Abstract
The noise level was assessed by measuring and processing the sound pressure during the mechanical treatment of large size aluminum extrusions utilized in high-speed trains. The noise control tests were proposed by various machining technologies including the adjustments of cutter tool, machining feed rate, cutting way and sealing the openings with sound-absorbing material or not. The results indicated that obvious noise suppression can be obtained by using monolithic cutters, and sealing the openings and ports with sound-absorbing materials, which has little effect on the whole machining efficiency. It is helpful for noise reduction using the machining technologies of cutting along milling and slowing the feed rate down, which requires a balance between noise level and machining efficiency.
1. Introduction
Many studies have been conducted regarding the noise level and quality of the inside and outside compartment of transportation systems [1-6], and even passengers’ psychology evaluation [7-9]. But, few literatures focus on the sound environment of the operators working during the production process. With the development of light weight trains, the hollow extruded aluminum alloy panel has become the main materials of the floor, ceiling and side wall of high speed trains. High-intensity structural vibration noise is released during the machining operation of large size extruded aluminum, especial when the cutter heads knock with the reinforcement ribs. Non-periodic instantaneous intensity noise will have a serious impact on physical and mental health of operators, such as excessive fatigue, irritability and so on, and further leads to a potential threat to the production safety. Thus, it is expected to acquire a method of the machining noise control to satisfy the needs of operators with a more sound-friendly environment. In this paper, a hollow extruded aluminum floor section utilized in high-speed trains is taken as the experiment object, and various machining technologies were carried out for researching the effect of machining noise control, including the adjustments of cutter tool, machining feed rate, cutting way and sealing the openings with sound-absorbing material or not.
2. Experiments
2.1. Experimental design
The machining noise intensity was measured on a 21 m long hollow extruded aluminum floor section with corrugated cross section during the machining operation. The machining experiments were performed in horizontal direction and set the cutters movement perpendicular to the aluminum extrusion, namely that the cutter heads would knock with the reinforcement ribs frequently. The sound samples were taken at the position of 3 m distance and 0.3 m high from the machining line by a single acoustic pressure sensor. Fig. 1 is the sketch map and scene photo of the experiments designed. The noise level was assessed by A-weighted sound pressure level under various machining technology adjustments of cutter tool, machining feed rate, cutting way, and sealing the openings with sound-absorbing materials or not.
Fig. 1The experiments designed for the machining noise measuring
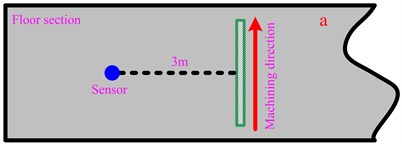
a) Sketch map
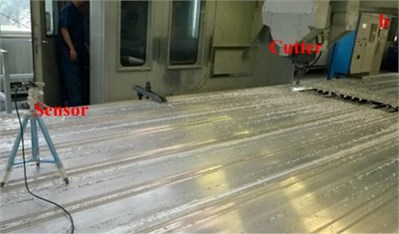
b) Scene photo
2.2. Procedures and results
2.2.1. Experiments of cutter tool
The aim of the experiments of cutter tool is to study the noise effect of various kinds of structure and size were tested under the machining parameters of 8000 r/min rotation speed, 1000 mm/min feed rate, cutting along milling, 20 mm transverse cutting depth and 28 mm vertical cutting depth. Fig. 2(a) and 2(b) is the photographs of monolithic milling cutters with head diameter Ø32 mm and Ø40 mm, and Fig. 2(c) and 2(d) is the photographs of assembled milling cutters with head diameter Ø72 mm and Ø32 mm respectively.
