Abstract
Collaborative robots are machines that work hand in hand with humans; or as the name suggests, collaborate with them in a specific workspace. These robots are not enclosed in confined safety zones like traditional robots, as they interact very closely with humans. Though this is the case, appropriate measures are captivated while designing these robots considering human safety. These robots are well-versed in adapting to changes and frequent upgrades. They are flexible enough to carry out complex tasks. Due to these abilities, they become a significant asset in the manufacturing field. It’s been many years now since cobots are introduced in the industry sector. So, this is the right time to review various applications of cobots in manufacturing. First, the paper starts with a brief introduction followed by an extensive literature review which was structured after reviewing 76 research papers and articles. It ends with some essential conclusions. This paper discusses the diverse applications of cobots used in the manufacturing sector and their advantages. Further, it highlights the future of cobots and how they will be a boon for a technology-driven world.
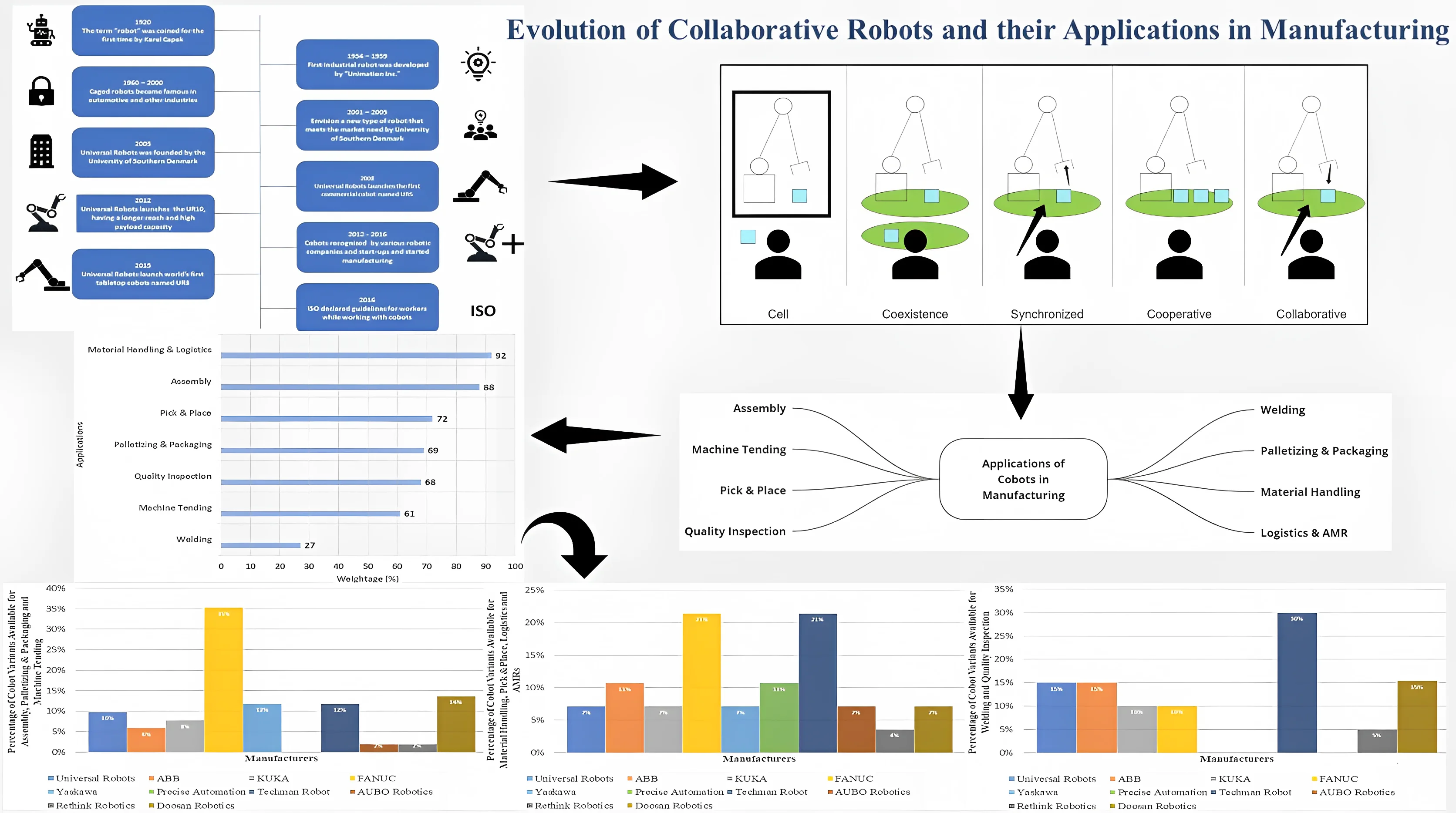
Highlights
- Application of collaborative robots in manufacturing sector.
- Evolution of cobots and cobot technology.
- Various methods of human-robot interaction.
- Cobot variants available in the market for various manufacturing applications.
- Future of collaborative robots.
1. Introduction
Over the past few years, the inclination towards industrial robots has increased tremendously. Traditional industrial robotic systems require heavy fence guarding and peripheral safety equipment, reducing flexibility while increasing costs and necessary space. Due to this, the requirement for flexible solutions has escalated. Hence, the introduction of collaborative robots has played an important role. Collaborative robots (cobots) are a type of robots that engage with humans closely, sharing the same workspace [1], [2]. The current market demands reduced lead time and operating costs. Cobots represent a natural evolution that can solve existing challenges in manufacturing and assembly tasks, as they allow for physical interaction with humans in a shared workspace; moreover, they are designed to be easily reprogrammed even by non-experts to be repurposed for different roles in a continuously evolving workflow [3]. They can solve complex manufacturing challenges and are seen as a promising way to achieve an increase in productivity [4]. The importance of cobots to today’s robotics society has been discussed by many researchers. For example, Lloyd argued that conventional robots tended to be evolved into cobots; the market share of cobots would be increased from 3 % in 2018 to 34 % in 2025. The total market value of cobots would increase from $9 to 12 billion at an annual growth rate of 57 % [5].
It’s been more than thirteen years since collaborative robots have been introduced in the industrial sector. Issues with traditional robots are being solved by using cobots and they are proving to be advantageous. The concept of these types of robots for manufacturing has been widely accepted to deal with human-robot interactions in open, unguarded, and unsaturated workspaces [6], [7]. Therefore, it’s an appropriate time to study and review the applications in this area. It has been observed that very negligible amount of papers highlight the maximum number of applications under one paper. This paper tries to solve this gap by giving a glimpse of various applications of cobots in the manufacturing sector. It also discusses the most recent developments in human-robot interactions, their benefits, and how the manufacturing industry finds them to be a valuable asset. Additionally, it highlights the cobots that are now available for various manufacturing applications, compares the number of versions offered by various cobot manufacturers, and identifies the market leader for each manufacturing application. This study covers eight different types of cobot-using manufacturing operations, ten different cobot manufacturing enterprises, and their various cobot models. Conclusions are drawn regarding which industrial applications lack collaborative robot technology, which companies lead which manufacturing applications, and which applications they should concentrate on for cobot development.
Here, what is collaborative robots, their history, and various types of human-robot interactions are explained in Section 2. Section 3 of the paper provides a detailed discussion of the various application of cobots in the manufacturing sector. Section 4 will give a brief overview of the future of cobots. Section 5 provides various discussions and results that are obtained from the study. The conclusion and future scope are provided in Section 6.
2. Collaborative robots
A robot is a programmable machine that performs a dedicated task. It can do complex assignments like humans and can learn itself by adapting to varying surroundings. The term “robot” derives from the Czech word robota (“forced labour”). It was first used by Karel Capek in his play R.U.R (1920). The field which studies robots and their behavior is called robotics. Industrial robots came into picture as the industrial revolution took place. The first industrial robot was developed by Unimation Inc. in the year 1954. It was a hydraulic heavy-lifting arm that could repeat arbitrary sequences of motions. Many robots emerged with advanced technologies as the years passed. From 1960 to 2000, many automotive and other types of industries became familiar with caged robots. From 2001 to 2005, researchers and scholars from the University of Southern Denmark envisioned a new type of robot that could meet future market needs. In the year 2005, the company named Universal Robots came into existence. With advancements, human and robot interactions increased. As days passed a new concept of collaborative robots came into reality. Universal Robots launched their first commercial collaborative robot named UR-5 in 2008. In 2010, UR-10 was put to sea having greater reach and payload capacity. Since the introduction of cobots into the world, many companies and start-ups get down to developing their commercial cobots. Universal Robots then launched UR-3, which was the world's first tabletop cobot. In 2016, ISO released a list of guidelines for workers’ safety while working with cobots. Cobots closely interact with humans to complete or achieve a definite task. They work in common workspaces with proper safety and precautions. Cobots are free from safety fences and walls, unlike traditional robots. Due to this prime disadvantage of traditional robots, there is an increase in lead time, operating cost, workspace utilization, and less flexibility to adapt to changes quickly. Hence, collaborative robots play an important role in eradicating these drawbacks. Collaboration between humans and robots will help reduce lead time, boost productivity, decrease operating costs, increase precision, and improve product quality [8], [9]. Fig. 1 shows the history of collaborative robots in a pictorial form. As years passed, many other organizations started developing their collaborative robot technologies. Table 1 shows us various companies that manufacture collaborative robots, their products, payload categories in which they work, and the year when they launched their first collaborative robot into the market.
There are many misconceptions generated regarding collaborative robots. Hence, there is a necessity to classify the types of collaborations human has; with robots. Muller et al. was the person to classify the different methodologies in which humans and robots can engage together, as recapitulated in Fig. 2 [1]. The diagram describes how the human-robot interaction evolves from a caged cell to a fully collaborative environment.
1) Coexistence: It is a type of collaboration in which the human handler and the cobot are in the same workspace but generally do not engage with each other.
2) Synchronized: When the human handler and the cobot work in the same work environment, but at different time intervals.
3) Cooperation: In this human handler and cobot work in the same workspace at the same time but they focus on different tasks.
