Abstract
Planetary gear trains (PGTs) are widely used in the field of mechanical transmission. PGTs significantly differ from fixed-axis gear trains and exhibit unique dynamic behavior. Dynamic characteristics of PGTs are popular research topic, particularly when attempting to solve the problem of vibration noise. Moreover, the effects of the planetary gear parameters on the dynamic characteristics are paramount important. And significant researches have been conducted in this field. However, few reviews regarding these studies have been published. In this paper, the effects of certain parameters, which include mesh phase difference, geometric errors (tooth profile error, eccentricity error and misalignment), tooth profile modification, mesh stiffness, and etc., on the dynamic characteristics of PGTs are summarized. Several conclusions obtained can be used for the PGTs design and dynamic characteristics analysis. Finally, the potential research trends are pointed out.
1. Introduction
PGTs are widely used in aerospace, automotive transmission, wind turbine and heavy industry applications and so on, owning to their high efficiency level, large transmission ratio and small volume, etc. [1]. Fig. 1 shows an example PGT has a ring gear, a sun gear that rotates around its own center. The planet gears are connected by bearings to the carrier and are simultaneously in mesh with both of the sun gear and ring gear. So the planet gears that not only rotate around the axis of carrier but also revolve around the center of the sun gear. The power is passed by the planet gears. The number of the planet gears is depended on the load of the PGT [2]. PGTs can achieve higher power density levels, because they use multiple parallel power paths formed by individual planet branches, and this coaxial and axisymmetric nature of PGTs makes them more compact [3].
Fig. 1Schematic diagram of PGT
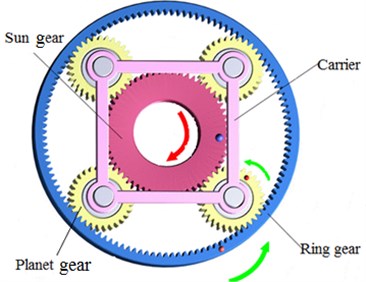
However, PGTs vibration and noise problems [4] are primary concerns in these applications because of the complexity of their system structures. But the vibration of the system can lead to excessive dynamic load and noise. The dynamic forces at the sun-planet and ring-planet meshes increase the risk of tooth or bearing failures. And the noise, which is caused by the vibration of gears, is important factor influencing occupant comfort and a measure of vehicle quality. Vibration can cause structural failure. These problems affect the transmission efficiency and service life of PGTs. The dynamic characteristics of PGTs are primary concerns both in terms of vibration and noise. In order to reduce vibration and noise of PGT, dynamics analysis is indispensable. On the other hand, PGTs significantly differ from fixed-axis gearboxes and exhibit unique dynamic behavior resulting in added noise, vibration, acoustic emissions, and unacceptable performance characteristics. These questions are severest when the transmission works in poor conditions (profile errors on teeth, geometric errors or lacking stiffness, etc.). Therefore, understanding the effects of these parameters on the dynamic behavior of PGTs is useful in design and analysis.
A number of papers have been published on dynamic characteristics of PGT, which consist of a finite element model [5-7] and deformable or hybrid models of varying complexities [8, 9]. Bu et al. [10] and Wu S. J. et al. [11] have reviewed the analysis model type of planetary gears, dynamic characteristics, calculation method of the dynamic respond, and so on. Meanwhile, the planetary gear dynamic characteristics are also affected by the parameters of the PGT. Sondkar and Kahraman [12] proposed a dynamic model of a double-helical PGT to demonstrate the effect of key design parameters including the right-to-left stagger angle, and support conditions on the dynamic response of the PGT. Parker and Lin [13] clarified the mesh phase properties for general planetary gears and provide a complete analytical description in terms of the fundamental parameters of tooth numbers and planet locations. Some analyses of the effects of mesh phase on planetary gear dynamic characteristics were conducted [14-21]. Several studies [22-24] confirmed that tooth profile errors can cause incorrect gear mesh and affect the transmission characteristic of the PGT.
The main research contents of this paper are as follows: in the first part, the effects of planetary gear parameters on the dynamics characteristics are summarized, which mainly include the mesh phase difference, geometric errors (tooth profile errors, electricity error and misalignment), TPM, and mesh stiffness. In the second part, the conclusions are discussed and summarized. These conclusions can be used to guide dynamic characteristic analysis and planetary gear design. Finally, future research trends in this area are described.
2. Effects of planetary gear parameters on dynamic characteristics
The effects of the planetary gear parameters on the dynamic characteristics are important to obtain an excellent PGT design. In the next part, the effects of the major planetary gear parameters on dynamic characteristic are respectively reviewed.
