Abstract
The date palm, or Phoenix dactylifera, is a crop that is grown for food and is used by many people on a regular basis. The cultivation of date palms, their processing, and consumer demand all produce tons of waste. Date palm seeds can account for up to 10 % of the total weight of the fruits. A topic of interest for research is the application of date seed waste in the fields of engineering, nutrition, and cosmetics. This work aims to show that epoxy/palm seed date composites are suitable for use as biomaterials by examining their wear behavior. Give a brief introduction to a few ideas before going over the fundamental idea of wear resistance. Future wear resistance improvements in biomedical applications and other industries that might benefit from this addition will continue to be achieved through the use of date palm seed microparticles in epoxy. In this study, epoxy composites containing palm seed particles are made by the mixing procedure. The studied composites made from date palm seed powder particles has micron particle size of 150 which is mixed with epoxy as a matrix. The percentages of date palm seeds are varying from 5 % to 20 %. The 20 percent sample had the best results, losing 7.03 percent of their starting weight. The 10 percent group, which lost 9.4 percent, the 15 percent group, which lost 12.2 percent, and the 5 percent sample, which lost 19.95 percent, were the next in line. Each of the four samples had 1 kg to 5 kg of weight applied to them at five different rotation speeds. Upon analysis of all the samples under investigation, it was discovered that the date palm seeds enhanced and increased wear resistance, leading to better outcomes.
1. Introduction
Polymers are materials made up of a large number of repeating subunits that combine to form exceedingly complex molecules, or macromolecules. Both synthetic and natural polymers are indispensable and widely used in daily life due to their numerous qualities. Polymers are created by polymerizing a large number of small molecules known as monomers. Polymers have unique physical properties such as toughness, high elasticity, viscoelasticity, and a proclivity to form amorphous and semicrystalline structures rather than crystals due to their larger molecular mass than small molecule compounds [1, 2]. A kind of thermoset polymer with at least two epoxide groups in the monomer is epoxy resin. The excellent adherence of epoxy resins (ERs) to various substrates and their chemical activity for crosslinking activities make them an important class of synthetic polymers. Epoxy is considered as one of the most beneficial materials materials which has cross-linking characteristic produces materials with excellent mechanical qualities, high heat stability, little shrinkage, wear resistance, resistance to chemicals and solvents, and low toxicity [3]. A long-chain molecular structure with reactive sites at either end produces epoxy resins. Epoxy has the chemical formula, -21., H-25., Clo-5. Moreover, two ring groups in the middle of the epoxy molecule absorb mechanical and thermal stresses more effectively than linear groups do, greatly increasing the stiffness, toughness, and heat resistance of the epoxy resin. An idealized chemical structure of a typical epoxy is shown in Fig. 1 [4].
Fig. 1Common chemical structure of an epoxy resins [4].
![Common chemical structure of an epoxy resins [4].](https://static-01.extrica.com/articles/23798/23798-img1.jpg)
Epoxy resins are used in many different industries, such as coatings, the aerospace sector, electronic materials, and biological systems.
Metals, ceramics, and polymers are the three basic types of materials. When any of these main ingredients are mixed without losing any of their distinct features, composites are formed [5]. A composite substance consists of two distinct chemical and physical characteristics. Together, they produce a material that is optimized to fulfill a certain function, such increasing strength, weight, or electrical resistance. Additionally, they can support the growth of stiffness and strength. They are preferred over conventional materials because they enhance the basic material's qualities and have a variety of practical uses. In today's enterprises, organic materials like composite or reinforced materials are becoming more and more crucial. These materials are also used because of their exceptional mechanical qualities and affordable cost. The emphasis on renewable resources, environmental consequences, and economic considerations all has an impact on the industrial usage of natural and organically reinforced materials. The use of renewable and sustainable fillers in place of organic ones is growing in popularity. These fillers’ low density, cheap cost, and reduced mechanical wear during processing are their key benefits [6-7]. Composite materials are widely used in infrastructure, electrical equipment, aeronautical structures, biomedical applications, pipelines, and tanks.
Date palms (Phoenix dactylifera L.) are a kind of flowering plant that are cultivated extensively worldwide, even in desert and semi-arid regions, for their tasty, edible fruit. It is important to remember that date palm trees are widespread in Pakistan, India, the Middle East, and Northern Africa. Both dry, hot weather and extreme cold may be tolerated by date palm plants. [8-9]. Because date seeds are abundant in plants, they are considered a biomass waste, and using them is therefore considered a low-cost value filler. Date seed (DS)-filled composites are the ideal material since they are simple to assemble and lightweight. Much work has been done to switch out dangerous and contaminated fillers with ones manufactured from bio-sources like eggshells as a result of growing environmental awareness and new laws. [10].
The relationship between date seed powder and poly (butylene adipate-co-terephthalate) biopolyesters was examined by Mittal et al. [11]. The research found a connection between the filler utilized in composites and the pure polymer. Phoenix dactylifera wastes from the processing of date palm fruit were investigated by Ruggiero et al. [12] to see whether they might be utilized to improve the mechanical properties of the composite. The outcomes demonstrated that the date particle had no discernible impact on the glue's sticking properties. At certain bio-filler concentrations, shear strength improved by up to 10.8 % and wear resistance increased by up to 11 %. The mechanical characteristics of polyester reinforced with aligned ramie fibers up to 30 % by volume were examined by Simonassi et al. [13]. The outcomes demonstrated a significant improvement in the toughness of polyester-ramie fiber composites. Impact energy estimates were around two orders of magnitude higher for composites with 30 % ramie fibers than for pure polyester. In general, wear is described as surface degradation caused by mechanical means, whereby material is progressively lost due to relative movement between the surface and the substance or substances it comes into contact with. A liquid, another surface, or hard, abrasive particles floating in a fluid or other solution, such a lubricant, are examples of contacting substances. Procedures including machining, cutting, grinding, and polishing can result in controlled wear.