4) Collaboration: When the human handler and cobot have to perform a task together, the action of one has an immediate effect on the other due to special sensors and a variety of machine vision systems.
The above-stated collaborative modes can also be adopted in traditional robots using quick response sensors and high-end machine vision systems. But additional hardware and integrations increase the equipment cost. Hence, one can prefer a commercial cobot that does not require additional hardware cost and comes with inbuilt technologically advanced features.
Table 1Information on other companies working on collaborative robot technologies
S. N | Company name | Year in which the company launched their first collaborative robot | Payload range of their collaborative robots | Collaborative Robots manufactured by the company |
1 | KUKA [10] | 2004 | 3-15 kg | LBR iisy, KMR iiwa, LBR iiwa, LBR Mrd |
2 | Rethink Robotics [11] | 2012 | 4 kg | Sawyer |
3 | Fanuc (Fuji Automatic Numerical Control) [12] | 2015 | 4-35 kg | CR-4, CR-7, CR-7, CR-14, CR-15, CR-35, CR-35, CRX Series Collaborative |
4 | ABB [13] | 2015 | 0.5-11 kg | YuMi series, GoFa series, SWIFTI series |
5 | Precise Automation [14] | 2015 | 2.5-8 kg | PF3400 SCARA PP100 Cartesian PFDD Direct Drive |
6 | Techman Robot [15] | 2015 | 4-20 kg | TM5-700, TM5-900, TM12, TM14, TM16, TM20 |
7 | AUBO Robotics [16] | 2015 | 3-16 kg | AUBO-i3, AUBO-i5, AUBO-i10, AUBO-i16 |
8 | Yaskawa [17] | 2017 | 10-30 kg | HC10DTP, HC20DTP, HC30PL |
9 | Doosan Robotics [18] | 2018 | 5-25 kg | H series, M series, A series |
Fig. 1Types of Human-Robot Collaborations (Source: Author’s own work)
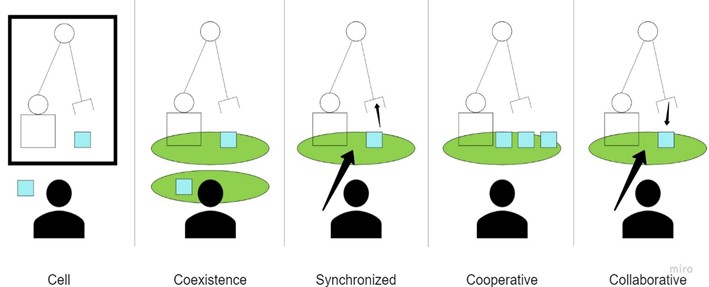
Fig. 2History of Cobots (Source: Author’s own work)
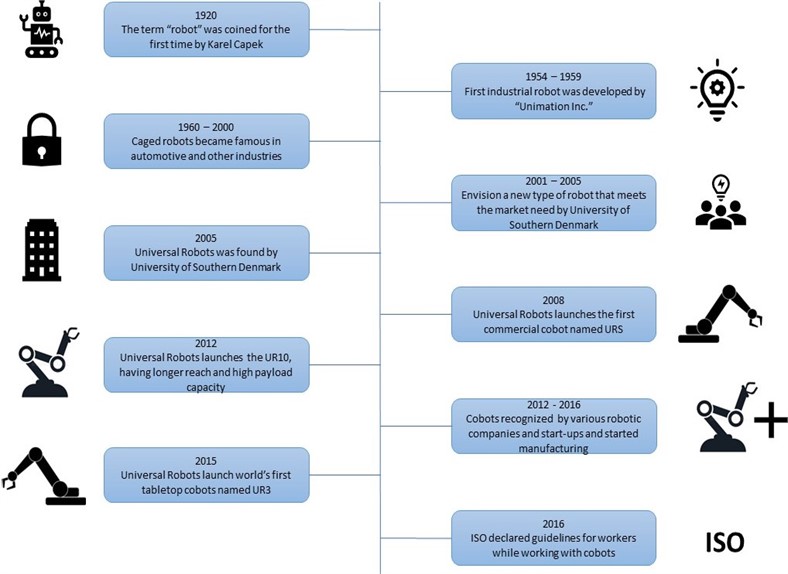
Cobots provide various benefits over conventional robots, including the following [19]-[22]:
1) Enhanced Safety: Cobots are made with a focus on security. They have cutting-edge sensors and algorithms that enable them to detect and steer clear of collisions with people. This lowers the possibility of injury and makes the workplace safer. According to research by the Occupational Safety and Health Administration (OSHA), using collaborative robots at work can lower the risk of accidents and injuries.
2) Flexibility: Cobots are incredibly adaptable and simple to program to carry out a range of jobs. They are therefore perfect for manufacturing in small batches and for special orders. Traditional robots are less adaptable and frequently created for specific purposes.
3) Cobots are more affordable than traditional robots, which makes them more available to small and medium-sized organizations. Additionally, they need minimal upkeep and may be readily reprogrammed to accommodate shifting production demands. According to research by the International Federation of Robotics, cobot adoption can boost output while lowering labour expenses.
4) Increased Productivity: Cobots can collaborate with humans to create more effective operations. Increased productivity and quicker turnaround times may result from this. According to the research of ABI Research, using cobots can boost industrial output by up to 30%.
5) Simple to Use: Cobots are made to be simple to use and program, even for persons without advanced robotics knowledge. This lessens the demand for highly specialized labour and may increase the accessibility of the production processes to a larger variety of people.
There are several reasons why cobots are generally considered easier to program than conventional robots [19]-[20]:
1) Intuitive programming interfaces: Cobots often have intuitive graphical user interfaces (GUIs) that allow users to program the robot using drag-and-drop functionality, without the need for complex coding skills. This makes the programming process more accessible and easier to learn.
2) Reduced need for specialized expertise: Traditional industrial robots typically require specialized programming skills and knowledge of complex programming languages. In contrast, cobots can be programmed by users with a wide range of technical backgrounds, including those without any prior programming experience.
3) Collaborative nature: Cobots are designed to work safely alongside humans, which means that they often have sensors and other safety features that allow them to detect and avoid collisions with humans and other objects. This makes programming cobots easier, as there are fewer safety considerations to take into account.
4) Flexibility: Cobots are typically designed to be easily reprogrammed for different tasks, which means that users can quickly adapt the robot's programming to changing production needs. This can make it easier to optimize the robot's performance and increase productivity.
5) Lower cost and complexity: Cobots are generally less expensive and less complex than traditional industrial robots, which means that they are more accessible to a wider range of businesses and industries. This can make it easier for businesses to adopt cobots and integrate them into their operations.
Overall, these factors make cobots easier to program and more accessible to a wider range of users than traditional industrial robots.
Collaborative robots, or cobots, can be programmed using several programming languages depending on the brand and model of the robot. Some of the most common programming languages used to program cobots include:
1) Universal Robots: Universal Robots cobots are programmed using a graphical user interface (GUI) called the Universal Robots Polyscope. The Polyscope uses a proprietary programming language based on a simplified version of Python [8].
2) ABB: ABB cobots are programmed using a programming language called RAPID (Robotics Application Programming Interface Description). RAPID is a high-level language that is similar to Pascal and is used to program ABB robots [13].
3) KUKA: KUKA cobots are programmed using a language called KRL (KUKA Robot Language). KRL is a high-level language that is similar to C++ and is used to program KUKA robots [10].
4) Fanuc: Fanuc cobots are programmed using a language called KAREL (Knowledge-based Articulated Robot Language). KAREL is a high-level language that is similar to Pascal and is used to program Fanuc robots [12].
5) Yaskawa: Yaskawa cobots are programmed using a language called INFORM (Interactive Robot Programming Language). INFORM is a high-level language that is similar to BASIC and is used to program Yaskawa robots [17].
These are just a few examples of programming languages used to program cobots. The specific programming language used will depend on the brand and model of the cobot.
Table 2 shows a comparison between conventional industrial robots and collaborative robots based on various factors [23]-[25].
128 research papers were downloaded for this investigation in total. This phase involved identification. Additionally, the stage of screening for relevance began by first eliminating research papers that were duplicates, which reduced the total to 115. 108 papers remained after scanning using the title and scrolling. 91 papers were read for the abstract and conclusion after 17 papers were eliminated. After eliminating studies that were unrelated to notions involving cobots, 80 papers were conceivably taken into consideration for full-text evaluation. After removing papers that did not pertain to cobot uses in manufacturing, the total number of papers mentioned in this study was 65. These 65 studies were divided into 6 categories, including Introduction and Cobot Concepts, which included 19 papers. Then comes assembly and machine tending with 13 papers, followed by 9 papers on cobots’ limitations, benefits, and future. There are eight papers for pick and place, and quality inspection. There are 9 papers for welding, palletizing, and packaging. Finally, there are 7 papers for material handling, logistics, and AMR.
Table 2Comparison between conventional industrial robots and collaborative robots based on various factors
S. N | Factors | Conventional industrial robots | Collaborative robots |
1 | Deployment | Hard to deploy | Easy to deploy |
2 | Programmability | Hard to program and is a time-consuming process | Easy to program |
3 | Flexibility | Hard to adapt to changes and are mostly designed for only one specific task | Can quickly adapt to changes |
4 | Space consumption | Requires more floor space to operate | Requires less floor space to operate |
5 | Cost | They are expensive | They are the low-cost and high-precision solution |
6 | Weight | Higher weight i.e., more than 50 kg | Lower weight i.e., less than 29 kg |
7 | Human-Robot Interaction and Job Security | Less interaction and dicey job security for operators | More interaction and a secured job for operators |
8 | Productivity | Helps to increase the overall productivity | Helps to increase the overall productivity as well as the productivity of workers |
9 | Safety | Due to minimal safety mechanisms, operators cannot work close to the robot | Complex and efficient safety mechanisms help the operators to interact with the robots in close proximity |
10 | Force sensors | Lack of external force sensors | External force sensors are present |
11 | Sensor Integrations and Machine Vision | Minimal sensor networks and standard machine vision systems can be integrated. | Advanced sensing technologies with high-end machine vision systems and end effectors can be integrated. |
Fig. 3 shows the search, selection, and inclusion/rejection criteria for research papers in a detailed manner.
