Abstract
Commercialized polyurethane foam products for automobile steering wheels have been committed to the development of products with comprehensive properties such as low density, high production efficiency and environmental protection. Based on this, this article has launched a series of experiments to explore the effects of different types of chain extenders, blowing agents and catalysts on the mechanical properties, cell structure, skin and reactivity of self-skinning polyurethane foams for automobile steering wheels. The results show that the hardness and tensile strength of the foam gradually decrease with the chain growth of small molecular chain extenders (ethylene glycol, 1.3-propanediol, 1.4-butanediol), and the elongation at break increases gradually. The foaming agent formic acid is more conducive than water as it favors the formation of small but compact cells, thus dense skin. The catalytic efficiency of non-reactive catalysts (A1, KC101 and DabcoEG) is higher than that of reactive catalysts (LED-103, ZR-50, DPA). The theoretical research for the development of high-performance and high-efficiency polyurethane foam products for automobile steering wheels.
1. Introduction
Polyurethane self-skinning foam, also known as integral skin molded foam, is polyurethane foam with a self-skinning structure formed by reaction injection molding [1]. The outer epidermis is a dense layer, and the inner has high resilience [2]. This polyurethane self-skinning foam is comfortable to the touch, and has the characteristics of high environmental protection and no pollution [3]. The material has been used in the mass production of automobile steering wheels in the market.
With the further improvement of the social environment’s requirements for green and healthy products, a number of low volatile organic compounds content polyurethane foams for automobile steering wheels have been developed in recent years. The foams have good mechanical properties, but in terms of foam reactivity, it takes 3~5 min to achieve the curing and molding of the product, which is inefficient in mass production. Therefore, a series of performance experiments were carried out in this paper, which laid a certain foundation for improving the reactivity of polyurethane foam and developing polyurethane foam products with excellent mechanical properties and high reactivity.
Herein, different types of chain extenders, blowing agents and catalysts are used to explore their influence and changing rules on the mechanical properties, cell structure, skin and reactivity of polyurethane foams [4-7]. The main research work includes: the effect of chain extenders ethylene glycol, 1,3-propanediol and 1,4-butanediol on the hardness, tensile strength and elongation at break of polyurethane foam; foaming agents water and formic acid effects on polyurethane foam cells and skin [8-9]; reactive catalystsLED-103, ZR-50, DPA and non-reactive catalystsA1, KC101, DabcoEG effects on the reactivity of polyurethane foam [10-11].
2. Experimental part
2.1. Main experimental materials and equipment
Polyether polyol F3135, modified isocyanate W1631, Wanhua Chemical Group Co., Ltd.; polymer polyolPOP3630, Ningbo Hongyi Chemical Co., Ltd.; chain extender include ethylene glycol, 1,3-propylene glycol and 1,4-butane Diol, Shanghai Aladdin Biochemical Technology Co., Ltd.; Foaming Agent Formic Acid, Sinopharm Chemical Reagent Co., Ltd.; Catalyst LED-103, ZR-50, DPA, A1, Huntsman Polyurethane (China) Co., Ltd.; Catalyst KC101, Nantong Miting Polyurethane Co., Ltd.; Catalyst DabcoEG, Xindian Chemical Materials (Shanghai) Co., Ltd.
Small high-speed dispersing mixer, Anhui Bojin Chemical Machinery Co., Ltd.; Universal Tensile Testing Machine, Taiwan High Speed Rail Testing Instrument Co., Ltd.; Foaming Mould, CangzhouJinzheng Mould Manufacturing Co., Ltd.
2.2. Synthesis of polyurethane foam
The basic formula used in this study is shown in Table 1.
Table 1Basic formula of polyurethane composite for automobile steering wheel
Component | Raw material name | Parts by mass |
A | Polyether polyol F3135 | 70-80 |
Polymer polyol POP3630 | 20-30 | |
Chain extender | 4-8 | |
Catalyst | 0.5-1.5 | |
Foaming agent | 0.3-0.8 | |
B | Modified isocyanate W1631 | 45-55 |
Preparation of component A combined polyether: After weighing 160 g F3135, 40 g POP3630, 10 g chain extender (Ethylene glycol or 1, 3-Propylene glycol or 1, 4-Butanediol), 1.2 g catalyst (LED-103 or Al or ZR-50 or KC101 or DPA or DabcoEG), 1 g foaming agent (formic acid or water), mix and stir evenly.
