Abstract
Through the practice of a highway pavement overhaul project, the feasibility of the old concrete pavement recycling scheme in terms of technology, economy and sustainable development is analyzed. The dynamic characteristics of concrete pavement were tested. The results show that crushing the old concrete panels into recycled aggregates and then re-use them not only eliminates the negative impact on the ecological environment caused by the land occupation of waste aggregates and needs to be disposed of, but also promotes the recycling of engineering waste and reduces the project cost. The pavement paved with recycled cement concrete can basically achieve the same dynamic performance as the pavement paved with conventional concrete.
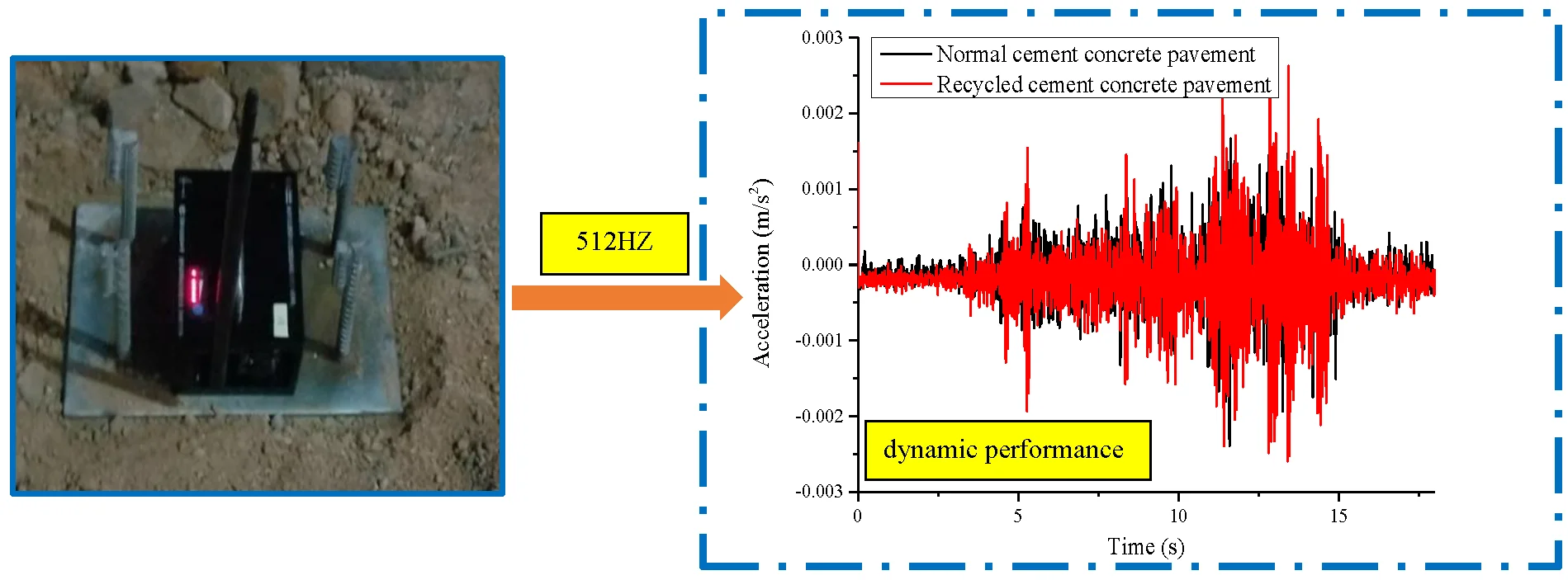
Highlights
- The measurement was made with the wireless units that contained accelerometer measuring vibration in the vertical direction with the sampling frequency of 512 Hz.
- The pavement paved with recycled cement concrete can basically achieve the same dynamic performance as the pavement paved with conventional concrete.
- The stable recycled mixture base can meet the road requirements under various traffic conditions.