Because wear leads to component failure or degradation, which is extremely undesired in the great majority of technical applications, wear is an expensive problem. Wear can be brought on by chemical reactions like corrosion or mechanical forces like erosion. Tribology is the study of wear and related processes. Functional surfaces are eroded by wear in machine parts and by other processes including fatigue and creep, which can lead to material failure or loss of functionality. There are several types of wear, including fretting, galling, adhesive, abrasive, corrosive, surface-fatigue, and cavitation erosion.
By adding organic reinforcing components to glass fiber and epoxy (G-E) composites, one can enhance the mechanical characteristics of materials. In this paper, they examine the application of date seeds (DSs) as a G-E composite reinforcing material. Using a semiautomatic process, a DS filler was added to G-E hybrid composites as a powder. Investigations were conducted on the hardness, tensile strength, and impact strength of G-E reinforced DS composites. At different parameter values, the impact of the DS filler on wear volume loss (VL) was examined. The outcomes demonstrated that DS reinforcement at a 10 % concentration enhanced the toughness, hardness, and wear resistance of G-E composites. In the end, the wear VL was minimized to optimize the G-E-DS composite. This led to an ideal DS reinforcement of 10 % at a typical load of 10 N, an abrasive size of 1200 mesh, and an abrading distance of 420 m. [14].
This paper examined the tensile, impact, and morphological characteristics of date palm stem fibers (DPF)/epoxy composites under different loadings (40, 50, and 60 percent wt. percent). The interfacial bonding in composite samples that had experienced tensile fracture was investigated using SEM (SEM). Tensile and impact tests showed that pure epoxy resin's mechanical strength, modulus, impact strength, and elongation at break were all enhanced by up to a 50 % increase in DPF loading. With the addition of DPF filler, the pure epoxy resin’s tensile strength, modulus, impact strength, and elongation at break improve from 20.5 to 25.7657 MPa, 0.5123 to 1.546 GPa, 45.81 to 98.71 J/m, and 0.91 to 1.412 percent, respectively. However, energy absorption reduces from 50 to 32 percent. [15].
It is advised that natural materials be used as polymer fillers in a variety of sectors because of their low cost, suitable mechanical qualities, and minimal environmental effect. Examining the mechanical characteristics of date seed-filled glass fiber (G-E) as a polymer filler is the aim of this work. We looked at how DS filler affected impact energy and wear rate (Ks) at different effective parameters. The kind of reinforcement was identified using FTIR light, and the surface was examined using SEM. The findings demonstrated that including 10 % DS reinforcement into G-E enhanced wear resistance by around 71 % and toughness by about 80 %. The organic DS filler contact surfaces and G-E had a physiochemical reaction, per FTIR measurements. Optimizing G-E reinforcement involved limiting wear rate, choosing the right filler load and type, normal load, and abrasive size [16]. Numerous studies [17-25] have examined the mechanical characteristics of epoxy-based composite materials and have deduced how reinforcing affects both mechanical and fracture qualities.
This study's main goals are to examine the wear behavior of epoxy/date seed powder bio-composites and the behavior of date palm seeds in the assessment of wear resistance.
2. Materials and methods
Epoxy resin comes in liquid form and may be mixed appropriately to make a resin and a hardener that can be set in a mold to the desired shape. After mixing, epoxy typically takes a day to harden. Our intention was to date palm seeds using various ratios of epoxy resin (as powder). In order to determine how much date palm seed powder to include with the necessary percentage, we will measure the mass and volume depending on the form. Epoxy resin and powdered palm date seeds mix readily; however it takes more work to distribute the powder uniformly than normal.
A variety of molds, including the pipes used to cover electrical lines in homes, can be utilized; however, it is difficult to remove the PVC pipe layer from the solid epoxy’s surface. The pipe must be properly cut on three sides before being removed. Epoxy resin is very sticky and resistant to abrasion and chemicals like acids, bases, and solvents because it cures with an insulating layer. Use this product as adhesive, mortar, or coating. This means that once the epoxy glue has set, a mold that can be removed is needed. Resin art is known to have been created using a silicon mold, which made it easy to create and remove. Although epoxy resin is sold by many firms, we selected the best and most highly recommended one, as indicated in Fig. 2.
Any local business that deals in date palms may provide you with date palm seeds. The seeds are from Medina, which is in Saudi Arabia's western region. Based on the latest data from the General Authority for Statistics, the Medina region is home to more than 4 million palm trees, yielding 189 thousand tons of fruit annually. Before being ground, the crushed seeds can be seen in Fig. 3.