B component is a modified isocyanate, W1361. Isocyanate index was used to calculate the ratio of the dosage of component A to component B. The calculation formula of isocyanate index R is as follows:
where n(-NCO) represents the amount of -NCO group substance in component B, n(-OH) represents the amount of -OH group substance in component A combined polyether. The R value is usually controlled at 0.95-1.05.
Preparation of polyurethane foam cup foam: According to isocyanate index 1.0, weigh 30 g of component A combined polyether, 15g of component B modified isocyanate W1631, the temperature of component A and B is maintained at (25±2) ℃, the speed of the high-speed disperser is adjusted to 2000 rpm, the B component is quickly poured into component A and stirring for 5-7 s, then poured into 240 ml disposable plastic cup. The foam reactivity (starting time, gel time and debonding time) was observed and recorded.
Preparation of polyurethane foam: According to the isocyanate index 1.0, 45 g of component A combined polyether and 22.5 g of component B modified isocyanate W1631 were weighed. The temperature of component A and B was maintained at (25±2) ℃, the speed of the high-speed disperser was adjusted to 2000 rpm, and component B was quickly poured into component A and stirring for 5-7 s. Pour it into the mold at 60 ℃ (mold size: 300×300×2 mm), close the mold, and release the mold after 3 min to produce the polyurethane foam sample with a density of about 350 kg/m3.
Preparation of automobile steering wheel sample: According to isocyanate index 1.0, weigh 120 g of component A combined polyether, 60 g of component B modified isocyanate W1631, keep the temperature of component A and B at (25±2) ℃, adjust the speed of the high-speed dispersing machine to 2000 rpm, quickly pour component B into component A and stir for 5-7 s, then pour into the mold at 80 ℃. The inner cavity of the mold is an automobile steering wheel structure and contains an aluminum metal skeleton. The mold is closed and demoulded 5 minutes later. The automobile steering wheel sample wrapped by polyurethane foam on the aluminum skeleton is made, as shown in Fig. 1. This photo was taken by Rao Houdong at The Materials Application Development Laboratory of Luoyang Ship Material Research Institute in November 2021.
Fig. 1Automotive steering wheel products made from polyurethane foam
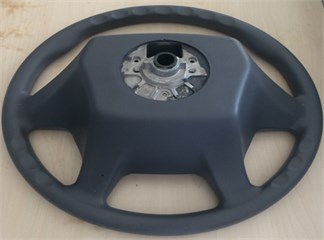
3. Performance test
3.1. Physical performance test
Foam hardness is measured by the method of GB/T 2411-2008; the tensile strength and elongation at break are measured by the method of GB/T 6344-2008; the tear strength is measured by the method of GB/T 10808-2006.
3.2. Foam reactivity test
Using a stopwatch, observe and record the reactivity of polyurethane foam in a disposable plastic cup, including rise time (the time when the foam starts to grow), gel time (the time for the foam to be drawn) and debonding time (the skin does not change after the foam is cured and formed).
4. Results and discussion
4.1. Influence of the type of chain extender on the mechanical properties of foam
Different types of chain extenders have different hydroxyl values. In order to keep the total hydroxyl value of the chain extenders added in the combined polyether unchanged, the addition amount of different types of chain extenders is adjusted accordingly. By changing the types of chain extenders, the foam samples with a density of 350 kg/m3weretested for performance under standard laboratory conditions. The results are shown in Table 2.
As can be seen from Table 2, with the growth of the molecular chain of the chain extender, the hardness and tensile strength of the polyurethane foam gradually decrease, and the elongation at break gradually increases. When the hydroxyl value content of the combined polyether and the isocyanate index keep the same, the content of the hard segment (urethane group generated when the isocyanate reacts with the hydroxyl group) in the molecular chain of the polyurethane foam remain unchanged. While with the chain growth of small molecule chain extender, the spacing of the urethane groups in the hard segment group gradually enlarges, the distribution of the hard segment in the molecular chain changes from centralized to disperse. Meanwhile the more enhanced flexibility of the molecular chain is observed, which indirectly increases the soft segment. Therefore, the hardness and strength of the polyurethane foam gradually decrease, and the elongation at break increases.
