Abstract
As the world population increases, energy consumption extensively increases in every field. Energy is a need in several applications, and depending on its importance, its production should be renewable and clean. In order to meet energy requirements sustainably nowadays various alternative energy resources and improvements are recommended in each sector. One of the environmental steps taken in the aviation industry is the improvement of the propulsion systems and the resources used. For this purpose, the use of electrical energy, a more sustainable option than the energy obtained from fossil fuels, is suggested. In order for electrical energy to be used efficiently, it must be stored. This article reviews energy storage technologies used in aviation, specifically for micro/mini Unmanned Aerial Vehicles (UAVs). Combinational energy storage technologies in hybrid propulsion system architectures and their individual usage in all-electric propulsion system architectures are examined. New-generation propulsion technologies are also evaluated and classified in detail.
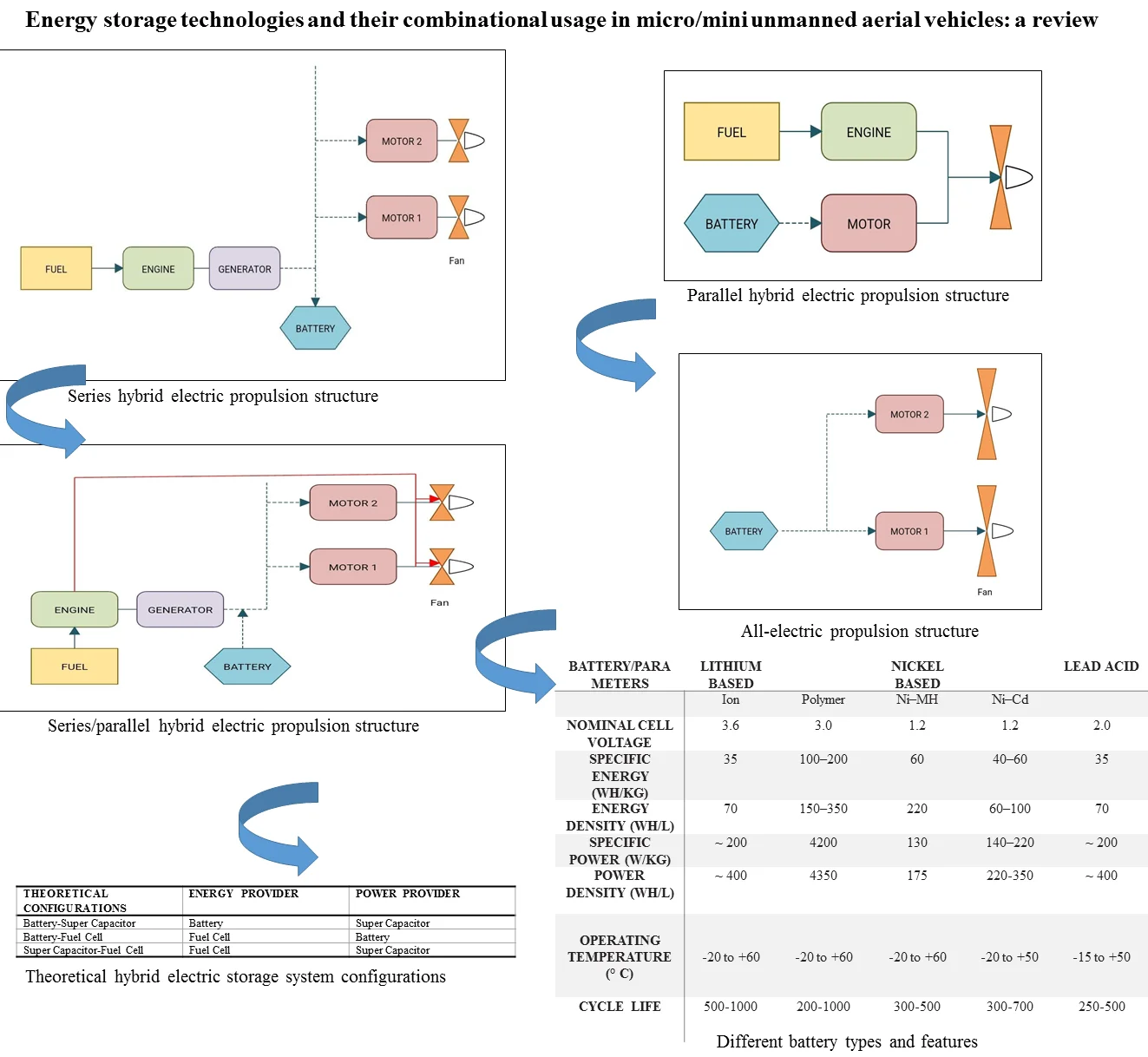
Highlights
- Emphasis in this paper is to examine energy storage technologies used in aviation specifically for micro/mini Unmanned Aerial Vehicles (UAVs).
- Explanation of each energy storage technology in terms of advantages, disadvantages.
- Explanation of each novel propulsion system structure in terms of advantages, disadvantages.
- Evaluation of combinational usage of energy storage technologies in hybrid propulsion system architectures and also their individual usage in all electric propulsion system architecture in terms of both their properties and connection types.
1. Introduction
Due to the world’s population growth, industrialization, and urbanization, the energy requirement is increasing daily. The use of energy can be seen in almost every field. It is also expected that the energy being used that much would be environmentally friendly, cheap, and reliable [1]. One of the most significant environmental problems of recent years is global warming. The negative consequences of global warming affect the lives of all living things. The adverse effects of fossil fuels on the environment caused an increase in the orientation toward renewable energy sources [2]. Although the exact date cannot be given, it is expected that fossil fuels will run out within this century. For this reason, limiting dependence on fossil fuels has become a necessity [3].
As an environmentalist approach, the aviation industry has set low noise and low emission targets. For this reason, the search for alternative systems continues to replace the traditional propulsion systems that harm the environment [4]. Negative results such as increasing CO2 emissions, the effects of emissions on human health, and the increasing costs of fossil fuels have also led to the search for alternative fuels [5]. In conventional propulsion systems, energy is obtained by breaking liquid fuels (rarely gaseous fuels are also used), resulting in gaseous emissions [6]. The International Air Transport Association has committed to reducing carbon emissions by 50 % by 2050 compared to 2005 [7]. At the same time, according to data published by the International Air Transport Association, the number of airline passengers increased from 1.4 billion in 1998 to approximately 4.1 billion in 2017 [8]. The global energy consumption of the transportation sector is about one-third of the total energy consumption in the world [9]. Air transport also has a high share in this area. According to 2011 data, civil air transport accounts for 2 % of human-induced CO2 emissions [10]. As a result of the COVID-19 pandemic that occurred in 2020, quarantines have been implemented around the world, and transportation activities have decreased significantly. As a result, it is observed that environmental quality increased in a short time [11]. There are many studies investigating the effects of air pollution on human health. According to a study conducted in 2002, it is determined that 40,000 deaths per year for Austria, France and Switzerland combined are due to air pollution, and about half of this is due to air pollution, especially from traffic [12]. Considering all these, electric propulsion systems, which are a sustainable option for the aviation industry, come to the fore as an alternative to traditional propulsion systems.
