Abstract
In this paper, effect on spring back values of different materials before and after laser bending are studied. Four different alloys were selected for laser bending test: Aluminum Alloy Al-5052M, Stainless Steel Alloy-304M, Low Carbon Steel (perpendicular rolling direction) and Titanium Alloy Ti-6Al-4V (TCL4). Thickness of alloys sheet is almost same. The influence of different mechanical parameters like tensile strength and hardness on spring back values before and after pre-loaded laser bending were analyzed. The results were compared which showed that Al-alloys has large amount of spring back even at small amount of displacement before laser bending which is due to their low tensile strength. But after laser bending titanium alloys have high value of spring back as compare to before pre-loaded laser bending value proving that this laser bending technique can be a useful method for those alloys which are not easy to deform at normal temperature.
1. Introduction and background study
Bending process is one of the important manufacturing techniques in sheet metal forming. Spring back is an important property of material during bending. Spring back occurs when material obtains its original shape during unloading of applied force. It is a complicated phenomenon which depends on material properties and process parameters [1-3]. Previously a lot of study has been done to calculate and find out the factors affecting the spring back. Mellor and Johnson [4] used rR=[1-3(∂yrET)+4(∂yrET)3] equation to calculate the spring back. Where r (mm) = internal radius curvature (before spring back), R (mm) = real internal radius curvature (after spring back), T (mm) = thickness of plate, E (N/mm2) = modulus of elasticity and σy (N/mm2) = yield stress. Values of r/R vary depending on the mechanical properties of material. The above equation has been used in many researches to calculate the spring back. In V-metal bending process Chen et al. [5] studied the spring back property and analyzed the results using Abaqus software. Albut [6] researched the sheet thickness effect on spring back by simulation. Thomas Schonbach [7] formed a new model to calculate and reduce the spring back during early stages of forming process. Dilip kumar [8] explained a finite element method which can be used for bending process of soft ferrous material like Al-alloys. Dr. Hani Aziz Ameen [9] calculated the effect of thickness and types of materials on spring back values using cylinder die for bending process by using ks=[(2Rit)+1]/[(2Rft)+1] equation to calculate the spring back factor.
During bending, metals are bound to show some amount of spring back due to their elastic recovery. Many practical attempts have been made to find out the spring back values as described earlier but those are on the basis of trial and error method. The current report is about the study of spring back of different alloys before and after pre-loaded laser bending process. Pre-loaded laser bending is a unique and relatively new forming technique in which at first by using mechanical clamp, a metal sheet is deformed then the elastic energy concentration region is scanned along a certain path by a laser beam as a heat source. Due to the heat treatment effect of laser beam, elastic energy of deformed region is concerted into plastic energy. As a result, deformation process can be accurate [10-12]. In recent years, there has been a lot of study for laser forming technique for those alloys which are difficult to deform mechanically at room temperature due to their high strength and toughness like titanium alloys.
2. Experimental study
Four different alloys sheet were selected for laser bending test. Table 1 showed the material details and the laser parameters used. The alloy sheet was cleaned with alcohol to remove any kind of dust and grease etc. The experimental work mainly consists of two steps: (1) Pre-loading: Firstly, the sheet was clamped to measure actual length and then certain compression force were applied to get some displacement change which appeared in the form of curve on the sheet metal. After that sheet was removed from the clamp and spring back was calculated. (2) Laser scanning process: Then the laser beam was irritated on the certain area of sheet along a specific path in the laser setup and finally spring back was measured when sample was cooled down. The same experimental method was repeated on every understudy alloy sheet as shown in Fig. 1.
