Abstract
Sufficient labeled fault samples are the key to ensuring the performance of deep learning diagnostic models. However, in practical engineering applications, machinery and equipment operate normally most of the time, and it is difficult to collect enough fault data. In contrast, through the kinetics analysis method, simulation data sets of various fault types can be easily obtained. However, there is a difference in distribution between simulation data and real data. The deep learning diagnosis model trained directly with simulation data lacks versatility and cannot be applied to fault diagnosis of real data. To this end, this paper proposes a simulation data-driven deep transfer learning fault diagnosis method, which applies the fault diagnosis knowledge in the simulation data to the real data fault diagnosis task. The effectiveness of the method is verified by experiments on the two-stage planetary gearbox in the Drivetrain Diagnostics Simulator (DDS) test bench.
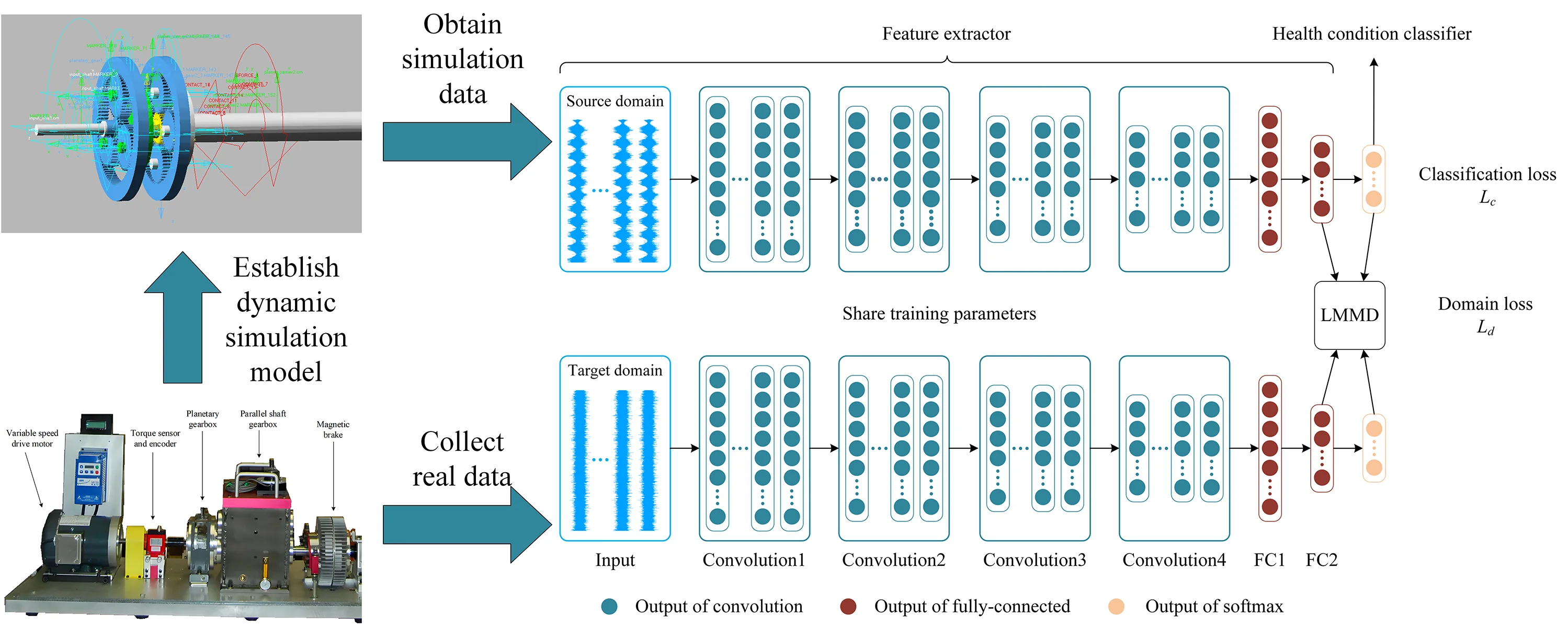
Highlights
- By establishing the dynamic simulation model of the planetary gearbox, a large number of various fault simulation data is obtained.
- Applying Fault Diagnosis Knowledge from Dynamic Simulation Models to Real Planetary Gearboxes.