Fig. 3Categorization of all the research papers considered for the current review (Source: Author’s own work)
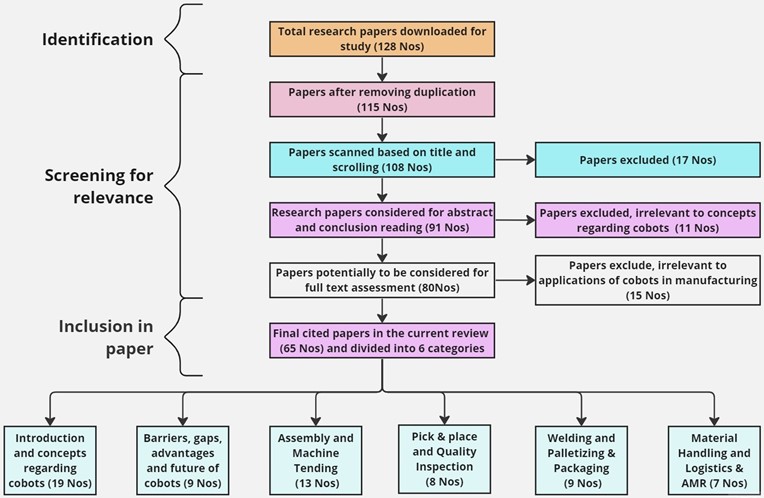
Further, Fig. 14 shows us the distribution of research papers referred to and cited based on their year of publication in the form of decades.
Fig. 4 shows us the distribution of research papers referred to and cited in this study based on their year of publication.
Fig. 4Percentage of papers referred for study based on the year of publication (Source: Author’s own work)
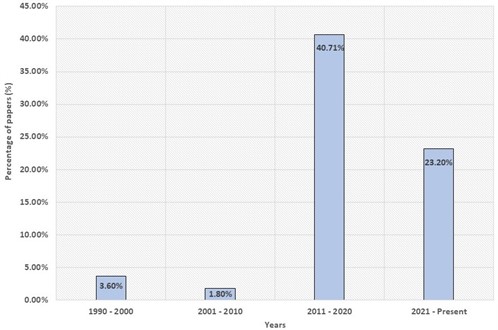
3. Applications of Cobots in the Manufacturing Sector
As years passed, recognition and demand for collaborative robots have increased. The market size of cobots is expected to swell up to 815 million US dollars in the year 2022 [26]. Though it's a new field of robotics, the need for its applications in manufacturing industries has escalated rapidly. Due to the introduction of autonomous systems, human involvement has been reduced drastically. As a result, required work goals are achieved with higher precision.
Though a sharp increase in automation has changed the course of employment, it has brought immense opportunities to the manufacturing sector. One of the most extensively used types of automation machines is collaborative robots. Due to continuous upgrades, it has been easy to program them. As the complications in industries increased, more was the development of building cobots for ill-structured workspaces. Nowadays, cobots can make decisions independently and make human-robot interaction more commanding [27]. Cobots have a wide range of applications in manufacturing industries. Some areas of applications are presented in Fig. 5.
Fig. 5Applications of Cobots in manufacturing (Source: Author’s own work)
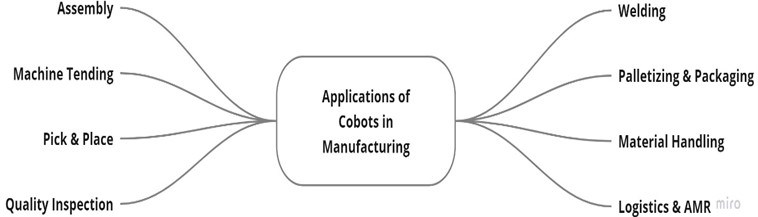
3.1. Assembly
Assembly is a manufacturing process in which components are sequentially fused using permanent or semi-permanent methods to obtain an effective product. However, the increasing complexity and new challenges in assembly operations have invited many new technologies. Collaborative robots provide a safe future for industries that need optimized production, reduced operating costs, and increased precision. Due to human-robot interaction, it is easier, less risky, and a lot faster to use robots for your assembly lines. Handling, loading, and unloading parts is not as simple as it sounds for a human [26]-[33]. Easy programming in cobots gives one the agility to automate heavy-duty and manual operations like assembly. They are beneficial with small workbenches and fast changeovers. There are many cobots in the market with a small range, longer range with heavier payload capabilities, tabletop, etc. Companies that are into developing cobots for assembly operations are; ABB Group, Universal Robots, KUKA AG, Fanuc Cooperation, and many more.
The advantages of collaborative robots for assembly are; an increase in consistency, labour productivity, quality, and speed of production, reduction in lead time and floor space utilization, ease to program and can be redeployed rapidly, increase in flexibility, improvement in quality, and less operation cost [34]-[37].
3.1.1. Case study: PSA and Fiat Chrysler automobiles [39]
The Mirafiori factory of PSA and Fiat Chrysler Automobiles in Turin, Italy, had installed 11 collaborative robot arms from Universal Robots to automate their Fiat 500 electric car production line. The two main challenges faced by the company were to maintain quality and repeatability in production to meet product standards and the high average age of factory workers. To overcome these drawbacks, they introduced 11 UR10e robots from Universal Robots to assemble waterproof liners to vehicle doors, soft-top assembly, tailgate riveting, hood mounting, extra door hinge tightening, and mudguard mounting. Due to the successful implementation of these initial cobots, they introduced more cobots in the manufacturing plant. The outcomes from this case study were that in order to achieve product standards, cobots can help maintain product quality and repeatability. They can do repetitive or physically demanding jobs that might be challenging for human workers, helping to alleviate labour shortages or a high average age of factory workers. Additionally, the successful adoption of 11 cobots by the Mirafiori factory shows how simply they may be integrated into current production lines. The fact that first cobot deployments can result in subsequent cobot adoption in industrial facilities suggests that cobots can provide real advantages in terms of productivity, efficiency, and safety.
Fig. 6Cobot performing assembly operation [38]
![Cobot performing assembly operation [38]](https://static-01.extrica.com/articles/23238/23238-img6.jpg)
3.2. Pick and place
The most attractive qualities of cobots are that they are precise and have a high degree of repeatability. Pick-and-place is one of the applications in manufacturing which desire such characteristics. It is hard for humans to work with the same intensity and energy levels; continuously without any errors [28]. Humans also tend to get bored with repetitive tasks. Hence interaction with cobots helps the human operator to make the task easy and riveting. Some cobots work autonomously, making the job more seamless and comfortable. They are easy to program and flexible enough to perform different pick and place operations. Unlike humans, they have speed and can work for hours or even days without interruptions [40]-[42]. There is a reduction in lead time. They also reduce safety hazards to humans by taking over taxing, repetitive tasks [43]. To enhance performance and capabilities various end effectors are designed for pick-and-place applications. Generally, cobots are limited to 15 Kg payload capabilities for this application.
3.2.1. Case study: King’s College London [45]
King’s College London is working on a project named GROWBOT (Grower-Reprogrammable Robot for Ornamental Plant Production Tasks). The main motive behind developing this cobot was to let non-experienced users work with robots for repetitive pick-and-place tasks and to help ease the shortages of seasonal labor. This cobot uses machine learning and artificial intelligence to hand out various herbs, plants, and seedlings. It helps to increase the efficiency of the process and also performs the same pick and place operation repetitively with the same accuracy. The outcomes from this case study were that cobots are more usable by novice users for repetitive pick-and-place operations. This is due to the fact that cobots, like the GROWBOT created by King's College London, employ artificial intelligence and machine learning to continually automate the pick-and-place action with the same accuracy. This benefit of cobots can help to reduce seasonal labour shortages and improve process efficiency.
Fig. 7Cobot performing pick and place operation [44]
![Cobot performing pick and place operation [44]](https://static-01.extrica.com/articles/23238/23238-img7.jpg)
3.3. Palletizing and packaging
The process of palletizing can be described as the process of stacking large quantities of similar items on a pallet for shipping purposes. The use of manual palletizers affects the human tendency of the workers as well as the rate of production. The main disadvantages of these palletizers are, they need constant monitoring, they are very slow, and even their payload capacity is less. The introduction of cobots in palletizing helps to refine the working environment of the workers. They can easily use these palletizer cobots to do heavy-duty tasks and monitor them easily [46], [47]. This is possible due to several sensors integrated into these systems that provide continuous feedback making them perform tasks more efficiently and precisely. Case palletizing cobots are used for stacking boxes, bags, pallets, and cartons ranging from medium to heavy payloads [43]. We know modern markets demand high and strict packing standards. For this, cobots prove to be a prime element for packaging applications. They help to avoid worker injuries by facilitating the lifting of heavy payloads [48]. Today there is a huge demand for packaging which has escalated the use of robots [49]. From studies, it has been observed that nine out of ten packaging companies are using robots. Reports have forecasted that there will be a 57 percent increase in Compound Growth Rate (CAGR) between now and 2023 [28]. Hence, there has been a surge in demand for cobots in these sectors to optimize fulfilment tasks. The advantages of cobots in palletizing and packaging are; easy to use and reprogram, require less maintenance, have higher strength and speed, and have a compact design.
3.3.1. Case study: Aillora [50]
Aillora is a company based in a town named Fougeres in France. They manufacture boxes for a wide range of clients in industries comprising board games, cosmetics, and champagne. They were always inclined towards automation, so they introduced industrial robots to their production lines. They had a bad experience with the robots as they were much more complex to use. Hence, they had to hire temporary workers when there use to be a hike in demand for supply. It was also observed that handling these boxes was hard and physically straining for workers. So, to overcome these challenges Aillora’s team installed cobots from Universal Robots to their production lines to make palletization operation easy. This resulted in smoother production and the company needed fewer temporary workers during peak demands. The outcomes from this case study were that cobots are significantly simpler to use than conventional robots, which can make them more challenging to run and program. Because Aillora was able to install cobots on their manufacturing lines to make palletization procedures simple, the case study suggests that they can be simply incorporated into current production lines. When they were installed, manufacturing ran more smoothly and there was less need for temporary labour during times of high demand. Workers found it physically taxing to handle boxes, thus cobots may have assisted by automating these chores to lower the risk of damage.
