Abstract
The angular displacement of the muzzle vibration has importance influence on the firing dispersion of gun. In order to solve the measuring problem on the angular displacement of the muzzle vibration in firing environment, a kind of measuring method of the angular displacement of the muzzle vibration based on the laser and the triangle principle was presented, and its measuring system was developed. The laser beam was sent by a laser. After the laser beam was reflected by a reflector on muzzle, the reflective beam was received by the position sensitive detector (PSD). Combining the optical distance parameter and the triangle relation, the angular displacement of the muzzle vibration could be obtained. The measuring error analysis of the system and the verification of the firing environment in shooting range were made. The performances of the measuring system were that the measuring range of the angular displacement was ±, its angle resolution was , its relative errors under the different illumination conditions were less than 2 %. The measuring system can meet the needs of the gun measurement.
1. Introduction
The gun firing can bring about the intense muzzle vibration. The muzzle vibration responses include the angular displacement, the angular velocity, linear displacement, linear velocity, and so on. For small caliber gun, the angular displacement of muzzle is one of the important factors influencing the firing dispersion of gun [1]. To know the rules of the angular displacement of muzzle vibration has the important effect for analyzing the influence of the gun vibration on firing dispersion. As the environment of muzzle vibration is complicated, and the present measuring system cannot meet the needs of measurement in gun, the measuring system about the angular displacement of the muzzle vibration is imminently needed in gun engineering practice. Therefore, the measuring methods of the angular displacement of the muzzle vibration with different principle were presented.
The measuring method about muzzle turbulence based on the optics lever principle was presented by the literature [2], but the plate of sheltering light which was surrounded in the muzzle shock wave was used in the measuring system, the muzzle shock wave disturbs the plate, and this method could not be used in practice. With the eddy current sensor, the linear displacement of the muzzle was first obtained, then, the angular displacement of the muzzle vibration based on triangle principle was obtained [3]. In the literature [4], using two set trackers, the linear displacement was first obtained, then, the angular displacement was obtained. In literature [3, 4], the transform errors could be introduced. In the literature [5], with the target plate method, according to the coordinates of projectile hole on vertical target from muzzle frontage, the angular displacement of the muzzle was obtained indirectly. In the literature [6], using the vertical target method based on the linear array CCD sensor to measure the coordinates of projectile hole, the angular displacement of the muzzle was obtained. But, for the portion while the ulterior period of projectile, the angular displacement of the muzzle could not be separated. In the literature [7], when the position sensitive detector (for short PSD) was fixed on the muzzle, and the laser was fixed on the cradle, the angular displacement of the muzzle was obtained. Here, the PSD was difficult to bear the shock wave of muzzle. In the literature [8], a gyroscope was fixed on a tube in order to that the angular displacement of the muzzle under the condition of static state was measured. As the strong impact factor in muzzle environment, the method cannot need the firing environment of the gun. In the literature [9], with the CCD coordinate target method, the angular displacement of the muzzle was measured, but the method can only be applied to the static condition.
For the measuring need of the angular displacement of the muzzle while firing, a kind of measuring method based on the laser and the triangle principle was presented, its measuring system was developed, and the measuring error analysis and the method verification on condition of firing were made.
2. Measuring principle
2.1. Measuring method
To use the PSD serves as the sensitive element, the measuring method of the angular displacement of the muzzle was studied. Fig. 1 was sketch map of the measuring method about the angular displacement of the muzzle vibration (vertical view). Its measuring system included a laser, a two dimensional PSD, a controller, a reflector, a tripod, and so on. The laser and two dimensional PSD were fixed to same foundation support which was fixed to ground with a tripod. On the one hand, the controller provided power supply for the laser, on the other hand, the controller did the signal conditioning for the PSD. The angular displacements of the muzzle in elevation and azimuth were simultaneity measured by the two dimensional PSD. For the recording convenience, the output signal of the PSD was translated into the voltage signal.