This paper evaluates energy storage technologies and their combinational usage in micro/mini unmanned aerial vehicles. The organization of the paper is as follows: (i) hybrid electric propulsion systems are defined, (ii) the importance of energy storage and energy storage components are examined, (iii) the combinational usage of energy storage components is explained, and (iv) finally, the paper is concluded by summarizing the paper and mentioning next future work.
2. Theory
2.1. Hybrıd electric propulsion systems
Electric drive systems have a quiet operation, low thermal signature, and low emissions. however, due to the low specific energy of the battery technology commonly used in existing systems, their usage times are short. Hybrid electric propulsion systems can combine the advantages of multiple systems by reducing fuel consumption, aircraft noise, and thermal signature [13-17].
More than one power source is used together in the hybrid electric drive system. The first source is an electric motor, while the other source is usually a conventional internal combustion engine (can also be a fuel cell, battery, or supercapacitor). In systems where electric motors and internal combustion engine are used together, the internal combustion engine is added to increase the range [16]. Aircraft powered by internal combustion engines can fly for long periods due to their high energy density. The range of a vehicle driven by a hybrid electric drive system is shorter than a vehicle driven solely by an internal combustion engine, but its efficiency is higher [15]. The combined thrust of the two power sources allows them to be designed in a smaller size [18].
Furthermore, the advantages of electric propulsion systems and conventional combustion engines can be combined in a single system. Hybrid electric propulsion systems are energy efficient and can be operated over long distances. An energy-efficient aircraft also saves costs and contributes to the conservation of resources. All these advantages also increase the system’s life [19-20].
2.1.1. Series hybrid electric propulsion system
In this architecture, the mechanical power produced by the internal combustion engine is converted into electrical energy with a generator. This power can drive the electric motor or be used to charge the battery. The internal combustion engine is not used directly to generate thrust, so it operates efficiently at its optimum operating point regardless of driving conditions [21]. It is the electric motor that provides the thrust. Fig. 1 shows the series hybrid electric propulsion structure. The dashed lines in the figure show the electrical connection paths.
Control of the system with serial architecture is simple and easy. This system is also compatible with multiple motor and fan structures. However, in serial architecture, a total of 3 drive components are needed together with the generator, therefore the system is heavy. Due to its weight, serial architecture is not preferred in aviation [13]. Also, since the electric motor provides all the thrust, it must be sized accordingly, creating aviation problems. There is a lot of energy loss in the serial architecture and additional components cause an increase in cost and mass. The serial hybrid electric drive architecture is suitable for short trips in aviation [23].
Fig. 1Series hybrid electric propulsion structure [22]
![Series hybrid electric propulsion structure [22]](https://static-01.extrica.com/articles/24104/24104-img1.jpg)
2.1.2. Parallel hybrid electric propulsion system
The electric motor and the combustion engine are connected to the same shaft in a parallel architecture. They can provide the thrust together or separately [18, 21]. In this architecture, two drive components are needed; the electric motor also acts as a generator [23]. Fig. 2 illustrates the parallel hybrid electric propulsion structure.
Fig. 2Parallel hybrid electric propulsion structure [22]
![Parallel hybrid electric propulsion structure [22]](https://static-01.extrica.com/articles/24104/24104-img2.jpg)
The control strategy of the parallel hybrid electric propulsion system is complex, so it is essential to ensure energy management. In addition, the system cannot operate silently [24]. In addition, the parallel hybrid system has a high specific power and specific energy. Although the specific power is increased in the series hybrid architecture, no systemic changes can be made as long as the battery power remains the same [25]. The parallel architecture consists of fewer drive components, which makes it lighter [26]. For this reason, the parallel structure in aircraft comes to the fore.
2.1.3. Series/parallel hybrid electric propulsion system
In this system, the combustion engine can provide the thrust directly. In addition, the battery or the generator driven by the combustion engine powers the electric motor, and this electric motor can also provide the thrust [22]. Fig. 3 shows the series/parallel hybrid electric propulsion system structure.
This architecture may have some advantages as well as disadvantages to serial and parallel architectures separately. There has been an increase in cost and mass due to the number of drive components. As the number of potential power flow paths increases, so does the power management complexity. The serial structure has the least number of potential power paths. The maximum potential power path is in a series/parallel structure. In other words, it can be sorted as Serial < Parallel < Serial/Parallel according to power management complexity. Serial/parallel structure is preferred in land vehicles because weight is not a problem, but weight is a significant disadvantage for aircraft [26].
Fig. 3Series/parallel hybrid electric propulsion structure [22]
![Series/parallel hybrid electric propulsion structure [22]](https://static-01.extrica.com/articles/24104/24104-img3.jpg)
2.2. All electric propulsion system
In hybrid architectures, batteries and gas turbine engines provide thrust at different times, and gas turbine engines are also used to charge the battery. In all-electric systems, the only source of propulsion in the aircraft is the batteries. Fig. 4 shows the construction of an all-electric propulsion system.
Fig. 4All-electric propulsion structure [22]
![All-electric propulsion structure [22]](https://static-01.extrica.com/articles/24104/24104-img4.jpg)
3. Importance of energy storage
Renewable energy has been used throughout human history. Solar energy was used for basic needs such as heating and growing food. Later, fossil fuels started to be used and replaced with renewable energy. The cost of solar energy in the 1900s is estimated to be ten times higher than that of fossil fuels. However, indirect effects such as environmental costs must also be considered for full cost calculation [27]. Today, the problems related to fossil fuels provide the orientation to renewable energy again. Power output is not constant in renewable energy sources. For example, solar energy is only possible during the daytime and on sunny days. This disadvantage can only be overcome by storing energy [28]. Energy storage provides a constant power output by reducing power fluctuations [29]. Energy can be stored in different ways and used when needed [30].
Different energy storage technologies have been developed to store energy. Each technology has different properties that are suitable for different applications. Energy storage systems are basically divided into two groups according to systems where electricity is stored directly or by converting it to another energy type. Examples of direct storage systems are supercapacitors stored in the electric field and superconducting magnetic energy storage systems (SMES) stored in the magnetic field. In indirect storage, electrical energy is first held by converting it to a different energy type and is used by converting it back to electrical energy when desired. Examples of this are batteries that store electrical energy in the form of chemical energy, flywheels that store it in the form of kinetic energy and pumped water plants that store it in the form of potential energy [31]. There are also many different methods and technologies for storing energy. The energy storage concept is very comprehensive, and its application area is also wide. In aviation, flywheels, superconducting magnetic energy storage systems (SMES), batteries, fuel cells, and supercapacitors have been used for energy storage. Looking at the features of these technologies, it will be more understandable which ones can be used in micro/mini UAVs.
3.1. Energy storage with flywheel
Flywheels are mechanical batteries. Flywheels have advantages such as long life, high efficiency, high power density, not being affected by temperature, and zero emissions. On the other hand, flywheels are mechanical systems and can break or explode. This means they carry risks. Besides the risk of explosion, flywheels need frequent maintenance. Additionally, due to mechanical movement, friction losses occur in the energy of the flywheels. Flywheels were used to drive the hybrid electric bus Gyrobus in Sweden in the 1950s. Thanks to the flywheel, some of the energy the bus lost during braking was recovered. However, in this bus, the volume occupied by the flywheel was very large, which narrowed the available space. From this perspective, it can be said that the energy that needs to be stored for flywheels should be proportional to the size of the flywheel. Large size also means large weight. Although it is possible to use a flywheel instead of a battery or with a battery in aviation, it is not a preferred system for small UAVs. The flywheel was also used in the Formula 1 championship in the 2009 season. The system in the Formula 1 vehicle is called KERS (Kinetic Energy Recovery System) and it is known that the rotor weight of the flywheel in this vehicle is 5 kilograms. Since the flywheel is a rotating mass, it needs to be balanced and balance errors cause vibration. To prevent this, additional weights are placed on the flywheel. This again shows that flywheels are not a good option for UAVs [31-32].
