Abstract
Research of the interaction of mechanical vibrations the car and driver and passenger is based on measurements of acceleration at predetermined points on the seat in three axes , , . Based on these measurements is possible to analyse the effect of mechanical vibrations on the biomechanics of human body. Short-term (fatigue) and long term (injury health) effect of mechanical vibration on the human body is described in many publications [1, 2] explaining this problem. The human body as a complex biomechanical assembly includes both elements as the spring elements and the damping elements. In case the assembly content damping elements exits in the assembly damping of the energy, of the mechanical oscillations (vibrations). How does the human body react to absorbed energy, is the question for detailed research. Surely we can reduce this energy to minimum, e.g. suitable isolation the source of mechanical vibrations.
1. Introduction
Research of correlation characteristics of the human body and active external factors (e.g. mechanical vibration), and body behaviour is challenging because there are experiments with human. For testing human we have got a lot of restrictions to protect their health during and after the experiment must not damage the health of the tested person. It is preferable to do with the test persons the laboratory experiments where the test can be accurately define and supervised by a responsible person (e.g. a doctor ...). The content of this article is verification tests on a car seat on a hexapod in the laboratory to determine the difference measurement results whole-body human and hard dummy.
2. Testing equipment at hydrodynamic laboratory
Measuring the effect of mechanical vibrations on human we provide more years [1] in hydrodynamic laboratory. The initial measurements were very limited implementation uniaxial vertical vibrations Fig. 1. On single cylinder was placed platform, on which was attached to a car seat.
Fig. 1Uniaxial vertical testing
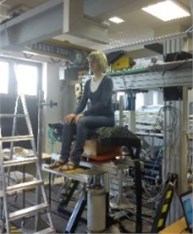
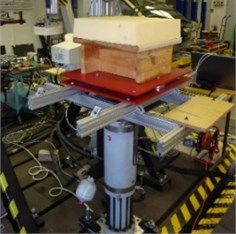
Fig. 2Multi-axis testing
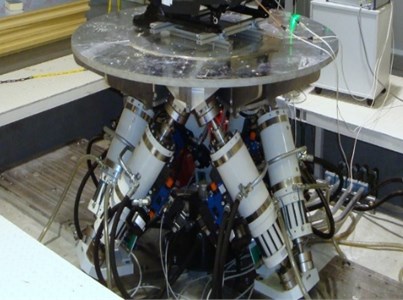
Fig. 3Testing car seat on hexapod
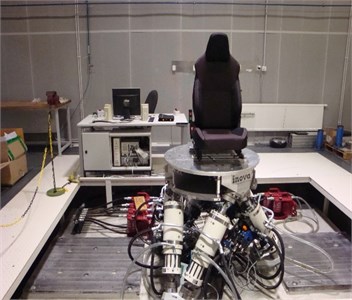
We now have a laboratory equipped by hexapod Fig. 2, where we can realize multi-axis vibration, thus space loading [2]. Hexapod has a parallel kinematic motion device providing six degrees of freedom: , , , pitch, roll and yaw Fig. 5. Of course can make loading only on “” axis direction or “” and “” axis. There was found by measuring on the floor in the car cabin, that the dominant component of the vibrations are vertical vibrations, i.e. component on axis “”, and only partially active side vibration on “” and “” axes. Thus, before, we proceed to implement space loading, we will now test a separate excitation axis on “” and so of the vertical vibration 100 % we derive lateral and anterior and posterior vibration 20 % Fig. 9.
As the first load was chosen figurine dummy type 3DH, which is made as a basic siting torso and hip joint according the standard test dummies TÜV SÜD Czech Fig. 4 Shaped back design complies with ISO 6549-1980. The knee joint and the legs are made accordance with the SEA J826, size group from 5 to 95 %. The material used is polished stainless steel, alloy steel and fiberglass. The total weight is 75 kg dummy-average physique.
