Abstract
The main objective of this study to develop efficient numerical techniques based on coupled finite and boundary element methods to estimate natural vibration frequencies in compound reservoirs with liquid. Elastic structures composed of cylindrical and conical shells connected by rings have been examined. The space between the shells is filled with an ideal, incompressible fluid. The advantage of the proposed approach lies in the ability to investigate both free and forced vibrations of empty and liquid-filled shells structures within the framework of the single computer technology. The benchmark test calculations demonstrated the high accuracy and efficiency of the proposed approach. The novelty and practical value of the obtained results lie in the ability to investigate fuel tanks of complex shapes under various conditions.
Highlights
- Liquid induced vibrations of shells.
- Elastic structures composed of cylindrical and conical shells.
- Modal analysis.
1. Introduction
Shells and shell-like structures play a significant role in modern mechanical engineering. These components are commonly used as fuel containers in launch vehicles, oil storage tanks, containers for storing various substances, including potentially dangerous ones. Nowadays, the cylindrical [1], conical, toroidal and coaxial cylindrical shells [2] are commonly employed as fuel tanks. The most precise strength assessment of liquid-filled tanks under significant external forces often relies on comprehensive, full-scale field experiments. However, these experiments are both expensive and pose risks. So, virtual experimentation is gaining prominence in scientific research as a safer and more cost-effective alternative. Various effective methods have been elaborated for computer modeling dynamic processes, including finite (FEM) [3] and boundary (BEM) [4] element methods, finite volume methods [5], and series expansions [6]. The initial step in dynamic modeling involves determining the frequencies and modes of natural vibrations. This aspect has been explored in [2], [7], and [8]. Papers [9], [10] are dedicated to developing analytical methods for analyzing vibrations in fluid-filled shells with baffles. The investigation [2] focused on examining the natural frequencies of toroidal and coaxial cylindrical shells, while [8] and [11] delved into the mitigation of liquid sloshing using rigid baffles. Furthermore, research involving the theoretical and experimental stability aspects of cylindrical shells and beams has been accomplished in [1], [12]. The design and manufacture of each new powerful launch vehicles necessitate the development of new fuel tanks. Compound shells are becoming more common in these tanks. To mitigate undesirable resonance, it is necessary to study the entire frequency spectrum of the tank’s vibrations. However, the vibrations of compound shells have not received sufficient attention in the literature [13]. Therefore, the vibrations study of compound coaxial cylindrical and cylindrical-conical shells with liquids is a topical problem.
2. Methodology
2.1. Problem statement
Elastic compound shells of revolution, partially filled with liquids, are considered, Fig. 1(a-b). The wetted surface of the shell is denoted as S1, while S0 represents the liquid free surface. It is assumed that the liquid is an ideal and incompressible. Reservoirs consist of coaxial cylindrical and conical shells connected by rings. The liquid is located between the shells. The surfaces of the shells and bottoms are wetted, and the free surface at rest is at a height of H, forming a ring, which is described in polar coordinate system as {z=H,R1<r<R0}. Here for the shell structure, depicted in Fig. 1(a), R0=R3+(R2-R3)(L-H)/L, whereas R0=R3+(R2-R3)H/L for the shell structure, depicted in Fig. 1(b). The wetted surface S1 consists of cylindrical and conical parts as well as the bottom. The liquid within the shells undergoes vibrations due to applied loads. The resulting flow from these loads is assumed to be irrotational. If V(Vx,Vy,Vz) represents the fluid velocity vector, the incompressibility condition of the continuum can be derived from the equation divV=0. So, the velocity potential Φ can be introduced as V=gradΦ, and it leads to the Laplace equation. The motion governing equations of liquid-filled elastic shells are given by [13]:
where L and M denote the operators corresponding to elastic and mass forces acting on the shell structure, U=(U1,U2,U3) is the displacement vector, Q is the vector of external surface loads, and Pl signifies hydrodynamic pressure, Pl=pn.