1. Introduction
The old aggregate that comes from the broken cement concrete panel is the recycled aggregate, which can play a better role in the base of the new road after effective treatment. By strictly controlling the particle size and quality of the aggregates produced when the old cement concrete pavement is broken, and using reasonable construction techniques, the paved base can meet the requirements of high-grade highway base detection indicators. Many domestic researchers and engineering technicians have carried out a lot of research on the recycling of waste concrete. Yang Q. G. [1] studied the physical properties and mechanical properties of recycled aggregates, and studied the application of old recycled aggregates in pavement base and surface. Gao Q. J. [2] and others studied the performance of cement-stabilized recycled aggregates, and verified that cement-stabilized recycled aggregates have good road performance by paving test sections. Zhang L. M. [3] studied and analyzed the physical and mechanical properties of recycled aggregates after crushing old cement concrete pavement. This project mainly studies the feasibility of using the aggregates produced by the processing of old cement concrete pavement as cement-stabilized crushed stone base materials. The dynamic characteristics of concrete pavement were tested to compare the dynamic performance of the pavement by using recycled old cement concrete.
2. Characteristics of recycled aggregates
2.1. Morphology of recycled aggregates
There are generally three forms of recycled coarse aggregates: one is composite particles, that is, stones with a part of cement mortar on the surface; the other is ordinary aggregate particles, which are basically ordinary aggregates or a small amount of adhesive mortar; the third is cement mortar particles. When the broken particles of the cement concrete panel are large, there are more composite particles; when the broken particles are small, the main particles are gravel particles and cement mortar particles. Due to the uneven size of the old mortar attachment surface on the surface of the particles, the composite particles themselves are very different, so it has a greater impact on the performance of the recycled base material. In general, among the recycled aggregates formed by the crushing of cement concrete pavement, the proportion of composite particles is the largest, and the proportion of particles in the form of ordinary aggregates is less.
2.2. Properties of recycled aggregates
2.2.1. Technical indicators of recycled aggregates
The gradation of recycled aggregates is the mutual proportional relationship between the different particle sizes that constitute the recycled aggregates, and it is an important indicator to reflect the properties of recycled aggregates. The quality of particle grading is related to the strength and shrinkage resistance of the material.
In this paper, the technical indicators of aggregates with a particle size of 16 mm-20 mm in the recycled aggregates were first tested. The comparison values between the test results and the standard standards are listed in Table 1. It can be seen from the test results that the water absorption performance of the recycled aggregate exceeds the standard value specified in the specification.
Table 1Technical indicators of 16 mm ~20 recycled aggregate
Test item | Test results | Standard specification |
Crush value, % | 26.7 | ≤ 28 |
Water absorption, % | 4.2 | ≤ 2.0 |
Needle-like particle content (mixture), % | 5.9 | ≤ 15 |
Methylene blue value, g/kg | 0.25 | ≤ 25 |
2.2.2. Recycled aggregate particle size and water absorption
In this paper, the water absorption rates of recycled aggregates and natural coarse aggregates with particle sizes ranging from 5 mm to 10 mm, 10 mm to 16 mm, and 16 mm to 20 mm were compared at 10 min, 30 min, and 40 h, respectively. The test results are shown in Table 2. It can be seen from the test results that the water absorption of the two coarse aggregates increases gradually with the increase of time, and decreases with the increase of the particle size. At the same particle size, the water absorption of the recycled aggregate is higher than that of the natural coarse aggregate. The water absorption rate of the material is higher.
Table 2Relationship between water absorption characteristics and aggregate particle size
Time | Natural coarse aggregate (%) | Recycled aggregates (%) | ||||
5-10 mm | 10-16 mm | 16-20 mm | 5-10 mm | 10-16 mm | 16-20 mm | |
10 min | 2.4 | 1.2 | 0.8 | 5.5 | 3.9 | 2.9 |
30 min | 3.2 | 1.6 | 1.0 | 6.2 | 4.4 | 3.2 |
40 h | 4.0 | 2.0 | 1.4 | 6.6 | 4.7 | 4.2 |
3. Determination of base layer configuration of recycled aggregate cement stabilized crushed stone
According to the design requirements of the mix ratio of inorganic binders, cements with a dosage of 4.5 %, 5.0 % and 5.5 % were added in the test, and the compaction test of the mixture was carried out to determine the optimal water content, and the unconfined compression was carried out for 7 days. In the strength test, the grading listed in Table 3 is all recycled aggregates, and the grading 0 mm-5 mm listed in Table 4 is new material, and river sand is not used.
