Abstract
Natural fibers are increasingly used for polymer composite intending to minimize the environmental impact. Bio-composite materials are increasingly being used in industrial transport structures, including aerospace and automotive. Natural fiber reinforces composites with equivalent performances of glass fiber composites, have higher amount of fiber, resulting in less pollution and much lighter weight, which reduces the fuel consumption. Also, they offer the ability to design complex parts and high mechanical properties structures. Barely visible impact damage (BVID) represent a serious threat to the efficiency of bio-composite materials. In this paper, modal analysis was used to investigate and evaluate the impact-induced damage of flax/epoxy composite plates. The vibratory behavior is an indicator of the structural health monitoring of composite materials. Natural frequency, damping loss factors and displacement pattern, named mode shapes, are studied in order to detect damage and anticipate perilous consequences through time.
1. Introduction
Lately, there has been a major interest and high technological development concerning bio-composites. The call for environmental friendliness has prompted the use of natural fibers as composite reinforcement. These materials are a good alternative to synthetic polymer composites, with less environmental impact and an important light-weight. They are increasingly used in different fields, namely transport, construction, sports [1].
Due to the ecological benefits and mechanical merits, the use of flax fibers has been significantly developed for various applications in recent years. Flax fibers are extracted from the skin of the stem of flax plant. France is the world’s largest grower and manufacturer of flax fibers, with 50 % of the global production. Besides the environmental benefits, the interest in flax is explained by the availability of this plant, length of the elementary fibers and their important mechanical properties compared to synthetic fibers, such as glass fiber [2], [3].
These characteristics can be explained by the structural function and the shape of flax fiber. The resistance to loading and bending is ensured by the fiber bundles, distributed outside the stem. Therefore, flax reinforced composite materials are considered as an alternative and are used in industrial transport (automotive, marine and aerospace) and in other sectors such as civil constructions and sporting. Flax stem is composed of three layers. The outer layer of bark protects the plant from external harassment except of water and nutriments [4]. However, the fiber properties depend on several parameters (growth conditions, retting and fiber extraction). Otherwise, controlling these parameters is compulsory for the manufacturing of flax fiber-reinforced polymer composite materials. The impregnability between fibers and matrix is a fundamental parameter for the choice of the resin. The use of flax fibers as reinforcement requires taking into consideration their sensitivity during the manufacturing process [5]. Epoxy is a matrix from thermoset family. It contributes to strength, stiffness, durability and chemical resistance to a composite. Epoxy resin is compatible with flax fibers. It can easily penetrate through these fibers and impregnates it.
Similarly, to conventional composite materials, bio-based composite materials have insignificant impact resistance because of their limited strength properties in all directions. In fact, natural fiber composites are reported to exhibit a limited resistance to impact loading. Low-velocity impact is considered as a crucial threat to flax fiber-based composite structures [6], [7].
Impact loading can occur during manufacturing, maintenance and operation, by foreign particles projection. Impact induced damage can be invisible or barely visible, yet it reduces significantly residual mechanical properties and may lead to the failure of the structure. Therefore, identifying damage in composite structures at its earliest possible stage of initiation, to prevent its further propagation is essential, even the smallest structural changes are necessary to be detected. Structural changes can be a local change of mass, damping, stiffness and flexibility of a structure. Recently, vibration based non-destructive testing (NDT) diagnostic is increasingly attractive due to its reliability and contact-less inspection of composite materials.
In this paper, an approach using structural vibrations and modal analysis has been developed to inspect and detect impact-induced damage in flax/epoxy plates.
This approach is able to detect barely visible or invisible impact damage in composite materials reinforced with natural flax fibers.
The proposed detection approach involves the use of an accelerometer to measure the acceleration applied to the system, and a laser Doppler vibrometer to measure the sample’s velocity. By following and analyzing the frequency-response functions, impact damage assessed on different types of stratifications of flax/epoxy composites are inspected. Furthermore, samples are impacted at different impact energy level. A drop-weight impact test is used to perform impact on these composite samples.
2. Material and methods
2.1. Material
FLAXPREG T-UD is a range of pre-impregnated material based on an epoxy resin system and the unidirectional (UD) flax fibers reinforcement developed and supplied by LINEO company and called the FlaxTape™. In this study, FLAXPREG T-UD (110 g/m²) are used for the manufacturing of flax/epoxy samples. The reference adopted is a FlaxTape™ with 110 gr of flax per m2 and 50 % epoxy of the total weight. Prepregs are stored at –18°C in order to keep the storage conditions during the time allowed for manufacturing parts and slow down the chemical reaction’s fiber/matrix.
2.2. Manufacturing process
The manufacturing process used in this study is film stacking by thermocompression. The cure cycle process of flax/epoxy composite materials applied is recommended by the material manufacturer. The cure of the prepreg was also monitored by a semi-automatic thermo-press machine with a 35×35 cm2 mold. The heating rate used between the isothermal temperatures was 3 °C/min. When the consolidation began, a pressure of 3 bars is applied to the mold. The pressure was maintained during the cooling part. Two different types of stacking sequence are considered in this study, presented in Table 1. In order to qualify and compare post-impact damage mechanisms in different laminates, specimens are manufacturing according to the sequences showed below.
