Abstract
Mechanical progressions in different spaces have widened the application skyline of advanced mechanics to an unbelievable degree. Packaging and processing are some of the important aspects involved in the food industry. As the global population continues to rise with increasing consumer demand for a wider variety of food products, food manufacturing is exploring various strategies, techniques, and methods to meet the demand and adapt to the change. Industrial robots are being integrated into every part of the food manufacturing sector to increase production rates and improve food quality and hygiene. The introduction of more stringent legislation is forcing the food sector to update its production process. On the vigorous review of 50 papers, this paper provides a comprehensive review of robotics in food processing and investigates its analysis in terms of the level of automation applied in various food processing industries. The expectation of food-Robo in the food sectors and robotics with an optimized protocol to fetch various ingredients and shape them into a final product.
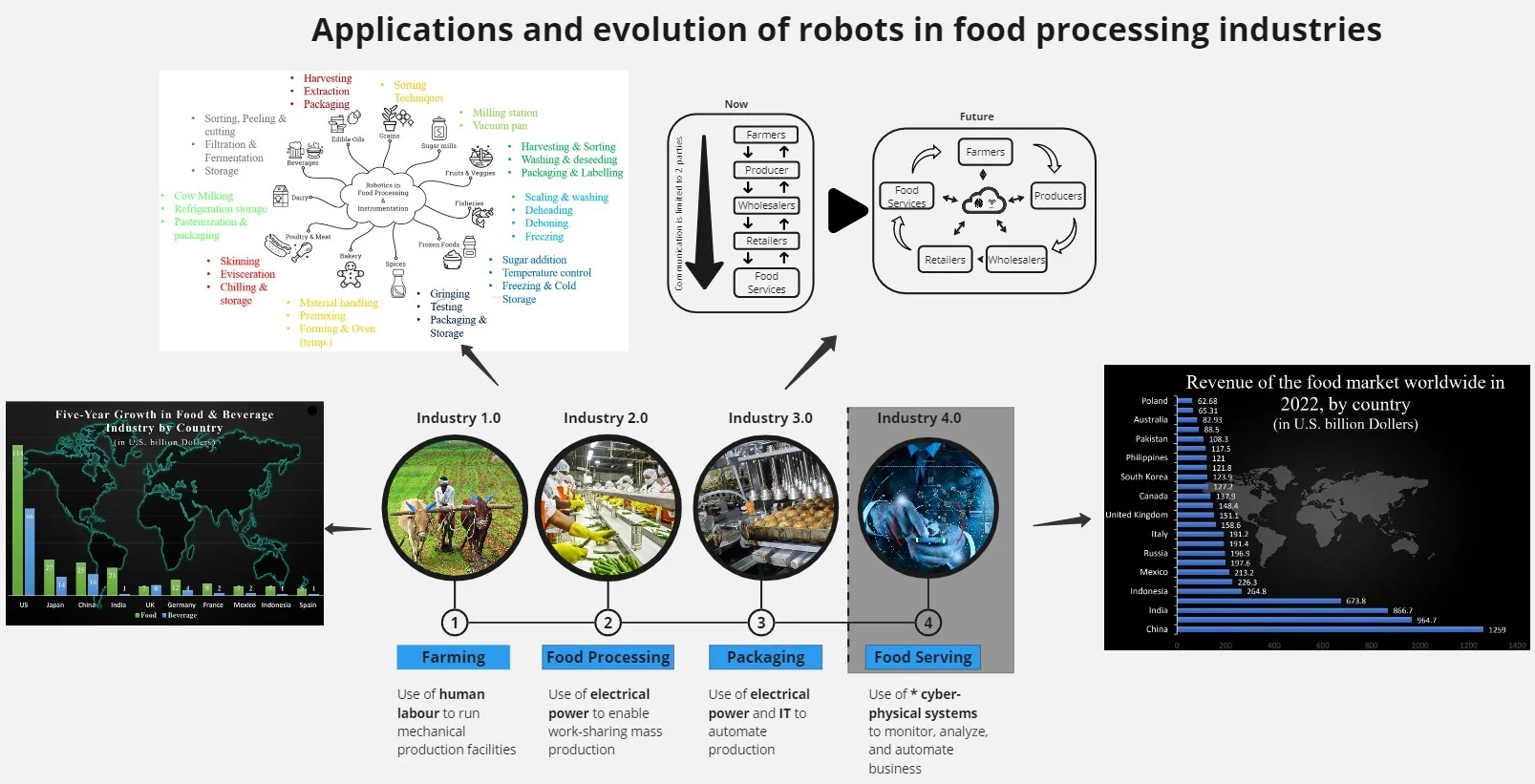
Highlights
- Prospects of Robots in food manufacturing world.
- Involvement of Robotics and automation in different food sectors.
- Development in Food industries due to Industry 4.0.
- Application of robotics in food economy.
1. Introduction
As one of the most established robotics applications is the food industry. Packaging provides protection from chemicals, biological changes, and physical modifications. Packaging tasks are easier to automate due to the uniformity of products at this point in the food supply chain. Technology, worker safety, maintainability, serviceability, reliability, ability, to integrate into packaging line, capital costs, floorspace, flexibility (changeover, material, etc.), energy usage, quality of outgoing packages, qualification (for food, pharmaceuticals, etc.) throughput efficiency, productivity, and ergonomics, at a minimum [1]. Keeping the societal scenario in mind, feeding the ever-growing population will be a major concern in the future. The increasing demands of consumers lead to atomization in this industrial sector. Although the food sector is somewhat slow to adopt robots, instead it is the fourth most automatable sector. Nowadays, food handling and packaging setups are limited in volume and output due to manual processing. Increasing the rate of production or multiplying the food variety is no longer a confrontation and worry, the rapid growth of sensitivity (allergies) and intolerance diet, which has increased the causes of illness, diseases like obesity, diabetes, appendix, heart and kidney problems, and many such more chronic diseases [2]. So, the solution for all these never-ending problems is the industrial revolution. Packaging provides total protection from the external environment, chemicals, biological and physical damages, or alterations to the packed food product. These all parameters of food safety, hygiene, environmental alterations, and the precision of the packaging can be only achieved by the intervention of robotics. The application of robots has deeply gladdened in every domain of food processing industries like edible oil extraction, Sugar mills, Beverages, Dairy products, Meat processing, fruits and vegetables, Bakery and etc. A variety of automated machinery can be found in modern food processing and packaging plants, including automated ovens, cutting and forming machines, sorting machines, mixers, and blenders, filling machines, wrapping machines, as well as robots working autonomously as highly automated automotive assembly line [3]. Fig. 1 is the same comparison and development of the industrial food supply chain present with the future industrial communication within the phases of the chain.
A rapid digital transformation is currently underway in the world economy, and that includes the food processing industry. Fig. 2 gives the estimate of the annual installation of robots worldwide in food industries. There are predictions that the market for industrial automation will reach $297 billion by 2026, with food and beverage applications accounting for 11 % of the market [4]. As a result of a survey conducted by the Association for Packaging and Processing Technologies, 94 % of food packaging operations are already using robotics. Robotics is being used by approximately one-third of food processing companies. Regarding food production, processing, supply, and consumption, India is the largest country in the world. Indian food market positioned sixth, with 70 % of deals, and fifth underway, utilization, and product [5]. This growth in the food industry has also experienced a benchmark in the overall growth in the country’s revenue. Fig. 3 shows the various revenues produced by the food sector worldwide.
Fig. 1Comparison of current food supply chain pattern with future Industry 4.0
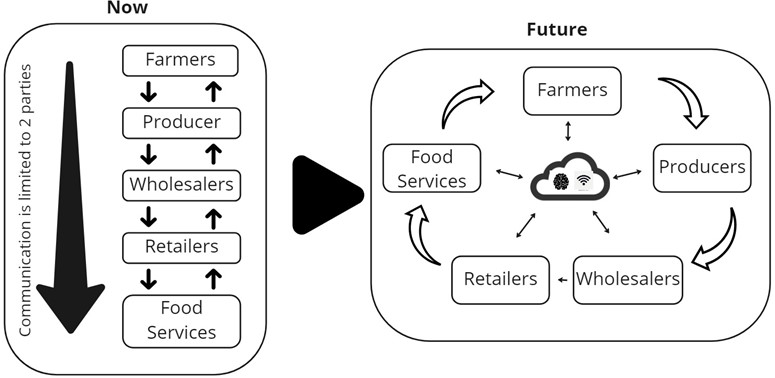
The overview of the Global Organization of Robots expresses that there was an offer of around 240,000 units overall in 2015 [6]. This addresses about an 8 % expansion in yearly development worldwide. Brazil has deals expanding by 33 % every year. Visual chart Fig. 4 expresses the yearly establishment of modern robots – around the world by various food sectors [8]. The utilization of Robots in food handling was principally for bundling and palletizing tasks. It is around 40 % of palletizing tasks and 26 % of food and refreshment bundling lines. In the year 1998, a flex picker robot was presented, upsetting the fast picking and setting of food things [7]. Food industry makers have revealed a 25 % increment in efficiency since the commitment of mechanical technology.