Through the analysis of the test data in Table 3 and Table 4, the unconfined compressive strength of the specimens whose aggregates are completely made of recycled old aggregates cannot fully meet the design requirements that the strength of the base layer should reach 3 MPa-4 MPa, and Unconfined compressive strength coefficient of variation is large. The coarse aggregate is made of recycled aggregate, and the fine aggregate is made of new aggregate, and the test data meets the design requirements. The technical quality indicators used in combination with recycled coarse aggregate and new fine aggregate all meet road performance and meet the requirements of specifications and design. Therefore, the overhaul project of cement concrete pavement of highway can use the coarse aggregate regenerated from old concrete panels. It is used as cement stabilized gravel base material.
Table 3Summary table of strength test of old aggregate completely using broken panel
Gradation type | 10-30 mm | 5-10 mm | 0-5 mm | Sand (%) | Unconfined compressive strength (MPa) | ||
4.5 % cement consumption | 5.0 % cement consumption | 5.5 % cement consumption | |||||
1 | 31.5 | 31.5 | 37 | – | 2.0 | 2.4 | 3.0 |
2 | 38 | 25 | 12 | 25 | 2.8 | 3.6 | 4.1 |
3 | 41.3 | 27.5 | 20.8 | 10.4 | 2.2 | 2.8 | 3.7 |
4 | 34.4 | 34.4 | 10.4 | 20.8 | 2.7 | 3.4 | 4.2 |
5 | 42.0 | 21.0 | 25 | 12 | 2.6 | 3.3 | 3.8 |
6 | 49 | 24 | 9.0 | 18.0 | 2.8 | 3.5 | 4.0 |
7 | 36.5 | 36.5 | 18.0 | 9.0 | 2.1 | 2.5 | 2.8 |
8 | 44 | 29 | 27.0 | – | 2.2 | 2.6 | 3.2 |
9 | 46 | 23 | 31 | – | 2.4 | 2.6 | 3.4 |
10 | 31.5 | 31.5 | 0.0 | 37.0 | 2.7 | 3.0 | 3.6 |
11 | 44 | 29 | 0.0 | 27.0 | 2.3 | 2.8 | 3.8 |
12 | 46 | 23 | 0.0 | 31 | 2.1 | 3.6 | 4.0 |
Table 4Summary table of strength test of recycled aggregates with 0-5 mm particle size using new materials
Gradation type | 10-30 mm | 5-10 mm | 0-5 mm | Sand | Unconfined compressive strength (MPa) | ||
4.5 % cement consumption | 5.0 % cement consumption | 5.5 % cement consumption | |||||
13 | 44 | 29 | 27.0 | – | 3.6 | 4.4 | 4.8 |
14 | 46 | 23 | 31 | – | 3.8 | 4.6 | 4.9 |
15 | 31.5 | 31.5 | 37.0 | – | 3.7 | 4.5 | 5.0 |
4. Mechanical properties of cement stabilized macadam base used by recycled aggregate
4.1. Unconfined compressive strength of recycled mixture
According to the test results in Table 4, it is comprehensively decided to use the 14th grading to mix and vibrate the compacted specimens to test the compressive strength on days 7, 28, 90 and 180. The test results are shown in Table 5.
