requirement.
After data analysis and rule combination of the above 100 Pareto solutions, 14 groups of excellent and practical multi-objective Paretosolutions are obtained, as shown in Table 1. (The method of analysis and rule combination has been omitted due to space constraints.)
Table 1Multi-objective Pareto solution of tapered roller bearing
No. | Design variables and target values | ||||||||||||
(mm) | (–) | (mm) | (°) | (°) | (mm) | (–) | (–) | (–) | (–) | (–) | (N) | (N) | |
1 | 18.83 | 22 | 38 | 10.49 | 1.38 | 156.99 | 0.347 | 0.596 | 0.064 | 0.842 | 0.401 | 600740 | 376480 |
2 | 23.28 | 18 | 38 | 12.63 | 1.07 | 156.95 | 0.353 | 0.590 | 0.065 | 0.848 | 0.412 | 584730 | 412840 |
3 | 21.24 | 20 | 38 | 10 | 1.25 | 156.93 | 0.304 | 0.590 | 0.065 | 0.831 | 0.413 | 606240 | 404850 |
4 | 21.22 | 20 | 38 | 13.16 | 1.09 | 156.84 | 0.314 | 0.590 | 0.065 | 0.830 | 0.425 | 599930 | 400440 |
5 | 24.26 | 17 | 38 | 11.45 | 1.20 | 156.35 | 0.328 | 0.588 | 0.065 | 0.839 | 0.407 | 573060 | 416280 |
6 | 20.21 | 21 | 38 | 10.01 | 1.40 | 156.97 | 0.356 | 0.596 | 0.068 | 0.830 | 0.421 | 610210 | 396060 |
7 | 18.83 | 22 | 38 | 10.49 | 1.18 | 156.96 | 0.323 | 0.596 | 0.063 | 0.842 | 0.401 | 600730 | 376490 |
8 | 21.22 | 20 | 38 | 13.58 | 1.16 | 156.85 | 0.314 | 0.596 | 0.065 | 0.832 | 0.404 | 599050 | 399820 |
9 | 18.83 | 22 | 38 | 10.49 | 1.00 | 156.96 | 0.305 | 0.596 | 0.061 | 0.825 | 0.422 | 600730 | 376490 |
10 | 24.26 | 17 | 38 | 11.45 | 1.20 | 156.22 | 0.342 | 0.594 | 0.065 | 0.847 | 0.407 | 572980 | 416300 |
11 | 18.83 | 22 | 38 | 10.49 | 1.20 | 156.99 | 0.304 | 0.596 | 0.063 | 0.832 | 0.401 | 600740 | 376480 |
12 | 20.22 | 21 | 38 | 10.00 | 1.09 | 156.91 | 0.340 | 0.591 | 0.067 | 0.840 | 0.435 | 610450 | 396310 |
13 | 18.82 | 22 | 38 | 10.49 | 1.15 | 156.97 | 0.325 | 0.596 | 0.057 | 0.837 | 0.422 | 600460 | 376250 |
14 | 21.23 | 20 | 38 | 10.00 | 1.06 | 156.93 | 0.304 | 0.590 | 0.065 | 0.831 | 0.413 | 606000 | 404630 |
Compared with the standard values, it can be observed that the basic rated static load and basic rated dynamic load of the bearing in Table 1 are at least 15 % and 17 % higher than the standard values.
Fig. 2100 Pareto solutions
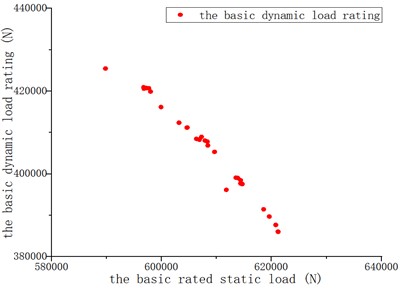
3. Conclusions
A general methodology for modelling and simulation of tapered roller bearings using in wind power gearbox was presented and discussed throughout this work. The tapered roller bearings used is modeled by introducing multi-function nonlinear optimization model, with two objectives, one is to maximize the basic dynamic load rating, and the other is to maximize the basic static load rating. Simultaneously, the above model contains nine constraints, which takes into account the pitch diameter of bearings, the effective contact length of rollers, the number of rollers, the raceway thickness of bearing outer ring, and the roller spacing. The solution method of the model is based on NSGA-II. The tapered roller bearings (32222) was used as a numerical example application.
From the results obtained, several feasible optimization schemes were easily obtained. Compared with the standard bearings in use, under the premise that the standard values such as inner diameter, outer diameter and width remained unchanged, the basic rated static load and basic rated dynamic load of post-optimality bearings are increased by at least 15 % and 17 % respectively. It is obvious that the bearing life is extended to a certain extent, the optimization method is feasible and reliable, and can provide effective support for the design and manufacture of wind power gearbox bearings.
The software of tapered roller bearing optimization for wind power equipment has been developed successfully. It can provide a guarantee for the rapid and efficient acquisition of multiple bearing schemes, provide an effective support for the rich bearing product series, high-performance bearing design and manufacturing, and provide a guarantee for meeting the diversified needs of customers.
References
-
J. M. Xie, B. H. Yu, and C. L. Zong, “Application of improved particle swarm optimization in tapered roller bearing,” Bearing, No. 9, pp. 4–7, 2009, https://doi.org/10.19533/j.issn1000-3762.2009.09.002
-
G. Zhang, J. Ruan, Q. Z. Yin, X. Zhang, D. D. Jiang, and Y. Liu, “Optimum design of crossed roller bearings based on genetic algorithms,” Bearing, No. 12, pp. 1–3, 2010, https://doi.org/10.19533/j.issn1000-3762.2010.12.001
-
E. Dragoni, “Optimal design of tapered roller bearings for maximum rating life under combined loads,” Mechanics and Industry, Vol. 18, No. 1, p. 112, 2017, https://doi.org/10.1051/meca/2016025
-
R. Tiwari and A. Jat, “Optimal design of spherical roller bearings based on multiple tasking operating requirements,” Multidiscipline Modeling in Materials and Structures, Vol. 16, No. 5, pp. 967–990, Aug. 2020, https://doi.org/10.1108/mmms-07-2019-0129
-
T. Zhang, L. Zhao, and C. Y. Mu, “Research on optimization design method of four-row tapered roller bearing with large conical angle (in Chinese),” (in Chinese), Electronic World, No. 19, pp. 19–20, 2018, https://doi.org/10.19353/j.cnki.dzsj.2018.19.006
-
H. L. Yuan, J. Qiu, Z. Wang, and D. L. Wang, “Multi-objective optimation design of bearing in wind power transmission system,” Machine Design and Manufacturing Engineering, Vol. 49, No. 10, pp. 21–26, 2020.
-
Y. P. Zhou, F. H. Mao, and J. Qiu, “Research on optimal design method of double-row tapered roller bearing,” Machinery Design and Manufacture, No. 8, pp. 17–20, 2021, https://doi.org/10.19356/j.cnki.1001-3997.2021.08.005
-
R. Tiwari, K. K. Sunil, and R. S. Reddy, “An optimal design methodology of tapered roller bearings using genetic algorithms,” International Journal for Computational Methods in Engineering Science and Mechanics, Vol. 13, No. 2, pp. 108–127, Mar. 2012, https://doi.org/10.1080/15502287.2011.654375
About this article
The authors have not disclosed any funding.
The datasets generated during and/or analyzed during the current study are available from the corresponding author on reasonable request.
The authors declare that they have no conflict of interest.