Fig. 2Annual installation of robots worldwide
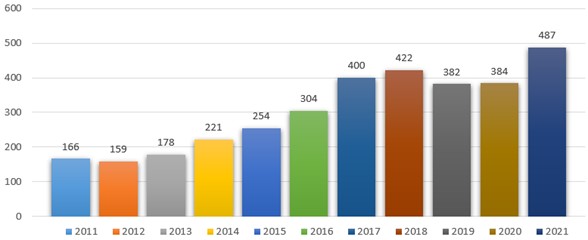
2. Automation in the food sector: A brief timeline
The evolution of robotics and automation in the field of the food sector has a great history. Their involvement in this sector is itself from the beginning that is from the sowing of seeds to the final packaging of the product [9]. But still, it did stop there nowadays they are even in the supply chain and warehouse management. Table 1. Gives the development of robotics in the food chain and its various applications in this sector. Robots have a wide application in any manufacturing industry, from sowing seeds, irrigation, and harvesting the yield to the processing of the food product till packaging and at the end storage in warehouses [10]. In present industries, they perform operations like Pick and Place, Palletizing, deplaning, Denesting, boxing, and warehousing [11]. Fig. 5 classifies the application of robotic operations in the food industry. After the industrial automation industries like Automobile, Manufacturing, Health care, Medical Science, Biotechnology, Mining, Art, and Craft, etc. but also there was, there the Food industry [12]. Many food companies made their stand and had a great contribution to the global economy. Top food processing companies like Nestle, Sysco Corporation, JBS, George Weston, Tyson Foods, Bunge, Mondelez, and much more supply their products worldwide, Fig. 6.
Table 1Robots and the latest development in the food chain in 2021
Description | Important features | Type of industry |
Robotic sending attachment to a tractor | Identify the soil properties for the seed best grow | Crop Fields (Food Industry) |
Cobots | Disinfect cows’ udders without affecting humans or animals, cow milking, and fetching eggs from the hen pen | Dairy and poultry farms, Food Production, packaging, and Palletizing. |
Vision guided robots | Color sorting, shape, or size and the improved gripper technology can assist in delicate products for example pizza production and biscuits | Bakery, and Snacks |
Contemporary robotics | Packaging robots’ tasks: open, fill, pack, seal, and label | Bulk Food Production |
Delivery robot | Four shelves for placing items can deliver items automatically and collaborate with other robots | Restaurants and Hotels |
Fig. 3Revenue of the food market worldwide by countries (in U.S. billion Dollars)
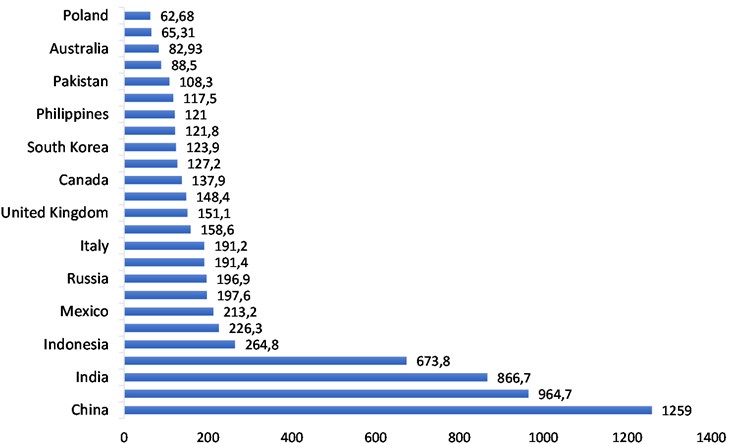
Fig. 4Production in the food sector
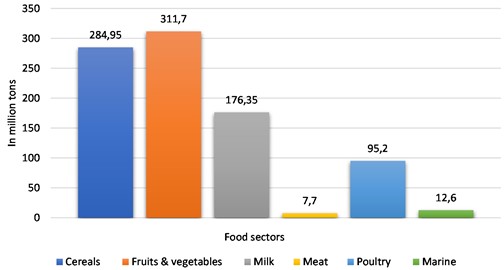
Fig. 5Applications of robots in food industries
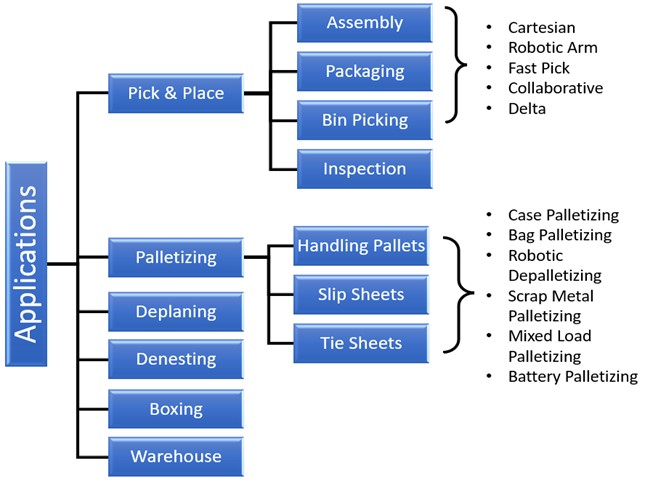
Fig. 6Top Indian food processing MNCs
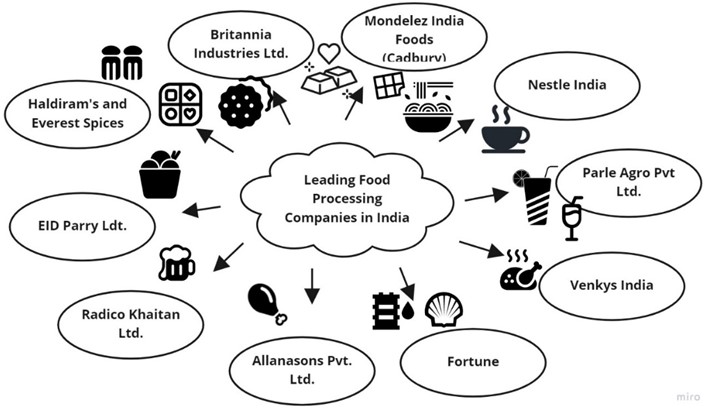
3. Major domains contributed.
The world’s food sector is divided into different domains like food grains oils, beverages, dairy, Fruit and vegetables, Poultry and meat processing, seafood (fisheries), bakery, frozen foods, and Spices. See Fig. 7.