Table 5Unconfined compressive strength test data table for four ages
Category | Cement dosage (%) | 4.5 | 5.0 | 5.5 |
Recycled mix | Day 7 unconfined compressive strength (MPa) | 3.8 | 4.6 | 4.9 |
Coefficient of deviation (%) | 11.84 | 10.56 | 10.33 | |
Day 28 unconfined compressive strength (MPa) | 4.9 | 5.8 | 6.1 | |
Coefficient of deviation (%) | 8.79 | 8.84 | 7.66 | |
Day 90 unconfined compressive strength (MPa) | 6.2 | 6.9 | 7.0 | |
Coefficient of deviation (%) | 8.84 | 7.47 | 7.39 | |
Day 180 unconfined compressive strength (MPa) | 7.3 | 7.8 | 8.1 | |
Coefficient of deviation (%) | 9.89 | 8.63 | 6.39 |
From the test results, it can be seen that:
(1) The deviation coefficient of the compressive strength of the recycled mixture on the 7th day and the 28th day is less than 15 %; and the deviation coefficient of the 90th day and the 180th day is less than 10 %, which can meet the design requirements.
(2) When the cement dosage of recycled aggregate is 4.5 %, the representative value of compressive strength on the 7th day is 3.8 MPa, which meets the requirements of A, B, C, and D grades of traffic on the base strength in “Specifications for Design of Highway Asphalt Pavement”.
4.2. Unconfined compressive elastic modulus
According to the test results of the optimum moisture content and maximum dry density, when the cement dosage was 4.5 %, 5.0 % and 5.5 %, respectively, the specimens were formed by vibration compaction method. The test results of the unconfined compressive elastic modulus of the specimens on the 28th day, the 90th day and the 180th day are shown in Table 6.
Table 6Summary of unconfined compressive resilience modulus
Category | Cement dosage (%) | 4.5 | 5.0 | 5.5 |
Recycled mix | Day 28 unconfined compressive resilience modulus (MPa) | 2886.1 | 4066.6 | 4704.4 |
Coefficient of deviation (%) | 6.50 | 10.02 | 12.79 | |
Day 90 unconfined compressive resilience modulus (MPa) | 3771.7 | 4982.7 | 5687.7 | |
Coefficient of deviation(%) | 10.28 | 8.32 | 10.0 | |
Day 180 unconfined compressive resilience modulus (MPa) | 5563.7 | 6527.5 | 7184.8 | |
Coefficient of deviation (%) | 12.42 | 13.68 | 3.73 |
From the test results in the table above, the following conclusions can be drawn:
(1) The compressive elastic modulus of recycled mixture on the 28th day, the 90th day and the 180th day, all increased with the increase of cement.
(2) The coefficient of variation of all test data of the compressive resilience modulus of recycled mixture is within 15 %, and the compressive resilience modulus increases rapidly in the early stage and slows down in the later stage, which is very consistent with the performance changes of cement-stabilized base layers.
(3) The compressive resilience modulus meets the requirements of grade road for semi-rigid base.
4.3. Splitting strength test
For the specimens with cement dosage of 4.5 %, 5.0 % and 5.5 %, the splitting strength test was carried out on the 7th, 28th, 90th and 180th days, and the results are shown in Table 7.
It can be seen from Table 8 that the deviation coefficients of the splitting strength of the recycled mixture at four ages are all within 10 %, which fully meets the requirements of the specification; The splitting strength of recycled mixture is significantly higher than that of other cement-stabilized bases under the same conditions. The stable recycled mixture base can meet the road requirements under various traffic conditions.