Fig. 2Packing for epoxy resin [25]
![Packing for epoxy resin [25]](https://static-01.extrica.com/articles/23798/23798-img2.jpg)
Fig. 3Date palm seeds after crushing [25]
![Date palm seeds after crushing [25]](https://static-01.extrica.com/articles/23798/23798-img3.jpg)
The hardness of the date palm seeds made grinding them difficult, and most grinders broke when they tried. Nevertheless, one of the greatest grinders on the market was found, and its makers even say it can grind boulders. Fig. 4 shows the 800 watt grinder with extremely strong blades.
Fig. 4800 watts grinder and extremely sharp blades used to reduce particle size of date palm seeds [25]
![800 watts grinder and extremely sharp blades used to reduce particle size of date palm seeds [25]](https://static-01.extrica.com/articles/23798/23798-img4.jpg)
Fig. 5Screen with Mesh size of 150 micrometers [25]
![Screen with Mesh size of 150 micrometers [25]](https://static-01.extrica.com/articles/23798/23798-img5.jpg)
Fig. 6Used silicon mold [25]
![Used silicon mold [25]](https://static-01.extrica.com/articles/23798/23798-img6.jpg)
Although there are several sizes available, as shown in Fig. 5, 150 micrometers was the size that was most similar to the particles used. As seen in Fig. 6, shaping and removing a Silicon Mold was simple.
The epoxy resin and hardener mixtures are mixed and stirred using wooden sticks and plastic cups, respectively. There’s also a scaled balance that reads three digits following the point and a little balance that holds 50 g. As an instance (0.001 g).
2.1. Molding method
The emphasis on renewable resources, environmental consequences, and economic considerations all have an impact on the industrial usage of natural and organically reinforced materials. The use of renewable and sustainable fillers in place of organic ones is growing in popularity. These fillers’ low density, cheap cost, and reduced mechanical wear during processing are their key benefits. Epoxy resin serves as the investigation's matrix substance. Epoxy was selected because of its distinct mechanical and physical qualities, which surpass those of conventional polymers. Date palm seed powder is used as a filler in the form of microparticulates. In this study, the mixing process is used to create epoxy composites. Particles of date palm seed powder, 150 microns in size, are used to make composites. There are four different formulas with five, ten, fifteen, and twenty percent filler. Additionally, by using micr0/nano date palm seed particles, the wear resistance of the epoxy is meant to be enhanced. It could be conceivable to employ date palm seed powder in the future to increase wear resistance in biomedical applications or any other disciplines that could benefit from this study because the human body responds extremely well to organic (natural) materials. Epoxy resin comes in liquid form and may be mixed appropriately to make a resin and a hardener that can be set in a mold to the desired shape. After mixing, epoxy typically takes a day to harden. The date palm seeds (in powder form) are intended to be mixed with four distinct ratios of epoxy resin: five percent, ten percent, fifteen percent, and twenty percent. Using an abrasive of 2000P grit, the abrasive wear performances of different specimens were measured under the same wear circumstances. Sand abrasive paper with a normal mass (kg) of 1 kg to 5 kg and a sliding speed (RPM) of 200 RPM to 750 RPM, which will be changed for every speed and weight to guarantee efficacy.
For each of the four samples, start by fastening one kilogram of weight at five different speeds. This will yield five rounds for five distinct weights. The diameter of the pin on the disc, where the sample comes into touch with the sandpaper, will be 12 cm, and each round will last 36 seconds. Every wear test was carried out in an unlubricated (air) environment at ambient temperature (27 °C). Pin specimens were thoroughly cleaned both prior to and during wear testing. The wear rate was computed using the weight loss technique. The sample weight was measured using a high precision (g) balance both before and after each test run.
Table 1 shows the speeds for each weight for all four samples since the speed must be increased as the weight increases.
Table 1Various load weights and rotational speeds have been employed at each load.
Weight (kg) | 1 | 2 | 3 | 4 | 5 | |||||||||||||||
Speeds (rpm) | 200 | 250 | 300 | 350 | 400 | 450 | 400 | 450 | 500 | 450 | 500 | 550 | 500 | 550 | 600 | |||||
350 | 400 | 500 | 550 | 550 | 600 | 600 | 650 | 700 | 750 |
2.2. Test procedure
Start the test by crushing one kilogram of date palm seeds and grinding the seeds, which was a challenging task. Subsequently, an effort was made to devise a method for reaching the nanoscale, but sadly, it was limited to 150 micrometer mesh size. Therefore, after using the meshing approach, around 200 g of the appropriate size are obtained; this means that a better grinder would be required even if the nano level were to be attempted. Second, it can be challenging to determine the optimal resin-to-hardener ratio; nevertheless, after considerable experimentation with several ratios, the optimal ratio of 1:1 was found. Additionally, it is decided to quantify the proportion of date palm seed powder in grams. Thus, a fixed quantity of 100 g is established, meaning that we will replace 5 g of date palm powder for the 5 percent, 5 g for the 10 percent, and so on.
Third, put together four cups with the ratio marked on them. In order to guarantee that the resin, hardener, and date palm seed powder are well blended, the mixture is first produced by hand using a handcrafted mixer. For the 5 percent, the measurements are 47.5 g of resin, 47.5 g of hardener, and 5 g of date seed powder. Ten grams of date seed powder, forty-five grams of hardener, and forty-five grams of resin make up the 10 %. There are 42.5 g of resin, 42.5 g of hardener, and 15 g of date seed powder in the 15 percent. 40 g of resin, 40 g of hardener, and 20 g of powdered date seed are utilized for the 20 percent. Lastly, use clearly defined written markings to identify the samples as you pour each percentage combination into the mold. Then, the samples ae left for 24 h in order to solidify.