Table 2Effect of chain extender types on polyurethane foam properties
Type | Density / (kg/m3) | Shore a hardness | Tensile strength / MPa | Elongation at break / % |
Ethylene Glycol | 350 | 60 | 3.3 | 105 |
1, 3 – Propanediol | 352 | 55 | 2.9 | 130 |
1, 4 – Butanediol | 351 | 53 | 2.1 | 225 |
4.2. Influence of foaming agent types on foam cells and skin
In this part, we mainly compared the influences of foaming agent water and formic acid. After a series of reactions of water molecules and formic acid molecules with isocyanate, both of the two foaming agents can generate 2 carbon dioxide molecules. Therefore, it is necessary to keep the amount of the substance added to the foaming agent constant. By changing the type of foaming agent, a foam sample block with a density of about 350 kg/m3 was obtained, and then the changes of the cells and skin were observed and compared. The results are shown in Table 3.
It can be seen from Table 3 that when foaming with water, the cells of the foam are larger, loosely arranged, and the skin is poor; when foaming with formic acid, the foam of the foam is small and closely distributed, and the skin is relatively dense. Although the amount of CO2 gas produced by the foaming agent water and formic acid is the same, the cell structure is quite different. It could be explained as follows, in the process of combining the polyether, some formic acid and amine catalysts undergo complex reaction to form salts (reversible reaction), with the progress of the polyurethane foam reaction, the complexed formic acid is gradually released, so the generation of CO2 gas is also gradually carried out. Compared with water foaming, the cells are smaller, and the arrangement is tighter. The epidermis is also denser.
Table 3Effect of blowing agent types on cells and skin of polyurethane foam
Type | Density / (kg/m3) | Epidermis | Cell structure |
Water | 348 | Crust is not dense Tactile bias | Cells are too large Loosely arranged |
Formic acid | 352 | Dense crust Good touch | Smaller cells Close distribution |
4.3. Effect of catalyst types on foam reactivity
Keeping the same amount of catalyst, by changing the type of catalyst, mainly compare the reactive catalyst with the non-reactive catalyst, the polyurethane foam cup cells were prepared, and then the reactivity was observed and compared. The results are shown in Table 4.
Table 4Effect of catalyst type on polyurethane foam reactivity
Type | Type | Departure (time/s) | Gel time / s | Debonding (time/s) |
LED-103 | Reactive start-up catalyst | 14 | 26 | 39 |
A1 | Non-reactive start-up catalyst | 10 | 25 | 38 |
ZR-50 | Reactive equilibrium catalyst | 13 | 27 | 42 |
KC101 | Non-reactive equilibrium catalyst | 12 | 24 | 38 |
DPA | Reactive gel catalyst | 12 | 25 | 36 |
DabcoEG | Non-reactive gel catalyst | 12 | 21 | 26 |
It can be seen from Table 4 that in terms of the reactivity of polyurethane foam, the non-reactive catalyst has better effect, and is faster than the reactive catalyst in the rise, gelation and debonding time. Because the molecular chain of the reactive catalyst is introduced. The active hydrogen group can react with the -NCO group in the isocyanate to be combined with the polymer chain of the polyurethane foam. Compared with the free non-reactive catalyst, its reactivity is significantly lower.
However, non-reactive catalysts are more volatile in polyurethane foam products. The introduction of reactive catalysts can effectively reduce the VOC content of polyurethane foams. Therefore, while improving the foam reactivity, it is necessary to consider other properties of the foam to comprehensively design the catalyst.
5. Conclusions
In this paper, by comparing different types of chain extenders, blowing agents and catalysts, the effects and changing laws on the mechanical properties, cell structure, skin and reactivity of polyurethane foams were studied. The results are shown as follows: First of all, the small molecule chain extenders include ethylene glycol, 1.3-propanediol and 1.4-butanediol, with the growth of their molecular chains, the hardness and tensile strength of polyurethane foam gradually decrease, and the elongation at break increases. Secondly, compared with water, using formic acid foaming, polyurethane foam has small cells, compact cell structure, dense skin crust and better touch feeling. Thirdly, compared with reactive catalysts A1, KC101 and DabcoEG, non-reactive catalysts A1, KC101 and DabcoEG are more helpful to improve the reactivity of polyurethane foam.
