Abstract
Face gear drives are focused by many researchers, due to several strong-points versus traditional spiral bevel gear drives. However, calculation solutions of face gear dynamics associated with engagement impact energy decay are not to be constructed, according to the limited published issues. Thus, in the study, a calculation solution of engagement impact energy decay of face gear drives is proposed, a face gear dynamic model is established, and the dynamic mesh forces of an example case of face gear drives without engagement impacts as well as with engagement impacts and engagement impact suppressions are simulated. The results indicate the fidelity of the proposed calculation solutions of face gear dynamics associated with engagement impact energy decay could be accepted. These contributions would improve the developments of face gear drive modifications and engineering applications of face gear drives in the future.
1. Introduction
Face gear drives are addressed by scholars, due to several strengths versus spiral bevel gear drives [1-15], and according to research achievements of Litvin et. al. [16-21], face gear drives are suggested to be used in first-stage gear drives of helicopter main gear boxes. Due to operating characteristics of first-stage gear drives, namely, input-stage gear drives in helicopter main gear boxes, face gear dynamics is focused by many researchers [22-27]. However, according to the limited published issues about face gear dynamics, calculation solutions of face gear dynamics associated with engagement impact energy decay are not to be constructed. Thus, in the study, an engagement impact energy decay calculation solution of face gear drives is proposed, and a four degree-of-freedom (DOF) face gear dynamic model is formulated. Furthermore, the dynamic mesh forces of an example case of face gear drives without considering engagement impacts, as well as with considering engagement impacts and engagement impact suppressions are simulated. The results indicate the fidelity of the proposed calculation solutions of face gear dynamics associated with engagement impact energy decay could be accepted. These contributions would benefit to construct face gear drive modification solutions, and improve engineering applications of face gear drives in the future.
2. Solutions of face gear dynamics associated with engagement impact energy decay
2.1. Calculation solution of engagement impact energy with considering energy decay
According to the reference [28], Li and Zhu proposed the calculation solutions of the engagement impact energy and the conversion between engagement impact energy and static transmission errors (STE) of face gear drives. But, they neglect energy decay of engagement impact contact interfaces.
Thus, according to the reference [29], engagement impact energy of face gear drives with considering energy decay can be derived by:
where E is an engagement impact energy, which can be calculated according to the reference [28], Ed is an engagement impact energy with considering energy decay, me is a quality of face gear drives, and mp is a quality of pinions.
2.2. Four DOF dynamic model
A four DOF dynamic model of face gear drives, as shown in Fig. 1, is formulated for assessing the fidelity of the proposed calculation solutions of face gear dynamics associated with engagement impact energy decay.
Fig. 1A four-DOF dynamic model
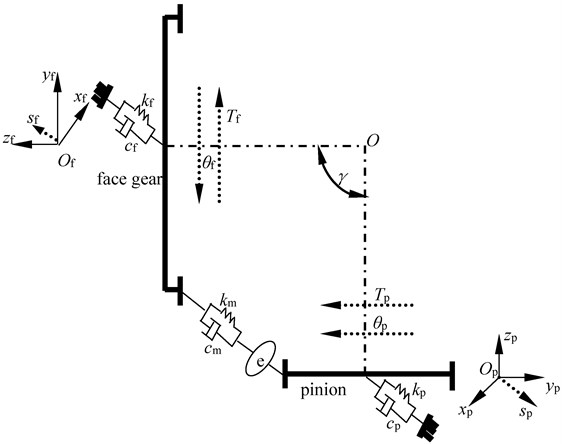
As illustrated in Fig. 1, mathematic equations of the dynamic model can be deduced as:
where Fm can be written in:
+cmsin(γ)(s'p-s'f+Rbpθ'p-Rbfθ'f-e'),
where θ is a torsion degree of freedom, s is a bending degree of freedom, T is a torsion, k is a bending stiffness, c is a bending damping, m is a quality, I is a moment of inertia, (') is first derivative, ('') is second derivative, subscript f and p express a face gear and a pinion respectively. In addition, km is mesh stiffness, cm is mesh damping, and e is a comprehensive meshing error.
3. Simulations
In order to investigate dynamic mesh force differences of face gear drives among three conditions, namely, without engagement impacts, with engagement impacts, and with engagement impacts associated with impact energy decay, as well as evaluate the fidelity of the proposed calculation solutions of face gear dynamics associated with engagement impact energy decay, geometric parameters, operating conditions and material characteristics of an example case of face gear drives are given in Table 1.
