Abstract
Unilateral external fixator is commonly used to stabilize initial fractured bone for polytraumatised patients, which is simple and effective method. The stiffness property of the external fixator has a great influence on the local biomechanical environment of bone tissue. In order to investigate the rigidity characteristics of a novel fixator with serrated structure through comparing the stiffness of the Sarafix fixator and the novel fixator in experimental measurement. Polyacetal tubes simulating human tibia were fixed in novel fixator. Axial stiffness, torsional stiffness and bending stiffness of novel fixator were measured through universal material testing machine. In order to improve reliability, corresponding test must be repeated ten times. Due to the improvement of novel fixator’s structural, which has serrated connection between fixator joints, the performance of the novel fixator is better than Sarafix fixator under bending and torsional loads, there is no big difference in axial load for two fixators. The novel fixator has good stiffness properties, the novel fixator with serrated structure plays an important role to improve the stiffness of the novel fixator system. These analysis results can also aid the performance assessment of an novel external fixator and facilitate appropriate application of such a device.
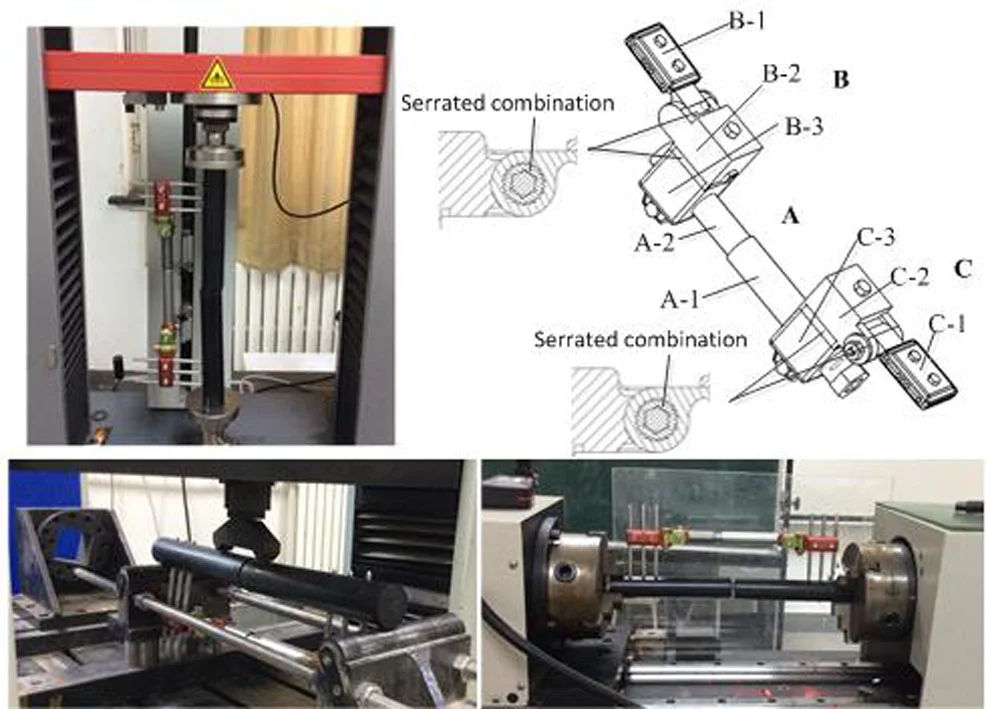
Highlights
- The mechanical properties of the novel fixator can be obtained through comparing the stiffness of the Sarafix fixator
- Axial stiffness, torsional stiffness and bending stiffness were measured in experiments
- The novel fixator performed better than the Sarafix external fixator when applied bending load and torsional load
1. Introduction
Unilateral external fixator is commonly used to stabilize initial fractured bone for polytraumatised patients who are prone to complications [1, 2]. If orthopedist can use the fixator well, the risk of complications is reduced to a very low level [3-8]. The mechanical environment has a great influence on the callus formation during the initial healing period. The stiffness of the fixator is important, because the motion of the device has not only effect on fracture correction and healing of bone tissue, but also affects the loosening of pin. This can easily lead to treatment failure if this factor is inadequate [9-11]. Many researchers have studied the stiffness of external fixators in terms of physiology under axial compression, bending and torsional loads, which will result in different mechanical environments in the fractured site [12-15]. They also equipped load sensor on external fixator to evaluate their characteristics [16, 17]. Different kinds of fixators have different loading paths, which exhibit different stiffnesses [18, 19]. Better understanding the stiffness of fixator helps adapt to reach the desired interfragmentary movement during the later consolidation stages [20]. In addition, well understanding fixator stiffnesses could help to control interfragmentary motion during bone healing process [21, 22].