3.2. Energy storage with SMES (superconductor magnetic energy storage) system
In this system, there is a coil wrapped with superconducting wires, and electrical energy is stored in the magnetic field in this coil. The system efficiency is high, and the response time is short (in the order of milliseconds). The stored energy can be given back to the system at any time [30]. The cooling system used for SMES can be quite complex and costly [33]. In addition, SMES are more expensive than other storage technologies and require a larger working volume [31]. They are not preferred for small-sized UAVs.
There are different energy storage technologies used or in use in aviation. In this study, energy storage technologies used in small-sized UAVs are examined in detail. These technologies are batteries, fuel cells, and supercapacitors. Batteries and fuel cells store energy chemically, while supercapacitors store it physically [34].
3.3. Energy storage with batteries
Batteries are the most widely used energy storage technology in electric aircraft. Batteries are systems that store chemical energy and convert it into electrical energy when necessary [35]. A typical battery; consists of two electrodes, an anode and cathode, an electrolyte, and a separator between them [36]. Fig. 5 shows the battery structure. While the anode is corroded during electrolysis, an electric current occurs at the cathode due to ionic exchange. The electrical energy formed from this reaction is used in various tools [37].
The electrical model of batteries can be expressed in several different circuits. The difference between them consists in emphasizing the importance of each circuit element. The simplest of these models is the internal resistance model. The Fig. 6 shows the internal resistance model of the battery. The internal resistance model describes the relationship between voltage drop and operating current.
Fig. 5Chargeable cell/battery diagram [28]
![Chargeable cell/battery diagram [28]](https://static-01.extrica.com/articles/24104/24104-img5.jpg)
Fig. 6Battery electrical model [38]
![Battery electrical model [38]](https://static-01.extrica.com/articles/24104/24104-img6.jpg)
In this model, the required power is calculated by multiplying the terminal voltage (Vt) and the battery current (I). Power equation:
Terminal voltage (Vt) is expressed by equation. Terminal voltage equation:
where Voc is the voltage value calculated based on the SOC value of the battery. I stands for battery current and Re stands for internal resistance [38]. These are the basic elements of the battery. The electrical circuit can be revised according to the feature. desired to be emphasized.
Batteries are divided into three classes according to the usage situation. The first of these are the batteries, which are called primary batteries and cannot be recharged once used. On the other hand, secondary batteries are rechargeable batteries that can be used repeatedly. Secondary batteries are also called accumulators [37]. The third class consists of special batteries designed to fulfill a specific purpose [35]. Many types of batteries vary according to the material used in the battery. The choice of material depends on the expected performance and cost of the battery. In addition to the electrode material, batteries are also available according to liquid (aqueous and organic) and solid (polymer and ceramic) electrolyte types [39]. The types of secondary batteries used in UAVs are explained below.
3.3.1. Secondary battery types
The main secondary batteries are named according to the electrode material, and their properties are given below.
Lead/Acid (Pb/A): It is the oldest type of battery used in electric vehicles [34, 40]. A lead acid battery has Pb at its anode and PbO2 at its cathode. The electrolyte material is sulfuric acid (H2SO4). While discharging, the lead of the negative electrodes and the lead dioxide of the positive electrode react with sulfuric acid. As a result of the reaction, lead sulfate is formed and the electrolyte loses its dissolved sulfuric acid and turns into water. Energy is released as the chemical reaction ends, and energy is added to reverse the process. General reaction:
Pb + PbO2 + 2H2SO4 ←→ 2PbSO4 + 2H2O.
Lead acid batteries have advantages such as low cost, long life cycle, and low maintenance, but they have disadvantages such as low specific energy and not being environmentally friendly. In addition, in the case of overcharging, irreversible polarization occurs in the electrodes [34, 37, 40]. Low specific energy shortens the range of the UAV. In addition, sustainable technologies are becoming increasingly important and are important in battery selection. For these reasons, Pb/A batteries are not a good option for UAVs.
Nickel Metal Hydride: Nickel-iron (Ni-Fe), nickel-zinc (Ni-Zn), nickel cadmium (Ni-Cd) and nickel metal hybrid (Ni-MH) are nickel-based batteries. Ni-Zn and Ni-Fe batteries have a short lifespan and low specific power. Therefore, they are not very suitable for electric vehicles. The properties of Ni-Cd and Ni-MH batteries are similar. Although Ni-Cd has been used for a long time, Ni-MH has replaced Ni-Cd due to its higher energy storage capacity and lighter weight. Since cadmium is not used in Ni-MH batteries, it is relatively environmentally friendly. It is suitable for use in electric vehicles. Ni-MH batteries have high specific power and are used in some electric vehicles such as the Honda Civic Hybrid. The lifespan of this battery can reach 3000 cycles. Ni-MH batteries have a long lifespan, these batteries can last as long as the life of the vehicle [34]. Shortly after the development of Ni-MH batteries, newer battery technologies were introduced and these batteries replaced the Ni-MH battery [41].
Ni-MH batteries contain metal hydride at the anode and Ni(OH)2 at the cathode. A potassium solution is used as the electrolyte. General reaction: MH + NiOOH ←→ M+ Ni(OH)2.
Lithium/Ion (Li-Ion): Li-Ion batteries have different types according to the positive and negative electrode material or the electrolyte used. Commercially available batteries usually use carbon with lithium as the anode. The most commonly used batteries use lithium carbon as the anode, lithium cobalt oxide (LiCoO), lithium manganese dioxide (LiMn2O4) or lithium iron phosphate (LiFePO4) as the cathode. The batteries used in mobile phones and laptop computers are lithium cobalt oxide batteries, and this battery is not a preferred type for electric vehicles. More advanced lithium batteries used for military applications are lithium sulfur dioxide (LiSO2) or lithium thionyl chloride (Li-SOCl2). Lithium-ion batteries generally use a liquid, anhydrous organic electrolyte, but solid electrolytes are also used for dry lithium-ion batteries. The most typical electrolyte solutes are lithium salts such as LiClO4, LiBr, LiCF3SO3 and LiAlCl [34].
The way Li-Ion batteries work is based on the transfer of lithium ions. During charging, lithium ions exit (de-intercalate) the lithium metal oxide cathode and enter the graphite-based anode. During discharge, the opposite happens. The lithium atom loses electrons during charging, forming the Li+ ion. There is a risk of explosion due to the volume increase of the electrodes during charge/discharge. The task of the electrolyte in the Li-Ion battery is to provide the transmission of ions. The electrolyte does not react [34, 37].