Fig. 1Сylindrical – conical compound shells and their drafts
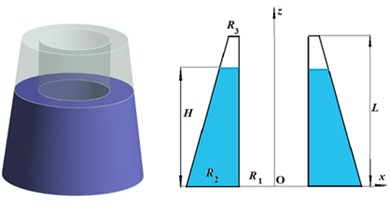
a)
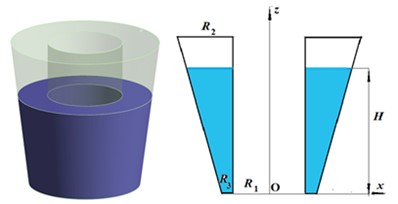
b)
The pressure value p, according to the Bernoulli integral, can be represented as p=-ρl∂Φ∂tp0, where p0 is atmospheric pressure. The region occupied by the liquid is denoted by Ω, and P is for points within Ω. Boundary conditions for the Laplace equation within Ω are outlined as follows. On surfaces S1, no-slip conditions are enforced, and on S0 the dynamic condition is set:
So, it is necessary to determine the unknown functions Φ and U through Eq. (1-2) including boundary and initial data. The unknown vector-function is represented as following series:
where functions uk(x,y,z) are natural vibration modes of the empty shell structure, and ck(t) are time-dependent unknown factors. To determine the vibration modes uk(x,y,z), the FEM is used [4]. To determine potential Φ, boundary value problem Eq. (2) is solved. The following series is incorporated Φ(r,θ,z,t)=∑nk=1φk(r,θ,z)˙ck(t). Here the functions φk(x,y,z) are solutions of boundary value problem Eq. (2) with ∂φk∂n=(uk,n).
For shells of revolution, all unknown functions for each l can be expressed in the form [4]:
Such presentations simplify the dynamical analysis by reducing the problem to a series of uncoupled single-degree-of-freedom systems, depending on l only.
3. Results and discussion
3.1. Validation
The validation study involves truncated isotropic conical tanks. Let R1 and R2 are the cone radii at its larger and smaller ends, α is the semi-vertex angle, and H is the cone height. In numerical simulations, the shell thickness is h/R1=0.01. The semi-vertex angle is α=45°, H/R2=1, E=2.11·106MPa, ν=0.3, ρs=8000 kg/m3, ρl= 1000 kg/m3, and R1=1 m, [16]. Shell edge fixations are clamped–clamped (CC), clamped–simply supported (C-SS), simply supported –clamped (SS-C), and clamped –free (C-F) ones. Convergence was achieved when the number of finite elements on the tank walls equals 30. Table 1 provides comparison of obtained results with data of [16]. The specified above boundary conditions are considered, with wave numbers l= 0, 1,…, 7.
Table 1Dimensionless frequency parameter Ω1 for empty conical tank
l | Boundary conditions | |||||
SS-C | C-SS | C-C | ||||
present FEM | Shu [16] | present FEM | Shu [16] | present FEM | Shu [16] | |
0 | 0,8701 | 0,8700 | 0,7157 | 0,7151 | 0.8730 | 0.8732 |
1 | 0,8119 | 0,8118 | 0,7097 | 0,7090 | 0,8120 | 0,8120 |
2 | 0,6614 | 0,6613 | 0,6479 | 0,6475 | 0,6694 | 0,6696 |
3 | 0.5247 | 0.5245 | 0,5203 | 0,5201 | 0,5427 | 0,5428 |
4 | 0,4321 | 0,4319 | 0,4166 | 0,4161 | 0,4563 | 0,4566 |
5 | 0,3828 | 0,3826 | 0.3596 | 0.3592 | 0,4087 | 0,4089 |
6 | 0,3739 | 0,3737 | 0,3458 | 0,3450 | 0,3960 | 0,3964 |
7 | 0,3984 | 0,3981 | 0,3651 | 0,3648 | 0,4141 | 0,4143 |
In this comparison, dimensionless frequencies are obtained for truncated isotropic elastic conical tanks for k=1, α=45°, using the frequency parameter Ω1 as in [16]. The results obtained by the proposed reduced BEM are in good agreement with data of [16].
3.2. Vibrations of elastic cylindrical-conical shells.
The vibration frequencies and modes of the empty and fluid-filled structures, depicted in Fig. 1, are estimated. The next parameters are chosen: L= 1 m, R1= 0.5 m, R2= 0.5 m, R3=0.25 m, the filling level H= 1.25 m. The material and mechanical properties are ρs=7800 kg/m3, E=2.1 106 MPa, ν=0.3, the thickness of the shell structure is 3 mm. The structure has been rigidly bottom fixed. The frequencies and modes of the empty structure are calculated first; the FEM [6] is used. Table 2 shows the lowest vibration frequencies of unfilled structures, Fig. 1(a)-(b).
Table 2Vibration frequencies of unfilled tanks, Hz
No. | 1 | 2 | 3 | 4 | 5 | 6 | 7 | 8 |
Shell structure, Fig. 1(a) | ||||||||
Values | 127,59 | 128,07 | 132,6 | 133,6 | 157,79 | 158,55 | 167,61 | 169,86 |
Shell structure, Fig. 1(b) | ||||||||
Values | 121,57 | 122,04 | 124,8 | 125,56 | 154,81 | 155,42 | 157,98 | 158,18 |
The frequencies of the structure depicted in Fig. 1(b) slightly differ from the frequencies of the structure shown in Fig. 1(a). The corresponding vibration modes ukl are shown in Fig. 2.