Fig. 8Cobot performing palletization [51]
![Cobot performing palletization [51]](https://static-01.extrica.com/articles/23238/23238-img8.jpg)
3.4. Machine tending
Machine tending is a process in which a human operator loads or unloads various parts or materials to a machine to execute a certain task. Cobots have been a boon for industrial automation and play a crucial role in present-day machine tending. The reason for the inclination of manufacturers toward cobots is due to their numerous characteristics. They help increase productivity, reduce lead time, quality improvement, and increase consistency [52]. So basically, in machine tending a human operator loads a workpiece onto the machine. Finally, after the execution of the task, the operator removes the finished workpiece and loads a new one. This kind of manual machine tending is slow, and from the safety point of view, it's risky too. According to human tendency doing repetitive tasks makes the job boring after some time. The introduction of cobots for machine tending applications helps to increase the pace of production and increase accuracy and precision. This makes the job interesting for human operators due to continuous engagement with the cobots [53], [54]. Operators no more have to work in hazardous workspaces and do repetitive tasks for a long time. Robotic machine tending is used for various applications like welding, injection moulding, milling, turning, grinding, stamping, forging, trimming, punching, etc. [43]. These cobots utilize less floor space, are easy to program, are easily deployable, and have a lower acquisition cost. Integration of these cobots with CNC makes it more advantageous and helps in the higher growth of the industry.
Fig. 9Cobot performing machine tending operation [55]
![Cobot performing machine tending operation [55]](https://static-01.extrica.com/articles/23238/23238-img9.jpg)
3.4.1. Case study: New England Union Company [56]
New England Union Company (NEU) is a machine shop that manufactures brass threaded pipe fittings for the plumbing and shipping industries. The first challenge faced by the company was due to long cycle times for production. The second was to automate less specialized tasks and upgrade the existing human power to a more complex piece of work like inspection and quality. To overcome this, the company used UR10e cobots for the palletizing function to pick and feed the workpieces from the tray to a gantry system. They further integrated these cobots with ActiNav systems, which helped in handling vision processing, collision-free motion planning, and autonomous real-time robot control for longer hours at night without human intervention. Hence, the time spent by the workers on these operations was reduced. The outcomes from this case study were that, in the context of industrial manufacturing, cobots have several benefits over traditional robots. Cobots can assist in reducing production cycle times, which can boost overall productivity and efficiency. They can automate less specialized jobs, freeing up human workers to concentrate on more difficult duties like inspection and quality control. To perform tasks like vision processing, collision-free motion planning, and autonomous real-time robot control, cobots can be connected with other systems, such as ActiNav. This could enhance the system's overall performance and dependability. Cobots can function for longer periods without the need for human interaction by automating tasks and interfacing with other systems. This could save labour expenses and enhance everything in general.
3.5. Quality inspection
Quality inspection is a process that comprises checking and measuring multiple characteristics and finding out flaws in a product by comparing it with standards. Introducing cobots in this process helps to make the job easy and ensures high order of flexibility. This process is automated by integrating cobots with high-end machine vision systems [57]. They are equipped with 2D and 3D vision sensors for increasing accuracy and precision. To use them, operators need not be skilled in programming as they are easy to use, deployable, and can perform cognitive tasks effortlessly. Cobots are consistent in quality inspection and perform operations with finesse with minimal deviation [58]. The products are checked rigorously by them before they are ready for packaging and shipping.
Applications and sectors in which cobots are used for quality inspection are; automotive industries, parts inspection of X-ray equipment, checking dimensions of fruits or vegetables in food and beverage industries, weld inspection, fabrication of metals, aircraft engines inspection, agriculture, and Inspection of central heating boilers [59]-[61].
Nowadays, these cobots are becoming autonomous or have a negligible amount of human interference and reduce the tedious job of human operators. Due to this, cobots ensure that the products meet the requirements and are responsible for maintaining strict quality standards. They also help in reducing operating costs.
Fig. 10Cobot performing quality inspection [62]
![Cobot performing quality inspection [62]](https://static-01.extrica.com/articles/23238/23238-img10.jpg)
3.5.1. Case study: Koyo electronics industries [63]
Koyo Electronics Industries is a company based in Japan that works in the automotive sector. They wanted to increase productivity and reduce operating costs by automating the quality inspection department. Production of in-vehicle electronic devices, PLCs, and rotary encoders requires high quality. To overcome these challenges, they introduced UR3 cobots from Universal Robots for quality inspection of touch panels. It was observed that after using these cobots, the daily work time was reduced from an average of 10 hours to 8 hours and boosted productivity by 31 %. The outcomes from this case study were that because fewer human workers were needed to complete the same amount of work, labour costs are likely to have decreased because of cobots. By lowering the possibility of human error and assuring reliable and consistent examination, the employment of cobots in quality inspection can raise the caliber of the final product.
3.6. Material handling
Material handling is nothing but the movement of various types of goods within a confined manufacturing workspace. It's a hectic job for human operators to move goods from one place to another in the workspace. To increase production rate and efficiency; companies have to automate repetitive tasks like material handling [28]. Cobots can do this work effortlessly, quicker, and precisely. They help to reduce industry mishaps and help in sustaining workers' safety.
Fig. 11Cobot performing material handling operation [65]
![Cobot performing material handling operation [65]](https://static-01.extrica.com/articles/23238/23238-img11.jpg)
Many new technologies have been introduced to increase human-robot interactions. Exoskeletons are one of those technologies which permit the human operator to wear them and handle heavy payloads up to 200 pounds with ease. They are flexible, made up of lightweight materials, easy to manoeuvre, and minimize strain [64]. Many industries like automotive, agriculture, medical and pharmaceutical, food and beverage, biotechnology, electronics, and semiconductors use cobots for material handling [43]. Hence, cobots help manufacturers to make their production cycles faster, reduce downtime and reduce operating costs.
3.6.1. Case study: Whirlpool [66]
Whirlpool is a company which is into manufacturing home appliances in Poland. The company was facing a challenge in combining the internal movement of components between the production lines with material handling automation. To overcome this challenge, they introduced three MiR200 autonomous mobile robots to transport dryer doors from pre-assembly to the assembly line. They were easy to program, safe, and helped in cost optimization. Due to their introduction, the company was able to increase productivity, increased safety, and transfer the workers to higher-valued tasks. The outcomes from this case study were that Whirlpool was able to quickly integrate the robot into their production process because of the MiR200’s simple programming, which didn’t require any advanced programming knowledge. It could carry components between production lines without endangering workers because it was safe to operate around people. By increasing productivity and enabling employees to concentrate on higher-value jobs, its implementation helped Whirlpool optimize its costs. Automating the movement of components between production lines, also helped to raise their productivity.
They were able to increase production process safety by lowering the danger of accidents brought on by manual material handling.
3.7. Welding
Welding is a process in which two or more parts are fused using heat, pressure, or both forming a join as it cools [67]. This fabrication process is one of the most intricate and requires skill. It demands accuracy and precision. Companies try to manufacture products according to the demand and expectations of the customer by keeping the cost low and maintaining quality. To achieve this, they have inclined towards modern technologies like collaborative robots. They help to make these fabrication processes like welding and soldering contented. Human operators can't achieve the same accuracy and precision repetitively.
Fig. 12Cobot performing welding operation [72]
![Cobot performing welding operation [72]](https://static-01.extrica.com/articles/23238/23238-img12.jpg)
Integrating cobots with high-end vision systems and sensing elements helps to do welding seamlessly [68]-[70]. We know that welding requires filler metals. They help to minimalize the wastage of filler metals and use them efficiently without compromising the quality of the products. Hence, this helps in reducing operating costs. We know, operators who perform welding operations are exposed to very harmful gases and work in risk-prone workspaces [71]. Cobots help human operators to avoid direct contact with hazardous environments and give priority to safety. Hence, accidents are prevented and loss of lives too [28]. Cobots help companies maintain high-level uniformity, improve quality, decrease errors, increase productivity and reduce wastage.
3.7.1. Case study: Sinouxland [73]
Sinouxland Fabricating is a company based in Rock Valley, Lowa, which provides custom fabrication services like assembly, welding, bending, and cutting. The main challenges faced by the company were concentrated in the welding department. It was hard for them to find skilled workers for welding operations, high cycle time, and operating costs. To overcome this, they introduced UR10e collaborative robots to perform arc welding operations. Due to these cobots, the cycle time was cut down to half, and the efficiency of production was increased. The outcomes from this case study were that cobots were introduced for welding processes, which significantly decreased cycle time and increased production effectiveness. Their use enables the business to boost productivity without needing to bring on more knowledgeable staff. By using less trained labour, the corporation was able to lower operational expenses. Cobots are an appealing alternative for businesses that may not have substantial programming skills because they are made to be simple to run and program.
3.8. Logistics and AMR
Logistics is a process of acquiring resources, storing goods, and moving them from the point of origin to the point of consumption using efficient transportation. Logistics is considered a sub-part of material handling and pick and place operations. Cobots used in logistics are mostly picked and place-oriented. They are used in large warehouses or fulfilment centers where various payloads are moved from point to point [74]-[76]. Stationary and mobile cobots, also known as autonomous mobile robots (AMR), are used to mobilize goods in these centers. According to a statistical report, 158 thousand logistic robots were sold worldwide in the year 2021. It has been forecasted that in the year 2022, this count will swell up to 207 thousand logistic robots worldwide [77]. It clearly states that the use of cobots in the logistics sector is expanding rapidly. Out of these cobots, the maximum was the mobile type. They help to increase productivity, do the task in minimum motion, and improve the work environment for the worker by making it safe. This is particularly true of AMRs, which can navigate dynamic settings, effectively locate and pick objects, more intelligently deliver these objects to human workers, and operate more quickly than manual picking and placing [78]. AMRs can carry heavy payloads as compared to stationary cobots. These types of cobots have a bright future and have great opportunities to make a difference in the logistics sector.