Fig. 7Date palm seeds powder after grinding (on the left) and after doing the meshing process (on the right) [25]
![Date palm seeds powder after grinding (on the left) and after doing the meshing process (on the right) [25]](https://static-01.extrica.com/articles/23798/23798-img7.jpg)
2.3. Wear test
The Pin-on-Disc devices seem to be easy to operate and have the ability to gauge wear resistance. An indenter or pin, usually spherical in form or flat, is pushed onto a test sample in the Pin-on-Disc measuring process. When the test sample rotates, the engagement mechanism precisely provides a force to the indenter. A strain gauge sensor is used to detect the resultant friction forces. Material lost during the test is used to compute wear coefficients for the sample and pin. The wear resistance, lubricity, and adhesion characteristics of a coating may all be ascertained by pin-on-disc testing. The pin may roll more easily over a surface with a low coefficient of friction and high lubricity, which reduces material loss and improves wear resistance. A coating with inadequate adhesion, on the other hand, would be stretched by the pin and cause coating loss and coating bond failure. Insufficient wear resistance would result even if the coating were hard. In present work, a pin-on-disc machine that was accessible in the Umm Al-Qura University workshop was used , even though the basic approach of the test was already specified. The stationary pins were cuboid-shaped specimens, and the horizontally rotating counter body was constructed from Emery sheets securely bound to large steel discs [23]. Fig. 8 shows a schematic representation of the investigation's test setup.
Fig. 8Schematic diagram of the used pin-on-disc device
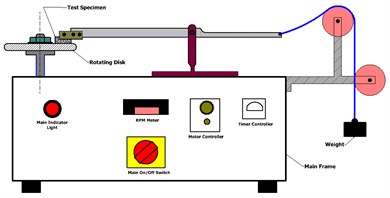
2.4. Hardness test
Indentation hardness tests are used in mechanical engineering to evaluate a material's ability to withstand plastic deformation (the permanent change in shape of a material caused by mechanical stress, comparable to what happens when you hit a piece of wood with a hammer). In order to conduct a hardness test, two materials with known mechanical characteristics and the material of interest with unknown attributes are often brought into contact. The hardness test a diamond or steel used element A and is able to permanently scratch element B, then element A is ranked harder than element B. Improvements like Brinell, Knoop, Vickers, and Rockwell were added later, but the basic idea remained the same. These tests are categorized into three categories based on the length scale of the penetration: macro, micro, and nanoindentation. The penetration length is expressed in millimeters, micrometers, and nanometers, respectively. A generalized schematic representation of the hardness test is shown in Fig. 9 [24]. Owing to its benefits, it is frequently used to forecast or estimate a range of mechanical properties, including fatigue limit, fracture toughness, ultimate tensile strength, and tensile yield strength.
Fig. 9Schematic diagram of a) the hardness tester and b) test mechanism
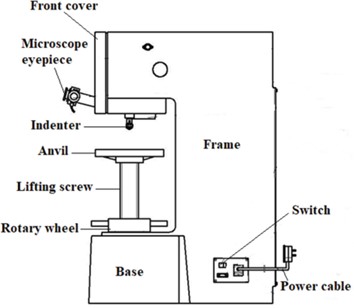
a)
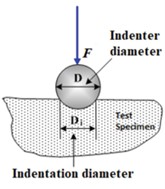
b)
3. Results and discussion
3.1. Weight losses
The amount of weight loss brought on by friction between the sample’s surface and a harder surface is known as the wear rate. Prior to the test, the specimen weighed 15.261 g for samples with a 5 percent powder content. spinning at five different speeds and beginning with a loading weight of 1 kg. Table 2 shows that at a load of 1 kg, the weight reduction for the five speeds is 15.261 – 14.711 = 0.055 g.
Table 2Weight losses of samples has 5 % of the date palm seed powder
1 kg | Speed (RPM) | 200 | 250 | 300 | 350 | 400 |
Weight (g) | 15.152 | 15.113 | 15.068 | 14.917 | 14.711 | |
2 kg | Speed (RPM) | 350 | 400 | 450 | 500 | 550 |
Weight (g) | 14.553 | 14.341 | 13.972 | 13.584 | 13.041 | |
3 kg | Speed (RPM) | 400 | 450 | 500 | 550 | 600 |
Weight (g) | 12.714 | 12.393 | 12.001 | 11.657 | 11.291 | |
4 kg | Speed (RPM) | 450 | 500 | 550 | 600 | 650 |
Weight (g) | 11.096 | 10.552 | 9.911 | 9.239 | 8.613 |
Similarly, the weight loss for the four speeds with a load of 2 kg was determined to be 14.711 – 13.041 = 0.167 g, 13.041 – 11.291 = 1.75 g for a load of 3 kg, and 11.291 – 8.613 = 2.678 g for a load of 4 kg.
