Abstract
In this paper, a modal analysis is carried out on a novel composite material reinforced by Washingtonia Filifera palm fibers with a 20 % loading rate. The experimental analysis by the ”PULSE” vibrations acquisition device was carried out for a composite beam reinforced by the studied fiber. The determination of natural frequencies and modal damping is of great importance for the survival of structures. The precise knowledge of these frequencies allows the elimination of the resonance phenomenon in these structures. For this purpose, an excitation pot equipped with an impedance head is used, which allows the determination of the transfer function directly. Theoretical calculation of the six first vibrations modes is carried out which are compared with experimental results. Dynamic studies show the possibility of using this biomaterial in industrial real operating conditions.
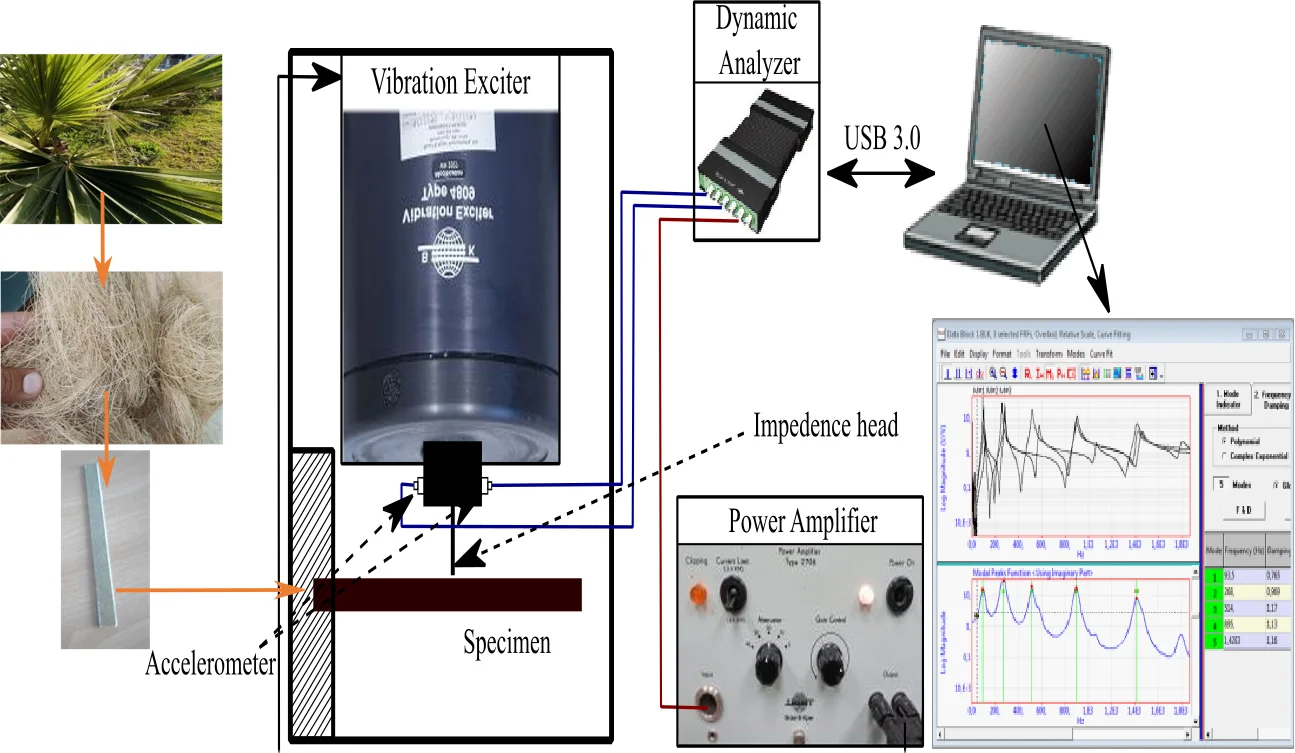
Highlights
- A modal analysis is carried out on a novel composite material reinforced by Washingtonia Filifera palm fibers with a 20% loading rate.