2.1. Mesh phase difference
Substantial researches [13-15, 18, 25] have been conducted on the mesh phase of PGT, which show that a mapping relationship exists between the phase matching and the excitation of PGT.
Jiang [16]studied the effect of the mesh phase of PGT on gear vibration and noise to better understand the application of mesh phase difference on the PGT. This application can reduce the gear vibration and noise levels, and these levels were less susceptible to the influence of the tooth surface mesh coefficient [16] and the tooth profile contact ratio [19, 26]. Chen and Ishibashi [19] designed and built an original PGT testing machine to examine how vibration and noise were affected by different contact ratios and meshing phase difference, and the testing results shown that the noise and vibration levels of PGT with a meshing phase difference can be further reduced by improving gear accuracy and tooth face roughness. Meanwhile, the PGT exists with combination of various mesh stiffness because of the mesh phase difference. This condition may lead to the PGT appearing to have a more dense frequency [17], and create a large difference for each planet gear vibration mode and an uneven load distribution. Thus, the reliability of PGT is reduced.
In the PGT, different mesh phase between the sun-planet and ring-planet mesh has powerful impact on the dynamic response and can have significant benefits in reducing vibration and noise[18, 19]. So a clear understanding of the relations governing the mesh phase is essential. Parker and Lin [13] clarified the mathematical relations for mesh phase for general PGT.
In the PGT, the planet gears are evenly distributed around the sun gear and each planet gear has the same parameters, the condition results in the periodic time-varying mesh stiffness of the sun gear. Through the design of the mesh phase difference, each planet gear acquires a different mesh phase and the effects of the excitation caused by mesh stiffness [20] can be reduced after superposition. Finally, the vibration can be neutralized or eliminated [21]. As shown in Fig. 2, a reasonable mesh phase difference was designed in PGT. Although the time-varying stiffness of each planet gear varies with the mesh periodic, the total mesh stiffness of PGT is a fixed value after the superposition.
Fig. 2Mesh stiffness of PGT [20]
![Mesh stiffness of PGT [20]](https://static-01.extrica.com/articles/15307/15307-img2.jpg)
a) Instantaneous mesh stiffness of sun-planets mesh
![Mesh stiffness of PGT [20]](https://static-01.extrica.com/articles/15307/15307-img3.jpg)
b) Total mesh stiffness of PGT after superposition
Therefore, the ultimate goal of designing the mesh phase difference is to change the time-varying mesh stiffness of the PGT. Finally, the vibration and noise are reduced.
2.2. Geometric errors
The effects of the geometric errors on the PGT dynamic characteristics have been studied extensively. Cheon and Parker [27] and James [28] studied the effect of manufacturing errors on the PGT dynamic characteristics. Typical errors of manufacturing errors, which include modulations include eccentricities and run-out errors of the gears and the carrier, and tooth-to-tooth spacing, tooth thickness and so forth, might cause modulations of PGT [29]. The combination of a series of incentive disturbance, which caused by the tooth profile errors, mounting errors, and deflections [30], cause the transmission error of PGT so that the vibration and noise are produced. The effects of the tooth profile errors, the eccentricities and the misalignments on the dynamic characteristics of the PGT are summarized in the follow paragraphs.
2.2.1. Tooth profile errors
Generally, tooth profile errors, which are induced by the manufacturing process, result in imperfections of the geometry of the tooth and create deviations from the perfect involute shape [31, 32]. As shown in Fig. 3, the solid lines show the actual tooth profile shapes and the dashed lines indicate the two closest tooth profile shape lines containing the actual tooth profile shape line.
Fig. 3Tooth profile errors [33]
![Tooth profile errors [33]](https://static-01.extrica.com/articles/15307/15307-img4.jpg)
The tooth profile errors may affect the contact quality of the tooth surface and cause the incorrect gear mesh, finally affect the transmission characteristic of the PGT. Moreover, the tooth profile errors can increase the gear mesh frequency amplitude. High values of these errors indicate poorly manufactured gears and tend to have dramatic consequences on the transmission [34]. A tooth profile can product an exciting force F(t), which represents an amplitude modulation of the gear mesh stiffness signal Ke(t) by the profile error signal Esn(t). It is expressed by:
where ˉEsm represents the profile error modulus, fe is the mesh frequency, ξsn is the phase difference of sun-planets mesh and m is the multiplicity of eigenvalues.
A previous study [24] suggested the tooth profile errors might be the cause of these variations in rattle amplitude. Another study [23] concluded that the composite profile errors of a gear pair had a stronger effect on the gear noise than the profile errors of a single gear. Moreover, the vibration noise of the gear mesh is correlated not only with the size of the shape errors but also with the direction of the tooth profile pressure angle error. At the meantime, the dynamic characteristics of PGT are affected by the tooth profile errors through affecting the mesh phase.
