Abstract
Ignition system is the main important part of the engine, and has absolute influence on engine performance. OpenECU for ignition timing strategy on the basis of the design and calibration work, greatly shorten the development difficulty and cycle; machine of a LNG gas ignition timing strategy has carried on the design and optimization, and combining the calculation model for the engine (air intake, compression, power, and exhaust) feedback and verification. It can save a lot of time and resources for experiment if experiments use openECU. It also can monitor the influence of the different inputs conditions on the ignition advance angle. It has realized the map of calibration, greatly shorten the development work and has certain actual application value.
1. Introduction
Ignition time properly in advance can improve engine performance and fuel economy, but the premature ignition can easy cause explosion. Ignition delay time can effectively reduce the emissions of HC and NOx, eliminate the explosion, but the ignition moment too late can make the engine performance and fuel economy worse. Practice has proved that in front of the engine check point on the compression stroke the certain point of ignition can improve the engine performance and fuel economy. It can also reduce emission’s pollution. This ignition advance angle is the best ignition advance angle. When engine is running, ECU according to the engine’s speed and load signal determines the basic ignition advance angle, and according to other relevant signal to correct, finally it ensures the optimum ignition advance angle. Then electronic controller output ignition indicator signal to control ignition system work.
Energy saving and environmental protection is the mainstream in the development of the car, with more attention paid to the natural gas vehicle. Natural gas engine’s ignition system is needed to work properly. So we need to develop a reliable performance, low cost ignition timing device.
As a large energy consumption of the vehicle, energy conservation and emissions reduction has become the important direction of its development. In the traditional gasoline engine and diesel engine based on natural gas engine become one of the important ways to relieve the energy problem. As one of the alternative green fuel oil, natural gas has its own advantages, such as abundant resources, complete combustion, well antidetonating quality, emission, low-temperature operation and so on.
2. Materials and methods
In the ignition system, electronic control unit to control of ignition advance angle can be divided into the starting condition and working condition after starting mode. The starting condition of ignition advance angle is according to engine speed and the pressure inside the intake manifold by querying pulse spectra. After the start of the operating mode is divided into whether in the idle state, but the ignition advance angle is determined by the type.
The actual ignition advance angle-basic ignition advance angle correction advance angle.
The starting condition of ignition advance angle is according to engine speed and the pressure inside the intake manifold by querying pulse spectra as the initial ignition advance angle.
Idle condition of the real ignition advance angle is equal to the basic ignition advance angle plus the correction ignition advance angle. The determination of basic ignition advance angle is according to whether connected to an air condition, if so, substitute the corresponding values for the ignition angle. The correction: warming correction, overheating correction and idle speed stability correction.
When the engine in the process of warming-up, ECU according to the cooling water temperature to check the Map, get the correction angle.
When engine is at idle condition, if the cooling water temperature is too high, in order to avoid overheating for long, it should increase ignition advance angle. It is called idle overheating correction.
When engine is at idle condition, due to the engine speed fluctuation is under the idle reference speed, so the ECU needs to adjust ignition advance angle and calculate the rotational speed of engine, and make a difference with idle reference speed, as a basis of correction. When the engine speed is greater than the idle reference speed, it should reduce the ignition advance angle; On the other hand, it should increase the ignition advance angle. The corresponding control strategy is shown in Fig. 1.
Fig. 1The ignition advance angle control strategy at idle condition
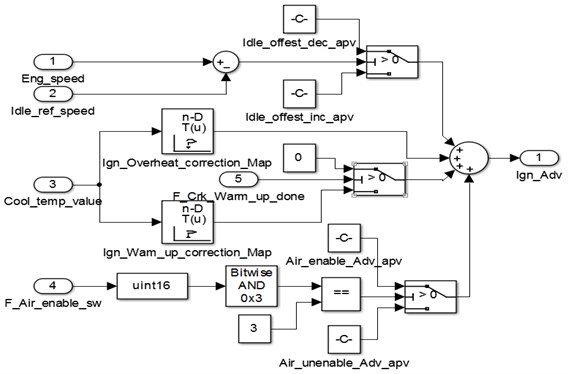
Normal condition of the real basic ignition advance angle is equal to the basic ignition advance angle plus the correction ignition advance angle. The basic ignition advance angle is according to engine speed and the pressure inside the intake manifold by querying pulse spectra. The correction: cooling water temperature correction, air-fuel ratio feedback correction, deflagration correction and in taking air temperature correction.
