Abstract
Due to the emergence of new technologies that make it possible to obtain hydrogen from associated petroleum gas, it has become necessary to store and transport it. As a solution to this problem, the possibility of hydrogen transportation as a methane-hydrogen mixture was considered, i.e. natural gas with a certain hydrogen content. The article considers the issues of methane-hydrogen mixture (MHM) transportation through existing main gas pipelines at various percentages of hydrogen to natural gas. As an example, the Urengoyskoye field was chosen, where it is possible to produce hydrogen from the associated gas of gas condensate fields, and a section of the Novopskovskiy corridor, through which it is possible to transport MHM. In the work, the influence of the hydrogen content in the methane-hydrogen mixture on the gas-dynamic characteristics of the pipeline, mainly on the pressure and throughput capacity of gas in the pipeline, as well as the influence of its content on the operating mode of the compressor station and the power of the gas turbine, when using MHM for the station's own needs, was studied. The obtained results show an insignificant effect of the hydrogen percentage in the mixture on the pressure and throughput of the gas pipeline, which is a weighty argument in favor of the possibility of transporting hydrogen through existing gas pipelines.
1. Introduction
Since 2020, decarbonization has begun to transform from a trend into a category of strategic goals. It has become part of the large-scale and ambitious plans of the world’s largest economies to move towards carbon neutrality. In the Energy Strategy of the Russian Federation until 2035, approved in June 2020, the development of hydrogen energy is indicated as one of the priority areas.
Hydrogen energy is one of the ways to achieve carbon neutrality. The essence of hydrogen energy is the use of hydrogen as a fuel in a variety of machines and devices, primarily in internal combustion engines.
The Rosneft Joint Research and Development Center RN-JRDC, which is part of Rosneft, has developed an innovative methane aromatization technology. The new technology makes it possible to simultaneously produce hydrogen and aromatic petrochemicals from natural and associated petroleum gas (APG) [7].
The developed technology makes it possible to obtain 1 billion m3 of hydrogen and 0.5 million tons of aromatic hydrocarbons (benzene, toluene) by processing 1 billion m3 of natural gas and/or APG.
The advantages of the technology are the reduction of carbon dioxide emissions, the reduction of specific capital costs, the increase in product yield and economic efficiency.
The new technology can be considered as a promising alternative to existing methods for producing hydrogen and synthetic hydrocarbons.
2. Problems of hydrogen transportation and storage
One of the main problems of hydrogen energy is the need to store and transport large volumes of hydrogen.
For the purposes of hydrogen storage, the most appropriate solution is underground storage in existing natural gas storage facilities or in purpose-built hydrogen storage facilities.
Hydrogen can be transported to the place of its use in gaseous or liquid states, as well as using solid or liquid carriers that contain hydrogen in bound form [1].
Pipelines with large wall thicknesses, as well as internal lining and several layers of external protective insulation, such as those used for the construction of deep-sea gas pipelines, can be used to transport hydrogen [4].
The first main hydrogen pipeline was put into operation in 1938 in Germany (Table 1). This pipeline has been used for more than half a century without any accidents [10]. There are currently about 16,000 km of hydrogen pipelines in the world. The longest, 400 km, connects Antwerp and Normandy [2]. In the USA, Germany, England, France and other countries, hydrogen pipelines with a length of 200...300 km under a pressure of 0.5...3 MPa and higher are used [2].
In the United States, major hydrogen producers such as Air Products, Praxair, Air Liquide, BOC Group supply most of it through a pipeline system. And in those areas where there is no access to the pipeline, special vehicles (cryogenic tanks) are used [8].
Table 1Operating hydrogen pipelines
Company | Location | Throughput capacity, m3/day | Length, km | Diameter, m | Pressure, MPa | Years of commissioning |
Praxair | Texas New Jersey Indiana | 2830 170 140 | – | 0,2 | – | 1970 |
Air products | Texas Louisiana | 1130 850 | 200 | 0,1…0,3 | 0,34…5,52 | 1970 |
ChemischeWerk Huls | Germany | 2830 | 220 | 0,1…0,3 | 2,48 | 1938 |
ICI, Teeside | England | 566 | 16 | – | 5,17 | 1970 |
Air Liquide | France, Belgium | 480 | 340 | 0,1 | 10,14 | 1980 |
Shell Canada | Scottford, AB | 2490 | 9 | 0,8 | 0,45 | 2002 |
It should be noted that for all the years of hydrogen pipeline systems operation in North America and Europe, there have been no problems associated with hydrogen embrittlement and safety [9].