Fig. 7Domains of the food sector
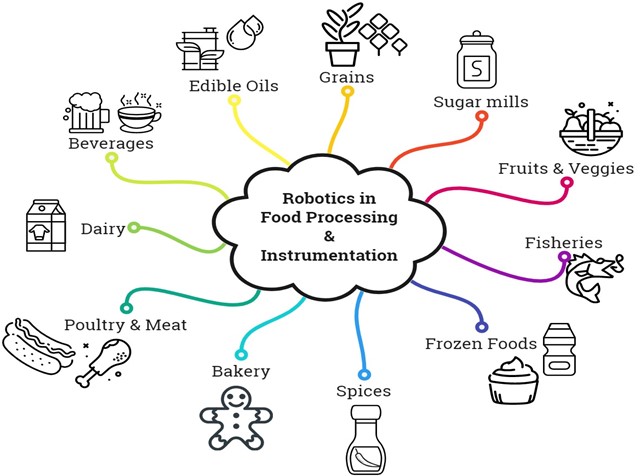
3.1. Grains
The demand for grains, flour, wet-milled corn products, and processed soybeans has taken in some other direction since 1972. There was a rise from 110 to 140 pounds of wheat flour from the year 1972 to 1992 (World Agricultural Supply and Demand Estimates, USDA). It lifted the domestic production to nearly 800 million bushels of wheat. These numbers encouraged grain processing companies [13]. Grain processing comprises different operations like the elevator process, drying process, preparation process, oil extraction, milling process, refining, loadout, packaging, material handling, and warehouse storage process [14]. The automation is mainly in oilseeds processing and refining, wet and dry grain milling. Fig. 8 presents the overall flow process of grain processing. The job of advanced mechanics application in this area is in grain arranging. The essential job of arranging is for item quality and security. Arranging grains like rice, wheat, jawar or bajra requires handling numerous tons each hour (t/hr) in nonstop cycles [15]. This arranging of such a mass amount is just made practical by utilizing a mechanized Optical Arranging strategy. An optical arranging machine naturally distinguishes the defectives and eliminates them. The deformities incorporate pollutants, for example, stones, glasses, bugs, shell pieces, spoiled items, and flawed, stained, or is-moulded items. The evacuation of imperfections as far as possible is important to keep up with its grade or quality standard. The optical arranging machine is incorporated by either cameras or leasers for ID of imperfections and commonly uses air ejectors for the expulsion of deformities. Additionally, the air discharge is non-contact (i.e., clean) and produces high paces of handling (i.e., high limit) [16]. The schematic chart of machine parts is displayed in Fig. 9.
Fig. 8Grains processing
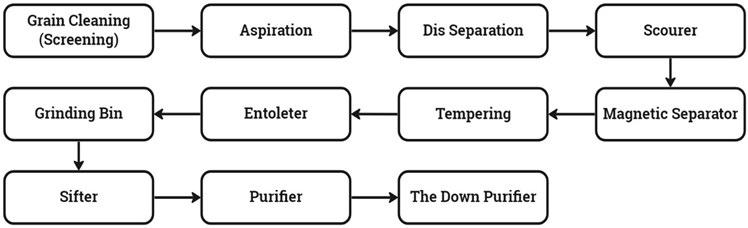
Fig. 9A schematic diagram of sorting machine components [15]
![A schematic diagram of sorting machine components [15]](https://static-01.extrica.com/articles/23209/23209-img9.jpg)
3.2. Advancement
Today, high-resolution line scan CCD array cameras are used for the identification of minute spot defects. Highly specialized hardware of the image processor is embedded with high-performance DSP chips or FPGA chips. The amount of computational processing power gradually increases exponentially according to the new generation of chips. This increased computational power has enabled the realization of sophisticated algorithms in optical sorting machines. This upgraded the machine for locating more smaller defects in grains against pecks (insect bites) or discolored yellow grains. Fig. 10(a), (b), and (c) [17] show the sorting of rice samples.
Fig. 10Sorting of rice samples
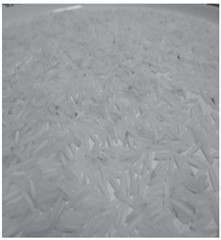
a) Rice sort input
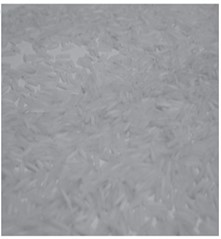
b) Accepted rice sample sort
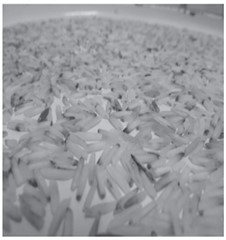
c) Rejected rice sor
3.3. Sugar mills
The absolute first synthetically refined sugar showed up on the scene in India around 2500 years quite a while back. From that point, the method spread east to China, and west to Persian and the early Islamic universes. Brazil stands first followed by India for sugar production. In the 13th century, a great revolution came in the sugar industry [17]. The automation and use of robots involved the harvesting of sugar cane the bag filling. Fig. 11 shows the process flow of sugar production.
Fig. 11Sugar processing
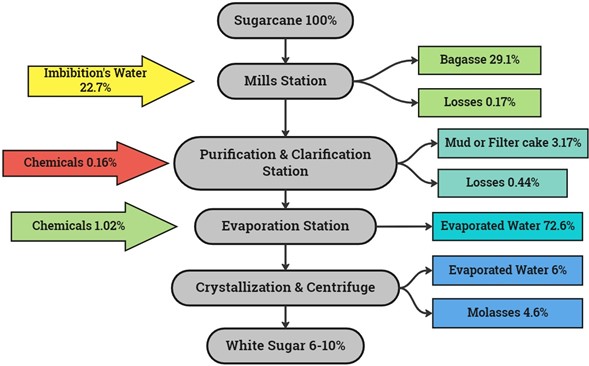
3.3.1. Automation for the Milling plant section
It is the station where the juice extraction from sticks happens. How much stick is being taken care of in-plant is shown by the load current of the stick switch, stick blades, and unigrator. The level of the stick chute of the principal factory controls the speed of the feed transport. By controlling the level of the principal stick chute, the plant works appropriately bringing about a consistent progression of material to the following factories [18]. In their factories, the degrees of stick chute change naturally as long as the general smashing rate control is dynamic, and speed is controlled appropriately. The speed of the factories relies just upon the set point stick pulverizing rate. The progression of the imbibition water is controlled to keep up with crude juice of steady Brix at the result of the processing plant area. Programmed control of imbibition water stream is by scaling of Brix estimation given before the bay of the crude juice and the thought of time postpone between the stick feed to the moment if response last factory [19]. The consequence of mechanization in this station is the steady progression of crude juice out of the factory area and furthermore crude juice of consistent brix.
3.3.2. Automation concept for a vacuum for pan or sugar boiling process
A vacuum skillet comprises a unit with obvious boundaries to the environmental elements and thus is reasonable for robotization. Robotization vacuum container is a direct result of about 33 % of the complete energy utilized inside the sugar handling plant. The principal necessity for a robotization control framework technique that empowers proficient computerization of the vacuum bunch dish is:
– Execution and unwavering quality in sugar applications.
– High accessibility.
– Low introductory venture because of the measured plan.
– Adaptability.
Vacuum pan automation is designed as an event-controlled sequential control. Variations in the juice quality and disturbance variables in the steam and vacuum control are considered [19]. The individual process steps are determined by the technology of the sugar boiling process. Manual control of steps like seeding, grinning, or boiling is difficult and requires a wide range of improvements for better product quality and energy saving. Automatically controlled and reproducible seeding and graining steps enable it to grow close to the physical possible maximum speed without generating undesired fine grains or false grains.
3.4. Beverages
It is known as one of the most important industries that satisfy daily human necessities and pleasure. The beverage industry is also known as the drink industry. The beverages mainly include alcoholic, non-alcoholic, and soft drinks, energy drinks, milk products, coffee, and tea-based products, and nutritional drinks. This industry gained importance and strengthened trends over the 20th century. There are lakhs of fruit types pineapples, oranges, passion fruit, etc. A fruit juice process begins with selecting and cleaning the raw material and then through the steps like extraction and filtration machine. The juice processing equipment varies according to the amount of water content in the fruit. The extraction process consists of cleaning, extraction, filtration, clarification, and mixing of fruit juices, and at last pasteurization, bottling, and packing. The quality of the syrup determines the taste of the juice. High-quality syrup is required for soft drinks, fruit juice, still drinks, flat or isotonic drinks, ice, tea, or alcoholic drinks [20]. Fig. 12 describes the in-plant processing of fruit juice.
Fig. 12Process flow of fruit juice extraction
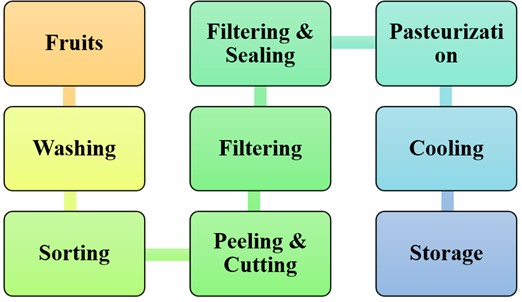
In the juice processing company, the in-line syrup room consists of sugar dissolution and pasteurizing of sugar solution, cooling, storage, receiving and preparing of bases and concentrates, and mixing the final product. One of the technologies is High-pressure processing (HPP) for the manufacturing of fruit juice, smoothies, and vegetable juice. This HPP unit is designed to increase the shelf-life of fresh juice without heat treatment while preserving its natural taste, color, vitamins, consistency, and nutritional values [21]. These fresh fruit juices are processed under cold conditions around 4 °C into HDPE or PET plastic bottles for keeping natural flavours and taste [22]. The bottles are loaded in a high-pressure vessel for up to less than a minute for a pressure intensifier and the pressure inside the vessel is released. This process is done to increase its shelf-life up to 3-4 weeks.