- The experimental analysis by the "PULSE" vibrations acquisition device was carried out for a composite beam reinforced by the studied fiber.
- Theoretical calculation of the six first vibrations modes is carried out which are compared with experimental results.
- Dynamic studies show the possibility of using this biomaterial in industrial real operating conditions.
1. Introduction
The industry demand for new materials that have excellent properties based on natural cellulosic fibers contributed to the creation of several novel fibers such as, Kenaf [1], flax [2], hemp [3], Diss [4], Banana [5], okra [6]. Different numerical approaches have been proposed to calculate natural frequencies whatever the vibratory behavior, for example longitudinal [7] and torsional [8].
Bernoulli’s theory has been used in different research works such as in [9], where authors analyzed the static behavior of nanobeams. The dynamic study by vibratory analysis allows the calculation of the natural frequencies of healthy or damaged materials. For this reason, several research works in the literature aim to find appropriate solutions for the determination of the dynamic behavior of composite materials by using samples in the form of beam or plate and microbeam [10]. The study of the bending vibration of such structures is essentially based on the search for frequencies and natural modes. Authors in [11] experimentally analyzed using the modal method the free vibration characteristics of short sisal fiber polyester (SFPC) and short banana fiber (BFPC) composites, it has been found that there is an increase in the fiber content, mechanical properties and natural frequencies. An experimental analysis was carried out in [12] to study the linear and non-linear vibrations on composites reinforced with flax fibers and the effect of natural viscoelastic layer. The proposed procedure consists of the excitation of samples with different amplitude levels in the six bending modes.
Researchers in [13] analyzed the effect of the orientation of natural fibers on the composite material by vibratory analysis. Dynamic properties were determined from the vibration measurements using the PULSE hammer at 1 kHz frequency. The analysis was applied to beam samples with the objective of studying the dynamic behavior of natural fiber reinforced polymer composites (NFPC) using different fiber orientations and lengths of the composite beams. The authors found that damping increased at 45° fiber orientation and then decreased. Finite element frequency analysis showed a relatively good agreement with the measured natural frequencies.
A comparative study for the dynamic responses of damaged and undamaged materials was conducted by Vigneshwaran et al. [14]. Vibratory characteristics of natural fiber-reinforced polymer composites have been studied with different vibration analysis techniques on natural fiber composites such as the finite element method. The vibration properties of flax fiber reinforced composites have been characterized by Prabhakaran et al. [15], and compared to fiber glass reinforced composites. In their study, three composite materials of different types (glass, linen, combination of glass and linen) were analyzed with vibration tests. In the research work [16], authors conducted experimental and numerical tests to determine the vibration behavior and damping performance of the flax fiber reinforced epoxy. After identification of natural frequencies and modal damping, the experimental results show that the modal damping is greater when the flax fibers are oriented at 90°. The viscoelastic behavior is described through a complex representation of mechanical properties considered constant in all layers, each mechanical parameter is identified from the first experimental mode. However, for synthetic fibers such as glass, the study analyzed numerically, and experimentally shell vibration laminated cylindrical fiber glass / epoxy composite [17]. The B&K FFT analyzer was used to experimentally extract the natural frequencies of vibrations by performing nondestructive tests. The authors found that vibration frequencies decrease with increasing temperature and humidity. The vibratory behavior of glass / epoxy composite laminates according to two higher order theories and a simulation model has been examined in [18]. A comparison of the responses was performed by experimental analysis using a three-point bending test with modal analysis for static and free vibration cases. On the other hand, the vibrations of the composite beam reinforced by natural and synthetic fibers with different boundary conditions has been analyzed in [19]. These beams are made with a unidirectional orientation for the measurement of transverse vibration with different end configurations. A comparison was made with the analytical and modal method by ANSYS. Vibration tests are performed using the LabVIEW software. To study the influence of the loading rate, authors in [20] analyzed the polyester composite reinforced with banana fibers with different loading rates. The natural frequencies and the temperature of the viscoelastic properties are reported. The research work [21] studied composites based on natural fibers in vibration with different percentages of jute fiber. An experimental modal analysis is performed on the samples. The authors found that adding 5 % of nanoclay and 15 % of jute increases the natural frequencies of this composite.