Fig. 4Testing car seat with 3DH dummy
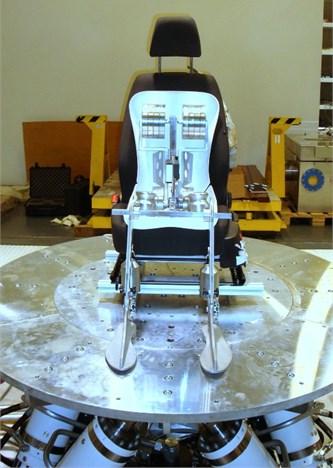
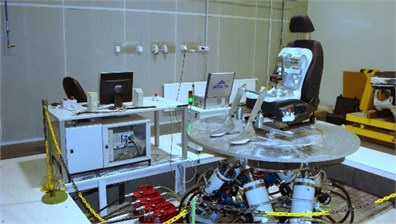
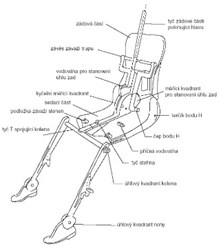
As the second load was chosen figurine type 2H Fig. 5, which is made as a basic 3DH siting torso. On torso is placed dual-mass load that is sprung up. The knee joint and the legs are not part of the dummy. The material used is polished stainless steel, alloy steel and fiberglass. The total weight is 65 kg dummy-average physique.
As the third load was chosen human type – average physique, weight is 75 kg Fig. 6.
Fig. 5Testing car seat with 2H dummy
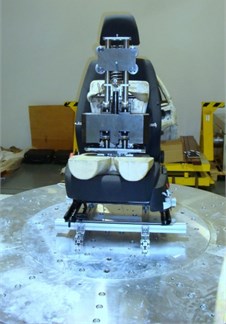
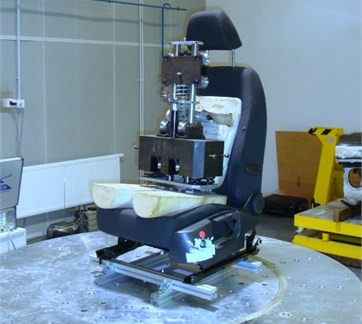
Fig. 6Testing car seat with whole-body human
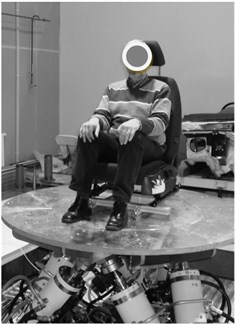
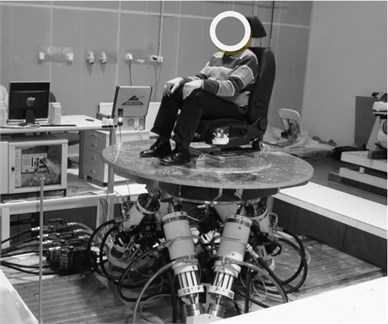
For getting good results is necessary to take great attention to the calibration of the sensors and the measurement channel. Calibration is made before each experiment. For calibration of accelerometers was made a special preparation in which are simultaneously inserted all the sensors to ensure equal conditions for calibration. Calibration of the sensors is saved simultaneously, successively in all axes. As a measurement device is a used device PC DEWE 5000. Calibrations are always saved with the measured data.
Fig. 7Location acceleration sensors
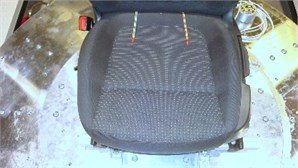
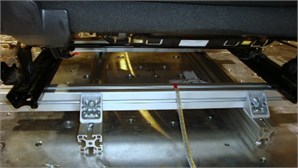
As test signals were chosen signals corresponding to driving car at constant speed on a flat part of road with an uneven surface Fig. 8. Before measurement sensors are placed at predetermined locations. For these measurements were used acceleration sensors that were placed on the seat anchorage, and two sensors on the rear seat under the buttock bones Fig. 7.
All sensors are triaxial acceleration sensor, i.e. measure the acceleration in the axes “” on Fig. 9 (and in axes “” and “”). Thus, we can evaluate both vertical and horizontal vibrations.
