Abstract
Fuel cell air filter can absorb harmful impurities and gases to fuel cell and is an important component to ensure the service life of fuel cell. The previous researches mainly focus on the activated carbon and filter paper materials in the laboratory. The object of this paper is the fuel cell air filter product assembly being used by the main engine plant. According to the tests of air filters with different carbon contents, it was found that the adsorption efficiency of current products for NO2 was better than that of C7H8, SO2 and C4H10. Based on the adsorption mechanism of activated carbon for different gases, the adsorption difference was explained. The testes also found that there was no direct relationship between the change of carbon content of products containing activated carbon and the fractional filtration efficiency. The main reason is that the gap between the activated carbon particles is large, which cannot effectively intercept dust particles. The filtering of small size particles still depends on the melt-blown layer material in the air filter element and its electrostatic electret process. It was also found that there was a positive correlation between inlet air resistance and carbon content, and a negative correlation between dust holding capacity and carbon content. This test results can help the main engine factory understand the performance and improvement direction of products.
1. Introduction
The development of hydrogen fuel cell vehicles (the fuel cells in this paper refer to hydrogen fuel cells using proton exchange membranes) is an important technical way to achieve carbon neutralization in transportation. One of the reasons that seriously hinder its development is that the durability and reliability of fuel cells cannot meet the requirements of application. The development of air filters that meet the requirements of fuel cell vehicles can effectively extend the life of fuel cells. As the proton exchange membrane fuel cell (PEMFC) directly uses ambient air as the cathode oxidation gas, particles in the air may block the fuel cell plate, and harmful gases in the air (such as SO2, NH3, NOx, etc.) may cause the decline of the battery system, or even permanent damage to the proton exchange membrane. As a result, the air filter shall have the ability to intercept particles and remove harmful impurities. The most commonly used adsorption material in fuel cell air filter is activated carbon or modified activated carbon. Activated carbon is a typical microporous carbon, which consists of a large amount of unsaturated carbon on the surface, forming a complex pore structure [1]. In addition to the complex structure, the activated carbon also contains rich alkaline and acidic functional groups on the surface of pore channels [2]. The unique physical structure and rich chemical structure constitute the adsorption mechanism of activated carbon for gas.
There are many fuel cell air filters on the market, while the filtration performance of the products is uneven due to the lack of relevant standards for fuel cell air filters at this stage. To this end, this study in this paper has more practical significance for the development of fuel cell air filter.
2. Effect of different carbon contents on the adsorption efficiency of different gases
Through the adsorption efficiency test of three fuel cell air filter products with different carbon contents on nitrogen dioxide, sulfur dioxide, toluene and n-butane, the influence of carbon content of fuel cell air filter on the adsorption efficiency of products is analyzed. The carbon contents of the three tested products were 150 g/m2, 250 g/m2 and 300 g/m2 respectively. The area of the filter element was 0.44 m2; the air volume was 150 m³/h; the concentration of nitrogen dioxide and sulfur dioxide was 30 ppm; the concentration of toluene and n-butane was 80 ppm; the ambient temperature was 23 ℃, and the humidity was 50 % RH. The test shall be terminated when the penetration rate reaches 95 % or the test time reaches 1h.
The calculation of adsorption efficiency is as follows:
where: C1 is the concentration of upstream gas; C2 is the concentration of downstream gas; Penetration rate = 100 % - E.
Determining the zero hour of the test is a key step to measure the zero hour efficiency. Before the test, the gas concentration time curve from the occurrence to the specified concentration without installing the test piece is drawn. The calculation of time 0 is as follows:
where: C0 is the set gas concentration; m is the tangent slope of the curve at point 50 % C0; t50% is the time when the tangent reaches 50 % C0.
Time 0 is determined according to Eq. (2). The corresponding adsorption efficiency of the gas at different times was collected and calculated according to formula (1), and the adsorption efficiency time curve of the four gases under three carbon contents was drawn. The adsorption efficiency time curves of NO2, SO2, C7H8 and C4H10 are shown in Figs. 1-4 respectively.