The Washingtonia Filifera (WF) plant is organic and environmentally friendly which is found in abundance in gardens. When it is cut, most of the time it is thrown away without using it in useful applications. In a previous study [22], the thermo-physico-chemical and statistical mechanical properties of WF have been identified and compared with other natural fibers in order to alert manufacturers to exploit it.
A mechanical and thermophysical studies were carried out in [23] on 20 % loading rate palm fibers Washingtonia filifera reinforced composite (WF20% / HDPE). The tensile tests has given an elongation of 17 % and a maximum stress of 15 MPa, a Young’s modulus of 858.6 MPa. The XRD analysis showed a crystallite number of 59.2 % with a size of 23 nm. TGA and DTG thermal analyzes were carried out experimentally by thermogravimetry, the results clearly showed a thermal stability of this composite at 210 °C, a residual mass of 2.5 with a maximum temperature of 745 °C. In this work, dynamic analysis is carried out to determine the properties of the composite materials reinforced by the Washingtonia Filifera vegetable fiber with a 20 % loading rate. A comparison with dynamic properties results based on in the Euler Bernoulli theory was also performed. These characterizations allow the choice of composite materials properties that meet the requirements of industrial uses.
2. Experimental procedure
2.1. Used materials and biocomposite preparation
Washingtonia Filifera palm plants are widely grown in the forest of Annaba and Skikda (Algeria) forests. The fiber of this plant has been investigated previously by the authors [22]. Firstly, the fibers are easily cut manually and immersed in distilled water in order to clean the surface of the fiber, see Fig. 1(a) and Fig. 1(b). Then, they are stored in a hot air oven for 24 hours at 105 °C to remove moisture.
Fig. 1Washingtonia Filifera plant and extracted fibers
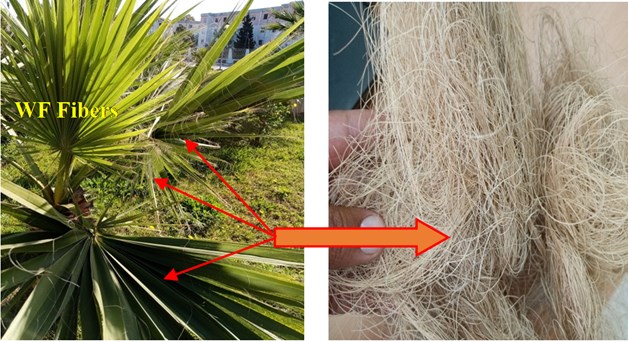
In order to prepare the biocomposite plates, the granola of plastic is mixed with high density polyethylene grade 5502 (HDPE) (a commercial product of "POLYMED" company) and 20 % of Washingtonian Filifera fiber at an angular speed of 32 revolutions per minute and at a temperature of 175 °C and using a mixer that has two cylinders rotating in opposite direction (Fig. 2(a)). Then, a composite film is obtained which is cut into small square pieces using a cutter (Fig. 2(c)). Next, the resulting elements are inserted into a mold (Fig. 2(d)) on the hot press (Fig. 2(g)). The hot press having two-plates is adjusted into a cycle of five steps to prepare the composite plate as follows:
1) Preheating of the mold until a temperature of 77 °C with a pressure of 10 bars for 1 min;
2) Heating until 177 °C with a pressure of 30 bars for 3 min;
3) Precooling of the mold until 80 °C with a maximum pressure of 100 bars for 7 min;
4) Cooling until 40 °C with a pressure of 50 Bars for 4 min;
5) Finally, a cooling until 30 °C with a pressure of 1 Bars for 5 min Fig. 2(f).