Fig. 2Vibration modes of the unfilled structures
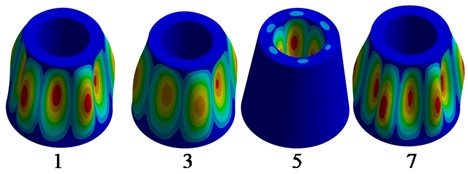
a) Modes of shell structure Fig. 1(a)
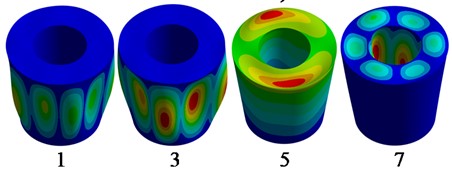
b) Modes of shell structure Fig. 1(b)
Note that, as in [16], the lowest frequencies correspond to 6th and 7th wavenumbers. It should also be noted the presence of practically multiple frequencies. Next, the base functions φk(r,θ,H) and the corresponding frequencies are obtained. These functions are vibration modes of the structure walls, considering the liquid added masses. The frequencies are provided in Table 3.
Table 3Vibration frequencies of elastic walls considering liquid added masses (Hz)
No | 1 | 2 | 3 | 4 | 5 | 6 | 7 | 8 |
Shell structure, Fig. 1(a) | ||||||||
Values | 45,327 | 45,597 | 47,141 | 47,602 | 51,264 | 51,433 | 52,787 | 54,053 |
Shell structure, Fig. 1(b) | ||||||||
Values | 43,542 | 43,619 | 48,367 | 48,384 | 50,004 | 50,291 | 57,81 | 57,896 |
Significant decreasing in frequencies compared to the empty shells has been observed. Multiple frequencies are also available. Fig. 3 depicts some characteristic vibration modes.
The lowest frequency corresponds to the eighth wave number. This result cannot be predicted theoretically, and only computer experiments allow to understand the nature of vibration patterns.
Fig. 3Vibration modes φkr,θ, H of elastic walls considering liquid added masses
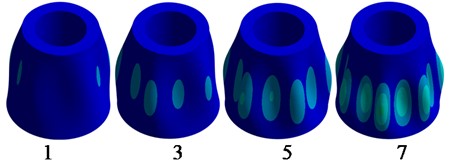
a) Modes of shell structure Fig. 1(a)
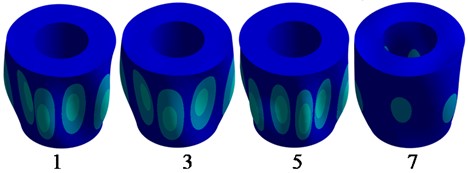
b) Modes of shell structure Fig. 1(b)
4. Conclusions
The approach has been developed based on the application of reduced finite and boundary element methods as well as mode superposition methods for analysing free vibrations of the coaxial elastic shell structures partially filled with liquid. The developed approach allows for the investigation of free and forced vibrations of unfilled shells, as well as for the problem of vibrations of liquid-filled shells. The further intention is to analyse the forced vibrations.
References
-
J. Liu, Q. Zang, W. Ye, and G. Lin, “High performance of sloshing problem in cylindrical tank with various barrels by isogeometric boundary element method,” Engineering Analysis with Boundary Elements, Vol. 114, pp. 148–165, 2020, https://doi.org/10.1016/j.enganabound
-
A. Karaiev and E. Strelnikova, “Liquid sloshing in circular toroidal and coaxial cylindrical shells,” in Advances in Design, Simulation and Manufacturing III, pp. 3–13, Jun. 2020, https://doi.org/10.1007/978-3-030-50491-5_1
-
S. Misura, N. Smetankina, and I. Misiura, “Optimal design of the cyclically symmetrical structure under static load,” in Lecture Notes in Networks and Systems, pp. 256–266, Jan. 2021, https://doi.org/10.1007/978-3-030-66717-7_21
-
V. I. Gnitko, K. G. Degtyariov, A. O. Karaiev, and E. A. Strelnikova, “Singular boundary method in a free vibration analysis of compound liquid-filled shells,” BEM/MRM 42 2019, Vol. 126, pp. 189–200, Sep. 2019, https://doi.org/10.2495/be420171
-
P. Lampart, A. Rusanov, S. Yershov, S. Marcinkowski, and A. Gardzilewicz, “Validation of a 3D RANS solver with a state equation of thermally perfect and calorically imperfect gas on a multi-stage low-pressure steam turbine flow,” Journal of Fluids Engineering, Vol. 127, No. 1, pp. 83–93, Jan. 2005, https://doi.org/10.1115/1.1852491
-
Q. Wang, D. Shi, Q. Liang, and F. Pang, “Free vibrations of composite laminated doubly-curved shells and panels of revolution with general elastic restraints,” Applied Mathematical Modelling, Vol. 46, pp. 227–262, Jun. 2017, https://doi.org/10.1016/j.apm.2017.01.070
-