Table 1Material details and laser parameters
Materials | Dimensions (L×W×T) mm | Laser parameters | ||
Output power (W) | Scanning speed (mm/s) | Laser spot diameter (mm) | ||
Aluminum Alloy Al-5052M | 68×32×1 | 700 | 10 | 4 |
Stainless Steel Alloy-304M | 65.86×32×1.7 | 400 | 30 | 5 |
Low Carbon Steel (perpendicular rolling direction) | 69×31.5×1 | 400 | 30 | 5 |
Titanium Alloy Ti-6Al-4V (TCL4) | 68×32×1 | 400 | 30 | 5 |
Fig. 1Experimental setup: a) clamping, b) spring back measurement before laser, c) laser irritation, d) spring back measurement after laser
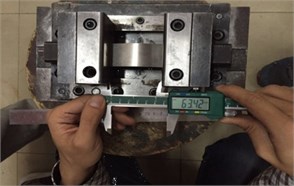
a)
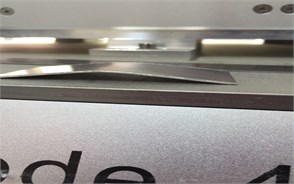
b)
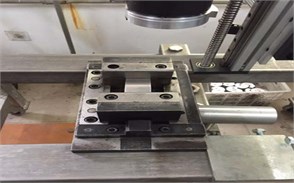
c)
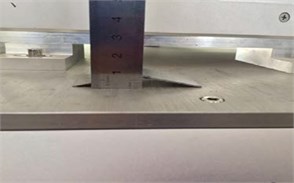
d)
3. Results
The design scheme of the experimental work was to calculate and compare the spring back values of different alloys sheet in preloaded laser bending process.
3.1. Spring back before laser application
The experimental calculations of spring back using preload clamping are shown in the form of graphs in Fig. 2. Spring back happens when the bent material tries to gain back its original form to a certain angle. During fabrication, material is usually over bend to the bending degree which is over past the required bending angle in order to compensate the spring back. In this way, over bending permits to acquire the desired bending angle and shape when the pressure is released from the material. Predicting the efficient values of spring back is quite critical. There are so many factors which influence on spring back: (1) The tensile strength of material (2) Thickness of the material (3) Type of tools being used during fabrication process (4) Types of bending [10, 13]. Metal sheets thickness and types of materials are major factors affecting on spring back values but in these experiments thickness of every metal sheet is almost same so we can eliminate the effect of thickness during bending on spring back. Bending process here is simple air forming when the force or pressure is applied on the metal sheet, it starts to bend and the material slightly springs back when the force is released.
Fig. 2(a) showed the spring back of Aluminum alloy Al-5052M, at even low displacement there is large amount of spring back. Behavior of Al-alloys can be explained on the fact that these alloys are malleable, light weight, low hardness 47B and ultimate tensile strength of 228 MPa and their compression modulus is about 2 % greater than tensile modulus. When material is bent, the inner part of the bend is compressed condition while the outer part is in stretched condition so as a result of this; the density of molecules is greater on inside of the bend as compare to the outer surface. The compressive forces are less on the outside surface of the bend which causes the material to try to return to its original position [13]. These properties make Al-alloys easy to bend and return to its original shape while giving high values of spring back. The mechanical properties of understudy alloys are given in Table 2.
Table 2Mechanical properties of understudy alloys
Alloys | Mechanical properties | |
Hardness (HRB) | Ultimate tensile strength (MPa) | |
Aluminum alloy | 47 | 228 |
Stainless steel alloy | 170 | 515 |
Low carbon steel | 71 | 440 |
Titanium alloy | 334 | 993 |
In case of low carbon steel in Fig. 2(b), rolling direction is perpendicular to the applied bending force which also has opposing effect on values of spring back. Due to opposite rolling direction it is hard for molecules to move during bending causing more tensile force application. These low carbon steels have ultimate tensile strength in range of 440 MPa and hardness 71 HRB which are more than Al-alloys. But due to low carbon contents in these steels they have good ductility which also contributes to spring back values. Fig. 2(c) showed the spring back values after releasing from mechanically clamping of stainless steel 304M. It is standard 18/8 stainless steel grade which has outstanding forming characteristics. These alloys have ultimate tensile strength of 515 MPa and high hardness (170 HRB).
Fig. 2(d) explained the spring back behavior of Titanium (Ti-6Al-4V) alloys. These alloys are not easy to deform at low temperature due to bad plasticity but when enough force is applied that the material approaches to its yield point then the deformation of the material occurs. Titanium alloys have high ultimate tensile strength of 993 MPa and very high hardness (334B) then Al-alloys. All these factors attribute to the values of spring back. It is clear from the figure as well that at low displacement amount of spring back is almost neglect able but after large amount of force application at high displacement, spring back values increased even at room temperature.
