Abstract
The paper provides a discussion on various solutions used in suspension systems of special-purpose vehicles. On account of its low cost and design simplicity owing to which it is commonly applied, the mechanical dependent suspension system based on leaf springs has been described. The paper also addresses non-conventional pneumatic and hydropneumatic systems based on gas springs, allowing for selected suspension parameters to be controlled, including clearance.
1. Introduction
Production of special-purpose vehicles (intended, for instance, for fire or rescue brigades etc.) is conducted on a short-series basis and it is adjusted to match specific requirements defined by the contracting party. On account of the special requirements, manufacture of such vehicles usually consists in adapting the chassis frame of the given manufacturer’s vehicle by appropriately modifying the structure. However, such modifications require that specific principles should be followed (e.g. it is impermissible that the steering and the braking system components should be modified). It is frequent that the body structure based on the chosen chassis requires adaptation of the vehicle frame which involves the necessity of extending the standard wheel base or the frame length. When extending the wheel base and the frame, the material used for extensions and reinforcing angles must conform to the standard vehicle frame in terms of quality and dimensions.
Fig. 1Sample special-purpose vehicle intended for fire brigades [23]
![Sample special-purpose vehicle intended for fire brigades [23]](https://static-01.extrica.com/articles/16511/16511-img1.jpg)
2. Suspension systems
In mechanical suspension systems of trucks, the function of elastic elements is typically performed by leaf springs, since they are both simple in design and economical. These elements are characterized by constant and non-exchangeable elasticity characteristics (Fig. 2) [1-6].
Fig. 3 illustrates a sample suspension system of a special-purpose vehicle.
Fig. 2Double leaf spring and its characteristics [16]
![Double leaf spring and its characteristics [16]](https://static-01.extrica.com/articles/16511/16511-img2.jpg)
![Double leaf spring and its characteristics [16]](https://static-01.extrica.com/articles/16511/16511-img3.jpg)
Fig. 3Sample suspension system of a special-purpose vehicle [23]
![Sample suspension system of a special-purpose vehicle [23]](https://static-01.extrica.com/articles/16511/16511-img4.jpg)
In mechanical suspension systems, as the load increases, static compression of the elastic element rises, whereas in cases of total loading, the range of available wheel travel on compression is reduced (see Fig. 4), this being one of the most considerable disadvantages of similar suspension systems. Therefore, one typically needs progressive characteristics to be obtained in spring-type suspension systems, which is achieved through appropriate design solutions (two parallel springs etc.).
Fig. 4a) Compression of springs in mechanical and b) pneumatic or hydropneumatic suspension systems [16]
![a) Compression of springs in mechanical and b) pneumatic or hydropneumatic suspension systems [16]](https://static-01.extrica.com/articles/16511/16511-img5.jpg)
With the hydropneumatic or pneumatic suspension system, static compression is independent of load, and the total range of the spring compression equals the dynamic compression. Consequently, there is no effect of the wheel travel range decreasing as static load rises, which makes it possible to use gas springs characterized by low rigidity coefficients compared to those of elastic elements applied in mechanical suspension systems, which additionally ensures high comfort of driving [1, 7-13].
In pneumatic suspension systems, gas springs of constant gas volume are used. With this solution, when static vehicle load changes, the compression compensation caused by loading is ensured by increasing the mass of gas inside the elastic spring (Fig. 4) [14-16].
Fig. 5Characteristics of pneumatic springs [16]
![Characteristics of pneumatic springs [16]](https://static-01.extrica.com/articles/16511/16511-img6.jpg)
![Characteristics of pneumatic springs [16]](https://static-01.extrica.com/articles/16511/16511-img7.jpg)
Hydropneumatic suspension systems feature gas springs (with constant gas mass), whereas the compression compensation triggered by the load proceeds through an increase of the liquid volume inside a hydraulic cylinder. In hydropneumatic suspension systems, the liquid is the incompressible coupling transferring the wheel motion to the gas spring’s elastic membrane [16-22].
Fig. 6Dynamic force vs. displacement characteristics for different static loads in a hydropneumatic strut (Citroen BX front strut)
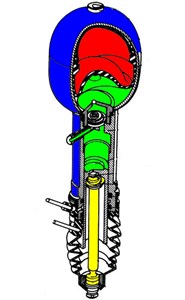
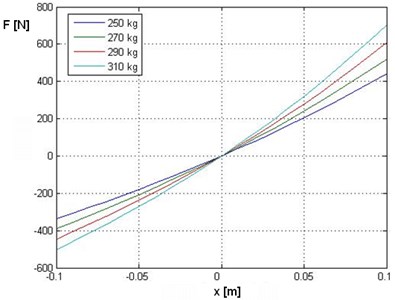
Application of different suspension design solutions affects many significant parameters, one of which is the system’s free vibration frequency. For a system with classical passive mechanical suspension (spring), the system’s free vibration frequency declines as load rises. In pneumatic suspension systems (constant gas volume springs), also frequency decreases as the load increases in a system featuring such a spring, however, not as considerably as in the system referred to.
In hydropneumatic suspension systems (featuring a constant gas mass spring), on the other hand, free vibration frequency rises as load does so (Fig. 7).
