Abstract
The vehicle suspension system optimal design problem is multi-objective, has a hierarchical multi-level structure and presents couplings with the rest of the vehicle design. Moreover, many of the vehicle performances are dependent of the suspension system, specifically on its geometry. For this reason, it is desirable to develop a strategy in which the geometry of the suspension system is automatically generated with optimal characteristics. For this type of problems, the Analytical Target Cascading (ATC) brings a powerful optimization strategy that permits the management of a complex optimal design problem in a partitioned manner. This work proposes a new approach for the automatic optimal geometry generation of the suspension system of the vehicle, the development of the optimization problem in order to use the ATC optimization strategy and a case study in which a full-scale functional prototype is designed with the use of the developed tools.
1. Introduction
This work presents the optimal geometry generation of the suspension system of an off-road vehicle. The suspension system optimization problem is multi-objective and has a hierarchical structure: various performance objectives must be reached not only in the suspension performance itself, but also overall vehicle and components performance must be included. One of the most important objectives to be reached by the suspension system is to diminish the vibrations of the vehicle caused by road irregularities. This behavior interacts with other desired performances such as road holding and maneuverability at the suspension system design problem hierarchical level.
Moreover, interactions with other systems must be taken into account in order to have an overall coherent design. Many of the interactions present between the vehicle performance and the suspension system, as well as interactions with other systems in the vehicle are strongly affected by the suspension geometry. All of the above characteristics make the suspension geometry design a relevant and complex problem.
In order to be able to manage the size and complexity of this problem, a proper optimization strategy must be applied. For this type of problem is proposed the implementation of the Analytical Target Cascading (ATC) optimization strategy: it is applicable for multi-level, multi-objective hierarchical optimization problems [1, 2]. Different hierarchical levels are defined as follows: the super-system hierarchical level comprises the entire vehicle; the systems design level includes the suspension, powertrain and steering systems, and finally, the components design level. With this strategy, interactions between different levels, as well as within each hierarchical level, can be easily identified and included into the optimization problem.
Additional to the need of an adequate optimization strategy, a proper formulation of the geometry of the suspension system must be developed: depending on its formulation, the optimization problem can gain or lose complexity. This complexity depends on the degree of couplings present in the optimization sub-problems, which are a product of the formulation itself [3, 4]. The proposed formulation of the geometry of the suspension is not based directly from hard point locations. It is instead defined from an alternative set of design variables of different nature such as component dimensions and kinematic instantaneous rotation centers.
The suspension system design problem also involves a packaging problem, which is an extensive and complex problem itself [5-7]. Even though the geometric abstraction and solution has a physical significance, it has been developed a software interaction tool for the communication between the numerical software and a computer aided design software (CAD). This permits to visualize and verify optimization results and packaging aspects that are not included inside the problem formulation.
In this work, the proposed methodology and a case study in which the numerical results are applied to the design of a functional full-scaled prototype of an off-road vehicle are presented.
2. Suspension system kinematics
The suspension system under analysis corresponds to the double-wishbone front suspension system of a 4×4 off-road vehicle. The wheel has 6 degrees of freedom (DOF): vertical, longitudinal and lateral displacements and camber, caster and steer rotations. From the 6 DOF, only one DOF is fully independent: the vertical displacement. The steer angle rotation can be actuated by the steering system but its performance is coupled to the vertical displacement of the wheel by means of the suspension system elements. The other 4 DOF are assumed to be fully kinematically constrained.
For an easier analysis of the kinematics of the suspension it is more convenient to define five reference frames: ground (G), vehicle (V), upper wishbone (U), lower wishbone (L) and wheel carrier (C). The spatial location of the reference frames can be seen in Fig. 1(a). It is also convenient to define a set of points for the tracking of the movement of the different components. The main set of points defined in the formulation is related to the location of mechanical joints between components. For example, in Fig. 1(a), point “d” is located in the spherical joint between the upper wishbone and the wheel carrier. Additional to the definition of kinematic points for movement reference, it is also necessary to define the axes at which the wishbones rotate, as shown in Fig. 1(b).