ECU according to the cooling water temperature to check the Map, gets the correction angle, if the cooling water temperature is lower, it should increase the ignition advance angle.
ECU adjust to the fuel of injection by the oxygen content of oxygen sensor feedback signal. In the process, air fuel ratio always fluctuates, therefore it can through air fuel ratio query corresponding Map to determine the ignition advance angle.
Deflagration correction can through engine speed and intake manifold pressure query corresponding Map to determine the ignition advance angle.
When it correct intake air temperature, two conditions must be met, intake air temperature and engine speed must achieve the corresponding threshold, otherwise, it will not modify for the intake air temperature. When it meets the conditions, through the intake air temperature query Map to determine the ignition advance angle. The corresponding control strategy is shown in Fig. 2.
The determination of optimum ignition advance angle MBT need to consider the control of engine EGR. The real ignition advance angle is equal to the basic ignition advance angle plus the correction ignition advance angle. Basic ignition advance angle and the normal running of the ignition advance angle use the same Map data. The corresponding correction has cooling water temperature correction, air fuel ratio feedback correction, and the angle of the EGR control and without EGR control’s difference multiply EGR rate’s correction. The strategy is shown in Fig. 3.
Fig. 2The ignition advance angle control strategy at normal condition
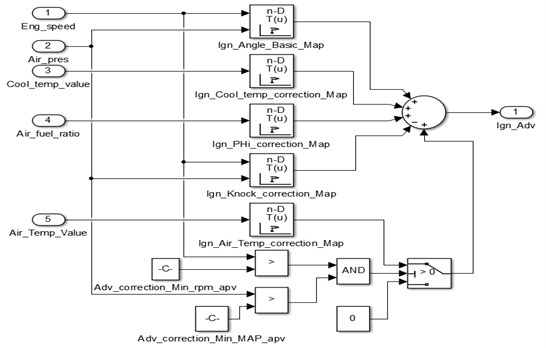
Fig. 3Control strategy of MBT

Fig. 4Maximum and minimum ignition advance angle control strategy
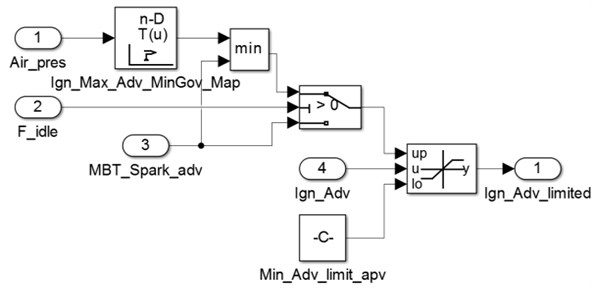
In order to make the engine run properly, the ECU for ignition advance angle must be within a reasonable range. Engine’s real ignition advance angle is equal to the basic ignition advance angle plus the correction ignition advance angle, the value should be within a certain range. The largest ignition advance angle should consider if the engine is at idle condition. When the engine is not at the idle condition, the largest ignition advance angle is the optimal ignition advance angle; When the engine is at the idle condition, it should according to intake air pressure query Map data to determine ignition advance angle, in the same time takes its smaller value with MBT as the largest ignition advance angle. Minimum ignition advance angle uses the fixed value instead. The specific control strategy shows in Fig. 4.
3. Results and discussion
Ope nECU M250 which is produced by Pi Lenovo company is often used with pisnoop, pisnoop is one of their own research and developments calibration tools. In Simulink, we configure M250’s hardware modules, and through its own library module, by the crankshaft sensor’s signal on the plate to simulate an engine speed, other inputs we temporarily do constants for processing. We can change their values in pisnoop in later. If we compile the model which is established (such as normal condition), it can generate A2Land S37 files, then add them to the pisnoop and electrify the M250, it can finish Flash programing. After finishing Flash programing, if we adjust the speed on the signal panel, M250 can realize real time detecting the change of the speed, and reflect its value in pisnoop interface. By increasing or decreasing speed to monitor the change of ignition advance angle, as shown in figure below.