3.5. Fruits and vegetables
The absolute initially robotized evaluating activities for foods grown from the ground opened up quite a while back. Refinement of late innovations like machine vision and close-to-infrared (NIR) advances as well as mechatronics and PC advances have prompted clients for some sorts of agrarian items. The cycle is displayed in the following stream outline underneath. The absolute first innovation which has been created is the machine vision for assessing farming items. Which requires some exact difficult work like lighting, picture procurement (focal point, television camera, picture catch board, PC), and programming for picture securing and handling. Utilization of a variety of camera sensors in machine vision framework as there exists a wide assortment of varieties, which can give data about their properties and conditions. These varieties of cameras make red, green, and blue (R, G&B) part pictures. What's more, different cameras have been utilized in reviewing frameworks to gauge the size, variety, shape, and imperfections of foods grown from the ground and furthermore free for proof of germination in cell plate. The R part (red) predicts the development of the item through the G and B for chlorophyll and contaminated natural products or vegetables.
Bright (UV) light is utilized for sanitizer impacts and lessens the number of microbes, infections, and moles. The UV-A (light of frequency 315-400 nm) is used to energize fluorescent substances. These fluorescent pictures are utilized for distinguishing harmed natural products (oranges), x-beams of frequencies of 10-0.01nm, and frequencies of between 30 PH2 and 30 EH2 are successfully utilized in examining the inward characteristics of horticultural items. Another innovation of modernized Tomography (CT) a non-disastrous procedure for catching food pictures, to the perception of the interior designs or quality. X-beam CT has been utilized for inner quality assessment: development of green tomatoes, inner characteristics of peaches, abandons in melons and watermelons, stones in apricots, and estimation of the harder substance of apples [22].
Fig. 13 explains the brief process flow of fruits and vegetable processing. Other robot systems like pick and place robots with carefully designed and programmed robotic arms are used for multi-purpose and have an array of different grippers depending on the type of texture of fruits like grapes, peppers, apples, bananas, etc. Cutting and slicing robots are used for cutting ingredients to a particular thickness and length for the end-users. Is the recent development in this industry [23].
Fig. 13Fruits and vegies
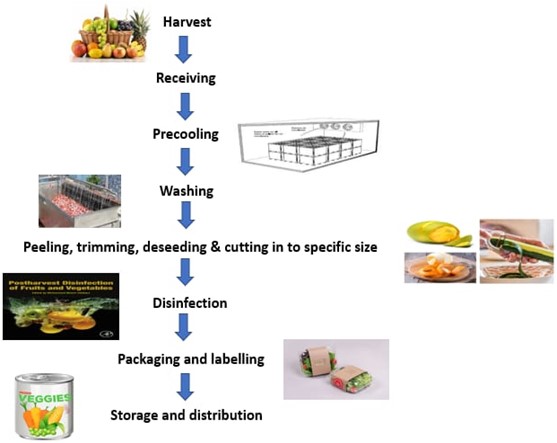
3.6. Seafood (Fisheries)
Seafood is one of the largest markets in the world. More than 75 % of the population consumes seafood, for its taste, nutrition and quality health. China is the largest producer of seafood products in the world, followed by India, Indonesia, Vietnam & Bangladesh. (Seafood Health Facts) [24]. Sea Food includes farmed freshwater and saltwater fish, molluscan shellfish, and crustaceans. The process of seafood processing is quite simple as mentioned in Fig. 14.
Fig. 14Fish processing
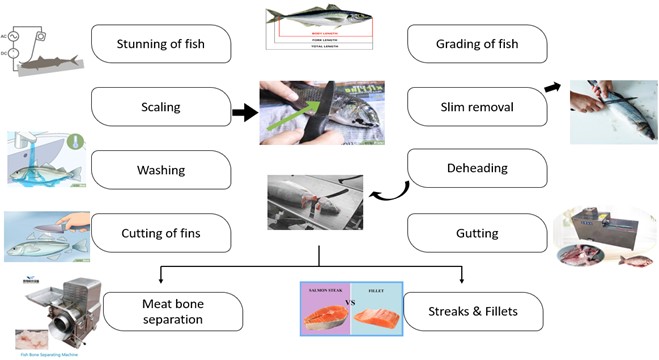
Because of the high factor both in shape, size, and design, a serious issue emerges for the improvement of sensor situations and controllers for dealing with fish items [24]. Different use of advanced mechanics and mechanization in fish businesses are utilized for fish butchering, fileting, and dividing.
3.6.1. Slaughtering operations
The alive wild-caught fish when bought onboard are killed by methods of gutting and de-heading immediately. For securing fish quality chilling or freezing wild-caught fish is very important. The previous old process of anesthetizing by the addition of carbon dioxide in the water tank has been ruled phased out. A new method of stunning, physical impact or electrical discharge is automatically performed. Simultaneously gill-arch cutting is done [25].
3.6.2. Sorting operations
Sorting operations the bases on different factors: Shape, size, fish type, external and internal characteristics, freshness, and quality-related factors. Research and study are being conducted on machine vision technology in fish sorting.
3.6.3. Fish filleting and other processing
After slaughtering filleting operations are carried out. Some pre-processing of descaling is done by various automated machines. A process called gutting which is the removal of insects from the fish belly is done before filleting [26]. Automatic feed for gutting machine and cleaning is done.
3.7. Poultry and meat processing
Poultry is also called the chicken industry. Meat and poultry products are an important source of nutrition for many people. Global demand for meat is growing over the past 50 years, with a triple increase in production. There are 340 million tonnes of meat production per year [27]. As the numbers are climbing industries have turned to robotics and automation for greater and faster production in a more efficient manner. Fig. 15 presents a rough process flow of Meat production.
Fig. 15Meat production
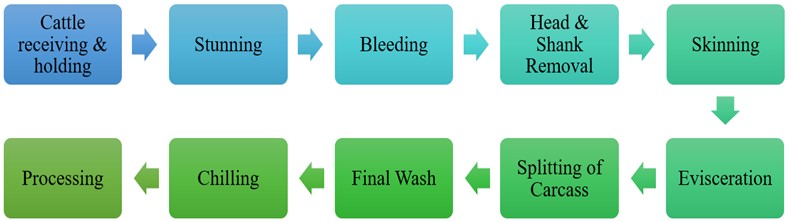
Present day handling plant, the underlying assignments are killing the birds and researching the birds. Birds are purchased online and should be clung to the shackle line by their feet. Exceptionally horrendous for laborers as well as a potential security risk because of residue, plumes, and excrement and hazardous because of pecks and scratches of birds. The following system is of chilling, deboning, and dividing the item by bundling it into plate gathers or packs/pockets. A mechanical arrangement was intended to recognize the position and direction (of the legs likewise whether the bosom up or bosom down) of the bird on a moving transport, with programming to follow the bird situate or getting a handle on and shackles second following.
Cutting and Managing corpses are the riskiest work for laborers. Robotized meat-handling robots consequently kill 360 cadavers each hour. Robots are additionally consolidated for handling hotdogs and deboning and cutting chickens. A new technology of X-ray robots detects bone location, length, and joints [27]. This system dismantles rather than cutting the meat off the bone, which prevents knife damage and improves final product quality and better yield.
3.8. Spices and chillies
Flavours are a food taste improver as well as a decent wellspring of nutrients B and C, calcium iron, and different cancer prevention agents. They are utilized in food as well as even in numerous restorative enterprises like corrective, drug, and fragrant perfumery. India is known for its flavours and world's biggest flavours maker. It produces around 10.7 million tons in the year 2020-21. India produces around 75 out of 109 assortments recorded by the Global Association for Normalization (ISO) [28]. The most widely recognized flavours created are cumin, pepper, turmeric, celery, stew, ginger, coriander, fennel, fenugreek, garlic, nutmeg and mace, curry powder, and zest oils.
As it adds taste to the food the quality and nourishment should be explored. We should accept an illustration of turmeric powder. The robotization utilized in this zest industry is PC vision strategy as a non-disastrous procedure for estimating the nature of food flavours. From old times, turmeric has been utilized as a flavour with antimicrobial capability all around the world.