- The proposed method outperforms existing transfer learning methods in the fault diagnosis task of transfer simulated data to real data.
1. Introduction
When applying deep learning methods for fault diagnosis, sufficient labeled training samples are an important condition to ensure the performance of deep learning models. However, in practical engineering applications, mechanical equipment usually stops immediately after failure, and it is impossible to operate with failure for a long time. Therefore, most of the monitoring data obtained from mechanical equipment is the data during healthy operation, and there is a lack of labeled fault data. How to train an effective deep learning fault diagnosis model in the absence of labeled fault data is a challenge for intelligent fault diagnosis technology.
Through the fault diagnosis method based on dynamic analysis, a large amount of labeled fault data can be obtained to solve the problem of lack of fault data. This method usually establishes the dynamic model of mechanical equipment first, so as to simulate the dynamic response of mechanical equipment under various health conditions, and carry out fault diagnosis through the analysis of dynamic response [1]. Assaad et al. [2] proposed a technology combining cyclostationary signal and autoregressive signal modeling for wear detection of multistage planetary gears, and extracted the residual signal containing relevant fault features. Li et al. [3] established the transverse and torsional coupling dynamic model to predict the modulation sideband of two-stage composite planetary gear, calculated the time-varying meshing stiffness of gear pair by using the improved potential energy method, and analyzed the influence of crack propagation on meshing stiffness. Yang et al. [4] proposed an improved rigid multi-body model for the kinetic analysis of planetary gearbox, introduced the element assembly method to establish the model, proposed the time-varying grid stiffness model, and carried out the modal analysis and transient analysis considering the time-varying grid stiffness. Xu et al. [5] proposed a dynamic gearbox model considering the structural flexibility of shaft and bearing seat based on lumped parameters and finite element method. Compared with lumped parameter and finite element model, this model has higher computational efficiency. Fan et al. [6] considered the nonlinear factors such as time-varying meshing stiffness, backlash and viscous damping, established the dynamic model of torsional vibration of planetary gear train with planetary carrier crack fault, and revealed the corresponding relationship between the vibration characteristics of planetary carrier crack and the crack condition from the fault characteristics extracted from the model.
Due to the difference between the simulation data obtained by the dynamic analysis and the actual data collected from the mechanical equipment, the intelligent diagnosis model trained with the simulation data set cannot achieve the expected performance in the fault diagnosis of the real mechanical equipment. Transfer learning is an effective method to solve the problem of data distribution differences. It can apply the knowledge learned from a diagnostic task to different tasks related to the task. Cao et al. [7] used a large amount of image data to pre-train the deep convolutional neural network, then converted the planetary gearbox fault data into grayscale images, and used these grayscale images to fine-tune the parameters of the last three layers of the deep convolutional neural network, so that the It is capable of classifying fault data. Jiao et al. [8] directly processed raw mechanical signals for adaptive feature learning through a one-dimensional residual network, in which a joint maximum mean difference and an adversarial adaptive discriminator were introduced to simultaneously reduce the skewness of joint and marginal distributions across different domains. He et al. [9] used enough auxiliary data in the source domain to pre-train the deep auto-encoder, and passed its parameters to the target model, and trained the deep transfer algorithm with small samples to adapt to the characteristics of the remaining test data. Chen et al. [10] proposed a domain adversarial transfer network, which uses an asymmetric encoding network fused with deep convolutional neural networks to learn feature representations, and uses weight value transfer and domain adversarial strategies to reduce the difference between source domains and target domains. Shao et al. [11] proposed a deep transfer learning method based on sub-domain adaptation, by introducing sub-domain adaptation and adversarial learning, while aligning the local and global feature distributions.
In view of the above problems, this paper takes the two-stage planetary gearbox as the research object, and proposes a simulation data-driven deep transfer learning fault diagnosis method. The simulation data of different health conditions are obtained by establishing the dynamic simulation model of the planetary gearbox. The features of simulation data and real data are extracted through a one-dimensional convolutional neural network, and local maximum mean discrepancy (LMMD) [12] is introduced to align the global distribution and class local distribution of simulation data and real data. The effectiveness of the method is verified by the DDS test bench, and the results show that the method can effectively overcome the problem of scarcity of labeled fault data.