Fig. 7Changes in free vibration frequency for different suspension systems [11]
![Changes in free vibration frequency for different suspension systems [11]](https://static-01.extrica.com/articles/16511/16511-img10.jpg)
3. Conclusions
To recapitulate the foregoing, it should be noted that one of the most popular suspension system solutions used in special-purposes vehicles is the dependent suspension with leaf springs. It is both relatively cheap and considerably reliable in terms of failure frequency. In cases when increased vehicle mobility in difficult terrain is required and when one must be able to adjust clearance, the solutions which provide an alternative towards mechanical systems are non-conventional pneumatic and hydropneumatic suspension systems. In pneumatic systems, constant gas volume springs are used and clearance is controlled by changing the gas quantity inside the system, whereas in a hydropneumatic system featuring a constant gas mass spring, clearance is adjusted by increasing the quantity of liquid in hydraulic cylinders.
References
-
Dixon J. C. The Shock Absorber. Handbook Society of Automotive Engineers Inc., Warrendale, PA, 1999.
-
Gillespie T. D. Fundamentals of Vehicle Dynamics. SAE International, 1992.
-
Grajnert J. Isolation of vibrations in machines and vehicles. Oficyna Wydawnicza Politechniki Wrocławskiej, Wrocław, 1997.
-
Szczęśniak G., Nogowczyk P., Burdzik R., Konieczny Ł. Requirements for construction of the bodies of special vehicles. Scientific Journal of Silesian University of Technology, Series Transport, Vol. 87, 2015, p. 73-79, (in Polish).
-
Szczęśniak G., Nogowczyk P., Burdzik R., Konieczny Ł. Application of mounting frames in special vehicles. Scientific Scientific Journal of Silesian University of Technology, Series Transport, Vol. 87, 2015, p. 81-86, (in Polish).
-
Warczek J., Burdzik R., Peruń G. The method for identification of damping coefficient of the trucks suspension. Key Engineering Materials, Vol. 588, 2014, p. 281-289.
-
Burdzik R., Konieczny Ł., Adamczyk B. Automatic control systems and control of vibrations in vehicles car. Communications in Computer and Information Science, Vol. 471, 2014, p. 1865-0929.
-
Czop P., Sławik D., Włodarczyk T. H. Wojtyczka M., Wszołek G. Six Sigma methodology applied to minimizing damping lag in hydraulic shock absorbers. Journal of Achievements in Materials and Manufacturing Engineering, Vol. 49, Issue 2, 2011.
-
Konieczny Ł. The statistical analysis of damping parameters of hydraulic shock absorbers. Diagnostyka, Vol. 15, Issue 1, 2014, p. 49-52.
-
Konieczny Ł., Burdzik R. Comparison of characteristics of the components used in mechanical and non-conventional automotive suspensions. Solid State Phenomena, Vol. 210, 2014, p. 26-31.
-
Kowal J. Vibration Control. Gutenberg, Kraków, 1996.
-
Lanzendoerfer J. The research on motor vehicles. Wydawnictwo Komunikacji i Łączności, Warszawa, 1997, (in Polish).
-
Reński A. Construction of car: brake systems and steering and suspension. Oficyna Wydawnicza Politechniki Warszawskiej, Warszawa, 2004, (in Polish).
-
Ławniczak S., Simiński P. Hydropneumatic suspension modelling for wheeled armoured fighting vehicle. Journal of KONES Powertrain and Transport, Vol. 16, Issue 2, 2009, p. 285-297.
-
Palej R. Dynamics and stability of active pneumatic vibration isolation systems. Wydawnictwo Politechniki Krakowskiej, Kraków, 1997.
-
Rau M. Modellierung, Simulation Und Auslegung Eines Hydropneumatischen Federbeins Mit Schnell Verstellbarer Dämpfung. Thesis, Universitat Stuttgart, 2001.
-
Burdzik R., Gardulski J., Konieczny Ł. Methodology for determining the damping forces of the hydropneumatic strut on t indicator test stand. Przegląd Mechaniczny, Vol. 2, 2007, p. 38-40.
-
Cao D. P., Rakheja S., Su C. Y. Roll plane analysis of interconnected hydro-pneumatic suspension struts. Proceedings of the ASME Design Engineering Division, 2005, p. 133-142.
-
Giliomee C. L. Analysis of a Four State Switchable Hydro-Pneumatic Spring and Damper System. University of Pretoria, 2005.
-
Konieczny Ł., Gardulski J. Application of simulation researches in diagnostics of vehicle hydropneumatic suspension. Transport Problems, Vol. 2, Issue 1, 2007, p. 13-21.
-
Konieczny Ł. Determination of the damping characteristics of hydropneumatic strut taking into account the chosen parameters. Scientific Journal of Silesian University of Technology, Series Transport, Vol. 69, 2010, p. 85-89, (in Polish).
-
Konieczny Ł., Burdzik R., Folęga P., Wieczorek A. N. Determination of the damping characteristics of hydro pneumatic suspension strut. Journal of Measurements in Engineering, Vol. 1, Issue 3, 2013, p. 155-158.
-
http://www.psszczesniak.pl/pl/produkty.
-
Konieczny Ł. Damping characteristics of hydropneumatic suspension strut in function of car static load. Journal of Vibroengineering, Vol. 17, Issue 1, 2015, p. 71-81.
About this article
This publication was prepared under implementation of Project No. WND-DEM-1-325/00 KoPlatWysMob entitled: “Development of a High-Mobility Wheeled Platform for Special Applications” co-financed from funds of the National Center for Research and Development as well as of the European Union under the European Regional Development Fund.