Abstract
This paper proposes a mechanical dispersion method of hydrated lime in a vibrating activator equipped with special blades that operate in a resonant mode. It has been found that during the vibro-activation process, hydrated lime consistently passes through proportionately increasing stages of dynamic viscosity, slowing its growth and ceasing dispersion. A new vibration method for determining the viscosity of the hydrated lime-water system has been developed. The effect of vibration treatment on changes in the dispersion of calcium hydroxide was studied. It has been found that vibration-treated lime, compared to conventional hydrated lime, has new properties: the ability to form durable coatings due to accelerated carbonization.
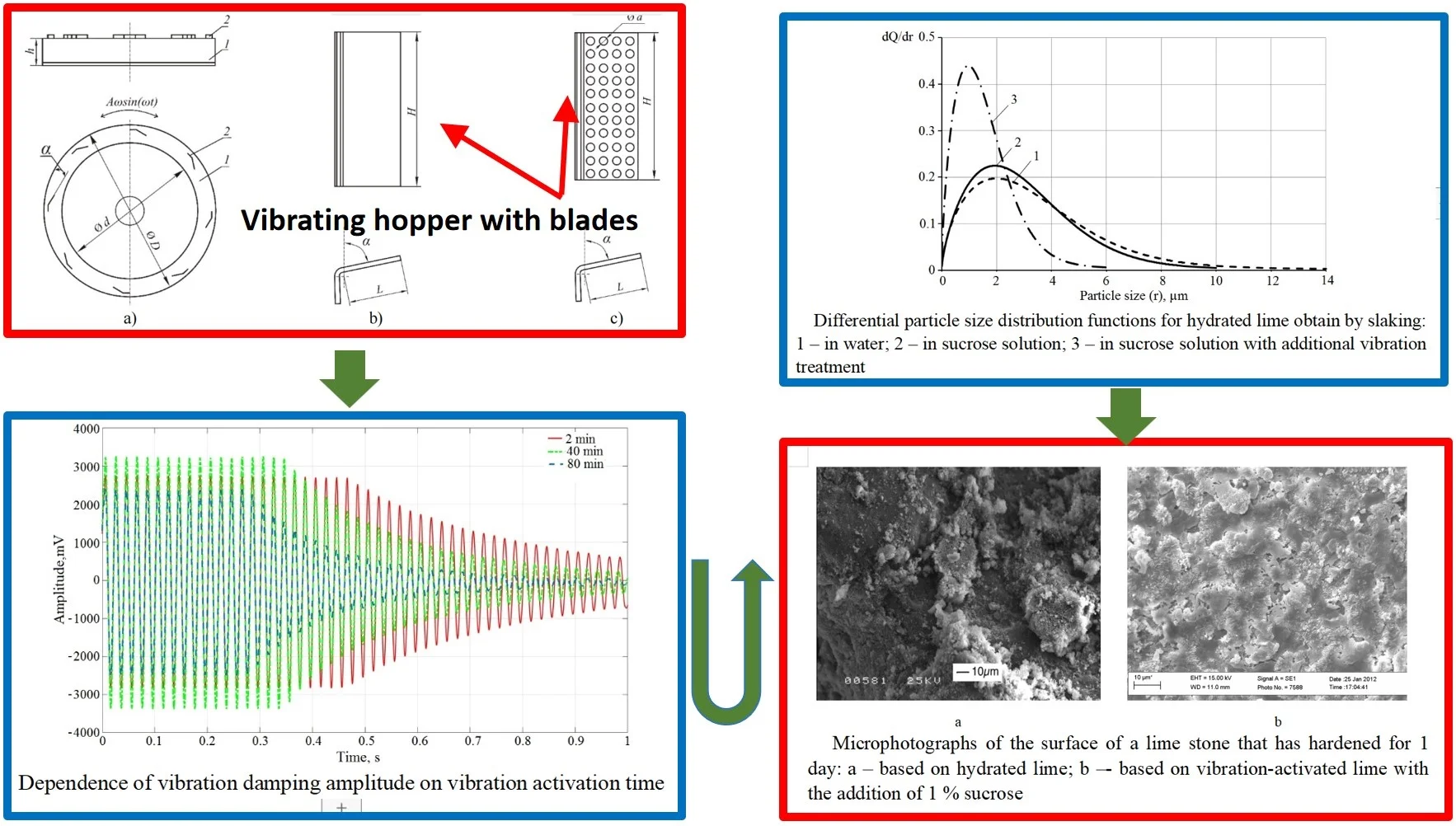
Highlights
- The design of a unit for the vibration activation of hydrated lime has been developed, which operates in a resonant mode.