In order to be dynamically tested, the composite plate is cut in to beam (Fig. 2(g)), having a length, width and thinness of 230 mm, 20 mm and 4 mm respectively
2.2. Scanning electron microscopy (SEM)
The SEM technique is used for the evaluation of surface morphology such as surface roughness. In this work, the SEM (JEOL-7600F) images were exploited at an acceleration voltage of 10 kV for the longitudinal surface of the WF fiber.
2.3. Dynamic characterization
In the vibratory analysis experimental part, the assembly shown in Fig. 3 is used for the measurement of the frequency response functions (FRFs) of the beam. The excitation and the measurement of the vibratory response are ensured by a B&K8001 impedance head (force sensor and accelerometer), fixed directly on the electrodynamic exciter. The sensitivities of the force sensor and the accelerometer are respectively 5 or 10 mV/N for the force sensor and 50 or 100 mV/g for the accelerometer with a [0 Hz-3.5 kHz] measuring range. The excitation is transmitted to the beam with a metal rod attached to the impedance head which, in turn, is attached to the end of the electrodynamic exciter. The beam is excited by a white noise generated by the Pulse Vibration Analyzer B & K 16.1 and amplified by a 2706 B & K power amplifier. The advantage of this technique of measuring FRFs, from which frequencies and modal damping are determined, is the absence of added mass to the structure (no sensor is glued to the beam). In the case of structures with low mass and thickness, the mass of the sensor may have a great influence on their natural frequencies.
Fig. 2Biocomposite manufacturing process: a) mixer machine; b) rollers; c) cutting of biocomposite film; d) cut biocomposite film in the mold; e) hot press; f) obtained biocomposite plate; g) cutting of the biocomposite into beams
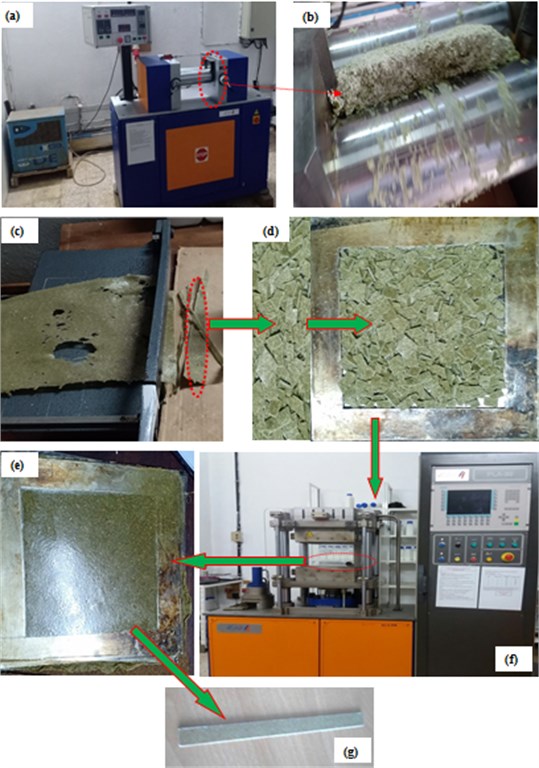
3. Results and discussion
3.1. SEM analysis
SEM images of the longitudinal surface of WF fibers which are given in Fig. 4 that the surface is rough with the presence of lignin.