To take the measuring method about the angular displacement of muzzle in azimuth as an example, the operational principle of the measuring system was given. The preparedness before measurement: a metal type reflector which was located lateral was fixed to a muzzle clamp, and the surface of the reflector faced on rear. The subassembly of the laser and two dimensional PSD was lain the tube lateral, the power supply of laser was turned on, and the incident light which was emitted by the laser illuminates to the reflector at muzzle position. After reflected, the reflected light illuminates to the sensitive surface of the PSD directly. The measurement while firing: reference Fig. 2, when firing, the angular displacement of muzzle was formed, and the reflector rotated with muzzle rotation. At the same time, the direction of the reflected light must change. The laser beam could move on the sensitive surface of the PSD, and the output voltage of the PSD was in proportional to the displacement of the laser beam. Taking the distance between the reflector and the sensitive surface of the PSD was , when the reflector rotated the angle from position to position , the displacement of the laser beam on the sensitive surface of the PSD in the direction of azimuth was . Thus, according to the triangle relation, had:
or
Note, according to the reflection law of light, when the reflector rotates the angle from position to position , the reflected light beam will rotate the angle . In the measuring system, the distance was two orders of magnitude bigger than the displacement . The angle was very small, in general, the angle was less than . Using the same method, the angular displacement of muzzle, or angle in elevation, could be obtained. Thus, the angular displacements of muzzle in elevation and azimuth where be obtained by the measuring method.
According to Eq. (2), as long as the distance and displacement were measured, the angular displacements of muzzle could be obtained. The PSD has higher frequency response, its response is (0.4-7.0) μs, the position resolution is 1 μm. By calibrating in laboratory, the angular displacement resolution of the measuring system was , and it could meet the need for measurement to the angular displacements of muzzle.
Fig. 1Sketch map of the measuring method about the angular displacement of muzzle vibration (vertical view)
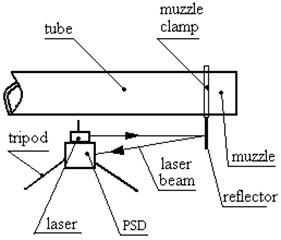
Fig. 2Sketch map of the measurement principle of the angular displacement
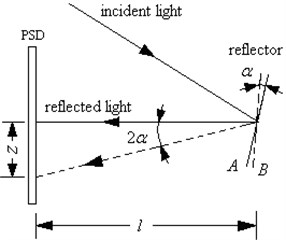
2.2. Measures of removing environmental light
If the anti-environmental light measures in the measuring system was not taken, the more error could be formed. Therefore, as the optical filtering technique, and the laser modulation and demodulation technique were used, the precision in the measuring system could meet the need for measurement.
Using the optical filtering technique decreased the interference of the environmental light. The property parameters of the filter were 640 nm-660 nm in passband range. Thus, the filter could basically insulate the environmental light beyond the passband range into the sensitive surface of the PSD. Thereby, the capacity of resisting disturbance of the measuring system was enhanced.
2.3. Eliminating non-linear error of PSD
The software way was used by this paper. Using the experiment method, the mathematics relation between the laser point displacement and the PSD output signal was found, and then, experiment results were corrected. In the software way, the equation of the polynomial curve fitting was used for the error correction.
2.4. Property verification of measuring system
For verifying the property of anti-environmental light of the measuring system, the property experiments in different illumination conditions were done. The verification conditions were: 1) the indoor, nature light, in the daytime, 2) the indoor, strong light lamp, in the daytime, 3) the indoor, to turn off light, at night, 4) the indoor, strong light lamp, at night, 5) midday under the sun. Every experiment condition was repeated three times, and found average. The illumination intensity of the strong light lamp was more than 30 thousand lx. The results showed that the measuring relative errors were less than 2 %, the measuring system had the ability of anti-environmental light.