- Vibratory processing technology reduces lime particles to nanoscale.
- It was found that vibro-activated lime has a high ability to carbonize, forming dense layers of calcite on the surface.
1. Introduction
At the present stage of the development of technology of binding materials, a new type of lime – nanolime – has been obtained. Nanolime is calcium hydroxide with microcrystals smaller than 150 nm. There are two approaches in nanomaterials production technologies [1, 2]. These approaches are commonly referred to as “top-down” and “bottom-up” nanotechnology. “Bottom-up” nanotechnology is a method for obtaining nanostructured materials in which nanoparticles are formed from atoms and molecules. This involves the enlargement of the initial elements of the structure to nanosized particles. This process mainly occurs by self-assembly or catalytic chemical reactions. In the technologies of nanolime production, this method is carried out through various chemical reactions, in which highly dispersed calcium hydroxide and other by-products are formed [4], or by carrying out CaO hydration in a special environment [5], or by adding certain lime quenching catalysts [6].
“Top-down” nanotechnology is a technology for producing nanostructured materials in which nanometer-sized particles are achieved by grinding large particles, powders, or grains of solid matter. This method is realized by grinding in ball planetary mills [7] or by using highly efficient vibration processing methods [8]. In addition to chemical methods for the production of Ca(OH)2 nanoparticles: a “bottom-up” method, a “top-down” technique has been proposed [9].
Thus, the analysis of the literature shows that most researchers for obtaining nanolime suggest using the technology “bottom-up” when nanoparticles of Ca(OH)2 are formed as a result of exchange reactions between soluble calcium salts and precipitant. The “top-down” technology, particularly the use of various methods of modification of the lime quenching process, is promising.
2. Test overview
For the research, hydrated lime powder produced by Lhoist trademark (Poland) was used. The content of the main oxides in hydrated lime, % wt: CaO – 97.2; MgO – 0.7; CO2 – 1.4; SO3 – 0.4. Free water content is 1.3 %. Vibration activation parameters: the frequency of harmonic circular oscillations of the hopper was 50 Hz, oscillation amplitude was 7 mm. Characteristics of the blades in the vibrating hopper: solid non-perforated vibrating blades fixed at an angle of 86° to the direction of oscillation. The optimal duration of hydrated lime mechanical treatment was 60 minutes.
The sedimentation analysis method was used to determine the degree of dispersion and particle size distribution of hydrated lime suspensions. The purpose of the method is to determine the sedimentation rate of particles of the dispersed phase of suspensions.
The structure and morphology of portlandite crystals were also studied using the scanning electron microscope JSM-6010PLUS/LA InTouchScope.
To optimize the process of vibration activation of lime dough, the vibration method was applied using MathLab software to recalculate the logarithmic decrement of the attenuation [10]. It should be noted that the logarithmic decrement of the attenuation is a reliable indicator of the viscosity change in the hydrated lime-water system over a wide range of measurements.
The investigated lime dough was obtained by mixing powdered lime with water to achieve a system moisture content of 48 %. The finished mixture was subjected to activation in the hopper of the vibration activator.
Structurally (Fig. 1(a)), the vibration activator consists of a torus-shaped hopper 1, with blades 2 fixed inside the torus cavity. The hopper performs harmonic angular oscillations due to the spring suspension (torsion) and electromagnetic drive.
Fig. 1The structural diagram of the vibration activator
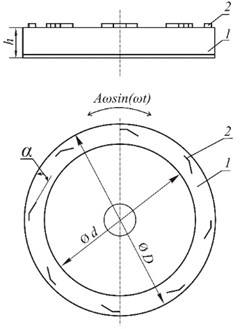
a)
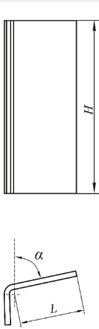
b)
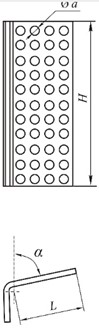
c)
The outer diameter of the torus bowl is 500 mm, the inner diameter d is 400 mm, the width of the circular channel is 50 mm, and the height is 100 mm. Since the tangential (circular) amplitude of angular vibrations is proportional to the hopper radius, it is a rational working body for intensive vibration activation of mixtures.