While Li-Ion batteries were in the research phase, ZEBRA batteries and Ni-MH batteries were used in electric vehicles. At the beginning of the 2000s, the most advanced technology used in hybrid and fully electric vehicles were Ni-MH batteries. Ni-MH batteries had many advantages over Ni-Cd and Pb-Acid batteries used in those years. However, Li-Ion technology began to be widely preferred after Li-Ion batteries were produced. Li-Ion batteries have some advantages over nickel-based batteries. These are the relatively high cell voltage and superior energy density. It also has a 1:4 lower self-discharge rate compared to nickel technology. In addition, Li-Ion batteries are lighter in weight, as lithium metal is the lightest of all metallic materials used in batteries. Li-Ion batteries have the advantages of high cycle life and efficiency. For this reason, it is preferred in electronic devices and electric vehicles. Tesla Roadstar can be given as an example of electric vehicle using Li-Ion batteries. Li-Ion batteries were introduced in 1991 by the Sonny company. Since then, its capacity has increased severalfold and continues to evolve [35, 42]. The high cost of Li-Ion batteries used today and the limitations of insufficient power density for some applications are still unresolved problems. In addition, Li-Ion batteries are less tolerant of abuse than Ni-based batteries. Cycle life is greatly reduced in case of overcharging or discharging. Another disadvantage of the Li-Ion battery is the problem of overheating and explosion. That’s why a battery management system is needed. From a cell perspective, Li-Ion batteries have a 20 % higher energy capacity than Ni-MH batteries. On the whole, it can be said that the battery management system of the Ni-MH battery is simpler and lighter than that of the Li-Ion battery because the battery management system required for the Li-Ion battery is quite complex [43].
Another promising technology for electric vehicles is lithium-polymer batteries. The only difference from the Li-Ion battery is that a polymer gel is used as the electrolyte. It is lighter and thinner than a Li-Ion battery. However, its service life is short, and its specific power is low. If lightness is the most important criterion for the application to be used, this battery type can be preferred [34].
Metal/Air: When metal-air batteries run out, their electrodes are replaced and they become usable again. For this reason, they are among the secondary battery types, but they cannot be recharged like the others. Magnesium/air, lithium/air, zinc/air, etc. There are varieties. Zinc/air is preferred in applications requiring long life due to its high energy density. Metal/air batteries have only one reagent, the other component being oxygen in the air. Lightness is at the forefront of this battery type. One of the places where it is used is hearing aids. However, electric vehicles are not among their usage areas [34].
Sodium/Nickel Chloride (NaNiCl2) (ZEBRA): The name ZEBRA comes from the Zero Emission Battery Research Association. The Zebra battery uses solid nickel chloride as the positive electrode and molten sodium as the negative electrode. The central positive electrode is impregnated in a liquid sodium-aluminum chloride electrolyte surrounded by a ceramic electrolyte. During discharge, nickel and sodium chloride are converted to salt and nickel [34]. General reaction: 2Na + NiCl2 ←→ Ni + 2NaCl.
Zebra battery has a high specific energy, and their life cycle is more than ten years. However, it works between 270 °C and 350 °C. Extra energy is required to keep the battery at this temperature. When the battery cools down, it takes one day to warm up again. Therefore, its usage area is a limited battery.
Although widely used, batteries also have many disadvantages and are still an emerging technology. Many criteria are considered when choosing the battery type to use in electric vehicles. The life span of the battery is the main selection criterion. In electric vehicles, the life of the battery should be as long as the life of the vehicle; otherwise, the battery needs to be replaced, which means extra cost [34]. Short-lived batteries are not preferred because they require both cost and maintenance frequency. Even the most advanced battery in current technology has some disadvantages. Batteries chemically store electrical energy, resulting in a physical change between the charged and discharged states. For this reason, they both charge slowly and have a limited lifespan [44-45]. However, batteries are the most commonly preferred technology in electric vehicles, and the choice of battery type to be used is of great importance. The type of battery to be used for the aircraft is selected according to the usage area of the aircraft [46]. Table 1 contains commonly used secondary battery types and their characteristics.
Table 1Different battery types and features [47-48]
Battery/parameters | Lithium based | Nickel based | Lead acid | ||
Ion | Polymer | Ni-MH | Ni-Cd | ||
Nominal cell voltage | 3.6 | 3.0 | 1.2 | 1.2 | 2.0 |
Specific energy (Wh/kg) | 35 | 100–200 | 60 | 40-60 | 35 |
Energy Density (Wh/l) | 70 | 150–350 | 220 | 60-100 | 70 |
Specific power (W/kg) | ~ 200 | 4200 | 130 | 140–220 | ~ 200 |
Power density (WH/L) | ~ 400 | 4350 | 175 | 220-350 | ~ 400 |
Operating temperature (°C) | –20 to +60 | –20 to +60 | –20 to +60 | –20 to +50 | –15 to +50 |
cycle life | 500-1000 | 200-1000 | 300-500 | 300-700 | 250-500 |
3.4. Energy storage with super capacitors
They are also known by names such as supercapacitors, electrochemical capacitors, ultracapacitors, and electric double-layer capacitors. These names have been given by different manufacturers of supercapacitors [49]. Supercapacitors are structurally similar to batteries. But unlike batteries, supercapacitors have a separator membrane that separates the two electrodes. In addition, while both electrodes are usually made of the same material in batteries, the electrodes in supercapacitors can be made of the same or different materials [50].
A simple capacitor is formed by placing an insulating material between two metal electrodes. Fig. 7 shows the capacitor structure. On the other hand, Supercapacitors have an electrolyte between two electrodes with a raised surface. Figure 8 shows the supercapacitor structure. The electrodes are connected to each other by a power source and current flows from one electrode to the other. Charge separation naturally occurs at each electrode-electrolyte interface, and energy is stored in this way. The voltage continues even if the power is disconnected. Equal but opposite charges attractions in the electrolyte in solid electrolytes. This is where the term ‘double layer’ comes from [51].
Fig. 7The capacitor structure [52]
![The capacitor structure [52]](https://static-01.extrica.com/articles/24104/24104-img7.jpg)
Fig. 8A supercapacitor with a surface-enhanced electrolyte [52]
![A supercapacitor with a surface-enhanced electrolyte [52]](https://static-01.extrica.com/articles/24104/24104-img8.jpg)
The storage capacity of conventional capacitors is in the micro and mini farad range. In capacitors, energy charges accumulate on the plates, while in supercapacitors, charges accumulate at the electrode-electrolyte interface. The most important factor determining a capacitor’s capacitance is the width of the surface area to which the electrons are attracted. Supercapacitors have a very large surface area, and the capacity of a supercapacitor can be defined in kilofarads, unlike other capacitors [53-54].
Due to its porous structure, the carbon material is very suitable for being an electrode material [54]. In addition, carbon nanotubes, which are allotropes of the element carbon, have high conductivity and good electrochemical stability, but carbon nanotubes exhibit a low capacitance [55]. Activated carbon is a form of graphite with a porous structure. Activating carbon increases the surface area and pore volume [56-57]. Supercapacitors can store more charge than others because activated carbon is used as the electrode material, and activated carbon has a spongy structure. Thus, the maximum area that the loads can hold is provided [52]. Carbon can be activated in different ways. There are many studies on obtaining activated carbon from biomass wastes. Activated carbon could be obtained from various biomass wastes such as sugar cane pulp, corn cob, coconut shell, rice husk [58]. It is easy and relatively inexpensive to obtain in this way [59].