Table 1Types of stacking sequence
Reference | Stacking sequence | Thickness (mm) |
S1 | [0/90]3S | 1.97 |
S2 | [45/-45/90/0/90/-45/45]S | 2.1 |
In order to highlight the delamination mechanism, essentially due to variation in the tensile modulus between the different layers, S1 is considered [8]. S2 is quasi-isotropic composite formed with 14 films of pre-impregnated flax/epoxy. This stacking sequence is mainly used for carbon composites employed on some aircrafts
3. Experiments
3.1. Impact test
The impact tests were performed by an instrumented drop-weight impact testing machine Instron Dynatup (see Fig. 1). The impactor has a hemispherical tip of 20 mm diameter, with an energy range from 0.6 to 40 Joules. Impact energy is obtained by changing the height of release and mass of the impactor. The tests are performed on specimens of 240 mm × 80 mm each, at room temperature. Specimens were clamped circumferentially in a pneumatic actuated clamping fixture.
The incident impact energy W is given by:W=mg, where m is mass of the impactor, g is gravity and h is height. In order to study the vibratory behavior of impacted bio-composite samples, the same energy is used to all samples from the same batch.
Fig. 1Impact testing machine Instron Dynatup
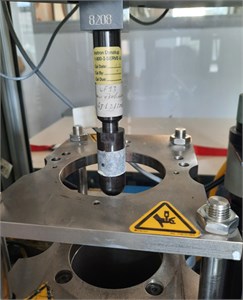
3.2. Test setup and measurement conditions for modal analysis
The test apparatus was similar to the device described by Wojtowicki et al. [9] where the specimen center is drilled in order to be clamped to the shaker with bolts, see Fig. 2. For this device, the holes can disturb the beam behavior due to the induced stress concentration. Therefore, a modified bench allowing fixing the sample between two small aluminum clamps, without external mass addition has been designed for this study. The clamping torque was set to 13 Nm. A PCB accelerometer was fixed to the end of the specimen of the shaker, at point M1, in order to measure the acceleration a(M1) imposed to the sample. Then, the vibration velocity v(M2) of the free end of the beam, at point M2, was measured by a vibrometer sensor head Polytec-OFV-503 coupled to a controller unit Polytec-OFV-500, via a mirror inclined at 45 above M2. A real-time signal analyzer Pulse LabShopB&K gave the frequency resp function H(ω) between v(M2) and a(M1).
4. Modal analysis results
Fig. 3 provides the mean response spectra obtained by a random excitation for three specimens of the stratification S1 impacted at three different energies, 0.8, 0.9 and 1 J. A shift of the resonant frequencies in the frequency response function (FRF) curves is noticed for the different specimens. In addition, this shift depends on the applied impact energy. However, the shape of the FRF curves is the same regardless of the applied impact energy. The shift observed in the FRF responses is due to the influence of impact energy on impact-induced damage of flax/epoxy composite samples.
Fig. 2Vibration test setup for modal analysis
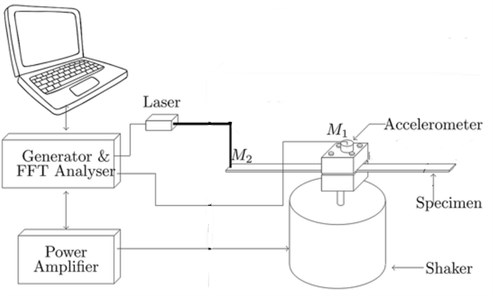
Fig. 3Frequency response functions for 0.8 J, 0.9 J and 1 J with S2
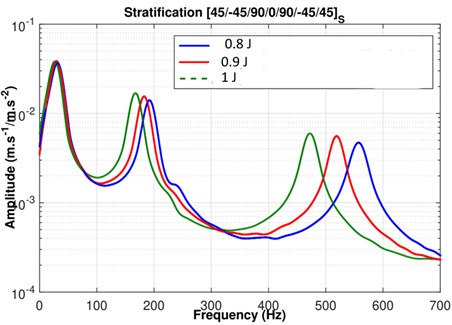
4.1. Modal damping ratio
For modal damping ratio estimation, the half-power bandwidth method has been used. It is applied on the FRF measured from vibration tests of the structure. It has been shown that this method is sufficiently accurate for a number of practical cases in which the damping ratio is less than 0.1, which has been verified in our case. Since the damping ratio is low, normalized damping ratio has been calculated and presented. Fig. 4 provides results of normalized damping ratio (%) for the three first natural modes depending on different impact energies. As shown in Fig. 4, the normalized damping ratio (%) increases when the impact energy increase. In other terms, the energy stored in the oscillation is more dissipated when the impact energy is more important
4.2. Modal stiffness
To see how the damage can affect the structure, another modal parameter has been studied. Modal stiffness indicates the capacity of the structure to resist deformation. This parameter is obtained using damping ratio values. For every modal testing, modal stiffness has been calculated and presented. Fig. 5 provides results of modal stiffness processing according to stratification and impact energy. As shown in this figure the normalized modal stiffness for S1 decreases when the impact energy increase. So that, when the impact energy is higher, the induced damage is more significant and the structure is, as well, more deteriorated. Thus, mechanical properties are considerably attenuated and the capacity of the structure to resist deformation is weakened.