The maximum amplitude of oscillations at the edge of the hopper loaded with a low-viscosity working mixture is 7 mm. An increase in the viscosity of the mixture leads to a decrease in the amplitude of oscillations. The oscillation frequency is a constant value equal to the frequency of the alternating current of the power grid and is 50 Hz.
Measuring the increase in the logarithmic decrement of the attenuation in the time interval of vibration activation of 30-60 minutes, it was found that the optimal machining time is 60 minutes.
3. Analysis of test results
3.1. Development of a method for controlling the viscosity of lime dough
Mechanical dispersion of calcium hydroxide was carried out in a special vibrating hopper. During the research, it was found that with an increase in the duration of vibration activation, the consistency of the lime dough changes from a viscous-fluid state to the formation of a solid plastic mass. To quantitatively describe the entire process of vibration activation of hydrated lime and to identify the characteristic patterns of dispersion, a new method for measuring and controlling changes in the consistency of lime dough during vibration treatment was developed.
In this regard, the vibration method of determining viscosity was used to study the process of lime dispersion. This method involves the creation of a complex electromechanical oscillatory system. The amplitude of oscillations in time is measured by a special sensor - accelerometer ANS 014-03. The range of measured accelerations is from 0.5 to 300 m/s2. The operating frequency range is from 1 to 125 Hz.
Studies have shown that the vibration method of determining viscosity gives reliable results and can be used to measure the nature of the dependence of the amplitude of the attenuation of the vibration unit during the processing of lime dough (Fig. 2).
Fig. 2Dependence of vibration damping amplitude on vibration activation time
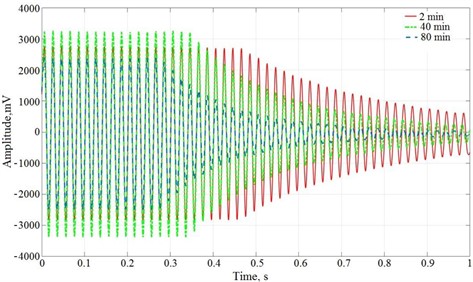
3.2. Production of highly dispersed lime
Modified high-activity hydrated lime was obtained by the interaction of CaO with water in the presence of sucrose. The rate of change of the lime temperature with the hydration time is shown in Fig. 3. The process of interaction of the calcium oxide with water without the addition of sucrose Fig. 3 (a) begins immediately after mixing the starting components and then proceeds autocatalytically.
The process of obtaining Ca(OH)2 in the presence of sucrose Fig. 3 (b) is characterized by the presence of an induction period that lasts up to the sixtieth sixty minutes from the beginning of the interaction. The difference in the kinetic curve of the process of CaO hydration in the presence of sucrose Fig. 3 (b) and without it Fig. 3 (a) is due to the slowing effect of this organic additive, the mechanism of action of which is described above. As a result of the interaction of CaO with water in the presence of sucrose, a modified hydrated lime is obtained, the main advantage of which over others is the increased reactivity due to the smaller size of Ca(OH)2 grains.
Immediately after the quenching process, the lime dough was loaded into a vibrating machine with a toroidal chamber. The chamber oscillated around the axis with a frequency of 50 Hz and an amplitude of 5-10 mm. The lime obtained by hydration of CaO in the presence of 1 % sucrose was subjected to the treatment. Fig. 4 shows a graph of the dependence of the sedimentation rate of different samples of Ca(OH)2 with time.
The settling rate of the lime suspension obtained by hydration of CaO in the absence of sucrose is characterized by a sharp decrease in its value over time. Instead, the lime obtained in the presence of sucrose settles much more slowly, which indicates the positive effect of this additive.