Fig. 1Suspension system reference points
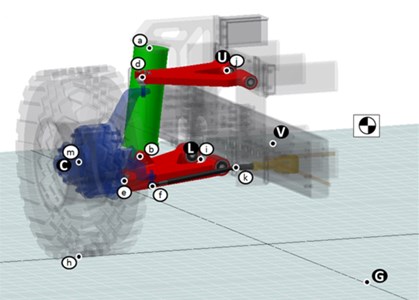
a)
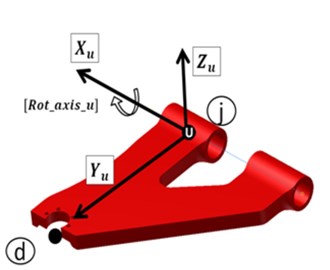
b)
The movement of the suspension system can be analyzed by three closed kinematic chains. Each loop contains a set of connected components that together determine the complete performance of the mechanism. The three kinematic chains are: upper wishbone kinematic chain as in Fig. 2(a); the lower wishbone kinematic chain as shown in Fig. 2(b); and the kinematic chain that contains the tie rod, as in Fig. 2(c). The mathematical representation of these chains is presented in Eq. (1)-(3):
Fig. 2Suspension system kinematic chains: a) upper wishbone kinematic chain; b) lower wishbone kinematic chain; c) tie-rod kinematic chain
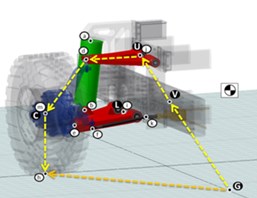
a)
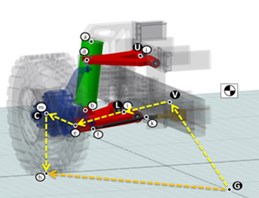
b)
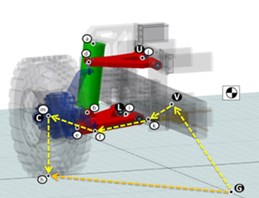
c)
The developed numerical model is based in an inverse kinematics formulation. Given that the position and orientation of the wheel carrier can be defined by three non-collinear points, the same number of linearly independent equations must be used such as Eq. (1)-(3). The variables that bring the solution to this system of equations are the rotation of the lower and upper wishbones, and the position of the joint between the steering system and the tie-rod (point “f”, Fig. 1(a)). The numerical abstraction of the suspension system is shown in Fig. 3(a). With this numerical model it is possible to find the position and orientation of all the components of the system at a given wheel vertical displacement, as shown in Fig. 3(b). This numerical model offers a low computational cost, making it attractive for iterative evaluations of alternative solutions.
Fig. 3Suspension system mathematical abstraction a) suspension system numerical model; b) suspension toe angle and bump-steer vs. wheel travel
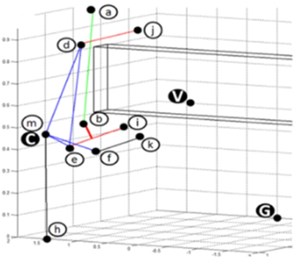
a)
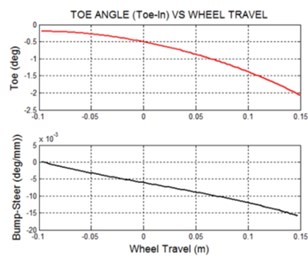
b)
3. Vehicle performance and suspension geometry
The general dynamics of a vehicle can be classified in three main sets: longitudinal, lateral and vertical dynamics. It is assumed that the vehicle is subjected to un-coupled dynamics in any of the three dynamics conditions. For example, for lateral dynamics, it is assumed that the vehicle is traveling on a regular road.
Each of the above dynamics operation conditions has a strong dependence on the suspension settings, mainly on its geometry. It is expected that a careful definition of the geometry of the suspension at early stages of the design will simplify later stages of development of the vehicle. Moreover, an efficient generation of its geometry will permit the designer to evaluate rapidly various design alternatives in order to cope with interactions with other systems in the vehicle.
Given that the vehicle performance depends strongly on the characteristics of its tires, and that tire performs according to the kinematics induced by the suspension system (or elasto-kinematics, in a more complex scenario analysis), a set of kinematic performance objectives must be included.
3.1. Longitudinal dynamics
For the longitudinal dynamics, upper and lower wishbone revolute joints location and orientation with respect to the horizontal plane are determinant to the pitch propensity of the vehicle when it is subjected to longitudinal accelerations [8]. There are four main performance parameters that quantify in a simple manner the pitch behavior of the vehicle: anti-dive, anti-squat, anti-rise and anti-lift [8]. For the current problem treatment, only the anti-dive performance parameter is considered.