3.9. Frozen foods
40 % of all food sources require refrigeration and chilling of items and just depend on a very much controlled cold chain to keep up with item quality and security to customers. Refrigeration is a strategy by which the pace of changes that happen in food is diminished. Fig. 16 is the freezing system of vegetable-based and organic product-based items. Robotization in this industry lies in absolute energy utilization for capacity, transportation, stacking, and dumping. Expulsion of intensity from the food item is simply by four fundamental components: radiation, conduction, convection, or vanishing. The significant pace of intensity misfortune is by transmitting huge temperature contrasts between the outer layer of the item and the fenced-in area. This happens in the underlying phases of chilling or freezing cooked or warm items. They require actual contact between food and the wellspring of refrigeration to extricate heat by conduction. Use of plate conduction coolers for quick cooling of packaged products and highly perishable products such as fish and meat blocks. Primarily the use of air systems for chilled and frozen foods, due to flexibility and ease of use.
Fig. 16Freezing process of vegetable and fruit-based food products
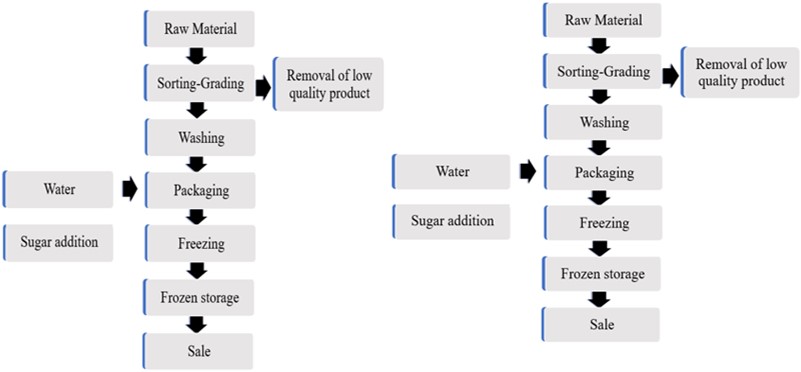
3.10. Dairy
Dairy products and milk are the delicious and daily needs of a person from a small child to an old age individual. This industry processes raw milk into an array of products including butter, ghee, condensed milk, dried milk powder, ice cream, etc., and produces many by-products including buttermilk, whey, ghee, and skim milk. Fig. 17 shows the dairy process and stages of various by-products produced during milk processing. With the increasing global demand for dairy products, there is a replacement of human operators with automated systems. Nowadays this technology is becoming more intelligent and affordable [29]. In milk processing, most fluids are transferred from one station to another by the pumps, but some solids need to be transferred also. The milk processing is done in a hazardous atmosphere (as in ice cream stored at –20 °C and in ice-cream hardening at –30 °C). this is the perfect area where robots are needed. One of the best applications of robots in dairy industries is the Automatic Milking System (AMS) or milk robots. This technology was available in 1992 but was introduced to the US in 2000. Robotics Milking is a voluntary milking system, which sets its own milking schedule. Initially, cows are trained with limited human interaction. An electronic tag is fitted to each cow on the robotics milking platform. This electronic tag helps the robot identify the cow. Where the ID is read and receives a feed reward customized to the level of production. The robots first clean the teats, attach the milk cups, and begin the milking process. When the milking is completed, the cups are disconnected. Thereafter that the robots are used in pasteurization, stirring, heating, and condensation where the by-products are produced [30]. The major application of robots is in the packaging as safety and hygiene is the most important concern for maintaining quality, taste, and long-life storage. Strict hygienic regulations are followed. The other applications of robots in dairy the industry is cheese packaging, cheese packaging, cheese slicing, curd slicing, etc. [31]. In cheese production, they stir curds, transfer cheese moulds, and turn, cut, portion, package, and palletize the cheese. Special gripper technology is used for cheese packs and placed on conveyors and cheese handling [32].
Fig. 17Dairy products processing
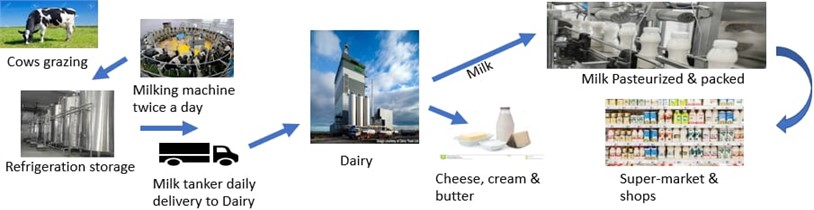
3.11. Bakery industry
One of the most loved or tasty products when we hear the word bakery is cake, cookies, and pastries. This industry is usually referred to as the grain-based food industry. Fig. 18 is the process flow of the bakery industry. This industry produces a wide range of products like bread, cake, cookies, pie, pastries, treats, pizza, burgers, buns, and many more.
Some of the areas where automation is done in this industry are.
– Material handling.
Conveyors are being used for loading or unloading materials. Pneumatic conveying for bulk handling and storage of raw material. Which are done with PLC-based pneumatic systems [33].
– Pre-mixing and mixing.
The PLC-based system includes weighing and batching raw material addition and transfer of liquids for mixing. Timers and software are connected to mixers to adjust mixing timing as per dough consistency.
Fig. 18Bakery processing
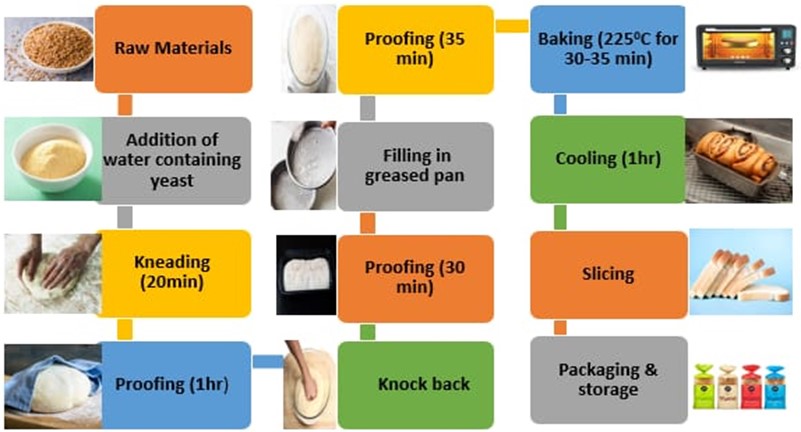
– Forming and laminating.
Mixture tipping is finished through tipping lifts. The speed of the Networks for the check roller can is expanded or diminished according to the prerequisite inside the baking time for bread rolls, treats, and saltine lines in a gathering.
– Oven.
There is full automation to control the Burner as per the requirement of heat inside the baking zone. With the use of temperature sensors or controllers loading of bread in the oven is automatic by conveyors with timing adjustment through PLC-based programs.
– Packing.
Full establishment of mechanization in bread kitchens is in the pressing segment. Taking care of framework rolls taking care of two pressing machines or bread loaders to cut bread and wrap. Even wrapping machines with activities like packs, prints, and seals are utilized for roll pressing, bread cutting, and pressing.
Robots are now used for cake and pastry decoration, burgers, and pizza topping and slicing. Automatic Storage and Retrieval system (AS/RS) robots are mainly used in ovens and warehouse storage. With the use of a PLC system, the complete process is real-time data monitoring [34].
4. Result and discussion
The impact of the industrial revolution has always transformed the food industry and the conceptualization of the food industry from industry 4.0, to 5.0 is now on the way to progression. As food industry involves many human elements and plays a vital role as a driver and the subject of environmental impacts. There is a rapid change in the innovation landscape, the demands of society, and challenges for pressure on natural resources, global warming, increasing population, and the ecosystem. Which has made high demand to adapt to Industry 5.0. Implementation of a health novelty plan can start with the labelling of the technology appropriate for food products, processes, and consideration of technical example shifts for a comprehensive advantage chain. The automation industry has an important role to play in providing the technology that will ensure that the sector continues to meet the demand for readily available, high-quality, and affordable food products. The urgent requirement is to simultaneously incorporate various technologies e.g., CPS, IoT, machine learning, cloud systems, cyber security, and autonomous robots in a collaborative environment to join hands for emerging solutions as proposed by Industry 4.0.
The automation system can be classified into two main groups:
– Centralized Control System (CCS). A system based on a powerful computer that controls and collects data for the entire factory floor.