Fig. 1NO2 adsorption efficiency-time curve
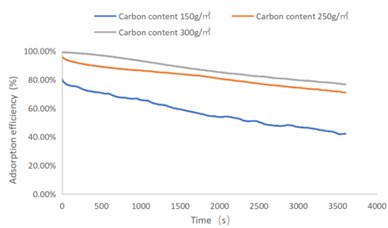
Fig. 2SO2 adsorption efficiency-time curve
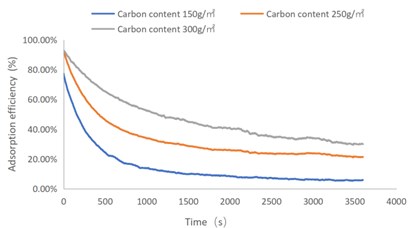
Fig. 3C7H8 adsorption efficiency-time curve
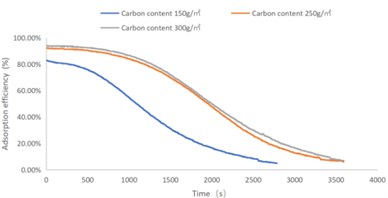
Fig. 4C4H10 adsorption efficiency-time curve
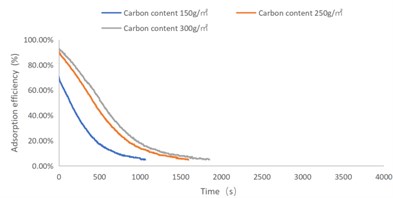
As shown in Figs. 1-4, there are the following rules: 1) As the carbon content increases, the efficiency of the test product at time 0 increases, and the product efficiency for terminating the test at 1h for NO2 and SO2 has also improved. For C7H8 and C4H10, the penetration time of the tested gas is also extended; 2) The absorption efficiency of the products for NO2 and C7H8 is better than SO2 and C4H10; 3) The absorption efficiency of NO2 declines the slowest, and the attenuation curve is close to linear change, followed by toluene, sulfur dioxide and n-butane. The accuracy of SO2and NO2 gas concentration test instrument used in this test can reach 1 ppb, and that of C7H8and C4H10 gas concentration detector can also reach 0.1 ppm. They have been calibrated before the test and can effectively ensure the accuracy of the test results. The reasons are: First, as the activated carbon content increases, more substances are available for gas adsorption and the adsorption efficiency of the products at time 0 is improved. As for the NO2 adsorption efficiency curve, the adsorption of activated carbon on NO2 is a combination of physical adsorption and chemical adsorption. The micropore volume and the number of surface oxygen containing groups are considered to be the key factors affecting NO2 adsorption [3]. Under the combined action of the two, the adsorption curve of NO2 presents a stable linear attenuation, and its adsorption capacity is also better than other gases. The adsorption of SO2 by activated carbon should be mainly chemical adsorption, supplemented by physical adsorption. This is also consistent with Wang et al. [4]. Because the chemisorption is mostly single-layer adsorption, the chemisorption will be quickly neutralized by high concentration SO2 in the early stage of the test. Its adsorption efficiency curve will decline rapidly. After reaching a certain time, the physical adsorption will play a leading role, which makes SO2 adsorption curve gradually become stable under the combined action of chemical adsorption. As for the adsorption curve of C7H8, the physical adsorption is the main method. At the early stage of the test, it is mainly the membrane diffusion stage and the pore diffusion stage of activated carbon, which basically maintain the complete adsorption of C7H8.As the outer membrane and inner pore of activated carbon are gradually occupied by C7H8, the adsorption efficiency begins to decline. After a certain period of time, the adsorption of activated carbon on C7H8 reaches the adsorption equilibrium stage, and the adsorption of activated carbon on C7H8 has multilayer adsorption, and gradually reaches an equilibrium state. The activated carbon has the worst adsorption effect on n-butane. The smaller molecular weight and small molecular diameter of n-butane may lead to the unsatisfactory physical adsorption efficiency. Some studies have shown that the main 1.2-2 nm micropores and 2-4 nm mesopores have a great effect on the adsorption of n-butane, and the other pore diameters with large volume will hinder the adsorption of n-butane.
3. Effect of different carbon contents on the fractional filtering effect of air filter
The dust filtering efficiency of the traditional air filter has reached a high level, especially the air filter element that uses the electrostatic electret material [5-6] (to inject electric charge into the melt blown cloth, so that the melt blown cloth is charged with static electricity and kept in this state for a long time). Based on the electrostatic electret materials, the air filters with different carbon contents are tested to study whether the carbon content will further improve the efficiency of fractional filtration.
According to the method of ISO 11155-2 [7], the fractional filtration efficiency test of four different products without carbon, 150 g/m2, 250 g/m2 and 300 g/m2 was carried out under an air volume of 300 m³/h. The area of the product filter element was 0.44 m2; the ambient temperature was 23 ℃, and the humidity was 50 % RH. The test results are shown in Table 1.