3.2. Lateral dynamics
The lateral dynamics problem is more complex. Various authors report several performance criteria to quantify the handling performance of a vehicle, recognizing the multi-objective characteristics of the problem [9-12]. An efficient way of manage this type of problems consists in the generation of Pareto optimal sets of design solutions. Picking a Pareto set solution will lead to a solution for which the performance with respect to one aspect cannot be improved without worsening at least other objective function [13]. The set of objective functions of the handling dynamics is composed by different indicators related with lateral acceleration and yaw rate, linked to a lateral maneuver. A first part of those objective functions has as desirable behavior to maximize their values; these objective functions are peak lateral acceleration, 90 % of maximum lateral acceleration, steady state lateral acceleration, peak yaw rate, 90 % of maximum yaw rate and steady state yaw rate. A second part of the objective function has as desirable behavior to minimize their values; these objective functions are time to reach the peak lateral acceleration, time to reach 90 % of maximum lateral acceleration, lateral acceleration overshoot, time to reach the peak yaw rate, time to reach 90 % of maximum yaw rate and yaw rate overshoot.
Lateral dynamics is affected both by geometry and by the springing and damping settings. The handling of the vehicle depends on rolling of the chassis, weight transfer and tire performance. Tire performance is affected by wheel rotations and vertical loads, between many other factors [14]. These rotations, together with load transfer, are strongly dependent on suspension geometry. Suspension characteristics such as roll stiffness and damping, roll centers, bump (or roll) steer and bump (or roll) camber are determinant in handling.
3.3. Vertical dynamics
Vertical dynamics include the vibration response of the vehicle, as well as the road holding of the tire in irregular road profiles. These aspects depend on the springing and damping of the mechanism, as well as the geometric settings of the suspension. Similar to the lateral dynamics problem, if comfort and road holding performances are included as objective functions, the best solution is not unique, but will rather be a set of solutions from a Pareto optimal set [15].
For the present analysis, only a comfort performance criteria is considered, which is expressed as the natural vibration frequency of the sprung mass of the suspension system.
3.4. Wheel kinematics
In order to have a control of the effects of the suspension mechanism over the wheel kinematics, thus the vehicle overall dynamic performance, a set of relevant objective functions is defined. The indicators chosen as objective functions are scrub (including scrub radius, scrub at 100 mm bump and scrub at 100 mm rebound), camber (including its variation at 100 mm bump and 100 mm rebound), toe (including its variation at 100 mm bump and 100 mm rebound), Ackerman steering criterion and bump steer. It is important to note that in this case the desired behavior of the objective functions is to search for a specific objective (target) in order to have the desired performance of the mechanism.
4. Suspension system design parameters
The desired vehicle specifications are set from an early design stage by means of the definition of a set of design parameters. This set of parameters is quasi-fixed: this means that the design process will assume them fixed unless the following design problem is unfeasible under that set of parameters. The set of suspension design parameters is composed by the orientation of the wheel carrier in the nominal condition (including camber, caster and toe), geometric characteristics of the vehicle (including wheelbase, track and clearance), inertial properties of the vehicle (including sprung mass, location of the center of mass and inertia tensor), and wheel characteristics (including wheel radius, location of kinematic point “e” in the wheel carrier and tire dynamic characteristics).
5. Suspension system design variables
The three dynamics performances have couplings based in physical properties as well as the geometric settings of the suspension. The strength of these couplings depends on the assignment of the design variables from which the design problem is defined [4].
Contrary to the traditional definition of the suspension geometry, which is typically based on hard point locations, a new set of design variables that include other characteristics of the mechanism is proposed. These characteristics include roll centers, components dimensions and the orientation of the revolute axes of the wishbones. The set of variables is presented in Table 1 [16-17]. This new set of variables defines the geometry of the mechanism while reducing the couplings between sub-problems that are based in design variables. The set of hard point locations is found indirectly from the new variable formulation.
Table 1List of design variables
Reference frame | Design variable | |
Location of kinematic points | Wheel carrier | Spatial location of kinematic points “m”, “d” and “f” |
Lower wishbone | Spatial location of kinematic point “b” | |
Vehicle | Spatial location of kinematic points “a” and “k” | |
Geometric characteristics | Ground | Anti-roll |
Ground | Anti-roll factor | |
Ground | Anti-dive | |
Ground | Anti-dive factor |
It can be seen that this set of variables does not include the spatial location of the hard points related to the assembly between the wishbones and the chassis. This location is the result of the geometric processing of the design variables.