Fig. 8Excitation signals
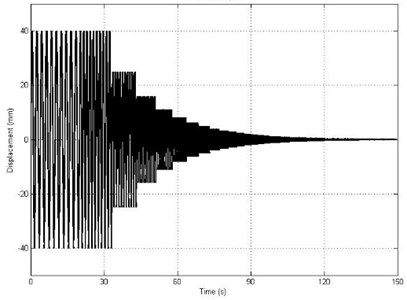
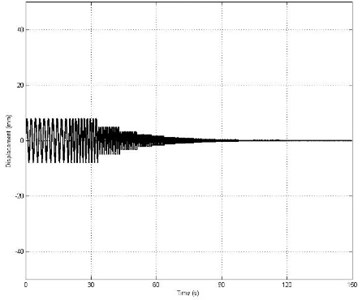
Fig. 9Measurement with 3DH dummy, 2H dummy, whole-body human
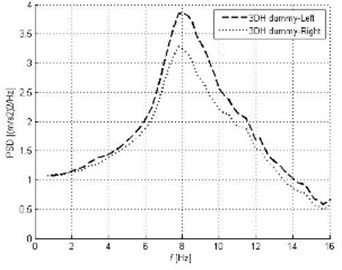
a)
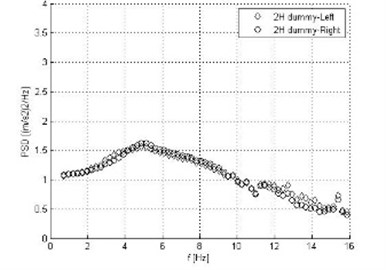
b)
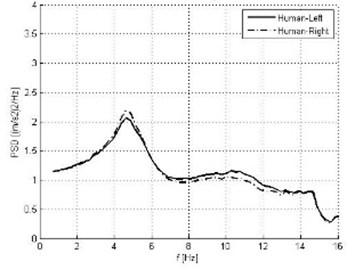
c)
3. Comparison of measurement
For comparison, the measurement we show as example test on Fig. 10. The measurements show a high disparity behavior of particular loads with the same test signal and the same test conditions (seat). The highest values PSD are achieved with 3DH dummy about 3.85, lower values was achieved with the human whole-body about 2.25 and lowest values with loads 2H dummy about 1.65. Resonance frequency is approximately 8.10 Hz, 4.25 Hz and 5.10 Hz. There is obvious that first load 3DH dummy don’t have damping of vibrations due to its construction, therefore are the highest values for both value PSD and resonance frequency. Second load 2H dummy and a third load human already behave as structured system and therefore have damping properties, resonance frequency almost no differences, but for human there appears lower damping, i.e. higher PSD. Each load behaves quite differently at the same conditions, on the same car seat. For relative comparison of various car seats are useful all loads. Not every car seat but is suitable for human seating, i.e. for long-term seating comfort. We must identify all the characteristics of interaction seats with whole-body human.
Fig. 11Measurement results and their comparison
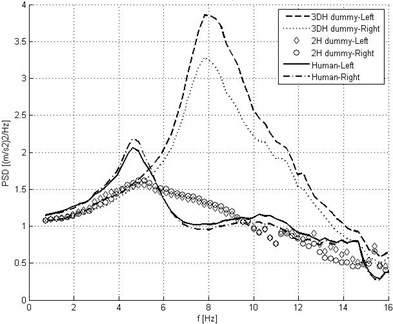
4. Conclusions
The results indicate is not quite possible to compare measurements of whole-body human and hard dummy. The human body behaves as biomechanical system with individual characteristics. Therefore, we will continue to proceed testing especially with whole-body human. It is important to make conclusions about human behavior under effect of mechanical vibration, especially with regard to the fatigue factor and limits damage to health. It has already been established that there is a correlation between the dissipated energy of mechanical vibration and fatigue test persons [3]. We too also focus to on identifying of static effect on fatigue, which imagines the same risk to human health as a dynamic effect.
References
-
Martonka R., Fliegel V. Absorbed energy of mechanical vibration by human and their comparison. 54th International Conference of Machine Design Department, Hejnice, Czech Republic, 2010, p. 111-116.
-
Martonka R., Fliegel V. Hexapod-the platform with 6DOF. 54th International Conference of Machine Design Department, Hejnice, Czech Republic, 2013, p. 111-116.
-
Mansfield Neil J. Human Response to Vibration. Libery of Congress Cataloging-in-Publication Data, CRC Press, 2005.