Sarafix fixator is known by the world, which won a lot of awards and prizes at international exhibitions [23]. Because the Sarafix fixator stiffness have been proven to have a good clinical result by experiment research in the treatment of bone fractures [23]. But the mechanical properties of the novel fixator has not been known, in order to investigate whether this novel fixator has sufficient stiffness. The mainly aim of this study was to comparing the stiffness of the Sarafix fixator and this novel fixator, investigating the stiffness characteristics of the novel fixator.
2. Materials and methods
2.1. The new fixator
The titanium central body (A) of the new fixator (Fig. 1) is extension rod, which constructed in two parts: A-1 and A-2. The two parts slide in a groove (range 0-4 cm). The central body rotary nut controls this motion. Rotaring 360 degrees can be obtain a 1 mm of axial movement. On the one side of the central body is connected to the pin clamps (B and C). The material of pin clamps are titanium. They are composed of three parts (B-1, B-2, B-3 and C-1, C-2, C-3). On both sides of the central body, three components are connected with serrated discs. Serrated connection can effectively improve close link between fixator joints shown in Fig.1, thus enhancing the fixation between joint components. The unilateral external fixator has a limited adjustability [24]. But this novel fixator has greater adjustment ability, because the components of pin clamp (B-1 and C-1) allow 120-degrees rotation around the axis. Joint components of the B-2, C-2, B-3 and C-3 allows a rotational movement of 360 degrees in each directions show as in Fig. 1. The connector nuts on pin clamps are responsible for locking these joints by a torque wrench. Therefor this novel fixator not only has tight connections, but also has great regulation ability.
Fig. 1The three-dimensional structure of the novel external fixator
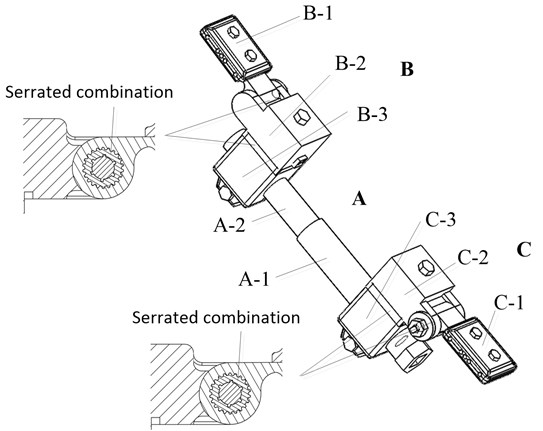
2.2. Test setup
Two polyacetal bars simulating tibia were used polyacetal model with 32 mm in diameter and 180 mm in length, and fixed with six pins (6 mm in diameter), there are three pins on each side of the polyacetal model. The distance between the most inner pins was 200 mm, and the length between the bone model and the fixator was 45 mm. The distance between the two pins is 20 mm (Fig. 2) at the each side of fixator. The fracture gap is 4mm.
Compression testing was tested at the Laboratory, as shown in Fig. 3. At the Laboratory, the novel fixator was performed on the axial load by using a universal material testing machine. The novel fixator was attached to proximal and distal polyacetal bars. During the testing, the load (0 to 600 N at the rate of 5 N/s) is applied on the proximal tibia model and dixtal tibia model was fixed.
Torsional load test was carried out by the proximal bone model in relation to the fixed distal segment. The torsional test were subject to a maximum load of 15 N.m at the rate of 4 N/s. We put cylindrical bearing constraint at the end of the upper segment of bone model in the appropriate place as shown in Fig. 4.
The bending tests were conducted using a servohydraulic testing machine LFV-50-HH (Walter Bai, Switzerland; Fig. 5) with a maximum load of 500 N, which has DIGWIN 2000-EDC120 digital control system. The loading and unloading speed was 5 N/s during the test.