6. Results
With the application of the optimization methodology it was possible to generate automatically the suspension geometry with optimal characteristics. Some optimization results for the kinematics objective functions are presented in Table 2.
Table 2Optimization results for kinematics performance
Objective function | Reference value | Target value | Optimized value |
Scrub radius (mm) | –88.5 | –20 | –67.3 |
Camber variation at 100 mm bump (deg) | –0.82 | –0.50 | –0.45 |
Camber variation at 100 mm rebound (deg) | 1.03 | 0.50 | 0.57 |
Scrub at 100 mm bump (mm) | 4.0 | 10 | 5.3 |
Scrub at 100 mm rebound (mm) | –28.2 | –10 | –26.8 |
7. Conclusion
The methodology for the optimal generation of the geometry of a double wishbone suspension system by means of the application of multi-objective hierarchical optimization method has been presented.
The new variable design definition presented advantages in the optimization process in terms of the reduction of sub-problem couplings.
The developed optimization and geometry generation tool permitted the evaluation of multiple solutions with optimal performance with respect to additional design aspects not included in the optimization problem such as components interferences.
References
-
Kim H. Target Cascading in Optimal System Design. Ph.D. Thesis. University of Michigan, 2001.
-
Kim H., Michelena N., Papalambros P. and Jiang T. Target cascading in optimal system design. Journal of Mechanical Design, Vol. 125, Issue 3, 2003, p. 474.
-
Alyaqout S., Peters D., Papalambros P., Ulsoy A. Generalized coupling management in complex engineering systems optimization. Journal of Mechanical Design, Vol. 133, Issue 9, 2011.
-
Allison J., Kokkolaras M., Papalambros P. Optimal partitioning and coordination decisions in decomposition-based design optimization. Journal of Mechanical Design, Vol. 131, Issue 8, 2009.
-
Miao Y., Fadel G., Gantovnik V. Vehicle configuration design with a packing genetic algorithm. Journal of Heavy Vehicle Systems, Vol. 15, Issue 2-4, 2008, p. 433-448.
-
Bénabès J., Bennis F., Poirson E. and Ravaut Y. An interactive-based approach to the layout design optimization. Proceedings of the 20th CIRP Design Conference, 2011.
-
Cagan J., Shimada K., Yin S. A survey of computational approaches to three-dimensional layout problems. Computer-Aided Design, Vol. 34, Issue 8, 2002, p. 597-611.
-
Dixon J. Suspension Geometry and Computation. Wiley, 2009.
-
Kasprzak E., Lewis K., Milliken D. Steady-state vehicle optimization using pareto-minimum analysis. Proceedings of SAE Motorsports Engineering Conference, 1998.
-
Benedetti A., Farina M., Gobbi M. Evolutionary multiobjective industrial design: The case of a racing car tire-suspension system. IEEE Transactions on Evolutionary Computation, Vol. 10, Issue 3, 2006, p. 230-244.
-
Schuller J., Haque I., Eckel M. An approach for optimisation of vehicle handling behaviour in simulation. Vehicle System Dynamics, Vol. 37, 2002, p. 34-37.
-
Haghiac H., Haque I., Fadel G. An assessment of a genetic algorithm-based approach for optimising multi-body systems with applications to vehicle handling performance. International Journal of Vehicle Design, Vol. 36, Issue 4, 2004, p. 320-344.
-
Mastinu G., Gobbi M., Miano C. Optimal Design of Complex Mechanical Systems. Springer, 2006.
-
Pacejka H. Tyre and Vehicle Dynamics. 3rd Edition. SAE International, 2012.
-
Gobbi M. and Mastinu G. Analytical description and optimization of the dynamic behaviour of passively suspended road vehicles. Journal of Sound and Vibration, Vol. 245, Issue 3, 2001, p. 457-481.
-
Blanco J., Munoz L. Methodology for the design of a double-wishbone suspension system by means of target cascading: problem statement. Proceedings of the SAE World Congress, 2013.
-
Blanco J., Munoz L. Methodology for the design of a double-wishbone suspension system by means of target cascading: model-geometry interactions and case study. Proceedings of the SAE World Congress, 2013.
About this article
The authors wish to acknowledge INDUMIL (Colombia), who has funded and supported this research.