Fig. 10Relationship between weight loss with load weight change at 5 % date palm seed
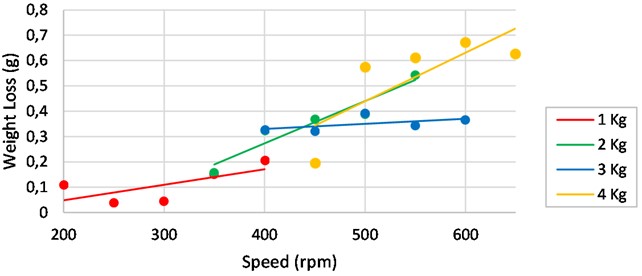
Fig. 11Relationship between weight loss with load weight change at 5 % date palm seed (with oil)
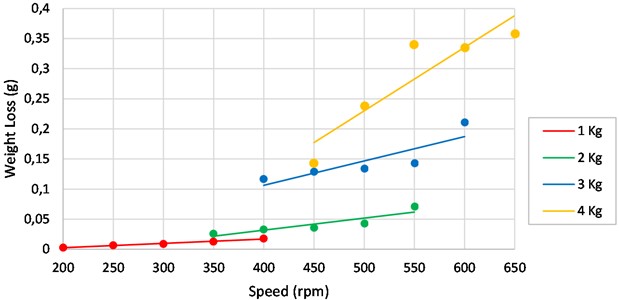
The specimen containing 10 % date palm seed powder weighed 14.752g prior to the test's commencement, and there were five possible rates at which to apply the initial load of 1 kg. With a load of 1 kg, as shown in Table 3, the weight reduction for the five speeds is 14.752 – 14.294 = 0.458 g.
Table 3Weight losses of samples has 10 % of the date palm seed powder
1 kg | Speed (RPM) | 200 | 250 | 300 | 350 | 400 |
Weight (g) | 14.684 | 14.645 | 14.614 | 14.495 | 14.294 | |
2 kg | Speed (RPM) | 350 | 400 | 450 | 500 | 550 |
Weight (g) | 14.068 | 13.897 | 13.678 | 13.418 | 13.103 | |
3 kg | Speed (RPM) | 400 | 450 | 500 | 550 | 600 |
Weight (g) | 12.85 | 12.602 | 12.402 | 12.201 | 11.765 | |
4 kg | Speed (RPM) | 450 | 500 | 550 | 600 | 650 |
Weight (g) | 11.326 | 10.902 | 10.283 | 9.653 | 9.003 |
Similarly, in the case of a load of 2, 3, and 4 kg, the weight loss at the five speeds was determined to be 14.294 – 13.103 = 0.191 g, 13.103 – 11.765 = 1.338 g, and 11.765 – 9.003 = 2.762 g, in that order.
The specimen's weight was 6.315 g prior to the test when 15 % of the date palm seed powder samples were examined. beginning with one kilogram and progressing at five distinct rates. For the five speeds at 1 kg, the weight loss is 6.315 – 5.57 = 0.745 g; for the five speeds at 2 kg, it is 5.57 – 4.752 = 0.818 g; for the load of 3 kg, it is 4.752 – 3.019 = 1.733 g; and for the load of 4 kg, it is 3.019 – 1.068 = 1.951 g.
Fig. 12Relationship between weight loss with load weight change at 10 % date palm seed
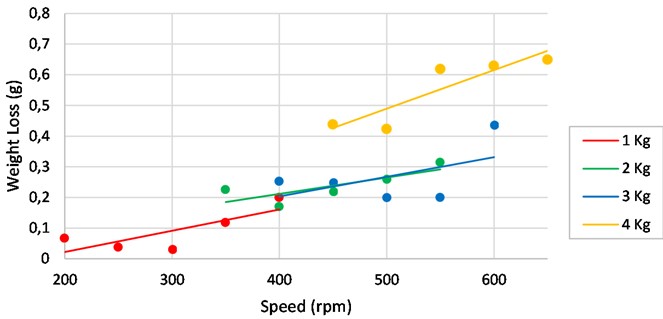
Fig. 13Relationship between weight loss with load weight change at 10 % date palm seed (with oil)
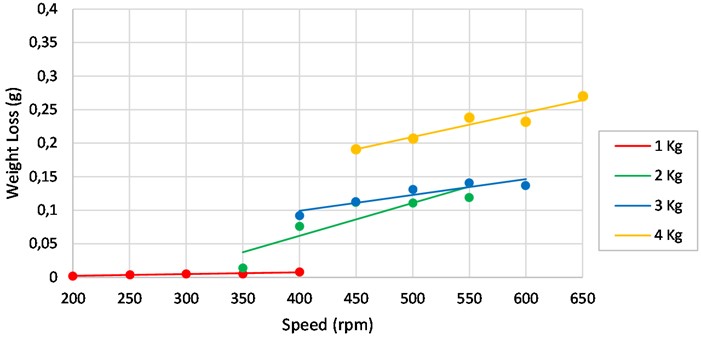
Fig. 14Relationship between weight loss with load weight change at 15 % date palm seed
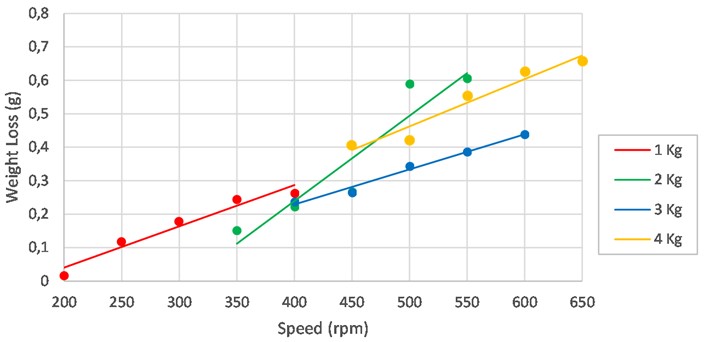
The specimen weight for the 20 percent date palm seed powder package was 13.363 g before the test began. beginning with one kilogram and progressing at five distinct rates. With a 1 kg load, the weight reduction for the five speeds is 13.363 – 12.955 = 0.408 g; with a 2 kg load, it is 12.955 – 12.213 = 0.742 g; with a 3 kg load, it is 12.213 – 11.059 = 1.154 g; and with a 4 kg load, it is 11.059 – 9.403 = 1.656 g.