Fig. 2A novel external fixator with fragments apart
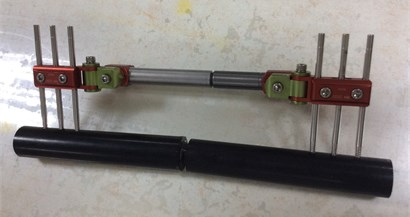
Fig. 3Experimental testing of novel fixator under compression load
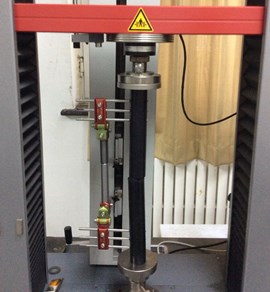
Fig. 4Experimental testing of novel fixator under torsional load
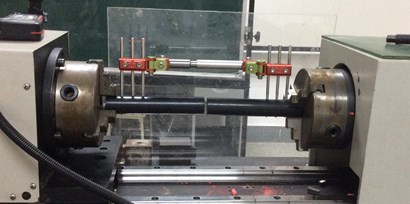
Fig. 5Experimental testing of novel fixator under 4-P bending
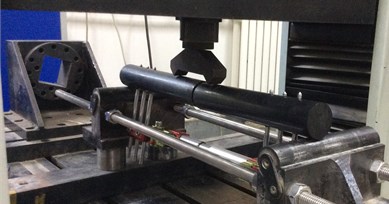
For both devices, measurements in compression, torsion and 4-P bending were measured ten times in order to enhance reliability. In every measurement, the whole device has to pull out six pins, and reassembled the entire fixator and bone model. Statistical analysis is adopted to use means and standard deviation calculation.
3. Results
The measurement results in the ten experimental groups show a fair share of statistically significant differences.
As shown in Fig. 6, the force with a maximum of 600 N in axial direction applied in fixator side will lead to higher rigidity of the Novel fixator (4.15±0.2 mm), when compared with the Sarafix fixator (4.35 mm). And with a increase of the axial load, the axial displacements of two fixator systems are also increased. Compare the growth rates of displacements of two fixators, Although there is no obvious stiffness difference between two fixators, but the Novel fixator show a relatively lower rate of growth, indicate that the axial stiffness of Novel fixator (144.57±6.64 N/mm) is relative slightly higher than that of sarafix fixator (137.93 N/mm).
As shown in Fig. 7, similar to axial stiffness, when applied the maximum torsional load (15 N/m), the rotation resultant was 4.43 degree for the Novel Fixator compared with (4.0±0.2 degree) for the Sarafix fixator (p< 0.005). The torsional angle with the increase of the load present a linear growth trend. The Novel fixator also show a relative lower rate of growth for torsional angle. Compare the torsional stiffness of two fixators, the torsional stiffness of Novel fixator (214.90±10.25 N/mm) is higher than that of sarafix fixator (197.37 N.m/rad), indicating that the torsional strength of the novel fixator is enough, when compared with sarafix fixator.
Fig. 6Axial force–displacement curve of the two fixator system for experimental testing. ‘■’ denote axial force–displacement curve of the novel fixator. ‘●’ denote axial force–displacement curve of the sarafix fixator (the data come from [1])
![Axial force–displacement curve of the two fixator system for experimental testing. ‘■’ denote axial force–displacement curve of the novel fixator. ‘●’ denote axial force–displacement curve of the sarafix fixator (the data come from [1])](https://static-01.extrica.com/articles/20909/20909-img6.jpg)
Fig. 7Torsional force–displacement curve of the two fixator system for experimental testing. ‘■’ denote torsional force-displacement curve of the novel fixator. ‘●’ denote torsional force-displacement curve of the sarafix fixator (the data come from [1])
![Torsional force–displacement curve of the two fixator system for experimental testing. ‘■’ denote torsional force-displacement curve of the novel fixator. ‘●’ denote torsional force-displacement curve of the sarafix fixator (the data come from [1])](https://static-01.extrica.com/articles/20909/20909-img7.jpg)
Fig. 8 show the bending force–displacement curve of the two fixator system, with the increase of bending load, bending displacement appears a linear upward trend. When applied the maximum bending load (500 N), Novel fixator produce a bending displacement of 2.59 mm, while Sarafix fixtor generate a bending displacement of 2.25±0.1 mm, indicate that the bending stiffness of Novel fixator (222.22±9.45 N/mm) is relative slightly higher than that of Sarafix fixator (193.05 N/mm). The bending stiffness of Novel fixator is not lower than that of Sarafix fixator.