3.8.1. Case Study: NorthShore Care Supply [79]
NorthShore Care Supply is a company situated in Green Oaks, Illinois. It is a leading e-commerce supplier of high-absorbency diapers for adults. As the company was scaling every year, there was a need for automation to meet market demands. So, they introduced autonomous mobile robots from RBR50 company Waypoint Robotics to magnify the output. First, the workers use to move the material using manual push carts. After the introduction of AMRs, there was a subsequent increase in material movement. The order picking efficiency increased by three folds, and the outbound boxes per labor doubled with a 99.9 % accuracy rate. The operational efficiency of the company saw a rise of 25 to 50 %. The outcomes from this case study were that the NorthShore Care Supply company's operations were significantly more efficient after the introduction of autonomous mobile robots (AMRs), as measured by operational efficiency, order picking efficiency, and outgoing boxes per labour. This shows that utilizing cobots or AMRs in industrial settings can improve productivity, accuracy, and efficiency.
Fig. 13Cobots (AMRs) in Fulfilment centre [80]
![Cobots (AMRs) in Fulfilment centre [80]](https://static-01.extrica.com/articles/23238/23238-img13.jpg)
3.9. Technological advancements in collaborative robots [81], [82]
1) Machine learning (ML) and artificial intelligence (AI): Collaborative robots are getting cleverer, enabling them to carry out more difficult jobs. Robots may be taught to recognize items and comprehend their surroundings using AI and ML. They can now work with people more effectively and safely thanks to this.
2) Advanced Sensing: Collaborative robots come with a variety of sophisticated sensors, including cameras, force sensors, and proximity sensors. The robots can sense things and people in their area with the use of these sensors, which allows them to modify their movements accordingly.
3) Human-Robot Interaction: Collaborative robots are made to communicate with people in a way that feels instinctive and natural. Robots can be made to comprehend and comply with human orders using technologies like face, gesture, and speech recognition.
4) Cloud Computing: By connecting to the cloud, collaborative robots can access and share data with other robots and devices. This makes it possible for them to collaborate better and learn from one another.
5) 5G Networks: Collaborative robots can take advantage of the fast, low-latency connectivity that 5G networks provide. This makes it possible for them to interact in real time with other robots and gadgets, resulting in more effective and well-organized processes.
The following are some instances of collaborative robots that make use of these newest technologies [81], [82]:
1) Universal Robots UR16e: This cobot performs a range of tasks, including machine tending, material handling, and packaging, using cutting-edge sensors and AI.
2) ABB YuMi: This cobot is made to assist people in the assembly and handling of small parts. To detect and prevent collisions with people, it makes use of cutting-edge sensing and AI.
3) FANUC CRX: This cobot can weld, paint, and handle materials thanks to its sophisticated sensing and cloud computing capabilities.
4) KUKA LBR iiwa: This collaborative robot (cobot) assists humans in tasks like assembly and material handling by utilizing cutting-edge sensors and human-robot interaction technology.
4. Future of collaborative robots
It’s been a long time since it has been supposed that programming a robot is arduous. But the evolution of cobots helped to break this point of view. Due to this, the world expects this evolution and simplification to continue. Research is going on in building mobile applications which can be used to develop complex programs [83]. Many robot manufacturers are presently working on developing a robot that can be programmed by anyone with limited experience or training and doesn't have a hardcore programming background. Integration of cobots with Big Data and Artificial Intelligence will help them make their own decisions and work with negligible human interference. According to a report by World Robotics 2018 Industrial Robots, the most crucial challenge faced by robot technology is the continuous tooling required when using new materials. Since that report, there has been an introduction of a vast variety of gripper innovations that handle both hard and soft parts. Soft grippers, grippers using electro-adhesion, grippers controlled by fluid volume, etc have been the recent developments in gripper technology [84], [85]. Presently more work is going on improving the flexibility of grippers and how can changeover and retooling be refined. Future cobots are expected to be more interactive by understanding certain voice commands or hand gestures and decreasing downtime. Work is going on to improve embedded vision systems to increase the efficiency and accuracy of the gripper to effectively grasp the workpiece by identifying its location and orientation of the workpiece. Cobot technology is also being developed which will support unstructured environments [23]-[25]. This quantum leap would be a revolutionary step for the future of the manufacturing sector and further boost the viability of cobots in less structured workspaces.
5. Results and discussion
A literature survey of around 65 technical papers including research papers and review papers from various journals, conferences, publications, etc. was conducted for the study of applications of collaborative robots in manufacturing. The distribution of papers based on various applications and topics is represented using a pie chart. (Refer to Fig. 12).
Fig. 14Literature survey on applications of Cobots
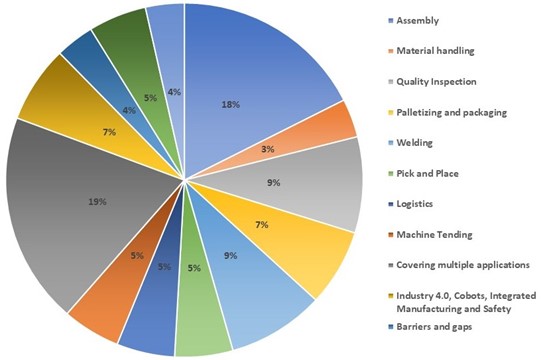
From Fig. 14, it is observed extensive research has been done in assembly (18 %), quality inspection (9 %), and welding (9 %) applications. Some papers had a glimpse of cobots, their history, and their involvement in integrated manufacturing (7 %). Next comes the palletizing (7 %) applications which have a moderate amount of research. Applications like pick and place, logistics, and machine tending have an equal amount of research done (5 %) followed by material handling and AMRs having a share of 4 % each. Finally, some papers covered multiple applications (19 %). It was observed that there were minimal papers that covered applications like welding, machine tending, and logistics.
Table 3 shows a list of various brands of collaborative robots comprising various cobot variants, their payload, reach, and the manufacturing applications for which they can be used.
After reviewing multiple applications of cobots, we can say that they are the future of modern-era manufacturing. They have proved advantageous for many manufacturing industries and helped them automate their facilities. By studying the various characteristics and factors of cobots we can determine the weightage of applications of cobots. Maximum weightage can be seen in material handling (92 %), assembly (88 %), and pick and place (72 %) applications. It is followed by palletizing (69 %), quality inspection (68 %), and machine tending (61 %) having intermediate weightage. Finally, welding (27 %) has the least weightage of the application of cobots. (Refer to Fig. 15 for more understanding).
Table 3Existing collaborative robots in the market for manufacturing applications
S.N. | Manufacturer | Product variant | Payload (Kg) | Reach (mm) | Application |
1 | Universal Robots [86] | UR3e | 3 | 500 | Assembly, Welding |
UR5e | 5 | 850 | Assembly, Machine Tending | ||
UR10e | 12.5 | 1300 | Material Handling, Welding | ||
UR16e | 16 | 900 | Palletizing, Material Removal | ||
UR20 | 20 | 1750 | Part Handling, Assembly, Welding | ||
2 | ABB [13] | YuMi Series | 0.5 | 559 | Vision Inspection, Part Handling, Assembly |
GoFa | 5 | 950 | Vision Inspection, Part Handling, Assembly | ||
SWIFTI | 11 | 1400 | Vision Inspection, Part Handling, Assembly | ||
3 | KUKA [10] | LBR iiay | 3-15 | 760-1300 | Material Handling, Assembly, Palletizing, Packaging, Inspection, Pick and Place |
LBR iiwa | 7-14 | 800-820 | Machining, Handling, Assembly, Appling, Painting, Palletizing, Packaging, Inspection | ||
4 | FANUC [12] | CR-4iA | 4 | 550 | Assembly, Machine Tending, Pick and Place, Palletizing, Packaging, Material Handling, Machining, Dispensing |
CR-7iA | 7 | 717 | Assembly, Machine Tending, Pick and Place, Palletizing, Packaging, Material Handling, Machining, Dispensing | ||
CR-7iA/L | 7 | 911 | Assembly, Machine Tending, Pick and Place, Palletizing, Packaging, Material Handling, Machining, Dispensing, Arc Welding | ||
CR-14iA/L | 14 | 911 | Assembly, Machine Tending, Pick and Place, Palletizing, Packaging, Material Handling, Machining, Dispensing | ||
CR-15iA | 15 | 1441 | Assembly, Machine Tending, Pick & Place, Palletizing, Packaging, Material Handling, Machining, Dispensing, Arc Welding | ||
CR-35iA & CR-35iB | 35 | 1813 | Assembly, Machine Tending, Pick and Place, Palletizing, Packaging, Material Handling, Machining, Dispensing | ||
5 | Yaskawa [17] | HC10DTP | 10 | 1200 | Assembly, Machine Tending, Material Handling, Pick & Place |
HC20DTP | 20 | 1700 | Assembly, Machine Tending, Material Handling, Pick & Place, Palletizing | ||
HC30PL | 30 | 1700 | Palletizing | ||
6 | Precise Automation [14] | PF3400 SCARA | 3 | 662 | Pick and Place |
PP100 CARTESIAN | 3 | 685 | Pick and Place | ||
PFDD6 & PFDD4 | 6-8 | 550-1420 | Mobile Applications | ||
7 | Techman Robot [15] | TM5-700 | 6 | 700 | Assembly, Machining, Material Handling, AMRs, Welding, Pick and Place |
TM5-900 | 4 | 900 | |||
TM12 | 12 | 1300 | |||
TM14 | 14 | 1100 | |||
TM16 | 16 | 900 | |||
TM20 | 20 | 1300 | |||
8 | AUBO Robotics [16] | AUBO-i3 | 3 | 625 | Pick and Place, Material Handling |
AUBO-i5 | 5 | 886.5 | AMRs, Material Handling | ||
AUBO-i10 | 10 | 1350 | Machining | ||
AUBO-i16 | 16 | 967.5 | Assembly | ||
9 | Rethink Robotics [11] | Sawyer | 4 | 1260 | Machining, Material Handling, Packaging, Inspection, Pick and Place |
10 | Doosan Robotics [18] | H- Series | 20-25 | 1500-1700 | Palletizing, Machine Tending, Material Handling, Welding, Pick, and Place |
M- Series | 6-15 | 900-1700 | Assembly, Machine Tending, Welding, Machining | ||
A- Series | 5-9 | 900-1200 | Machine Tending, Pick and Place, Packaging, Inspection, Machining, Assembly |
Fig. 15Literature available on Cobot applications
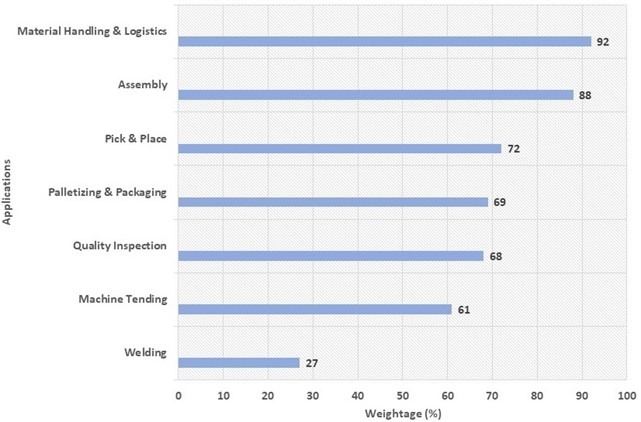
From Fig. 16, it is observed that FANUC is the manufacturer which shares the maximum market for the greatest number of variants of collaborative robots for assembly, palletizing, packaging, and machine tending applications i.e., 35 %. It is followed by Doosan Robotics with 14 %. Further, Yaskawa and Techman Robot have a 12 % share each. Lastly, Universal Robots has 10 %, KUKA has 8 %, ABB has 6 %, AUBO Robotics has 2 %, and Rethink Robotics has 2 % shares respectively. Precise Automation does not develop cobots for assembly, palletizing, packaging, and machine tending applications.