Table 1Parameters of an example case
Names | Values | Units | |
Geometric parameters | Modulus | 2.5 | mm |
Pressure angle | 22.5 | ° | |
Tooth number of pinions | 21 | – | |
Drive ratio | 3.476 | – | |
Shaft angle | 87 | ° | |
Tooth number difference between pinions and generation gears | 1 | – | |
Addendum coefficient | 1 | – | |
Clearance coefficient | 0.25 | – | |
Operating conditions | Power | 50 | kW |
Input rotation speed | 4000 | r/min | |
Material characteristics | Modulus of elasticity | 210000 | MPa |
Poisson ratio | 0.3 | – |
Based on the parameters, listed in Table 1, the STE, which can be calculated according to the reference [28], of the example case among three conditions, meaning, without engagement impacts, with engagement impacts, and with engagement impacts associated with impact energy decay, are simulated, as shown in Fig. 2.
Fig. 3A dynamic mesh force simulation of the example case
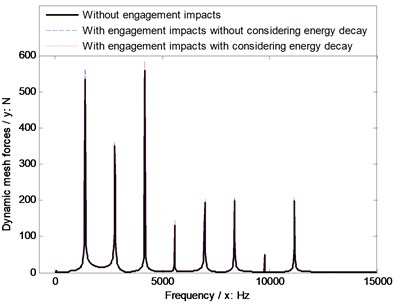
Fig. 2A simulation of STE of the example case
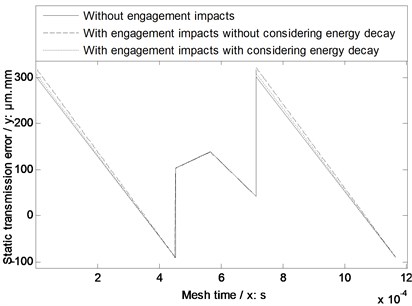
Introducing the results of Fig. 2 into Eq. (2), the dynamic mesh forces of the example case of face gear drives among three conditions are simulated, as shown in Fig. 3.
As illustrated in Fig. 2 and Fig. 3, the STE and dynamic mesh force simulation results with considering engagement impacts associated with energy decay are between the simulation results without engagement impacts and those with engagement impacts, in which energy decay is not considered, which is consistent with the general knowledge and phenomenon of face gear dynamics. Thus, the fidelity of the proposed calculation solutions of face gear dynamics associated with engagement impact energy decay could be accepted.
4. Conclusions
In this study, the most important work is to construct calculation solutions of face gear dynamics associated with engagement impact energy decay. Secondly, the fidelity of the proposed calculation solutions could be accepted according to the simulation results of an example case of face gear drives, which is fit for general cognitions of gear dynamics. These contributions would benefit to improve face gear drive modifications and engineering applications of face gear drives in the future.
References
-
Barone S., Borgianni L., Forte P. Evaluation of the effect of misalignment and profile modification in face gear drive by a finite element meshing simulation. Journal of Mechanical Design, Vol. 126, Issue 5, 2004, p. 916-924.
-
Guingand M., De Vaujany J.-P., Jacquin C.-Y. Quasi-static analysis of a face gear under torque. Computer Methods in Applied Mechanics and Engineering, Vol. 194, Issue 39, 2005, p. 4301-4318.
-
Zanzi C., Pedrero J. I. Application of modified geometry of face gear drive. Computer Methods in Applied Mechanics and Engineering, Vol. 194, Issues 27-29, 2005, p. 3047-3066.
-
Fang Z.-D., Cao X.-M., Shen Y.-B. Tooth surface design and manufacture for arcuate tooth trace face-gear. Journal of Aerospace Power, Vol. 25, Issue 1, 2010, p. 224-227, (in Chinese).
-
Frąckowiak P. Modelling and cutting a face-gear with straight line on CNC milling-machine. Manufacturing Engineering, Vol. 9, Issue 3, 2010, p. 19-21.
-
Bucur B., Boloş V. Experimental study of the thermal limit for the gearbox worm face-gear with reverse tapered pinion. Proceeding of the 9th International Conference MTeM, 2011.
-
Saribay Z. B., Bill R. C., Smith E. C., Rao S. B. Elastohydrodynamic lubrication analysis of conjugate meshing face gear pairs. Journal of the American Helicopter Society, Vol. 57, Issue 3, 2012, p. 1-9.
-
Shi-xing F., Guang Z. Research on the rolling process technology of face gear. Mechanical Research and Application, 2012, (in Chinese).
-
Wang W. J., Zhang J., Zhao J., Zhang L. L., Wang T. Y. Design, generation and bending stress analysis of face-gear with curvilinear shaped teeth. Advanced Materials Research, Vol. 472, 2012, p. 74-77.
-
Wang Y., Wu C., Tang W., Zhao X.-F., Lv Q.-J., Lian Y. Analysis on isothermal elastohydrodynamic lubrication of orthogonal face gear. Tribology Transactions, Vol. 55, Issue 6, 2012, p. 863-871.