2.2.2. Eccentricity error
Eccentricity may be introduced during manufacture, or during set-up via shaft misalignment, imperfections in grub screw (set screw) tightness or ill- fitting bearings [22]. Moreover, eccentricity errors generate dynamic excitations and complex modulations which may downgrade the overall dynamic performance. To classic parallel axis gears, PTGs can be very sensitive to eccentricities, even in static conditions, when no central member is allowed to float. Chaari et al. [34] studied the effects of the eccentricity error (run-out error) on PGT dynamic response. He concluded that an exciting force is produced by the eccentricity error, which is expressed by Eq. (3), (4):
Gu and Velex [35] concluded that the eccentricity error could lead to contact loss at the critical speed. As far as dynamic tooth loads are considered, eccentricity errors do not introduce additional critical speeds but lead to more complex response spectra with modulation sidebands. As shown in Fig. 4, the eccentricity error increases the gear load ratio, which causes the gear tooth to bear excessive dynamic load and eventually leads to transmission failure. Furthermore, the gear with eccentricity errors, which subjected the varying mesh stiffness, can produce larger load ratio than the gear subjected constant mesh stiffness.
Fig. 4Effect of eccentricity error on gear load [35]
![Effect of eccentricity error on gear load [35]](https://static-01.extrica.com/articles/15307/15307-img5.jpg)
a) Maximum and minimum tooth load ratio of sun/planet gear
![Effect of eccentricity error on gear load [35]](https://static-01.extrica.com/articles/15307/15307-img6.jpg)
b) Maximum load ratio of sun/planet gear with different eccentricity error
2.2.3. Misalignment
The misalignment of PGT varies with time, which results in increasing the vibration, the time-varying contact stress and the probability of the failure of PGT, and reducing the gear life [36]. Litvin [37] reminded that due to misalignment the line contact of tooth surfaces is turned out into point contact. Litvin et al. [38] concluded that misalignment can cause the discontinuous transmission errors, and the bearing contact should be oriented longitudinally to increase the contact ratio. Thus the shift of bearing contact caused by misalignment is reduced. Crowther et al. [36] pointed out that when the bearing clearance is optimal, the contact stress amplitude can be decreased and a mean stress is achieved (Fig. 5). The gears are still misaligned, but this misalignment is now consistent with the rotation and can be corrected with lead slope adjustments.
Fig. 5Planet gears bearing maximum contact stress with carrier rotation after planet gears bearing clearance optimization [36]
![Planet gears bearing maximum contact stress with carrier rotation after planet gears bearing clearance optimization [36]](https://static-01.extrica.com/articles/15307/15307-img7.jpg)
Through the analysis of Crowther et al. [36], the misalignment is relative to bearing clearance of PGT, so the misalignment can be reduced by optimizing the bearing clearance.
Vecchiato [39] applied the new ideas of tooth contact analysis to prove that an isostatic PGT is a self-regulated system because of the existence of floating gears. He considered an isostatic planetary gear train is not sensitive to most misalignment and has capable of self-regulation in order to compensate for various alignment errors.
2.3. Tooth profile modification (TPM)
Excessive gear tooth deflection due to applied torque causes undesirable tooth contact patterns and increases gear vibration, noise, and contact stress. TPM is extensively used to compensate for the elastic gear and tooth deflection from the applied torque. Moreover, TPM can improve load distribution of PGT [40], eliminate the tooth elastic deformation, increase wear resistance and reduce gear contact stress. Meanwhile Abousleiman and Velex [7] showed that tip relief greatly reduces dynamic tooth loads and displacement amplitudes by the numerical simulations of the PGT model. Depending on the amount of mesh stiffness fluctuation and the mesh phase, different TPMs are required to minimize the gear vibration [41]. The changing of the sun-planet mesh stiffness with regard to TPM is shown in Fig. 6.
Fig. 6Sun-planet mesh stiffness with TPM
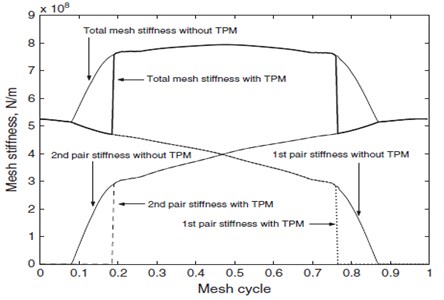
TPM is used to optimize contact patterns, to compensate manufacturing errors, and to reduce gear dynamic destruction. Liu and Parker [42] concluded that for the multimesh gear trains, the dynamic effect of the TPM is commonly correlated with the static transmission error. Furthermore, the TPM of individual mesh gear is correlated with mesh stiffness variations and contact ratios. The gear contact pattern is mainly affected by the TPM and dynamic response [41, 42].