– Distributed Control System (DCS). The factory is divided into small process sedation each with PLC or process computer attached.
Table 2 presents the list of the most used robotic manipulators in the food industry, their specifications, and their handling capacity.
4.1. Impact of Industry 4.0 on food industries
Concepts of Industry 4.0 have exploited the processing operations through the concepts like monitoring, traceability, improvement in safety and control of food quality, automation, and manufacturing with training. The use of IoT technology for sensory prediction and consumer preferences reduces loss, and waste and saves resources, energy, and most important time [49]. IoT components and digitalization tools have now been used for various processes, dairy production, and mostly to agricultural production. The use of multi-sensor technology in production like ultraviolet fluorescence imaging, solenoid actuators, infrared detection, metal detection and sorting, acoustic sensors, etc. helps in fault detection and made the entire process quick and fast decision-making. These sensory networking and data analytics tools have been used to improve business productivity, manufacturing sustainability, and the human-centricity of the digital transfer of data and information [50]. Fig. 19 shows the evolution of Industry 1.0 to Industry 4.0. Cyber-Physical Systems (CPSs) are computer-based algorithms in which the sensing network, computing device, communication device, communication network, and physical components are tightly integrated. CPS integration also refers to a new system capability that can interact with the physical world depending on the uncertainty of the physical environment. This made the brilliant communication between the industry to consumers, for feeding people globally. The machine sensors are combined with the IoT cloud to view and data visualization platform to improve industry performance and drive continuous improvement activities, maintenance, and quality framework. As a part of primitive maintenance services, routine action alerts based on real-time data and models acquired from manufacturing assets are monitored by a worldwide quality and performance management centre and automatically communicated to field-based employees and consumer maintenance people. Data analytics, cloud-based training, human-machine collaboration apps, and AI-based product improvement has made improvement in predicting specific equipment issue and monitoring production and downtimes with a near 100 % success rate [51].
Table 2Comparison of various robots in the food industry and their specifications
Application | Manipulator | Workspace diameter (mm) | DOF | Theoretical payload (kg) | Maker company | Ref |
Pick and Placing | TS60 SCARA | 600 | 4 | 2 | Staubi, Switzerland | [35] |
M-430iA/2F | 1130 | 5 | 1-2 | FANUC, USA | [36] | |
KA AGILUS | 1101 | 6 | 6-10 | KUKA, Germany | [37] | |
Palletizing | IRB 660 | 3150 | 4 | 180/250 | ABB, Switzerland | [37] |
KA QUANTEC | 3190 | 5 | 120-240 | KUKA, Germany | [38] | |
HC30PL | 3400 | 6 | 30 | Yaskawa, Japan | [39] | |
Inspection and Testing | FANUC M-liA parallel link robot | 420 (max) | 3/4/6 | 1 (max) | FANUC, Canada | [40] |
IRB 360 Flex Picker robot | 1600 (max) | 4 | 1-8 | ABB Robotics | [41] | |
IRB 4600s | 4600 (max) | 6+3 | 20-60 | ABB Robotics | [42] | |
Serving in Restaurants | Pizza Hut Pepper robot | 12 hours of operation with motion speed up to 2km/hr | 17 | - | SoftBank Corp Aldebaran Robotics | [43] |
Nao | 1-1.5hr | 14 | - | SoftBank Corp Aldebaran Robotics | [44] | |
Connie | 1-1.5hr | 14 | - | Hilton/IBM | [45] | |
Decorating and topping | Epson Robots G20 | 850 and 1000 | 6 | 20 | EPSON, America | [46] |
Material Handling | MX350L | 3018 | 6 | 350 | Kawasaki Robotics | [47] |
4.2. Revolution by AI applications
Artificial intelligence has added to future optimization, improved automation, and rapid decision-making through machine learning and computer vision technology. It is used without dispensing light unnecessarily on food products. One of the remarkable discoveries in the food business is predicting customer tastes. Based on the reviews from the customer demographics, segmentation by factors like religion, age, and gender. Analytical flavor system Gastrographic AI takes on this problem using genetic algorithms in artificial intelligence. Another AI-based model in food safety is the Kankan with face and object recognition technology to track operator movement and food safety compliance practices. The use of data on bacterial spoilage indicators from 23 dairy processing plants to detect post-pasteurization contamination causes elements is another effective application of machine learning [52].
Fig. 19Food industry development in each industrial revolution stage
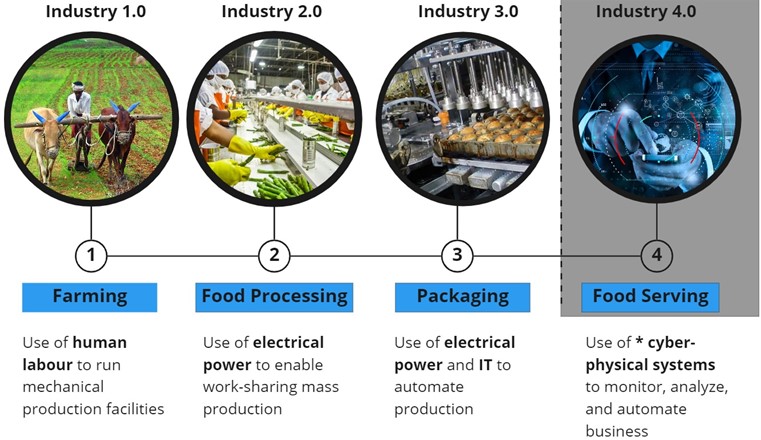
This investigation bought to light how sensitive it is to reduce contamination using appropriate manufacturing practices, diverse equipment, and internal final product inspection. In Fig. 20, the statical set of five-year (2018-2022) data with the growth of the food and beverage industry country-wise is graphically presented. This explains that the growth is continuous, but it does not meet consumer demands due to population and environmental factors [33].
Fig. 20Food and beverage industry growth country wise (in U.S. billion Dollars)
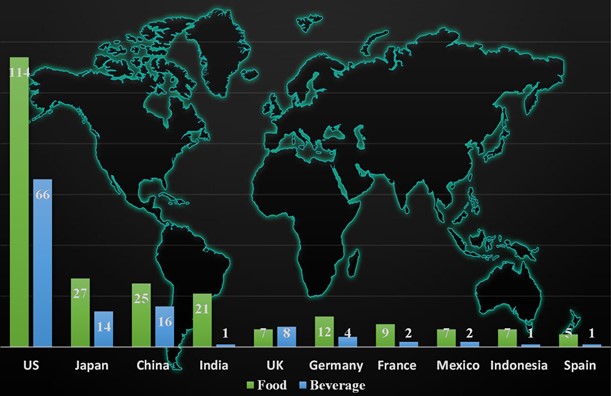
There still requires more advancement and research in some sectors of the food domain like in the fish industry for sorting and machines that removes pin bones from fishes, which are often left after mechanical treatment [54]. In the dairy industry for gripper technology in handling cheese and butter packing. And more studies are to be done in the spices industry for processing, identification, and sorting. There is not enough amount of research work done in the field of automation in the food sector. The study says that most of the food sectors including Seafood, bakery, edible oil, beverages, and meat and poultry have just 9 % of research work available. The application of robotics is mostly in the field of the food sector. A variety of robot installations and automatization is possible in these industries. Recent advancements and one of the emerging techniques are the 3D printing technology. A great amount of research has been carried out on the printing of plant-based or vegetarian meat products that present the same taste, texture, and even smell as real meat.
Fig. 21 gives the research work available to date in the various fields of the food sectors. It clearly states that still there is a lack of research literature to be done in various fields of food science. As technology has reached heights but still or development is very slow in a few areas like sugar mills and grains industries. Most of these sectors also fall under small-scale industries like jaggery making, spices, grains storage, oil mills, and seafood cultivation. The intervention of small robots and automation technology in these small-scale industries has a remarkable development in production but also in social and economic benefits shown in Fig. 22. Use of blockchain technology has wide applications in the food industry emerging from the year 2017 and most publications in the year 2019 [55].