From Fig. 17, it is observed that FANUC and Techman Robot are the manufacturers which share the maximum market for the greatest number of variants of collaborative robots for Material Handling, Pick and Place, Logistics, and AMRs applications i.e., 21 %. They are followed by ABB and Precise Automation with 11 %. Further Universal Robots, KUKA, Yaskawa, AUBO Robotics, and Doosan Robotics have a 7 % share each. Lastly, Rethink Robotics has the least number of variants with a share of 4 %. Almost all manufacturers develop cobots for Material Handling, Pick and Place, Logistics, and AMRs.
From Fig. 18, it is observed that Techman Robot is the manufacturer which shares the maximum market for the greatest number of variants of collaborative robots for assembly, palletizing, packaging, and machine tending applications i.e., 30 %. It is followed by Universal Robots, ABB, and Doosan Robotics share 15 % each. Further, KUKA and FANUC have a 10 % share each. Lastly, Rethink Robotics has 5 %. Yaskawa, Precise Automation, and AUBO Robotics do not develop cobots for welding and quality inspection applications.
Fig. 16Number of cobot variants developed by various manufacturers for assembly, palletizing, and machine tending (In percentage)
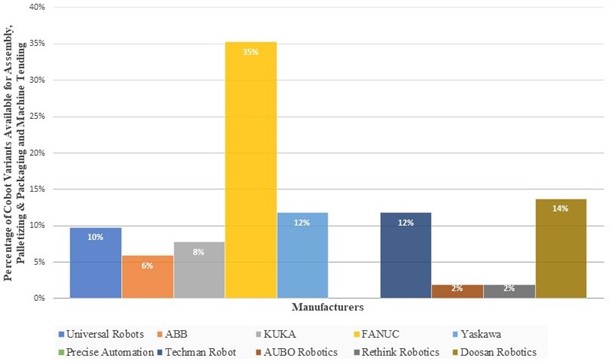
Fig. 17Number of cobot variants developed by various manufacturers for material handling, pick and place, logistics, and AMRs (In percentage)
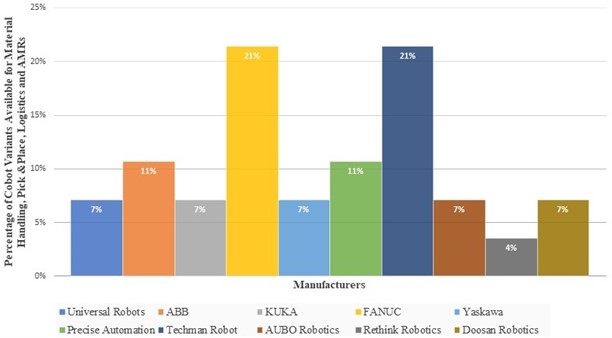
Fig. 18Number of cobot variants developed by various manufacturers for welding and quality inspection (In percentage)
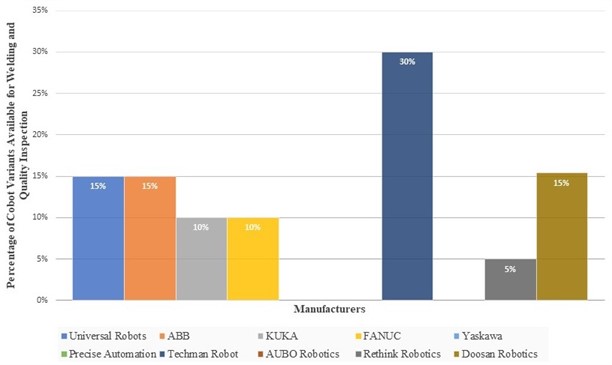
6. Conclusions
The main aim of the proposed investigation is to carry out a systematic study of applications of collaborative robots in the manufacturing sector. The findings of the proposed work are presented below:
1) The use of cobots in applications such as assembly, machine tending, pick and place, quality inspection, welding, palletizing, packaging, material handling, logistics, and AMR is discussed successfully.
2) A thorough analysis of the cobot variants currently on the market by multiple enterprises for various manufacturing applications is conducted based on factors like payload and reach.
3) Cobot versions for welding, machine tending, and quality inspection tasks are being developed by a very small number of businesses. In industries, the adoption of cobots for these tasks is even lower. The following are the causes for this:
4) Lack of precision: When compared to regular robots, cobots’ lack of precision is one of their main drawbacks in welding, machine tending, and quality inspection operations. Cobots make some accuracy and repeatability sacrifices for flexibility because they are made to work collaboratively and react to changes in the production environment. In applications where precise control is required to attain the desired quality and consistency of the finished result, this might be a considerable disadvantage.
5) Limited payload capacity: Because cobots often have smaller payload capacities than traditional robots, their applicability in tasks requiring heavy lifting or the manipulation of large objects may be constrained. This can be a particular problem when welding and machine tending activities take place since the cobot may be unable to handle the weight of the workpiece and the equipment.
6) Limited speed: Cobots have a limited speed range, which might be a drawback in applications requiring high throughput or quick cycle times. Cobots are often slower than standard robots. In welding and machine tending tasks, where speed can have a direct impact on productivity and efficiency, this can be a particular problem.
7) Cost: Compared to regular robots, cobots can be more expensive, especially when programming and additional safety features are needed to ensure their safe interaction with human operators. For businesses trying to automate their welding, machine tending, and quality inspection tasks, this may make them less desirable.
In the future, the work may be extended by considering the introduction of new technologies like AI, ML, 5G Networks, and Cloud Computing in collaborative robot technology. Further, how they are used in cobots, their advantages and disadvantages, and in what manufacturing applications they were used can be highlighted.
References
-
E. Matheson, R. Minto, E. G. G. Zampieri, M. Faccio, and G. Rosati, “Human-robot collaboration in manufacturing applications: a review,” Robotics, Vol. 8, No. 4, p. 100, Dec. 2019, https://doi.org/10.3390/robotics8040100
-
L. Wang, S. Liu, H. Liu, and X. V. Wang, “Overview of human-robot collaboration in manufacturing,” in Lecture Notes in Mechanical Engineering, pp. 15–58, 2020, https://doi.org/10.1007/978-3-030-46212-3_2
-
V. Villani, F. Pini, F. Leali, and C. Secchi, “Survey on human-robot collaboration in industrial settings: Safety, intuitive interfaces and applications,” Mechatronics, Vol. 55, pp. 248–266, Nov. 2018, https://doi.org/10.1016/j.mechatronics.2018.02.009
-
S. Hjorth and D. Chrysostomou, “Human-robot collaboration in industrial environments: A literature review on non-destructive disassembly,” Robotics and Computer-Integrated Manufacturing, Vol. 73, p. 102208, Feb. 2022, https://doi.org/10.1016/j.rcim.2021.102208
-
Z. M. Bi, C. Luo, Z. Miao, B. Zhang, W. J. Zhang, and L. Wang, “Safety assurance mechanisms of collaborative robotic systems in manufacturing,” Robotics and Computer-Integrated Manufacturing, Vol. 67, p. 102022, Feb. 2021, https://doi.org/10.1016/j.rcim.2020.102022
-
“Collaboration, dialogue and human-robot interaction,” in Robotics Research. Springer Tracts in Advanced Robotics, Vol. 6, Springer, 2003, https://doi.org/10.1007/3-540-36460-9_17
-
D. Mukherjee, K. Gupta, L. H. Chang, and H. Najjaran, “A survey of robot learning strategies for human-robot collaboration in industrial settings,” Robotics and Computer-Integrated Manufacturing, Vol. 73, p. 102231, Feb. 2022, https://doi.org/10.1016/j.rcim.2021.102231
-
Prafulla V. and Balu Krishnakumar M., “Application of cobots in automotive assembly line,” 2018.