To analyze the actual effect of the TPM on vibration reduction, Wu Y. J. et al. [43] studied the vibration level reduction under different working conditions through an experiment, as illustrated in Fig. 7.
Fig. 7Experimental vibration reduction of TPM
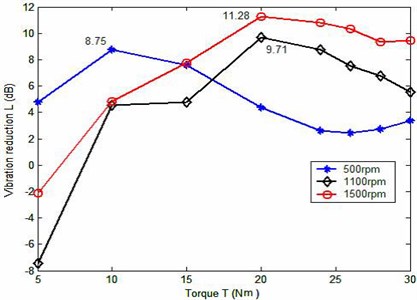
Fig. 6 shows that the effect of the presented TPM is not independent with the working conditions. With the increase of the torque, the effect of the TPM on vibration reduction is different for each speed, but the trends of the vibration reduction are almost the same for different speeds.
The TPM may deviate from the optimal area along with the change of mesh phase during optimization, and considering the interaction between the two gears mesh is necessary. According to Liu and Parker [42],the TPM for the minimal static transmission error (STE) depends only on the load and mesh stiffness of the single mesh. The optimal TPM for the minimal dynamic transmission error (DTE) is determined by mesh stiffness variations, contact ratios, mesh phase, and vibration modes. The TPM for the minimal STE does not necessarily lead to the minimal DTE, and it is proved by Bahk and Parker [41] by experimental verification.
2.4. Mesh stiffness
Gear mesh stiffness is a parametric excitation, and the effect of its dynamic excitation on gear dynamic characteristics is one of the main points of this study. According to Kahraman and Blankenship [44] and Chaari [45] mesh stiffness variation is one of the major sources of gear vibration. The time-varying mesh stiffness is a periodic function caused by the change in the number of contact tooth pairs and the contact positions of the gear teeth [46]. Experiments [47]demonstrated that the large amplitude vibration is induced by parametric instability wherein the gear mesh frequency equals twice the natural frequency (primary instability). Mesh stiffness directly affects the gear deformation and transmission error. Therefore, gear resonance excited by the harmonics of the transmission error fundamentally arises from the mesh stiffness variation [47, 48].
Liang et al. [46] stated that when to evaluate the mesh stiffness of PGT, the Hertzian contact stiffness, bending stiffness, axial compressive stiffness and shear stiffness should be considered. By studying the vibration response of the single-stage ear pair, Tian et al. [49] concluded that for the single-tooth-pair mesh duration, the total mesh stiffness is expressed as:
where subscripts 1 and 2 represent the pinion and the corresponding gear, respectively, kh is the Hertzian contact stiffness and kh=πEL/4(1-v2), kbis the bending stiffness and:
ka is the axial compressive stiffness and:
ks is the shear stiffness and:
α2 is the half tooth angle on the base circle of the external gear, α1 is the angle between the force component Fb and the acting force F which can be decomposed into two orthogonal component forces: Fa and Fb [46] (Fig. 8).
For the double-tooth-pair mesh duration, there are two pairs of gears mesh at the same time. The total mesh stiffness is expressed as [49]:
where i= 1 for the first pair of mesh teeth and i=2 for the second pair.
According to the above equations, Fspn is the dynamic gear mesh forces which can be expressed as [50]:
where kspn and cspn represents the nth sun-planet gear mesh stiffness and mesh damping, respectively, and δspn denotes the compression of the nth sun-planet mesh spring.
Fig. 8Elastic force on the external gear tooth [46]
![Elastic force on the external gear tooth [46]](https://static-01.extrica.com/articles/15307/15307-img10.jpg)
The instability of the mesh stiffness of PGT is sensitive to the contact ratio and mesh phase, and the instability can be inhibited by changing the two parameters [51, 52]. Lin and Parker [51, 52] concluded that the parametric excitation from the time-varying mesh stiffness causes instability and severe vibration under certain operating conditions (that is, mesh frequency and stiffness variation amplitude).
2.5. Effects of other factors
In addition to the aforementioned parameters, the amount of planet gears [53], pressure angle [54], tooth width [55], clearances [56, 57], backlash [58] and bearing stiffness [59] also affect the dynamic behavior of the PGT.
For instance, the backlash, which is essential for assembly of the gears [60], namely the clearance, tends to make gear systems exhibit typical nonlinear dynamic behavior, undesirable noise and vibration problems [56, 61, 62]. Furthermore, with the increasing of the backlash, the tooth contact force is increased and the contact time is reduced (Fig. 7) [58]. Litvin et al. [64] developed new types of PGT and the new designs were based on regulating backlash between the gears, which is to achieve almost uniform load distribution.