Fig. 3Rate of temperature change with time of CaO hydration for lime
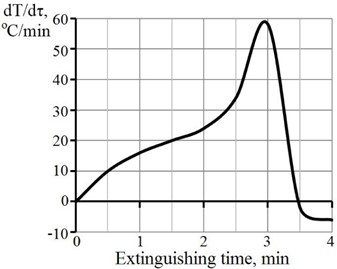
a) Without sucrose
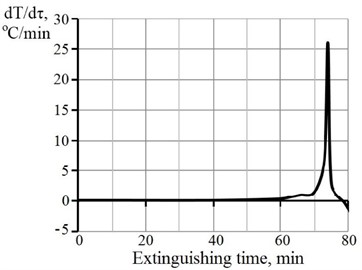
b) With 1 % sucrose
Fig. 4Influence of the method of hydrated lime production on the settling rate of the slurry obtained by slaking: 1 – in water; 2 – in sucrose solution; 3 – in sucrose solution with additional vibration treatment
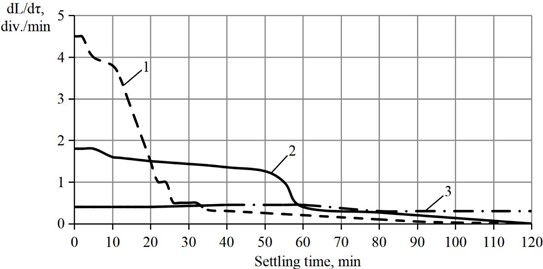
3.3. Physical properties of finely dispersed activated lime
Fig. 5 shows the differential distribution functions of the studied lime samples. The most probable particle radius for lime processed in a vibratory installation is 0.967 μm, while for lime obtained in the presence of sucrose and without it, respectively, it is 1.947 and 1.994 μm. The analysis of the data obtained makes it possible to conclude that the use of sucrose during the hydration of CaO provides lime with a dispersion slightly higher than lime slaked in the absence of sucrose.
Fig. 5Differential particle size distribution functions for hydrated lime obtained by slaking: 1 – in water; 2 – in sucrose solution; 3 – in sucrose solution with additional vibration treatment
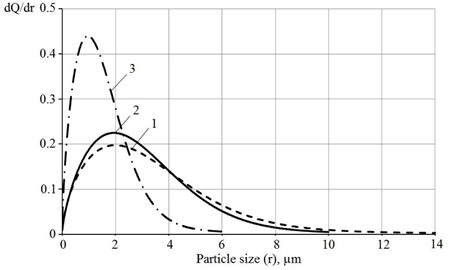
Additional processing of lime in a vibrating unit reduces the particle size by 2.0-2.5 times. It is worth noting that lime obtained by slaking CaO in water is polydisperse, consisting of particles of different sizes. Vibrationally activated lime is characterized by almost monodisperse particles.
3.4. Effect of lime type on carbonation rate
The carbonization process of lime is accompanied by an increase in the mass of the sample since the molecular weight of CaCO3 is about 35 % higher than Ca(OH)2. This makes it possible to study the process of interaction between lime and air CO2 in a gravimetric way.
Fig. 6 shows the dependence of the degree of carbonization with time. The sample based on highly dispersed lime, having reached a certain level of carbonization, practically does not gain weight at all starting from the 20th day of curing, unlike sample No. 1.
Fig. 6Change in the degree of carbonization over time of lime obtained by quenching: 1 – in a sucrose solution followed by vibration treatment; 2 – in water
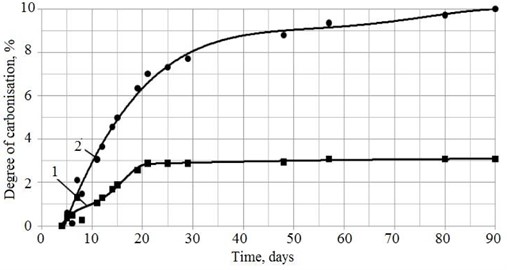
Fig. 7 shows microphotographs of the surface of a lime stone that hardened for 1 day for samples based on highly dispersed and non-ground lime. The surface of the stone made of ordinary lime is formed by compacted Ca(OH)2 crystals Fig. 7 (a). Single calcite crystals in the form of leaf-like formations with a size of 1-2 μm can also be observed. On the surface of the vibro-activated lime stone Fig. 7 (b), a continuous coating of irregularly shaped lamellar CaCO3particles 10-15 μm in size were found. Moreover, in the places of contact between them, the formation of a large number of calcite crystallites in the form of elongated leaf-like forms is observed. Their mutual germination strengthens the surface layer and makes it shiny. The high carbonization rate of activated lime and the ability to form thin-layer durable coatings can be the basis for producing high-quality and environmentally friendly lime paints.