-
A. Hentout, M. Aouache, A. Maoudj, and I. Akli, “Human-robot interaction in industrial collaborative robotics: a literature review of the decade 2008-2017,” Advanced Robotics, Vol. 33, No. 15-16, pp. 764–799, Aug. 2019, https://doi.org/10.1080/01691864.2019.1636714
-
“Cobots: the intelligent robot as a colleague.” KUKA. https://www.kuka.com/en-in/future-production/human-robot-collaboration/cobots#:~:text=cobots%20are%20collaborative%20or%20collaborating,never%20injure%20its%20human%20colleagues
-
“Rethink Robotics Meets German Engineering.” Rethink Robotics, https://www.rethinkrobotics.com/
-
“CR and CRX of Collaborative Robot Models.” Fanuc, https://www.fanucamerica.com/products/robots/series/collaborative-robot#:~:text=fanuc
-
“Collaborative Robots.” ABB, https://new.abb.com/products/robotics/robots/collaborative-robots#:~:text=our%20collaborative%20robots%20are%20made,step%20of%20your%20automation%20journey
-
“What is a Collaborative Robot,” https://preciseautomation.com/collaborative.html
-
“Techman AI Cobot.” TM robot, https://www.tm-robot.com/en/
-
“AUBO Family.” AUBO, https://www.aubo-cobot.com/public/index4
-
“HC Series.” Yaskawa, https://www.motoman.com/en-us/products/robots/collaborative/hc-series
-
“H Series.” Doosan Robotics, https://www.doosanrobotics.com/en/products/series
-
“Collaborative Robotics.” OSHA, https://www.osha.gov/collaborative-robotics
-
“Why Collaborative Robots are the Future of Manufacturing.” Forbes, https://www.forbes.com/sites/forbestechcouncil/2021/04/12/why-collaborative-robots-are-the-future-of-manufacturing/?sh=197d2fbb1ed3
-
“Collaborative Robots.” International Federation of Robotics, https://ifr.org/collaborative-robots
-
“Collaborative Robots: Improving Productivity in Manufacturing and Logistics.” ABI Research, https://www.abiresearch.com/whitepaper/collaborative-robots-improving-productivity-manufacturing-and-logistics/
-
R. Bloss, “Collaborative robots are rapidly providing major improvements in productivity, safety, programing ease, portability and cost while addressing many new applications,” Industrial Robot: An International Journal, Vol. 43, No. 5, pp. 463–468, Aug. 2016, https://doi.org/10.1108/ir-05-2016-0148
-
A. Dimitrokalli, G.-C. Vosniakos, D. Nathanael, and E. Matsas, “On the assessment of human-robot collaboration in mechanical product assembly by use of virtual reality,” Procedia Manufacturing, Vol. 51, pp. 627–634, 2020, https://doi.org/10.1016/j.promfg.2020.10.088
-
R. Galin, R. Meshcheryakov, S. Kamesheva, and A. Samoshina, “Cobots and the benefits of their implementation in intelligent manufacturing,” in IOP Conference Series: Materials Science and Engineering, Vol. 862, No. 3, p. 032075, May 2020, https://doi.org/10.1088/1757-899x/862/3/032075
-
“Size of the collaborative (cobot) robot market worldwide in 2020 and 2021, with a forecast for 2022 to 2030.” Statista, https://www.statista.com/statistics/748234/global-market-size-collaborative-robots.
-
F. Gil-Vilda, A. Sune, J. A. Yagüe-Fabra, C. Crespo, and H. Serrano, “Integration of a collaborative robot in a U-shaped production line: a real case study,” Procedia Manufacturing, Vol. 13, pp. 109–115, 2017, https://doi.org/10.1016/j.promfg.2017.09.015
-
S. Vojić, “Applications of collaborative industrial robots.,” Machines, Technologies, Materials, Vol. 14, No. 3, pp. 96–99, 2020.
-
Fast-Berglund, F. Palmkvist, P. Nyqvist, S. Ekered, and M. Åkerman, “Evaluating cobots for final assembly,” Procedia CIRP, Vol. 44, pp. 175–180, 2016, https://doi.org/10.1016/j.procir.2016.02.114
-
M. Safeea, P. Neto, and R. Béarée, “The third hand, cobots assisted precise assembly,” in Towards Autonomous Robotic Systems, pp. 454–457, 2019, https://doi.org/10.1007/978-3-030-25332-5_39
-
Y. Cohen, S. Shoval, and M. Faccio, “Strategic view on cobot deployment in assembly 4.0 systems,” IFAC-PapersOnLine, Vol. 52, No. 13, pp. 1519–1524, 2019, https://doi.org/10.1016/j.ifacol.2019.11.415
-
R. Calvo and P. Gil, “Evaluation of collaborative robot sustainable integration in manufacturing assembly by using process time savings,” Materials, Vol. 15, No. 2, p. 611, Jan. 2022, https://doi.org/10.3390/ma15020611
-
F. Rossi et al., “Effective integration of Cobots and additive manufacturing for reconfigurable assembly solutions of biomedical products,” International Journal on Interactive Design and Manufacturing (IJIDeM), Vol. 14, No. 3, pp. 1085–1089, Sep. 2020, https://doi.org/10.1007/s12008-020-00682-9
-
C. J. Conti, A. S. Varde, and W. Wang, “Robot action planning by commonsense knowledge in human-robot collaborative tasks,” in IEEE International IOT, Electronics and Mechatronics Conference (IEMTRONICS), Sep. 2020, https://doi.org/10.1109/iemtronics51293.2020.9216410
-
L. Wang et al., “Symbiotic human-robot collaborative assembly,” CIRP Annals, Vol. 68, No. 2, pp. 701–726, 2019, https://doi.org/10.1016/j.cirp.2019.05.002
-
A. A. Malik and A. Bilberg, “Collaborative robots in assembly: A practical approach for tasks distribution,” Procedia CIRP, Vol. 81, pp. 665–670, 2019, https://doi.org/10.1016/j.procir.2019.03.173
-
Akella et al., “Cobots for the automobile assembly line,” in Proceedings 1999 IEEE International Conference on Robotics and Automation, 1999, https://doi.org/10.1109/robot.1999.770061
-
“The new world of automotive manufacturing: cobots optimize quality, output and ROI for OEMs and suppliers,” https://www.google.com/imgres?imgurl=https://www.universal-robots.com/media/1811283/automotive-manufacturing-cobots.jpg?width%3D1000&imgrefurl=https://www.universal-robots.com/blog/the-new-world-of-automotive-manufacturing-cobots-optimize-quality-output-and-roi-for-oems-and-suppliers/&h=668&w=1000&tbnid=Xbk9c9J-0HZjwM&tbnh=183&tbnw=275&usg=AI4_-kTiwnzkTdvWh9jeKL2t9LmuZgHg8A&vet=1&docid=fW7_mnuLuIRA-M
-
“11 Cobots Assemble Fiat 500 electric car,” https://www.cobottrends.com/11-cobots-assemble-fiat-500-electric-car/
-
N. M. Gomes, F. N. Martins, J. Lima, and H. Wörtche, “Reinforcement learning for collaborative robots pick-and-place applications: a case study,” Automation, Vol. 3, No. 1, pp. 223–241, Mar. 2022, https://doi.org/10.3390/automation3010011
-
R. Accorsi et al., “An application of collaborative robots in a food production facility,” Procedia Manufacturing, Vol. 38, pp. 341–348, 2019, https://doi.org/10.1016/j.promfg.2020.01.044
-
F. Coelho, S. Relvas, and A. P. Barbosa-Povoa, “Simulation of an order picking system in a manufacturing supermarket using collaborative robots,” in 32nd Conference on Modelling and Simulation, May 2018, https://doi.org/10.7148/2018-0083
-
Lakshmanan, S., Chandravadhana, and S., “Collaborative robots for industries,” International Research Journal in Global Engineering and Sciences, Vol. 4, No. 3, pp. 144–150, 2019.