Fig. 15Relationship between weight loss with load weight change at 15 % date palm seed (with oil)
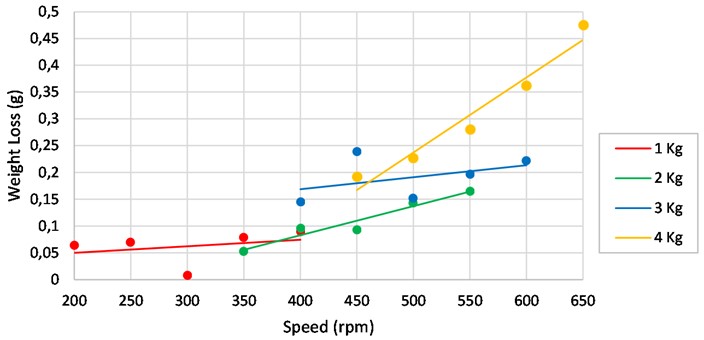
Fig. 16Relationship between weight loss with load weight change at 20 % date palm seed
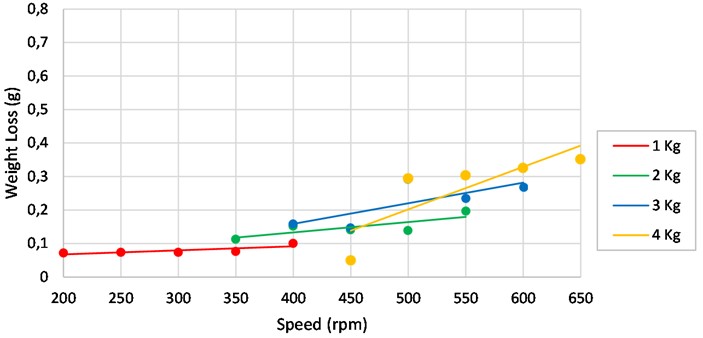
Fig. 17Relationship between weight loss with load weight change at 20 % date palm seed (with oil)
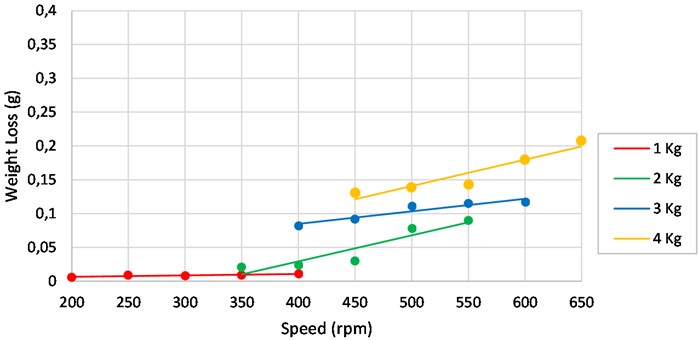
3.2. Cumulative weight loss
It is evident that the cumulative weight loss rises with increasing load and speed. For the sample of the five percent date palm seed, the weight loss is as follows: 0.55 g at first, 1.67 g, 1.75 g for the third load, and 2.678 g for the fourth load. This adds up to a total loss of 6.648 g. Table 4 shows the load procedure from start to finish for every load. Furthermore, Fig. 18 shows a schematic of the date palm seed (5 percent) that illustrates how speed and weight loss are related.
Table 4Four different weights at five different speeds for each, for the 5 % of date palm seed
5 % (Mass = 15.261 g) | ||||
Weight load (kg) | 1 | 2 | 3 | 4 |
Speed (RPM) | ||||
200 | 15.152 | |||
250 | 15.113 | |||
300 | 15.068 | |||
350 | 14.917 | 14.553 | ||
400 | 14.711 | 14.341 | 12.714 | |
450 | 13.972 | 12.393 | 11.096 | |
500 | 13.584 | 12.001 | 10.522 | |
550 | 13.041 | 11.657 | 9.911 | |
600 | 11.291 | 9.239 | ||
650 | 8.613 | |||
700 | ||||
750 |
Fig. 18Relationship between speed and weight loss for samples containing 5 % date palm seeds
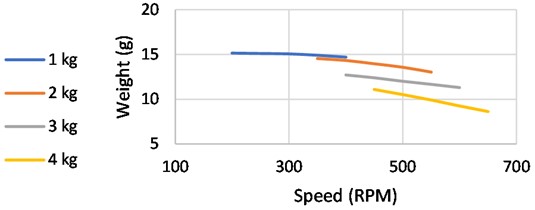
The weight declined after that, initially increasing to 1.191 g, then decreasing to 0.458 g. 1.338 g is the third load, while 2.762 g is the fourth. This is noteworthy as the sample with 10 % date palm seed lost 5.749 g in total. A flowchart of 10 % date palm seed showing the connection between speed and weight reduction is shown in Fig. 19.