Fig. 3Schematic view of the dynamic test setup
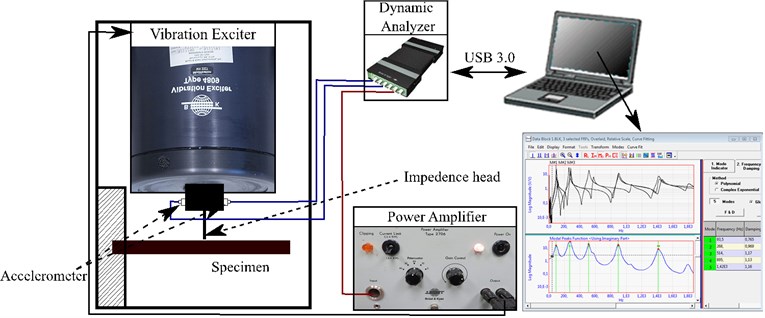
Fig. 4SEM image of longitudinal WF fibers
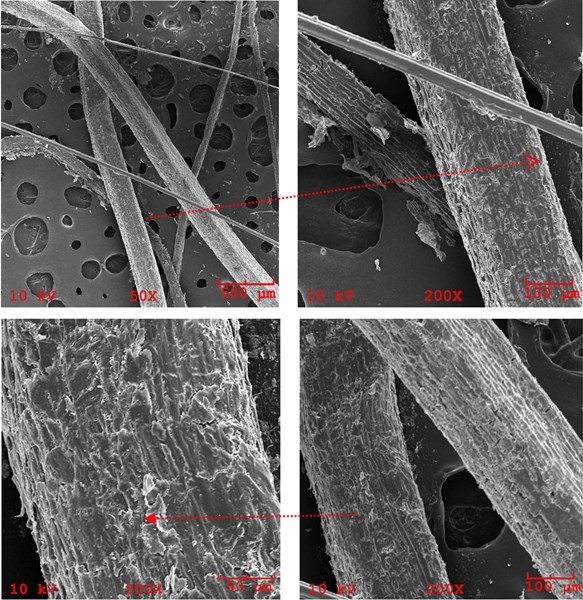
4. Modal analysis of the (WF 20% / HDPE) composite
The dimensions of the composite beam with a 20 % loading rate are given as follows:
– A total length of L= 0.23 m (the embedded-free part of the beam l= 0.2 m),
– a drop b= 0.02 m,
– the thickness h= 0.004 m,
– a mass m= 18.7 g,
– the density is calculated by a 1016.3 Kg/m3 of mass to volume ratio,
– the Young’s modulus E= 858.6 MPa [23] is experimentally determined by a tensile test,
– the moment of inertia I=bh3 / 12 = 0.1067×10-9 m4
– the section S= 80×10-6 m2.
In order to be compared with experimental measurements of the natural frequencies, the theoretical natural frequencies are calculated using Eq. (1), in which the effects of shear and rotational inertia are neglected:
where Xp is wave numbers, the with f1= 14.85 Hz, f2=93.07 Hz, f3= 260.64 Hz, f4=510.8 Hz, f5=844.15 Hz, f6=1261.4 Hz.
In Fig. 6, an example is given of the frequency response function of the beam, which shows the first six modes. The good synchronization between the force sensor and the accelerometer allows obtaining frequency spectra clearly showing all the resonances and anti-resonances of the beam. The values of the frequencies and the modal damping are presented in Table 1. The average of the modal damping of the first six modes is 0.66 %, which corresponds to the depreciation of the composite material
Fig. 5FRF frequency response as function of a WF 20 % / HDPE composite beam
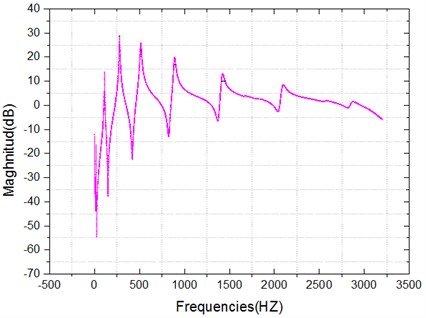
From the frequency response curve in Fig. 5, natural frequencies and modal dampings ζp are determined for each vibration mode, using the –3 dB band width given by Eq. (2):
where fp is peak frequency. In Fig. 5, the first mode does not appear clearly and is hidden by ranked high modes. To remedy to such issue, FRF's in low frequency is measured in the band [0-200 Hz].