Table 7Splitting strength test results at four ages
Category | Cement dosage (%) | 4.5 | 5.0 | 5.5 |
Recycled mix | Day 7 splitting strength (MPa) | 0.393 | 0.469 | 0.573 |
Coefficient of deviation (%) | 3.0 | 4.60 | 4.80 | |
Day 28 splitting strength (MPa) | 0.640 | 0.765 | 0.916 | |
Coefficient of deviation (%) | 9.90 | 1.67 | 6.80 | |
Day 90 splitting strength (MPa) | 0.89 | 1.15 | 1.52 | |
Coefficient of deviation (%) | 5.28 | 3.10 | 3.92 | |
Day 180 splitting strength (MPa) | 0.98 | 1.23 | 1.77 | |
Coefficient of deviation (%) | 6.92 | 6.61 | 3.87 |
5. Field vibration measurement of a highway after paving recycled cement concrete
A road was selected, and the pavement was paved with recycled cement concrete and conventional cement concrete respectively. The measurement was made with the wireless units that contained accelerometer measuring vibration in the vertical direction with the sampling frequency of 512 Hz, as shown in Fig. 1. The vehicle-induced vibration of the two kinds of pavement was tested, and the dynamic performance of the two kinds of cement concrete pavement was compared, as shown in Fig. 2.
Fig. 1Photo of wireless unit
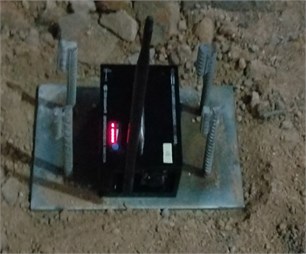
During the test, 20 seconds of vehicle-induced vibration data were randomly tested. It can be found that the vibration acceleration of the two different concrete pavement is relatively close, and the peak value is around 0.0025 m/s2. It can be seen that the pavement paved with recycled cement concrete can basically achieve the same dynamic performance as the pavement paved with conventional concrete.
Fig. 2Vibration measurement of two kinds of cement concrete pavement
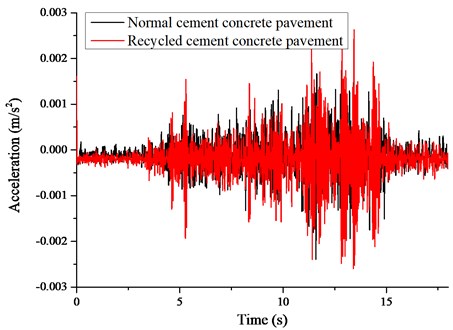
6. Conclusions
Through the research on the recycling technology of old concrete panels in a highway overhaul project, combined with the economic and environmental benefits, and the good road performance of the pavement after the overhaul, the following conclusions are drawn:
1) Through the test of recycled aggregates and the research on the mix ratio design of recycled cement stabilized crushed stone base, it is found that the designed strength of recycled cement stabilized crushed stone base can meet the requirements of the specification for the strength of cement base.
2) Through the inspection of the overhauled pavement, the driving quality index and anti-skid performance of the pavement are evaluated as “excellent” and “good”, and the deflection test also meets the requirements, indicating that the application of recycled cement stabilized gravel base is feasible.
3) Although recycled aggregates require a series of processing, which requires a certain amount of manpower and material resources, from the perspective of cost savings, the application of recycled aggregates is worthy of continued research and promotion.
4) The pavement paved with recycled cement concrete can basically achieve the same dynamic performance as the pavement paved with conventional concrete
References
-
Q. G. Yang, Z. J. Yi, Z. W. Lee, and T. L. Wan, “Recycling of old road cement and concrete,” China Highway Society, 2002.
-
Q. J. Gao, L. Cong, and Z. Y. Guo, “Recycling of waste cement concrete pavement in pavement base,” Highway Traffic Science and Technology, Vol. 2, pp. 20–23, 2008.
-
L. M. Zhang, “Research on the performance of cement stabilized recycled cement concrete aggregate base,” Harbin Institute of Technology, 2006.
-
B. Li, H. L. Yang, and Z. F. Zhu, “Research on mechanical properties of cement stabilized recycled aggregate base,” Shanxi Architecture, Vol. 22, pp. 161–162, 2008.
-
H. C. Zhou, “Performance analysis and construction of recycled aggregate concrete,” Chongqing University, 2007.
About this article
The authors have not disclosed any funding.
The datasets generated during and/or analyzed during the current study are available from the corresponding author on reasonable request.
The authors declare that they have no conflict of interest.