Fig. 2photographs of four kinds of cutters
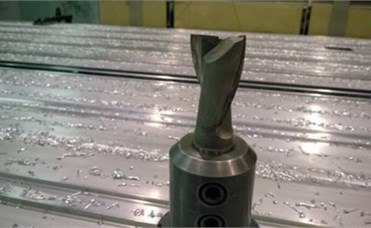
a) Ø32 mm monolithic milling cutter
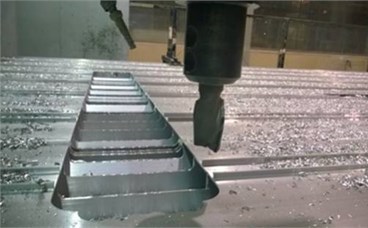
b) Ø40 mm monolithic milling cutter
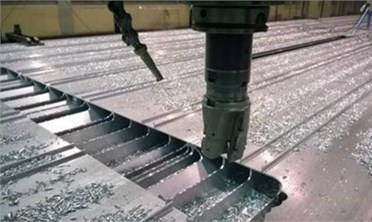
c) Ø72 mm assembled milling cutter
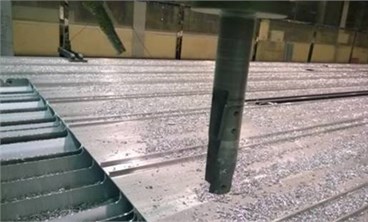
d) Ø32 mm assembled milling cutter
Fig. 3 is the A-weighted sound pressure level contrast between Ø32 mm monolithic and assembled cutters, Ø32 mm and Ø72 mm assembled cutters, as well as Ø32 mm and Ø40 mm monolithic cutters. The sharp peaks come from the cutter’s knocking with reinforcement ribs during the machining. Obvious noise intensity diversity was observed in Fig. 3, which indicated that monolithic cutters were superior to assembled, and thick diameter was superior to slim diameter. An exception exists in the first half time of Fig. 3(c), and author think that it could be from some non-steady state factors such as no clamping cutter.
Fig. 3The A-weighted sound pressure level contrast of various cutters
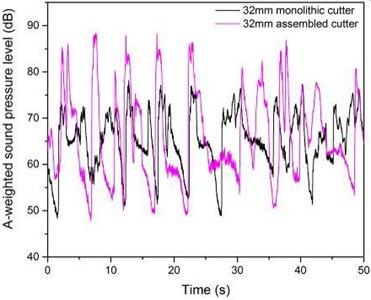
a) Ø32 mm monolithic and assembled cutters
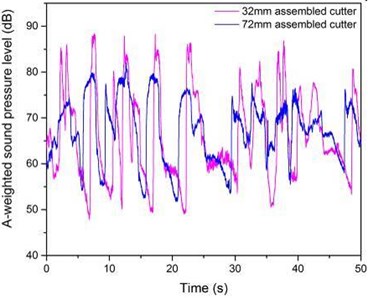
b) Ø32 mm and Ø72 mm assembled cutters
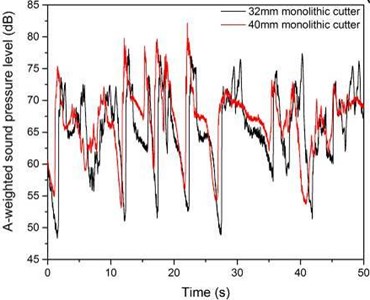
c) Ø32 mm and Ø40 mm monolithic cutters
Fig. 4The A-weighted sound pressure level contrast among the feed rates of 1000 mm/min, 800 mm/min and 600 mm/min
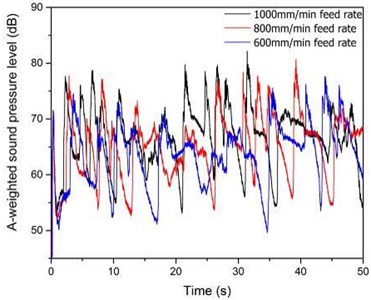
2.2.2. Experiments of machining feed rate
Three kinds of machining feed rates, 1000 mm/min, 800 mm/min and 600 mm/min, were tested under the machining parameters of Ø40 mm monolithic cutter, 8000 r/min rotation speed, cutting along milling, 20 mm transverse cutting depth and 28 mm vertical cutting depth. Fig. 4 is the A-weighted sound pressure level contrast among the feed rates of 1000 mm/min, 800 mm/min and 600 mm/min. It can easily be shown that a low feed rate present a weak noise level, but too low feed rate will seriously affect the machining efficiency, which is not what the producers want to see.
2.2.3. Experiments of cutting direction
Two kinds of cutting way, cutting along milling and reverse milling as sketched in Fig. 5, were tested by using Ø32 mm monolithic cutter, Ø40 mm monolithic cutter, Ø32 mm assembled cutter and Ø72 mm assembled cutter. The other machining parameters are 8000 r/min rotation speed, 1000 mm/min feed rate, 20 mm transverse cutting depth and 28 mm vertical cutting depth.