N. Choudhary and E. Strelnikova, “Liquid vibrations in a container with a membrane at the free surface,” Vibroengineering Procedia, Vol. 37, pp. 13–18, May 2021, https://doi.org/10.21595/vp.2021.21996
-
N. Kumar and N. Choudhary, “Sloshing reduction in three-dimensional rectangular container using rigid baffles,” Vibroengineering Procedia, Vol. 42, pp. 39–44, May 2022, https://doi.org/10.21595/vp.2022.22550
-
N. Kumar and N. Choudhary, “Simulation and semi-analytical approach on sloshing mitigation,” in 2021 International Conference on Recent Advances in Mathematics and Informatics (ICRAMI), Sep. 2021, https://doi.org/10.1109/icrami52622.2021.9585926
-
N. Choudhary, S. N. Bora, and E. Strelnikova, “Study on liquid sloshing in an annular rigid circular cylindrical tank with damping device placed in liquid domain,” Journal of Vibration Engineering and Technologies, Vol. 9, No. 7, pp. 1577–1589, Jun. 2021, https://doi.org/10.1007/s42417-021-00314-w
-
E. A. Strelnikova, N. Choudhary, D. V. Kriutchenko, V. I. Gnitko, and A. M. Tonkonozhenko, “Liquid vibrations in circular cylindrical tanks with and without baffles under horizontal and vertical excitations,” Engineering Analysis with Boundary Elements, Vol. 120, pp. 13–27, Nov. 2020, https://doi.org/10.1016/j.enganabound.2020.07.024
-
K. Murawski, “Technical stability of very slender rectangular columns compressed by ball-and-socket joints without friction,” International Journal of Structural Glass and Advanced Materials Research, Vol. 4, No. 1, pp. 186–208, Jan. 2020, https://doi.org/10.3844/sgamrsp.2020.186.208
-
V. V. Gnitko, K. G. Degtyariov, V. V. Naumenko, and E. A. Strelnikova, “Coupled BEM and FEM analysis of fluid-structure interaction in dual compartment tanks,” International Journal of Computational Methods and Experimental Measurements, Vol. 6, No. 6, pp. 976–988, Jan. 2018, https://doi.org/10.2495/cmem-v6-n6-976-988
-
Z. Zhang, A.-F. Tao, Q.-R. Wu, and Y.-H. Xie, “Review on the progress and issues in liquid tank sloshing of ships,” China Ocean Engineering, Vol. 37, No. 5, pp. 709–724, Nov. 2023, https://doi.org/10.1007/s13344-023-0060-0
-
N. Choudhary and S. N. Bora, “Linear sloshing frequencies in the annular region of a circular cylindrical container in the presence of a rigid baffle,” Sādhanā, Vol. 42, No. 5, pp. 805–815, Apr. 2017, https://doi.org/10.1007/s12046-017-0642-8
-
N. Choudhary and S. N. Bora, “Liquid sloshing in a circular cylindrical container containing a two-layer fluid,” International Journal of Advances in Engineering Sciences and Applied Mathematics, Vol. 8, No. 4, pp. 240–248, Nov. 2016, https://doi.org/10.1007/s12572-016-0176-z
-
A. Karaiev and E. Strelnikova, “Axisymmetric polyharmonic spline approximation in the dual reciprocity method,” ZAMM – Journal of Applied Mathematics and Mechanics / Zeitschrift für Angewandte Mathematik und Mechanik, Vol. 101, No. 4, Jan. 2021, https://doi.org/10.1002/zamm.201800339
-
A. Karaiev and E. Strelnikova, “Singular integrals in axisymmetric problems of elastostatics,” International Journal of Modeling, Simulation, and Scientific Computing, Vol. 11, No. 1, p. 2050003, Feb. 2020, https://doi.org/10.1142/s1793962320500038
-
C. Shu, “An efficient approach for free vibration analysis of conical shells,” International Journal of Mechanical Sciences, Vol. 38, No. 8-9, pp. 935–949, Aug. 1996, https://doi.org/10.1016/0020-7403(95)00096-8
About this article
The authors have not disclosed any funding.
The datasets generated during and/or analyzed during the current study are available from the corresponding author on reasonable request.
The authors declare that they have no conflict of interest.