The frequency extraction and modal damping of the beam from the FRFs is obtained by ME' Scope VES'4 software, which uses the –3 dB bandwidth method for the calculation of modal damping. Fig.6 shows the superposition of the FRFs measured in three different points of the beam to ensure that natural frequencies are not missed by measuring on one of its vibration nodes.
Fig. 7 gives a comparison between experimental and theoretical natural frequency results, which show a good agreement. The natural frequencies of the first four modes obtained experimentally are close to those obtained by Eq. (1). The differences existing between them are due to the experimental conditions that cannot be respected given the fragility of the composite material that risks to shear under the effect of clamping, and also due to the heterogeneity of the composite. For the fifth and sixth modes, the difference between the theoretical and experimental results increases with the increase of the rank of the modes Fig. 7, which is explained by not taking into account of the shear effect and the rotational inertia in Eq. (1).
Fig. 6Modal damping: a) modal frequencies; b) damping s obtained from FRF’s by ME’ Scope VES'4 software
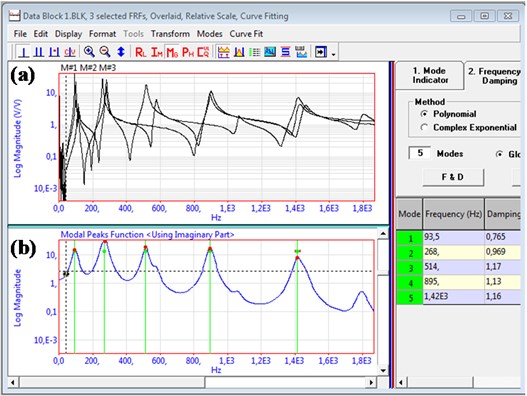
Table 1Comparison between the experimental and the theoretical results of the composite beams
Composite 20 %WF/ HDPE | Frequencies (Hz) | |||||||||||
Mode 1 | Mode 2 | Mode 3 | Mode 4 | Mode 5 | Mode 6 | |||||||
f1 Hz | ζ1 % | f2 Hz | ζ2 % | f3 Hz | ζ3 % | f4 Hz | ζ4 % | f5 Hz | ζ5 % | f6 Hz | ζ6 % | |
Experimental | 15 | 0.55 | 93.5 | 0.765 | 268 | 0.969 | 514 | 1.17 | 895 | 1.13 | 1420 | 1.16 |
Theory | 14.85 | – | 93.07 | – | 260.64 | – | 510.8 | – | 844 | – | 1261 | – |
Fig. 7Comparison between theoretical and experimental natural frequencies results
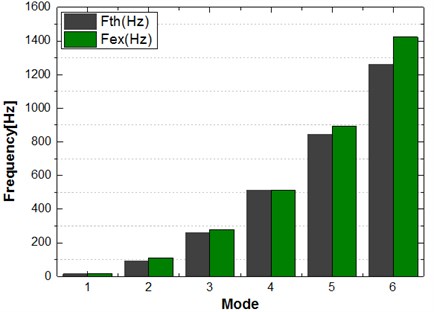
5. Conclusions
In this work, a vibration analysis was carried out in order to study the dynamic properties of Washingtonia Filifera vegetable fiber reinforced composite materials at a 20 % loading rate. The determination of the dynamic response is then treated using the Euler Bernoulli approach. The experimental and theoretical results of this study show that the composite material is characterized by the following properties:
– The six first modes of vibrations have been calculated theoretically and compared with those obtained experimentally.
– The comparison of the two results shows a good agreement until the mode 6 where the discrepancy is noticed due to the neglected effects of shear and rotational inertia.
According to the results obtained in the research works using the Washignonia Filifera as a reinforcing fiber, the current study further highlight using a modal analysis the properties of the resulting composite material which allows it to be used in various industrial and structural applications.