The rational pressure for the main transportation of hydrogen, taking into account its physicochemical properties, is 7...14 MPa [6], for example, in the USA, hydrogen pipelines operate at a pressure of 3.5...10 MPa [5].
The cost of special hydrogen gas pipelines is quite high. The highest costs are for expensive materials and account for approximately 70 % of the construction cost.
Thus, of the most important tasks of the formation and development of hydrogen energy is the development of new technologies for transporting hydrogen through pipelines over long distances. The transport aspect of the problem is practically at the initial stage of development. There are not many proposals in the technical literature on how to transport hydrogen through gas pipelines.
Of course, in the world practice, a certain experience has been accumulated in the creation and operation of special pipelines for the transportation of gaseous hydrogen, however, promising and attractive in all respects is the idea to use the existing network of main gas pipelines for transportation of hydrogen in the form of methane-hydrogen mixture.
The article considers the possibility of transporting hydrogen through the existing pipeline system as a methane-hydrogen mixture, as well as the mode of operation of the compressor station. In this case, the compressor station, using the pumped gas as fuel for gas turbine plants, will operate on a methane-hydrogen mixture.
Hydrogen, having a low density, is difficult to compress, which has a significant impact on the pumping mode. The article discusses various percentages of natural gas and hydrogen in the mixture.
3. Results of calculations
The Urengoy-Novopskov pipeline section was taken as an example. Hydrogen is added to the gas transported from the Urengoy field, resulting in the formation of MHM (various percentages are considered).
The physical parameters of the gas are determined by the rule of additivity and depend on the amount and percentage of the components that make up its composition. The gas density under standard conditions (293K and 0.101325 MPa) is determined as:
where ai – the share of each component in the mixture for a given gas composition; ρsti – the density of the component under standard conditions, kg/m3.
Similarly, other parameters are determined, such as molar mass and pseudocritical pressure and temperature, which, in turn, affect the compressibility coefficient of the pumped methane-hydrogen mixture.
Therefore, in the course of the work, a refined thermal and hydraulic calculation of the pipeline was performed for different percentage contents of hydrogen in the mixture.
Change in the parameters of the pumped gas depending on the increase in the amount of added hydrogen is presented in Table 2.
Table 2MHM parameters depending on the percentage of hydrogen
Percentage of hydrogen introduction into the mixture, % | MHM density under standard conditions, kg/m3 | The compressibility coefficient of the resulting mixture at the operating pressure in the pipeline |
0 | 0,763 | 0,795 |
5 | 0,729 | 0,808 |
10 | 0,696 | 0,820 |
15 | 0,662 | 0,833 |
20 | 0,628 | 0,846 |
30 | 0,561 | 0,870 |
40 | 0,494 | 0,894 |
The following tasks were set:
1. Determine how the hydraulic characteristics of the gas pipeline will change at different values of hydrogen concentration in the mixture, determine the pressure in the pipeline and establish the suitability of the existing pipeline system for pumping MHM.
2. Determine the change in compressor station operating modes, the capacity of the gas compressor unit and gas consumption for the station's own needs during pumping through the MHM pipeline.
Fig. 1 shows graphs of pressure changes in the gas pipeline in the section between compressor stations at various percentages of hydrogen in the methane-hydrogen mixture.
Pressure at each point of the pipeline is determined by the formula:
where Ps – the pressure at the beginning of the gas pipeline, MPa; Q – throughput capacity, m3/day; ∆ – relative density; λ – friction resistance coefficient; Zav – average compressibility coefficient; Tav – average temperature; x – distance from compressor station; K – coefficient of heat transfer, W/(m2·K); D – pipeline diameter, m.
As can be seen from the graphs, with an increase in the hydrogen content in the mixture, the pressure in the gas pipeline increases, which indicates a decrease in friction pressure losses, compared with the transportation of pure natural gas.
Fig. 1Change in pressure in the gas pipeline at various concentrations of hydrogen
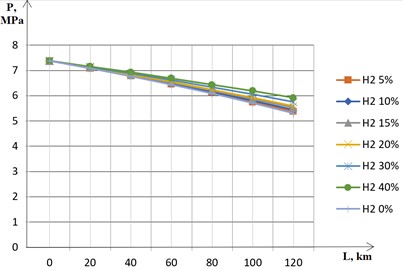
To solve the second problem, the operating modes of the compressor station equipped with GPA-16R gas compressor units (GCU) were considered, and the change in the gas-turbine unit indicator power was determined.
The efficiency of the gas compressor unit is determined by the formula:
where ηgcu is the effective efficiency of the GCU; ηpol polytropic efficiency of centrifugal compressor.