Supercapacitors are devices with high specific power, and electrical energy loading into the device occurs rather quickly compared to the battery [60]. No chemical reaction takes place inside supercapacitors and energy is physically stored. Therefore, the charge-discharge cycle is almost unlimited. In addition, they do not need service during their lifetime [61]. Since they do not contain dangerous and toxic substances, their production and disposal do not have a negative impact on the environment. They can also operate smoothly in a wide temperature range (–40 °C to +85 °C) [30, 62-64].
Their energy densities are relatively low [64-65]. However, this also makes them less hot and they can operate in a wide temperature range. They perform much better than batteries at very low temperatures.
Super capacitors are an emerging, new and promising technology. Using them together with the battery in UAVs improves the battery and increases the system performance.
3.5. Energy storage with fuel cells
Fuel cells are systems that generate electrical energy from chemical energy and use pure hydrogen or oxygen in the air as fuel [66]. As in batteries, energy conversion in fuel cells occurs through redox reactions that take place at the anode and cathode electrodes.
Fuel cells have a higher energy density compared to batteries. With this feature, it provides a longer flight and a longer range. However, the chemical reaction in it causes long response times, as in batteries. This means they cannot rise to an advanced level in terms of power density. Fuel cells can operate in different temperature ranges depending on their type. The operating temperature range for PEM (Proton-exchange membrane fuel cell) fuel cells used in UAVs varies between 80 °C and 1000 °C [67]. It is more advantageous in weight than batteries. A fuel cell is much lighter than a lithium-ion battery with the same energy capacity. In addition, it is suitable for use in covert operations thanks to its lower thermal trace and low noise characteristics [68-69]. Although its use on UAVs is becoming widespread, it has certain limitations.
4. Hybrid use of energy storage technologies
Energy storage technologies can be used together, and their advantages can be combined. What is expected from a hybrid electric system is that it can meet the long-term energy needs while at the same time meeting the sudden power need [70]. The combined uses of energy storage technologies are discussed below.
4.1. Battery-super capacitor
In this combination, the battery provides long range and durability with its high specific energy, while the supercapacitor meets the sudden power need with its high specific power. Batteries and fuel cells cannot meet the power needs of the system in some situations, such as sudden maneuvers. The power used when the vehicle accelerates or slows down shortens the life of the battery. During high power demands, the battery voltage may drop below the minimum limit. Battery-supercapacitor hybridization can be used to protect system voltage from sudden drops. Supercapacitors and batteries can be used together to extend battery life and improve performance in electric vehicles. Since battery-supercapacitor hybridization increases efficiency, it also reduces costs in high-cycle applications. It has also been found that adding a supercapacitor in parallel with the battery increases the energy capacity by 20 % compared to discharging the battery alone [71].
In order to increase the power density in batteries, it is necessary to increase the size of the battery, but this causes additional cost increases and increases the weight. Weight gain is a disadvantage for aircraft. It has also been observed that the battery-super capacitor hybridization has higher specific power than the battery-powered system alone [72-73]. For this reason, it is seen as a rational solution to add an additional super capacitor to the battery instead of increasing the battery size.
4.2. Battery-Fuel Cell
This was one of the first hybrid electric systems proposed. The battery provides high power pulses and offers the required power density in this structure. The fuel cell converts the fuel into electrical energy at a constant rate to provide a high energy density for long-term missions, thus providing high efficiency [74].
Fuel cells are efficient and also have low emissions but require expensive filtration to prevent pollution. It is also heavy. In battery-fuel cell hybridization, the fact that both technologies are separately heavy causes the system to be overloaded, and this creates a disadvantage in aviation applications. Weight is a big problem, especially in UAVs. Additionally, the hydrogen used in fuel cells can only be stored by liquefying it. For this purpose, hydrogen is stored in high-pressure tubes and there is a possibility that these tubes may explode. In addition to the hydrogen storage problem, its availability also poses a disadvantage [4]. Although this hybridization is a system used in UAVs, its disadvantages cannot be ignored.
4.3. Super capacitor-fuel cell
The supercapacitor has high specific power while the fuel cell has high energy density. In this combination, the fuel cell meets long-term power requirements, while the supercapacitor serves high pulse power requirements at short intervals (energy control). However, due to the fuel cell’s undesirable features, such as the risk of explosion, high volume, and most importantly, the need for an additional source for the starting energy, batteries are preferred in addition to the supercapacitor instead of this structure.
In hybrid electric system configurations, the aim is to use one of the technologies as a power provider and one as an energy provider. The task undertaken by each technology in these configurations is briefly summarized in Table 2.
Table 2Theoretical hybrid electric storage system configurations [70]
Theoretical configurations | Energy provider | Power provider |
Battery-super capacitor | Battery | Super capacitor |
Battery-fuel cell | Fuel cell | Battery |
Super capacitor-fuel cell | Fuel cell | Super capacitor |
4.4. Hybrid electric drive system examples and combination technologies
The hybrid use of energy storage devices in electric vehicle technology, especially supercapacitors, is a topic that has come to the fore recently. the fact that it does not have a long historical background also limits the knowledge of the literature on this subject. in particular, most studies on aircraft are limited to theoretical knowledge. However, some experimental studies were also found. Examples of theoretical and experimental studies are as follows; in an article published in Bulgaria in 2010, it aimed to improve the flight time by connecting a supercapacitor in addition to the battery in the propulsion system of the UAV, and the system was designed. in the article, more attention was paid to the design of the energy management system of this structure. No experimental study has been conducted [75]. Xiong et al published a review article on battery-supercapacitor hybridization in 2018. This article examines energy management systems and hybrid propulsion system architectures for hybrid propulsion. as a result of the study, it was concluded that connecting an additional supercapacitor to the battery extends the battery life and reduces the overall cost [76]. in the study conducted by Gong and Verstraete in 2018, fuel cell, battery and supercapacitor were used together in the UAV propulsion system, and flight tests evaluated the performance of the UAV. This study aims to reduce the fuel cell’s load and thus increase its life by using the supercapacitor and the relatively high specific powers of the battery in situations that require sudden maneuvers such as landing and take-off. This system has been tested on a fixed-wing UAV with components connected in parallel. It was concluded that the triple hybrid propulsion system reduces the load of the fuel cell and increases its life [77]. the use of fuel cells in the study increased the weight of the propulsion system, and although this extra weight is not a problem for a fixed-wing UAV, it is undesirable for a micro/mini-class UAV. as a result, although using three technologies together creates a system with very good features by combining the advantages of all three, it is useless for micro/mini UAVs.
5. Conclusions
In this article, it is aimed to emphasize the importance of energy storage technologies of novel propulsion systems specifically for micro/mini UAVs. They have many advantages in terms of the environment. They store the clean energy required for novel propulsion systems. Systems in which these technologies are used together or individually have been examined in terms of both their properties and connection types. By scanning the literature, each energy storage technology and each propulsion system structure were examined in terms of advantages and disadvantages.
Although electric and hybrid electric propulsion technologies provide improvements in operating costs, noise, fuel consumption, and most importantly emissions compared to conventional propulsion system, all-electric and hybrid electric aircraft configurations will not be preferred for large aircraft unless improvements are made in the specific power of the batteries and fuel cells. for this reason, supercapacitors stand out as a newer technology, which has high specific power as well as weight and size advantages and also attracts attention with its environmentally friendly material structure.