Fig. 2Spring back before laser: a) Al-alloys, b) low carbon steel, c) stainless steel, d) titanium alloys
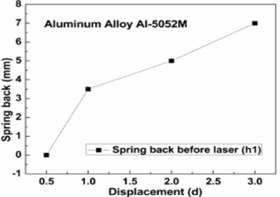
a)
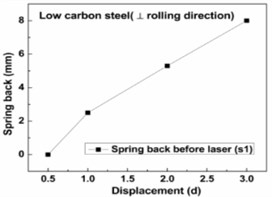
b)
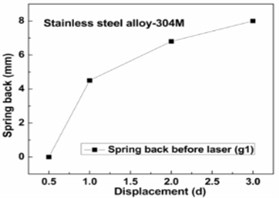
c)
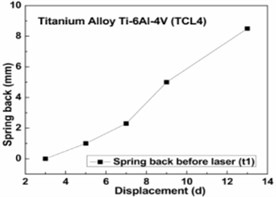
d)
3.2. Spring back after laser application
The laser parameters were selected on the basis of material properties and the Gaussian distribution was used. To set the values of laser bending process, following steps calculation were used. Laser spot moving time by:
where – distance travelled, – laser scanning speed. The distribution of heat flux density is considered to have uniform values with laser spot moving time can be calculated by using following formula:
Here – absorption coefficient of metal sheet, – Laser output power. The energy lost during the heat transfer can be found by equation, where – heat exchange coefficient (radiation and convection), – Room temperature at test time. In Fig. 3 spring back values are shown in form of graphs after laser scanning. It is obvious that spring back values are high than the preload condition for all kind of understudy work pieces after laser scanning process. There are so many factors in laser bending process which effect on the spring back values which are: 1) input power (P), 2) scanning speed (S), 3) laser spot diameter (D), 4) laser scanning path [14-16].
In present report, results showed that after laser bending spring back values increased as compared to the mechanically clamping. Heating effect in laser bending plays an important role. High temperature helps in the movement of molecules/ atoms of material causing more plastic deformation. Previous studies showed that the as the laser power (P) increases, tensile strength of material decreases. The bending of materials decreases with the increase of scanning speed (S). Fig. 3(a) showed the Al-alloys spring back value after laser scanning. As it is explained earlier that due to malleable nature of Al alloys, it is easy to bend them even at low displacement (low application of force) at room temperature, but after laser scanning value of spring back increases. The output power for Al-alloys during the experiment is 700 W which helps to decrease the tensile strength causing more deformation. The scanning speed 10 mm/s is low which may have contributed to the low bending of Al-alloys here.
Fig. 3Spring back after laser: a) Al-alloys, b) low carbon steel, c) stainless steel, d) titanium alloys
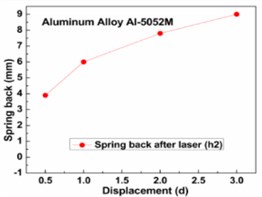
a)
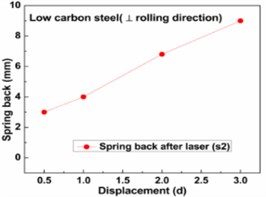
b)
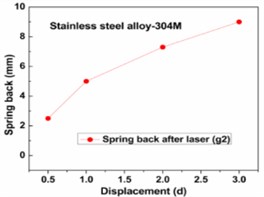
c)
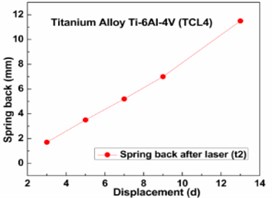
d)
For other understudy alloys in this experiment, the laser parameters laser power and scanning speed are same. Low carbon steel (perpendicular rolling direction) and stainless steel 304M alloys have shown high values of spring back in Figs. 3(b) and (c) respectively than spring back from preloaded clamping. In Fig. 3(d) there is a great improvement in spring back value of titanium alloys than room temperature values which showed that deformation increases while reducing the tensile strength and hardness of these alloys. And when laser power releases, elastic recovery improves.
So the laser scanning method is more beneficial for those alloys that are more difficult to deform at low temperature. Since Al-alloys, low carbon steels and stainless steel have lower tensile strength and hardness, they can easily be shaped for different requirements. But titanium alloys have low plasticity so it is tough to use them. But laser bending technique could provide an efficient bending method for titanium alloys for practical applications.
4. Discussion
The comparison of spring back at room temperature and after laser application is given in bar graph form in Figs. 4(a) and (b). At room temperature after mechanically clamping in Fig. 4(a), all the understudy alloys except titanium alloys showed a large amount of spring back value even at low displacement. This showed that these alloys have a lot of deformation even after a small amount of force application. But titanium alloys have low spring back value at low displacement but as the applied bending force increased, these alloys have shown an increase in spring back. In Fig. 4(b) spring back values of the alloys increase which is due to the fact that laser power and scanning speed effect the tensile strength and hardness of materials. Which cause the more deformation of alloys even for titanium alloys which has highest tensile strength and hardness.