In the field of polyurethane foam for automobile steering wheel, this paper lays a theoretical research foundation for the development of polyurethane foam with better performance, summarizes the effects and influences of different kinds of additives, further standardizes and optimizes the formulation and development system of polyurethane foam for automobile steering wheel, and has certain guiding significance for the product research of automobile steering wheel, improving production efficiency and reducing production cost.
References
-
A. Paupério and R. N. Santos, “Development of integral skin foams based on modified isocyanate with self-Releasing Characteristics,” Journal of Cellular Plastics, Vol. 23, No. 5, pp. 448–459, Sep. 1987, https://doi.org/10.1177/0021955x8702300504
-
N. Gama, A. Ferreira, and A. Barros-Timmons, “Polyurethane foams: past, present, and future,” Materials, Vol. 11, No. 10, p. 1841, Sep. 2018, https://doi.org/10.3390/ma11101841
-
H. G. Ostfield, “Polyurethanes in automotive: technical aspects for their use in passenger vehicles,” Journal of Cellular Plastics, Vol. 19, No. 3, pp. 141–151, May 1983, https://doi.org/10.1177/0021955x8301900302
-
W. J. Seo et al., “Mechanical, Morphological, and thermal properties of rigid polyurethane foams blown by distilled water,” Journal of Applied Polymer Science, Vol. 90, No. 1, pp. 12–21, Oct. 2003, https://doi.org/10.1002/app.12238
-
K. H. Choe, D. S. Lee, W. J. Seo, and W. N. Kim, “Properties of rigid polyurethane foams with blowing agents and catalysts,” Polymer Journal, Vol. 36, No. 5, pp. 368–373, May 2004, https://doi.org/10.1295/polymj.36.368
-
Y. M. Son, J. D. Kim, S. W. Choi, J. H. Kim, N. Y. Her, and J. M. Lee, “Synthesis of polyurethane foam considering mixture blowing agents for application to cryogenic environments,” Macromolecular Materials and Engineering, Vol. 304, No. 11, p. 1900294, Nov. 2019, https://doi.org/10.1002/mame.201900294
-
S. Okuzono, H. Yoshimura, S. Arai, and D. W. Lowe, “Characterization of innovative tertiary amine catalyst systems for water-blown flexible polyurethane foams,” Journal of Cellular Plastics, Vol. 28, No. 2, pp. 130–148, Mar. 1992, https://doi.org/10.1177/0021955x9202800203
-
Z. Wang, C. Ma, C. Zhang, X. Li, S. Duan, and M. Chen, “Study on all water foaming of rigid polyurethane foam and design of high-performance formula,” in IOP Conference Series: Earth and Environmental Science, Vol. 446, No. 2, p. 022082, Feb. 2020, https://doi.org/10.1088/1755-1315/446/2/022082
-
M. Modesti, N. Baldoin, and F. Simioni, “Formic acid as a co-blowing agent in rigid polyurethane foams,” European Polymer Journal, Vol. 34, No. 9, pp. 1233–1241, Sep. 1998, https://doi.org/10.1016/s0014-3057(97)00263-2
-
A. Strachota, B. Strachotová, and M. Špírková, “Comparison of environmentally friendly, selective polyurethane catalysts,” Materials and Manufacturing Processes, Vol. 23, No. 6, pp. 566–570, Jul. 2008, https://doi.org/10.1080/10426910802157938
-
D. Sridaeng, W. Jitaree, P. Thiampanya, and N. Chantarasiri, “Preparation of rigid polyurethane foams using low-emission catalysts derived from metal acetates and ethanolamine,” e-Polymers, Vol. 16, No. 4, pp. 265–275, Jul. 2016, https://doi.org/10.1515/epoly-2016-0021
About this article
The authors have not disclosed any funding.
The datasets generated during and/or analyzed during the current study are available from the corresponding author on reasonable request.
The authors declare that they have no conflict of interest.