Electric energy storage devices are still under development and each has advantages as well as disadvantages. By using them together, efficient systems can be obtained and one step closer to completely environmentally friendly systems. This article provides a broad overview of energy storage technologies used in micro/mini UAVs. a paper, which includes an extensive literature review, in which supercapacitors with all these features will be our future study in detail.
References
-
N. Yilmaz and A. Atmanli, “Havacilikta alternatif yakit kullanilmasinin incelenmesi,” Journal of Sustainable Aviation Research, pp. 3–10, Mar. 2016, https://doi.org/10.23890/suhad.2016.0103
-
I. Turk, I. Yazar, Ü. Basaran Filik, and T. H. Karakoc, “Simulation based mathematical model of a solar powered DC motor for UAV applications,” in Global Conference on Global Warning GCGW-2018, 2018, https://doi.org/10.1108/aeat-04-2019-0063/full/html
-
B. Khandelwal, A. Karakurt, P. R. Sekaran, V. Sethi, and R. Singh, “Hydrogen powered aircraft: the future of air transport,” Progress in Aerospace Sciences, Vol. 60, pp. 45–59, Jul. 2013, https://doi.org/10.1016/j.paerosci.2012.12.002
-
E. Yiğit, I. Yazar, and T. H. Karakoç, “A new trend for future aircraft propulsion: electric propulsion,” in International Symposium on Sustainable Aviation-ISSA, 2017.
-
Z. O., Ozdemir, and H. Mutlubas, “Enerji taşiyicisi olarak hidrojen ve hidrojen üretim yöntemleri,” Bartın University International Journal of Natural and Applied Sciences, Vol. 2, No. 1, pp. 16–34, 2019.
-
E. Yiğit, “Orta sinif bir insansız hava aracinin elektrikli itki sisteminin matematiksel modellemesi ve deneysel doğrulanmasi,” Eskisehir Anadolu University, Institute of Science and Technology, 2018.
-
K. Santos and L. Delina, “Soaring sustainably: promoting the uptake of sustainable aviation fuels during and post-pandemic,” Energy Research and Social Science, Vol. 77, p. 102074, Jul. 2021, https://doi.org/10.1016/j.erss.2021.102074
-
N. K. Ragbir, S. Rice, S. R. Winter, and E. C. Choy, “Emotions and caring mediate the relationship between knowledge of sustainability and willingness to pay for greener aviation,” Technology in Society, Vol. 64, p. 101491, Feb. 2021, https://doi.org/10.1016/j.techsoc.2020.101491
-
Y. F. Wang, K. P. Li, X. M. Xu, and Y. R. Zhang, “Transport energy consumption and saving in China,” Renewable and Sustainable Energy Reviews, Vol. 29, pp. 641–655, Jan. 2014, https://doi.org/10.1016/j.rser.2013.08.104
-
Wenping Cao, B. C. Mecrow, G. J. Atkinson, J. W. Bennett, and D. J. Atkinson, “Overview of electric motor technologies used for more electric aircraft (MEA),” IEEE Transactions on Industrial Electronics, Vol. 59, No. 9, pp. 3523–3531, Sep. 2012, https://doi.org/10.1109/tie.2011.2165453
-
S. Gautam, “COVID-19: air pollution remains low as people stay at home,” Air Quality, Atmosphere and Health, Vol. 13, No. 7, pp. 853–857, May 2020, https://doi.org/10.1007/s11869-020-00842-6
-
B. Brunekreef and S. T. Holgate, “Air pollution and health,” The Lancet, Vol. 360, No. 9341, pp. 1233–1242, Oct. 2002, https://doi.org/10.1016/s0140-6736(02)11274-8
-
R. Hiserote and F. Harmon, “Analysis of hybrid-electric propulsion system designs for small unmanned aircraft systems,” in 8th Annual International Energy Conversion Engineering Conference, Jul. 2010, https://doi.org/10.2514/6.2010-6687
-
D. Verstraete, K. Lehmkuehler, A. Gong, J. R. Harvey, G. Brian, and J. L. Palmer, “Characterisation of a hybrid, fuel-cell-based propulsion system for small unmanned aircraft,” Journal of Power Sources, Vol. 250, pp. 204–211, Mar. 2014, https://doi.org/10.1016/j.jpowsour.2013.11.017
-
C. Friedrich and P. A. Robertson, “Hybrid-electric propulsion for aircraft,” Journal of Aircraft, Vol. 52, No. 1, pp. 176–189, Jan. 2015, https://doi.org/10.2514/1.c032660
-
D. W. Corson, “High power battery systems for hybrid vehicles,” Journal of Power Sources, Vol. 105, No. 2, pp. 110–113, Mar. 2002, https://doi.org/10.1016/s0378-7753(01)00927-2
-
C. Friedrich and P. A. Robertson, “Hybrid-electric propulsion for automotive and aviation applications,” CEAS Aeronautical Journal, Vol. 6, No. 2, pp. 279–290, Dec. 2014, https://doi.org/10.1007/s13272-014-0144-x
-
E. Yiğit, I. Yazar, and T. H. Karakoç, “Hibrit elektrik itki sistemleri ve sistem tasariminda komponent seçiminin önemi,” in UHUK, 2018.
-
I. Geiß and R. Voit-Nitschmann, “Sizing of the energy storage system of hybrid-electric aircraft in general aviation,” CEAS Aeronautical Journal, Vol. 8, No. 1, pp. 53–65, Nov. 2016, https://doi.org/10.1007/s13272-016-0220-5
-
T. Bocklisch, “Hybrid energy storage approach for renewable energy applications,” Journal of Energy Storage, Vol. 8, pp. 311–319, Nov. 2016, https://doi.org/10.1016/j.est.2016.01.004
-
J. Y. Hung and L. F. Gonzalez, “On parallel hybrid-electric propulsion system for unmanned aerial vehicles,” Progress in Aerospace Sciences, Vol. 51, pp. 1–17, May 2012, https://doi.org/10.1016/j.paerosci.2011.12.001
-
Commercial Aircraft Propulsion and Energy Systems Research: Reducing Global Carbon Emissions. Washington, DC: The National Academies, 2016, https://doi.org/10.17226/23490
-
C. Friedrich and P. A. Robertson, “Design of hybrid-electric propulsion systems for light aircraft,” in 14th AIAA Aviation Technology, Integration, and Operations Conference, Jun. 2014, https://doi.org/10.2514/6.2014-3008
-
A. Kerem, “Elektrikli araç teknolojisinin gelişimi ve gelecek beklentileri,” Mehmet Akif Ersoy University Journal of Science Institute, Vol. 5, No. 1, pp. 1–13, 2014.