2.5. Simulation of measuring system
The known angle was given by an electronic theodolite, and the angle measured was obtained by the measuring system. Precision of the electronic theodolite was . In order to simulate the known angle, a reflector on the running part of the electronic theodolite was fixed, the reflector was rotated with the running part of the electronic theodolite. The angles in elevation and azimuth were measured. The change ranges of the known angles were from –-+, its interval was . The results showed that the relative errors of the simulation results of angle in the measuring system were less than 2 %, and the angle resolution was .
2.6. Precision analysis
According to the data measured, the static characteristic analysis of the measuring system was done. The non-linearity of the measuring system was 0.56 %, the repeatability of the measuring system was 1.12 %, the overall precision of the measuring system was 1.25 %.
3. Verification in shooting range
In order to verify the adaptability of the firing environment in the shooting range for the measuring system, the firing test of the small caliber gun was done, and the angular displacement of the muzzle was measured with the measuring system developed by authors. The measuring curve of the angular displacement of the muzzle in elevation with continuous firing mode was shown in Fig. 3. The upward curve denoted the upward angular displacement of the muzzle. The results showed that with the increase of the firing projectile number, the muzzle position was gradually raised. When the firing projectile number was accumulated to a certain value, the muzzle vibration in the positive amplitude was happened until the stop firing. The maximum of the angular displacement of the muzzle in elevation was , and the average in elevation was more than 0. The measuring system could meet the need for the firing environment in the shooting range.
Fig. 3Measuring curve of the angular displacement of muzzle in elevation

4. Conclusions
1) The measuring system of the angular displacement of muzzle based on the laser and the triangle principle could solve the measuring problem on the angular displacement of muzzle.
2) For the measuring system, its range of angular displacement was , its angle resolution was , and non-linearity was 0.56 %.
3) For the measuring system, the measuring relative errors on different illumination condition were less than 2 %, it could meet the need for the measurement of the firing environment in the shooting range.
References
-
Wang Baoyuan, Gao Xiaoke, Li Baohui, et al. Review of measurement methods for jump angle of gun. Journal of Test and Measurement Technology, Vol. 27, Issue 4, 2013, p. 294-299, (in Chinese).
-
Zhu Qi, Xue Ting, Guo Qian, et al. Measurement of muzzle disturbance angle based on principle of optical lever. Laser and Infrared, Vol. 43, Issue 3, 2013, p. 281-285, (in Chinese).
-
Wei Xiaoda Analysis of reducing vibration measures on raising the dispersion of antiaircraft of gun. Journal of Gun Launch and Control, Issue. 3, 1994, p. 26-66, (in Chinese).
-
Haug Bailey T., Bornstein Jonathan A. Gun dynamics measurements for tank gun systems. AD-A186238, U.S. Army Armament Research Development and Engineering Center, Proceedings of the Fifth U.S. Army Symposium on Gun Dynamics, USA, NY, 1987, p. 224-240.
-
Zhao Chengji A reinvestigation into validity of the traditional method of jump-angle determination. Acta Armamentarii, Vol. 6, Issue 4, 1985, p. 61-64, (in Chinese).
-
Zuo Dan The application of linear matrix CCD vertical target in the low extend trajectory. Radio Engineering, Vol. 23, Issue 5, 1993, p. 57-61, (in Chinese).
-
Xue Changsheng, Lu Aimin, Deng Qibin, et al. A Study of measurement method of gun dump angle. Proceedings of 4th International Symposium on Test and Measurement, China, Shanghai, Vol. 2, 2003, p. 1154-1156.
-
Luo Yu, Chen Weiyi, Shen Yuan Data processing technology in angular displacement test system based on DTG. Ship Electronic Engineering, Vol. 31, Issue 12, 2011, p. 90-93, (in Chinese).
-
Chang Tianqing, Shi Shaohua, Zhang Lei, et al. Research on characteristic measurement method of gun control system. Fire Control and Command Control, Vol. 37, Issue 5, 2012, p. 156-163, (in Chinese).