Fig. 8Bending force-displacement curve of the two fixator system for experimental testing. ‘■’ denote bending force-displacement curve of the novel fixator. ‘●’ denote bending force-displacement curve of the sarafix fixator (The data come from [1])
![Bending force-displacement curve of the two fixator system for experimental testing. ‘■’ denote bending force-displacement curve of the novel fixator. ‘●’ denote bending force-displacement curve of the sarafix fixator (The data come from [1])](https://static-01.extrica.com/articles/20909/20909-img8.jpg)
4. Discussion
The vitro testing is conducted to compare the stiffness of two unilateral external fixators, one is commonly used Sarafix fixator, the other is the novel fixator. Sarafix fixator was generally considered to have good healing effect due to it has enough stiffness. By comparing the stiffness of two kinds fixator, judge whether the novel fixator has enough stiffness. In this study, the external fixators in every measurements were assembled in a standard configuration, so reused external fixators had no effect on the stiffness.
In this study, for sarafix fixator, the mean stiffness was only 95.407 % (axial load), 91.84 % (torsional load) and 86.87 % (bending load) compared with the novel Fixator. The novel fixator performed better than the Sarafix external fixator when applied bending load and torsional load, while no obvious difference was seen in axial loads for two fixators, as shown in numerical results of these two fixators. These results indicate that the novel unilateral fixator with serrated mechanism can improve the close connection between the joints of fixator, thereby increasing the stiffness of the fixator. The novel fixator has good stiffness properties mainly because of two reasons: the first one includes structural improvement in fixator, the second one is material improvement, we are committed to using new materials (titanium). These improvements help to reduce some problems related to application of the external fixator. In addition, good stiffness property make novel fixator is an useful method not only for fracture healing in orthopedic surgery, but also for war casualties.
This study also exists a lot of limitations, although experimental results of the novel fixator is favorable, but this should also be tested on the clinical experiment before a more practical and general conclusion can be made. So the novel fixator needs to be used in live animal or use in humans in the future. Nevertheless, the novel fixator still has sufficient stiffness to treat the injured tibia.
5. Conclusions
In conclusion, these results demonstrate that the structure of fixator plays an important role to improve the stiffness of the novel fixator system. Better understanding of an external fixator is crucial step toward its successful applications. These analysis results can also aid the performance assessment of a novel external fixator and facilitate appropriate application of such a device.
References
-
O’Brien P. J. Fracture fixation in patients having multiple injuries. Canadian Journal of Surgery, Vol. 46, 2003, p. 124-128.
-
Pape H. C., Giannoudis P., Krettek C. The timing of fracture treatment in polytrauma patients: relevance of damage control orthopedic surgery. The American Journal of Surgery, Vol. 183, 2002, p. 622-629.
-
Hayda R. A., Mazurek M. T., Powell Iv E. T., et al. From Iraq back to Iraq: modern combat orthopaedic care. Instructional Course Lectures, Vol. 57, 2008, p. 87-99.
-
Lin D. L., Kirk K. L., Murphy K. P., et al. Evaluation of orthopaedic injuries in operation enduring freedom. Journal of Orthopaedic Trauma, Vol. 18, 2004, p. 48-53.
-
Murray C. K., Hsu J. R., Solomkin J. S., et al. Prevention and management of infections associated with combat-related extremity injuries. The Journal of Trauma, Vol. 64, 2008, p. 239-251.
-
Tuttle M. S., Smith W. R., Williams A. E., et al. Safety and efficacy of damage control external fixation versus early definitive stabilization for femoral shaft fractures in the multiple-injured patient. The Journal of Trauma, Vol. 67, 2009, p. 602-605.
-
Zeljko B., Lovrc Z., Amc E., et al. War injuries of the extremities: twelve-year follow-up data. Military Medicine, Vol. 171, 2006, p. 55-57.
-
Aro H. T., Chao E. Y. Biomechanics and biology of fracture repair under external fixation. Hand Clinics, Vol. 9, 1993, p. 531-542.