2. Experiment
2.1. Dynamics simulation
This paper takes the two-stage planetary gearbox in the DDS test bench designed by American SpectraQuest company as the research object. The physical model of the DDS test bench is shown in Fig. 1. By adjusting the speed, changing the load, and replacing the faulty sun gear, the test bench can simulate various failures under different working conditions. The two-stage planetary gearbox in the test bench is mainly composed of a box body, an input shaft, two sun gears, seven planetary gears, two inner gears and two planet carriers. The number of the first stage planetary gear is 3 and the number of the second stage planetary gear is 4, and the basic parameters of the gear are shown in Table 1.
The rigid-flexible coupling model of the secondary planetary gearbox is established by ADAMS, as shown in Fig. 2, in which the primary planet carrier and the secondary sun gear are flexible bodies, and the rest of the parts are rigid bodies. Set the termination time to 10s and the number of simulation steps to 128000 for simulation. After the simulation, the centroid angular acceleration of secondary planet carrier is derived as the simulation data. The time domain diagram of the simulation data of secondary sun gear broken tooth fault and secondary sun gear missing tooth fault is shown in Fig. 3.
Fig. 1DDS test bench physical model

Fig. 2Rigid-flexible coupling model of two-stage planetary gearbox
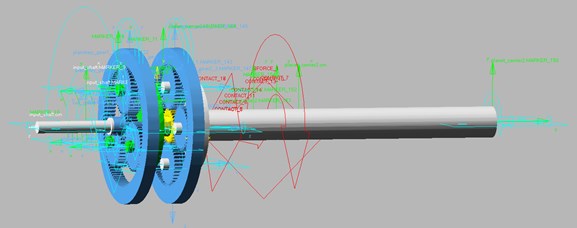
Fig. 3Time domain diagram of secondary sun gear fault simulation data
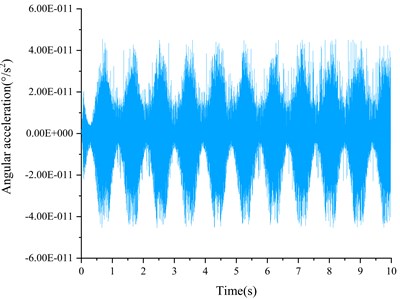
a) Broken tooth fault
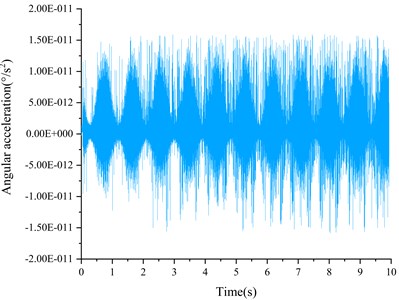
a) Missing tooth fault
3. Deep transfer learning
Build the deep transfer learning network model shown in Fig. 4. The network model consists of three parts: feature extractor, health status classifier, and LMMD. The feature extractor contains four convolutional layers and two fully connected layers to extract features from the source and target domain datasets. The health classifier is used to predict the labels of the source and target domain features. LMMD is used to measure the global distribution and class local distribution differences between source and target domains. There are two optimization goals in the training process of this network model: 1) Minimize the classification loss of the source domain dataset and guide the health state classifier to output correctly predicted labels. 2) Minimize the domain loss between the source domain dataset and the target domain dataset, and guide the feature extractor to output domain-invariant features.
Table 1Basic parameters of gear
Spare parts | Number of teeth | Modulus | Pressure angle | Tooth width |
Primary sun gear | 20 | 1 | 20° | 10 mm |
Primary planetary gear | 40 | 1 | 20° | 10 mm |
Primary ring gear | 100 | 1 | 20° | 10 mm |
Secondary sun gear | 28 | 1 | 20° | 10 mm |
Secondary planetary gear | 36 | 1 | 20° | 10 mm |
Secondary ring gear | 100 | 1 | 20° | 10 mm |
The real data is the vibration signal collected from the DDS test bench, including two health conditions: broken teeth of secondary sun gear and missing teeth of secondary sun gear. When collecting the signal, the sampling frequency is 12.8 kHz, the rotation frequency of the input shaft of the planetary gearbox is 30 Hz, and the current on the magnetic brake is 0.8 A.