Fig. 19Relationship between speed and weight loss for samples containing 10 % date palm seeds
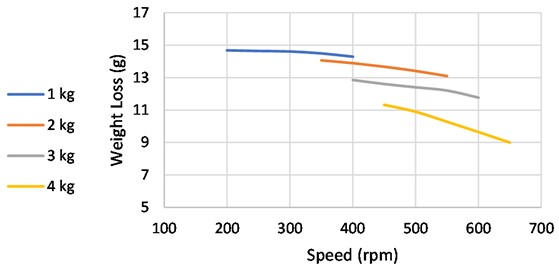
After the 15 percent, the weight loss started at 0.818 g and then climbed to 1.833 g. 1.668 g makes up the third load, while 2.664 g makes up the fourth. This accounts for the variation, as the sample's total loss for the 15 % date palm seed is 6.983 g. A graphic of the 15 % of date palm seeds in Fig. 20 illustrates the relationship between weight loss and speed.
After the twenty percent drop, the weight decreases from 0.398 g to 0.742 g. The fourth weight weighs 1.327 g, while the third load weighs 1.101 g. This is significant since the sample of date palm seeds that had a 20 percent loss totaled 3.568 g. The relationship between speed and weight reduction with 20 % date palm seed is shown in Fig. 21.
Fig. 20Relationship between speed and weight loss for samples containing 15 % date palm seeds
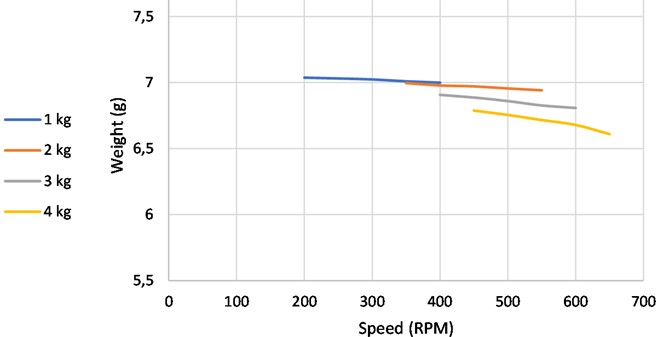
Fig. 21Relationship between speed and weight loss for samples containing 10 % date palm seeds
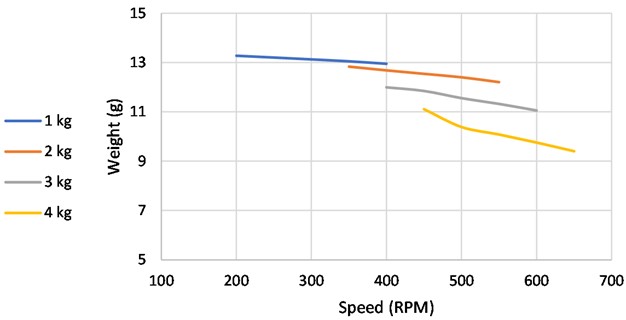
Fig. 22Vickers microhardness using a durometer (shore D) for a 20 % date palm seed samples
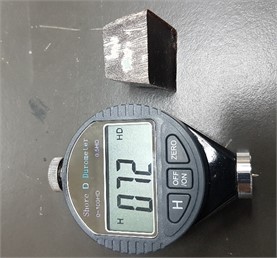
3.3. Hardness test results
By measuring the permanent depth of the indentation, the Vickers hardness test is used to calculate the number indicated as indentation resistance. Put simply, when a consistent force (load) is applied to a certain indenter, the material becomes harder the smaller the indentation. In addition, the Vickers hardness test for soft materials was performed using a durometer (shore D), therefore the used composites were tested using the shore D-type, as shown in Fig. 22.
The results of the hardness test are shown in Fig. 23 and indicate that the sample is harder the more date palm seed there is in it.
Fig. 23Vickers microhardness values with a proportion of date palm seeds
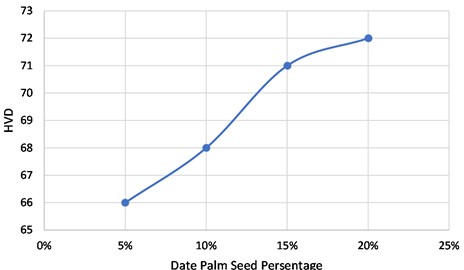
4. Conclusions
Observations show that the 5 percent sample's weight loss has reached 19.95 percent of its initial weight, suggesting that the wear test has eliminated almost one-fifth of the sample’s weight. However, a weight reduction of 9.4 % from the initial weight in the 10 % sample let it perform better in the wear test. This suggests that the date palm seed is giving the material higher wear resistance after it reaches 10 % of its original mass. The results of the weight loss reached 12.2 percent, which was not expected to be lower than the 10 percent sample. It was also found that there are some discrepancies in findings that appear on the 15 percent sample, but this might be related to other circumstances. Ultimately, the 20 percent sample lost 7.03 percent of their starting weight, which was the best result of all. Upon analysis of all tested samples, it was concluded that the date palm seed improved and increased wear resistance to get better results.