Fig. 4Comparison of spring back of understudy alloys before and after laser application
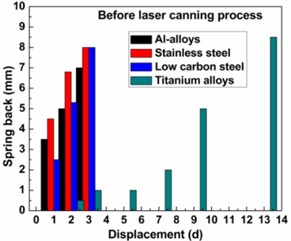
a)
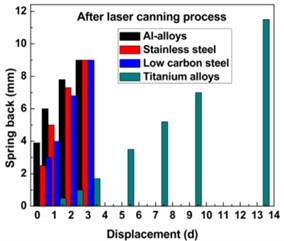
b)
5. Conclusions
From the above reported study, following conclusions can be drawn: 1) It is easy to deform Al-alloys, stainless steel and low carbon steels mechanically due to their low tensile strength and hardness but it is hard to deform titanium alloys at room temperature. 2) Thermal effect of laser helps to reduce the material resistance to deformation during bending process. 3) Spring back values increased during pre-loaded laser bending process for even titanium alloys. 4) Per-loaded laser bending is an ideal option for high strength alloys with poor plasticity.
References
-
Gawade S., Nandedkar V. M. Spring back in sheet metal bending – a review. 2nd International Conference on Emerging Trends in Engineering, Journal of Mechanical and Civil Engineering, India, 2009, p. 53-56.
-
Suchi Ivana Handbook of Die Design. McGraw Hill, 1998.
-
Ozgur T., Nedim G., Ulvi S. Determination of spring back of stainless steel sheet metal in V bending dies. Materials and Design, Vol. 29, 2008, p. 1043-1050.
-
Johnson W., Mellor P. B. Engineering Plasticity. Van Nostrand Co., London, New York, 1973.
-
Chan W. M., Chew H. I., Lee H. P., Cheok B. T. Finite element analysis of spring back of V-bending sheet metal forming processes. Journal of Materials Processing Technology, Vol. 172, 2006, p. 35-41.
-
Aurelian A. The Sheet Thickness Effect on Spring Back Phenomia. University of Galti Fascicle Technologies in Machine Building, 2008.
-
Thomas S. New Method to Calculate and Compensate Spring Back. Mashhad, Iran, 2008.
-
Dilip Kumr K. Thinning and spring back of aluminum sheet metal during L-bending operation. International Journal of Engineering Science and Technology, Vol. 2, Issue 10, 2010, p. 5120-5129.
-
Hani Aziz Ameen Effect of sheet thickness and type of alloys on the spring back phenomenon for cylindrical die. American Journal of Scientific and Industrial Research, 2012, p. 480-486.
-
Xiang Y., Hu L., Peng D., Huijuan X. Study of laser bending of a preloaded Titanium alloy sheet. Research on Manufacturing Technology, Vol. 5, 2010, p. 20-25, (in Chinese).
-
Liu C., Liu Liu S. H. J. L., Hu K. P., Xiao P. Study on shape and size precision control of titanium alloy in laser bending. Applied Laser, Vol. 31, 2011, p. 50-56.
-
Zhang Y. C., Wang X. F., Wang X. B., Guo J. Laser prestressed bending of titanium alloy sheet. Applied Mechanics and Materials, Vol. 633, Issue 634, 2014, p. 773-776.
-
Chinese Aviation Materials Handbook. Second Edition, China Standard Press, Vol. 4, 2002, p. 104-132, (in Chinese).
-
Shidid D. P., Hoseinpour Gollo M., Brandt M., Mahdanian M. Study of effect of process parameters on Titanium sheet metal bending sing Nd: YAG laser. Optics and Laser Technology, Vol. 47, 2013, p. 242-247.
-
Li L. Q., Chen Y. B., Zhang L. W., Feng X. S. Laser bending characteristics of Ti-6Al-4V Titanium alloy. The Chinese Journal of Nonferrous Metals, Vol. 15, 2005, p. 842-848, (in Chinese).
-
Wang X., Liu D., Li W., Xu L., Dong Y. Study of laser bending of a preloaded Titanium alloy sheet. Manufacturing Review, Vol. 1, 2014, p. 25.