-
D. Cericola, P. Novák, A. Wokaun, and R. Kötz, “Hybridization of electrochemical capacitors and rechargeable batteries: An experimental analysis of the different possible approaches utilizing activated carbon, Li4Ti5O12 and LiMn2O4,” Journal of Power Sources, Vol. 196, No. 23, pp. 10305–10313, Dec. 2011, https://doi.org/10.1016/j.jpowsour.2011.07.032
-
T. J. Wall and R. Meyer, “A survey of hybrid electric propulsion for aircraft,” in 53rd AIAA/SAE/ASEE Joint Propulsion Conference, Jul. 2017, https://doi.org/10.2514/6.2017-4700
-
B. Sørensen, “A history of renewable energy technology,” Energy Policy, Vol. 19, No. 1, pp. 8–12, Jan. 1991, https://doi.org/10.1016/0301-4215(91)90072-v
-
I. Hadjipaschalis, A. Poullikkas, and V. Efthimiou, “Overview of current and future energy storage technologies for electric power applications,” Renewable and Sustainable Energy Reviews, Vol. 13, No. 6-7, pp. 1513–1522, Aug. 2009, https://doi.org/10.1016/j.rser.2008.09.028
-
S. Ould Amrouche, D. Rekioua, T. Rekioua, and S. Bacha, “Overview of energy storage in renewable energy systems,” International Journal of Hydrogen Energy, Vol. 41, No. 45, pp. 20914–20927, Dec. 2016, https://doi.org/10.1016/j.ijhydene.2016.06.243
-
B. Kocaman, “Akilli şebekeler ve mikro şebekelerde enerji depolama teknolojileri,” Bitlis Eren Üniversitesi Fen Bilimleri Dergisi, Vol. 2, No. 1, pp. 119–127, 2013.
-
S. S. Gemici, “Elektrikli ulaşım sistemlerinde enerji depolama yöntemlerinin incelenmesi,” Institute of Science, Yildiz Teknik University, 2006.
-
J. Plomer and J. First, “Flywheel energy storage retrofit system for hybrid and electric vehicles,” in Smart Cities Symposium, 2015.
-
H. Ibrahim, A. Ilinca, and J. Perron, “Energy storage systems-characteristics and comparisons,” Renewable and Sustainable Energy Reviews, Vol. 12, No. 5, pp. 1221–1250, Jun. 2008, https://doi.org/10.1016/j.rser.2007.01.023
-
D. Bakker, “Battery electric vehicles: performance, CO2 emissions, lifecycle costs and advanced battery technology development,” Energy and Resources Copernicus institute University of Utrecht, 2010.
-
M. Winter and R. J. Brodd, “What are batteries, fuel cells, and supercapacitors?,” Chemical Reviews, Vol. 104, No. 10, pp. 4245–4270, Oct. 2004, https://doi.org/10.1021/cr020730k
-
S. C. Gorgulu, I. Yazar, and T. H. Karakoç, “Comparison of energy storage components in aviation,” in International Symposium on Aircraft Technology, MRO and Operations (ISATECH-2021)., 2021, https://doi.org/10.3389/fpace.2022.1002258/full
-
Ş. Efe and Z. A. Güngör, “Geçmişten Günümüze Batarya Teknolojisi,” European Journal of Science and Technology, Vol. 32, pp. 947–955, Jan. 2022, https://doi.org/10.31590/ejosat.1048673
-
G. Marin-Garcia, G. Vazquez-Guzman, J. M. Sosa, A. R. Lopez, P. R. Martinez-Rodriguez, and D. Langarica, “Battery types and electrical models: a review,” in 2020 IEEE International Autumn Meeting on Power, Electronics and Computing (ROPEC), Vol. 4, pp. 1–6, Nov. 2020, https://doi.org/10.1109/ropec50909.2020.9258711
-
Y. Miao, P. Hynan, A. Von Jouanne, and A. Yokochi, “Current li-ion battery technologies in electric vehicles and opportunities for advancements,” Energies, Vol. 12, No. 6, p. 1074, Mar. 2019, https://doi.org/10.3390/en12061074
-
S. Satpathy, S. Das, and B. K. Bhattacharyya, “How and where to use super-capacitors effectively, an integration of review of past and new characterization works on super-capacitors,” Journal of Energy Storage, Vol. 27, p. 101044, Feb. 2020, https://doi.org/10.1016/j.est.2019.101044
-
M. Fichtner et al., “Recent research and progress in batteries for electric vehicles,” Batteries and Supercaps, Vol. 5, No. 2, pp. 4441–4461, Oct. 2021, https://doi.org/10.1002/batt.202100224
-
A. Affanni, A. Bellini, G. Franceschini, P. Guglielmi, and C. Tassoni, “Battery choice and management for new-generation electric vehicles,” IEEE Transactions on Industrial Electronics, Vol. 52, No. 5, pp. 1343–1349, Oct. 2005, https://doi.org/10.1109/tie.2005.855664
-
C. Iclodean, B. Varga, N. Burnete, D. Cimerdean, and B. Jurchiş, “Comparison of different battery types for electric vehicles,” in IOP Conference Series: Materials Science and Engineering, Vol. 252, p. 012058, Oct. 2017, https://doi.org/10.1088/1757-899x/252/1/012058
-
J. R. Miller and A. Burke, “Electrochemical capacitors: challenges and opportunities for real-world applications,” The Electrochemical Society Interface, Vol. 17, No. 1, pp. 53–57, Mar. 2008, https://doi.org/10.1149/2.f08081if
-
A. Burke, “R&D considerations for the performance and application of electrochemical capacitors,” Electrochimica Acta, Vol. 53, No. 3, pp. 1083–1091, Dec. 2007, https://doi.org/10.1016/j.electacta.2007.01.011
-
M. Yıldız and T. H. Karakoç, “Havacilikta kullanilan bataryaların tasarim parametrelerine göre boyutlandirilmasi,” Journal of Sustainable Aviation Research, Vol. 2, No. 1, pp. 27–37, Mar. 2017, https://doi.org/10.23890/suhad.2017.0104
-
L. Kumar and S. Jain, “Electric propulsion system for electric vehicular technology: a review,” Renewable and Sustainable Energy Reviews, Vol. 29, pp. 924–940, Jan. 2014, https://doi.org/10.1016/j.rser.2013.09.014
-
J. Y. Yong, V. K. Ramachandaramurthy, K. M. Tan, and N. Mithulananthan, “A review on the state-of-the-art technologies of electric vehicle, its impacts and prospects,” Renewable and Sustainable Energy Reviews, Vol. 49, pp. 365–385, Sep. 2015, https://doi.org/10.1016/j.rser.2015.04.130
-
P. Sharma and T. S. Bhatti, “A review on electrochemical double-layer capacitors,” Energy Conversion and Management, Vol. 51, No. 12, pp. 2901–2912, Dec. 2010, https://doi.org/10.1016/j.enconman.2010.06.031
-
M. Balbaşı and A. Şahin, “Düşük karbon içerikli simetrik süperkapasitör uygulamasi,” Gazi Üniversitesi Mühendislik-Mimarlık Fakültesi Dergisi, Vol. 30, No. 4, pp. 683–692, Dec. 2015, https://doi.org/10.17341/gummfd.63887
-
J. R. Miller and P. Simon, “The Chalkboard: fundamentals of electrochemical capacitor design and operation,” The Electrochemical Society Interface, Vol. 17, No. 1, pp. 31–32, Mar. 2008, https://doi.org/10.1149/2.f02081if
-
J. Schindall, “The charge of the ultra-capacitors,” IEEE Spectrum, Vol. 44, No. 11, pp. 42–46, 2007.
-
A. M. San, “Bir süper kapasitörün elektronik modellemesi,” Maltepe University Graduate School of Natural and Applied Sciences, 2019.
