Abstract
This paper presents the values of dynamics loads determined during experimental investigations as multi-layered corrugated cardboard packages were subjected to loading mass and underwent shock loads. Existence of such loadings cause undesirable mechanical and exploitation damage to packages.
1. Introduction
A package has a number of functions. One the most important of them is protection. It has dual purpose – to protect the product during transportation and against the effect of environmental factors. A suitable package is one of the conditions of product protection that significantly reduces the losses occurring due the damage during loading and transporting [1, 2]. Great attention is focused on exploitation criteria by designing the packages because packages are subjected to various loading during their life cycle [3]. Not only static, but also and dynamic loading as the package could fall or be affected by vibrations during transportation [4-6].
The authors of works [7-9] analyzed the effect of the geometrical shape of corrugated cardboard boxes during shock loadings. In some cases the damage to packed products was determined, or deformations were measured, or visual assessment was performed based on relevant criteria.
This work differs from the previously mentioned ones by the fact that it analyses dangerous shock load values that have the greatest effect on deformations of a rectangle package. The aim of this work is to evaluate the resistance to dynamic loads of a rectangle corrugated cardboard package loaded by mass .
Fig. 1General view of a three-layered, B type corrugated paperboard used for experimental testing: height of corrugated paperboard: S= 3 mm; corrugated medium height: Sw= 2.14 mm; thickness of upper and lower layers: tt= 0.43 mm and tb= 0.43 mm; corrugated layer: tw= 0.45 mm; corrugated medium step: λ= 6.5 mm
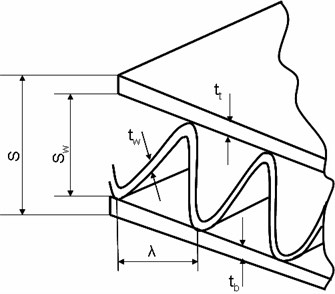
2. Methods and equipment used for the tests
Methods and equipment of deformation dependences of packages on mass and shock load.
18 rectangle corrugated cardboard packages were made for the tests with the following parameters: 140 mm; 250 mm; 160 mm (see Fig. 2). The tests were carried out at the ambient temperature 20±2 °C and air humidity 50±5 °C. The shock load testing stand, whose structural scheme and parameters are shown in Fig. 4 and Table 1, was used.
A study of a corrugated cardboard package (its geometrical parameters and the cross section of the corrugated cardboard are shown in Figs. 1 and 2) was carried out in order to determine the resistance to compression of packages under 15 kg mass and shock loads [10].
Fig. 2Tile of a three-layered corrugated paperboard package
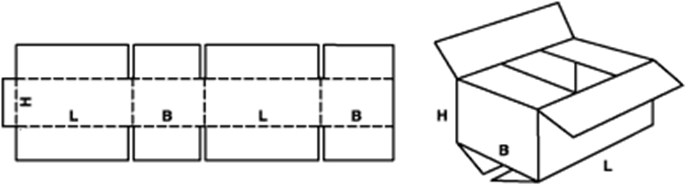
A stand was used for testing (see Fig. 3), where the corrugated cardboard package 3 was placed on steel plate 2 that is attached to shock generator 1 whose more detailed characteristics are listed in Table 1. On the package 3 15 kg mass was placed that could move in direction. The deformations of the package were recorded using sensors 5, 6. The obtained testing data were sent to personal computer 8.
Fig. 3General view of the shock load testing stand: 1 – shock generator; 2 – steel plate; 3 – sample; 4 – loading mass m; 5 – shock sensors; 6 – ultrasound distance sensor; 7 – oscilloscope; 8 – personal computer, h – move direction of mass m
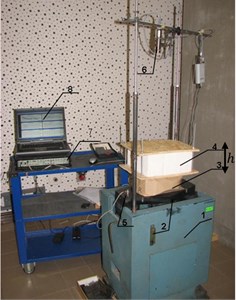
Fig. 4Structural scheme of the stand: 1 – shock generator; 2 – steel plate; 3 – sample; 4 – loading mass m; 5 – shock sensors; 6 – ultrasound distance sensor; 7 – oscilloscope; 8 – personal computer, h – move direction of mass m
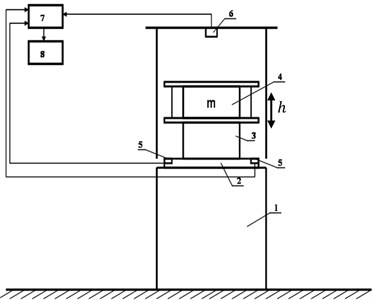
Table 1Parameters of shock impulse
Loading mass | Up to 5 kg | Up to 50 kg | Up to 100 kg |
Impulse duration | 1, 5,…, 20 ms | 2,..., 18 ms | 2,..., 15 ms |
Impulse acceleration | 100 m/s2,..., 4000 m/s2 | 100 m/s2,…, 1600 m/s2 | 100 m/s2,…, 500 m/s2 |
The parameters of the shock impulse presented in Table 1 were formed using the shock load testing stand. During the testing, the corrugated cardboard package is attached to a moving table raised to a particular height and dropped on a solid surface.