To determine the efficiency indicators of gas turbine unit, namely the effective efficiency of gas turbines, the change in the internal or indicator power of centrifugal supercharger was considered (Table 3):
where kk-1 is the pseudoisentropic index; zav – average value of the MHM compressibility factor; T2n, T1n – gas temperature at the inlet and outlet of the group (centrifugal supercharger), K; Gn – mass productivity of centrifugal supercharger, kg/s; qn – commercial productivity of centrifugal supercharger, million m3/day; R – gas constant, kJ/kg·K.
The effective power on the drive shaft, Ne, is equal to the ratio of the internal power to the mechanical efficiency, and the effective efficiency of the gas turbine is determined by the formula:
where Ne is the effective power on the drive shaft, kW; GT – fuel gas mass flow rate, kg/s, Qnm – actual mass net calorific value of MHM, kJ/kg.
Table 3Change in the indicator power of the gas turbine at various concentrations of hydrogen in the MHM
Percentage of hydrogen introduction into the mixture, % | Indicator power of gas-turbine unit, kW |
0 | 12883,5 |
10 | 11664 |
20 | 10454 |
30 | 9883,9 |
40 | 8118,1 |
4. Conclusions
The performed calculations show that methane-hydrogen mixtures obtained from methane by adding hydrogen to it in a volume of up to 40 % change the gas parameters within acceptable limits, which are of decisive importance for its transportation through main gas pipelines. This conclusion confirms the statement that the existing main gas pipelines can be used to transport hydrogen as a methane-hydrogen mixtures. Hydrogen transportation also has the advantage that centrifugal superchargers of compressor stations, in which the compression ratio is proportional to density gas, are able to provide sufficient pressure for pumping. At the same time, the continuous compression of the lighter hydrogen with sufficient flow would cause technical difficulties.
According to the results obtained in [3], it can be seen that the consumption of the fuel methane-hydrogen mixture decreases, as a result, the effective efficiency of the entire installation remains practically unchanged.
The energy characteristics of gas compressor unit operation as part of the compressor station does not change significantly, which makes it possible to transport MHM through the network of existing main gas pipelines.
The unexplored problems of transporting hydrogen through the system of existing gas pipelines include problems of safety and reliability due to both physical properties the transported medium itself, and because of the phenomenon of metal hydrogenation, which can affect the reliability of the pipeline.
References
-
S. I. Kozlov and V. N. Fateev, Hydrogen Energy: Current State, Problems, Prospects. (in Russian), Moscow, Russian Federation: Gazprom VNIIGAZ, 2009.
-
D. D. Simbeck and E. Chang, “Hydrogen supply: Cost estimates for hydrogen pathways. Scoping analysis,” Mountain View, California: SFA Pasific inc., 2002.
-
S. V. Kitaev, R. R. Farukhshina, and N. M. Darsaliya, “Study of the work of gas turbine engines on methane-hydrogen mixture in the main transport of natural gas,” Transport and Storage of Petroleum Products and Hydrocarbons, No. 3, pp. 52–64, 2022.
-
“Freedom CAR and Fuel partnership,” Hydrogen Delivery Technologies Roadmap, 2005.
-
W. Jasionowski, J. Pangborn, and D. Johnson, “Gas distribution equipment in hydrogen service,” International Journal of Hydrogen Energy, Vol. 5, No. 3, pp. 323–336, 1980, https://doi.org/10.1016/0360-3199(80)90076-2
-
N. F. Dubrovkin, Hydrogen. Properties, Obtaining, Storage, Transportation, Application. Moscow: Chemistry, 1989.
-
“Rosneft develops methane aromatization technologies.” Rosneft official website. https://www.rosneft.ru/press/news/item/203423/
-
“Building Blocks for a Cleaner and Eco-Friendly Heavy-Duty Fleet.” Transpower website. http://transpowerusa.com/zero_emission_solutions/
-
J. M. Ogden, M. Steinbugler, and E. Dennis, “Hydrogen energy systems studies,” Princeton University, 1995.
-
R. Wurster and W. Zittel, “Hydrogen Energy,” Energy technologies to reduce CO2 emissions in Europe: prospects, competition, synergy. Energieonderzoek Centrum Nederland ECN, Apr. 1994.
About this article
The authors have not disclosed any funding.
The datasets generated during and/or analyzed during the current study are available from the corresponding author on reasonable request.
Nana Darsaaliya: conceptualization, data curation, formal analysis, project administration, investigation, writing – original draft preparation. Regina Farukhshina: conceptualization, data curation, formal analysis, investigation, validation, supervision. Zeinab Saddik: writing – software, visualization, review and editing.
The authors declare that they have no conflict of interest.