-
Y. Ma et al., “A two step approach for making super capacitors from waste wood,” Journal of Cleaner Production, Vol. 279, p. 123786, Jan. 2021, https://doi.org/10.1016/j.jclepro.2020.123786
-
F. Li, J. Shi, and X. Qin, “Synthesis and supercapacitor characteristics of PANI/CNTs composites,” Chinese Science Bulletin, Springer Science and Business Media LLC, 2010.
-
Q. Jiang, M. Z. Qu, G. M. Zhou, B. L. Zhang, and Z. L. Yu, “A study of activated carbon nanotubes as electrochemical super capacitors electrode materials,” Materials Letters, Vol. 57, No. 4, pp. 988–991, Dec. 2002, https://doi.org/10.1016/s0167-577x(02)00911-4
-
M. N. Mohd Iqbaldin, I. Khudzir, M. I. Mohd Azlan, A. G. Zaidi, B. Surani, and Z. Zubri, “Properties of coconut shell activated carbon,” Journal of Tropical Forest Science, Vol. 25, No. 4, pp. 497–503, Oct. 2013.
-
E. Taer, R. Taslim, Z. Aini, S. D. Hartati, and W. S. Mustika, “Activated carbon electrode from banana-peel waste for supercapacitor applications,” in The 6th International Conference on Theoretical and Applied Physics (The 6th ICTAP), Jan. 2017, https://doi.org/10.1063/1.4973093
-
W. B. Kurniawan, A. Indriawati, and D. Marina, “The effect of particle size on the performance of electrode supercapacitor based on pepper (pipper nigrum) shell activated carbon,” in IOP Conference Series: Earth and Environmental Science, Vol. 353, No. 1, p. 012041, Oct. 2019, https://doi.org/10.1088/1755-1315/353/1/012041
-
E. B. O. Sihite, Stepanus, and Budiarto, “Study of the effect of supercapasitors types on crystal structure and microstructure of supercapasitor electrode materials,” in IOP Conference Series: Materials Science and Engineering, Vol. 725, p. 012042, Jan. 2020, https://doi.org/10.1088/1757-899x/725/1/012042
-
R. Kötz and M. Carlen, “Principles and applications of electrochemical capacitors,” Electrochimica Acta, Vol. 45, No. 15-16, pp. 2483–2498, May 2000, https://doi.org/10.1016/s0013-4686(00)00354-6
-
J. Nan, X. Xu, J. Wang, and Z. Gao, “Estimate of super capacitor’s dynamic capacity,” Energy Procedia, Vol. 105, pp. 2194–2200, May 2017.
-
A. K. Shukla, A. Banerjee, M. K. Ravikumar, and A. Jalajakshi, “Electrochemical capacitors: technical challenges and prognosis for future markets,” Electrochimica Acta, Vol. 84, pp. 165–173, Dec. 2012, https://doi.org/10.1016/j.electacta.2012.03.059
-
Y. Zhang et al., “Progress of electrochemical capacitor electrode materials: a review,” International Journal of Hydrogen Energy, Vol. 34, No. 11, pp. 4889–4899, Jun. 2009, https://doi.org/10.1016/j.ijhydene.2009.04.005
-
D. Zhang, J. Wang, Q. Wang, S. Huang, H. Feng, and H. Luo, “Nitrogen self-doped porous carbon material derived from metal-organic framework for high-performance super-capacitors,” Journal of Energy Storage, Vol. 25, p. 100904, Oct. 2019, https://doi.org/10.1016/j.est.2019.100904
-
E. Özbek, G. Yalin, S. Ekici, and T. H. Karakoc, “Evaluation of design methodology, limitations, and iterations of a hydrogen fuelled hybrid fuel cell mini UAV,” Energy, Vol. 213, p. 118757, Dec. 2020, https://doi.org/10.1016/j.energy.2020.118757
-
B. Kocaman, Enerji Depolama Teknolojileri. Ankara,Turkey: İksad Yayınevi, 2021.
-
M. Yacoubi, C. Lemone, A. Bourguignon, and P. Hendrick, “Study of the propulsion system of a VTOL MUAV using fuel cells,” in 9th National Congress on Theoretical and Applied Mechanics, 2012.
-
Z. F. Pan, L. An, and C. Y. Wen, “Recent advances in fuel cells based propulsion systems for unmanned aerial vehicles,” Applied Energy, Vol. 240, pp. 473–485, Apr. 2019, https://doi.org/10.1016/j.apenergy.2019.02.079
-
S. Kusdogan, “Yenilenebilir enerji uygulamalarında hibrit enerji depolama teknolojileri ve uygulamaları,” in V. Electrical Installation National Congress and Exhibition, III. Power and Energy Energy Systems Symposium, 2017.
-
C. E. Holland, J. W. Weidner, R. A. Dougal, and R. E. White, “Experimental characterization of hybrid power systems under pulse current loads,” Journal of Power Sources, Vol. 109, No. 1, pp. 32–37, Jun. 2002, https://doi.org/10.1016/s0378-7753(02)00044-7
-
Jian Cao and A. Emadi, “A new battery/ultra capacitor hybrid energy storage system for electric, hybrid, and plug-in hybrid electric vehicles,” IEEE Transactions on Power Electronics, Vol. 27, No. 1, pp. 122–132, Jan. 2012, https://doi.org/10.1109/tpel.2011.2151206
-
M. E. Glavin, P. K. W. Chan, S. Armstrong, and W. G. Hurley, “A stand-alone photovoltaic supercapacitor battery hybrid energy storage system,” in 2008 13th International Power Electronics and Motion Control Conference (EPE/PEMC 2008), pp. 1688–1695, Sep. 2008, https://doi.org/10.1109/epepemc.2008.4635510
-
R. Hemmati and H. Saboori, “Emergence of hybrid energy storage systems in renewable energy and transport applications – a review,” Renewable and Sustainable Energy Reviews, Vol. 65, pp. 11–23, Nov. 2016, https://doi.org/10.1016/j.rser.2016.06.029
-
M. Mladenov, E. Petrov, K. Kanev, and I. Chavdarov, “Unmanned aerial vehicle energy efficiency improvement by batery-supercapacitor system,” (in Russian), in 19th NNTC with international participation "ADP-2010", 2021.
-
R. Xiong, H. Chen, C. Wang, and F. Sun, “Towards a smarter hybrid energy storage system based on battery and ultracapacitor – a critical review on topology and energy management,” Journal of Cleaner Production, Vol. 202, pp. 1228–1240, Nov. 2018, https://doi.org/10.1016/j.jclepro.2018.08.134
-
A. Gong and D. Verstraete, “Flight test of a fuel-cell/battery/supercapacitor triple hybrid UAV propulsion system,” in 31st Congress of the International Council of the Aeronautical Sciences, 2018.
About this article
The authors have not disclosed any funding.
The datasets generated during and/or analyzed during the current study are available from the corresponding author on reasonable request.
Saliha Cansu Gorgulu: conceptualization, methodology, resources, visualization, writing-original draft preparation. Isil Yazar: conceptualization, methodology, supervision. Tahir Hikmet Karakoc: supervision.
The authors declare that they have no conflict of interest.