Fig. 4Normalized damping ratio (%) of the first three modes for the 3 impact energy levels 0.8, 0.9 and 1 J
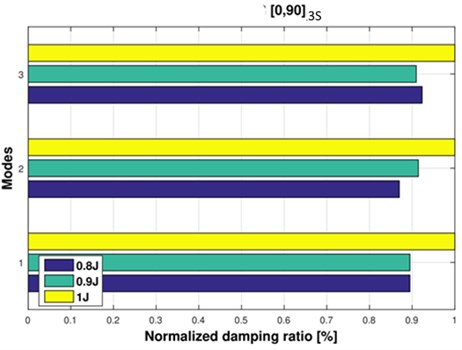
Fig. 5Normalized modal stiffness (%) of the first three modes for the 3 impact energy levels 0.8, 0.9 and 1 J
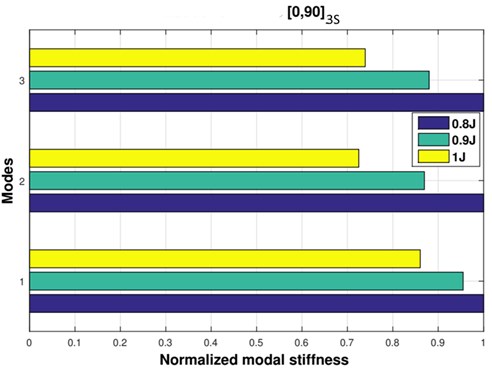
5. Conclusions
Modal analysis techniques have been used for damage identification in composite-based structural systems. Several parameters are studied to show the correlation between the modal response and a damage. Natural frequency, damping ratio and modal stiffness are indicators of the health integrity of a structure. The main goal of this study was to verify if vibratory analysis could testify the presence of an invisible or a barely visible impact damage in a flax/epoxy composite structure. Eventually, the goal was reached. The offset of frequency response curves confirms the influence of the impact energy on flax/epoxy composite samples. As a matter of fact, a decrease in natural frequencies is observed, when the impact energy increases. For the damping ratio, results are more conclusive. The damping ratio (%) increases when the impact energy increase. So, when the impact energy is more important the dissipation energy increases as well.
For modal stiffness, modal stiffness decreases when the impact energy increase. Namely, flax/epoxy composite samples capacity to resist deformation diminishes with the damage severity in the structure.
This study emphasizes on the influence of the damage severity in terms of modal analysis parameters. However, the current feed-back of the study proves to be deficient for the localization of these induced-impact damages, which will be the purpose of future work.
References
-
A. Bourmaud, J. Beaugrand, D. U. Shah, V. Placet, and C. Baley, “Towards the design of high-performance plant fibre composites,” Progress in Materials Science, Vol. 97, pp. 347–408, Aug. 2018, https://doi.org/10.1016/j.pmatsci.2018.05.005
-
Anselm Ogah, “Natural fiber polymer composites: A review,” Advances in Polymer Technology, Vol. 18, No. 4, pp. 351–363, Jan. 1999.
-
W. D. Brouwer, “Natural fibre composites: Where can flax compete with glass?,” SAMPE Journal, Vol. 36, No. 6, pp. 18–23, Nov. 2000.
-
A. Bos, “Agglomeration in suspension,” Ph.D. thesis, 1983.
-
D. Gay, Matériaux Composites. Hermes, 1997.
-
F. Bensadoun, D. Depuydt, J. Baets, I. Verpoest, and A. W. van Vuure, “Low velocity impact properties of flax composites,” Composite Structures, Vol. 176, pp. 933–944, Sep. 2017, https://doi.org/10.1016/j.compstruct.2017.05.005
-
C. Baley, M. Gomina, J. Breard, A. Bourmaud, and P. Davies, “Variability of mechanical properties of flax fibres for composite reinforcement. a review,” Industrial Crops and Products, Vol. 145, p. 111984, Mar. 2020, https://doi.org/10.1016/j.indcrop.2019.111984
-
G. Y. Xu, W. D. Zhu, and B. H. Emory, “Experimental and numerical investigation of structural damage detection using changes in natural frequencies,” Journal of Vibration and Acoustics, Vol. 129, No. 6, pp. 686–700, Dec. 2007, https://doi.org/10.1115/1.2731409
-
J. Wojtowicki, L. Jaouen, and R. Panneton, “New approach for the measurement of damping properties of materials using the Oberst beam,” Review of Scientific Instruments, Vol. 75, No. 8, 2004.
About this article
This work has been supported by the Région Bourgogne Franche Comté and the European FEDER (Fonds Européen de Développement Régional).