-
Yanping T. J. L. Loaded meshing simulation of face-gear drive with spur involute pinion based on finite element analysis. Journal of Mechanical Engineering, Vol. 48, Issue 5, 2012, p. 124-130, (in Chinese).
-
Dudás I., Bodzás S. Production geometry analysis, modeling, and rapid prototyping production of manufacturing tool of spiroid face gear. The International Journal of Advanced Manufacturing Technology, Vol. 66, Issues 1-4, 2013, p. 271-281.
-
Guo H., Zhang S. Y. Grinding experiment research of face gear with CNC machine. Applied Mechanics and Materials, Vol. 496, 2014, p. 503-506.
-
Ning Z., Mengqi Z., Hui G. Stress analysis of asymmetric spur face-gear pair based on finite element method. Advanced Materials Research, Vol. 483, 2014, p. 309-314.
-
Wu C. H. Characteristic analysis on elastohydrodynamic lubrication of orthogonal face-gear. Advanced Materials Research, Vol. 912, 2014, p. 598-604.
-
Litvin F., Bossler R., Chen Y.-J., Zhang Y., Wang J.-C. Design and geometry of face-gear drives. Journal of Mechanical Design, Vol. 114, Issue 4, 1992, p. 642-647.
-
Litvin F., Bossler R., Chen Y.-J., Lewicki D., Heath G., Wang J.-C. Application of face-gear drives in helicopter transmissions. Journal of Mechanical Design, Vol. 116, Issue 3, 1994, p. 672-676.
-
Litvin F. L., Egelja A., Tan J., Chen D., Heath G. Handbook on Face Gear Drives with a Spur Involute Pinion. DTIC Document, 2000.
-
Litvin F. L., Fuentes A., Howkins M. Design, generation and TCA of new type of asymmetric face-gear drive with modified geometry. Computer Methods in Applied Mechanics and Engineering, Vol. 190, Issue 43, 2001, p. 5837-5865.
-
Litvin F. L., Fuentes A., Zanzi C., Pontiggia M. Design, generation, and stress analysis of two versions of geometry of face-gear drives. Mechanism and Machine Theory, Vol. 37, Issue 10, 2002, p. 1179-1211.
-
Litvin F. L., Gonzalez-Perez I., Fuentes A., Vecchiato D., Hansen B. D., Binney D. Design, generation and stress analysis of face-gear drive with helical pinion. Computer Methods in Applied Mechanics and Engineering, Vol. 194, Issue 36, 2005, p. 3870-3901.
-
Jin G., Zhu R., Bao H. Nonlinear dynamical characteristics of face gear transmission system. Journal of Central South University (SciTechnol), Vol. 5, Issue 41, 2010, p. 1807-1813, (in Chinese).
-
Yang Z., Wang S.-M., Fan Y.-S., Liu H.-X. Bifurcation charactristics of face-gear transmission system. Journal of Harbin Institute of Technology, Vol. 3, Issue 43, 2011, p. 107-110, (in Chinese).
-
Yang Z., Wang S.-M., Fan Y.-S., Liu H.-X. Vibration characteristics of face-gear transmission system with parametric excitation. Journal of Chongqing University, Vol. 35, Issue 1, 2011, p. 26-35, (in Chinese).
-
Hu Z. H., Tang J. Y., Chen S. Y., Lei D. C. Effect of mesh stiffness on the dynamic response of face gear transmission system. Journal of Mechanical Design, Vol. 135, Issue 7, 2013, p. 071005.
-
Wang R., Zhao N., Tao L., Jia Q., Guo H. Floating shaft load sharing method for face gear split torque transmission system. Research Journal of Applied Sciences, Engineering and Technology, Vol. 5, Issue 12, 2013, p. 3386-3392.
-
Wang Z., Chen Q., Lin J. C., Yang L. L. Study of the dynamic behavior of face gear transmission system. Applied Mechanics and Materials, Vol. 268, 2013, p. 1063-1066.
-
Li Z. M. Q., Zhu R. P. Sensitivity predictions of geometric parameters on engagement impacts of face gear drives. Journal of Vibroengineering, Vol. 17, Issue 5, 2015, p. 2236-2246.
-
Shen G. Y. W. A method of calculating impact load by considering loss of kinetic energy for common construction. Chinese Journal of Applied Mechanics, Vol. 5, Issue 3, 1988, p. 111-113, (in Chinese).
About this article
The authors are grateful for the financial support provided by the National Natural Science Foundation of China under No. 51105194 and No. 51375226, and the Fundamental Research Funds for the Central Universities under No. NS2015049. In addition, the authors declare that there is no conflict of interests regarding the publication of this article.