References
-
S. N. A. Khalid et al., “Mechanical performances of twill kenaf woven fiber reinforced polyester composites,” International Journal of Integrated Engineering, Vol. 10, No. 4, pp. 49–59, 2018.
-
C. Baley and A. Bourmaud, “Average tensile properties of French elementary flax fibers,” Materials Letters, Vol. 122, pp. 159–161, May 2014, https://doi.org/10.1016/j.matlet.2014.02.030
-
A. Keller, “Compounding and mechanical properties of biodegradable hemp fibre composites,” Composites Science and Technology, Vol. 63, No. 9, pp. 1307–1316, Jul. 2003, https://doi.org/10.1016/s0266-3538(03)00102-7
-
B. Mustapha, I. Bahim, B. Mourad, and B. Abderrahim, “Effect of fiber volume fraction in the tensile properties of renewable Diss fiber /polyester composite,” Engineering Solid Mechanics, Vol. 4, pp. 91–96, 2016, https://doi.org/10.5267/j.esm.2015.11.002
-
M. M. Ibrahim, A. Dufresne, W. K. El-Zawawy, and F. A. Agblevor, “Banana fibers and microfibrils as lignocellulosic reinforcements in polymer composites,” Carbohydrate Polymers, No. 81, pp. 811–819, 2010.
-
I. M. de Rosa, J. M. Kenny, D. Puglia, C. Santulli, and F. Sarasini, “Morphological, thermal and mechanical characterization of okra (Abelmoschus esculentus) fibres as potential reinforcement in polymer composites,” Composites Science and Technology, Vol. 70, No. 1, pp. 116–122, Jan. 2010, https://doi.org/10.1016/j.compscitech.2009.09.013
-
M. Yayli, F. Yanik, and S. Y. Kandemir, “Longitudinal vibration of nanorods embedded in an elastic medium with elastic restraints at both ends,” Micro and Nano Letters, Vol. 10, No. 11, pp. 641–644, Nov. 2015, https://doi.org/10.1049/mnl.2014.0680
-
M. Yayli, S. Y. Kandemir, and A. E. Çerçevik, “Torsional vibration of cracked carbon nanotubes with torsional restraints using Eringen’s nonlocal differential model,” Journal of Low Frequency Noise, Vibration and Active Control, Vol. 38, No. 1, pp. 70–87, Mar. 2019, https://doi.org/10.1177/1461348418813255
-
M. Yaylı, “Bending Analysis of A cantilever nanobeam with end forces by laplace transform,” International Journal of Engineering and Applied Sciences, Vol. 9, No. 2, pp. 103–103, Jun. 2017, https://doi.org/10.24107/ijeas.314635
-
M. Yaylı, S. Yerel Kandemir, and A. E. Çerçevik, “A practical method for calculating eigenfrequencies of a cantilever microbeam with the attached tip mass,” Journal of Vibroengineering, Vol. 18, No. 5, pp. 3070–3077, Aug. 2016, https://doi.org/10.21595/jve.2016.16636
-
K. Senthil Kumar, I. Siva, P. Jeyaraj, J. T. Winowlin Jappes, S. C. Amico, and N. Rajini, “Synergy of fiber length and content on free vibration and damping behavior of natural fiber reinforced polyester composite beams,” Materials and Design (1980-2015), Vol. 56, pp. 379–386, Apr. 2014, https://doi.org/10.1016/j.matdes.2013.11.039
-
D. Hajer, E. M. Abderrahim, R. Jean-Luc, M. Charfeddin, T. Mohamed, and H. Mohamed, “Experimental analysis of the linear and nonlinear vibration behavior of flax fibre reinforced composites with an interleaved natural viscoelastic layer,” Composites Part B: Engineering, Vol. 151, pp. 201–214, Oct. 2018, https://doi.org/10.1016/j.compositesb.2018.06.015
-
M. Z. Rahman, B. R. Mace, K. Jayaraman, and N. Zealand, “Vibration damping of natural fibre-reinforced composite materials,” in ECCM17 – 17th European Conference on Composite Materials, pp. 26–30, 2016.