Fig. 21Chart corresponding literature survey of different food domains
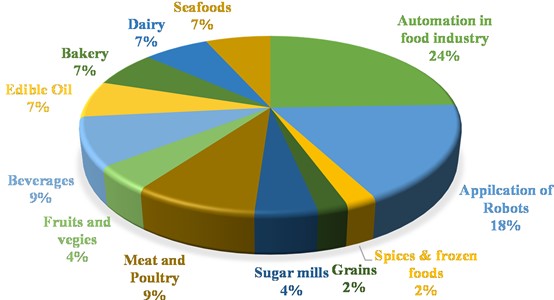
Fig. 22Benefits of robots
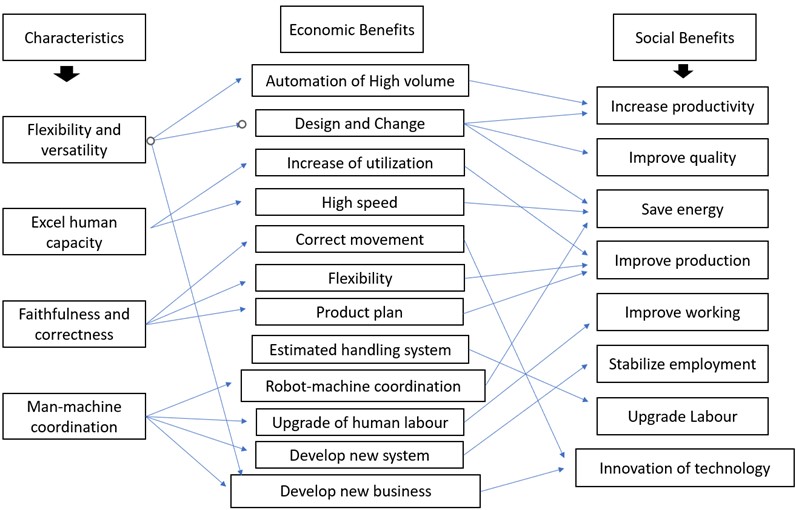
Robots are now recognized as they help reverse productivity declines and fill repetitive jobs human workers do not want. Both Cobots and robots are used in various ways in both primary and secondary food processing applications like fruit and vegetable pick and place, robotic cutting and slicing of fish and meat products, cake decoration and dispensing, cleaning and safe working surrounding, vision-guided for grain and fruit sorting, palletizing and depalletizing and many it goes furthermore.
The most advancement in robotic technology in the food sector has been introduced of more advanced and adaptive grippers. They are capable of handling soft, hard delicate, irregular shapes, and varying temperature materials as hot as boiling oil and as cold as ice cream. These grippers are paired with vision technology to guide the robotic arm. The reach of robots is also in the food delivery sector. Autonomous ground vehicles to deliver packed food products and drone technology using the GPS system to take and deliver the food items have increased their craze in recent 4 years.
5. Conclusions
The application of robots and automation has helped the food industry in all ways in loading raw materials, cleaning, processing, manufacturing, packaging, storage in warehouses, business, marketing, and selling. It is revealed that robotics has significantly augmented the yield as compared to manual systems. The use of robotic applications in the food industry has grown remarkably over recent years, helping revolutionization food processing, handling, sorting, picking, palletizing, packaging and storage, and delivery. The benefits include enhanced traceability, standardized quality control, improve workplace safety, increase efficiency, provide flexibility, advanced computerized technology in monitoring the production and each operation, emerging techniques like machine vision, IR, deep learning, machine learning, CNN, color sorting, artificial intelligence and etc. Automation has not created unemployment or ruled out labour from industries but has converted unskilled labour into skilled labour. It encouraged them to educate training on new generation machines and work on automated machines lines. Due to automated equipment, it has become easy to standardize the food production process. The food contamination SOC (Source of Contamination) and intervention of pathogens have come to a count of negligence due to robot handling and elimination of human intervention in the processing. Solved many problems of hard-to-reach (HTR) areas and hazardous working conditions like extreme temperatures, cutting operations, and radiations or chemical reactions of workers.
Challenges faced by different food processing industry depends largely on the type of raw material in each domain and the type of product delivery in batches or continuous shipments. The problem lies in the transition of human employees over the roles of robots taking over. And the adaptability of the robots according to the variability of the raw material feeder. The transition to food-producing robots offers significant benefits to the industry. The implementation of robotics can solve the food chain's workforce shortage. Not only will labour shortages be addressed, but issues such as vacation and sick leave absences, duty hours (24X7), cultural differences, labour issues, the cost of incorrect training by vocational training centers, less costly human errors, an added layer of safety, less human contact, especially during pandemics, and consistent cleaning procedures will also be addressed.
References
-
Kokane Sanket B., Kalamnurikar Shalaka S., and Khose Suyog B., “Robotics in food processing industries: A review,” The Pharma Innovation Journal, Vol. 11, No. 7S, pp. 948–953, Jul. 2022.
-
Z. H. Khan, A. Khalid, and J. Iqbal, “Towards realizing robotic potential in future intelligent food manufacturing systems,” Innovative Food Science and Emerging Technologies, Vol. 48, pp. 11–24, Aug. 2018, https://doi.org/10.1016/j.ifset.2018.05.011
-
F. Bader and S. Rahimifard, “A methodology for the selection of industrial robots in food handling,” Innovative Food Science and Emerging Technologies, Vol. 64, p. 102379, Aug. 2020, https://doi.org/10.1016/j.ifset.2020.102379
-
Sarangi, Prasant, and Navi Mumbai Icsi-Ccgrt., “A review on indian food processing industry: challenges and opportunities,” ICSI-CCGRT.
-
S. Hyder and P. K. Bhargava, “Indian food processing industry – opportunities and challenges,” International Journal of Economics and Business Research, Vol. 11, No. 1, 2016, https://doi.org/10.1504/ijebr.2016.074422
-
A. Wedler et al., “Preliminary results for the multi-robot, multi-partner , multi-mission , planetary exploration analogue campaign on mount Etna,” in International Astronautical Congress, 2021.
-
W. Grobbelaar, A. Verma, and V. K. Shukla, “Analyzing human robotic interaction in the food industry,” in Journal of Physics: Conference Series, Vol. 1714, No. 1, p. 012032, Jan. 2021, https://doi.org/10.1088/1742-6596/1714/1/012032
-
Z. Wang, S. Hirai, and S. Kawamura, “Challenges and opportunities in robotic food handling: a review,” Frontiers in Robotics and AI, Vol. 8, Jan. 2022, https://doi.org/10.3389/frobt.2021.789107
-
J. Iqbal, Z. H. Khan, and A. Khalid, “Prospects of robotics in food industry,” Food Science and Technology, Vol. 37, No. 2, pp. 159–165, May 2017, https://doi.org/10.1590/1678-457x.14616
-
F. Bader and S. Rahimifard, “Challenges for industrial robot applications in food manufacturing,” in ISCSIC’18: The 2nd International Symposium on Computer Science and Intelligent Control, Sep. 2018, https://doi.org/10.1145/3284557.3284723
-
“What is the demand for grains, pulses and oilseeds on the European market?”, 2023 https://www.cbi.eu/market-information/grains-pulses-oilseeds/trade-statistics.
-
H. Zareiforoush, S. Minaei, M. R. Alizadeh, and A. Banakar, “Qualitative classification of milled rice grains using computer vision and metaheuristic techniques,” Journal of Food Science and Technology, Vol. 53, No. 1, pp. 118–131, Jan. 2016, https://doi.org/10.1007/s13197-015-1947-4
-
Caldwell, Darwin G., and Ed., Robotics and automation in the food industry: current and future technologies. Elsevier, 2012.
-
Konakbayev, O. B., and K. I. Mizamova, “Grain receiving automation.,” (in Russian), Journal Sciences, Vol. 39, pp. 315–322.
-
“A history of sugar – the food nobody needs, but everyone craves.”. https://theconversation.com/a-history-of-sugar-the-food-nobody-needs-but-everyone-craves-49823
-
L. Rózsa, “A few thoughts on automation in sugar manufacturing,” International Sugar Journal, Vol. 105, pp. 156–158, 2003.
-
S. K. Sunori, G. Singh Jethi, S. Arora, A. Mittal, F. Khan, and P. Juneja, “Controller design for dead time approximated model of juice extraction unit of sugar factory,” in 6th International Conference on Computing Methodologies and Communication (ICCMC), Mar. 2022, https://doi.org/10.1109/iccmc53470.2022.9753728
-
Zemse et al., “Sugar factory boiler automation,” International Journal of Scientific and Technical Advancements, Vol. 2, No. 2, pp. 107–109, 2016.
-
F. Gandhi, P. Himanshu, and R. Mahavirsinhgohil, “Advanced instrumentation and automation for filling and packaging of beverages.,” International Journal of Electrical and Electronics Engineering Research (IJEEER), Vol. 5, No. 1, pp. 1–10, 2015.