-
“Pick and place robots offer high speed and precision.” Association for Advancing Automation, https://www.automate.org/a3-content/collaborative-robots-pick-and-place
-
“6 novel applications for collaborative robots.” Collaborative Robotics Trends, https://www.cobottrends.com/6-novel-applications-for-collaborative-robots/
-
A. Baldassarri, G. Innero, R. Di Leva, G. Palli, and M. Carricato, “Development of a mobile robotized system for palletizing applications,” in 2020 25th IEEE International Conference on Emerging Technologies and Factory Automation (ETFA), Sep. 2020, https://doi.org/10.1109/etfa46521.2020.9212124
-
E. Lamon, M. Leonori, W. Kim, and A. Ajoudani, “Towards an intelligent collaborative robotic system for mixed case palletizing,” in 2020 IEEE International Conference on Robotics and Automation (ICRA), May 2020, https://doi.org/10.1109/icra40945.2020.9196850
-
T. Salmi, J. M. Ahola, T. Heikkilä, P. Kilpeläinen, and T. Malm, “Human-robot collaboration and sensor-based robots in industrial applications and construction,” Springer Series in Adaptive Environments, pp. 25–52, 2018, https://doi.org/10.1007/978-3-319-70866-9_2
-
Y.-J. Chuang, H. Chang, Y.-T. Sun, and T.-T. Tsung, “Stick-slip in hand guidance of palletizing robot as collaborative robot,” International Journal of Advanced Robotic Systems, Vol. 19, No. 5, p. 172988062211311, Sep. 2022, https://doi.org/10.1177/17298806221131138
-
“How a box manufacturer tackled labor issues with robotics.” Collaborative robotics trends, https://www.cobottrends.com/how-a-box-manufacturer-alliora-tackled-labor-issues-with-robotics/
-
“Adaptation, Business Continuity and Cobots: Packaging and Palletizing”, https://www.google.com/imgres?imgurl=https://blog.universal-robots.com/hubfs/HQ%2520Images/Blog/2020/week%252030/Packaging%2520and%2520palletizing.jpg&imgrefurl=https://www.universal-robots.com/blog/adaptation-business-continuity-cobots-packaging-and-palletizing/&h=675&w=1200&tbnid=dXtHliy6UOZPsM&tbnh=168&tbnw=300&usg=AI4_-kQuuT8RvoKZpbXplk6ztK9mmiTFFA&vet=1&docid=MipJaoO_ixhy5M
-
F. Sherwani, M. M. Asad, and B. S. K. K. Ibrahim, “Collaborative robots and industrial revolution 4.0 (IR 4.0),” in International Conference on Emerging Trends in Smart Technologies (ICETST), Mar. 2020, https://doi.org/10.1109/icetst49965.2020.9080724
-
C. Byner, B. Matthias, and H. Ding, “Dynamic speed and separation monitoring for collaborative robot applications – Concepts and performance,” Robotics and Computer-Integrated Manufacturing, Vol. 58, pp. 239–252, Aug. 2019, https://doi.org/10.1016/j.rcim.2018.11.002
-
A. Cesta, A. Orlandini, G. Bernardi, and A. Umbrico, “Towards a planning-based framework for symbiotic human-robot collaboration,” in IEEE 21st International Conference on Emerging Technologies and Factory Automation (ETFA), pp. 1–8, Sep. 2016, https://doi.org/10.1109/etfa.2016.7733585
-
“Universal Robots Launches First Virtual Expo Focused on Automating Machine Tending Tasks with Collaborative Robots,” https://www.google.com/imgres?imgurl=https://www.automation.com/getmedia/9c202c91-265d-498b-af27-a4e80c580d11/universal-robots-news-feb-15-2021-web.png?width%3d500%26height%3d313%26ext%3d.png&imgrefurl=https://www.automation.com/en-us/articles/february-2021/universal-robots-first-virtual-expo-machine-scobots&h=313&w=500&tbnid=cp72phfuppkobm&tbnh=178&tbnw=284&usg=ai4_-ksignidyvh23lz95h6whahisyhdia&vet=1&docid=tkorucrx_etssm
-
“ActiNav enables lights-out machine tending at family-owned manufacturer.” Collaborative Robotics Trends, https://www.cobottrends.com/actinav-enables-lights-out-machine-tending-at-family-owned-manufacturer/
-
P. Magalhaes and N. Ferreira, “Inspection application in an industrial environment with collaborative robots,” Automation, Vol. 3, No. 2, pp. 258–268, Apr. 2022, https://doi.org/10.3390/automation3020013
-
H. Cai and Y. Mostofi, “Human-robot collaborative site inspection under resource constraints,” IEEE Transactions on Robotics, Vol. 35, No. 1, pp. 200–215, Feb. 2019, https://doi.org/10.1109/tro.2018.2875389
-
H. Karami, K. Darvish, and F. Mastrogiovanni, “A task allocation approach for human-robot collaboration in product defects inspection scenarios,” in 29th IEEE International Conference on Robot and Human Interactive Communication (RO-MAN), Aug. 2020, https://doi.org/10.1109/ro-man47096.2020.9223455
-
Donadio et al., “Human-robot collaboration to perform aircraft inspection in working environment.,” in Proceedings of 5th International Conference on Machine Control and Guidance, 2016.
-
T. Brito, J. Queiroz, L. Piardi, L. A. Fernandes, J. Lima, and P. Leitão, “A machine learning approach for collaborative robot smart manufacturing inspection for quality control systems,” Procedia Manufacturing, Vol. 51, pp. 11–18, 2020, https://doi.org/10.1016/j.promfg.2020.10.003
-
“Quality Testing and Inspection with a Cobot.”. https://www.google.com/imgres?imgurl=https://wiredworkers.io/wp-content/uploads/2022/03/chip-testing-thumbnail-e1646838731278.png&imgrefurl=https://wiredworkers.io/cobot-applications/quality-testing-and-inspection-with-a-cobot/&h=1078&w=1701&tbnid=m27d0bxecj6vfm&tbnh=179&tbnw=282&usg=ai4_-kskxqqsgf6mte021-qm-a0sgu6xwg&vet=1&docid=eycbs_3liu1u7m
-
“UR3 cobot automates quality testing at Koyo Electronics.” Collaborative Robotics Trends. https://www.cobottrends.com/ur3-cobot-automates-quality-inspection-koyo/
-
M. Peshkin et al., “Cobots in materials handling,” Northwestern University, Evanston, 2000.
-
“Palletizer,” https://d2n4wb9orp1vta.cloudfront.net/cms/brand/pt/2020-pt/pt0420cobots-proco-palletizer.jpg;maxwidth=720
-
“Whirpool factory uses 3 AMRs to optimize intralogistics.” Collaborative Robotics Trends, https://www.cobottrends.com/whirlpool-factory-amrs-optimize-intralogistics/
-
D. Antonelli and S. Astanin, “Qualification of a collaborative human-robot welding cell,” Procedia CIRP, Vol. 41, pp. 352–357, 2016, https://doi.org/10.1016/j.procir.2015.12.036
-
M. Tannous et al., “Haptic-based touch detection for collaborative robots in welding applications,” Robotics and Computer-Integrated Manufacturing, Vol. 64, p. 101952, Aug. 2020, https://doi.org/10.1016/j.rcim.2020.101952
-
P. Francesco and G. G. Paolo, “AURA: an example of collaborative robot for automotive and general industry applications,” Procedia Manufacturing, Vol. 11, pp. 338–345, 2017, https://doi.org/10.1016/j.promfg.2017.07.116
-
R. Müller, M. Vette, and A. Geenen, “Skill-based dynamic task allocation in human-robot-cooperation with the example of welding application,” Procedia Manufacturing, Vol. 11, pp. 13–21, 2017, https://doi.org/10.1016/j.promfg.2017.07.113
-
Ranoj Maharjan, “Semi-Automatic Robot Pipe Welding System,” 2019.
-
“Maximize Your Investment in a Welding Cobot,” https://www.google.com/imgres?imgurl=https://www.fabricatingandmetalworking.com/wp-content/uploads/2021/01/resized-hc10xp_thermal_ppe.jpg&imgrefurl=https://www.fabricatingandmetalworking.com/2021/01/maximize-your-investment-in-a-welding-cobot/&h=325&w=455&tbnid=84bhwteoxusham&tbnh=190&tbnw=266&usg=ai4_-krgk0oj2efnud3twobt_vpbjey3qq&vet=1&docid=qk0b2zikdn6wom
-
“UR10e cobot cuts welding time in half at Sinouxland Fabricating.” Collaborative Robotics Trends, https://www.cobottrends.com/ur10e-cobot-cuts-welding-time-in-half-siouxland-fabricating/
-
G. Atzeni, G. Vignali, L. Tebaldi, and E. Bottani, “A bibliometric analysis on collaborative robots in Logistics 4.0 environments,” Procedia Computer Science, Vol. 180, pp. 686–695, 2021, https://doi.org/10.1016/j.procs.2021.01.291
-
F. D. ’Souza, J. Costa, and J. N. Pires, “Development of a solution for adding a collaborative robot to an industrial AGV,” Industrial Robot: the International Journal of Robotics Research and Application, Vol. 47, No. 5, pp. 723–735, May 2020, https://doi.org/10.1108/ir-01-2020-0004
-
C. Cimini, A. Lagorio, D. Romero, S. Cavalieri, and J. Stahre, “Smart logistics and the logistics operator 4.0,” IFAC-PapersOnLine, Vol. 53, No. 2, pp. 10615–10620, 2020, https://doi.org/10.1016/j.ifacol.2020.12.2818
-
M. N. Zafar and J. C. Mohanta, “Methodology for path planning and optimization of mobile robots: a review,” Procedia Computer Science, Vol. 133, pp. 141–152, 2018, https://doi.org/10.1016/j.procs.2018.07.018
-
C. Lamini, S. Benhlima, and A. Elbekri, “Genetic algorithm based approach for autonomous mobile robot path planning,” Procedia Computer Science, Vol. 127, pp. 180–189, 2018, https://doi.org/10.1016/j.procs.2018.01.113
-
“AMRs, voice picking help e-commerce supplier double output.” Collaborative Robotics Trends, https://www.cobottrends.com/amrs-voice-picking-supplier-double-output/
-
“How XPO logistics uses robots to meet e-commerce demand,” https://www.google.com/imgres?imgurl=https://www.roboticsbusinessreview.com/wp-content/uploads/2019/10/xpo-logistics-cobots-picking.jpg&imgrefurl=https://www.roboticsbusinessreview.com/supply-chain/how-xpo-logistics-uses-robots-to-meet-e-commerce-demand/&h=650&w=1102&tbnid=sszqnyxrcnhwym&tbnh=172&tbnw=292&usg=ai4_-ktp8uzcxsugwmxv36ibjijfv2q7yg&vet=1&docid=stsqyacchlw-lm
-
“The latest technologies in collaborative robots.” Association for Advancing Automation, https://www.robotics.org/blog-article.cfm/the-latest-technologies-in-collaborative-robots/154
-
“The top 5 collaborative robots of 2021.” Robotics Business Review, https://www.roboticsbusinessreview.com/rbr50/top-5-collaborative-robots-of-2021/.
-
“Peek into the future of collaborative robots.” Genesis Systems, an IPG Photonics Company, https://www.genesis-systems.com/blog/peek-into-the-future-of-collaborative-robots
-
A. Borboni, K. V. V. Reddy, I. Elamvazuthi, M. S. Al-Quraishi, E. Natarajan, and S. S. Azhar Ali, “The expanding role of artificial intelligence in collaborative robots for industrial applications: a systematic review of recent works,” Machines, Vol. 11, No. 1, p. 111, Jan. 2023, https://doi.org/10.3390/machines11010111
-
S. Singh, M. Sajwan, G. Singh, A. K. Dixit, and A. Mehta, “Efficient surface detection for assisting collaborative robots,” Robotics and Autonomous Systems, Vol. 161, p. 104339, Mar. 2023, https://doi.org/10.1016/j.robot.2022.104339
-
“Universal robots – products.” Universal Robots, https://www.universal-robots.com/
Cited by
About this article
The authors have not disclosed any funding.
The datasets generated during and/or analyzed during the current study are available from the corresponding author on reasonable request.
Siddhant Kakade: conceptualization, data curation, analysis and interpretation of results, writing-original draft preparation. Bhumeshwar Patle: conceptualization, supervision, writing-review and editing. Ashish Umbarkar: conceptualization, supervision, writing-review and editing.
The authors declare that they have no conflict of interest.