-
K. Vigneshwaran, G. Rajeshkumar, and V. Hariharan, “Vibration characteristics of natural fiber reinforced polymer composites – a review,” in International Conference on Recent Trends in Engineering and Management, pp. 13–16, 2014.
-
S. Prabhakaran, V. Krishnaraj, M. S. Kumar, and R. Zitoune, “Sound and vibration damping properties of flax fiber reinforced composites,” Procedia Engineering, Vol. 97, pp. 573–581, 2014, https://doi.org/10.1016/j.proeng.2014.12.285
-
S. Mahmoudi, A. Kervoelen, G. Robin, L. Duigou, E. M. Daya, and J. M. Cadou, “Experimental and numerical investigation of the damping of flax-epoxy composite plates,” Composite Structures, Vol. 208, pp. 426–433, Jan. 2019, https://doi.org/10.1016/j.compstruct.2018.10.030
-
M. Biswal, S. K. Sahu, and A. V. Asha, “Vibration of composite cylindrical shallow shells subjected to hygrothermal loading-experimental and numerical results,” Composites Part B: Engineering, Vol. 98, pp. 108–119, Aug. 2016, https://doi.org/10.1016/j.compositesb.2016.05.037
-
S. S. Sahoo, S. K. Panda, and T. R. Mahapatra, “Static, free vibration and transient response of laminated composite curved shallow panel – An experimental approach,” European Journal of Mechanics – A/Solids, Vol. 59, pp. 95–113, Sep. 2016, https://doi.org/10.1016/j.euromechsol.2016.03.014
-
Manan S. Shah, Mr. Jay H. Khatri, Dr. Haresh P. Patolia, and Mr. Ketul B. Brahmbhatt, “Vibration analysis of natural fiber composite beam under various end conditions,” International Journal of Engineering Research and Technology, Vol. 7, No. 5, pp. 6–13, May 2018, https://doi.org/10.17577/ijertv7is050048
-
L. A. Pothan, Z. Oommen, and S. Thomas, “Dynamic mechanical analysis of banana fiber reinforced polyester composites,” Composites Science and Technology, Vol. 63, No. 2, pp. 283–293, Feb. 2003, https://doi.org/10.1016/s0266-3538(02)00254-3
-
S. Arulmurugan and N. Venkateshwaran, “Vibration analysis of nanoclay filled natural fiber composites,” Polymers and Polymer Composites, Vol. 24, No. 7, pp. 507–516, Sep. 2016, https://doi.org/10.1177/096739111602400709
-
D. E. Gaagaia, M. Bouakba, and A. Layachi, “Thermo-physico-chemical and statistical mechanical properties of Washingtonian filifera new lignocellulosic fiber,” Engineering Solid Mechanics, Vol. 7, No. 2, pp. 137–150, 2019, https://doi.org/10.5267/j.esm.2019.3.002
-
D. E. Gaagaia, M. Bouakba, M. D. M. Barbero-Barrera, L. Abdelheq, and N. Boutasseta, “Physico-chemical and thermomechanical analysis and characterization of a thermoplastic composite material reinforced by Washingtonia Filifera novel vegetable fibers,” in International Journal of Engineering Research in Africa, Vol. 59, pp. 43–55, Mar. 2022, https://doi.org/10.4028/p-8ew64s
Cited by
About this article
The authors have not disclosed any funding.
The datasets generated during and/or analyzed during the current study are available from the corresponding author on reasonable request.
Ramdane Youns performing the experiments, and data collection. And using the new head impedance method. Nouredine Ouelaa analyze the experimental results and also compare them with the theoretical results (Bernoulli equation). Nadire Boutessta check the language and correction of the article.
The authors declare that they have no conflict of interest.