Fig. 9Gear contact force with different backlash [58]
![Gear contact force with different backlash [58]](https://static-01.extrica.com/articles/15307/15307-img11.jpg)
3. Conclusions
PGTs may exhibit undesirable dynamic behavior resulting in added noise, acoustic emissions, and unacceptable performance characteristics. The studies of the effects of the parameters on the dynamic characteristics of PGT are essential. Based on the above summaries, several conclusions obtained can be used for PGT design and analysis of dynamic characteristics.
1. Mesh phase difference can reduce the effect of the tooth surface mesh coefficient on the vibration and noise. In the PGT, phase difference design is necessary to acquire a different mesh phase for each planet gear. Therefore, the effect of time-varying stiffness on the dynamic responses of PGT can be reduced after the superposition.
2. The contact quality of the tooth surface is affected by the tooth profile errors. The dynamic characteristic of PGT also is affected by the tooth profile errors through affecting the mesh phase. The composite profile errors of a gear pair is the key factor that affects gear noise.
3. The eccentricity error can lead to contact loss and more complex response spectra. Furthermore, the misalignment can cause discontinuous transmission errors. The misalignment of the PGT is sensitive to the size of the bearing clearance and the bearing contact. Therefore, the bearing clearance should be optimized firstly, and the bearing contact should be oriented longitudinally to reduce the negative effects of misalignment.
4. TPM can improve the load distribution, eliminate the tooth elastic deformation, increase wear resistance, and reduce the contact stress. Meanwhile, in optimizing the TPM for the minimum DTE, the interaction between the two meshes as well as the effect of mesh phase on TPM should be considered.
5. The gear resonance excited by the harmonics of the transmission error fundamentally arises from the mesh stiffness variation. The instability of the mesh stiffness parameters can be reduced by reasonably choosing the gear contact ratio and mesh phase. Furthermore, the effects of mesh stiffness on the vibration are relative to the operating conditions.
4. Research prospects
Several key areas that may be targeted in further research include:
1. The preceding summaries show that certain parameters have mutual effects, such as [41, 64]. Bahk and Parker [50] through the experiment to prove that dynamic response is not guaranteed to be minimized by TPM, instead it may continuously grow for larger TPM for certain mesh phase choices. Thus, it is critical to take into account the mesh phase when designing profile modifications for planetary gears. Comprehensively considering the mutual effect of the parameters is important to study the effect of the dynamic characteristics and design of the PGT.
2. In addition to the aforementioned factors, the oil film stiffness [65] should also be considered and the friction between the meshing teeth is inevitable and has been suggested to play a considerable role in gear dynamics [66, 67]. Furthermore, the effect of the parameters on the dynamic characteristics of the PGT should also be considered for the “lost oil” condition of the gear.
3. Significant researches have been conducted on the dynamic characteristics of single-stage PGT, but studies on the multi-stage PGTs are few [68]. Thus, the mutual effect of compound planetary transmission [24, 69, 70] and the effects of various parameters on the dynamic characteristics of the compound PGTs require further research, such as that presented by the reference [24].
4. The effects of PGT parameters with non-circular gears [71] on dynamic characteristics should be studied further.
References
-
Qian P. Y., Zhang Y. L., Cheng G., et al. Model analysis and verification of 2K-H planetary gear system. Journal of Vibration and Control, 2013, p. 1-12.
-
Cooley C. G., Parker R. G. A review of planetary and epicyclic gear dynamics and vibrations research. Applied Mechanics Reviews, Vol. 66, Issue 4, 2014, p. 040804-1-040804-15.
-
Ligata H., Kahraman A., Singh A. An experimental study of the influence of manufacturing errors on the planetary gear stresses and planet load sharing. Journal of Mechanical Design, Vol. 130, Issue 4, 2008, p. 041701-1-041701-9.
-
Parker R. G., Lin J. Modeling, modal properties, and mesh stiffness variation instabilities of planetary gears. Report, Ohio State University, Department of Mechanical Engineering, Columbus, Ohio, May, 2001.
-
Parker R. G., Agashe V., Vijayakar S. M. Dynamic response of a planetary gear system using a finite element/contact mechanics model. Journal of Mechanical Design, Vol. 122, 2000, p. 304-310.
-
Ambarisha V. K., Parker R. G. Nonlinear dynamics of planetary gears using analytical and finite element models. Journal of sound and vibration, Vol. 302, Issue 3, 2007, p. 577-595.
-
Abousleiman V., Velex P. A hybrid 3D finite element/lumped parameter model for quasi-static and dynamic analyses of planetary/epicyclic gear sets. Mechanism and Machine Theory, Vol. 41, Issue 6, 2006, p. 725-748.