As shown in Table 1, as the carbon content increases, the filtration efficiency of air filter products under different particle sizes does not increase significantly. The reason is that the filtering mechanism of air filter products for particles is direct interception, inertial interception and diffusion interception of particles [8]. The gap between activated carbon particles is relatively large, which cannot block the passage of small particles. It can be seen from the curves that the filtration efficiency of the product with a carbon content of 300 g/m2 is even lower than that with a carbon content of 0 g/m2 at a particle size of about 0.3 microns. It may be that under the same process flow, as the carbon content of the product increases, the carbon powder with high content will be crushed by greater extrusion, and a part of the tiny carbon powder particles generated will attach to the filter product. At the beginning of the test, these small particles will enter the downstream of the filter with the air flow, resulting in a slight decline in its filtering efficiency. This also reminds product designers to take into account the strength of activated carbon particles when selecting activated carbon, instead of blindly pursuing the pore volume and porosity of it. The laboratory has tested the efficiency of multistage staged filtration, and the test results were slightly different each time. However, the test results pointed to that there was no absolute relationship between different carbon content and fractional filtration efficiency.
Table 1Fractional filtration efficiency corresponding to different carbon contents
Particle size (μm) | 0 g/m2(%) | 150 g/m2(%) | 250 g/m2(%) | 300 g/m2(%) |
0.34 | 95.53 % | 95.72 % | 96.72 % | 95.43 % |
0.39 | 95.72 % | 95.91 % | 96.91 % | 95.41 % |
0.45 | 96.02 % | 96.11 % | 97.11 % | 97.53 % |
0.52 | 96.34 % | 96.44 % | 97.44 % | 98.99 % |
0.60 | 96.57 % | 96.67 % | 97.67 % | 99.31 % |
0.70 | 97.22 % | 97.03 % | 97.93 % | 99.36 % |
0.81 | 97.56 % | 97.37 % | 98.20 % | 99.38 % |
0.93 | 98.05 % | 97.85 % | 98.35 % | 99.52 % |
1.07 | 98.40 % | 98.21 % | 98.61 % | 99.49 % |
1.24 | 98.57 % | 98.37 % | 98.77 % | 99.59 % |
1.43 | 98.68 % | 98.48 % | 98.88 % | 99.56 % |
1.65 | 98.75 % | 98.65 % | 99.02 % | 99.63 % |
1.91 | 98.97 % | 99.17 % | 99.07 % | 99.57 % |
2.21 | 99.16 % | 99.06 % | 99.26 % | 99.64 % |
2.55 | 99.26 % | 99.36 % | 99.46 % | 99.66 % |
2.94 | 99.28 % | 99.38 % | 99.38 % | 99.62 % |
3.40 | 99.35 % | 99.45 % | 99.45 % | 99.62 % |
3.92 | 99.61 % | 99.51 % | 99.61 % | 99.78 % |
4.53 | 99.58 % | 99.68 % | 99.68 % | 99.81 % |
5.23 | 99.58 % | 99.48 % | 99.51 % | 99.84 % |
6.04 | 99.50 % | 99.40 % | 99.79 % | 99.86 % |
6.98 | 99.66 % | 99.56 % | 99.47 % | 99.86 % |
8.06 | 99.48 % | 99.68 % | 99.48 % | 99.75 % |
9.31 | 99.27 % | 99.47 % | 99.50 % | 99.83 % |
4. Effect of different carbon contents on air inlet resistance and dust holding capacity of air filter
The intake resistance of the fuel cell air filter will affect the power consumption of the vehicle, and excessive resistance will also affect the gas adsorption efficiency. The dust holding capacity of the air filter will determines its service life. The air filter with small dust holding capacity will increase the frequency of product replacement and increase the cost. To more intuitively analyze the impact of different carbon contents on dust holding capacity and resistance, the air filter element of fuel cell air filter is selected for testing. The intake resistance of four products with different carbon content: no carbon, 150 g/m2, 250 g/m2 and 300 g/m2 was tested. The test basis refers to GB/T 32085.1-2015 [9]. The test conditions were set as ambient temperature, humidity 50 % RH, and the flow rate is from 100 m3/h to 600 m3/h.
As shown in Fig. 5, as the carbon content increases, the air inlet resistance increases at the same air volume. The increase of resistance has a strong linear relationship with the increase of carbon content. Part of the drift points in our test results that deviate from the linear relationship should be caused by the inconsistent processing of the filter materials, such as the pre-filter layer, melt blown cloth layer and activated carbon support layer of the air filter element.
The dust holding capacity test was carried out with A2 ash at an air volume of 300 m³/h [10], and the resistance increased by 200 Pa as the termination condition. The test results showed that the dust holding capacity of the four air filter elements without carbon, 150 g/m2, 250 g/m2 and 300 g/m2 was 10.9 g, 10.1 g, 9.3 g and 9.0 g, respectively. With the increase of carbon content, the dust holding capacity decreased. This is because as the activated carbon increases, the resistance of the air filters increases. The higher the carbon content, the greater the increase in resistance caused by the added A2 dust and the faster it will reach the test termination condition of 200 Pa.