3. Research of package deformation dependences under dynamic loading
All the tested packages during the experiment were loaded with the same mass 15 kg. During the test, the acceleration of shock mass changes from 360 m/s2 to 140 m/s2. The aim of this research was to determine the effect of shock frequency and loading on the package deformation.
The test findings are given in Fig. 5.
Fig. 5Dependences of deformations of rectangle three-layered corrugated cardboard packages under dynamic effect when the load mass m= 15 kg
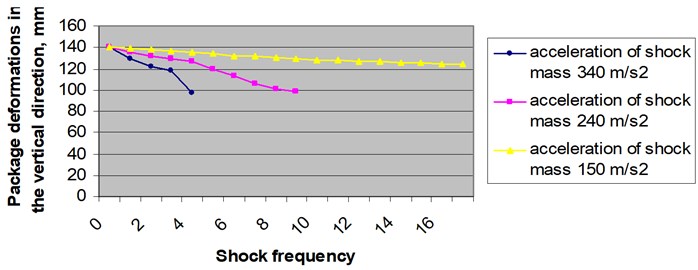
Carrying out the research in 340 m/s2 mode, it was determined that up to 5 shocks of the package on the solid surface, the package height in the vertical direction decreases by up to 40 mm. Besides, the edges of the package fold and the longest sidewall of the package buckles to the outer side (see Fig. 6).
Fig. 6General view of rectangle three-layered corrugated cardboard package after the experiment at shock acceleration 340 m/s2 and vertical load mass: 1 – shock generator; 2 – steel plate; 3 – sample; 4 – buckling of package longest sidewall into outer side; 5 – load mass m= 15 kg; 6 – shock sensors
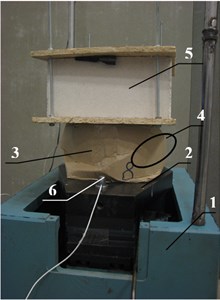
The other study carried out in 230 m/s2 mode has shown that a corrugated cardboard package is able to withstand almost a double number of shocks (9) as the package deforms in the same way after 5 shocks in 340 m/s2 mode under the same load mass 15 kg (see Fig. 5). In this case the height of the package after 5 shocks to a solid surface decreased only by 13 mm, meanwhile at 340 m/s2 shock the package decreased by 40 mm.
Carrying out the test in 150 m/s2 mode under the same conditions as in previous tests, the height of the package after 5 shocks to a solid surface decreased by only 5 mm. Such deformation is not clearly seen visually. As can be seen from the graph (see Fig. 5), at shock acceleration 150 m/s2 and mass 15 kg, the height of the package changes in 0.2÷1 mm range, depending on the number of shocks to a solid surface.
4. Conclusions
1) It was determined that dynamic loads with shock acceleration 340 m/s2 and load mass 15 kg are most dangerous to package deformations.
2) At the 210 m/s2-240 m/s2 range of 15 kg mass acceleration, the package can withstand two times more shocks to a solid surface than at the same 15 mass 340 m/s2 acceleration.
3) It was determined that the corrugated cardboard package loaded by mass 15 kg and at 150 m/s2 shock mass acceleration deforms very marginally after 4-5 shocks to a solid surface. At this shock mode, the deformation of the package in the vertical direction after 5 shocks is 5 mm.
4) It was determined that during package transportation, the most dangerous regime for their deformations is at 340 m/s2 shock mass acceleration.
References
-
Liaudenskis M. Product packaging and Research. Marketingas, Vols. 7-8, 2006, (in Lithuanian).
-
Hellstrom D., Nilsson F. Logistics-driven packaging innovation: a case study at IKEA. International Journal of Retail and Distribution Management, Vol. 39, Issue 9. 2011.
-
Prendergast P. G., Pitt L. Packaging, marketing, logistics and the environment: are there trade-offs? International Journal of Physical Distribution and Logistics Management, Vol. 26, Issue 6, 1996.
-
Sharan G., Srivastav S., Rawale K. P., Dave U. Development of corrugated fibre board cartons for long distance transport of tomatoes in India. International Journal for Service Learning in Engineering, Penn State University, Vol. 4, Issue 1, 2009, p. 31-43.
-
Luo S., Suhling J. C., Laufenberg T. L. Bending and twisting tests for measurement of the stiffness of corrugated board. Mechanics of Cellulosic Materials, Vol. 209, Issue 60, 1995.
-
Lu T. J., Chen C. Compressive behaviour of corrugated board panels. Journal of Composite Materials, Vol. 35, Issue 23, 2001, p. 2098-2126.
-
Krusper A., Isaksson P., Gradin P. Modeling of out-of-plane compression loading of corrugated paper board structures. Journal of Engineering Mechanics, Vol. 133, Issue 11, 2007, p. 1171-1177.
-
Silayoi P., Speece M. Packaging and purchase decisions: an exploratory study on the impact of involvement level and time pressure. British Food Journal, Vol. 106, Issue 8, 2004.
-
Naganathan Prabakaran B., Marcondes Jorge A. Effect of specimen size on test results to determine cushioning characteristics of corrugated fibreboard. Packaging Technology and Science, Vol. 8, Issue 2, 1995, p. 85-95.
-
LST EN 60068-2-27:2009. Enviromental testing. Part 2-27. Experiments. Ea Testing and instructions. Smūgis (IEC 60068-2-27:2008), (in Lithuanian).