-
Kahraman A., Kharazi A. A., Umrani M. A deformable body dynamic analysis of planetary gears with thin rims. Journal of Sound and Vibration, Vol. 262, Issue 3, 2003, p. 752-768.
-
Heege A., Betran J., Radovcic Y. Fatigue load computation of wind turbine gearboxes by coupled finite element, multi-body system and aerodynamic analysis. Wind Energy, Vol. 10, Issue 5, 2007, p. 395-413.
-
Bu Z. H., Liu G., Wu L. Y. Research advances in planetary gear trains dynamics. Journal of Vibration and Shock, Vol. 9, Issue 9, 2010, p. 161-166, (in Chinese).
-
Wu S. J., Ren H., Zhu E. Y., et al. Research advances for dynamics of planetary gear trains. Engineering Journal of Wuhan University, Vol. 43, Issue 3, 2010, p. 398-403, (in Chinese).
-
Sondkar P., Kahraman A. A dynamic model of a double-helical planetary gear set. Mechanism and Machine Theory, Vol. 70, 2013, p. 157-174.
-
Parker R. G., Lin J. Mesh phasing relationships in planetary and epicyclic gears. Journal of Mechanical Design, Vol. 126, Issue 2, 2004, p. 365-370.
-
Ambarisha V. K., Parker R. G. Suppression of planet mode response in planetary gear dynamics through mesh phasing. Journal of Vibration and Acoustics, Vol. 128, Issue 2, 2006, p. 133-142.
-
Canchi S. V., Parker R. G. Effect of ring-planet mesh phasing and contact ratio on the parametric instabilities of a planetary gear ring. Journal of Mechanical Design, Vol. 130, Issue 1, 2008, p. 014501-1-014501-6.
-
Jiang C. M. Research of noise and vibration of planetary gear driver. Automobile Gear, Vol. 2, 2009, p. 9-16, (in Chinese).
-
Duan F. H. Effects of meshing phase on natural characteristics of planetary gears. Chinese Mechanical Engineering, Vol. 20, Issue 17, 2009, p. 2035-2040, (in Chinese).
-
Parker R. G. A physical explanation for the effectiveness of planet phasing to suppress planetary gear vibration. Journal of Sound and Vibration, Vol. 236, Issue 4, 2000, p. 561-573.
-
Chen Y., Ishibashi A. Investigation of the noise and vibration of planetary gear drives. ASME 2003 Design Engineering Technical Conferences and Computers and Information in Engineering Conference, Chicago, Illinois, USA, 2003, p. 507-513.
-
Liu S. H. Study on the characteristic of vibration of the sun gear for planetary gear trains with or without phase difference. Master’s Thesis, Jilin University, 2006, (in Chinese).
-
Blunt D. M., Keller J. A. Detection of a fatigue crack in a UH-60A planet gear carrier using vibration analysis. Mechanical Systems and Signal Processing, Vol. 20, Issue 8, 2006, p. 2095-2111.
-
Ottewill J. R., Neild S. A., Wilson R. E. Intermittent gear rattle due to interactions between forcing and manufacturing errors. Journal of Sound and Vibration, Vol. 321, Issue 3, 2009, p. 913-935.
-
Dai Z. M., Li G. Y. Influence of comprehensive tooth profile error of gear pair on gear transmission accuracy. Science and Technology Innovation Herald, Vol. 1, 2009, p. 085, (in Chinese).
-
Ottewill J. R., Neild S. A., Wilson R. E. An investigation into the effect of tooth profile errors on gear rattle. Journal of Sound and Vibration, Vol. 329, Issue 17, 2010, p. 3495-3506.
-
Guo Y., Parker R. G. Analytical determination of mesh phase relations in general compound planetary gears. Mechanism and Machine Theory, Vol. 46, Issue 12, 2011, p. 1869-1887.
-
Parker R. G. A physical explanation for the effectiveness of planet phasing to suppress planetary gear vibration. Journal of Sound and Vibration, Vol. 236, Issue 4, 2000, p. 561-573.
-
Cheon G. J., Parker R. G. Influence of manufacturing errors on the dynamic characteristics of planetary gear systems. KSME International Journal, Vol. 18, Issue 4, 2004, p. 606-621.
-
James B., Harris O. Predicting unequal planetary load sharing due to manufacturing errors and system deflections, with validation against test data. Transmission and Driveline Systems Symposium, 2002, p. 1655.
-
Ligata H., Kahraman A., Singh A. An experimental study on the influence of manufacturing errors on the planetary gear stresses and planet load sharing. Journal of Mechanical Design, Vol. 130, Issue 4, 2008, p. 041701-1–041701-9.