Fig. 4Deep transfer learning network model structure
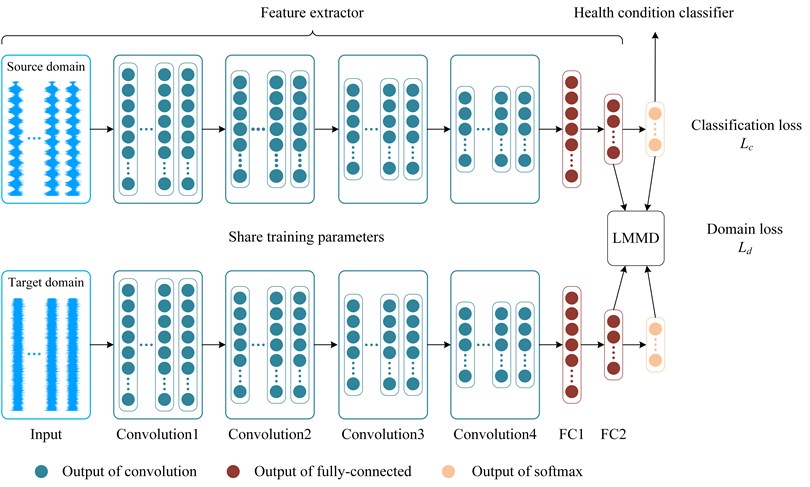
The experiment adopts the method of overlapping sampling to generate the data set, sampling 2048 points every 100 points, that is, each sample has 2048 data points, and the number of samples is shown in Table 2. All samples in the simulation data set are used for training. 2000 samples in the real data set are used for training, and the remaining 400 samples are used for testing. In order to verify the effectiveness of the proposed method, the simulation data set A is used as the source domain, and the unlabeled real data set B is the target domain for transfer learning, and DeepCoral [13], DDC [14], DANN [15], JAN [16] are selected for comparison experiment.
Table 2Dataset description
Name | Dataset | Health condition | Number of samples | Load |
A | Simulation data | Broken tooth | 1000 | 0.8 |
Missing tooth | 1000 | 0.8 | ||
B | Real data | Broken tooth | 1200 | 0.4 |
Missing tooth | 1200 | 0.4 |
The experimental results are shown in Table 3. It can be seen from Table 3 that several transfer learning methods have taken higher diagnosis accuracy, and the accuracy rate of the method proposed in this paper is 87 %, which is better than other methods, which shows that it is feasible to apply the diagnosis knowledge in the simulation data to the fault diagnosis of the real planetary gearbox, and verifies the effectiveness of the simulation data-driven deep transfer learning fault diagnosis method.
Table 3Diagnostic accuracy
Method | Accuracy |
DeepCoral | 84.5 |
DDC | 85.75 |
DANN | 82.25 |
JAN | 84.25 |
Proposed | 87 |
4. Conclusions
Aiming at the scarcity of labeled fault data, this paper implements a simulation data-driven deep transfer learning fault diagnosis method, which transfer fault diagnosis knowledge from simulation data to real data. The dynamic simulation model of the two-stage planetary gearbox of the DDS test bench is established by ADASM, and the simulation data of different fault types are obtained through the model. On this basis, a deep transfer learning network model is constructed, through which the domain-invariant features are learned from the simulation data, and then the fault diagnosis of the real data is realized. The effectiveness of the method is verified by experiments on the two-stage planetary gearbox in the DDS test bench. In the future, we plan to perform transfer learning on simulation datasets of more health conditions and real datasets of more health conditions.