-
Z. Li, X. Yuan, and C. Wang, “A review on structural development and recognition-localization methods for end-effector of fruit-vegetable picking robots,” International Journal of Advanced Robotic Systems, Vol. 19, No. 3, p. 172988062211049, May 2022, https://doi.org/10.1177/17298806221104906
-
S. F. Sim and W. Ting, “An automated approach for analysis of Fourier transform infrared (FTIR) spectra of edible oils,” Talanta, Vol. 88, pp. 537–543, Jan. 2012, https://doi.org/10.1016/j.talanta.2011.11.030
-
J. I. Reyes-De-Corcuera, R. M. Goodrich-Schneider, S. A. Barringer, and M. A. Landeros-Urbina, “Processing of fruit and vegetable beverages,” Food Processing, pp. 339–362, Apr. 2014, https://doi.org/10.1002/9781118846315.ch15
-
Adam Vaughan. “Global demand for fish expected to almost double by 2050.” New Scientist, 2021, https://www.newscientist.com/article/2290082-global-demand-for-fish-expected-to-almost-double-by-2050/
-
T. A. Khoroshailo and Y. A. Kozub, “Robotization in the production of dairy, meat and fish products,” Journal of Physics: Conference Series, Vol. 1515, No. 2, p. 022007, Apr. 2020, https://doi.org/10.1088/1742-6596/1515/2/022007
-
J. O. Buljo and T. B. Gjerstad, “Robotics and automation in seafood processing,” Robotics and Automation in the Food Industry, pp. 354–384, 2013, https://doi.org/10.1533/9780857095763.2.354
-
Hannah Ritchie, Pablo Rosado, and Max Roser, “Meat and dairy production,” Our World in Data, Aug. 2017.
-
M. Ollinger, “Structural change in the meat, poultry, dairy, and grain processing industries,” U.S. Dept. of Agriculture, Economic Research Service, 2005.
-
A. Jahanbakhshi, Y. Abbaspour-Gilandeh, K. Heidarbeigi, and M. Momeny, “A novel method based on machine vision system and deep learning to detect fraud in turmeric powder,” Computers in Biology and Medicine, Vol. 136, p. 104728, Sep. 2021, https://doi.org/10.1016/j.compbiomed.2021.104728
-
R. J. Delmore, “Automation in the global meat industry,” Animal Frontiers, Vol. 12, No. 2, pp. 3–4, Apr. 2022, https://doi.org/10.1093/af/vfac021
-
A. Mathath and Yudi Fernando, “Robotic transformation and its business applications in food industry,” IGI Global, pp. 281–305, 2015, https://doi.org/10.4018/978-1-5225-1759-7.ch091
-
Meshram, B. D., Shaikh Adil, and Suvartan Ranvir., “Robotics: An emerging technology in dairy and food industry.,” International Journal of Chemical Studies, Vol. 6, No. 2, pp. 440–449, 2018.
-
A. K. Legg, A. J. Carr, R. J. Bennett, and K. A. Johnston, “General aspects of cheese technology,” Cheese: chemistry, physics and microbiology, pp. 643–675, 2017, https://doi.org/10.1016/b978-0-12-417012-4.00026-0
-
Z. E. Martins, O. Pinho, and I. M. P. L. V. O. Ferreira, “Food industry by-products used as functional ingredients of bakery products,” Trends in Food Science and Technology, Vol. 67, pp. 106–128, Sep. 2017, https://doi.org/10.1016/j.tifs.2017.07.003
-
D. Diann. “What is Industry 4.0? Definition from SearchERP”, https://www.techtarget.com/searcherp/definition/industry-40
-
“TS2-60 SCARA industrial robots.” Stäubli, https://www.staubli.com/global/en/robotics/products/industrial-robots/ts2-60.html
-
E. Nikolov, V. Karlova-Sergieva, and B. Grasiani, “Design control system of robot-manipulator FANUC M-430iA/4FH,” in IOP Conference Series: Materials Science and Engineering, Vol. 878, No. 1, p. 012007, Jun. 2020, https://doi.org/10.1088/1757-899x/878/1/012007
-
B. K. Panda, S. S. Panigrahi, G. Mishra, and V. Kumar, “Robotics for general material handling machines in food plants,” Transporting Operations of Food Materials Within Food Factories, pp. 341–372, 2023, https://doi.org/10.1016/b978-0-12-818585-8.00005-2
-
G. Lefranc, “Review of trends in manufacturing systems based on industry 4.0: the opportunities,” in Intelligent Methods Systems and Applications in Computing, Communications and Control, pp. 182–192, 2023, https://doi.org/10.1007/978-3-031-16684-6_15
-
J.-M. Clairand, M. Briceno-Leon, G. Escriva-Escriva, and A. M. Pantaleo, “Review of energy efficiency technologies in the food industry: trends, barriers, and opportunities,” IEEE Access, Vol. 8, pp. 48015–48029, 2020, https://doi.org/10.1109/access.2020.2979077
-
“Motoman HC30PL 30-kg Collaborative Robot.” IP67 Rated. https://www.motoman.com/en-us/products/robots/collaborative/hc-series/hc30pl
-
Midwest Engineered Systems, https://www.mwes.com/?ppc_keyword=fanuc%20robotics&gclid=cjwkcajw0n6hbhaueiwaxab-ttpql40_uwx8xgeiggvkseeczutk8ij5uccl8dgslwsahhqvwimcehoc0asqavd_bwe
-
S. Gibbons, S. Mourato, and G. M. Resende, “The amenity value of english nature: a hedonic price approach,” Environmental and Resource Economics, Vol. 57, No. 2, pp. 175–196, Feb. 2014, https://doi.org/10.1007/s10640-013-9664-9
-
ABB Robotics, https://new.abb.com/products/robotics/robots/delta-robots/irb-360
-
IRB 4600, ABB Robotics.
-
“Meet Pepper: the first robot with emotions” Time, https://time.com/2845040/robot-emotions-pepper-softbank/
-
D. Cazzato, C. Cimarelli, J. L. Sanchez-Lopez, M. A. Olivares-Mendez, and H. Voos, “Real-Time Human Head Imitation for Humanoid Robots,” in 3rd International Conference on Artificial Intelligence and Virtual Reality, Jul. 2019, https://doi.org/10.1145/3348488.3348501
-
This Watson-powered robot concierge is rethinking the hotel industry, ZDNET.
-
Extra large robots up to 1,500kg payload, Industrial Robots by Kawasaki Robotics.
-
B. R. Rawal, V. Pare, and K. Tripathi, “Development of noncontact end effector for handling of bakery products,” The International Journal of Advanced Manufacturing Technology, Vol. 38, No. 5-6, pp. 524–528, Aug. 2008, https://doi.org/10.1007/s00170-007-1166-x
-
Industrial automation worldwide, Statista.
-
Z. Baz, “Moving food processing to industry 4.0 and beyond.,” Food Technology, Vol. 75, No. 6, pp. 62–65, 2021.
-
Epson Scara G-Series – Epson Robotic Solutions – PDF Catalogs, Technical Documentation, directindustry.com.
-
N. Kalchayanand, M. Koohmaraie, and T. L. Wheeler, “Fate of Shiga toxin-producing Escherichia coli (STEC) and salmonella during kosher processing of fresh beef,” Journal of Food Protection, Vol. 86, No. 6, p. 100088, Jun. 2023, https://doi.org/10.1016/j.jfp.2023.100088
-
A. Hassoun et al., “Seafood processing, preservation, and analytical techniques in the age of industry 4.0,” Applied Sciences, Vol. 12, No. 3, p. 1703, Feb. 2022, https://doi.org/10.3390/app12031703
-
A. Rejeb, J. G. Keogh, S. Zailani, H. Treiblmaier, and K. Rejeb, “Blockchain technology in the food industry: a review of potentials, challenges and future research directions,” Logistics, Vol. 4, No. 4, p. 27, Oct. 2020, https://doi.org/10.3390/logistics4040027
Cited by
About this article
The authors have not disclosed any funding.
The datasets generated during and/or analyzed during the current study are available from the corresponding author on reasonable request.
Paper research work, analysis and paper writing is done by Yash Wakchaure. Editing and checking of the data and formatting by Bhumeshwar Patle and Sachin Pawar.
The authors declare that they have no conflict of interest.