Fig. 5The sketch maps of cutting directions
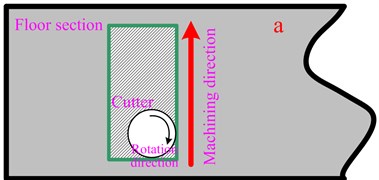
a) Cutting along milling
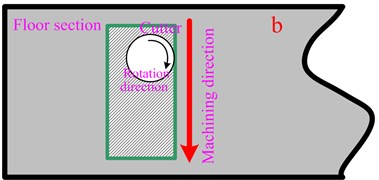
b) Cutting reverse milling
Fig. 6The A-weighted sound pressure level contrast of various cutting directions
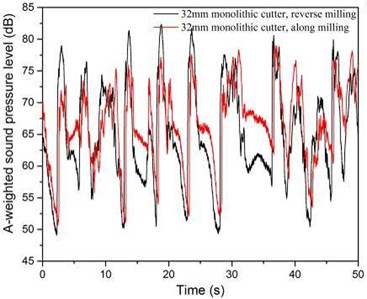
a) Ø32 mm monolithic cutter
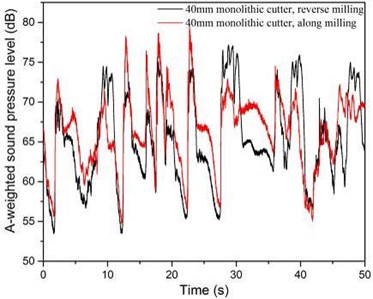
b) Ø40 mm monolithic cutter
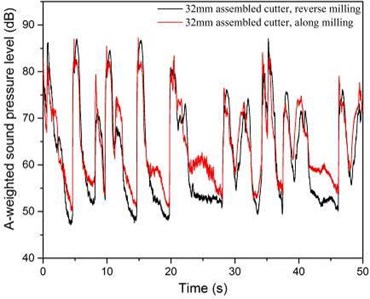
c) Ø32 mm assembled cutter
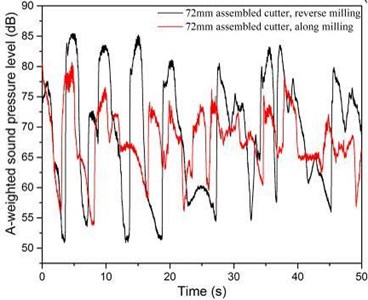
d) Ø72 mm assembled cutter
Fig. 6(a) is the A-weighted sound pressure level contrast between cutting along milling and reverse milling using Ø32 mm monolithic cutter, and Fig. 6(b)-(d) is Ø40 mm monolithic cutter, Ø32 mm assembled cutter and Ø72 mm assembled cutter respectively. It can be concluded that cutting along milling is good for noise control compared with reverse milling, no matter what kind of cutter. Furthermore, the effect of noise control is more notable when the cutter diameter is thicker.
2.2.4. Experiments of sealing the openings
In order to study the noise reduction, all the openings and ports on the extruded aluminum surface and cross section were sealed for blocking the sound transmission with sound-absorbing materials as shown in Fig. 7. The machining parameters are Ø32 mm assembled cutter, 8000 r/min rotation speed, 1000 mm/min feed rate, cutting along milling, 20 mm transverse cutting depth and 28 mm vertical cutting depth.
Fig. 7the photographs of sealing the openings and ports on the extruded aluminum
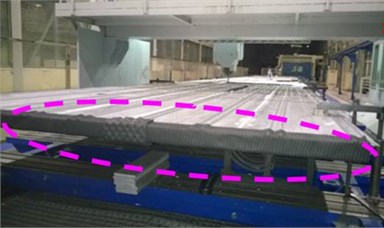
a) Ports on cross section
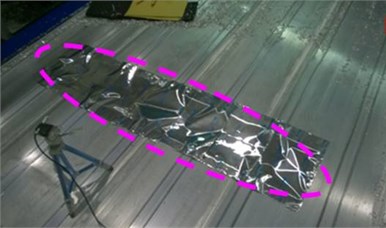
b) Openings on surface
Fig. 8Wavelet transforms of machining sound before a) and after b) pasting sound-absorbing materials
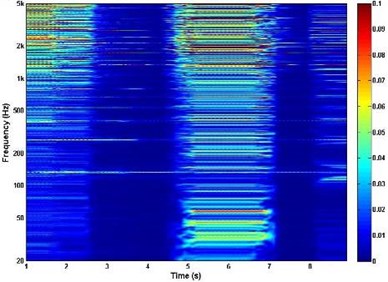
a)
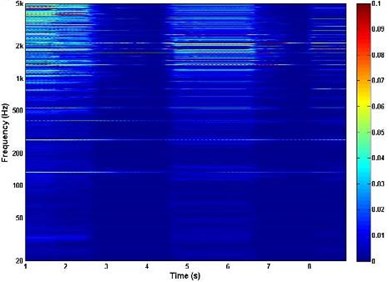
b)
Fig. 9The A-weighted sound pressure level contrast of before and after pasting sound-absorbing materials with different zooms
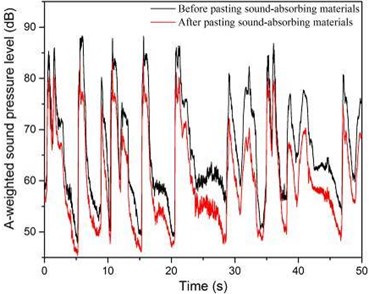
a) Global region
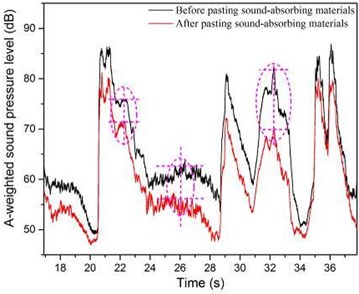
b) Local region
Measurements were conducted before and after pasting sound-absorbing materials, and Fig. 8 shows the sound pressure level in the range of 20-5000 Hz frequency band. Note that the reduction in sound pressure level was even distinct for the noise after pasting sound-absorbing materials on openings and ports as shown in Fig. 8(b) when compared to that before as shown in Fig. 8(a).
Fig. 9 shows the results of the A-weighted sound pressure level contrast with different zooms. An overall more than 5 dB noise reduction was observed by this means, which is an extremely simple and effective way of controlling the noise.