-
Moss D. P., Tejwani N. C. Biomechanics of external fixation: a review of the literature. Bulletin of the NYU Hospital for Joint Diseases, Vol. 65, 2007, p. 294-299.
-
Willie B., Adkins K., Zheng X., et al. Mechanical characterization of external fixator stiffness for a rat femoral fracture model. Journal of Orthopaedic Research, Vol. 27, 2009, p. 687-693.
-
Finlay J. B., Moroz T. K., Rorabeck C. H., Davey J. R., Bourne R. B. Stability of ten configurations of the Hoffmann external-fixation frame. Journal of Bone and Joint Surgery, Vol. 69, Issue 5, 1987, p. 734-744.
-
Hoffmann R., Mckellop H. A., Sarmiento A., Lu B., Ebramzadeh E. Three-dimensional measurement of fracture gap motion. biomechanical study of experimental tibial fractures with anterior clasp fixator and ring fixator. Unfallchirurg, Vol. 94, Issue 8, 1991, p. 395-400.
-
Kassi J. P., Hoffmann J. E., Heller M., Raschke M., Duda G. N. Evaluating the stability of fracture fixation systems: mechanical device for evaluation of 3-d stiffness in vitro. Biomedical Technology, Vol. 46, Issue 9, 2001, p. 247-252.
-
Kowalski M., Schemitsch E. H., Harrington R. M., Chapman J. R., Swiontkowski M. F. Comp arative biomechanical evaluation of different external fixation sidebars: stainless-steel tubes versus carbon fiber rods. Journal of Orthopaedic Trauma, Vol. 10, Issue 7, 1996, p. 470-475.
-
Merloz P., Maurel N., Marchard D., Lavaste F., Barnole J., Faure C., Butel J. Three -dimensional rigidity of the ilizarov external fixator (original and modified) implanted at the femur. Experimental study and clinical deductions. Revue de Chirurgie Orthopédique et Réparatrice de l Appareil MoteurVol. 77, Issue 2, 1991, p. 65-76.
-
Draper E. R., Wallace A. L., Strachan R. K., Hughes S. P., Nicol A. C., Paul J. P. The design and performance of an experimental external fixation device with load transducers. Medical Engineering and Physics, Vol. 17, Issue 8, 1995, p. 618-624.
-
Draper E. R., Strachan R. K., Hughes S. P., Nicol A. C., Paul J. P. The design and performance of an experimental external fixator with variable axial stiffness and a compressive force transducer. Medical Engineering and Physics, Vol. 19, Issue 8, 1997, p. 690-695.
-
Caja V., Kim W., Larsson S., E Y. C. Comparison of the mechanical performance of three types of external fixators: linear, circular and hybrid. Clinical Biomechanics, Vol. 10, Issue 8, 1995, p. 401-406.
-
Vidal J. External fixation. yesterday, today, and tomorrow. Clinical Orthopaedics and Related Research, Vol. 180, 1983, p. 7-14.
-
Goodship A. E., Watkins P. E., Rigby H. S., Kenwright J. The role of fixator frame stiffness in the control of fracture healing. An experimental study. Journal of Biomechanics, Vol. 26, Issue 9, 1993, p. 1027-1035.
-
Beaupre G. S., Hayes W. C., Jofe M. H., White A. A. Monitoring fracture site properties with external fixation. Journal of Biomechanical Engineering, Vol. 105, Issue 2, 1983, p. 120-126.
-
Bishop N. E., Schneider E., Ito K. An experimental two degrees-of-freedom actuated external fixator for in vivo investigation of fracture healing. Medical Engineering and Physics, Vol. 25, Issue 4, 2003, p. 335-340.
-
Mešić Elmedin, Avdić Vahid Finite element analysis and experimental testing of stiffness of the sarafix external fixator. Procedia Engineering, Vol. 100, 2015, p. 1598-1607.
-
Paley, Tetsworth, K. Mechanical axis deviation of the lower limbs; preoperative planning of uniapical deformities of the tibia and femur. Clinical Orthopaedics and Related Research, Vol. 280, 1992, p. 48-64.
About this article
This work was supported by the National Natural Science Foundation of China under Grant No. 61273342, Beijing Natural Science Foundation under Grants No. 3132005, and the Evaluation and Extension of the Verification and Evaluation of the Metrology Instruments in the Domestic Quality Inspection under Z181100009518012.