-
Velex P., Maatar M. A mathematical model for analyzing the influence of shape deviations and mounting errors on gear dynamic behaviour. Journal of Sound and Vibration, Vol. 191, Issue 5, 1996, p. 629-660.
-
Wagaj P., Kahraman A. Influence of tooth profile modification on helical gear durability. Journal of Mechanical Design, Vol. 124, Issue 3, 2002, p. 501-510.
-
Bodas A., Kahraman A. Influence of carrier and gear manufacturing errors on the static load sharing behavior of planetary gear sets. JSME International Journal Series C, Vol. 47, Issue 3, 2004, p. 908-915.
-
Luo T. J. Control method of the gear tooth profile deviations. Mechanical Transmission, Vol. 32, Issue 4, 2008, p. 97-98, (in Chinese).
-
Chaari F., Fakhfakh T., Hbaieb R., et al. Influence of manufacturing errors on the dynamic behavior of planetary gears. The International Journal of Advanced Manufacturing Technology, Vol. 27, Issue 7-8, 2006, p. 738-746.
-
Gu X., Velex P. On the dynamic simulation of eccentricity errors in planetary gears. Mechanism and Machine Theory, Vol. 61, 2013, p. 14-29.
-
Crowther A., Ramakrishnan V., Zaidi N. A., et al. Sources of time – varying contact stress and misalignments in wind turbine planetary sets. Wind Energy, Vol. 14, Issue 5, 2011, p. 637-651.
-
Litvin F. L., Lu J., Townsend D. P., et al. Computerized simulation of meshing of conventional helical involute gears and modification of geometry. Mechanism and Machine Theory, Vol. 34, Issue 1, 1999, p. 123-147.
-
Litvin F. L., Fuentes A., Gonzalez-Perez I., et al. Modified involute helical gears: computerized design, simulation of meshing and stress analysis. Computer Methods in Applied Mechanics and Engineering, Vol. 192, Issue 33, 2003, p. 3619-3655.
-
Vecchiato D. Tooth contact analysis of a misaligned isostatic planetary gear train. Mechanism and Machine Theory, Vol. 41, Issue 6, 2006, p. 617-631.
-
Litvin F. L., Vecchiato D., Demenego A., et al. Design of one stage planetary gear train with improved conditions of load distribution and reduced transmission errors. Journal of Mechanical Design, Vol. 124, Issue 4, 2002, p. 745-752.
-
Bahk C. J., Parker R. G. Analytical investigation of tooth profile modification effects on planetary gear dynamics. Mechanism and Machine Theory, Vol. 70, 2013, p. 298-319.
-
Liu G., Parker R. G. Dynamic modeling and analysis of tooth profile modification for multimesh gear vibration. Journal of Mechanical Design, Vol. 130, 2008, p. 121402.
-
Wu Y. J., Wang J. J., Han Q. K. Static/dynamic contact FEA and experimental study for tooth profile modification of helical gears. Journal of Mechanical Science and Technology, Vol. 26, Issue 5, 2012, p. 1409-1417.
-
Kahraman A., Blankenship G. W. Interactions between commensurate parametric and forcing excitations in a system with clearance. Journal of Sound and Vibration, Vol. 194, Issue 3, 1996, p. 317-336.
-
Chaari F., Baccar W., Abbes M. S., et al. Effect of spalling or tooth breakage on gearmesh stiffness and dynamic response of a one-stage spur gear transmission. European Journal of Mechanics-A/Solids, Vol. 27, Issue 4, 2008, p. 691-705.
-
Liang X., Zuo M. J., Patel T. H. Evaluating the time-varying mesh stiffness of a planetary gear set using the potential energy method. Proceedings of the Institution of Mechanical Engineers, Part C: Journal of Mechanical Engineering Science, Vol. 228, Issue 3, 2014, p. 535-547.
-
Kahraman A., Blankenship G. W. Experiments on nonlinear dynamic behavior of an oscillator with clearance and periodically time-varying parameters. Journal of Applied Mechanics, Vol. 64, Issue 1, 1997, p. 217-226.
-
Parker R. G., Vijayakar S. M., Imajo T. Non-linear dynamic response of a spur gear pair: modelling and experimental comparisons. Journal of Sound and Vibration, Vol. 237, Issue 3, 2000, p. 435-455.
-
Tian X. H., Zuo M. J., Fyfe K. R. Analysis of the vibration response of a gearbox with gear tooth faults. ASME 2004 International Mechanical Engineering Congress and Exposition, Anaheim, California, 2004, p. 785-793.
-
Liang X., Zuo M. J. Dynamic simulation of a planetary gear set and estimation of fault growth on the sun gear. International Conference on Quality, Reliability, Risk, Maintenance, and Safety Engineering, 2013, p. 1667-1672.