3. Conclusions
In this study, the intensity of machining noise of large size extruded aluminum floor section utilized in high-speed trains was investigated. The sound pressure was measured and converted to A-weighted sound pressure level in order to evaluate the noise control effects of various machining technologies such as cutter tool, machining feed rate, cutting way and sealing the openings with sound-absorbing material or not. The comparison results indicated that, by taking monolithic cutters and sealing the openings and ports with sound-absorbing materials, the machining noise level can be improved without the impact of machining efficiency. The noise can also be reduced by cutting along milling and slowing the feed rate down, in despite of sacrificing a certain machining efficiency.
References
-
Hardy A. E. J. Measure and assessment of noise within passenger trains. Journal of Sound and Vibration, Vol. 231, Issue 3, 2000, p. 819-829.
-
Parizet Etienne, Hamzaoui Nacer, Jacquemoud Johan Noise assessment in a high-speed train. Applied Acoustics, Vol. 63, 2002, p. 1109-1124.
-
Mellet C., Le’tourneaux F., Poisson F., Talotte C. High speed train noise emission: latest investigation of the aerodynamic/rolling noise contribution. Journal of Sound and Vibration, Vol. 293, 2006, p. 535-546.
-
Lee Pyoung Jik, Hong Joo Young, Jeon Jin Yong Assessment of rural soundscapes with high-speed train noise. Science of the Total Environment, Vols. 482-483, 2014, p. 432-439.
-
Connolly D. P., Kouroussis G., Woodward P. K., Giannopoulos A., Verlinden O., Forde M. C. Scoping prediction of re-radiated ground-borne noise and vibration near high speed rail lines with variable soils. Soil Dynamics and Earthquake Engineering, Vol. 66, 2014, p. 78-88.
-
Nagakura K. Localization of aerodynamic noise sources of Shinkansen trains. Journal of Sound and Vibration, Vol. 293, 2006, p. 547-556.
-
Kuwano Sonoko, Namba Seiichiro, Okamoto Takehisa Psychological evaluation of sound environment in a compartment of a high-speed train. Journal of Sound and Vibration, Vol. 277, 2004, p. 491-500.
-
Patsouras C., Fastl H., Widmann U., Hoelzl G. Psychoacoustic evaluation of tonal components in view of sound quality design for high-speed train interior noise. Acoustical Science and Technology, Vol. 23, 2002, p. 113-116.
-
Park Buhm, Jeon Jin-Yong, Choi Sunghoon, Park Junhong Short-term noise annoyance assessment in passenger compartments of high-speed trains under sudden variation. Applied Acoustics, Vol. 97, 2015, p. 46-53.
About this article
The authors would like to thank Changchun Railway Vehicles Co., Ltd., China for providing funding and experimental site support for this research.