References
-
X. Liang, M. J. Zuo, and Z. Feng, “Dynamic modeling of gearbox faults: A review,” Mechanical Systems and Signal Processing, Vol. 98, pp. 852–876, Jan. 2018, https://doi.org/10.1016/j.ymssp.2017.05.024
-
B. Assaad and M. Eltabach, “Vibration monitoring of winch epicyclic gearboxes using cyclostationarity and autoregressive signal model,” Lecture Notes in Mechanical Engineering, pp. 261–271, 2014, https://doi.org/10.1007/978-3-642-39348-8_22
-
G. Li, F. Li, Y. Wang, and D. Dong, “Fault diagnosis for a multistage planetary gear set using model-based simulation and experimental investigation,” Shock and Vibration, Vol. 2016, pp. 1–19, 2016, https://doi.org/10.1155/2016/9263298
-
W. Yang and D. Jiang, “An improved rigid multibody model for the dynamic analysis of the planetary gearbox in a wind turbine,” Shock and Vibration, Vol. 2016, pp. 1–18, 2016, https://doi.org/10.1155/2016/9742673
-
H. Xu, D. Qin, C. Liu, Y. Yi, and H. Jia, “Dynamic modeling of multistage gearbox and analysis method of resonance danger path,” IEEE Access, Vol. 7, No. 99, pp. 154796–154807, 2019, https://doi.org/10.1109/access.2019.2944685
-
L. Fan, S. Wang, X. Wang, F. Han, and H. Lyu, “Nonlinear dynamic modeling of a helicopter planetary gear train for carrier plate crack fault diagnosis,” Chinese Journal of Aeronautics, Vol. 29, No. 3, pp. 675–687, Jun. 2016, https://doi.org/10.1016/j.cja.2016.04.008
-
P. Cao, S. Zhang, and J. Tang, “Pre-processing-free gear fault diagnosis using small datasets with deep convolutional neural network-based transfer learning,” IEEE Access, Vol. 6, No. 99, pp. 26241–26253, 2018, https://doi.org/10.1109/access.2018.2837621
-
J. Jiao, M. Zhao, J. Lin, and K. Liang, “Residual joint adaptation adversarial network for intelligent transfer fault diagnosis,” Mechanical Systems and Signal Processing, Vol. 145, p. 106962, Nov. 2020, https://doi.org/10.1016/j.ymssp.2020.106962
-
Z. He, H. Shao, X. Zhang, J. Cheng, and Y. Yang, “Improved deep transfer auto-encoder for fault diagnosis of gearbox under variable working conditions with small training samples,” IEEE Access, Vol. 7, pp. 115368–115377, 2019, https://doi.org/10.1109/access.2019.2936243
-
Z. Chen, G. He, J. Li, Y. Liao, K. Gryllias, and W. Li, “Domain adversarial transfer network for cross-domain fault diagnosis of rotary machinery,” IEEE Transactions on Instrumentation and Measurement, Vol. 69, No. 11, pp. 8702–8712, Nov. 2020, https://doi.org/10.1109/tim.2020.2995441
-
J. Shao, Z. Huang, Y. Zhu, J. Zhu, and D. Fang, “Rotating machinery fault diagnosis by deep adversarial transfer learning based on subdomain adaptation,” Advances in Mechanical Engineering, Vol. 13, No. 8, p. 168781402110402, Aug. 2021, https://doi.org/10.1177/16878140211040226
-
Y. Zhu et al., “Deep subdomain adaptation network for image classification,” IEEE Transactions on Neural Networks and Learning Systems, Vol. 32, No. 4, pp. 1713–1722, Apr. 2021, https://doi.org/10.1109/tnnls.2020.2988928
-
B. Sun and K. Saenko, “Deep coral: Correlation alignment for deep domain adaptation,” in European Conference on Computer Vision, pp. 443–450, 2016, https://doi.org/10.48550/arxiv.1607.01719
-
E. Tzeng, J. Hoffman, N. Zhang, K. Saenko, and T. Darrell, “Deep domain confusion: maximizing for domain invariance,” arXiv preprint arXiv:1412.3474, 2014.
-
Y. Ganin and V. Lempitsky, “Unsupervised domain adaptation by backpropagation,” in International Conference on Machine Learning, pp. 1180–1189, 2014, https://doi.org/10.48550/arxiv.1409.7495
-
M. Long, H. Zhu, J. Wang, and M. I. Jordan, “Deep transfer learning with joint adaptation networks,” in International Conference on Machine Learning, pp. 2208–2217, 2016, https://doi.org/10.48550/arxiv.1605.06636
About this article
This paper was supported by the following research projects: by the Natural Science Foundation of Fujian Province (Grant No. 2020J01432 and No. 2021J011168), the Major training project of Ningde Normal University (Grant No. 2020ZDK01), Innovation Team of Ningde Normal University (No. 2020T02) and Special Project of Ningde Normal University (Grant No. 2019ZX403). These supports are gratefully acknowledged.