Fig. 5Carbon content-resistance curve
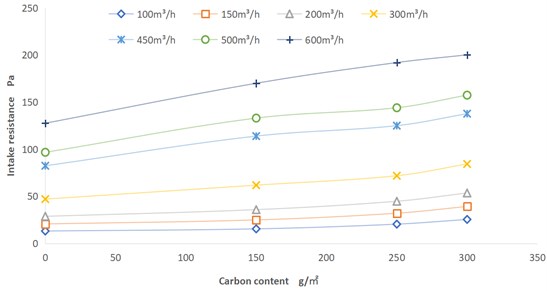
5. Conclusions
1) As the carbon content increases, the adsorption efficiency of the test gas at time 0 has been significantly improved. The adsorption efficiency of fuel cell air filter products for NO2 is better than that of C7H8, SO2 and C4H10.
2) The following views are put forward on the adsorption capacity of fuel cell air filter products to different gases: the adsorption of NO2 by activated carbon is a combination of physical adsorption and chemical adsorption. The adsorption of SO2 is mainly chemical adsorption, supplemented by physical adsorption. The adsorption of C7H8 is mainly physical adsorption, supplemented by chemical adsorption. The poor adsorption effect on C4H10 may be related to the small molecular weight and molecular diameter of n-butane.
3) In the fuel cell air filter products, the change of carbon content has no significant effect on the fractional filtration efficiency of air filter products. In the case of high carbon content, the broken activated carbon particles may occur, causing some small particle size harmful impurities to enter the downstream of the air filter with the air flow. It is suggested that certain strength of activated carbon should be selected when designing products, instead of blindly pursuing the parameters such as specific surface area to improve the adsorption performance of activated carbon.
4) The air inlet resistance of the air filter element basically has a linear relationship with the carbon content, while the dust holding capacity of the product has a negative correlation with the carbon content.
References
-
W. N. Gao, J. M. Zhang, and K. Sun, “Adsorption principle of benzene on activated carbon fiber and its prospect,” (in Chinese), Gansu Science and Technology, Vol. 25, No. 5, pp. 30–31, 2009, https://doi.org/10.3969/j.issn.1000-0952.2009.05.012
-
M. A. Fulazzaky, “Study of the dispersion and specific interactions affected by chemical functions of the granular activated carbons,” Environmental Nanotechnology, Monitoring and Management, Vol. 12, p. 100230, Dec. 2019, https://doi.org/10.1016/j.enmm.2019.100230
-
M. Jeguirim, M. Belhachemi, L. Limousy, and S. Bennici, “Adsorption/reduction of nitrogen dioxide on activated carbons: Textural properties versus surface chemistry – A review,” Chemical Engineering Journal, Vol. 347, pp. 493–504, Sep. 2018, https://doi.org/10.1016/j.cej.2018.04.063
-
Z. Q. Wang, J. J. Zhang, X. C. Liu, and W. F. Jin, “Study on adsorption kinetics model of modified activated carbon on SO2 with low concentration,” Inorganic Chemicals Industry, Vol. 54, No. 9, pp. 69–76, 2022, https://doi.org/10.19964/j.issn.1006-4990.2021-0721
-
X. Yang et al., “Multifunctional composite membrane based on BaTiO3@PU/PSA nanofibers for high-efficiency PM2.5 removal,” Journal of Hazardous Materials, Vol. 391, p. 122254, Jun. 2020, https://doi.org/10.1016/j.jhazmat.2020.122254
-
S. Wang, X. Zhao, X. Yin, J. Yu, and B. Ding, “Electret polyvinylidene fluoride nanofibers hybridized by polytetrafluoroethylene nanoparticles for high-efficiency air filtration,” ACS Applied Materials and Interfaces, Vol. 8, No. 36, pp. 23985–23994, Sep. 2016, https://doi.org/10.1021/acsami.6b08262
-
“ISO 11155-2, Road vehicles-Air filters for passenger compartments Part 2: Test for gaseous filtration,” 2009.
-
F. Q. Wu and H. R. Zhong, “Discussion on the Air Filter for FCEV,” Automobile Parts, Vol. 12, pp. 60–64, 2019, https://doi.org/10.19466/j.cnki.1674-1986.2019.12.014
-
“GB/T 32085.1-2015, Cabin air filter Part 1: Test for particulate filtration,” National Standards of the People’s Republic of China, 2015.
-
“ISO 12103-1, Road vehicles-Test contaminants for filter evaluation – Part 1: Arizona test dust,” 2016.
About this article
The authors have not disclosed any funding.
The datasets generated during and/or analyzed during the current study are available from the corresponding author on reasonable request.
The authors declare that they have no conflict of interest.