Fig. 5Pre-calibration interface
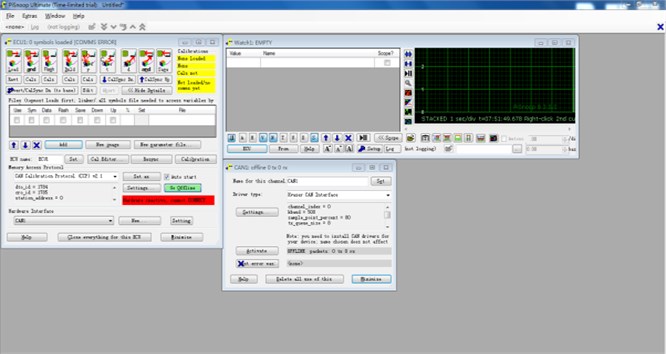
Fig. 6Increase engine speed
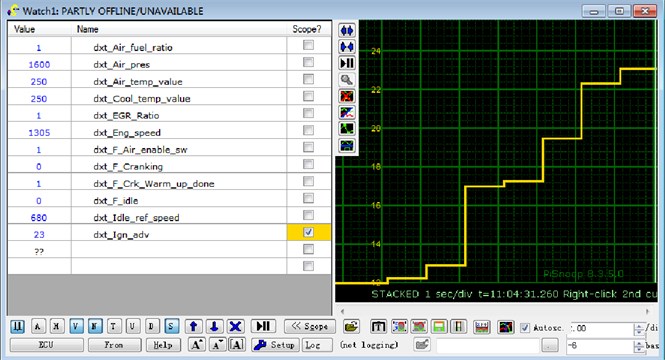
Fig. 7Decrease engine speed
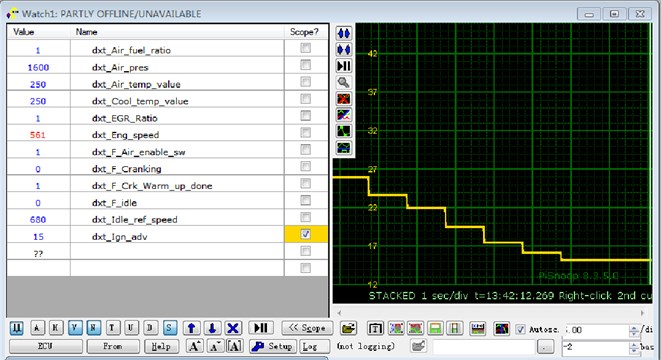
4. Conclusion
1) This paper puts forward a kind of natural gas engine ignition timing control strategy, the ignition advance angle adopts different strategies according to different working conditions, each working conditions calculate the current basic ignition advance angle and correct according to the different conditions of the outside world. After threshold processing the ignition advance angle is the final ignition advance angle.
2) It realize the ignition control strategy program compilation and flash. Through calibration tools pisnoop real-time monitor the influence of different input conditions on the ignition advance angle, realize Maps’ pre-calibration, which greatly shortens the development work.
3) Using open ECU for experiment development, can save a lot of time and resources for the experiment, has certain actual application value.
References
-
Yu Wenming Microcomputer controlled ignition system in the application of the modern automobile engine. Journal of Huaiyin Institute of Technology, Vol. 12, Issue 3, 2003, p. 5558
-
Feng Xinfu, Wu Tongqi CNG and LPG Station Technology. Electronic Industry Press, Beijing, 2000, p. 40-51.
-
Lin Zaili Natural gas vehicle fuel’s application and development in our country. Journal of Internal Combustion Engine, Vol. 2, 2007, p. 1-4.
-
Hao Lijun, Zhang Fujun, Huang Ying, et al. Natural gas engine development present situation and prospect. Journal of Development Present Situation and Prospect of Automotive Engineering, Vol. 22, Issue 5, 2000, p. 332-337.
-
Zhuo Bin Natural gas engine combustion characteristics and power recovery. Journal of Automotive Engine, Vol. 1, 1999, p. 11-17.
-
Zhou Longbao, Liu Jun Gao Zongying, et al. The Internal Combustion Engine Learning. Mechanical Industry Publishing House, Beijing, 2005.
-
Ji Quanxi GDI Engine Cold Start Control Strategy Research. Jilin University, 2011.