-
Lin J., Parker R. G. Planetary gear parametric instability caused by mesh stiffness variation. Journal of Sound and Vibration, Vol. 249, Issue 1, 2002, p. 129-145.
-
Lin J., Parker R. G. Mesh stiffness variation instabilities in two-stage gear systems. Journal of Vibration and Acoustics, Vol. 124, Issue 1, 2002, p. 68-76.
-
Inalpolat M., Kahraman A. A dynamic model to predict modulation sidebands of a planetary gear set having manufacturing errors. Journal of Sound and Vibration, Vol. 329, Issue 4, 2010, p. 371-393.
-
Kim W., Lee J. Y., Chung J. Dynamic analysis for a planetary gear with time-varying pressure angles and contact ratios. Journal of Sound and Vibration, Vol. 331, Issue 4, 2012, p. 883-901.
-
İmrek H., Düzcükoğlu H. Relation between wear and tooth width modification in spur gears. Wear, Vol. 262, Issue 3, 2007, p. 390-394.
-
Sun T., Hu H. Y. Nonlinear dynamics of a planetary gear system with multiple clearances. Mechanism and Machine Theory, Vol. 38, Issue 12, 2003, p. 1371-1390.
-
Guo Y., Parker R. G. Dynamic modeling and analysis of a spur planetary gear involving tooth wedging and bearing clearance nonlinearity. European Journal of Mechanics-A/Solids, Vol. 29, Issue 6, 2010, p. 1022-1033.
-
Lin T., Ou H., Li R. A finite element method for 3D static and dynamic contact/impact analysis of gear drives. Computer Methods in Applied Mechanics and Engineering, Vol. 196, Issue 9, 2007, p. 1716-1728.
-
Gill-Jeong C., Parker R. G. Influence of bearing stiffness on the static properties of a planetary gear system with manufacturing errors. KSME International Journal, Vol. 18, Issue 11, 2004, p. 1978-1988.
-
Theodossiades S., Natsiavas S. Non-linear dynamics of gear-pair systems with periodic stiffness and backlash. Journal of Sound and Vibration, Vol. 229, Issue 2, 2000, p. 287-310.
-
Shyi-Jeng Tsai, Huang G. L, Ye S. Y. Gear meshing analysis of planetary gear sets with a floating sun gear. Mechanism and Machine Theory, 2014.
-
Litak G., Friswell M. I. Vibration in gear systems. Chaos, Solitons and Fractals, Vol. 16, Issue 5, 2003, p. 795-800.
-
Litvin F. L., Fuentes A., Vecchiato D., et al. New design and improvement of planetary gear trains. NASA Glenn Research Center, Technical Report Issue NASA/CR-2004-213101, http://gltrs.grc.nasa.gov.
-
Guo Y., Jonathan K., LaCava W. Combine effects of gravity, bending moment, bearing clearance, and input torque on wind turbine planetary gear load sharing. American Gear Manufacturers Association Fall Technical Meeting, Dearborn, Michigan, 2012, p. 53-68.
-
Singh A. Influence of planetary needle bearings on the performance of single and double pinion planetary systems. Journal of Mechanical Design, Vol. 129, Issue 1, 2007, p. 85-94.
-
Vaishya M., Singh R. Strategies for modeling friction in gear dynamics. Journal of Mechanical Design, Vol. 125, Issue 2, 2003, p. 383-393.
-
Vaishya M., Singh R. Sliding friction-induced non-linearity and parametric effects in gear dynamics. Journal of Sound and Vibration, Vol. 248, Issue 4, 2001, p. 671-694.
-
Cai Z. C., Liu H., Xiang C. L., et al. Research on natural characteristics and sensitivity for torsional vibration of a vehicle multistage planetary gears. China Mechanical Engineering, Vol. 22, Issue 1, 2011, p. 96-101, (in Chinese).
-
Kiracofe D. R., Parker R. G. Structured vibration modes of general compound planetary gear systems. Journal of Vibration and Acoustics, Vol. 129, Issue 1, 2007, p. 1-16.
-
Guo Y. C., Parker R. G. Sensitivity of general compound planetary gear natural frequencies and vibration modes to model parameters. Journal of Vibration and Acoustics, Vol. 132, Issue 1, 2010, p. 011006-1-011006-13.
-
Mundo D. Geometric design of a planetary gear train with non-circular gears. Mechanism and Machine Theory, Vol. 41, Issue 4, 2006, p. 456-472.
About this article
The authors acknowledge the financial support from National Natural Science Foundation of China (Issue 51375202 and 51075179) and Scientific Frontier and Interdisciplinary Merit Aid Projects of Jilin University, China (Issue 2013ZY08).