References
-
V. Korshak, Technology of Plastics. Moscow: Khimia, 1976, pp. 436–455.
-
Mindlin and S. S., Technology of Polymer Production and Plastics on Their Base. Leningrad: Khimia, 1973, pp. 287–349.
-
Bryan Ellis, Chemistry and Technology of Epoxy Resins. Dordrecht: Springer Netherlands, 1993, https://doi.org/10.1007/978-94-011-2932-9
-
Soo-Jin Park and Min-Kang Seo, Interface Science and Technology. Elsevier, 2011.
-
Amit Bandyopadhyay and Susmita Bose, Characterization of Biomaterials. Elsevier, 2013.
-
P. Valášek, A. Ruggiero, and M. Müller, “Experimental description of strength and tribological characteristic of EFB oil palm fibres/epoxy composites with technologically undemanding preparation,” Composites Part B: Engineering, Vol. 122, pp. 79–88, Aug. 2017, https://doi.org/10.1016/j.compositesb.2017.04.014
-
R. K. Abdel-Magied, M. F. Aly, and H. I. Elkhouly, “The effect of fiber orientation on wear behavior of glass fiber-epoxy filled with particles,” Industrial Lubrication and Tribology, Vol. 70, No. 8, pp. 1552–1559, Nov. 2018, https://doi.org/10.1108/ilt-09-2017-0277
-
W. Abid, S. Magdich, I. B. Mahmoud, K. Medhioub, and E. Ammar, “Date palm wastes co-composted product: an efficient substrate for tomato (Solanum lycopercicum L.) seedling production,” Waste and Biomass Valorization, Vol. 9, No. 1, pp. 45–55, Jan. 2018, https://doi.org/10.1007/s12649-016-9767-y
-
T. Alsaeed, B. Yousif, and H. Ku, “The potential of using date palm fibres as reinforcement for polymeric composites,” Materials and Design, Vol. 43, pp. 177–184, Jul. 2012, https://doi.org/10.1016/j.matdes.2012.06.061
-
K. A. Iyer and J. M. Torkelson, “Green composites of polypropylene and eggshell: effective biofiller size reduction and dispersion by single-step processing with solid-state shear pulverization,” Composites Science and Technology, Vol. 102, pp. 152–160, Oct. 2014, https://doi.org/10.1016/j.compscitech.2014.07.029
-
V. Mittal, A. U. Chaudhry, and N. B. Matsko, ““True” biocomposites with biopolyesters and date seed powder: Mechanical, thermal, and degradation properties,” Journal of Applied Polymer Science, Vol. 131, No. 19, pp. 1–7, Oct. 2014, https://doi.org/10.1002/app.40816
-
A. Ruggiero, P. Valášek, and M. Müller, “Exploitation of waste date seeds of Phoenix dactylifera in form of polymeric particle biocomposite: Investigation on adhesion, cohesion and wear,” Composites Part B: Engineering, Vol. 104, pp. 9–16, Nov. 2016, https://doi.org/10.1016/j.compositesb.2016.08.014
-
N. T. Simonassi et al., “Reinforcement of polyester with renewable ramie fibers,” Materials Research, Vol. 20, No. suppl 2, pp. 51–59, May 2017, https://doi.org/10.1590/1980-5373-mr-2016-1046
-
Heba I. Elkhouly, Ragab K. Abdel-Magied, and Mohamed F. Aly, “An investigation of date palm seed as effective filler material of glass-epoxy composites using optimization techniques,” Polymers and Polymer Composites, Oct. 2019.
-
N. Saba, O. Y. Alothman, Z. Almutairi, M. Jawaid, and W. Ghori, “Date palm reinforced epoxy composites: tensile, impact and morphological properties,” Journal of Materials Research and Technology, Vol. 8, No. 5, pp. 3959–3969, Sep. 2019, https://doi.org/10.1016/j.jmrt.2019.07.004
-
H. I. Elkhouly, R. K. Abdel-Magied, and M. F. Aly, “Date palm seed as suitable filler material in glass-epoxy composites,” Iranian Polymer Journal, Vol. 28, No. 1, pp. 65–73, Jan. 2019, https://doi.org/10.1007/s13726-018-0678-6
-
M. K. Hassan, M. Y. Abdellah, T. S. Elabiadi, A. F. Mohamed, S. Azam, and W. W. Marzouk, “Essential Work of fracture and size effect in copper/glass-reinforced epoxy laminate composites used as MEMS devices,” American Journal of Mechanical Engineering, Vol. 5, No. 5, pp. 234–238, Dec. 2017, https://doi.org/10.12691/ajme-5-5-7
-
M. Y. Abdellah, “Essential work of fracture assessment for thin aluminium strips using finite element analysis,” Engineering Fracture Mechanics, Vol. 179, pp. 190–202, Jun. 2017, https://doi.org/10.1016/j.engfracmech.2017.04.042
-
Y. Mohammed, M. K. Hassan, A. El-Ainin H., and A. M. Hashem, “Effect of stacking sequence and geometric scaling on the brittleness number of glass fiber composite laminate with stress raiser,” Science and Engineering of Composite Materials, Vol. 21, No. 2, pp. 281–288, Mar. 2014, https://doi.org/10.1515/secm-2013-0038
About this article
The authors have not disclosed any funding.
The datasets generated during and/or analyzed during the current study are available from the corresponding author on reasonable request.
The contribution is equally for both authors.
The authors declare that they have no conflict of interest.