Fig. 7Microphotographs of the surface of a lime stone that has hardened for 1 day
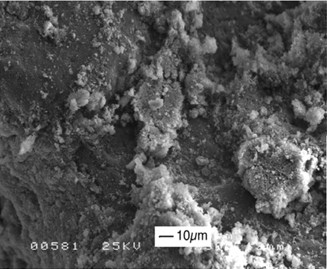
а) Based on hydrated lime
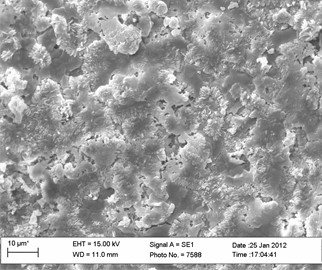
b) Based on vibration-activated lime with the addition of 1 % sucrose
4. Conclusions
A technology for the production of highly active hydrated lime has been developed using the addition of sucrose during the interaction of CaO with water and subsequent processing of the resulting lime dough in a resonant-type vibrating activator. Studies have shown that with such a complex treatment of calcium oxide, the particle size of Ca(OH)2 decreases by 2-2.5 times, while the average size of microcrystals is within 0.967 μm.
Vibro-activated lime is characterized by a high rate of carbonization in surface thin-layer coatings with the formation of a dense layer of lamellar calcite crystals with sizes up to 10-15 μm. At the same time, a dense layer up to 50 μm thick is formed on the surface of the coating.
An efficient and cheap technology for producing highly active hydrated lime using vibromechanical treatment of lime suspensions has been developed. The obtained results allow us to predict the chemical properties of activated lime, which can be used to produce new types of binders based on it.
References
-
A. M. Abdalla et al., “Nanomaterials for solid oxide fuel cells: A review,” Renewable and Sustainable Energy Reviews, Vol. 82, No. 82, pp. 353–368, Feb. 2018, https://doi.org/10.1016/j.rser.2017.09.046
-
F. Laborda et al., “Detection, characterization and quantification of inorganic engineered nanomaterials: A review of techniques and methodological approaches for the analysis of complex samples,” Analytica Chimica Acta, Vol. 904, pp. 10–32, Jan. 2016, https://doi.org/10.1016/j.aca.2015.11.008
-
A. Samanta, D. K. Chanda, P. S. Das, J. Ghosh, A. K. Mukhopadhyay, and A. Dey, “Synthesis of nano calcium hydroxide in aqueous medium,” Journal of the American Ceramic Society, Vol. 99, No. 3, pp. 787–795, Nov. 2015, https://doi.org/10.1111/jace.14023
-
S. Martínez-Ramírez, L. R. Higueruela, I. Cascales, M. Martín-Garrido, and M. T. Blanco-Varela, “New approach to nanolime synthesis at ambient temperature,” SN Applied Sciences, Vol. 1, p. 105, Dec. 2018, https://doi.org/10.1007/s42452-018-0122-8
-
C. Rodriguez-Navarro, I. Vettori, and E. Ruiz-Agudo, “Kinetics and mechanism of calcium hydroxide conversion into calcium alkoxides: implications in heritage conservation using nanolimes,” Langmuir, Vol. 32, No. 20, pp. 5183–5194, May 2016, https://doi.org/10.1021/acs.langmuir.6b01065
-
C. Rodriguez-Navarro, A. Suzuki, and E. Ruiz-Agudo, “Alcohol dispersions of calcium hydroxide nanoparticles for stone conservation,” Langmuir, Vol. 29, No. 36, pp. 11457–11470, Sep. 2013, https://doi.org/10.1021/la4017728
-
G. Borsoi et al., “Effect of solvent on nanolime transport within limestone: How to improve in-depth deposition,” Colloids and Surfaces A: Physicochemical and Engineering Aspects, Vol. 497, pp. 171–181, May 2016, https://doi.org/10.1016/j.colsurfa.2016.03.007
-
G. Taglieri, V. Daniele, G. Del Re, and R. Volpe, “A new and original method to produce Ca(OH)2 nanoparticles by using an anion exchange resin,” Advances in Nanoparticles, Vol. 4, No. 2, pp. 17–24, Jan. 2015, https://doi.org/10.4236/anp.2015.42003
-
P. Eswaramoorthi, P. Sachin Prabhu, V. Senthil Kumar, P. Prabu, and S. Lavanya, “Influence of nano size silica and lime particles on the behaviour of soil,” International Journal of Civil Engineering and Technology, Vol. 8, No. 9, pp. 353–360, 2017.
-
A. Zahraj, Z. Borovets, I. Lutsyuk, and Y. Novitskyj, “Criteria for studying the dispersion process of the hydrated lime-water system,” Chemistry, Technology of Substances and Their Application, Vol. 3, No. 2, pp. 23–27, 2020.
About this article
The authors have not disclosed any funding.
The datasets generated during and/or analyzed during the current study are available from the corresponding author on reasonable request.
The authors declare that they have no conflict of interest.